电镀电铸电泳溅镀阳极处理的区别.docx
《电镀电铸电泳溅镀阳极处理的区别.docx》由会员分享,可在线阅读,更多相关《电镀电铸电泳溅镀阳极处理的区别.docx(13页珍藏版)》请在冰豆网上搜索。
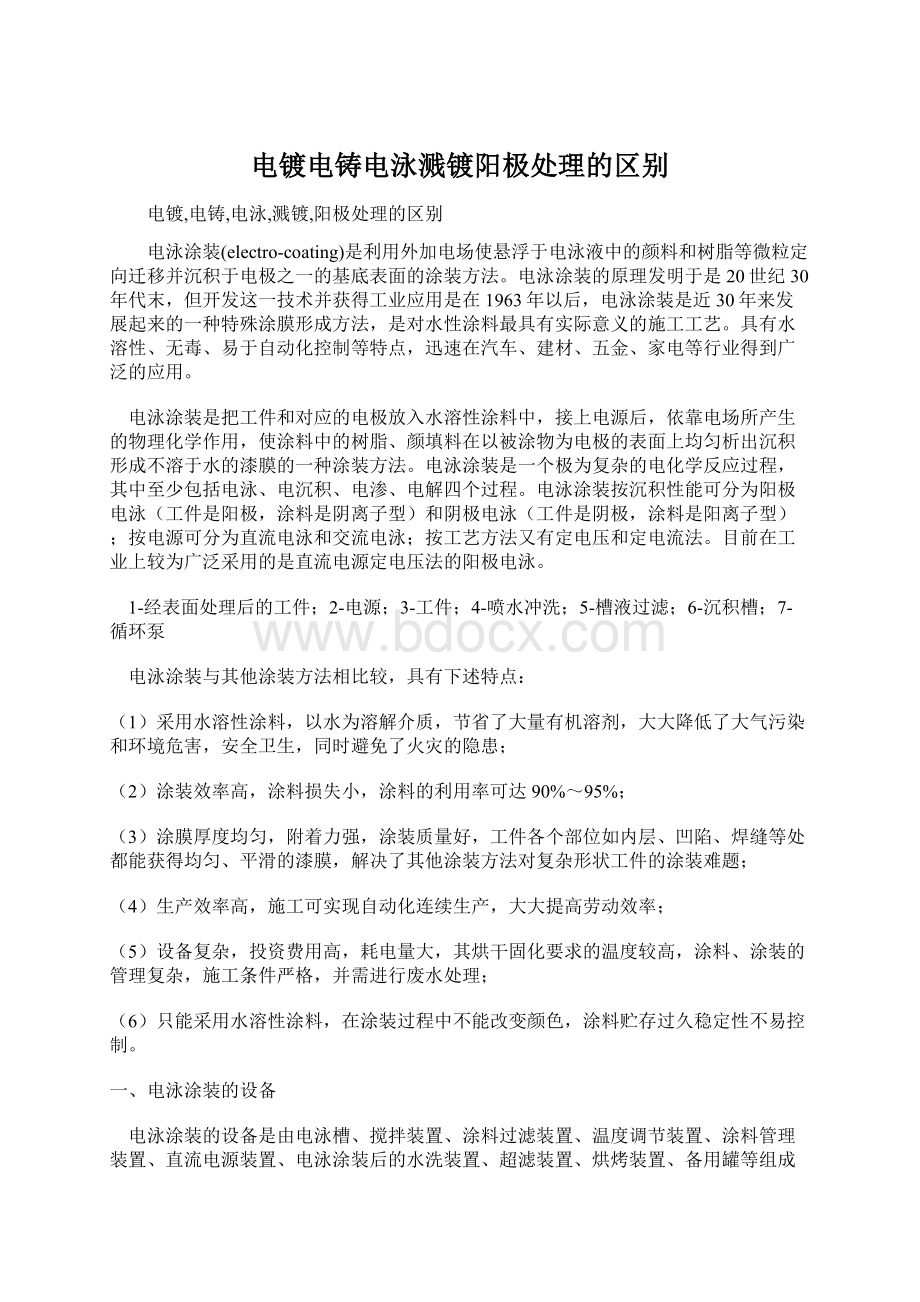
电镀电铸电泳溅镀阳极处理的区别
电镀,电铸,电泳,溅镀,阳极处理的区别
电泳涂装(electro-coating)是利用外加电场使悬浮于电泳液中的颜料和树脂等微粒定向迁移并沉积于电极之一的基底表面的涂装方法。
电泳涂装的原理发明于是20世纪30年代末,但开发这一技术并获得工业应用是在1963年以后,电泳涂装是近30年来发展起来的一种特殊涂膜形成方法,是对水性涂料最具有实际意义的施工工艺。
具有水溶性、无毒、易于自动化控制等特点,迅速在汽车、建材、五金、家电等行业得到广泛的应用。
电泳涂装是把工件和对应的电极放入水溶性涂料中,接上电源后,依靠电场所产生的物理化学作用,使涂料中的树脂、颜填料在以被涂物为电极的表面上均匀析出沉积形成不溶于水的漆膜的一种涂装方法。
电泳涂装是一个极为复杂的电化学反应过程,其中至少包括电泳、电沉积、电渗、电解四个过程。
电泳涂装按沉积性能可分为阳极电泳(工件是阳极,涂料是阴离子型)和阴极电泳(工件是阴极,涂料是阳离子型);按电源可分为直流电泳和交流电泳;按工艺方法又有定电压和定电流法。
目前在工业上较为广泛采用的是直流电源定电压法的阳极电泳。
1-经表面处理后的工件;2-电源;3-工件;4-喷水冲洗;5-槽液过滤;6-沉积槽;7-循环泵
电泳涂装与其他涂装方法相比较,具有下述特点:
(1)采用水溶性涂料,以水为溶解介质,节省了大量有机溶剂,大大降低了大气污染和环境危害,安全卫生,同时避免了火灾的隐患;
(2)涂装效率高,涂料损失小,涂料的利用率可达90%~95%;
(3)涂膜厚度均匀,附着力强,涂装质量好,工件各个部位如内层、凹陷、焊缝等处都能获得均匀、平滑的漆膜,解决了其他涂装方法对复杂形状工件的涂装难题;
(4)生产效率高,施工可实现自动化连续生产,大大提高劳动效率;
(5)设备复杂,投资费用高,耗电量大,其烘干固化要求的温度较高,涂料、涂装的管理复杂,施工条件严格,并需进行废水处理;
(6)只能采用水溶性涂料,在涂装过程中不能改变颜色,涂料贮存过久稳定性不易控制。
一、电泳涂装的设备
电泳涂装的设备是由电泳槽、搅拌装置、涂料过滤装置、温度调节装置、涂料管理装置、直流电源装置、电泳涂装后的水洗装置、超滤装置、烘烤装置、备用罐等组成。
电泳槽槽体的大小及形状需根据工件大小、形状和施工工艺确定。
在保证一定的极间距离条件下,应尽可能设计小些。
槽内装有过滤装置及温度调节装置,以保证漆液一定的温度和除去循环漆液中的杂质和气泡。
