06管道超声波检测工艺标准解析.docx
《06管道超声波检测工艺标准解析.docx》由会员分享,可在线阅读,更多相关《06管道超声波检测工艺标准解析.docx(28页珍藏版)》请在冰豆网上搜索。
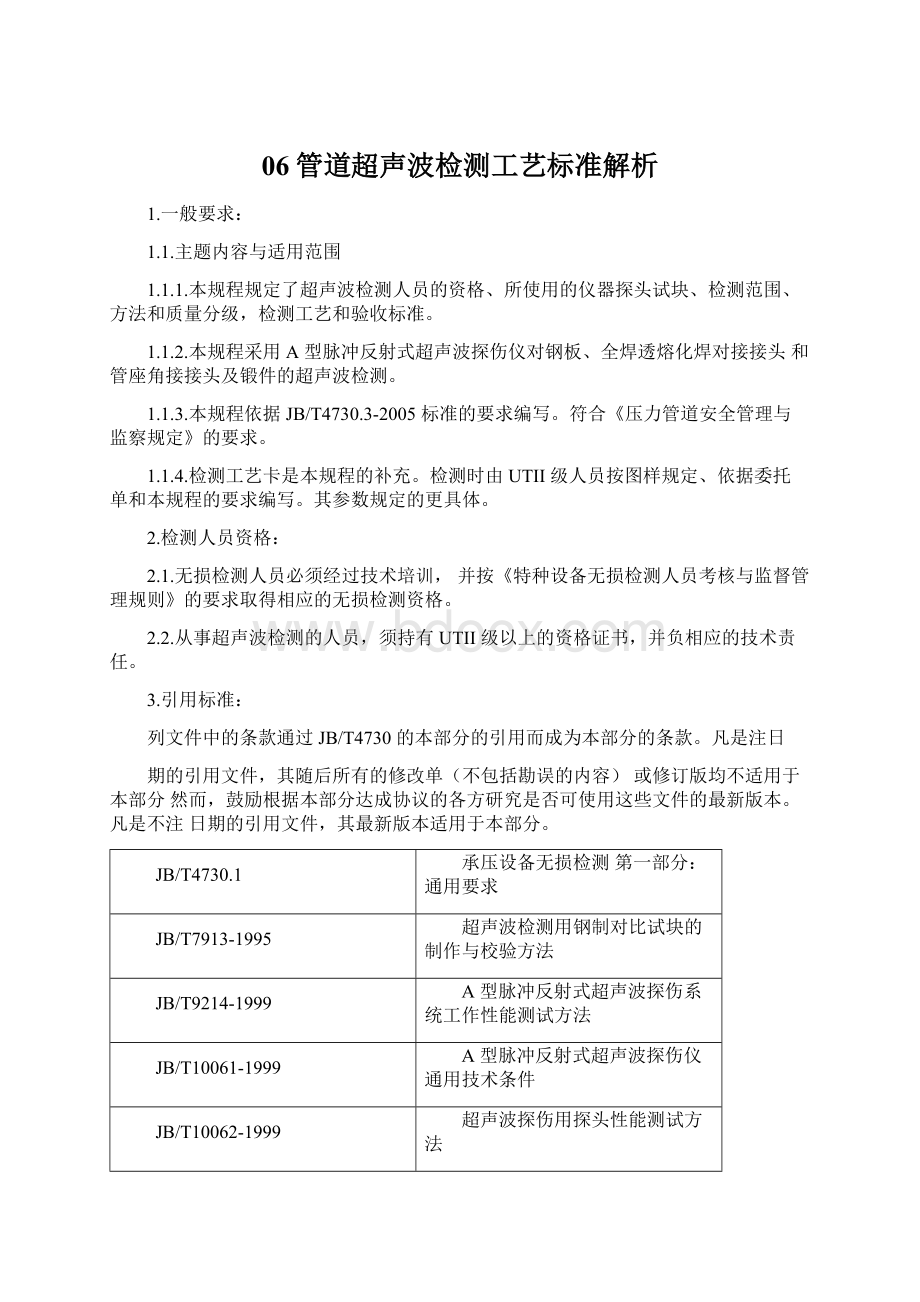
06管道超声波检测工艺标准解析
1.一般要求:
1.1.主题内容与适用范围
1.1.1.本规程规定了超声波检测人员的资格、所使用的仪器探头试块、检测范围、方法和质量分级,检测工艺和验收标准。
1.1.2.本规程采用A型脉冲反射式超声波探伤仪对钢板、全焊透熔化焊对接接头和管座角接接头及锻件的超声波检测。
1.1.3.本规程依据JB/T4730.3-2005标准的要求编写。
符合《压力管道安全管理与监察规定》的要求。
1.1.4.检测工艺卡是本规程的补充。
检测时由UTII级人员按图样规定、依据委托单和本规程的要求编写。
其参数规定的更具体。
2.检测人员资格:
2.1.无损检测人员必须经过技术培训,并按《特种设备无损检测人员考核与监督管理规则》的要求取得相应的无损检测资格。
2.2.从事超声波检测的人员,须持有UTII级以上的资格证书,并负相应的技术责任。
3.引用标准:
列文件中的条款通过JB/T4730的本部分的引用而成为本部分的条款。
凡是注日
期的引用文件,其随后所有的修改单(不包括勘误的内容)或修订版均不适用于本部分然而,鼓励根据本部分达成协议的各方研究是否可使用这些文件的最新版本。
凡是不注日期的引用文件,其最新版本适用于本部分。
JB/T4730.1
承压设备无损检测第一部分:
通用要求
JB/T7913-1995
超声波检测用钢制对比试块的制作与校验方法
JB/T9214-1999
A型脉冲反射式超声波探伤系统工作性能测试方法
JB/T10061-1999
A型脉冲反射式超声波探伤仪通用技术条件
JB/T10062-1999
超声波探伤用探头性能测试方法
JB/T10063-1999
超声波探伤用1号标准试块技术条件
4.探伤仪、探头和系统性能
4.1.探伤仪
4.1.1.探伤仪现采用A型脉冲反射式汕头CTS-22、CTS-26型模拟和北京QKS-958
数字式超声波探伤仪。
4.1.2.探伤仪应满足工作频率范围0.5MHz-10MHz,仪器至少在荧光屏满刻度80%范围内呈线性显示,探伤仪应具有80dB以上的连续可调衰减器,步进级每档不大于2dB,其精度为任意相邻12dB的误差在土1dB以内,最大累积误差不超过1dB。
水平线性误差不大于1%,垂直线性误差不大于5%。
其于指标应符合JB/T10061的规定。
4.2.探头
421.晶片面积一般不应大于500伽2,且任一边长原则上不大于25伽。
4.2.2.单斜探头声束轴线水平偏离角不应大于2%,主声束垂直方向上不应有明显
的双峰。
4.3.探伤仪和探头的系统性能
4.3.1.在达到所探工件的最大检测声程时,其有效灵敏度余量应不小于10dB。
