第一篇 金属液态成形及铸造工艺设计.docx
《第一篇 金属液态成形及铸造工艺设计.docx》由会员分享,可在线阅读,更多相关《第一篇 金属液态成形及铸造工艺设计.docx(67页珍藏版)》请在冰豆网上搜索。
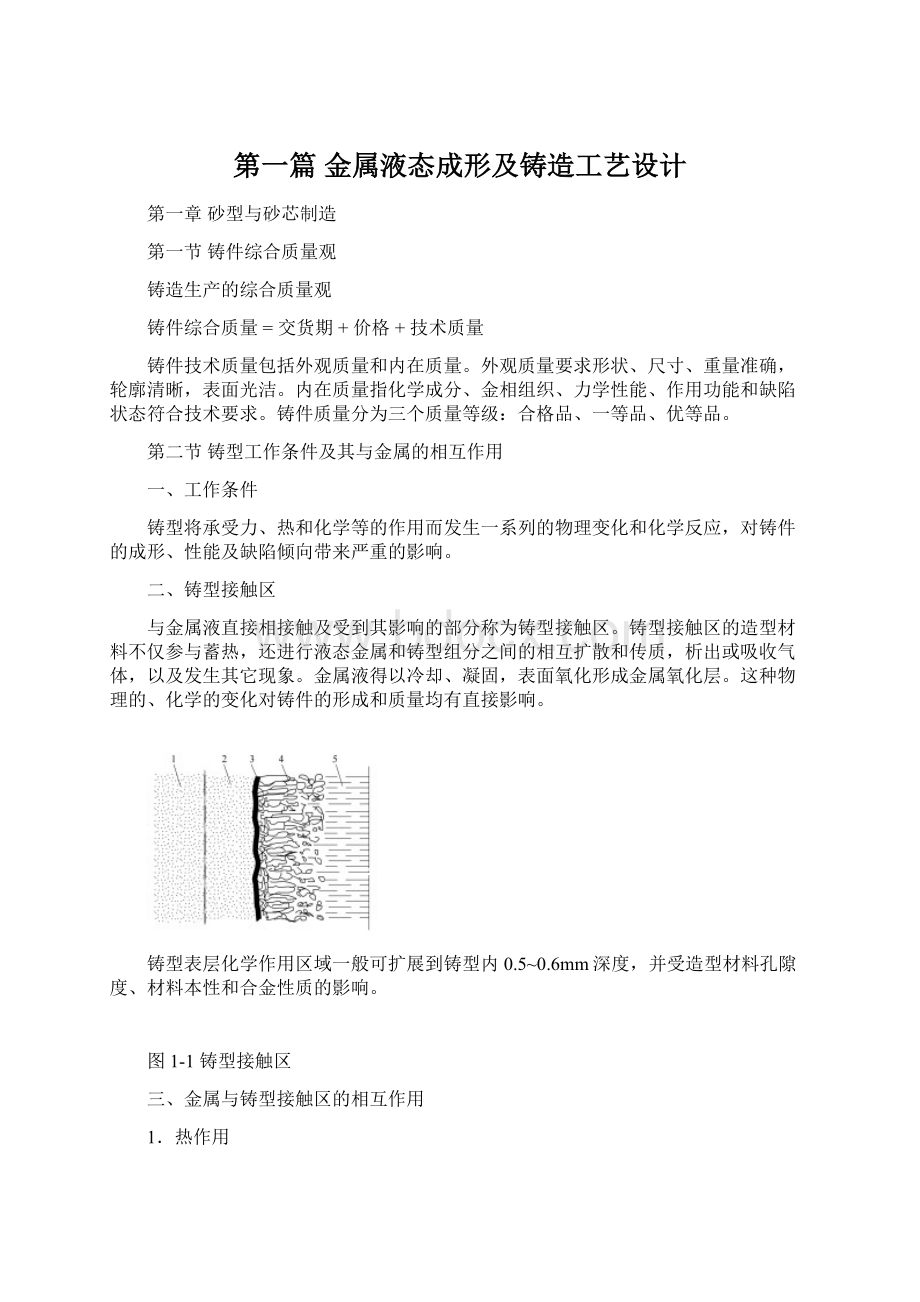
第一篇金属液态成形及铸造工艺设计
第一章砂型与砂芯制造
第一节铸件综合质量观
铸造生产的综合质量观
铸件综合质量=交货期+价格+技术质量
铸件技术质量包括外观质量和内在质量。
外观质量要求形状、尺寸、重量准确,轮廓清晰,表面光洁。
内在质量指化学成分、金相组织、力学性能、作用功能和缺陷状态符合技术要求。
铸件质量分为三个质量等级:
合格品、一等品、优等品。
第二节铸型工作条件及其与金属的相互作用
一、工作条件
铸型将承受力、热和化学等的作用而发生一系列的物理变化和化学反应,对铸件的成形、性能及缺陷倾向带来严重的影响。
二、铸型接触区
与金属液直接相接触及受到其影响的部分称为铸型接触区。
铸型接触区的造型材料不仅参与蓄热,还进行液态金属和铸型组分之间的相互扩散和传质,析出或吸收气体,以及发生其它现象。
金属液得以冷却、凝固,表面氧化形成金属氧化层。
这种物理的、化学的变化对铸件的形成和质量均有直接影响。
铸型表层化学作用区域一般可扩展到铸型内0.5~0.6mm深度,并受造型材料孔隙度、材料本性和合金性质的影响。
图1-1铸型接触区
三、金属与铸型接触区的相互作用
1.热作用
液态金属浇入铸型后,由于金属与铸型间存在很大的温差而发生强烈的热交换。
在热作用下,铸型水分蒸发并发生迁移,使铸型沿型壁出现较大的温度梯度和湿分梯度,从而使铸型各部分的强度发生变化。
2.机械作用
液态金属会对铸型型壁产生冲击和冲刷作用,铸型还将承受液态金属的静压力。
铸件凝固收缩时亦将受到铸型和砂芯的机械阻碍作用。
这些力的作用有可能造成铸件砂眼、裂纹、变形及尺寸超差等缺陷。
3.化学作用
液态高温金属对铸型的热作用将使铸型在高温下析出气体,引起铸型中各种附加物、有机物的燃烧、分解和升华,可能使铸件产生气孔。
比如,在有色合金铸造中,在通常的浇注温度下将发生下列化学反应:
Mg+H2O=MgO+H2↑+434500J
3Mg+N2=Mg3N2+485700J
2Al+3H2O=Al2O3+3H2↑
反应产生的气体、氧化物和放出大量的反应热导致了铸件中气体、夹渣缺陷的形成和铸件的进一步氧化燃烧。
第三节 砂型与砂芯
一、对造型材料性能的基本要求
1)型砂、芯砂应具有一定的强度,保证在造型、合箱、搬运和浇注过程中不变形,不损坏。
2)良好的透气性。
铸型或型芯中产生的气体能够通过砂粒间的空隙顺利排出型(芯)外,以消除或减少铸件中的气孔缺陷。
