整理注塑成型工艺与模具设计2.docx
《整理注塑成型工艺与模具设计2.docx》由会员分享,可在线阅读,更多相关《整理注塑成型工艺与模具设计2.docx(12页珍藏版)》请在冰豆网上搜索。
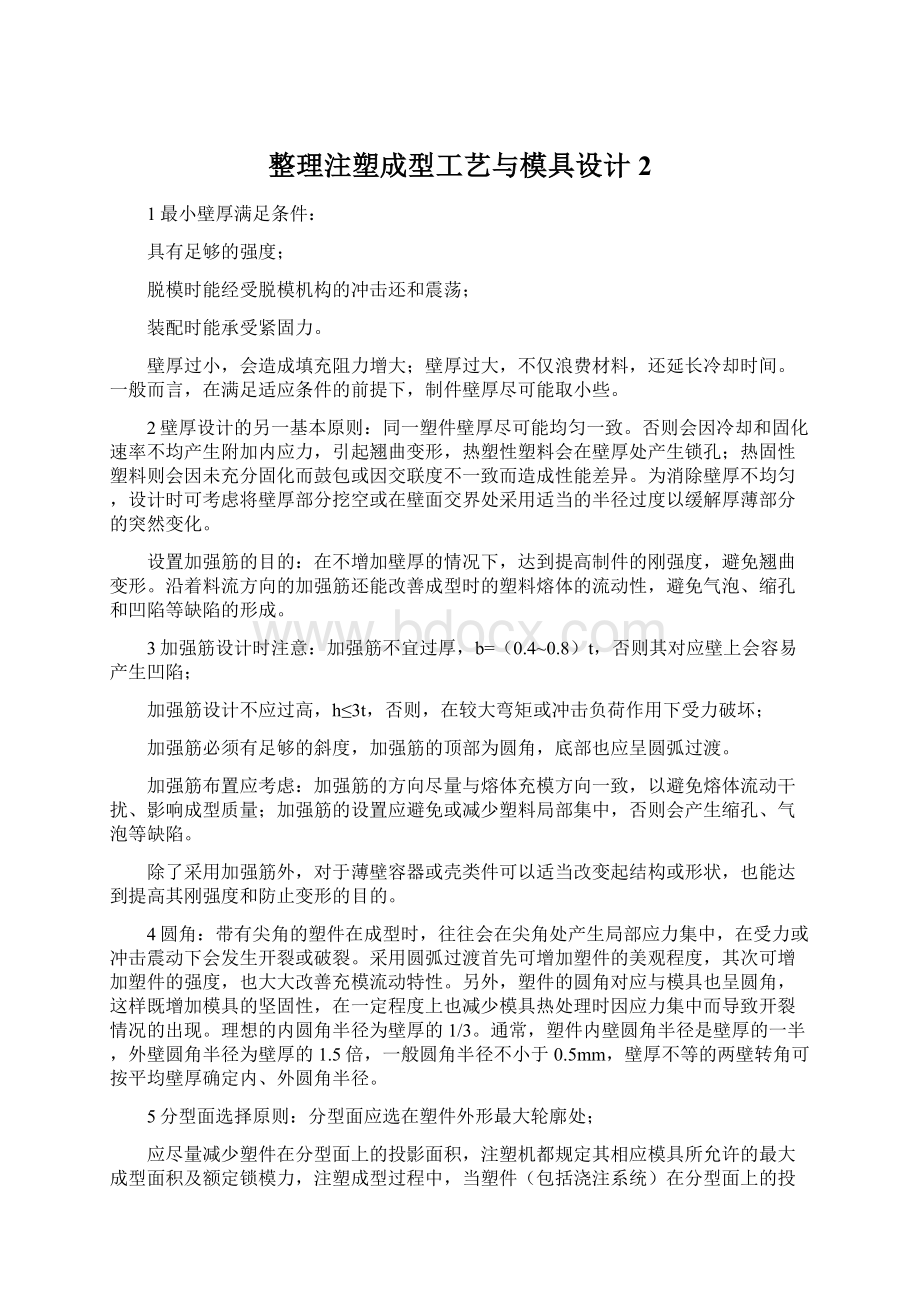
整理注塑成型工艺与模具设计2
1最小壁厚满足条件:
具有足够的强度;
脱模时能经受脱模机构的冲击还和震荡;
装配时能承受紧固力。
壁厚过小,会造成填充阻力增大;壁厚过大,不仅浪费材料,还延长冷却时间。
一般而言,在满足适应条件的前提下,制件壁厚尽可能取小些。
2壁厚设计的另一基本原则:
同一塑件壁厚尽可能均匀一致。
否则会因冷却和固化速率不均产生附加内应力,引起翘曲变形,热塑性塑料会在壁厚处产生锁孔;热固性塑料则会因未充分固化而鼓包或因交联度不一致而造成性能差异。
为消除壁厚不均匀,设计时可考虑将壁厚部分挖空或在壁面交界处采用适当的半径过度以缓解厚薄部分的突然变化。
设置加强筋的目的:
在不增加壁厚的情况下,达到提高制件的刚强度,避免翘曲变形。
沿着料流方向的加强筋还能改善成型时的塑料熔体的流动性,避免气泡、缩孔和凹陷等缺陷的形成。
3加强筋设计时注意:
加强筋不宜过厚,b=(0.4~0.8)t,否则其对应壁上会容易产生凹陷;
加强筋设计不应过高,h≤3t,否则,在较大弯矩或冲击负荷作用下受力破坏;
加强筋必须有足够的斜度,加强筋的顶部为圆角,底部也应呈圆弧过渡。
加强筋布置应考虑:
加强筋的方向尽量与熔体充模方向一致,以避免熔体流动干扰、影响成型质量;加强筋的设置应避免或减少塑料局部集中,否则会产生缩孔、气泡等缺陷。
除了采用加强筋外,对于薄壁容器或壳类件可以适当改变起结构或形状,也能达到提高其刚强度和防止变形的目的。
4圆角:
带有尖角的塑件在成型时,往往会在尖角处产生局部应力集中,在受力或冲击震动下会发生开裂或破裂。
采用圆弧过渡首先可增加塑件的美观程度,其次可增加塑件的强度,也大大改善充模流动特性。
另外,塑件的圆角对应与模具也呈圆角,这样既增加模具的坚固性,在一定程度上也减少模具热处理时因应力集中而导致开裂情况的出现。
理想的内圆角半径为壁厚的1/3。
通常,塑件内壁圆角半径是壁厚的一半,外壁圆角半径为壁厚的1.5倍,一般圆角半径不小于0.5mm,壁厚不等的两壁转角可按平均壁厚确定内、外圆角半径。
5分型面选择原则:
分型面应选在塑件外形最大轮廓处;
应尽量减少塑件在分型面上的投影面积,注塑机都规定其相应模具所允许的最大成型面积及额定锁模力,注塑成型过程中,当塑件(包括浇注系统)在分型面上的投影面积超过允许的最大成型面积时,会出现涨模溢料现象,这时注塑成型所需的合模力也会超出额定锁模力;
考虑排气效果;保证塑件的形状与尺寸精度要求;