搅拌装置可使工作漆液保持均匀一致,多采用循环泵,漆液的循环一般每小时4~6次,当循环泵开动时,槽内漆液液面应均匀翻动。
涂料管理装置的作用在于补充调整涂料成分,控制槽液的PH值,用隔膜电极除去中和剂和用超滤装置排除低分子量成分等。
电泳电源的选择,一般采用直流电源。
整流设备可采用硅整流器或可控硅。
电流的大小与涂料的性质、温度、工作面积、通电方式等有关,一般为30~50A/m2。
水洗装置用于电泳涂装前后工件的冲洗,一般用去离子水,但需加压设备,常用的是一种带螺旋体的淋洗喷嘴。
烘烤装置用来促进电泳涂料的干燥成膜,可采用电阻炉、感应电热炉和红外线烘烤设备。
烘房设计要有预热、加热和后热三段,应根据涂料的品种和工件的情况制订。
二、影响电泳涂装的主要工艺参数
1、电压
电泳涂装采用的是定电压法,设备相对简单,易于控制。
电压对漆膜的影响很大;电压越高,电泳漆膜越厚,对于难以涂装的部位可相应提高涂装能力,缩短施工时间。
但电压过高,会引起漆膜表面粗糙,烘干后易产生“橘皮”现象。
电压过低,电解反应慢,漆膜薄而均匀,泳透力差。
电压的选择由涂料种类和施工要求等确定。
一般情况下,电压与涂料的固体分及漆温成反比,与两极间距成正比。
钢铁表面为40~70V,铝和铝合金表面可采用60~100V,镀锌件采用70~85V。
2、电泳时间
漆膜厚度随着电泳时间的延长而增加,但当漆膜达到一定厚度时,继续延长时间,也不能增加厚度,反而会加剧副反应;反之,电泳时间过短,涂层过薄。
电泳时间应根据所用的电压,在保证涂层质量的条件下,越短越好。
一般工件电泳时间为1至3分钟,大型工件为3至4分钟。
如果被涂物件表面几何形状复杂,可适当提高电压和延长时间。
3、涂料温度
涂料温度高,成膜速率快,但漆膜外观粗糙,还会引起涂料变质;温度低,电沉积量少,成膜慢,涂膜薄而致密。
施工过程中,由于电沉积时部分电能转化成热能,循环系统内机械摩擦产生热量,将导致涂料温度上升。
一般漆液温度控制在某些方面15~30℃。
4、涂料的固体分和颜基比
市售的电泳涂料的固体分一般为50%左右,施工时,需用蒸馏水将涂料固体分控制在10%~15%。
固体含量太低,漆膜的遮盖力不好,颜料易沉淀,涂料的稳定性差。
固体分过高,粘度提高,会造成漆膜粗糙疏松,附着力差。
一般颜基比为1比2左右,高光泽电泳涂料的颜基比可控制在1比4。
由于实际操作中,涂料的颜料量会逐渐下降,必须随时添加颜料分高的涂料来调节。
5、涂料的PH值
电泳涂料的PH值直接影响槽液的稳定性。
PH值过高,新沉积的涂膜会再溶解,漆膜变薄,电泳后冲洗会脱膜。
PH值过低,工件表面光泽不一致,漆液的稳定性不好,已溶解的树脂会析出,漆膜表面粗糙,附着力降低。