3)对铸件收缩的可退让性(或容让性)。
当铸件冷却收缩时,铸型会发生相应的变形和退让,图1-3。
4)一定的耐火度和化学稳定性。
在高温液态金属作用下,造型材料不软化;不与液态金属发生化学反应;不产生或少产生反应性气体。
5)良好的工艺性能,即在造型、制芯时不粘模,具有好的型(芯)砂流动性和可塑性;在铸件落砂和清理时具有好的出砂性。
6)对于铝、镁合金,还要有保护性,以防止合金在浇注和凝固过程中氧化、燃烧。
图1-3受收缩应力的铸件示意图图1-4粘土型砂结构示意图
1-原砂粒2-粘土-水分胶体3-附加物4-透气孔隙
二、湿型砂用原材料
湿型砂一般常用粘土型砂,由原砂、粘土、附加物及水按一定比例混碾而成,其结构见图1-4。
粘土、附加物和水混合成浆,包覆并以薄膜形式把砂粒联结起来,使型砂具有一定强度和可塑性。
型砂中的孔隙使其具有一定的透气能力。
附加物通常是为了改善砂的某些性能而加入的。
1.铸造用原砂
原砂按矿物组成不同分为石英质原砂和非石英质原砂两类。
石英质原砂主要来自天然硅砂,以圆形颗粒为优。
铸造用硅砂按二氧化硅含量分为7级(表1-3)。
表1-3铸造用硅砂按Wsio2%分级(GB9442-88)
分级代号
98
96
93
90
85
80
75
Wsio2(%)
≥98
≥96
≥93
≥90
≥85
≥80
≥75
W泥分(%)
≤0.2,≤0.5,≤1.0
≤0.3,≤0.5,≤2.0
≤1.0,≤2.0,≤10.0
非石英质原砂主要有镁砂、橄榄石砂、锆砂、铬铁矿砂、石灰石砂等。
镁砂主要成分是MgO,属碱性耐火材料,常用于高锰钢型砂或涂料。
橄榄石砂组分主要为[(Mg,Fe)2SiO4]。
用镁橄榄石砂替代石英砂生产高锰钢铸件,铸件表面质量良好,还可避免工人接触有害硅粉尘。
锆砂主要矿物是锆英石(ZrSiO4),锆砂熔点高,锆砂热膨胀性小,其热导率、蓄热系数、密度都比硅砂高很多,故铸件在锆砂型内冷凝速度快,一定程度上可以细化晶粒,提高铸件力学性能。
而且锆砂热化学稳定性好,几乎不被熔融金属或金属氧化物浸润,有利于阻止金属液浸入铸型孔隙,可防止化学粘砂,减少机械粘砂缺陷。
锆砂价贵较贵,一般只用其粉料配制抗粘砂涂料、涂膏。
石灰石砂化学成分主要是CaCO3,经破碎、筛选后配制。
石灰石砂无硅尘危害,铸件表面光洁,不粘砂,用于铸钢时成型流动性好。
但是,石灰石砂硬度低,混制中易破碎,限制了其使用范围。
2.粘土
粘土是湿型砂的主体粘结剂。
粘土被水湿润后具有粘结性和可塑性;烘干后硬结,具有干强度。
重新湿润后,粘结性和可塑性又能恢复而具复用性。
粘土颗粒直径大多数为1~2μm以下。
按晶体结构分为普通粘土、高岭土(Al2O3·2SiO2·2H2O)和膨润土蒙脱石(Al2O3·4SiO2·nH2O)。
