型焦厂观摩会经验交流DOC.docx
《型焦厂观摩会经验交流DOC.docx》由会员分享,可在线阅读,更多相关《型焦厂观摩会经验交流DOC.docx(15页珍藏版)》请在冰豆网上搜索。
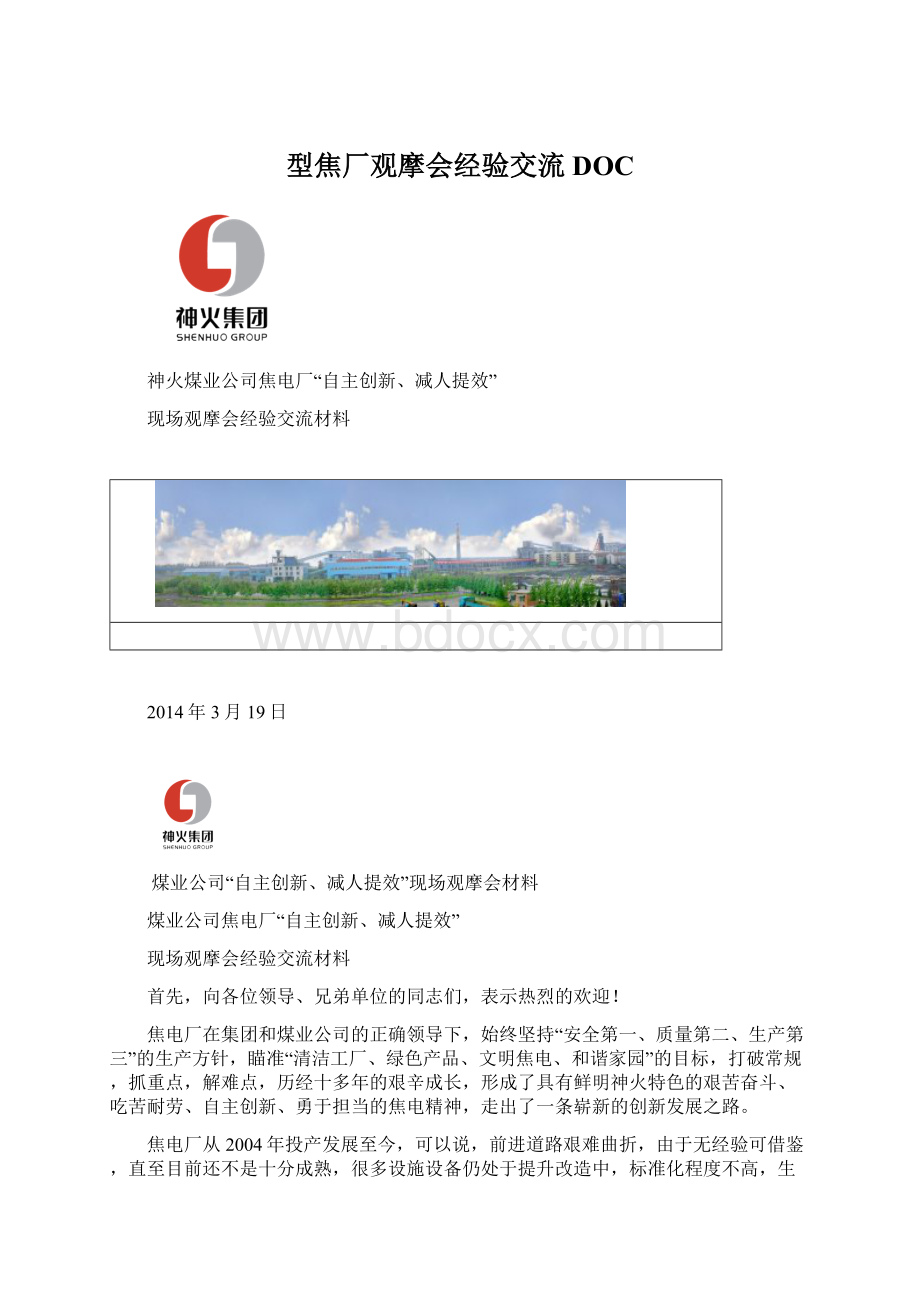
型焦厂观摩会经验交流DOC
神火煤业公司焦电厂“自主创新、减人提效”
现场观摩会经验交流材料
2014年3月19日
煤业公司“自主创新、减人提效”现场观摩会材料
煤业公司焦电厂“自主创新、减人提效”
现场观摩会经验交流材料
首先,向各位领导、兄弟单位的同志们,表示热烈的欢迎!