4.3.2.仪器和探头的组合频率与公称频率误差不得大于±10%。
4.3.3.仪器和直探头组合的始脉冲宽度(在基准灵敏度下):
对于频率为5MHz的探头,宽度〉10mm;对于频率为2.5MHz的探头,宽度〉15伽。
4.3.4.直探头的远场分辨力应玄30dB,斜探头的远场分辨力应玄6dB。
4.3.5.探伤议和探头的系统性能应按JB/T9214和JB/T10062的规定进行测试。
5.超声波检测一般方法
5.1.检测前准备;
超声波检测的时机及抽检率等应按《压力管道规范工业管道》GB/T20801-2006
5.1.1.及设计要求执行。
5.1.2.所确定检测面应保证工件受检部分均能得到充分检查。
5.1.3.焊缝表面质量应经外观检查合格,并确认。
不得有影响超声波检测的锈蚀、飞溅和污物,其表面粗糙度应满足检测要求。
表面不规则状态不得影响检测的正确性和完整性,否则应做适当的处理。
5.2.扫查覆盖率:
为确保检测时超声声束能扫查到工件的整个被检区域,探头的每次扫查覆盖率应大于探头直径的15%。
5.3.探头的移动速度:
探头的扫查速度不应超过150mm/s。
5.4.扫查灵敏度:
扫查灵敏度通常不得低于基准灵敏度。
5.5.耦合剂:
采用透声性良好,且不损伤检测面的耦合剂,如机油、浆糊、甘油和水。
5.6.灵敏度补偿:
5.6.1.耦合补偿。
在检测和缺陷定量时,应对由表面粗糙度引起的耦合损失进行补偿。
5.6.2.衰减补偿。
在检测和缺陷定量时,应对材料衰减引起的灵敏度下降和缺陷定量误差进行补偿。
5.6.3.曲面补偿。
对探测面是曲面的工件,应采用曲率半径与工件相同或相近的试块,通过对比试验进行曲率补偿。
6.系统校准和复核
一般要求:
6.1.系统校准应在标准试块上进行,校准时应使探头主声束垂直对准反射体的反射面,以获得稳定和最大的反射信号。
6.2.仪器校准每隔三个月至少对仪器的水平线性和垂直线性进行一次测定,测定方法按JB/T10061的规定执行。
6.3.新购探头的测定新购探头应有探头性能参数说明书,新探头使用前应进行前沿距离、K值、主声束偏离角、灵敏度余量和分辨力等参数的测定。
测定应按JB/T10062的规定进行,并满足其要求。
6.4.检测前仪器和探头系统测定:
641.使用仪器一斜探头系统,检测前应测定前沿距离、K值和主声束偏离,调节
或复核扫描量程和扫查灵敏度。
6.4.2.使用仪器—直探头系统,检测前应测定始脉冲宽度、灵敏度余量和分辨力,调节或复核扫描量程和扫查灵敏度。
6.5.检测过程中仪器和探头系统的复核遇有下述情况应对系统进行复核:
6.5.1.校准后的探头、耦合剂和仪器调节旋钮发生变化时;
6.5.2.检测人员怀疑扫描量程或扫查灵敏度有变化时;
6.5.3.连续工作4h以上时;
6.5.4.工作结束时。
6.6.检测结束前仪器和探头系统的复核
6.6.1.每次检测结束前,应对扫描量程进行复核。
