引线片冲裁模具设计.docx
《引线片冲裁模具设计.docx》由会员分享,可在线阅读,更多相关《引线片冲裁模具设计.docx(15页珍藏版)》请在冰豆网上搜索。
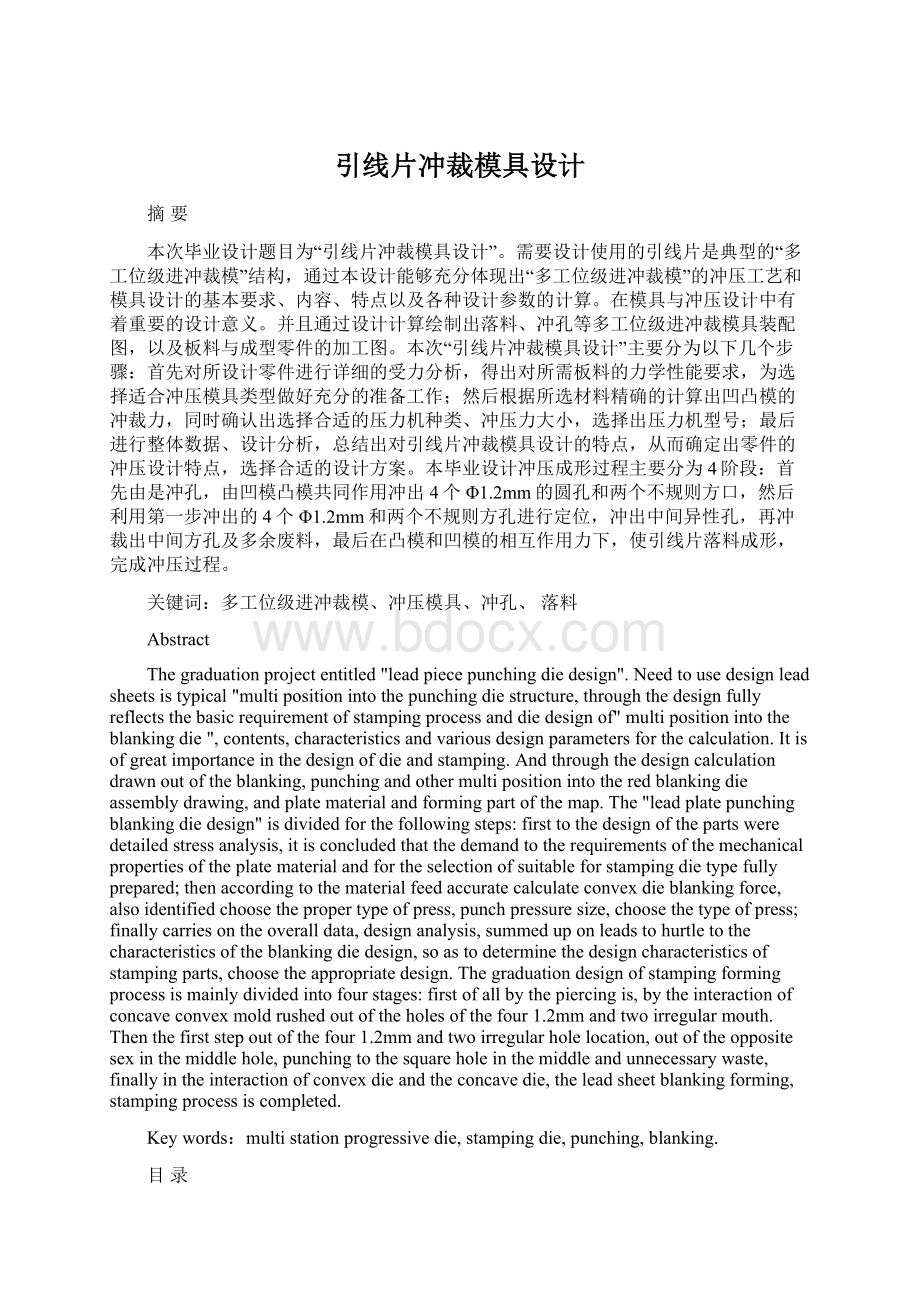
引线片冲裁模具设计
摘要
本次毕业设计题目为“引线片冲裁模具设计”。
需要设计使用的引线片是典型的“多工位级进冲裁模”结构,通过本设计能够充分体现出“多工位级进冲裁模”的冲压工艺和模具设计的基本要求、内容、特点以及各种设计参数的计算。
在模具与冲压设计中有着重要的设计意义。
并且通过设计计算绘制出落料、冲孔等多工位级进冲裁模具装配图,以及板料与成型零件的加工图。
本次“引线片冲裁模具设计”主要分为以下几个步骤:
首先对所设计零件进行详细的受力分析,得出对所需板料的力学性能要求,为选择适合冲压模具类型做好充分的准备工作;然后根据所选材料精确的计算出凹凸模的冲裁力,同时确认出选择合适的压力机种类、冲压力大小,选择出压力机型号;最后进行整体数据、设计分析,总结出对引线片冲裁模具设计的特点,从而确定出零件的冲压设计特点,选择合适的设计方案。
本毕业设计冲压成形过程主要分为4阶段:
首先由是冲孔,由凹模凸模共同作用冲出4个Φ1.2mm的圆孔和两个不规则方口,然后利用第一步冲出的4个Φ1.2mm和两个不规则方孔进行定位,冲出中间异性孔,再冲裁出中间方孔及多余废料,最后在凸模和凹模的相互作用力下,使引线片落料成形,完成冲压过程。
关键词:
多工位级进冲裁模、冲压模具、冲孔、落料
Abstract
Thegraduationprojectentitled"leadpiecepunchingdiedesign".Needtousedesignleadsheetsistypical"multipositionintothepunchingdiestructure,throughthedesignfullyreflectsthebasicrequirementofstampingprocessanddiedesignof"multipositionintotheblankingdie",contents,characteristicsandvariousdesignparametersforthecalculation.Itisofgreatimportanceinthedesignofdieandstamping.Andthroughthedesigncalculationdrawnoutoftheblanking,punchingandothermultipositionintotheredblankingdieassemblydrawing,andplatematerialandformingpartofthemap.The"leadplatepunchingblankingdiedesign"isdividedforthefollowingsteps:
firsttothedesignofthepartsweredetailedstressanalysis,itisconcludedthatthedemandtotherequirementsofthemechanicalpropertiesoftheplatematerialandfortheselectionofsuitableforstampingdietypefullyprepared;thenaccordingtothematerialfeedaccuratecalculateconvexdieblankingforce,alsoidentifiedchoosethepropertypeofpress,punchpressuresize,choosethetypeofpress;finallycarriesontheoveralldata,designanalysis,summeduponleadstohurtletothecharacteristicsoftheblankingdiedesign,soastodeterminethedesigncharacteristicsofstampingparts,choosetheappropriatedesign.Thegraduationdesignofstampingformingprocessismainlydividedintofourstages:
firstofallbythepiercingis,bytheinteractionofconcaveconvexmoldrushedoutoftheholesofthefour1.2mmandtwoirregularmouth.Thenthefirststepoutofthefour1.2mmandtwoirregularholelocation,outoftheoppositesexinthemiddlehole,punchingtothesquareholeinthemiddleandunnecessarywaste,finallyintheinteractionofconvexdieandtheconcavedie,theleadsheetblankingforming,stampingprocessiscompleted.
Keywords:
multistationprogressivedie,stampingdie,punching,blanking.