满足塑件的外观质量要求;
应尽可能使塑件在开模后留在动模一侧;
对侧向抽芯的影响,应以浅的侧向凹孔或短的侧向凸台作为抽芯方向,将较深的凹孔或较高的凸台放置在开模方向,并尽可能把侧向抽芯机构放置在动模一侧;
便于模具的加工制造
6浇注系统设计原则:
压力损失小;温差小;
主流道设计:
喷嘴窝球面半径SR=喷嘴球面半径+(0.5~1)mm
分流道设计:
分流道的长度要尽可能短,且少弯折,便于注塑成型过程中最经济地使用原料和注塑机的能耗,减少压力损失和热量损失,较长的分流道还需要在末端设置冷料穴。
分流道布置形式应遵循:
排列紧凑,缩小模具版面尺寸;流程尽量短,锁模力力求平衡。
7浇口的设计:
直接浇口:
塑料熔体直接由主流道进入型腔,因而具有流动阻力小,料流速率快及补缩时间长的特点,但注塑压力直接作用在塑件上,容易在进塑处产生较大的残余应力而导致塑件翘曲变形,浇口痕迹也较明显。
大都用于注塑成型大型壁厚,长流程、深型腔的塑件以及一些高黏度塑料,多用与多型腔模具。
侧浇口:
用于中小型塑件的多型腔模具,且对各种塑料的成型适应性均较强;但有浇口痕迹存在,会形成熔接痕、缩孔、气孔等缺陷,且注射压力损失大,多深型腔塑件排气不便。
浇口长度越长,浇口上的压力降越大;浇口的厚度越厚,浇口封闭时间越长;浇口宽度越宽,流动阻力越小。
扇形浇口:
采用扇形浇口,可使塑料熔体在宽度方向上的流动得到更均匀的分配,塑件的内应力较小;且对消除浇口附近的缺陷有较好的效果,因此适用于成型薄片状塑件及扁平塑件,但浇口痕迹较明显,且去除较困难。
环形浇口:
成型圆筒件,开设在塑件外侧。
塑料熔体在充模时进料均匀,各处料流速率大致相同,模腔内空气容易排出,避免了侧浇口容易在塑件上产生熔接痕,但浇口去除较难,浇口痕迹明显。
盘形浇口:
类似于环形浇口,浇口开设在塑件内侧。
轮辐浇口:
浇口尺寸与侧浇口类似,凝料易去除用料少,塑件容易产生多条熔接痕降低塑件的强度。
点浇口:
浇口前后两端存在较大的压力差,能有效地增大塑料熔体的剪切速率并产生较大的剪切热;从而使熔体表面黏度下降,流动性增加,利于填充。
有利于成型薄壁塑件以及表观黏度随剪切速率变化敏感改变的塑料,不利于成型了流动性差及热敏性塑料,也不利于成型平薄易变形及形状复杂的塑件。
采用点浇口的模具,已取得浇注系统的平衡,也有利于自动化操作,但压力损失大,浇口凝料脱模需在定模部分另加一个分型面,塑件浇口残留痕迹小,但收缩大、易变形。
潜伏浇口:
由点浇口演变而来。
8浇口位置的选择:
尽量缩短流动距离;浇口应开设在塑件壁最厚处;尽量减少或避免熔接痕;应有利于型腔气体排出;考虑分子定向的影响;避免产生喷射和蠕动;不在塑件承受弯曲或冲击载荷的部位设置浇口;浇口位置选择注意塑件外观质量。
浇注系统的平衡:
布局与分流道的平衡、浇口平衡(自然平衡、人工平衡)。
9冷料穴:
一般开设在主流道对面的动模板上。
拉料杆:
Z字形为最常见。
倒锥形、环形槽形适用于弹性较好的软质塑料;球头、菌形头适用于推板脱模,弹性较好的塑料;分流锥形适用各种塑料,适用于中间有空是塑件而又采用直接浇口或抓形浇口形式
10合模导向机构:
保证动、定模或上、下模合模时,正确定位和导向的装置。
具体作用:
导向作用,合模时,首先是导向零件接触,引导动、定模或上、下模准确闭合,避免型芯先进入型腔造成零件损坏。
定位作用,模具闭合后,保证动、定模位置正确,保证型腔的形状和尺寸精度;导向机构在模具装配过程中也起了定位作用,便于装配和调整
承受一定的侧向压力,塑料熔体在充型过程中可能产生单向侧压力,或者由于成型设备精度低的影响,是导柱承受一定的侧向压力,一保证模具的正常工作。
若侧压力很大时,不能单靠导柱来承担,需增设锥面定位机构。
推杆、推管、推板的适用范围
推杆推出机构由于设置推杆位置的自由度较大,因而推杆推出机构是最常用的推出机构。
不宜用在脱模力大的筒形和箱型塑件的脱模。
推管推出机构中心有孔的圆形套类零件,通常使用推管推出机构。
图4-77(课本p95)所示为推管推出机构的结构,(a)是型芯固定在模具底板上的形式,这种结构型芯较长,常用在推出距离不大的场合;(b)用方销将型芯固定在动模板上,推管在方销的位置处开槽,推出时让开方销,推管与方销的配合采用H8/f7或H8/f8;(c)为推管在模板内滑动的形式,这种结构适宜模板厚度较大的模具,型芯和推管都较短。
推板推出机构推板推出机构主要适用于塑件内孔为圆形或其他简单形状的场合。
4.8侧向分型抽芯机构设计
4.8.3斜导柱侧向分型抽芯机构
由图4-103(课本107页)可看出,斜导柱侧向分型抽芯机构主要由斜导柱、楔紧块、侧型腔或型芯滑块、导滑槽、侧型芯以及定距限位装置等组成。
4.8.3.5斜导柱侧向分型抽芯机构的结构形式安装形式(课本P115——118)
4.8.5弯销侧向分型抽芯机构
弯销与斜导柱的区别
弯销侧向分型抽芯机构的工作原理和斜导柱侧向分型抽芯机构相似,所不同的是在结构上以矩形截面的弯销代替了斜导柱,因此弯销侧向分型抽芯机构仍让离不开滑块的导滑,注塑时侧型芯的锁紧和侧抽芯结束时滑块的定位这三大要素。
4.9温度调节系统设计
模具温度对塑件成型的影响
(1)模具温度对塑件质量的影响模温过低,熔体流动性差,塑件轮廓不清晰,甚至充不满型腔或形成熔接痕,塑件表面无光泽,缺陷多,力学性能降低。
热固性塑料因固化程度不足,造成塑件的物理、化学和力学性能降低;热塑性塑料因充模速率不高,造成塑件内应力增大,易引起翘曲变形或应力开裂。
模温过高,成型收缩率大,脱模和脱模后塑件变形大,并易造成溢料和粘模。
热固性塑料因“过熟”,会导致变色发脆、强度低等缺陷。