如果任意一点在扫描线上的偏移超过扫描线读数10%,则扫描量程应重新调整,并对上一次复核以来所有的检测部位进行复检。
6.6.2.每次检测结束前,应对扫查灵敏度进行复核。
一般对距离——波幅曲线的校核不少于三点。
如曲线上任何一点幅度下降2dB,则应对上一次复核以来所有的检测部位进行复检;如幅度上升2dB,则应对所有的记录信号进行重新评定。
6.7.校准、复核的有关注意事项校准、复核和对仪器进行线性检测时,任何影响仪器线性的控制器(如抑制或滤波开关等)都应放在“关”的位置或处于最低水平上。
7.试块
7.1.标准试块
7.1.1.标准试块是指本部分规定的用于仪器探头系统性能校准和检测校准的试块,本部分采用的试块有:
(a)钢板用标准试块:
CBI、CBn;
(b)锻件用标准试块:
CSI、CSU、CSH;
(c)焊接接头用标准试块:
CSK-IA、CSK-HA、CSK-IHA;
7.1.2.标准试块应采用与被检工件声学性能相同或相近似的材料制成,该材料用直探头检测时,不得有》©2伽平底孔当量直径的缺陷。
7.1.3.标准试块尺寸精度应符合本部分的要求,并应经计量部门检定合格。
7.14标准试块的其它制造要求应符合JB/T10063和JB/T7913的规定
7.2.对比试块
7.2.1.对比试块是指用于检测校准的试块。
7.2.2.对比试块的外型尺寸应能代表被检工件的特征,试块厚度应与被检工件的厚度相对应。
如果涉及到两种或两种以上不同部件焊接接头的检测,试块的厚度应由其最大厚度来确定。
7.2.3.对比试块反射体的形状、尺寸和数量应符合本部分的规定
8.承压设备用钢板超声波检测和质量分级
8.1.范围
本条适用于板厚为6mm-250m的碳素钢、低合金钢制承压设备用板材的超声波检测和质量分级。
8.2.探头选用
8.2.1.探头选用应按表一的规定执行。
8.2.2.双晶直探头性能应符合JB/T4730-2005附录A(规范性附录)的要求。
表1.承压设备用板材超声检测探头选用
板厚mm
采用探头
公称频率MHz
探头晶片尺寸
6〜20
双晶直探头
5
晶片面积玄150mm
>20〜40
单晶直探头
5
©14mm-©20mm
>40〜250
单晶直探头
2.5
©20mm—©25mm
8.3.标准试块
8.3.1.用双晶直探头检测厚度〉20mm的钢板时,采用如图1所示的CBI标准试块
8.3.2.用单晶直探头检测厚度〉20mm的钢板时CBH标准试块应符合图2和表2
的规定。
试块厚度应与被检钢板厚度相近似。
如经合同双方协商同意,也可采用双晶直
探头进行检测。
表2CBH标准试块mm
试块编号
被检钢板厚度
检测面到平底孔的距离s
试块厚度T
CBH-1
>20-40
15
>20
CBH-2
>40-60
30
>40
CBH-3
>60-100
50
>65
CBH-4
>100-160
90
>110
CBH-5
>160-200
140
>170
CBH-6