目录
摘要I
AbstractII
1绪论1
2工艺设计2
2.1设计介绍2
2.2设计结构分析2
2.3设计工艺分析2
2.4排样的设计分析3
2.5模具材料分析4
3冲压排样设计6
3.1毛胚的排样设计6
3.2毛胚刃口的分解设计7
3.3毛胚工序排样设计7
3.3.1毛胚工序的排样设计原则7
3.3.2毛胚工序具体排样7
4冲压工艺9
4.1冲压工艺方案的确定9
4.2冲裁力的计算10
4.3卸料力的计算11
5模具总体设计12
5.1选择模具12
5.2选择送料的具体方式13
5.3选择定位的具体方式13
5.4选择卸料和出件的具体的方式13
5.5选择导向的方式13
结论15
致谢16
参考文献17
1绪论
大学本科学习结束前,毕业设计是最后一个重要环节,毕业设计是对大学这几年所学知识的检验以及技能与理论的综合运用实践。
在我国高速发展的今天,模具冲压设计发挥着重要作用,是不可缺少的一个工业发展环节。
通过大学这几年的课程学习以及课程实习,我熟练的掌握了机械制图、金属工艺、工程力学、机械设计以及CAD、UG画图软件的学习等等课程,让我在机械方面的专业知识有着全面系统的了解,达到了学习的目的,为这次能够完成毕业设计打下了好的基础。
对于模具设计这个应用非常广、实践性强的设计课题,我将通过本次毕业设计对模具设计过程有一个新的认识,了解模具的结构工作过程以及零件材料的选取校验等等。
通过设计分析对冲压卸料力,模具冲压力,冲裁刃口尺寸计算,校核出各个板料、冲裁模具的力学性能,并进行详细而精准的计算。
根据凹模轮廓尺寸设计计算,挑选合适种类规格型号的模具,以及对其他设备尺寸的选择,满足冲压模具设计的结构要求以及对其他工件的尺寸设计要求。
通过这两个月的毕业设计我查阅大量相关书籍,与老师同学一起查阅相关手册,互相讨论解决了一个又一个疑问,制定出合理的模具冲压方案,经过本次毕业设计大大加深对“冲压工艺与模具设计”基础知识的掌握、理解及实践应用,通过本毕业设计也能够大大提高冲裁模具的设计思路和实践能力。
同时又能够为将来设计更加复杂的冲裁模具做好充分的准备。
本次毕业设计采用了冲孔、落料工艺以及模具设计基础知识顺利完成本次毕业设计。
2工艺设计
2.1设计介绍
本毕业设计为“引线片冲裁模设计”,该产品材料为无氧铜带,厚度0.15mm,要求小规模批量生产。
该零件属于典型的多工位级冲裁模。
如图2-1所示:
图2-1引线片
2.2设计结构分析
引线片结构:
属于典型的“多工位级进冲裁模”,由9个直径为Φ1.2mm的小孔分布在Φ10mm直径周边,有两个窄长的悬臂长宽分别为10mm、3mm,两个带有45̊直角过渡长宽分别为10mm、8mm悬臂,外轮廓宽为2mm,厚度为0.15mm整体结构对称分布。
由于Φ1.2mm的小孔间距太小,悬臂过长过窄,需要保证冲压模具的强度要求,所以不能采用“复合模”进行冲压;如果采用“单工序模”进行冲压不仅悬臂会过长过窄,导致强度达不到要求,而且还会由于多次定位导致产品精度过低;多工位级进冲裁模工位数量的设置,具有一定的灵活性,恰好能够将9个小孔分布在不同的工位上,分别将周边废料分次冲出,充分保证了冲压模具的强度,也保证了工件的质量与精度。
2.3设计工艺分析
通常来讲,制件成品的结构,形状、精度、形位等因素在很大程度上取决于冲裁件工艺性。
而冲裁件的工艺性直接决定冲裁件的寿命、质量、材料利用率以及冲裁成功率等,所以材料的选择及形状的确定,是非常重要的,甚至是设计成败的关键之处。