生产中可以对膨润土进行活化处理,以提高其粘结性能。
我国出产供货的膨润土多系钙基膨润土。
为提高钙基膨润土的粘性,根据阳离子交换性质,可以在湿型砂混制中加配一定量(膨润土量的4%~5%(质量分数))的Na2CO3进行活化处理即可获到良好的粘结性能和可塑性。
粘土阳离子交换过程(膨润土活化处理)的化学反应机理可示意为:
Ca++基蒙脱石+Na2CO3→Na++基蒙脱石+CaCO3↓
粘土型砂的干态粘结机理可解释为:
烘干过程中砂型逐步失水和体积收缩使砂粒和粘土颗粒间相互靠近,紧密接触而产生附着作用而依靠分子间引力产生“干”强度。
3.附加物
型砂加入一些如煤粉、渣油、淀粉等附加材料,使型砂具有特定的性能,改善铸件的表面质量。
煤粉作用主要是在合金液的高温作用下于铸型表面产生大量还原性气体(CO),防止金属液被氧化,并使铁液表面的氧化铁还原。
总的来说,煤粉的加入能够显著改善铸铁件的表面质量。
湿型铸铁件所用型砂中煤粉含量常在3%~8%(质量分数)范围内。
三、湿型砂制备
湿型砂用于铸铁和有色合金,有时铸钢也用。
拟定好湿型砂的物料配方,控制和稳定好湿型砂性能以符合使用要求。
1.铸铁用湿型砂
表1-5为国外一些厂家的湿型砂性能情况。
型砂性能和组分的控制范围差别很大。
表1-5国外铸铁件湿型砂性能
铸铁湿型砂中含有煤粉及失效煤粉。
型砂含水量通常高达4.5%-6%。
水分过量,透气性低,铸件容易出现气孔。
因此,必须对型砂性能进行严格控制才能保证铸件质量的稳定。
大、中型铸件采用表面干型或干型。
表面干型和干型一般采用颗粒较粗的原砂。
为提高其透气性、退让性和抗夹砂能力,型砂中通常还要加入0.5%-2%(质量分数)的木屑。
2.铸钢用粘土砂
铸钢的浇注温度高(≥1500℃),钢水密度大,收缩率大,易氧化,因此,铸钢用型砂应有较高的耐火度,好的透气性、退让性,低的发气性和热膨胀性。
铸钢用原砂颗粒要比铸铁用的粗,小件用天然石英砂;大件用人造石英砂;重要的大型铸件用镁砂、铬铁矿砂或锆砂作为面砂。
铸钢件干型及型芯表面都要喷、刷涂料。
一般铸钢件用石英粉涂料;高锰钢、耐热钢、不锈钢等高合金钢和厚大铸钢件,可采用刚玉粉、锆砂粉或镁砂粉涂料。
3.有色合金用湿型砂
有色金属熔化后极易氧化、吸气,要求型砂必须干净,否则最易产生气孔。
常用较细的天然粘土砂。
4.粘土型砂的制备
粘土型砂是将原砂、粘土等原材料按照一定配方进入混砂机混制,使之均匀混合,让湿质粘土以薄膜形式包覆于砂粒表面(图1-4)。
混砂质量决定于混砂机型式、加料顺序和混砂时间。
混砂时一般的加料顺序是:
先加原砂、粘土和附加物,干混2~3min后再加入水和液态粘结剂,进行湿混。
混制好的型砂应在不失水的条件下停放一段时间后再使用,有一定回性(或调匀)过程。
