强化传热技术进展 华中科技大学能源与动力工程学院 黄素逸.docx
《强化传热技术进展 华中科技大学能源与动力工程学院 黄素逸.docx》由会员分享,可在线阅读,更多相关《强化传热技术进展 华中科技大学能源与动力工程学院 黄素逸.docx(12页珍藏版)》请在冰豆网上搜索。
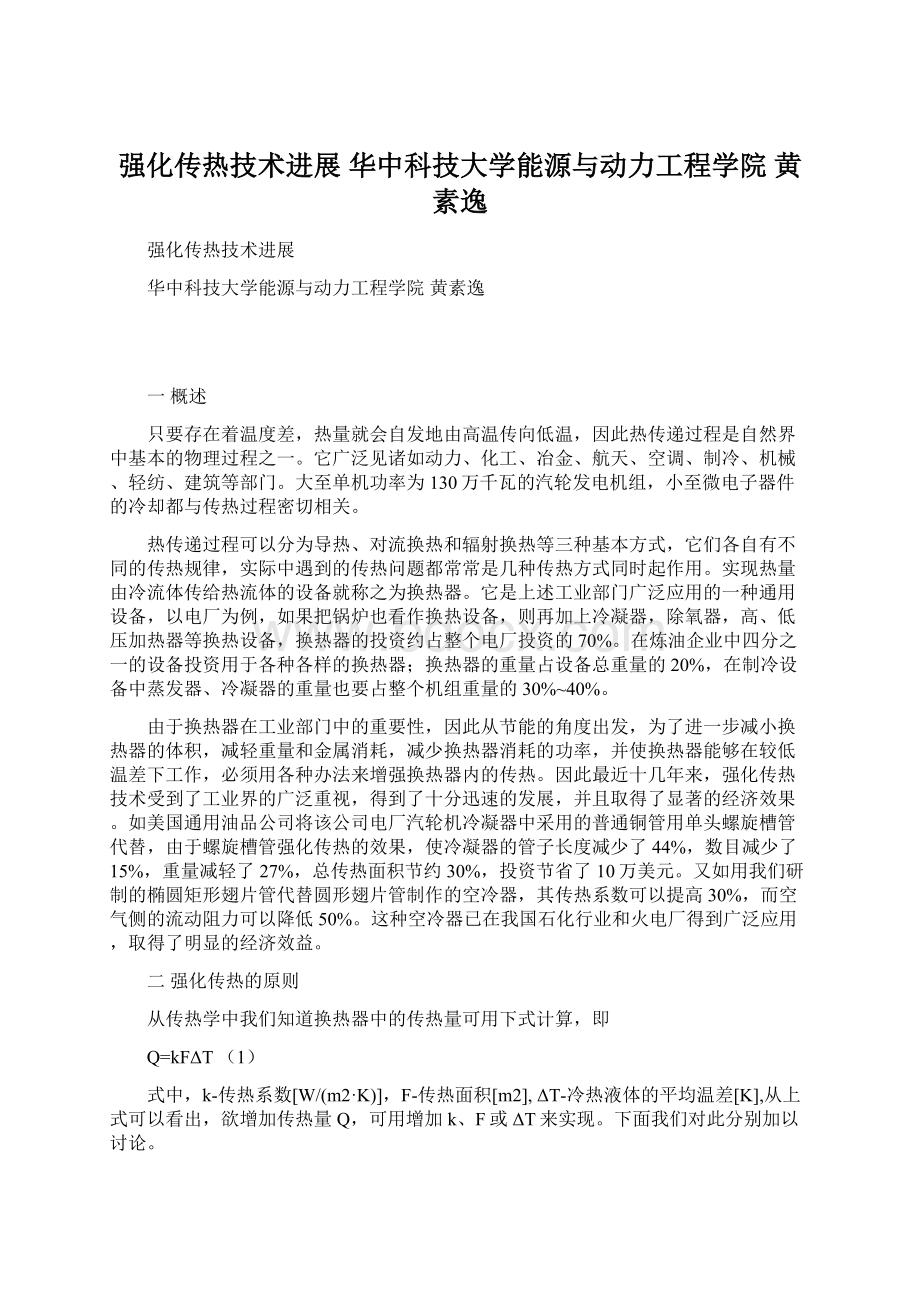
强化传热技术进展华中科技大学能源与动力工程学院黄素逸
强化传热技术进展
华中科技大学能源与动力工程学院黄素逸
一概述
只要存在着温度差,热量就会自发地由高温传向低温,因此热传递过程是自然界中基本的物理过程之一。
它广泛见诸如动力、化工、冶金、航天、空调、制冷、机械、轻纺、建筑等部门。
大至单机功率为130万千瓦的汽轮发电机组,小至微电子器件的冷却都与传热过程密切相关。
热传递过程可以分为导热、对流换热和辐射换热等三种基本方式,它们各自有不同的传热规律,实际中遇到的传热问题都常常是几种传热方式同时起作用。
实现热量由冷流体传给热流体的设备就称之为换热器。
它是上述工业部门广泛应用的一种通用设备,以电厂为例,如果把锅炉也看作换热设备,则再加上冷凝器,除氧器,高、低压加热器等换热设备,换热器的投资约占整个电厂投资的70%。
在炼油企业中四分之一的设备投资用于各种各样的换热器;换热器的重量占设备总重量的20%,在制冷设备中蒸发器、冷凝器的重量也要占整个机组重量的30%~40%。
由于换热器在工业部门中的重要性,因此从节能的角度出发,为了进一步减小换热器的体积,减轻重量和金属消耗,减少换热器消耗的功率,并使换热器能够在较低温差下工作,必须用各种办法来增强换热器内的传热。
因此最近十几年来,强化传热技术受到了工业界的广泛重视,得到了十分迅速的发展,并且取得了显著的经济效果。
如美国通用油品公司将该公司电厂汽轮机冷凝器中采用的普通铜管用单头螺旋槽管代替,由于螺旋槽管强化传热的效果,使冷凝器的管子长度减少了44%,数目减少了15%,重量减轻了27%,总传热面积节约30%,投资节省了10万美元。
又如用我们研制的椭圆矩形翅片管代替圆形翅片管制作的空冷器,其传热系数可以提高30%,而空气侧的流动阻力可以降低50%。
这种空冷器已在我国石化行业和火电厂得到广泛应用,取得了明显的经济效益。
二强化传热的原则
从传热学中我们知道换热器中的传热量可用下式计算,即
Q=kFΔT
(1)
式中,k-传热系数[W/(m2·K)],F-传热面积[m2],ΔT-冷热液体的平均温差[K],从上式可以看出,欲增加传热量Q,可用增加k、F或ΔT来实现。
下面我们对此分别加以讨论。
1.增加冷热液体的平均温差ΔT
在换热器中冷热液体的流动方式有四种,即顺流、逆流、交叉流、混合流。
在冷热流体进出口温度相同时,逆流的平均温差ΔT最大,顺流时ΔT最小,因此为增加传热量应尽可能采用逆流或接近于逆流的布置。
当然可以用增加冷热流体进出口温度的差别来增加ΔT。