焦电厂在集团和煤业公司的正确领导下,始终坚持“安全第一、质量第二、生产第三”的生产方针,瞄准“清洁工厂、绿色产品、文明焦电、和谐家园”的目标,打破常规,抓重点,解难点,历经十多年的艰辛成长,形成了具有鲜明神火特色的艰苦奋斗、吃苦耐劳、自主创新、勇于担当的焦电精神,走出了一条崭新的创新发展之路。
焦电厂从2004年投产发展至今,可以说,前进道路艰难曲折,由于无经验可借鉴,直至目前还不是十分成熟,很多设施设备仍处于提升改造中,标准化程度不高,生产现场环境、细节管理与兄弟单位相比还有一定的差距,需要向兄弟单位学习借鉴的地方很多。
今天在我们这里谈不上观摩,谈不上什么经验,只是把我们几年来的思路具体做法向大家简要汇报,不妥不当之处,敬请在座的领导、同志们给予批评指正。
煤业公司“自主创新、减人提效”现场观摩会材料
第一部分艰苦创业培育出勤俭节约文化
焦电厂是我们公司采用新技术、新工艺的创新项目,许多工艺方法、设备选型、生产系统都靠自己摸索,无任何经验可借鉴,是边设计、边调试、边生产实验的“三边”工程。
在初期,由于生产经验缺乏,各项工艺流程不健全,设备设施不完善,造成工作环境恶劣,职工工作、生活条件艰苦,脏、乱、差、苦、累、险是焦电厂当时最真实的写照。
原料破碎粉尘铺天盖地,工人天天都像处在尘暴中;成型半成品沥青烟气浓厚,熏得人喘不过气;厂区道路坑洼不平、尘土飞扬,晴天是“扬灰路”,雨天是“水泥路”。
生产系统不完善,职工劳动强度大。
常常是人工上料、人工搬球,几乎天天加班。
半成品生产时,含有沥青的浓浓烟气充满整个车间,二楼、三楼的操作人员一、二米外看不清任何东西,有时呛得喘不过气,新工人一个班下来,大都被熏得头晕目眩、腹胀恶心,吃不下饭。
在这里工作时间长的人,都被熏得黝黑,怎么洗都洗不净。
热搅拌机周围40多度的高温,操作人员衣服被汗水湿透一遍又一遍。
系统不能正常生产是常有的事,此时就要靠人工拉料、上料,搬球,人员在一个班内要靠一把铁锨搬运近20吨原料,年轻的农民工累走了一批又一批;刚走出校门的女工,为避免烟气的侵害,上岗穿得像防化兵一样,工作起来
煤业公司“自主创新、减人提效”现场观摩会材料
每人每班要搬5-6吨热半成品,手上磨起了串串血泡,一个班下来很多人累得站都站不起来。
当时焦电厂没有澡堂、没有更衣柜,工人下班背着装衣服的化肥袋,走很远到新庄矿洗澡、更衣。
“远看是拾破烂的,近看是下井挖炭的,仔细看是焦电的。
”正是对他们当时状况的形象描述。
就如此的环境状况,广大干部职工也没有退缩,硬是咬着牙坚持、再坚持。
正是在这种长期艰苦环境下的磨练,逐步形成了神火焦电人特别能吃苦、特别能战斗的艰苦创业精神。
这种艰苦奋斗、勤俭节约的精神,在焦电厂的成长历程中,不断得到传承、发扬光大。
“自己动手、不等不靠、攻坚克难、敢作敢为”已成为厂广大干部职工的行为习惯。
目前从大的生产工艺系统完善,大型设施设备技术改造,到铺路种花种草等大事、小事;从来不等不靠不轻言外委,依靠广大职工自己摸索、自己干;没有技术,就学技术,没有人才,就多方面培养。
历经十年的艰苦创业,厂里涌现出一大批“能人”、“专家”。
机电自动化“专家”孙继伟、空调维修“能人”葛紫燕、土建工程“能手”王守初、炭化炉组维修“技师”孙启河、有专业修车的“大拿”黄文仁等,他们不但能修、能改,而且还有许多创新、创造,这种精神体现在厂的方方面面。