>200-250
190
>220
8.4.基准灵敏度
8.4.1.板厚不大于20mm时,用CBI试块将工件等厚部位第一次底波高度调整到
满刻度的50%,再提高10dB作为基准灵敏度。
8.4.2.板厚大于20mm时,应将CBU试块©5平底孔第一次反射波高调整到满刻
度的50%作为基准灵敏度
843.板厚不小于探头的3倍近场区时,也可取钢板无缺陷完好部位的第一次底波
来校准灵敏度,其结果应与8.4.2.的要求相一致。
8.5.检测方法
8.5.1.检测面
可选用钢板的任一扎制表面进行检测。
若检测人员认为需要或设计上有要求时,也可选用钢板的上、下扎制表面分别进行检测。
8.5.2.耦合方式
耦合方式可采用直接接触法或液浸法。
鎬曹
注:
尺寸耀S05血
g
A
40
8X40
卜
5
I
A
◎丄毗
8.5.3.扫查方式
(a)探头沿垂直于钢板压延方向,间距不大于100mm勺平行线进行扫查。
在钢板刨口预定线两侧各50m(当板厚超过100mm寸,以板厚的一半为准)内应作100%3查,扫查示意图见图3。
(b)根据合同、技术协议书或图样的要求,也可采用其它形式的扫查。
8.6.缺陷的测定和记录
8.6.1.在检测过程中,发现下列情况之一即作为缺陷:
(a)缺陷第一次反射波(Fi)波高大于或等于满刻度的50%即Fi>50%
(b)当底面第一次反射波(B)波高未达到满刻度,此时,缺陷第一次反射波(Fi)波高与底面第一次反射波(Bi)波高之比大于或等于50%即BiV100%而Fi/Bi>50%
(c)底面第一次反射波(B)波高低于满刻度的50%即BV50%
8.6.2.缺陷的边界范围或指示长度的测定方法
(a)检出缺陷后,应在它的周围继续进行检测,以确定缺陷的范围。
(b)用双晶直探头确定缺陷的边界范围或指示长度时,探头的移动方向应与探
头的隔声层相垂直,并使缺陷波下降到基准灵敏度条件下荧光屏满刻度的25%或使缺陷
第一次反射波波高与底面第一次反射波波高之比为50%此时,探头中心的移动距离即
为缺陷的指示长度,探头中心即为缺陷的边界点,两种方法测得的结果以较严重者为准。
(c)用单直探头确定缺陷的边界范围或指示长度时,移动探头使缺陷第一次反
射波波高下降到基准灵敏度条件下荧光屏满刻度的25%或使缺陷第一次反射波波高与底
面第一次反射波波高之比为50%此时,探头中心的移动距离即为缺陷的指示长度,探头中心即为缺陷的边界点。
两种方法测得的结果以较严重者为准。
(d)确定8.6.1.(c)中缺陷的边界范围或指示长度时,移动探头使(单直探头
或双晶直探头)底面第一次反射波升高到荧光屏满刻度的50%此时,探头中心的移动
距离即为缺陷的指示长度,探头中心即为缺陷的边界点。
(e)当板厚较薄,确需采用第二次缺陷波和第二次底波来评定缺陷时,基准灵敏度应以相应的第二次反射波来校准。
8.7.缺陷的评定方法
8.7.1.缺陷指示长度的评定规则
单个缺陷按其指示的最大长度作为该缺陷的指示长度。