比如某一设备采用水冷却时传热量达不到要求,则可采用氟里昂来进行冷却,这时平均温差ΔT就会显著增加。
但是在一般的工业设备中,冷热流体的种类和温度的选择常常受到生产工艺过程的限制,不能随意变动;而且这里还存在一个经济性的问题,如许多工业部门经常采用饱和水蒸气作加热工质,当压力为15.86×105Pa时,相应的饱和温度为437K,若为了增加ΔT,采用更高温度的饱和水蒸气,则其饱和压力亦相应提高,此时饱和温度每增高2.5K,相应压力就要上升105Pa。
压力增加后换热器设备的壁厚必须增加,从而使设备庞大,笨重,金属消耗量大大增加,虽然可采用矿物油,联苯等作为加热工质,但选择的余地并不大。
综上所述,用增加平均温差ΔT的办法来增加传热只能适用于个别情况。
2.扩大换热面积F
扩大换热面积是常用的一种增强换热量的有效方法,如采用小管径。
管径越小,耐压越高,而且在金属重量相同的情况下,表面积也越大。
采用各种形状的肋片管来增加传热面积其效果就更佳了。
这里应特别注意的是肋片(扩展表面)要加在换热系数小的一侧,否则会达不到增强传热的效果。
一些新型的紧凑式换热器,如板式和板翅式换热器,同管壳式换热器相比,在单位体积内可布置的换热面积多得多。
如管壳式换热器在1m3体积内仅能布置换热面积150m2左右。
而在板式换热器中则可达1500m2,板翅式换热器中更可达5000m2,因此在后两种换热器中其传热量要大得多。
这就是它们在制冷、石油、化工、航天等部门得以广泛应用的原因。
当然紧凑式的板式结构对高温、高压工况就不宜应用。
对于高温、高压工况一般都采用简单的扩展表面,如普通肋片管、销钉管、鳍片管,虽然它们扩展的程度不如板式结构高,但效果仍然是显著的。
采用扩展表面后,如果几何参数选择合适还可同时提高换热器的传热系数,这样增强传热的效果就更好了。
值得注意的是,采用扩展面常会使流动阻力增加,金属消耗增加,因此在应用时应进行技术经济比较。
3.提高传热系数k
提高传热系数k是强化传热的最重要的的途径,且在换热面积和平均温差给定时,是增加换热量的唯一途径。
当管壁较薄时从传热学中我们知道,传热系数k可用下式计算:
(2)
式中,α1—热液体和管壁之间的对流换热系数,α2—冷流体和管壁之间的对流换热系数,δ—管壁的厚度,λ—管壁的导热系数。
一般讲金属壁很薄,导热系数很大,δ/λ可以忽略。
因此传热系数k可以近似写成:
k=α1α2/(α1+α2)。
由此可知欲增加k,就必须增加α1和α2,但当α1和α2相差较大时,增加它们之中较小的一个最有效。
要想增加对流换热系数,就需根据对流换热的特点,采用不同的强化方法。
我国学者过增元院士在研究对流换热强化时,提出了著名的场协同理论。
该理论指出要获得高的对流换热系数的主要途径有:
1)提高流体速度场和温度场的均匀性;
2)改变速度矢量和热流矢量的夹角,使两矢量的方向尽量一致;
根据上述理论,目前强化传热技术有两类:
一类是耗功强化传热技术,一类是无功强化传热技术。