比如在整个厂区,有大小空调60多台,生产系统使用的大型制冷设备6台,车间使用环境差的地方,一年一台空调需要修好几次,前期外委维修,一年修理费用8万多元且无法保证维修质量。
为保证维修质
煤业公司“自主创新、减人提效”现场观摩会材料
量减少费用,厂2012年成立了空调维修专业小组,从车间优秀技工中选派3人,到济南进行专业培训,自己购买维修工具、配件,厂所有空调、制冷设备全部自己维修。
两年来,每年的全部维修费用不超过1万元。
这样,不但节省了大量的资金,葛紫燕、曹明伟等人也从实践锻炼中成长为名副其实的空调维修“专家”,这也为以后的工作开展打下了良好的基础。
焦场土建工程“能手”王守初,他的工程组,承揽了厂基础建设的所有工程。
大到设备基础钢筋绑扎、水泥浇筑,路面硬化、路边石铺设,绿化广场、鱼塘观桥建造,厂区下水道整修、盖板预制,小到墙壁粉刷、管道铺设、厕所整修、澡堂水池面砖粘贴等等都是他们自我设计、独立完成。
成型车间新液压机运行的辅助设施,输送皮带、斗提、热搅拌桶等全部由废旧材料改造而成。
成型机冲头磨损快、更换周期短,废旧冲头经机修工王兰民精心修复后,再次使用,一年少购买100多套,节约资金30余万元。
发电系统汽机阀门较多,为避免误操作,该车间对每个阀门都进行命名标识,这些小巧精致的标识牌,都是由发电车间的员工们利用外部施工队伍进行保温时裁下边角料、铝箔皮,通过裁剪、描字、绘画、注漆加工制作而成。
一个个设计美观的标识牌,工整、清晰的字迹,生动逼真的警示图案,显示出了职工们灵巧的笔法和较强的书写绘画功底,同时又对现场岗位安全起到了较好地警醒作用。
煤业公司“自主创新、减人提效”现场观摩会材料
为了改变焦电厂的环境,我们自己对厂区进行了重新规划设计,并提出“自己的工厂自己建、自己的面貌自己变”的基本方针,在对整个厂区绿化美化过程中,全部由厂干部职工利用业余时间加班加点自己动手进行。
同时为了保证所植花木的成活率,大家下班后跟从园林绿技术员,现场学习技术,积累经验,并不断实践,确保挖坑、栽植、浇水等各个环节的工作质量。
望着自己亲手栽植的一株株树苗陆续成活,大家都十分开心地说:
“我们厂一定会成为绿树成荫的“花果山”。
同时也节约了资金,仅办公广场一处的硬化、绿化、美化工程,如交给外委公司就需资金70多万元,我们自己设计,购买树木、路边石等花费不到8万,节约费用60余万元。
在给职工创造良好的生产生活环境的同时,传承了艰苦奋斗的优良传统,增强了企业的凝聚力。
在抓大的同时,我们更注重在枝节细微之处引导员工养成厉行节俭的良好习惯。
如:
在对机关科室日常管理方面,根据用水情况,实行茶水分具体时间段供应,这样可以减少无人用水时的电能消耗;在空调使用方面,除落实室内温度在夏季高于26度,在冬季低于5度方可开启外,实行电量考核制度及空调使用寿命奖惩制度;在办公用品使用管理方面,实行科室个人定量承包,一支笔换多支笔芯再使用,一张纸双面打印充分利用,内部信息能够通过BQQ等通讯手段解决的问题,不采用纸质传递;生活用品使用管理方面,实行自我修复,如拖把“换头不换把”、笤帚磨损后,用废旧布条、塑料带绑扎,几个拼凑起来
煤业公司“自主创新、减人提效”现场观摩会材料
继续使用;在澡堂用水方面,实行定时定量供水,避免浪费;在职工用餐方面,开展班中餐饭盒无剩菜的“光盘”行动等等。