原砂细,粘土含量越高的型砂,回性时间应较长。
一般单一砂停放2~3h,面砂停放4~5h。
四、水玻璃砂
水玻璃砂是以水玻璃为粘结剂的一种型砂,广泛用于铸钢件生产。
水玻璃砂依其硬化方式不同可分为“CO2硬化砂”、“自硬砂”和“流态自硬砂”。
(一)水玻璃的特性
铸造用水玻璃是一种粘稠的硅酸钠水溶液,呈碱性,是各种聚硅酸盐水溶液的总称(Na2O·mSiO2·nH2O),具有粘性,并在一定的硬化条件下能转变为凝胶状态,因而可用作型砂和芯砂的粘结剂。
模数和密度是衡量水玻璃性质的两个重要指标,它直接影响水玻璃砂的一系列性能。
1.水玻璃的模数
钠水玻璃中SiO2和Na2O两种物质量之比称为水玻璃模数,用M表示,即
M=
式中
%,
%——分别为硅酸钠中SiO2和Na2O的质量分数。
水玻璃的模数越大,其硬化速度越快,保存性越差,不利于造型。
生产中一般控制水玻璃模数M=2~3来作为型砂中的粘结剂。
如果水玻璃模数不符合要求时,可加入一定的苛性钠或氯化铵来降低或升高水玻璃的模数,其化学反应式如下:
降低模数
mSiO2+2NaOH=Na2O·mSiO2+H2O
提高模数
Na2O·mSiO2+2NH4Cl=mSiO2+2NaCl+2NH3↑+H2O
2.水玻璃的密度
当模数一定时,水玻璃的密度取决于溶解在其中的硅酸钠含量。
硅酸钠含量越高,水玻璃的密度越大。
水玻璃密度可以通过温水稀释或浓缩的方法进行调整。
造型用水玻璃密度一般控制为(1.45~1.6)g/cm3。
(二)水玻璃砂硬化原理及方法
对水玻璃砂铸型吹入CO2气体能够实现铸型快速硬化。
其快速硬化原理在于CO2能与硅酸钠水解产物NaOH反应生成盐和水,促使硅酸溶胶的生成。
其反应式如下:
Na2O·mSiO2+(n+1)H2O=2NaOH+mSiO2·nH2O
2NaOH+CO2=Na2CO3+H2O
mSiO2·nH2O=mSiO2·pH2O+(n-p)H2O
向铸型吹入CO2的方法很多。
生产中广泛采用的是起模前扎气眼吹气或取模后用吹气罩覆盖吹气。
(三)水玻璃砂的配制
通常采用低模数的水玻璃或配砂时加入适量的NaOH以减少粘模性,还可延长型砂的存放时间;加入0.5%~1%的重油或柴油,可以提高型砂的流动性,改善溃散性;加入3%~5%的粘土,可提高湿强度。
水玻璃砂混制工艺如下:
原砂+粘土(干粉)
五、有机粘结剂砂
(一)合脂砂
合脂砂是制皂生产中的残液,是一种粘稠的膏状物,经煤油或汽油稀释后可用作粘结剂。
价格较低,提高其湿强度,可在合脂砂中适量加入糊精、纸浆或粘土。
合脂砂所用原砂较细。
合脂稀释比一般控制在10:
6~10:
10的范围内。
合脂加入量一般为2%~4%,应尽量少加。
过高时会降低湿强度,加重粘膜。