前者需要应用外部能量来达到强化传热的目的,如机械搅拌法、振动法、静电场法等。
后者不需外部能量,如表面特殊处理法、粗糙表面法、强化元件法、添加剂法等。
由于强化传热的方法很多,因此在应用强化传热技术时,我们应遵循以下原则:
1)首先应根据工程上的要求,确定强化传热的目的,如减小换热器的体积和重量;提高现有换热器的换热量;减少换热器的阻力,以降低换热器的动力消耗等。
因为目的不同,采用的方法也不同,与此同时确定技术上的具体要求。
2)根据各种强化方法的特点和上述要求,确定应采用哪一类的强化手段。
3)对拟采用的强化方法从制造工艺,安全运行,维修方便和技术经济性等方面进行具体比较和计算,最后选定强化的具体技术措施。
只有按上述步骤才能使强化传热达到最佳的经济效益。
三单向介质管内对流换热的强化
1流体旋转法
强化单向介质管内对流换热的有效方法之一是使流体在管内产生旋转运动,这时靠壁面的流体速度增加,加强了边界层内流体的搅动。
同时由于流体旋转,使整个流动结构发生变化,边界层内的流体和主流流体得以更好的混合。
以上这些因素都使换热的到了强化。
使流体旋转的方法很多,在工艺上可行的有以下几种:
(1)管内插入物
使流体旋转最简单的方法是管内插入各种可使流体旋转的插入物。
如扭带、静态混合器、螺旋片等。
a.扭带
扭带是一种最简单而又使流体旋转的旋流发生器。
它是由薄金属片(通常是铝片)扭转而成。
扭带的扭转程度由每扭转3600的长度H(称为全节距)与管子内径d之比来表征。
H/d称之为扭率。
扭率不同强化传热的效果也不同,试验表明,扭率为5左右效果最好。
b.错开扭带
错开扭带是将扭带剪成扭转180°的短元件,互相错开90°再点焊而成。
c.静态混合器
由一系列左、右扭转180°的短元件,按照一个左旋、一个右旋的排列顺序,互相错开900再点焊而成。
d.螺旋片
由宽度一定的薄金属片在预先车制出的有一定深度和一定节距的螺旋槽的心轴上绕成。
e.径向混合器
用薄金属片冲压成具有一个圆锥形收缩环和一个圆锥形扩张环的元件,在环上开许多小孔,然后将这些元件按一定间距点焊在一根金属丝上,插入管内就成为一个径向混合器。
f.金属螺旋线圈
用细金属丝绕制成三叶或四叶的螺旋线圈,插入管内,即可使流体旋转。
除上述常用的插入物外,还有其它一些形状的插入物。
管内插入上述插入物后,由于流体的旋转,使管内流体由层流向湍流过渡的临界雷诺数Re降低,强化了管内换热。
当然由于流体的旋转,流动阻力也会相应增加。
实验研究证明,在低Re数区采用插入物比高Re数区强化传热的效果更加显著,这说明层流时采用插入物是很有效的。
等功率和等流量的试验研究表明,各种插入物的强化效果在层流区都随Re的增加而增加。
在相当于光管由层流向湍流过渡的临界Re时达到最大值,然后又随Re的增加而减小。
在Re=500~10000的范围内,在相同的流量下,静态混合器可获得较强的传热效果。