这一系列的日常小事,体现的不仅仅是全厂上下的节俭意识,更为主要的是,通过这些让大家自发养成困中求变的良好思维。
这也正是焦电厂“自主、主动、不等不靠、勇于担当”精神的真实写照。
艰苦奋斗既是我们党的优良传统,更是我们“焦电人”的立身法宝。
凡成就一番事业,不可能一帆风顺。
困难并不可怕,关键在于如何对待,采取什么行动。
当前,市场竞争激烈,企业发展、生存的不确定因素千变万化,困难随时发生。
只有长期坚持“走最困难的路”,企业的发展才会勇立潮头,求得生存,立于不败之地。
第二部分优化系统全面实现自动化控制
为了完善生产系统,减少人员控制环节,减少岗位不安全因素,实现自动化生产。
我们不断优化生产系统,由生产的机械化迈向自动化系统控制,从而减轻员工岗位劳动强度、降低企业生产成本、提高人员
煤业公司“自主创新、减人提效”现场观摩会材料
生产功效。
几年来,我们在探索中前行,在实践中提升,大胆进行工艺系统创新改造,自主设计开发了有一定技术水平的斜体炭化炉组自动化控制,成型液压机自动化控制系统,半成品收集称重自动化系统,原料破碎自动化计量系统,环保降尘自动化洒水系统,热风利用自动化系统,发电集控自动化系统,澡堂供水自动化系统,安保红外线报警自动化系统,办公流程自动化系统等多个自动化控制系统。
使原料输送、搅拌、计量、成型、炭化、余热利用发电等整个生产线,实现了自动运输、自动搅拌、自动给料的闭环控制。
先后完成20多项重点技术攻关。
每项改造工作在付出艰辛的同时,也得到了丰厚的回报。
也为焦电厂的发展奠定了坚实的基础。
自动化系统完善提升历程。
作为一种全新的生产模式,由于没有现成的经验可以借鉴,焦电厂在2004年投入试运行时,可以说每条系统,每台设备都是独立运行,每台设备的启动、停止是由生产人员操作的。
当时焦电厂生产系统面临两大问题:
一个是产能的问题。
实际产能与设计产能相差悬殊,设备运行稳定性差;一个是自动化建设的问题。
生线运行缺少测控手段,系统运行不能形成流水线。
针对这两大问题,我们把生产系统化为五个单元,分别为:
烘干系统生产线;原料配仓输送系统生产线;破碎计量系统生产线;半成品成型系统生产线;炭化系统生产线。
并确定从两个方面同时突破,一手抓生产线系统的完善与消缺;一手抓自动化的建设。
因为焦电厂生产工艺的特殊性没有同行业成功的经验可以借鉴。
在自动化的建设上要求技术人员必须了解焦电厂各系统生产工艺,设备性能及逻辑关系。
基于这个基础,我们需要培养自己的自动化建设人才。
从管理层(组态与通讯系统)、逻辑层(PLC、测控系统)、控制层(变频器、智能开关等)需要有独立的开发和选型能力以满足生产线对自动化控制的要求。
同年,我们开始实施烘干系统的自动化建设,当时由于人员力量薄弱、技术水平也很有限,我们把烘干系统的17台主机设备通过硬接线的方式连接到烘干的控制室,在控制室建立了一个集中控制台,设计了17个启动按扭、17个停止按扭,将设备按流水线闭锁了起来。
在终端设备安装了摄像头。
就这样,形成了焦电厂第一个生产线子系统的集中控制。
当然,这个距自动控制的距离还相差甚远,但也收到了良好的效果。
当时烘干系统运行人员一个小班需要4个人,定员16人。
系统投用后只需要1人操作。
减少了12个生产运行人员。
系统的建立与投用也减少了运行人员的劳动强度,不用来回的跑着启动、停止设备。