一般要求施工过程中,PH值控制在7.5~8.5之间。
在施工工程中,由于连续进行电泳,阳离子的铵化合物在涂料中积蓄,导致PH值的上升。
可采用补加低PH值的原液,更换阴极罩蒸馏水,用离子交换树脂除去铵离子,采用阳极罩等方法降低PH值。
若PH值过低时,可加入乙醇铵来调节。
6、涂料电阻
被涂物件从前一道工序带入电泳槽的杂质离子等引起涂料电阻值的下降,从而导致漆膜出现粗糙不均和针孔等弊病。
在涂装施工中,需对涂料进行净化处理。
为了得到高质量涂膜,可采用阴极罩设备,以除去铵及钙、镁等杂质正离子。
7、工件与阴极间距离
距离近,沉积效率高。
但距离过近,会使漆膜太厚而产生流挂、橘皮等弊病。
一般距离不低于20cm。
对大型而形状复杂的工件,当出现外部已沉积很厚涂膜,而内部涂膜仍较薄时,应在距离阴极较远的部位,增加辅助阴极。
三、电泳涂装的方法及技巧
(1)一般金属表面的电泳涂装,其工艺流程为:
预清理→上线→除油→水洗→除锈→水洗→中和→水洗→磷化→水洗→钝化→电泳涂装→槽上清洗→超滤水洗→烘干→下线。
(2)被涂物的底材及前处理对电泳涂膜有极大影响。
铸件一般采用喷砂或喷丸进行除锈,用棉纱清除工件表面的浮尘,用80#~120#砂纸清除表面残留的钢丸等杂物。
钢铁表面采用除油和除锈处理,对表面要求过高时,进行磷化和钝化表面处理。
黑色金属工件在阳极电泳前必须进行磷化处理,否则漆膜的耐腐蚀性能较差。
磷化处理时,一般选用锌盐磷化膜,厚度约1~2μm,要求磷化膜结晶细而均匀。
(3)在过滤系统中,一般采用一级过滤,过滤器为网袋式结构,孔径为25~75μm。
电泳涂料通过立式泵输送到过滤器进行过滤。
从综合更换周期和漆膜质量等因素考虑,孔径50μm的过滤袋最佳,它不但能满足漆膜的质量要求,而且解决了过滤袋的堵塞问题。
(4)电泳涂装的循环系统循环量的大小,直接影响着槽液的稳定性和漆膜的质量。
加大循环量,槽液的沉淀和气泡减少;但槽液老化加快,能源消耗增加,槽液的稳定性变差。
将槽液的循环次数控制6~8次/h较为理想,不但保证漆膜质量,而且确保槽液的稳定运行。
5)随着生产时间的延长,阳极隔膜的阻抗会增加,有效的工作电压下降。
因此,生产中应根据电压的损失情况,逐步调高电源的工作电压,以补偿阳极隔膜的电压降。
(6)超滤系统控制工件带入的杂质离子的浓度,保证涂装质量。
在此系统的运行中应注意,系统一经运行后应连续运行,严禁间断运行,以防超滤膜干枯。
干枯后的树脂和颜料附着在超滤膜上,无法彻底清洗,将严重影响超滤膜的透水率和使用寿命。
超滤膜的出水率随运行时间而呈下降趋势,连续工作30~40天应清洗一次,以保证超滤浸洗和冲洗所需的超滤水。
(7)电泳涂装法适用于大量流水线的生产工艺。