表1-9为有色合金铸件用合脂砂的成分与性能实例。
表1-9有色合金铸件用合脂砂的成分与性能
合脂砂的混制过程:
烘干温度控制在200~240℃,最合适为210±5℃。
烘干时间取决于砂芯尺寸、厚度、合脂加入量、稀释溶剂种类和烘干温度等,一般为1.5~3h。
(二)树脂砂及其制芯工艺
铸造用树脂粘结剂有酚醛树脂、糠醇改性脲醛树脂(呋喃Ⅰ型树脂)。
使用时再另加一定量的固化剂或辅以加热,使之发生化学反应,由线结构的热塑性树脂变为体型结构的热固性树脂。
树脂砂分为壳芯砂、热芯盒树脂砂和自硬树脂砂三类。
1.壳芯法树脂砂及其制芯
用壳芯法制芯可以在壳芯机内生产出表层仅数毫米的砂壳,中部空心,既节约了原材料,又有利于型芯排气。
此法可用来造型和制芯。
该法所配制的型(芯)砂又称为覆膜砂。
制芯时,壳芯砂(覆膜砂)倒入砂斗中,用压缩空气将砂吹入预热至200-280℃的金属芯盒中,靠近芯盒壁的树脂受热固化,保持20-30秒,当结壳厚度达5-15mm时,将砂芯内未能固化的松散树脂砂倒出,就可制取中空型芯。
树脂壳芯砂目前主要用于技术要求较高的成批中、小型砂芯,如汽车变速箱壳体、进、排气管等砂芯。
2.自硬树脂砂
这种砂又称冷硬树脂砂。
用冷硬树脂砂制造的砂芯,强度好,尺寸精度高,工序简化,特别适用于批量小、产品多变和要求较高的航空铸件的生产或其它新产品试制。
冷芯盒树脂砂主要是呋喃改性树脂(如KJN-1型呋喃改性脲醛树脂、7501型呋喃树脂),大部分用于铸造灰铁件和有色合金铸件。
在配制冷硬树脂砂时要用酸来作催化剂,以加快树脂的化学硬化过程。
常用的催化剂有硫酸乙酯和甲苯磺酸(有机酸)、磷酸(无机酸)等。
采用硫酸乙脂,加入量控制在树脂量的30%-40%。
若用磷酸,则控制为树脂量的40%-50%。
3.热芯盒树脂砂
用射芯法制芯通常用热芯盒树脂砂。
它是将树脂砂射入预热到180-260℃的金属芯盒中,经几十秒硬化,就可形成具有一定厚度固化层的砂芯。
砂芯取出后,砂芯余热及其固化反应时的放热,还能使砂芯内部继续硬化。
热芯盒树脂砂所用的粘结剂主要有呋喃Ⅰ、Ⅱ型两种糠醇改性树脂,加入量一般为原砂的(2~3)%(质量分数)。
其固化剂则采用氯化铵和尿素的水溶液(配比:
氯化铵:
尿素:
水=1:
3:
3),其加入量为树脂重的20%左右。
呋喃Ⅱ型树脂属于无氮树脂,芯砂高温性能好,主要用于铸钢件和球铁件砂芯,且铸件不易产生针孔或皮下气孔等缺陷。
加入量为原砂的4%(质量分数)。
采用乌洛托品作固化剂,用量为树脂重的(15~20)%。
这种砂的混制工艺类同于油砂混制。
加料顺序为:
第四节铸造用涂料
一、涂料的作用
具体说来,有以下三方面的作用:
(1)、改善铸件表面质量。
(2)、减少砂型铸造不用涂料易形成的许多缺陷倾向。