若单个缺陷的指示长度小于
40mm寸,可不作记录。
8.7.2.单个缺陷的指示面积的评定规则
(a)一个缺陷按其指示的面积作为该缺陷的单个指示面积。
(b)多个缺陷其相邻间距小于100mm或间距小于相邻较小缺陷的指示长度(取其较大值)时,以各个缺陷面积之和作为单个缺陷面积。
(c)指示面积不计的单个缺陷见表3。
i.缺陷面积百分比的评定规则
在任一1mx1m检测面积内,按缺陷面积所占的百分比来确定。
如钢板面积小于1m
xim可按比例折算。
8.8.钢板质量分级
8.8.1.钢板质量分级见表3。
8.8.2.在坡口预定线两侧各50mm(板厚大于100mm时,以板厚的一半为准)内,缺陷的指示长度大于或等于50mm时,应评为V级
表3钢板质量分级
等级
单个缺陷
指示长度
mm
单个缺陷指示长度
2
cm
在任一1mX1m检测面积内存在的
缺陷面积百分比
%
以下单个缺陷指示面积不计
2
cm
I
v80
v25
<3
v9
n
v100
v50
<5
v15
出
v120
v100
<10
v25
IV
v150
v100
<10
v25
V
超过V级者
8.8.3.在检测过程中,检测人员确认钢板中有白点、裂纹等危害性缺陷存在时,应
评为V级
8.9.横波检测
8.9.1.在检测过程中对缺陷有疑问或合同双方技术协议中有规定时,可采用横波检测。
8.9.2.钢板横波检测应按JB/T4730-2005附录B(规范性附录)进行。
9.承压设备用钢锻件超声波检测和质量分级
9.1.范围
本条适用于承压设备用碳钢和低合金钢锻件的超声波检测和质量分级。
本条不适用于奥氏体钢等粗晶材料锻件的超声波检测,也不适用于内外经之比小于
80%勺环形和筒形锻件的周向横波检测。
9.2.探头
双晶直探头的公称频率应选用5MHz探头晶片面积不小于150mm单晶直探头的公称频率应选用2MHz-5MHz探头晶片一般为©14m叶©25mm
9.3.试块应符合7.的规定。
9.3.1.单直探头标准试块
采用CSI试块,其形状和尺寸应符合图4和表4的规定。
如确有需要也可采用其它形式的对比试块。
9.3.2.双晶直探头试块
表4CSII标准试块尺寸mm
试块
序号
孔
径
检测距离L
1
2
3
4
5
6
7
8
9
csn-1
©
5
10
15
20
25
30
35
45
45
csn-2
©
csn-3
©
csn-4
©
(a)工件检测距离小于45mm时,应采用CSII标准试块
(b)工件检测距离小于45mm时,应采用CSII标准试块
(c)CSII试块的形状和尺寸应符合图5和表4的规定。
全部等
933.检测面是曲面是,应采用CSE标准试块来测定由于曲率不同引起的声能损失,其形状和尺寸按图6所示。
9.4.检测时机
Re<6.3卩m
检测原则上应安排在热处理后,孔、台等结构机加工前进行,检测面的表面粗糙度
9.5.检测方法
9.5.1.一般原则
Ah
U
Il1巾巾诵
77
2W
苗