电泳槽液的更新周期应在3个月以内。
以一个年产30万份钢圈的电泳生产线为例,对槽液的科学管理极为重要,对槽液的各种参数定期进行检测,并根据检测结果对槽液进行调整和更换。
一般按如下频率测量槽液的参数:
电泳液、超滤液及超滤清洗液、阴(阳)极液、循环洗液、去离子清洗液的PH值、固体含量和电导率 每天一次;颜基比、有机溶剂含量、试验室小槽试验 每周2次。
(8)对漆膜质量的管理,应经常检查涂膜的均一性和膜厚,外观不应有针孔、流挂、橘皮、皱纹等现象,定期检查涂膜的附着力、耐腐蚀性能等物理化学指标。
检验周期按生产厂家的检验标准,一般每个批次都需检测。
电铸大致可分为三类,即装饰性电镀(以镀镍-铬、金、银为代表)、防护性电铸(以镀锌为代表)和功能电镀(以镀硬铬为代表
电铸是利用电镀法来制造产品的功能电镀之一。
据称电铸始于1838年。
当时,苏联的Jacoli在石膏母型上涂敷石腊,通过石墨使其表面具有导电性,然后表面镀铜,镀后脱模,以此制成铜的复制品。
日本昭和初年,京都市工业研究所和大板造币司等单位就已积极开展了在石膏母型上铸铜,在绝缘体上电镀等方面的研究,并制作了许多精美的金属工艺品。
但是,以石膏或腊等作为母型模进行电铸时,不仅制造技艺要求高、操作麻烦,而且母型易破损,难以制出精致的复制品,所以电铸的应用范围十分有限。
后来,由于塑料母型材料的问世以及电镀水平的提高,电铸技术也得到很大发展,并广泛应用于制造那些采用其它方法不能制造的或加工有困难的急需产品。
特别是最近几年,由于电铸用于制造宇航或原子能的某些零件,它已作为一种尖端加工技术而为人们所瞩目。
(此外通过电镀使金属与金属相结合的所谓“电结合技术”也进行了研究。
这种电结合的金属不会因热而改变金属材质的机械性能和物理性。
)
二、电铸特征与电铸制品
电铸法的优点:
1、 能进行超精密加工(复制精度好)。
电铸最重要的特征是它具有高度“逼真性”。
电铸甚至可复制0.5微米以下的金属线。
例如:
1英寸的宽度内,有2500根3.5微米的超细线的电视摄像机用的高精度金属网(超细金属网),就使用了电铸法进行生产的。
而香烟过滤嘴的纤维,也是使用纤维素通过超细金属网制成的,这是用其他金属加工法所不能达到的。
电铸复制的精度是非常高的。
高精度金属网的制造法,是在底板上用照相制板技术按需要涂上绝缘层(保护层),然后以此作为模板进行电铸。
2、 能调节沉积金属的物理性质。
可以通过改变电镀条件,镀液的组分的方法来调节沉积金属的硬度、韧性和拉伸强度等。
还可以采用多层电镀、合金电镀、复合电度镀方法得到其他加工方法不能得到的物理性质。
3、 不受制品大小的限制。
只要能够放入电镀槽就行。
4、 容易制出复杂形状的零件。
电铸法的缺点:
1、 操作时间长。
例如:
用3A/dmm的阴极电流密度沉积3mm厚的镍层,需要25h20min。
即使用是小薄零件要镀厚层时,成本很高,但是电镀过程中可以无人管理。
2、 要有经验和熟练技能的人员操作。
电铸装置是简单的,但在复制复杂形状的模型中要制造母模、导电层处理、剥离处理等,这些工序都要求有经验和熟练技能的人员才能操作。
3、 必须有很大的作业面积。
即使是小制品,也需要有镀槽、水洗槽等平面布置,废水处理装置必须有相当大的作业面积。
4、 除了要有电镀操作技术外,还必须有机械加工和金属加工知识。
电铸法并不是单用电镀操作而制出制品,还要进行衬底加工、研磨等机械操作,所以必须具备这些方面的知识和技巧。
电铸制品
1、 制造复制品。
包括原版录音片及其压模、印模、粗糙度标准片、美术工艺品、建筑五金、佛具等金属五金类。
2、 制造模具。
包括塑料成形模具、冲压模具、镍-钴-钨硬质合金电铸模具、印刷用字母等。
3、 金属箔与金属网的制造。
印刷线路板用铜箔,各种金属网、平板或旋转过滤网(印染、电器及电子零件用)、特殊刀片等。
4、 其它。
用于制造电火花加工电极、防涂装遮蔽板、金刚石锉刀、钻头、波导管,贮藏液态氢的球型真空容器,熔融盐电解制造钨等耐热金属的透平叶片,从非水溶液制造铝太阳能集热板等。
溅镀的原理主要利用辉光放电(glowdis-charge)将氩气(Ar)离子撞击靶(tar-get)表面,靶材的原子被弹出而堆积在基板表面形成薄膜。
溅镀薄膜的性质、均匀度都比蒸镀薄膜来的好,但是镀膜速度却比蒸镀慢很多。
新型的溅镀设备几乎都使用强力磁铁将电子成螺旋状运动以加速靶材周围的氩气离子化,造成靶与氩气离子间的撞击机率增加,提高溅镀速率。
一般金属镀膜大都采用直流溅镀,而不导电的陶磁材料则使用RF交流溅镀,基本的原理是在真空中利用辉光放电(glowdis-charge)将氩气(Ar)离子撞击靶材(tar-get)表面,电浆中的阳离子会加速冲向作为被溅镀材的负电极表面,这个冲击将使靶材的物质飞出而沉积在基板上形成薄膜。
一般来说,利用溅镀制程进行薄膜披覆有几项特点:
(1)金属、合金或绝缘物均可做成薄膜材料。
(2)再适当的设定条件下可将多元复杂的靶材制作出同一组成的薄
(3)利用放电气氛中加入氧或其它的活性气体,可以制作靶材物质与气体分子的混合物或化合物。
(4)靶材输入电流及溅射时间可以控制,容易得到高精度的膜厚。
(5)较其它制程利于生产大面积的均一薄膜。
(6)溅射粒子几不受重力影响,靶材与基板位置可自由安排。
(7)基板与膜的附着强度是一般蒸镀膜的10倍以上,且由于溅射粒子带有高能量,在成膜面会继续表面扩散而得到硬且致密的薄膜,同时此高能量使基板只要较低的温度即可得到结晶膜。
(8)薄膜形成初期成核密度高,可生产10nm以下的极薄连续膜。