大家第一次体会到集中控制的优越性。
2005年,我们选派专业人员到圣源科技有限公司学习培训,开始合作建立了我厂第一个真正意义上自动化生产线——原料配仓输送系统生产线。
从自动检带、自动配仓、无线摇控到语音预警等真正实现了一键化操作。
这个系统的建立更加深远的意义在于,通过实践锻炼,我厂自己的技术人员掌握了自动化控制逻辑层(PLC及测控技术)的一些基础知识,大家慢慢的开始动手做一些PLC程序设计与测控传感器的设计。
慢慢的建立自动化的理论体系与逻辑思维。
2006年,我们开始对机械成型机进行多点测控,包括机械保护与故障报警、在基于混合料高温、高粘结性物料设计出了自动复位式料位检测装置。
同年,我们建立了我厂第一个以计算机运算为基础的,多点测控的集中控制生产线。
其中包括流体测控、压力测控、容积计量等技术应用。
我们厂的技术人员在系统的建立中对工厂工业自动化系统的整体架构有了一个更加清晰的认识,技术水平同时也得到了很大的提升,掌握了基本的计算平台工业应用软件及组态的开发。
2007年,我厂开始对生产线进行升级改造,主要对制约产能、生产效率及环保问题进行集中、重点解决。
同年,针对3#料的特殊性,通过实验成功利用高细磨替代环锤破碎机破碎3#料,解决了破碎能力小、配件消耗量大的难题。
3#料破碎产能由原来的5t/h提升到23t/h;材料消耗由原工艺60万/年,降低到12万/年。
2008年开始,我们开始着手对劳动强度大、生产工效低、环境卫生差的工艺系统进行优化、改造。
通过四年多的不断攻关,我们先后自行设计、安装并正式投用了“原料煤场自动化配煤运输系统生产线”;“基于仓储定位的原料入仓自动控制生产线”;“伺服式自动化控制破碎生产系统”;“自动化四柱大吨位液压机半成品生产线”;“半成品定量收集自动化控制系统”;“半成品识别输送自动运行系统”;“炉组运行自动化控制系统”;在基础环境系统方面建立了“厂区定时洒水降尘系统”;“职工澡堂自动换热供水系统”;“厂区安防系统”等。
在综合利用方面我们建成并投用了“3MW余热发电系统”。
成功实现了基于DCS系统的“炉、机、电、化水”同室监控系统以及行政办公自动化系统。
截止2012年底,我厂建立了环形以态网结构的中央集控系统,15个分站并入中央集控系统,统一在中央集控系统监控、操作运行。
半成品产能达到30万吨/年产能。
目前原料破碎、半成品生产只需要一个单班运行,即能满足现在炭化炉10万吨/年的生产规模。
根据公司分时电价政策,我们的原料输送系统、破碎系统、半成品生产系统只在零点班运行,即可满足炭化生产。
通过中央集控系统对各分站的整合与投运,大幅度提高了劳动生产功效,降低了生产成本。
一、焦电厂自2004年投产历经十年,生产系统实现了四大跨越。
(一)生产工效的跨越。
2004年投产厂定员560人,产能1200吨到3000吨之间/月,人均工效约22吨;目前厂定员230人,产能10万吨/年。
人均工效440吨。
2004年吨产品电耗130KW.h,目前吨产品电耗50KW.h。
(二)产品层次的跨越。
前期只有115一种规格产品,目前我们可制造115、135、160及棱形产品。
生产线通过配方调整可生产二级、一级、特级及特一级产品,同时可根据市场及客户要求定制产品。
(三)创新能力的跨越。
焦电厂通过自主创新培养和锻炼了一大批技术人员。