冲裁件形状要尽量简单并且要求形状基本对称、要注意避开复杂的曲线。
秉承着科学绿色的原则,减少冲裁设计,减少设计剩余的材料。
同时冲裁件的各个连接处都要避开尖锐的角取而代之的是圆角。
圆角有利于延长模具的寿命和质量。
冲裁凹凸部分通常都要求避免过窄,同时也都要避免悬臂和窄槽超长。
冲裁件的孔径因为直接地受孔凸模的材料性能的限制,要求其不能过小,防止强度、硬度不够,免压弯甚至是折断。
由于小孔孔距太小,并且有两个比较窄的悬臂,为了保证工件的精度,同时保证冲压模具的强度,硬度等力学性能,选择多工位级进冲模,它具有较高的灵活性,能将小孔分布在不同工序上冲压,不但保证了零件的精度,而且也保证了模具的力学性能。
从零件的生产成本和零件的力学性能,零件的使用要求综合考虑,选择的冲压材料为无氧铜带。
2.4排样的设计分析
排样的设计合理性,能够提高材料的使用率,影响经济效益,甚至在模具结构、制件质量、操作的安全性和操作的方便等因素也有着重要的决定性作用。
综上,排样也是本次设计中的一项重要且必要的工作。
毛坯材料的经费是在经济成本中占有极其重大的比重的,甚至是在占到60%以上,排样可以更加合理的使用材料,提高材料的利用率,减少对材料的浪费。
同时排样还可以合理的安排工序,提高工作效率。
在生产中废料的产生途径有二,一是结构废料,这种废料主要是以为存在着工件内孔而不可避免地产生的废料。
二是工艺废料,这种废料的产生原因可以追溯到工件与工件之间或则是工件与条料的连接边缘之间的搭边。
这种废料的存在就是由冲压方式和排样方式共同决定的。
所以,要减少工艺废料,就要依靠于排样。
按照冲压材料的利用率高低可分为:
有废料排样,少废料排样和无废料排样。
有废料排样是利用率最低的一种。
材料的利用率约85%~95%它仅仅是沿着工件的外形进行冲裁工作,工件与工件和条料侧边之间都有大量搭边存在着这些工业废料的存在使得利用率不高。
由于这种方法制成的制件质量较高并且冲模寿命也更加长,这种排样适用于形状复杂、尺寸要求精确的情况下。
少废料排样利用率相对来讲是会比较高一些的,当选择为少废料排样时材料的利用率可以达到70%~90%。
他将工件的一部分外形轮廓进行处理,将之切断或者是进行冲裁,因而减少了这一部分的废料生成,只是在工件之间或工件与条料侧边任然存在着少量的搭边。
这一部分是就是主要的废料生成。
无废料排样是利用率最高的一种排样方法,但无废料排样不管是在工件与工件之间还是工件与材料边之间都存在着搭边问题。
但是少废料排样、无废料排样也是有其本身的缺陷,虽然减少废料可以提高材料的利用率,但是在应用时会产生对材料的限制更大一点。
排样会受到工件的自身形状的限制,并且材料本身就存在不可避免的尺寸公差,甚至会材料导向与定位也同时会产生不可避免的误差,使得工件的尺寸也相应的受到一定的影响,从而影响到精度。
毛刺的产生主要分布在零件的交界处。
并且它的单边剪切方法,会使得模具的本身发生磨损,这样就更容易使冲模的寿命受到负面的影响,甚至连工件的断面的质量会从很大程度上受到巨大的影响。
故而少废料排样和无废料排样一般是应用于精度的要求不太高的状况之下的。
以下因素是影响搭边值的重要原因:
首先是材料本身,它的力学性能和厚度强度和硬度都起到了重要的影响作用。
材料的塑性越好,材料厚度越大,材料的强度、硬度越高那么材料的搭边值就越大,反之越小。
其次是工件自身的形状和它具有的尺寸。