因此当系统压降有裕量的情况下,为强化传热可优先采用静态混合器。
在要求消耗功率一定的情况下,则可选用螺旋片和扭带,此时螺旋片还有节约材料的优点。
许多研究者提供了管内加插入物后计算流动阻力和传热的公式,这些公式大多是以实验研究为基础的。
在选用这些公式时应注意这些公式的应用条件和范围。
同时值得注意的是,采用管内插入物后传热增加了,但流动阻力也随之增加,因此通常在计算强化传热的同时,还应进行流动阻力的核算和经济性的比较,才能获得满意的结果。
(2)螺旋槽管和螺旋内肋管
管内插入物的方法,其结构不够牢靠,制造安装工作量大,一般宜在增强现有换热设备的传热能力上采用。
对新设计制造的换热设备,可以采用螺旋槽管或螺旋内肋管来使流体旋转。
螺旋槽管可以用普通圆管滚压加工而成,它有单头和多头之分。
螺旋槽管的作用也是引起流体旋转,使边界层厚度减薄并在边界层内产生扰动,从而使传热增强。
研究表明,在相同的Re及槽距、槽深的情况下,单头螺旋和三头螺旋相比,强化传热的效果差别不大,但流动阻力却减小很多,因此实际上多采用单头螺旋槽管。
采用螺旋内肋管,一方面可使流体旋转,另一方面内肋片又加大了管内换热面积,有利于增强传热或降低壁温。
虽然其加工比较复杂,但仍是一种理想的强化传热管。
2.改变流道截面形状
1)层流工况和过渡工况
流动截面形状对换热和阻力有很大的影响,特别是对层流工况而言。
试验证明,当管道长度较长及雷诺数Re较小时,换热的Nu数实际上与雷诺数Re数无关。
表1列出了各种不同截面的流道中最小的Nu数及阻力系数ξ的值。
表1层流时不同截面形状的Nu数
管道截面形状
热流恒定时的Nu
壁温恒定时的Nu
ξRe
等腰三角形20°
40°
60°
80°
100°
120°
2.7
2.95
3.0
2.95
2.8
2.7
2.7
2.7
2.7
2.7
2.7
2.7
51.5
53
53.3
52.7
52
51
圆形
4.36
3.66
64
矩形a/b=1
a/b=0.7
a/b=0.5
a/b=0.3
a/b=0.1
a/b=0
3.63
3.8
4.1
4.9
6.8
8.24
2.89
3.0
3.3
4.3
6.1
7.54
56.8
58
62
70
85
96
从表1中可以看出,合适高度比的矩形截面的换热比三角形截面和圆形截面要高得多,以锅炉中的回转式空气预热器为例,由波纹板和平板可组成不同形状的流道,如三角形和近似矩形。
计算表明在传递相同的热量时,三角形流道将比矩形流道的换热器长18%,而流动阻力矩形流道比三角形流道要低30%。
对一般圆管和矩形截面而言,在管道中温度条件相同时,采用矩形管道也能增加换热系数,但与此同时流动阻力会急剧增加。
在由层流向湍流过渡的过渡区中管道截面形状对换热也有较大的影响。
例如在具有槽形截面通道的板式换热器中改用波纹板可以显著提高换热系数。
2)湍流工况
a.横槽纹管
湍流工况时为改变管子的流道截面情况,应用最广的是所谓横槽纹管。
它是由普通圆管滚轧而成。