(3)、改善铸件局部的表面性能和表层内在质量。
二、优质涂料应具有的性能
优质涂料应具有好的悬浮性、再搅匀性、覆盖能力、密度、粘度、粘结强度、耐火性、低的发气性、涂刷性以及贮存性等,且需原材料丰富,成本低廉。
(1)、悬浮性。
悬浮性即涂料粉末在载液中保持均匀悬浮而不沉淀的能力。
(2)、粘度。
粘度即涂料本身粘性的大小,指涂料受到力作用时将如何形变和流动的性质。
(3)、耐激热性。
耐激热性即金属硬化或干燥后承受高温激热作用而不予开裂和剥落的能力。
三、涂料的基本组成
铸造用涂料通常由耐火粉料、载液、悬浮剂、粘结剂及其它有用添加剂组成。
1.耐火粉料
耐火粉料是涂料的主要组分,其组成质量分数通常高于50%,由耐火材料粉碎而成的细粉。
2.载液体
载液体的作用是承载耐火粉料使之均匀分散或悬浮在载液中,使涂料保持一定粘度和密度,便于喷涂、浸涂、流涂或刷涂到位,不宜过分粘稠或过稀。
常用的载液是水和乙醇。
3.悬浮剂
悬浮剂是稠化载液,形成胶体,促使耐火粉料悬浮,防止沉淀、分层和载液过分渗入砂型(芯)而加入的物质。
水基涂料的悬浮剂有两类:
一类是无机粘结剂,如膨润土,蒙托石等;一类是有机悬浮剂,比如羧甲基纤维素(CMC)、海藻酸钠、聚乙烯醇(PVA)、糖浆等。
当前应用普遍的是膨润土和CMC的复合稠化体系。
醇基涂料较理想的悬浮剂也分两类:
一类是在乙醇中可溶胀的有机膨润土、锂基膨润土、钠基膨润土及改性蒙托石等;另一类是PVB(聚乙烯醇缩丁醛)等。
4.粘结剂
水基涂料,属于低温型的,要加入一定量的水溶性合成树脂、乳白胶、淀粉、干性植物油、纸浆废液等;属于高温型的有钠水玻璃、硅溶胶、聚合磷酸等。
醇基涂料用的粘结剂属于低温型的有松香、漆片(虫胶)、PVB等;属于高温型的有加了六亚甲基四胺的线性酚醛树脂,热固性酚醛树脂、硅酸乙酯等。
5.其它添加剂
为了改善涂料某些性能,常常另外添加少量的添加剂。
四、涂料的配制
涂料的组分和配比依据使用的合金种类和铸型(芯)性质不同而不同。
涂料配制的关键是要保证各种组分达到高度分散,使之具备其所要求的稳定性能。
配制时各组分定量要准,所用容器和设备要清洗干净,有些组分要先行预处理,比如对某些组分先要配制溶液,对膨润土常用水先泡,使其充分溶胀。
复习思考题
1.如何评价铸件综合质量和铸件技术质量?
铸件技术质量分有哪三个等级?
各有何要求?
与工业发达国家相比,目前我国铸造生产还存在哪些差距?
2.铸型接触区是一个什么概念?
金属与铸型接触区有何相互作用?
它们对铸件质量将分别带来什么影响?
3.在砂型(芯)制造中,对造型材料有何基本要求?
湿型砂一般常用哪些原材料混碾而成?
它们是怎样来满足造型材料基本要求的?
4.铸造用原砂主要有几类?