机械、电气及自动控制均达到了基础专业水平,自动化专业从控制层(计算机运算组态系统)、到逻辑层(PLC程序设计)、到控制层(变频器和智能开关)我们均达到了自主设计、自主调试、自主施工的能力。
(四)人员思想的跨越。
从前期的把问题推出去到现在的自主想办法、自主试验、自主制作的思想跨越。
二、四大自动化系统研发及关键技术创新点简介。
在基于焦电厂工业环形以太网基础上,根据自动化系统的作用性质不同大致分为四个方面。
第一方面,生产工艺自动化系统;第二方面,生产辅助自动化系统;第三方面,生活设施自动化系统;第四方面,行政办公自动化系统。
(一)生产工艺自动化系统。
生产自动化系统包括8条,分别为:
“原料煤,场地自动化计量配煤运输系统”、“基于仓储定位的原料煤入仓自动控制生产线”、“伺服式自动化控制破碎生产系统”、“原料计量配比自动化控制系统”、“半成品液压生产线自动化系统”、“半成品定量收集自动化控制系统”、“半成品识别输送自动运行系统”、“炭炉组运行自动化控制系统”(附系统控制图)。
以上八个子系统构成生产自动化系统,各子系统可独立自动运行,也可以在中央集控统一协调操作。
由于时间关系,在这里我重点介绍三个系统。
炭化炉组自动化系统、半成品液压生产线自动化系统和3MW余热发电系统。
1、炭化炉组自动化系统。
自动化控制前,炭化工艺存在诸多缺陷:
炭化过程为人工操作控制,易因为人为原因造成控制操作一人一个样,很难在操作技术上统一,从而造成同一炉孔产品质量波动和反复,影响成品质量的稳定性和合格率。
参与炭化炉组控制人员较多,整体用工成本较高。
炭化过程控制较复杂,人员操作不安全因素多,劳动量较大。
炭化过程相关的数据记录不详不准,甚至存在弄虚作假,对炉组炭化工艺的摸索和改造缺少相关的数据依据。
(1)炉组自动化研究与实践。
为有效地消除以上问题,将炭化控制实行相关技术改造,实现炉组炭化控制自动化及信息采集自动化。
本项目采用现场炭化控制步骤摸索、理论分析与自动测试相结合的方式进行。
其技术路线为:
对炭化过程中现场操作步骤进行划分归类,归纳出不同炭化进程针对性控制步骤及要点;根据炭化不同进程控制步骤及要点配套相关控制设备及设施;根据归纳出的不同炭化进程控制步骤设定自动控制程序,实现现场自动控制,根据控制结果适当微调。
对自动控制过程或认为控制过程实行全程信息采集,实现重要数据记录、操作提醒及异常报警提示。
(2)炉组炭化自动化控制达到的效果。
a.炉组炭化控制过程实行程序化,步骤化。
对于不同阶段的炭化进程,自动调节相关温度、负压、风量等参数。
各参数调节时间段及调节大小实现量化。
b.炉组炭化控制过程实行可视控制,通过电脑界面显示,能够及时方便掌握每个炉孔的炭化状态。
c.炉组炭化控制过程相关参数信息实现即时采集,包括:
温度、负压、配风量、返火质量等重要的参数。
d.炉组炭化控制实现自动和人工分体控制,对于人工控制时,自动化系统对整个控制工程有全程跟踪记录,并在炭化进程转换时给予控制操作自动提示。
(3)炉组炭化自动控制产生的效益。
a.炉组炭化自动控制及信息采集系统完全投用后,可减少岗位操作人员21人,每年可直接节约用工成本70万元。
b.对稳定炉组炉况及炭化质量帮助很大,炉组炭化自动控制与信息采集系统投用以来,每天成品出炉质量合格率由85%提升到97%,每吨焦炭增收36元,年10万吨,约300余万元;