流体流过横槽纹管会形成漩涡和强烈的扰动,从而强化了传热。
强化的效果取决于节距p和横槽纹的突出高度h之比。
实际应用中p/h
10。
与前述的螺旋槽管相比,由于横槽纹管的漩涡主要在管壁处形成,对流体主流的影响较小,所以其流动阻力比相同节距与槽深的螺旋管小。
谭盈科等对p/d=0.5,h/d=0.03的横槽纹管的测定表明,当工质为空气时,Re=3.4×104。
横槽纹管可比普通光管的换热系数提高1.7倍,阻力增加2.2倍;如工质为水,Re=4000,换热系数可提高1.4倍,阻力增加1.7倍。
当流体纵向冲刷环形槽道时,为了强化传热可在管内采用横槽纹管,这样内外流体都能得到强化。
b.扩张—收缩管
流体沿流动方向依次交替流过收缩段和扩张段。
流体在扩张段中产生强烈的漩涡被流体带入收缩段时得到了有效的利用,且收缩段内流速增高会使流体层流底层变薄,这些都有利于增强传热。
一般扩缩管中扩张段和收缩段的角度应使流体产生不稳定的分离现象,从而有利于传热,而流动阻力却增加不多。
扩缩管是一种很有前途的强化传热管,特别是对污染的流体,扩缩管不易产生堵塞现象。
对于非圆形槽道亦可利用扩缩管的原理使流道扩缩,如在两块平板间加入两块带锯齿表面的板,就可构成扩缩槽道。
四单向介质管束外对流换热的强化
单向介质横向或纵向掠过管束是工程上常见的对流换热过程,其最实用的强化方法是扩展换热面和采用各种异形管。
1.扩展换热面
当换热面一侧为气体,另一侧为液体时,由于气体侧的换热系数比液体侧小得多(一般小10~50倍)。
这时应用扩展换热面的方法来提高传热系数是最有效的办法。
为了使换热器更加紧凑和进一步提高气侧的换热,现在各种异性扩展换热面得以迅速发展,它们可使气侧的换热系数较普通扩展面再提高0.5~1.5倍。
(1)平行板肋换热器中各种异性扩展换热面
平行板肋换热器中的异性扩展换热面发展最快,应用也最广。
他们是各种普通扩展面(如矩形、三角形)的变形,其种类繁多,形状各异。
最常用的有波形、叉排短肋形、销钉形、多孔形和百叶窗形。
这些换热面的肋片密度都很高,一般为每米300~500片。
由于通常当量直径小,气体密度小,因此它们经常处于低Re数的范围,即Re=500~1500,亦即处于层流状态。
它们的特点,或者是利用流道的特殊截面形状来强化传热,如波形通道中产生的二次流;或者是使通道中流动的边界层反复形成又反复破坏来强化换热,叉排短肋形、销钉形就是如此。
下面分别对常用的异性扩展面加以讨论。
a.波形扩展换热面
波形扩展换热面能使气体流过波形表面的凹面时形成漩涡,造成反方向的旋转;而在凸面处又会形成局部的流体脱离,这两种因素会使换热得到强化。
b.叉排短肋形扩展面
这种叉排短肋形扩展面是将通常的矩形长直肋变成短肋,并错开排列,这样在前一块短肋上形成的层流边界层在随后的叉排肋处被破坏,并在其后形成漩涡,这一过程反复进行。
由于边界层开始形成时较薄(入口效应),热阻较小,因此换热得到充分的强化。