重点说明石英砂、镁砂、铬铁矿砂和锆砂的成分、特性和应用。
5.铸造用粘土的粘结性和可塑性是如何形成的?
目前市场上供应的粘土有哪几种?
请分别说明其成分、性能及其应用?
6.普通粘土和膨润土有何区别?
何谓膨润土的活化处理?
有何实用价值?
说明其活化原理?
7.湿型砂中加入煤粉,渣油等附加物将起何作用?
如何控制其加入量?
8.铸钢用粘土砂与铸铁用粘土砂在性能、成分上有何不同,为什么?
请各举一型砂配方予以对比分析。
9.铸造有色金属用砂有何要求?
为什么在铸造镁合金时必须加入一定量的菱镁矿附加物和硼酸?
它们对铸造质量的保障将起到何种效果?
10.说明水玻璃模数的意义和调节水玻璃模数和密度的措施。
说明水玻璃砂的特性及其应用?
列举一种水玻璃砂配方并分析其原材料的作用及用量控制范围?
11.砂型(芯)制造中,常使用哪几种有机粘结剂?
请对比分析其成分、特性、应用规范和混制工艺(可用表格统计分析)。
12.近代比较广泛地应用三种制芯法配用的树脂砂,请分别说明这三种树脂砂的树脂特性、用量、附加物、硬结原理及制芯工艺规范。
13.铸造用涂料有何作用?
主要由哪些基本组分组成?
各有何功能?
铸造涂料配制时应注意哪些问题?
第二章铸造工艺方案
第一节铸造工艺设计的工作任务和设计依据
一、工作任务
铸造工艺设计的工作任务是要根据铸造零件的结构特点、技术要求、生产批量、交货期限和现有生产条件等,拟定铸件工艺方案和工艺参数,绘制铸造工艺图,编制产品铸造工艺规程或铸造工艺卡,作为生产准备、管理和产品验收的依据,并用于直接指导生产操作和中间检查。
二、设计依据
1.生产任务
接受生产任务时,应予明确:
1)仔细审查图样,确定铸造零件图样清晰无误,有完整的视图、尺寸和各种标记。
2)零件技术要求明确、合理。
铸造材质牌号、金相组织、力学性能要求、铸件尺寸及重量公差、表面和内部缺陷以及其它特殊性能要求。
3)产品数量与生产期限。
2.生产条件
生产条件主要指设备、原材料、企业工人技术水平和模具等工装加工能力等。
1)设备能力。
2)车间原材料的应用情况和供应情况。
3)工人技术水平、生产经验及技术习惯。
4)模样芯盒等工艺装备的加工能力和生产经验。
3.经济性原则
三、设计工作内容和程序
一般包括:
铸造工艺图、铸件图、铸型装配图(合箱图)、工艺卡、操作工艺规程。
铸造工艺图是制造模样、芯盒和指导生产操作的依据。
铸造工艺设计程序如次:
1.看清零件图纸,对零件技术条件和结构进行工艺性分析。
2.拟定铸造工艺方案,包括选择铸造和造型方法;确定铸件在铸型内的浇注位置和分型面;选定各加工面的机械加工余量、起模斜度和收缩率;决定不铸孔。
3.完成砂芯设计。
4.设计浇冒口、冷铁和铸筋。
5.绘制铸造工艺图和铸件图。
6.设计模样、模板、芯盒、等工艺装备,为工装制造提供技术依据。
7.编制铸造工艺卡或产品铸造工艺规程,其中包括对造型、制芯、型(芯)砂配方、混砂、铸造合金熔炼、浇注、开箱清理和热处理等工序在内的整个生产过程的要求。
第二节铸造工艺方案的拟定
一、零件结构的铸造工艺性分析
零件结构的铸造工艺性指零件进行铸造生产的难易程度。
如发现结构设计不合理,应与用户一起商量、研究,在不影响使用要求的前提下,予以更改,便于保证产品质量,简化工艺过程和降低成本。
(一)先做好整体性的了解