c.炉子运行安全方面,完全可控,表现在运行过程控制和单孔炉温稳定方面,采用自动控制,使用单孔炉子炭化过程和升温得到自动控制,并根据反馈回控制中心各项数据,能进行自动或手动的修正调整,从而实现炉温稳定,质量可控;
d.环境影响方面,基本杜绝了因人为操作不当,造成炉温下降或煤气燃烧不充分,排烟中有害气体量超标,造成对环境污染的影响;
e.单孔炉子运行寿命方面,因实现炭化过程温度、配风量、负压的可控,大大延长炉底和火道耐火材料的使用寿命;
2、半成品液压生产线自动化系统。
半成品液压生产线自动化系统是基于液压机为主体,以仓储为以基础自动跟随液压机节拍喂料,液压机生产产品自动定量收集,根据炭化炉所需求产品规格、级别自动识别并输送到炭化炉。
整个过程不需要人工干预。
(1)整个系统情况。
半成品液压生产线自动化系统的主要优势在于大仓储、全自动化、生产节拍高、半成品质量可控等优点。
首先,我们投用了800吨的仓储系统,比原来的的40吨仓储提高了20倍。
这样,可以实现单班配料三班生产的工艺调整。
一方面提高了生产效率;另一方面提高了生产系统抵抗风险的能力。
破碎系统的检修、维护时间更加充足。
更进一步提高设备运行的稳定性。
其次,实现系统自动化,原料的存储、输送自动跟踪液压机运行,可实现一键启停。
减少生产线转载点人员操作的环节。
一方面通过物料平衡确保物料输送的稳定性;另一方面整体生产线集中控制,同时也保证了物料供给系统工作的连续性。
三是生产节拍高,单台液压机的产能达到机械成型机的两倍,可长周期连续运行,维护量小。
克服了机械成型机故障率高,维护量大的问题。
四是半成品质量稳定可控,液压机生产过程本身的过程测量可以进行压力的调整,以达到合格半成品密度的要求。
克服机械成型机压力定值的局限性。
(2)液压机工作机理及我们对程序的再设计情况。
液压机是针对蒸压砖而设计的定型产品,最早起源于日本,是基于PLC逻辑与触摸屏数字化定义为基础的工业生产机器人,无论是测控还是逻辑已经非常成熟。
而我们的型煤产品与蒸压砖还不完全相同。
在使用过程中因压制步骤与成品脱膜方式造成模具使用寿命只有8万次,也就是一个月的时间,虽然高于机械成型机模具使用寿命,但是每月要更换一模具,费用在3.5万元。
三台液压机模具消耗每年要130万。
另外,模具磨损过程造成成品开裂,影响成品质量及整球率。
根据以上情况,我们仔细研究了压制与脱膜过程及原理。
若仍沿用蒸压砖的方式压制与脱膜,将在生产过程造成大量无谓的模具磨损。
鉴于此,我们对液压机自动控制程序进行了重新设计,并对组态系统进行逻辑定义。
改变压机的工作方式。
现在一套模具的使用寿命达到60万次。
三台液压机每年总的模具投入费用由原来的130万降低到16万元。
(3)与下级系统“炉组自动化系统”接口情况。
液压机生产的产品定量收集后最终要输送到炭化炉进行炭化。
最终生成成品。
在基于“炉组自动化系统”基础上,利用炉组自动化信息数据库,把出炉信息自动传输到“液压系统工作站平台”通过液压系统工作站选定需求的半成品级别、规格,自动运输到炭化炉。
(4)液压机生产自动化系统意义。
一是采用模框浮动式,液压分级加压,多次自动排气技术结构,通过调整压制活塞同模框运动的速度差实现双向加压,产品密度均匀、质量好。
有效解决了模具的重度磨损问题。