一般叉排短肋要比矩形直肋换热系数高一倍,当然相应阻力也要增加,一般约增大2倍。
c.销钉形扩展表面
销钉形扩展表面与叉排短肋类似,它使用销钉来代替短肋,其强化换热的机理也与短肋类似。
d.多孔形扩展换热面
这种换热面是先在板上打许多孔,再将板弯成通道,当孔足够多时,由于孔的扰动可以破坏板上的流动边界层,从而强化传热。
e.百叶窗形扩展换热面
在板上冲许多百叶窗,再将板弯成通道,这些百叶窗的凸出物能破坏边界层,从而增强传热的效果。
(2)圆管上的各种异形扩展换热面
圆管上的异形扩展换热面通常是在普通圆肋的基础上形成的,如开槽肋片,开三角孔并弯边的肋片,扇形肋片,绕圈形肋片等,它们的目的都是为了破坏流动边界层从而强化传热。
肋片的形状对换热有很大的影响。
我们研究过椭圆管上套圆形肋片、椭圆形肋片和矩形翅片(其四角上带有绕流孔),结果发现矩形翅片效果最好,可使换热系数较前者提高7%。
2.采用异形管
为了强化管束传热,在工程应用上已越来越广泛地采用异形管来代替圆管。
如椭圆管、滴形管、透镜管等。
其中以扁管和椭圆管应用最广。
以作者研究的椭圆矩形翅片管为例,与圆管相比,由于椭圆管的流动性好,流动阻力小,且在相同的管横截面积下,椭圆管的传热周边比圆管长;从布置上讲在单位体积内可布置更多的管子。
因此单位体积的传热量高。
作者研制的TZ型椭圆矩形翅片管散热器与SRZ型圆形圆翅片管散热器相比,阻力可降低59%,传热系数可增加67%,单位体积的传热量可提高80%,性能明显改进。
目前国内外大规模的风冷技术中广泛应用的也是各种椭圆矩形翅片管。
在国外直接空冷电厂中换热面积常常达到几十万平方米。
此时椭圆管的尺寸(长、短轴之比)和翅片的形状、间距以及翅片与管子接触的紧密程度对换热性能有很重要的影响。
随着技术的发展,螺旋扁管、螺旋椭圆扁盘及交叉缩放椭圆管等也获得越来越多的应用。
五单相介质对流换热的耗功强化技术
强化单相介质对流换热,除上面介绍的普遍应用的无功方法外,针对一些特殊的换热问题,也可采用耗功的强化方法。
1.机械搅拌法
此法主要应用于强化容器中的对流换热。
容器中的单相介质对流换热主要是自然对流,这时换热系数低,温度分布很不均匀,采用机械搅拌法可以得到很好的效果。
容器中的介质粘度较低时,通常采用小尺寸的机械搅拌器。
搅拌器的直径d一般为容器直径D的1/4~1/2,搅拌叶片的高度,从底部算起约为液体总高度H的1/3。
容器中为高粘度介质时,则应用比容器直径略小的低速螺旋式或锚式搅拌器。
在进行搅拌器计算时应区分容器中的介质是牛顿流体还是非牛顿流体,它们的计算方法是不同的。
2.振动法
有两种振动法,一种是使换热面振动,一种是使流体脉动或振动,这两种方法均可强化传热。
(1)换热面的振动
对于自然对流,实验证明,对静止流体中的水平加热圆柱体振动,当振动强度达到临界值时,可以强化自然对流换热系数。
实验还证明圆柱体垂直振动比水平振动效果好。
在小振幅和高频率时,振动可使换热系数增加7~50%