首先查对图纸标题栏,了解铸造零件名称,分析工作条件;认定铸件材质,分析力学性能要求;看清本体轮廓尺寸、主要壁厚大小及其分布和重量;阅读技术要求,查对特殊要求和标记。
(二)从壁厚大小、分布及热节布局去审查铸件结构的合理性
1.铸件壁厚是否合理铸件壁厚是否合理,不应太薄也不宜太厚。
铸件太薄会引起冷隔、浇不到等缺陷。
铸件太厚,容易使厚壁中心晶粒粗大,且常出现缩松、缩孔,力学性能反而下降。
设计受力铸件时,可用加强筋结构。
建议采用的加强筋结构形式,如图2-1所示。
图2-1采用加强筋和合理壁厚的铸件结构
a)不合理b)合理
2.铸件内壁应薄于外壁。
铸件内壁和加强筋等,其厚度应薄于外壁,促使内、外壁能均匀冷却,以减小热应力和预防裂纹发生。
3.壁厚力求均匀,减小厚壁部分尺寸,缩小热节。
应取消那些不必要的厚大壁部。
筋与壁的布局应尽可能减少十字交叉,减小热节。
4.铸件壁的连接要求科学合理。
1)采用圆弧连接,圆滑过渡,避免直角相交。
直角相交处在承载时将产生应力集中,且形成热节,处易出现缩孔或缩松。
2)避免锐角交接。
a)b)
3)厚壁与薄壁间的连接提倡逐步过渡,防止壁厚突变。
4)对于轮形铸件(如带轮,齿轮,飞轮等)的轮辐或辐板结构,以奇数轮辐、弯曲轮辐(或S形轮辐)和开孔辐板、弯曲辐板为合理。
5)细长形铸件的横截面力求对称,尽可能采用工字形;大型平板件采用加强筋结构,预防铸件翘曲变形。
6)避免尺寸较大的水平面。
呈水平状态确定浇注位置,可能导致大平面上出现冷隔、气孔、夹渣或浇不到等缺陷。
7)对于铸钢件,审查实现定向凝固的可行性,有利于补缩。
(三)从简化铸造工艺方面去分析或改进零件结构
1.简化外形,改进防碍起模的凸台、凸缘和筋板的结构,取消铸件外表侧凹
图2-11所示变速箱体的外形结构工艺性极差,对此可做如下分析:
①三个凸台低于分型面不利于起模。
②左右侧壁上有3个悬挂吊耳,只有用三个附加砂芯才能成形。
③前、右侧壁均有凹坑,均属妨碍起模的结构;底部凹进深度高,也不便于起模和自带砂芯。
④分型面如图中选用,吊耳外圆和分型面处外圆角均低于分型面,造型很麻烦。
进行了如图2-12的改进。
图2-11结构工艺性极差的变速箱体铸件 图2-12修改后的变速箱体结构
2.审查并改进铸件内腔结构,做到:
1)减少不必要的砂芯,以降低成本,提高铸件精度。
图2-15为用自带型芯(亦称砂垛)替代专制砂芯的实例,减少砂芯数目,降低成本。
图2-15以自带砂芯替代专制砂芯的内腔结构改进
a)-改进前 b)-改进后
2)有利于砂芯固定和排气。
图2-16a为撑架铸件的原结构,2号砂芯呈悬臂式,要用芯撑固定;改进后(图2-16b)。
图2-16撑架铸件结构的改进
a)改进前 b)改进后
3)易于铸件清理。
铸件清理包括清除表面粘砂、内部砂芯(包括芯骨),去除浇冒口和毛刺等。
3.减少和简化分型面,简化模具制造
对于大型复杂件则可采用分体铸造,对于简易小件则可用连体铸造。
图2-18a所示铸件必须选用异面分型,分型面不在一个平面上,增加了制造模样和模板的工作量。
改进后(图2-18b)就不会有这种现象了。
图2-18简化分型面的铸件结构
a)不合理b)合理
对于大而复杂的铸件可考虑分成若干简单铸件分开铸造再行焊接或用螺栓将其连接固定。
例如我国生产第一台12000t水压机曾采用铸焊结构成功地制造出长16960mm、直径1000mm、厚300mm的立柱(中