(9)靶材的寿命长,可长时间自动化连续生产。
(10)靶材可制作成各种形状,配合机台的特殊设计做更好的控制及最有效率的生产。
阳极处理为一种电解过程,提供镀层金属的金属片作用有如阳极,电解液通常为镀着金属的离子溶液,被镀物作用则有如阴极。
阳极与阴极间输入电压后,吸引电解液中的金属离子游至阴极,还原后即镀着其上。
同时阳极的金属再溶解,提供电解液更多的金属离子。
某些情况下使用不溶性阳极,电镀时需添加新群电解液补充镀着金属离子。
一般铝合金很容易氧化,氧化层虽有一定钝化作用,但长期曝露之结果,氧化层仍会剥落,丧失保护作用,因此阳极处理的目的即利用其易氧化之特性,藉电化学方法控制氧化层之生成,以防止铝材进一步氧化,同时增加表面的机械性质。
电镀的涵义
电镀是应用电解原理在某些金属表面镀上一薄层其他金属或合金的过程。
(2)、电镀的目的
电镀的目的主要是使金属增强抗腐蚀能力、增加美观和表面硬度。
(3)、电镀的原理
电镀的原理与电解精炼铜的原理是一致的。
电镀时,一般都是用含有镀层金属离子的电解质配成电镀液;把待镀金属制品浸入电镀液中与直流电源的负极相连,作为阴极;用镀层金属作为阳极,与直流电源正极相连。
通入低压直流电,阳极金属溶解在溶液中成为阳离子,移向阴极,这些离子在阴极获得电子被还原成金属,覆盖在需要电镀的金属制品上。
金属表面容易氧化生锈是世人皆知的现象,特别是近几年来,酸雨及空气的污染,更加重了金属的腐蚀程度。
为此,金属表面处理工艺--电镀铬技术应用十分广泛。
在我国,传统的电镀铬金属表面处理工艺已有180多年的历史。
这种工艺通过阳极溶解、阴极吸附的技术原理,可在各种易氧化生锈的金属工件表面形成保护层。
然而,随着市场经济的飞速发展,电镀铬技术应用领域的不断扩大,传统电镀处理工艺的缺点也越来越明显,其缺点主要表现为以下几个方面:
1、设备投资过大。
电镀槽的制备技术标准高,要求严,令一般投资者望而却步。
2、生产过程中需直流电,能源消耗极大。
3、生产成本高。
所使用的铬酐价格昂贵,且有很大的毒害性,故而限制其应用范围。
4、生产过程中产生的含铬废水,排放渗入地下后不能分解,严重污染地下水源。
还会产生毒害气体排放,污染环境和空气,危害人们的身心健康和生态环境,恶化了广大城镇居民的居住质量。
電鍍完成後:
我們會發現正極減少的重量等於負極增加的重量。
主要是因為正極金屬溶解,形成金屬離子於溶液中,所以正極重量減少;而金屬離子在負極形成金屬原子析出,故負極重量增加。
另外電鍍液中的離子數目保持一定,所以電鍍液的濃度也不變。
最後要提醒的是電鍍時,被鍍物表面上的金屬薄膜是否均勻堅實,受到溫度、電流強度及電鍍液濃度等因素影響。
所以電鍍也是需要技巧的呢!