二是采用皮带升降防破碎装置及半成品装框称重系统实现半成品自动装框。
三是主机采用机电液一体化及智能控制技术,实现了布料、成型、装框等工序全自动化,产品质量高、成本低。
四是利用PLC逻辑控制与蒸汽压力温度实现蒸汽喷入的可调可控。
五是利用PLC逻辑控制及物料平衡料位的检测,实现了生产过程中物料动态平衡供应。
六是利用工业以太网技术实现了两级系统的无缝链接,有效解决了炭化系统与半成品生产系统的信息交换。
3、3MW余热发电系统。
本项目在论证初期,我们组织相关人员进行了大量的考察和调研,对目前的余热电厂系统运行方式进行了分析和论证,结合焦电厂实际情况,提出并确立了我们自己的系统运行方式及由锅炉系统、化水系统、汽机热力系统、发电机系统及电气五大系统集为一体的运行方式,整个系统控制由DCS整合集中控制的控制理念。
项目总投资679万元,其中基建投资190万。
设备及安装投资489万元。
建设周期为8个月。
3MW余热发电系统机组自2013年5月12日正式投运试发电。
劳动定员8人,三班24小时运行。
每班组两个人。
原锅炉定员人数不增加。
实现了“锅炉、化水、汽机、电气”同室监控运行,在国内是首创,项目达到国内领先水平。
项目正式投运后。
因焦电厂产能未完全释放,锅炉有效的热量低,实际发电量在1300-1500度/h。
月发电量在100万度左右。
产能释放后平均发电量可达到2600度/小时。
发电量1400万KW.h。
按公司2013年网购综合电价KW.h/0.62每年可新增销售收入约860万元。
(二)生产辅助自动化系统。
生产辅助系统包括:
厂区定时洒水降尘系统和基于工业以太网结构的厂区安防系统。
1、定时洒水系统建设情况。
2010年,我们厂自已设计了厂区定时洒水系统。
在生产现场安装了17个50米喷枪。
在生活区及花坛安装了14个。
当时选购喷枪时,我们喷射距离达50米的多为进口产品,以美国雨鸟喷枪为代表的价位都在3000元以上。
通过网络查询我们选购了舟山一家模仿进口喷枪的厂家。
通过对比,雾化程度与喷射距离基本达到进口喷枪的效果。
同时,我们建立了计算机控制系统。
在计算机组态系统中输入洒水时间,系统自动循环运行。
整个系统下来投入材料费用9万多元。
有效的改善了生产环境,尤其是大风天气环境污染问题,自安装至今,未出现质量问题。
2、厂区安防系统建设情况。
厂区安防视频监控、及红外报警自动化系统。
我们在办公楼、库房及厂区围墙建立了以计算机组态分析的报警系统。
该系统把PLC控制技术引入到安防监控系统中,构造了一个智能化、网络化、立体的多媒体监控系统。
该平台采用先进的服务器架构管理模式,一套组态软件就可实现对监控系统各项相关硬件设备和所有用户的集中管理。
具有以下优点:
一是可靠性与安全性。
系统的设计应具有较高的可靠性,在系统故障或事故造成中断后,能确保数据的准确性、完整性和一致性,并具备迅速恢复的功能,同时系统具有一整套完成的系统管理策略,可以保证系统的运行安全。
二是可扩充性。
系统设计中考虑到今后技术的发展和使用的需要,具有更新、扩充和升级的可能。
并根据今后该项目工程的实际要求扩展系统功能,同时,本方案在设计中留有冗余,以满足今后的发展要求。
此系统设定报警时段后,有人接触围墙、接触办公区及库房,系统自动声光报警提醒调度员,调度员根据报警地点通知厂值班人员及保卫人员及进到现场查看情况,有