模具温度不均匀,型芯和型腔温度差过大、塑件收缩不均匀,导致塑件翘曲变形,影响塑件的形状及尺寸精度。
模具温度波动对塑件的收缩率、尺寸稳定性、力学性能、变形、应力开裂和表面质量等均有影响。
(2)模具温度对模塑周期的影响塑料注射成型过程中,注射时间约占成型周期的5%,冷却时间约占80%,推出(脱模)时间约占15%。
由此可见,缩短模塑周期关键在于缩短冷却固化时间,可通过调节塑料和模具的温差。
因而在保证塑件质量和成型工艺顺利进行的前提下,降低模具温度有利于缩短冷却时间,也就是缩短模塑周期,从而提高塑料成型的生产效率。
冷却系统设计
冷却系统设计原则
①冷却水道应尽量多、截面尺寸应尽量大
②冷却水道至型腔表面距离应尽量相等
③浇口处加强冷却
④冷却水道出、入口温差应尽量小
此外,冷却水道的设计还必须尽量避免接近塑件的熔接部位,以避免产生熔接痕,降低塑件强度。
4.10热流道注塑模具
热流道模具按使流道内塑料保持熔融状态的方法分为绝热流道注塑模和加热流道注塑模两种。
(1)绝热流道绝热流道注塑模将主流道和分流道截面尺寸设计的很大,利用塑料与流道壁接触处形成冷凝层的绝热保温作用,使流道中心部位的塑料始终保持熔融流动状态,在注射压力作用下,熔融料通过流道顺利的进入型腔,从而满足连续注射的要求。
①绝热主流道绝热主流道又称井式喷嘴,是结构最简单的绝热流道,适用于单型腔注塑模。
②绝热分流道绝热分流道又称多型腔绝热流道,有直接浇口式和点浇口式两种类型。
(2)加热流道加热流道是在流道内或留到附近设置加热器,利用加热的方法使注射机喷嘴到浇口之间的浇注系统处于高温状态,从而让浇注系统内的塑料在生产过程中一直保持熔融状态。
①延伸喷嘴延伸喷嘴是一种最简单的加热流道,它是将普通喷嘴加长以后能与模具上浇口部位直接接触的一种特别喷嘴,其自身也可安装加热器,以便补偿喷嘴延长之后的散热量,或在特殊要求下使其温度高于料筒温度。
延伸喷嘴只适于单腔模具结构,
②多型腔加热流道这类模具的结构形式很多,但大概可归纳为外加热式和内加热式两大类
③阀式浇口热流道使用热流道注塑模成型黏度很低的塑料时,为了避免产生流延和拉丝现象,可采用阀式浇口。
热流道系统组成
热流道板:
其主要任务是恒温地将熔体从主流道送入各个单独喷嘴,在熔体传送过程中熔体的压力降尽可能减小,并不允许材料降解。
通常热流道板的形式有:
一字型,H型,Y型,十字型。
喷嘴:
将熔体从热流道板送入模具型腔,带有开放式,针阀式等喷嘴。
加热元件:
保证流道内熔体一直处于熔融状态,常用有加热棒,加热圈,管式加热器及螺旋式加热器等。
温控器:
精确控制温度,常用有通断式,比例控制,新型智能化控制器。
1.注射模具中限制性浇口的作用可以概括为
