连接座注塑模模具设计说明书.docx
《连接座注塑模模具设计说明书.docx》由会员分享,可在线阅读,更多相关《连接座注塑模模具设计说明书.docx(17页珍藏版)》请在冰豆网上搜索。
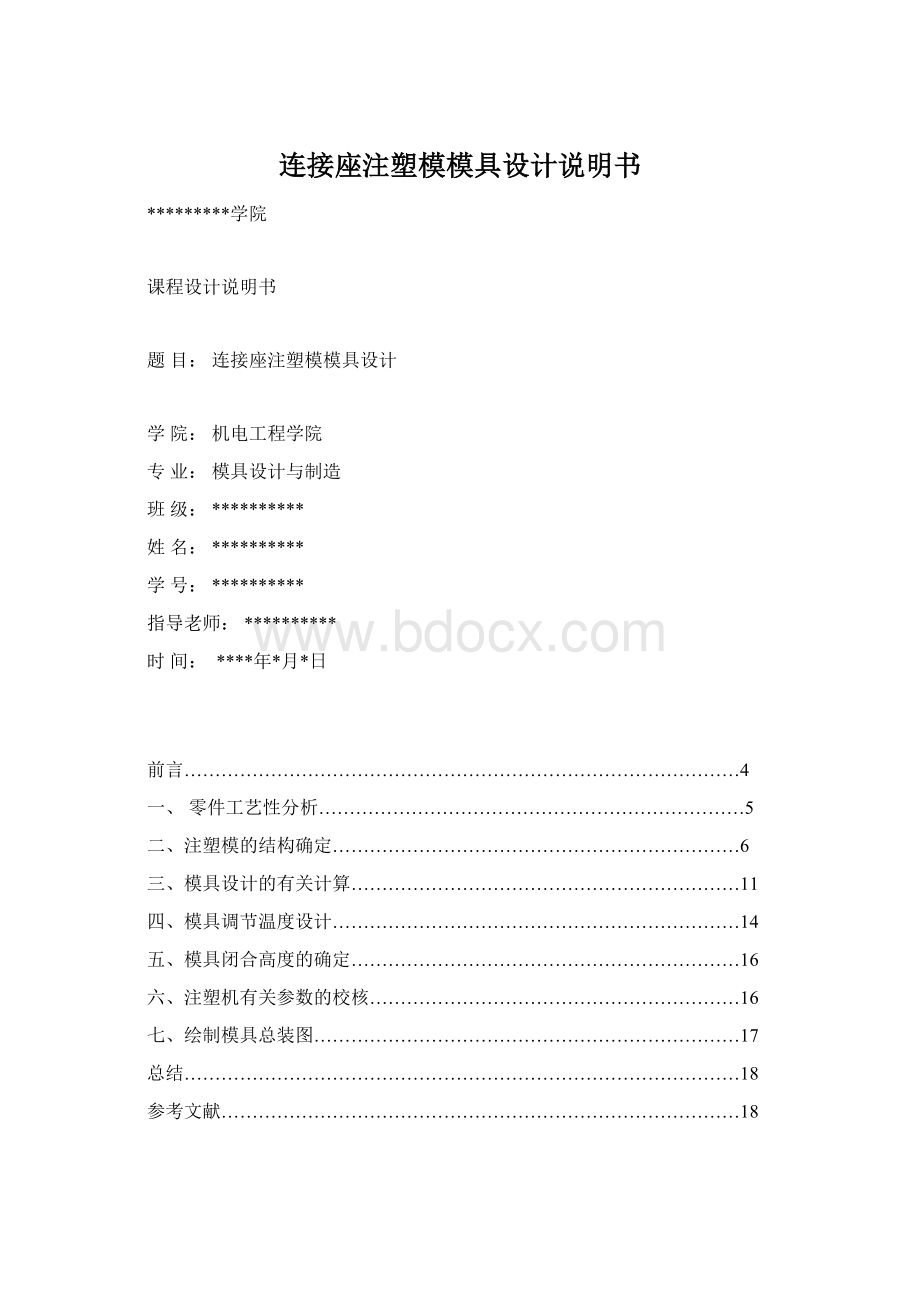
连接座注塑模模具设计说明书
*********学院
课程设计说明书
题目:
连接座注塑模模具设计
学院:
机电工程学院
专业:
模具设计与制造
班级:
**********
姓名:
**********
学号:
**********
指导老师:
**********
时间:
****年*月*日
前言………………………………………………………………………………4
一、零件工艺性分析……………………………………………………………5
二、注塑模的结构确定…………………………………………………………6
三、模具设计的有关计算………………………………………………………11
四、模具调节温度设计…………………………………………………………14
五、模具闭合高度的确定………………………………………………………16
六、注塑机有关参数的校核……………………………………………………16
七、绘制模具总装图……………………………………………………………17
总结………………………………………………………………………………18
参考文献…………………………………………………………………………18
引言
注塑模具课程设计比较全面的训练,其意义在于为以后的设计工作打基础,培养学生在设计过程中严肃认真、刻苦钻研、一丝不苟、精益求精的态度,使其在设计思想、方法和技能等各方面均获得锻炼和提高。
经过一学期对塑料模具整体结构和细节的学习和了解,为了更进一步的了解模具制造和加工,利用所学模具知识设计一套简单的注塑模具,来巩固所学模具知识。
通过完成模具课程设计,综合应用和巩固模具设计课程以及相关课程的理论基础和专业知识,系统地掌握产品零件的成型工艺分析、模具结构设计的基本方法和步骤、非标准模具零件的设计等模具设计基本方法。
同时,学会准确运用技术标准和资料,培养了认真负责、踏实细致的工作作风和严谨的工作态度,强化了质量意识和时间观念,从而形成了从业的基本职业素质。
第二部分:
模具设计实例
一、零件工艺性分析
工件为图1所示的落料冲孔件,材料为ABS,尺寸精度为4级,生产批量为大批量。
工艺性分析内容如下:
技术要求:
表面光亮无划伤痕迹
1:
塑件的原材料分析塑件的材料采用工程塑料ABS,属热塑性塑料,是由丙烯腈,丁二烯和苯乙烯组成的三不共聚物。
本身耐热性和溶性比HIPS佳,且具有光泽性。
由于丙烯腈的腈基极性较强,所以冲击强度,拉伸强度及塑料件的表面硬度均较HIPS佳。
综合物理-力学性能更是优良。