外形更复杂搭边值越大更简单则搭边值越小,它的圆角半径和搭边值也呈现出负相关。
排样的形式也对搭边值有着极其重大的影响。
并且送、搭料的方法方式也对搭边值影响巨大。
2.5模具材料分析
模具所应用的材料在很大的程度上决定了模具使用的寿命,同在也在制件质量上起到了重要的决定性作用。
本次设计秉承着经济、实用、适用的原则对材料进行选择。
除了钢的强度大小,硬度大小和韧性都是重要参考因素之外。
同时,塑料模具钢的工性能和镜面度也很重要。
本次设计选用的是Cr12钢。
经由查询文件《机械工程材料P126表8-11》得知,它的C含量约为0.9%~1.05%,Mn的含量大约为0.8%~1.1%,Si含量大约是0.15%~0.35%左右,同时它的Cr含量可以达到0.9%~1.2%,其淬火的温度约为820~840℃,HRC不低于62,回火温度140~160℃,HRC60~64并且它也具有相当高的淬透性、高的硬度和十分耐磨的的特征。
同时也因为它是由钨而形成碳化物,它会在淬火和低温回火后具有相对来讲更高的硬度以及耐磨性。
除此之外,钨也对保存晶粒具有重要的作用,从而会使得钢得到更加好的韧性。
由于本次设计使用该模具的目的是冲裁复杂形状的工件,故使用材料Cr12,热处理HRC58~60。
落料凸模尺寸及工艺如图2-5所示:
图2-5落料凸模
3冲压排样设计
在设计多工位级进冲裁模时,需要考虑注意的问题有很多,不过我们第一要考虑的是冲裁模的用料排样。
多工位级进冲裁模的排样需要体现出冲压顺序过程与冲裁工艺要求,明确指出运料、冲料、取模的详细过程。
排样还与选择结构、冲裁的利用率、冲裁的效率、成本都有着密切的联系。
排样的设计原则在于:
首先冲切刃口、再进行冲压弯曲、最后落料取模。
需要注意冲裁模具的刚度、硬度、强度等等力学参数。
3.1毛胚的排样设计
毛胚排样如图3-1所示:
图3-1毛胚排样图
材料的利用率计算为:
(3-1)
式中A——表示冲裁面积(包括冲裁小孔在内,单位:
mm2);
n——表示在一张板上一个步距内的冲件的总数目(n取1);
B——表示板料的宽度(单位:
mm);
H——表示板料进距长度(单位用mm);
其结果以下:
A=3.14¡Á86/2¡Á86/2=5800mm2
3.2毛胚刃口的分解设计
毛胚刃口的分解设计需注意冲裁模具的结构简单,分离过程需要简洁,模具的凸模与凹模结构要可靠、简洁,同时需满足冲压的强度、硬度等要求;毛胚刃口的分解还要保证冲压零件的精度要求,需要保证尺寸、误差、形状、光滑度都要求;冲裁刃口分段要尽可能减少,防止由于分段过多导致工件变形、撕裂;毛胚刃口的外轮廓有毛刺时需要做不同的分解进行冲压;过于复杂的零件或者有细窄长槽时需分解进行冲压;同时要注意加工的成本,要在保证质量的条件下降低成本。
3.3毛胚工序排样设计
再设计多工位级冲裁模时,由于各个工序加工的过程不同,工件在冲压时会随着冲床的每一个步距向前移动,实现不同的工序过程。
因此在毛胚板料排样时要进行工序的排样。
3.3.1毛胚工序的排样设计原则
(1)毛胚工序的排样需要保障设计零件的强度、硬度、精度、以及材料的利用率。
(2)毛胚工序的排样设计时应考虑模具的寿命、模具的结构简洁、模具的装拆方便。
(3)设计毛胚工序的排样应先冲孔再冲切、落料。
(4)当需要很大的冲裁力时可以考虑设计多加一个空位,来弥补模具的强度,提高模具的寿命。
(5)毛胚工序的排样设计时应预留出搭边值,防止产生毛刺影响工件的精度。