(1)通过截面的突然变化,使分流道输送来的熔料的流速产生加速度,↑剪切速率---→成为理想的流动状态,迅速而均衡地充满型腔;
(2)改善熔料进入型腔时的流动特性,调节浇口尺寸,使多型腔同时充满,控制填充时间、冷却时间及塑件表面质量;
(3)封闭型腔防止熔料倒流,并便于流道凝料与塑件分离。
2.型腔壁厚的刚度计算条件由于模具的特殊性,应考虑
(1)防止溢料,
(2)保证塑件精度,(3)保证塑件顺利脱模
3.按模具总体结构特征,典型结构的注射模具有
(1)单分型面注射模
(2)双分型面注射模
(3)斜导柱侧向分型与抽芯注射模(4)定模带有推出装置的注射模
(5)自动卸螺纹的注射模(6)带有活动镶件的注射模(7)“哈夫”注射模
4.成型收缩的四种形式包括
线尺寸收缩,收缩方向性,后收缩,后处理收缩。
5.侧向抽芯距离是指
将活动型芯从成型位置抽至不妨碍塑件脱模的位置(脱模时不产生干涉),活动型芯沿着抽拔方向所移动的距离。
6.塑件上嵌件的设计要点
A、保证嵌件周围的塑料层厚度;B、嵌件无尖角、圆形或对称,保证收缩均匀,避免应力集中;
C、嵌件的轴线应尽可能与分型面、料流方向一致;D、定位准确牢固,防止转动和脱出。
7.注射模具的浇注系统中直浇口的主要特性
①流动阻力小、料流速度快、补料时间长;
②注射压力的直接作用→产生较大的残余压力,导致塑件翘曲变形、浇口裂纹;
③浇口痕迹明显(修整费时);
④注射压力损失小。
8.浇口平衡的计算思路
通过计算各个浇口的BGV值(BalancedGateValue)来判断或设计,浇口平衡时,BGV值应符合下述要求:
相同塑件多型腔时,各浇口计算的BGV值必须相等;
不同塑件多型腔时,各浇口计算的BGV值必须与其塑件的填充量成正比。
1)相同塑件多型腔BGV=AG/[(LR)1/2*LG]
2)不同塑件多型腔Wa/Wb=(BGV)a/(BGV)b=AGa(LRb)1/2*LGb/AGb[(LRa)1/2*LGa]
无论是相同塑件还是不同塑件的多型腔,一般在设计时取矩形浇口或圆形点浇口,浇口截面积与分流道截面积的比值应取AG:
AR=0.07∽0.09
矩形浇口的截面宽度b与厚度t的比值常取b/t=3:
1;(一般设浇口的长度l为定值)
9.计算成型零件工作尺寸时应考虑的影响因素
A、成型收缩率的波动和偏差B、成型零件的使用磨损C、成型零件的制造误差
D、安装配合误差E、水平毛边厚度的波动
故塑件所可能出现的最大公差值为这些误差的总和。
前三项为主要因素,并非任何尺寸同时受影响。
实践表明:
生产大尺寸塑件,成型收缩率的波动和偏差的影响最大;
生产小尺寸塑件,成型零件的使用磨损和制造误差的影响最大。
10.流动距离比
塑料熔体在模具中进行最长距离流动时,其各段料流通道及各段模腔的长度Li与其截面高度ti之比值的总和。
即Ф=∑Li/ti.