ABS树脂为浅黄色粒状或珠状树脂,熔融温度为217-237℃,热分解温度为250℃以上,无毒,无味,吸水率低,具有优良的综合物理-力学性能,优异的低温抗冲击性能,尺寸稳定性,电性能,耐磨性,抗化学药品性,染色性,成型加工和机械加工较好。
ABS树脂耐水,无机盐,碱和酸类,不溶于大部分酸类溶剂,而容易溶于醛酮,脂和某些氯化氢中。
ABS树脂热变形温度较低,不透明,可燃,耐侯性较差,其成型性能较好,流动性好,成形收缩率较小(通常为0.3-0.8%),比热容较低,在料筒中塑化效率高,在模具中凝固较快,成型周期短,但吸水性较大,成形前必须充分干燥,可在柱塞式或螺杆式卧式注射机上成形。
2:
塑件结构分析从零件图上分析,该零件总体形状为长方体,在宽度方向的一侧有一个凸台,零件壁厚均匀。
因此,设计时可采用单个分型面抽芯机构。
3:
尺寸精度分析制件尺寸选用尺寸精度4级(GB/T14486—1993),零件的尺寸精度中等,对应的模具相关零件的尺寸加工可以得到保证。
从塑件的壁厚来看,壁厚较均匀,有利于制件的成型。
4:
表面质量分析该零件的表面除要求没有缺陷、毛刺,内部不得有杂质外,没有特别的表面质量要求,故比较容易实现。
综上分析可以看出,注塑时在工艺参数控制得较好的情况下,零件的成型要求可以得到保证。
5:
计算塑件的体积和重量
计算塑件的体积:
=15285.6641mm3
计算塑件的重量:
根据设计手册可查得工程塑料ABS的密度为
=1.03g/㎝3,故塑件的重量为:
=15140.0094×1.03g=15594.21g采用一模一件的模具结构,考虑其外形尺寸、注塑时所需压力和工厂现有设备等情况,初步选用注塑机为XS-ZY-125型。
额定注射量:
125
;
螺杆(柱塞)直径:
42mm;
注射压力:
120MPa;
注射行程:
115mm;
注射方式:
螺杆式;
合模力:
900KN;
最大开模行程:
300mm;
模具最大厚度:
300mm;
模具最小厚度:
200mm;
6:
塑件注塑工艺参数的确定
查找附录H和参考工厂实际应用的情况,增强ABS的成型工艺参数可作如下选择。
试模时,可根据实际情况作适当调整。
注塑温度:
包括料筒温度和喷嘴温度。
料筒温度:
后段温度
选用160℃
中段温度t
选用170
前段温度
选用190℃;
注塑压力:
选用100MPa(相当于注塑机表压35kgf);
注塑时间:
选用25s;
保压:
选用72MPa(相当于注塑机表压25kgf);
保压时间:
选用4s;
冷却时间:
选用20s。
二、注塑模的结构设计:
1:
分型面选择
制品在模具中的位置,直接影响到模具结构的复杂程度,模具分型面的确定,浇口的设置,制品尺寸精度和质量等。
因此,开始制定模具方案时,首先必须正确考虑制品在其中的位置;然后再考虑具体的生产条件(包括模具制造的),生产的批量所需的机械化和自动化程度等其他设计问题。
选择分型面的原则是:
脱出塑件方便、模具结构简单、型腔排气顺利、确保塑件质量,无损塑件外观、设备利用合理。
所以,模具设计中,分型面的选择很关键,它决定了模具的结构。
应根据分型面选择原则和塑件的成型要求来选择分型面。
故选用下图所示的分型方式较为合理。
这样有利于成型后,塑件的脱模。
2:
确定型腔的排列方式
本塑件在注塑时采用一模一件,即模具需要一个型腔。
3:
浇注系统设计
1主流道设计:
直浇口式主浇道呈截锥体,主浇道入口直径d应大于注射机喷嘴直径1㎜左右。
主浇道入口的凹坑球面半径R应大于注射机喷嘴球头半径约2-3㎜。
锥孔壁粗糙度Ra≦0.8,主流道锥角为2°-4°过大的锥角会产生湍流或涡流,卷入空气。
根据设计手册查得XS-ZY-125型注塑机喷嘴的有关尺寸:
喷嘴前端孔径:
0=φ4mm;
喷嘴前端球面半径:
0=12mm;
根据模具主流道与喷嘴的关系
R=RO+(1~2)mm
d=d0+(0.5~1)mm
取主流道球面半径R=13mm;
取主流道的小端直径d=φ4.5mm。
经换算得主流道大端直径D=8.5mm;可在主流道出料端设计半径r=1.5mm的圆弧过渡。
2分流道设计:
分流道的形状及尺寸,应根据塑件的体积、壁厚、形状的复杂程度、注射速率、分流道长度因素来确定。
本塑件的形状不算太复杂,熔料填充型腔比较容易。
根据型腔的排列方式可知分流道的长度较短,为了方便加工起见,选用截面形状为半圆形的分流道,查表5-3取R=4mm
③:
浇口的设计
浇口是流道和型腔之间的连接部分,也是注塑模进料系统的最后部分,其基本作用是:
1》使从流道来的熔融塑料以最快的速度进入并充满型腔。
2》型腔充满后,浇口能迅速冷却封闭,防止型腔内还未冷却的热料回流。
浇口的设计与塑件形状,断面尺寸,模具结构,注塑工艺条件(压力)及塑料性能等因素有关。
浇口截面要小,长度要短,因为只有这样才能满足增料流速度,快速冷却封闭,便于与塑件分离,以及浇口残痕最小等要求。
根据上面的要求,我采用侧浇口形式。
在侧浇口进入或连接型腔的部位,应用圆角以防劈裂。
故侧浇口初选尺寸为1mm×0.8mm×1.2mm(b×L×h),试模时修正。
④:
导柱的选择
导柱的选择直形导柱和阶梯形导柱的前端都设计为锥形,便于导向。
两种导柱都可以在工作部分带有贮油槽。
带贮油槽的导柱可以贮存润滑油,延长润滑时间。
直形导柱用于塑件生产批量不大的模具,可以不用导套。
阶梯形导柱用于塑件大批量生产的模具,或导向精度要求高,必须采用导套的模具,装在模具另一侧的导套安装孔可以和导柱安装孔采用同一尺寸,一次加工而成,保证了严格的同轴,本模具采用有肩导柱I型
导柱直径尺寸随模具分型面处模板外形尺寸而定,模板尺寸愈大,导柱间的中心距应愈大,所选导柱直径也应愈大。
除了导柱长度按模具具体结构确定外,导柱其余尺寸随导柱直径而定。
本模具导柱选用I型,直径为25mm。
选用d=25mm,L=100mm,L1=32mm有肩导柱。