对于强制对流,许多研究者证明,根据振动强度和振动系统的不同,换热系数比不振时可增大20%~400%。
值得注意的是,强制对流时换热面的振动有时会造成局部地区的压力降低到液体的饱和压力,从而有产生汽蚀的危险。
(2)流体的振动
利用换热面振动来强化传热,在工程实际应用上有许多困难,如换热面有一定质量,实现振动很难;且振动还容易损坏设备,因此另一种方法是使流体振动。
对于自然对流,许多人研究了振动的声场对换热的影响,一般根据具体条件的不同,当声强超过140分贝使可使换热系数增加1~3倍。
值得注意的是,采用声振动也有不少困难。
实际应用中如有可能首先应用强制对流来代替自然对流,或用机械搅拌,这样才能更有效果。
对于强制对流,由于强制对流换热系数已经很高,采用声振动时其效果并不十分显著。
除了声振动外,其它的低频脉动(如泵发生的脉动)也能起到类似强化传热的作用。
众所周知,当流体横掠单管或管束时,由于漩涡脱落,湍流抖振,流体弹性激振及声共鸣等诸多原因,会引起管子产生振动。
这种振动通常称之为流体诱导振动,它常常是导致换热器管子磨损、泄漏、断裂的主要原因。
因此在换热器设计时,人们都尽量采用各种措施来避免流体的诱导振动。
能否利用上述诱导振动来强化传热呢?
我国学者程林创新地提出并解决了这一问题。
它设计了一种弹性盘管,该盘管有两个自由端及两个固定端,通过弹性盘管的曲率半径、管径、管壁厚及端部附加质量等参数的组合来得到一种最有利的固定频率,同时,程林还设计了一种脉动流发生器,它将进入换热器的水流分成两股,其中一股通过一正置三角块后,在下游方向就会产生不同强度的脉动流,该脉动流直接作用在弹性盘管的附加质量端,从而诱发弹性盘管发生周期性的振动。
这种流体振动,换热面也振动的强化传热新方法,几乎不耗外功,却能极大地提高换热系数,根据这种原理设计的弹性盘管汽水加热器,在流速很低的情况下,可使传热系数达到4000~5000W/(m2·℃),是普通管壳式换热器的二倍。
现在这种换热器已在供热工程中得到了广泛的应用。
3.添加剂法
在流动液体中加入气体或固体颗粒,在气体中喷入液体或固体颗粒以强化传热是此法的特点。
有的研究者提出在上升的水流中注入氮气泡,由于气泡的扰动作用可使换热系数提高50%。
在油中加入呈悬浮状态的聚苯乙烯小球,可是换热系数提高40%。
在实际应用中,在气体中喷入液体或固体颗粒是一种有前途的强化换热的方法。
如在汽车散热器的冷却空气中喷入水或乙烯乙二醇后,由于液体在散热片中形成薄的液膜,液膜吸热蒸发以及蒸发时对边界层的扰动都可以增加传热。
我们研究了竖夹层空间的自然对流,此时如果在竖夹层空间加入极少量的水,由于水在竖夹层空间一侧沸腾蒸发,在另一侧凝结,从而使换热系数提高数倍。
气体中加入固体颗粒亦能强化换热。
Babcock公司在气体中加入石墨颗粒后发现换热系数可提高9倍。
现在沸腾床的迅速发展也与气固混合流能强化传热有密切关系。
4.抽压法