因為被鍍物上的鏽斑和油汙不導電,若不除去便無法鍍上,所以我們使用砂紙磨除鏽斑,再以氫氧化鈉水溶液洗去油汙,最後用蒸餾水沖洗。
電鍍完成後,被鍍物必須先以蒸餾水沖洗,再以丙酮洗淨,並靜置使之乾燥,使電鍍層硬化,最後用軟布摩擦,使其光亮。
註:
丙酮為一種極易揮發的溶劑,電鍍後的物體以丙酮沖洗後靜置,有助於快速乾燥硬化
2:
阴极电泳漆比阳极电泳漆更昂贵,就阴极电泳漆的设备成本就比阳极电泳漆的高出大约30%,但阴极电泳漆优异的抗腐蚀性经常使它们成为首选。
这两种涂料有各自特殊的使用领域。
现在全球超过98%的汽车生产商使用电泳底漆。
汽车车身和附件,设备、热交换器、金属装饰件都采用电泳涂装。
这种方法被广泛使用在金属或需要大量生产的金属表面的一次性涂装中,尤其适用很难采用其它涂装进行涂装的复杂形状物体。
环氧型阳极电沉积涂料:
农具、汽车零部件、型钢
丙烯酸型阳极电沉积涂料:
金属办公室家俱、空气扩散器、金属丝网、吊架
环氧型阴极电沉积涂料:
汽车车身及部件、转换器、家用电器
丙烯酸型阴极电沉积涂料:
草坪和花园农具、仪器、汽车轮和汽车门窗
真空鍍膜技術
蒸鍍(Evaporation)&濺鍍(Sputter)
薄膜沈積(ThinFilmDeposition)
在機械工業、電子工業或半導體工業領域,為了對所使用的材料賦與某種特性在材料表面上以各種方法形成被膜(一層薄膜),而加以使用,假如此被膜經由原子層的過程所形成時,一般將此等薄膜沈積稱為蒸鍍(蒸著)處理。
採用蒸鍍處理時,以原子或分子的層次控制蒸鍍粒子使其形成被膜,因此可以得到以熱平衡狀態無法得到的具有特殊構造及功能的被膜。
薄膜沈積的兩種常見的製程
物理氣相沈積--PVD
(PhysicalVaporDeposition)
化學氣相沈積CVD
(ChemicalVaporDeposition)
真空電鍍簡介
被鍍物與塑膠不產生化學反應
環保製程;無化學物污染
可鍍多重金屬
生產速度快
可對各種素材加工
屬低溫製程
化学镀镍的定义与分类
化学镀镍,又称为无电解镀镍,是在金属盐和还原剂共同存在的溶液中靠自催化的化学反应而在金属表面沉积了金属镀层的新的成膜技术。
氢脆的控制
在任何电镀溶液中,由于水分子的离解,总或多或少地存在一定数量的氢离子。
因此,电镀过程中,在阴极析出金属(主反应)的同时,伴有氢气的析出(副反应)。
析氢的影响是多方面的,其中最主要的是氢脆。
氢脆是表面处理中最严重的质量隐患之一,析氢严重的零件在使用过程中就可能断裂,造成严重的事故。
表面处理技术人员必须掌握避免和消除氢脆的技术,以使氢脆的影响降低到最低限度。
一、氢脆
1氢脆现象
氢脆通常表现为应力作用下的延迟断裂现象。
曾经出现过汽车弹簧、垫圈、螺钉、片簧等镀锌件,在装配之后数小时内陆续发生断裂,断裂比例达40%~50%。
某特种产品镀镉件在使用过程中曾出现过批量裂纹断裂,曾组织过全国性攻关,制订严格的去氢工艺。
另外,有一些氢脆并不表现为延迟断裂现象,例如:
电镀挂具(钢丝、铜丝)由于经多次电镀和酸洗退镀,渗氢较严重,在使用中经常出现一折便发生脆断的现象;猎枪精锻用的芯棒,经多次镀铬之后,堕地断裂;有的淬火零件(内应力大)在酸洗时便产生裂纹。
这些零件渗氢严重,无需外加应力就产生裂纹,再也无法用去氢来恢复原有的韧性。
氢脆机理