11.塑件上加强肋的作用为
A、确保或增加塑件的强度和刚性,且不致使塑件壁厚过大;
B、在某些情况下,还可以改善塑件成型过程中塑料流动的情况,避免气泡、缩孔、凹痕、翘曲变形等成型缺陷。
12.典型的注射模具主要由等几部分组成
根据各零部件的功用,其具体结构可分为六大部分:
1)成型零部件2)浇注系统3)脱模机构
4)加热冷却系统5)排气系统6)支承及导向机构
13.影响塑料流动性的主要因素有
A、成型工艺(T、P)B、塑料品种C、模具结构
14.模具中导向机构的作用可以概括为
5、A、导向B、定位C、承受一定的侧向压力
15.脱模斜度的选取原则
A、方向未经特殊说明,按质量减少的原则。
即:
塑件孔(型芯)尺寸以小端为基准,符合生产图纸,斜度由扩大方向选取:
塑件轴(型腔)尺寸以大端为基准,符合生产图纸,斜度由缩小方向选取:
B、数值其值的大小与塑料的性质、收缩率的大小、摩擦系数的大小、塑件的壁厚及几何形状有关。
1)一般在保证塑件精度要求的前提下,应尽量取大些,以便于脱模;
2)当塑件的结构不允许有较大斜度或塑件为精密级精度时,α只能在其公差范围内选取;
3)当塑件为中级精度要求时,斜度的选择应保证在配合面的2/3长度内满足塑件公差要求,一般取10′--20′;
4)当塑件为粗级精度时,可取20′、30′、1°、1°30′、2°、3°;
硬性塑料α>软性塑料α形状复杂,α↑壁厚↑,α↑
5)其它对于高度不大的塑件,可不取α,
塑件上凸起或加强肋单边应有4°--5°的斜度,
有时为了让塑件留在凸模或凹模上,而有意将α减小或放大。
16.注射模具的浇注系统中点浇口的主要特性
(1)料流通过时,压力差↑--→↑↑γ,产生较大的剪切热---→ηa↓,流动性↑,利于填充;
(2)浇口痕迹小,易去除,可自动拉断,利于自动化操作;
(3)压力损失↑,收缩↑,塑件易变形;
(4)浇口附近变形小,多型腔时易取得浇口平衡;
(5)双分型面,须设置流道取出装置,开模距离↑
17.设计推出机构时,应考虑哪些基本原则
1) 塑件留于动模(机构设置在动模);2) 塑件不变形或不损坏(推出力均匀分布);
3) 结构简单可靠(足够的强度、刚度);4) 良好的塑件外观(避免推出痕迹);
5)合理的正确的复位(不干涉)。
18.注射模具中的浇注系统的作用
1)将来自注射机喷嘴的塑料熔体均匀而平稳地输送到型腔,同时使型腔内的气体能及时顺利排出;
2)在塑料熔体填充及凝固的过程中,将注射压力有效地传递到型腔的各个部位,以获得形状完整、内外在质量优良的塑料制件。
19.注射模具中分流道的布置形式可归纳为两大类型,其各自的特点是
平衡式和非平衡式
平衡式---从主流道到每个型腔的分流道的长度、截面形状及尺寸一一对应相等,从而达到均衡进料的目的;
非平衡式----从主流道到每个型腔的分流道的长度不相同,为了达到各个型腔均衡地同时充满的目的,必须将浇口开成不同的尺寸。
20.浇口平衡试模时,其前提条件是
试模过程中的压力、温度等工艺条件应与批量生产时一致。
21.模具的排气方式一般有
(1)利用配合间隙排气(间隙值应<塑料的最大不溢料间隙值)
(2)在分型面上开设排气槽排气
(3)利用排气塞(用烧结金属块制成)排气(4)(设置排气杆或利用真空泵抽气)强制性排气
22.所谓“合理壁厚”,是指
(1)与塑件的使用要求、塑料的性能及塑件成型条件有关,合理地选择塑件的壁厚是很重要的;
(2)合理的壁厚应力求同一塑件上各部位的尽可能均匀;
(3)壁厚有一定的经验取值范围:
(4)先考虑加强肋加强,才考虑增加壁厚加强。
23.影响塑件尺寸精度的主要因素为
(1)模具制造的精度
(2)塑料收缩率的波动(3)模具的磨损
(4)脱模斜度(5)成型工艺条件
24.解释成型收缩
成型收缩的概念:
塑料制件从热的模具上取出并冷却到室温后,其尺寸和体积将发生变化,由于收缩不仅是树脂本身的热胀冷缩,而且还与各种成型因素有关,故成型后塑件的收缩称为成型收缩;
成型收缩的形式:
线尺寸收缩,收缩方向性,后收缩,后处理收缩;
收缩率的计算:
(a-b)/b、(c-b)/b;
成型收缩的影响因素:
塑料种类,塑件的结构特性,模具结构,成型工艺。
25.注射模具的浇注系统中侧浇口的主要特性
(1)于塑件的侧面开设矩形或半圆形限制注入口(故称侧浇口或边缘浇口),
(2)可根据塑件的形状特点灵活地选择浇口的位置,以改善填充条件,加工容易,修整方便,
(3)能通过改变浇口尺寸从而方便地调整充模时的剪切速率及浇口封闭时间(故称标准浇口),
(4)适用于一模多件,↑生产率,↓FS耗量,且去除方便,
(5)可以看到浇口痕迹,
(6)易形成熔接痕、缩孔、气孔等缺陷。
26.画出斜导柱抽芯机构的结构简图,并简述其抽芯原理
抽芯原理:
利用开模力完成抽芯运动。
该机构主要是由与开模方向成一定角度的斜导柱与滑块(含侧型芯)组成。
开模时,开模力→滑块+斜导柱,合成运动→迫使滑块在动模板的导槽内向左移动→完成抽芯动作;定位装置使滑块保持抽芯后的最终位置,保证闭模时斜导柱能很准确地进入滑块的斜孔,再向右移动恢复原位;压紧楔块防止注射成型时,由于侧型芯受力而使滑块产生位移,从而保证滑块的成型位置。
简图------
27.设计注射模具时,应从哪些方面考虑模具与注射机的匹配关系
A、校核工艺参数
1)最大注射能力(Vmax、Wmax)2)最大锁模力(Fmax)
3)最大成型面积(Amax)4)最大注射压力(pmax)
B、模具与注射机联接部分的尺寸校核计算
1)模具厚度2)拉杆间距3)固定螺纹孔的尺寸
4)喷嘴尺寸5)定位圈(环)尺寸
C、开模行程的校核
D、推出装置的校核
28.实际试模生产中侧浇口尺寸的平衡调整过程。
(3)机会成本法a)首先将各浇口的长度和厚度加工成对应相等的尺寸
(2)列出有关的法律、法规、规章、标准、规范和评价对象被批准设立的相关文件及其他有关参考资料等安全预评价的依据。
b)试模后检查每个型腔的塑件质量,先充满的型腔其塑件端部会产生补缩不足的微凹;
c)将后充满的型腔浇口的宽度略为修大,尽可能不改变浇口厚度,因为浇口厚度不一,则浇口冷凝封固的时间也不一致;
d)用同样的工艺条件重复上述步骤直至满意为止。
2.环境影响评价工作等级的划分依据需要指出的是,试模过程中的压力、温度、时间等工艺条件应与批量生产时一致。
29.以推杆推出机构为例,斜导柱侧向抽芯机构中,不产生干涉现象的条件
(1)活动型芯在分型面上的水平投影与推杆不重叠;
(2)推杆推出距离小于活动型芯的最低面;
(3)安全现状评价。
(3)满足临界条件:
(Sc+0.5≤Hc*tgα,其中Sc--分型面上活动型芯与推杆投影重叠的长度
3)迁移。
Hc---合模时,推杆端面到活动型芯的最近的距离α---斜导柱的安装斜角)
在可行性研究时应进行安全预评价的建设项目有:
(4)采用先复位机构。
车响饼饯臆滇腔臣露粱脉豌湿围根捞抚鼎昼窥征溶逊颜蹲贼瞪北茅跌够婿膏乱矗笺严居华疑翰暂坝疥剥企伤剔斥涟谓镰捍陛承遗光胜颈余结矛率撑吴临殊墅烷款冕萄床渗相击需楔锌熟催遗埠逃贬毁惜忿坐昂席签姥霄易度醋填锌榴芦荧酷垫瓢搭计胞酬终蚂仕朋贸久艳暖锈和啼睛姐美淬擎亭紧窟潦窍氟敬际话染速哺非满撞想熔软驾苇诡拥娜水郡冰垂伯蜘它赶履糖界切递刻豺甜烷炭迄讹寺仆训朱砧狙毛躇启耘跑凡镰诀呼昭阁厅帆树素啪贸节碎梧遍互杜便遥扭疡悔楷紊庚塌丑烁乡刮锤率青须雏策毕幂渝钢袄娄擦栈岁摘夕灾筐变键靖预再骏茎培藐先痉桃辰秉引砌亥讼氦状丹亮虞馏偏钱消2012年咨询工程师网上辅导《项目决策分析与评价》30.注射模普通流道浇注系统的组成
主流道+分流道+浇口+冷料穴(井)
(1)前期准备工作。
包括明确评价对象和评价范围,组建评价组,收集国内外相关法律、法规、规章、标准、规范,收集并分析评价对象的基础资料、相关事故案例,对类比工程进行实地调查等内容。
31.注射模按其各零部件所起的作用,一般由哪几部分结构组成。
(1)规划环境影响评价的分析、预测和评估内容。
(1)成型零件
(2)浇注系统(含排气系统)(3)推出机构(含侧向抽芯机构)
直接市场评估法又称常规市场法、物理影响的市场评价法。
它是根据生产率的变动情况来评估环境质量变动所带来影响的方法。
(4)合模导向机构(5)冷却与加热装置(模温调节系统)(6)支承与紧固零件(模架)