抽压法多用于高温叶片的冷却。
此时冷却介质通过抽吸或压出的方法从叶片或管道的多孔壁流出,由于冷却介质和受热壁面的良好接触能带走大量热量,并且冷却介质在壁上形成的薄膜可把金属表面和高温工质隔开,从而对金属起到了保护作用。
此法在燃汽轮机叶片的冷却中已得到了广泛的应用。
除了上述方法外还有使用换热面在静止流体中旋转的方法,利用静电场强化换热的方法,但它们的应用还十分有限。
在工程应用上,应尽可能地根据实际情况,同时采用多种强化传热的方法,以求获得更好的效果。
六沸腾换热的强化
沸腾是一种普遍的相变现象,在工业上有广泛的应用。
沸腾换热的特点是换热系数很高,在以往的应用中人们认为已不必进行强化了,而把主要的注意力集中在单相介质对流换热的强化上。
但随着工业的发展,特别是高热负荷的出现,相变传热(沸腾和凝结)的强化日益受到重视并在工业上得到越来越多的应用。
沸腾换热的强化主要从增多汽化核心和提高汽泡脱离频率两方面着手,具体方法有粗糙表面和对表面进行特殊处理,扩展表面,在沸腾液体中加添加剂等。
下面介绍常用的强化沸腾换热的方法。
1.使表面粗糙和对表面进行特殊处理
粗糙表面可使汽化核心数目大大增加,因此和光滑表面相比其沸腾换热强度可以提高许多倍。
最简单的粗糙表面的办法是用砂纸打磨表面或者采用喷砂的方法。
在使壁面粗糙度增加以强化沸腾换热时,应注意存在一极限的粗糙度,超过此之后,换热系数就不再随粗糙度的增加而增加。
此外增加粗糙度并不能提高沸腾的临界热负荷。
工程上为增强沸腾换热应用最多的还是对表面进行特殊处理。
特殊处理的目的是使表面形成许多理想的内凹穴,这些理想的内凹穴在低过热度时就会形成稳定的汽化核心;且内凹穴的颈口半径越大,形成气泡所需的过热度就越低。
因此这些特殊处理过的表面能在低过热度时形成大量的汽泡,从而大大地强化了泡状沸腾过程。
实验证明,表面多孔管的沸腾换热系数可提高2~10倍。
此外临界热负荷也相应得到提高。
在相同热负荷下特殊处理过的表面的传热温差也比普通表面低的多。
制造上述表面多孔管的方法很多,一种是在加热面上覆盖一层多孔覆盖层;另一种是对换热面进行机械加工以形成表面多孔管。
(1)带金属覆盖层的表面多孔管
上世纪六十年代末在美国首先出现用烧结法制成的带金属覆盖层的表面多孔管。
除了烧结法外还可采用火焰喷涂法、电镀法等。
一般讲烧结法的效果最好。
作为覆盖层的材料有铜、铝、钢、不锈钢等。
用烧结法制成的多孔管已在工业部门获得广泛的应用。
这种多孔管一般可使沸腾换热系数提高4~10倍,从而推迟膜态沸腾的发生。
(2)机械加工的表面多孔管
用机械加工方法可使换热表面形成整齐的T型凹沟槽。
这种机械加工的表面多孔管亦能大大强化沸腾换热过程和提高临界热负荷值。
对形状和尺寸不同的凹沟槽,沸腾换热系数可提高2~10倍。
用机械加工的方法还可克服烧结法带来的表面孔层不均的缺点,且多孔层也不易阻塞。
2.采用扩展表面
用肋管代替光管可以增加沸腾换热系数。
这一方面是肋管与