⑤:
导套的选择
导向孔可带导套,也可不带导套,带导套的导向孔用于生产批量大或导向精度高的模具。
无论带导套或不带导套的导向空,都不应该设计盲孔,盲孔会增加模具闭合时的阻力,并使模具不能紧密闭合。
带导套的模具应采用阶梯形导柱。
导套长度取决于含导套的模板厚度,其余尺寸随导套导向孔直径而定。
本模具选用d=25mm,L=40mm带肩导套。
⑥:
排气系统的设计
塑料熔体注入模腔的同时,必须置换出型腔内空气和从物料中逸出的挥发性气体,排气系统是注塑模设计的重要组成部分。
排气不良有很多危害:
增加熔体充模流动的阻力,使型腔不能充满,会使塑件棱边不清
在制品上呈现明显可见的流动痕和熔合缝,其力学性能降低
滞留气体使塑件产生银纹,气孔,剥层等表面缺陷
型腔内气体受到压缩后产生瞬间局部高温,使塑件熔体分解变色,甚至炭化烧焦
由于排气不良,降低了充模速度,增长了注塑成型周期.常用的排气系统设计方法:
分型面排气
拼接裂缝
利用烧结块
冷料井
排气槽.对于小型模具可利用分型面排气,本模具的分型面位于塑料溶体流动的末端,易于排气。
4:
推出机构设计
该零件采用推件板推出机构
①推杆位置、推杆形状尺寸及推杆数量等的确定
推杆位置、推杆形状尺寸如图所示:
由该模具结构确定推杆的数量为6。
②推杆安装固定及配合
推杆直径d与推件板上的推杆孔采用H8/f7间隙配合,推件板进行淬火处理,硬度HRC>50。
推杆的材料为T8,且工作端配合部分的表面粗糙度Ra<0.8
;
④推出机构导向设计
推杆导套的结构形式及尺寸如图所示:
5:
成型零件结构设计
①:
凹模的结构设计本模具采用一模两件的结构形式,凹模拟采用整体式结构,分流道和浇口均设在凹模上。
②:
凸模结构设计
三、模具设计的有关计算:
成型零件工作尺寸计算时采用平均尺寸、平均收缩率、平均制造公差和平均磨损量来进行计算。
查表得工程塑料(ABS)的收缩率为Q=0.3%--0.8%,故平均收缩率为Qcp=(0.3+0.8)%/2=0.55%,模具制造公差取△m=﹙1/4~1/5﹚△。
;
;
;
;
;
;
;
;
;
;
①:
型腔和型芯工作尺寸计算
按平均收缩率计算模具成型零件工作尺寸
型腔径向尺寸
型芯径向尺寸
型腔深度尺寸
型芯高度尺寸
中心距
②:
型芯尺寸的计算
=
;
=
=
=
③:
型腔尺寸计算
=
=
=
=
=
④:
凹模型腔侧壁计算
成型零件的工作尺寸,要保证所成型塑料制品的尺寸。
而影响塑料制品尺寸和公差的因素相当复杂,如模具的制造误差及模具的磨损;塑料成型收缩率的偏差及波动;溢料飞边厚度及其波动;模具在成型设备上的安装调整误差、成型方法及成型工艺的影响等。
成型零件的工作尺寸计算,要考虑塑料制品的尺寸公差,所成型塑料的收缩率、溢料飞边厚度、塑料制品脱模、模具制造的加工条件及可达到的水平等因素。
由于大尺寸模具主要存