(6)毛胚工序的排样设计时还应考虑模具的加工条件及成本。
3.3.2毛胚工序具体排样
根据零件的尺寸、工艺、材料及结构等特点分析,采用冲压工序方案为“多工位级进冲裁”。
工序排样如图3-2所示:
图3-2工序排样图
为了保证条料的定位精度、工件与条料冲压是的间距问题,具体工序方案为:
侧刃冲侧边—冲圆孔、中间异型孔—再冲另一侧冲圆孔、中间异型孔—冲圆孔、切中间余料—落料。
多工位级进冲裁的突出特点是能够将工件进行分部冲压,把工序进行分解,利用冲裁废料的办法来避免冲裁过窄过小的悬臂和凹槽带来的误差:
也可以通过分解工序的方法来实现孔与孔之间距离过小或群孔冲压问题。
尽管多工位级进模的结够复杂,但是组成模具的零件仍然是工作零件,定位零件、卸料零件、压料零件以及送料零件,导向零件和固定零件分为5个部分,因此可以根据排样图的工位数找到每个零件的凹凸模。
4冲压工艺
冲压模具工艺主要包括工艺方案的确定与冲压工艺计算。
受力分析主要包含冲裁力的计算、冲孔力的计算、翻边力的计算、卸料力的计算等等,通过计算分析来校核压力机、模具设计强度,选择合适的压力机以及冲压模具。
4.1冲压工艺方案的确定
冲压成形主要包含冲孔、落料、拉深、翻边4种基础工序,根据工序的排列顺序可以设计出三种方案:
1、落料——冲孔——拉深——翻边,单工序成型。
2、落料——冲孔——翻边——拉深,级进模成型。
3、落料——冲孔——翻边——拉深,复合模成型。
第一种方案虽然结构相对来讲比较简单,可是程序相对更加复杂完成两副模具需两道工序。
不但效率低,而且精度也变得更加难以掌控。
这种方案不仅是违背了经济原则,并且也很难推广难以适应大规模的生产。
第二种方案一般称为级进模模具生产。
级进模模具依靠压力机,可以一次完成多个工序的冲压加工。
他的优点是安全,快捷。
并且模具的强度和寿命都较前者有了很大的提升。
但是它依然存在着巨大的缺陷:
比如生产周期长,降低了生产的效率,模具成本相对更高而且结构也变得更加复杂,不符合经济的要求等。
更重要的是料的定位与送进尚且未能完全掌控。
第三种方案是本次设计的最终方案,较之前者它有着明显的优势。
第三种方案被称为复合模模具生产。
复合模具生产步骤为:
落料——冲孔——翻边——拉深成型。
模具成型只需要一个模板,生产效率高并且产品精美工整,质量也好。
压力机只需要工作一次,落料、冲孔、拉深、翻边等工序均可一次性完成。
不仅是安全方便并且快捷适应生产需求。
复合模具主要特征是:
首先对冲件而言,表面工整无毛边,外形对称一致;并且精度也是比较高的。
其次是适应范围广阔,适用于各种厚度和特质的材料,对材料的软硬要求也不苛刻。
并且提高去了材料的利用率,使得无论是边角余料还是短料都得到了再利用。
还有他的板料的定位精度要求是绝对比级进模还要更低一些的。
同时复合模冲膜面积也是比较小的。
当然复合模也是完美无缺的方案。
即使是这样他也依旧是存在着一些问题的。
首先是复合模具结较为复杂其次凸凹模内、外形间壁厚,内形与外形间壁厚,应当适中,过薄是会减小强度。
出件问题也没有的到完美的解决。
采用筒形料加工和板料加工也可以用来替代复合模模具生产。
他们分别的问题是弓箭厚度问题与结构问题。
综上所诉,方案三更加适合此次设计的要求。
4.2冲裁力的计算
冲裁力是指冲裁过程中凸模与凹模之间发生相对运动,对材料的挤压作用,使得工件与板料之间成功相互分离,它随着凸模的运动变化而改变。
它的力的大小值取决于选用的材料的力学性能、材料本身的厚薄程度及冲裁件的形状长短等因素。