延迟断裂现象的产生是由于零件内部的氢向应力集中的部位扩散聚集,应力集中部位的金属缺陷多(原子点阵错位、空穴等)。
氢扩散到这些缺陷处,氢原子变成氢分子,产生巨大的压力,这个压力与材料内部的残留应力及材料受的外加应力,组成一个合力,当这合力超过材料的屈服强度,就会导致断裂发生。
氢脆既然与氢原子的扩散有关,扩散是需要时间的,扩散的速度与浓差梯度、温度和材料种类有关。
因此,氢脆通常表现为延迟断裂。
氢原子具有最小的原子半径,容易在钢、铜等金属中扩散,而在镉、锡、锌及其合金中氢的扩散比较困难。
镀镉层是最难扩散的,镀镉时产生的氢,最初停留在镀层中和镀层下的金属表层,很难向外扩散,去氢特别困难。
经过一段时间后,氢扩散到金属内部,特别是进入金属内部缺陷处的氢,就很难扩散出来。
常温下氢的扩散速度相当缓慢,所以需要即时加热去氢。
温度升高,增加氢在钢中的溶解度,过高的温度会降低材料的硬度,所以镀前去应力和镀后去氢的温度选择,必须考虑不致于降低材料硬度,不得处于某些钢材的脆性回火温度,不破坏镀层本身的性能。
避免和消除的措施
.1 减少金属中渗氢的数量
在除锈和氧化皮时,尽量采用吹砂除锈,若采用酸洗,需在酸洗液中添加若丁等缓蚀剂;在除油时,采用化学除油、清洗剂或溶剂除油,渗氢量较少,若采用电化学除油,先阴极后阳极;在电镀时,碱性镀液或高电流效率的镀液渗氢量较少。
2 采用低氢扩散性和低氢溶解度的镀涂层
一般认为,在电镀Cr、Zn、Cd、Ni、Sn、Pb时,渗入钢件的氢容易残留下来,而Cu、Mo、Al、Ag、Au、W等金属镀层具有低氢扩散性和低氢溶解度,渗氢较少。
在满足产品技术条件要求的情况下,可采用不会造成渗氢的涂层,如达克罗涂覆层可以代替镀锌,不会发生氢脆,耐蚀性提高7~10倍,附着力好,膜厚6~8μm,相当于较薄的镀锌层,不影响装配。
3 镀前去应力和镀后去氢以消除氢脆隐患
若零件经淬火、焊接等工序后内部残留应力较大,镀前应进行回火处理,减少发生严重渗氢的隐患。
对电镀过程中渗氢较多的零件原则上应尽快去氢,因为镀层中的氢和表层基体金属中的氢在向钢基体内部扩散,其数量随时间的延长而增加。
新的国际标准草案规定“最好在镀后1h内,但不迟于3h,进行去氢处理”。
国内也有相应的标准,对电镀锌前、后的去氢处理作了规定。
电镀后去氢处理工艺广泛采用加热烘烤,常用的烘烤温度为150~300°C,保温2~24h。
具体的处理温度和时间应根据零件大小、强度、镀层性质和电镀时间的长短而定。
去氢处理常在烘箱内进行。
镀锌零件的去氢处理温度为110~220°C,温度控制的高低应根椐基体材料而定。
对于弹性材料、0.5mm以下的薄壁件及机械强度要求较高的钢铁零件,镀锌后必须进行去氢处理。
为了防止“镉脆”,镀镉零件的去氢处理温度不能太高,通常为180~200°C。
应注意的问题
材料强度越大,其氢脆敏感性也越大,这是表面处理技术人员在编制电镀工艺规范时必须明确的基本概念。
国际标准要求抗拉强度σb>105kg/mm2的钢材,要进行相应的镀前去应力和镀后去氢处理。
法国航空工业对屈服强度σs>90kg/mm2的钢件就要求作相应去氢处理。
由于钢材强度与硬度有很好的对应关系,因此,用材料硬度来判断材料氢脆敏感比用强度来判断更为直观、方便。
因为一份完善的产品图和机加工工艺都应标注钢材硬度。
在电镀中我们发