冲裁力的大小是选择冲压机的重要参数。
合理且精确地计算冲裁力有利于更加合理地选择冲压使用的设备和模具。
冲压压力机的标准冲压力不能小于设计分析计算得出的理论冲裁力,模具的受力设计要求,必须满足传递并承受的标准冲裁力要大于计算校核出的最大冲裁力。
冲裁力F的大小取决与材料的力学性能、选择材料的厚度、冲压时分离的轮廓和冲裁件的周边长度。
普通平刃冲裁模具的冲裁力计算为:
(4-2)
式中L——表示冲裁件周边长度(单位:
mm);
T——表示材料厚度(单位:
mm);
τ——表示材料抗剪强度(单位:
MPa);
K——表示系数。
(由于充分地考虑到了模具本身其对刃口有不可避免的磨损,模具间隙也不可避免,会产生不可避免的波动,除上面因素以外,冲压材料的力学性能也会随着外界条件因素,导致一些实验数据产生偏差,此处取一般系数K=1.3。
)
通过对零件的分析计算得出各冲裁工序的冲裁周长为:
工序1侧刃冲侧边:
L=65.6mm
工序2冲圆孔、中间异型孔:
L=14.1mm
工序3冲另一侧冲圆孔、中间异型孔:
L=18mm
工序4冲圆孔、切中间余料:
L=173.7mm
工序5冲孔:
L=116mm
各冲裁力为:
F1=6.4KN;F2=1.6KN;F3=1.65KN;F4=17KN;F5=15.3KN;
F冲总=F1+F2+F3+F4+F5=41KN;
如果在设计中出现所需最大冲裁力超过压力机的最大冲裁力,那么就需要考虑通过其他方法降低冲裁力,降低冲裁力的方法主要有:
阶梯凸模冲裁、斜刃口冲裁和加热材料等方法。
4.3卸料力的计算
F卸=K卸F
查表得:
K卸=0.04
F=F冲总=41KN
所以F卸=K卸F=0.041*41=2.4KN
5模具总体设计
5.1选择模具
由前文通过对冲压工艺的计算分析可以得出本次设计采用的是多工位级进冲裁模具方案进行冲压。
如图5-1所示。
图5-1模具结构图
5.2选择送料的具体方式
在本次设计中采用的是自前而后的纵向的送料的方式,并且是自右而左的横向送料的方式。
选择的标准是凹模周界的尺寸大小。
若L<B(字母L和B分别表示的是送料的方向凹模的本身的长度的大小值和垂直于送料的方向凹模的宽度的大小值)时,选用纵向的送料;若L>B,选择横向送料;若L=B,无论是纵由于充分地考虑到了模具本身其对刃口也有一定的磨损量,冲压模具的间隙也是不会避免的,产生的波动是无法消除的,除了这些以外冲压材料的力学性能也会跟随外界因素,发生一些必然的变化及部分实验数据的偏差因素,此处取一般系数K=1.3。
向还是横向都是可以的。
就本次设计中采用的复合模具来讲,就算是L=B它的送料的方式也是应该采用横向送料的这种方式的。
5.3选择定位的具体方式
本次设计使用的是条料,依靠挡料销与导料柱共同工作协调来控制条料的进入。
但是由于首件工件冲压的位置依靠条料自身长度大笑有一些余剩,这样的情况依据实验员的大约目测量而确定出来。
5.4选择卸料和出件的具体的方式
本次设计在实验过程中主要使用的是弹压卸料板,并且还同时使用了固定卸料板,这种选择主要是由卸料力强度决定的,同时材料厚度也是我们需要主要考虑的一些具体的因素。
显然弹压卸料在具体操作中比较起来固定卸料模具会更加的快捷和方便。
工作过程可以被清楚地看见,而且使用弹压卸料板使用的是更加柔和的力量,对工件的损伤显然更小。
故,弹压卸料板无疑是是实验的首选,只有在弹压卸料板的卸料力过小,不能满足工作需求时,才