~\'
25
250
锻件应进行纵波检测,对筒型和环型锻件还应增加横波检测。
9.5.2.纵波检测
(a)原则上应从两个相互垂直的方向进行检测,尽可能地检测到锻件的全体积。
主要检测方向如图7所示。
其他形式的锻件也可参照执行。
(b)锻件厚度超过400mm时,应从相对两端进行100%3查
9.5.3.横波检测
钢锻件横波检测应按JB/T4730-2005附录C(规范性附录)的要求进行。
9.6.灵敏度的确定
9.6.1.单直探头基本灵敏度的确定
当被检部位的厚度》探头的3倍近场区长度,且探测面与底面平行时,原则上可
采用底波计算法确定基准灵敏度。
对由于几何形状所限,不能获得底波或壁厚小于探头的3倍近长区时,可直接采用CSI标准试块确定基准灵敏度。
9.6.2.双晶直探头基本灵敏度的确定
使用CSII试块,依次测试一组不同检测距离的©3mm平底孔(至少3个)。
调节衰减器,作出双晶直探头的距离--波幅曲线,并以此作为基准灵敏度。
9.6.3.扫查灵敏度一般不得低于最大检测距离处的©2mm平底孔当量直径。
9.7.工件材质衰减系数的测定
9.7.1.在工件无缺陷完好区域,选取三处检测面与底面平行且有代表性的部位,调
节仪器使第一次底面回波幅度(B1或Bn)为满刻度的50%,
记录此时衰减器的读数,再调节衰减器,使第二次底面回波幅度(B或B)为满刻度的50%两次调节衰减器读数之差即为(B、庄)或(B的dB差值(不考虑底面反射损失)。
9.7.2.衰减系数(Tv3N,且满足希>3N/T,m=2n=按式
(1)计算:
a=[(B-Bm)—6]/2(m-n)T
(1)
式中:
a—衰减系数,dB/m(单程);
(B-Bm)—两次衰减器的读数之差,dB;
T—工件检测厚度,mm
N-单直探头近场区长度,mm
mn—底波反射次数。
9.7.3.衰减系数(T>3N)按式
(2)计算
a=[(B-B2)—6]/2T……
(2)
式中:
(B1-B2)—两次衰减器的读数之差,dB;
其余符号意义同式
(1)。
9.7.4.工件上三处衰减系数的平均值即作为该工件的衰减系数。
9.8.缺陷当量的确定
9.8.1.被检缺陷的深度大于或等于探头的3倍近场区时,采用AVG曲线及计算法确定缺陷当量。
对于3倍近场区内的缺陷,可采用单直探头或双晶直探头的距离-波幅曲线来确定缺陷当量,也可采用其它等效方法来确定。
9.8.2.计算缺陷当量时,若材质衰减系数超过4dB,应考虑修正。
9.9.缺陷记录
9.9.1.记录缺陷当量直径超过©4mm的单个缺陷的波幅和位置。
9.9.2.密集区缺陷:
记录密集区缺陷中最大当量缺陷的位置和缺陷分布。
饼形锻件应记录大于或等于©4mm当量直径的缺陷密集区,其他锻件应记录大于或等于©3mm当量直径的缺陷密集区。
缺陷密集区面积以50mm<50mn!
勺方块作为最小量度
单位,其边界可由6dB法决定。
9.9.3.底波降低量应按表6的要求记录。
表5由缺陷引起底波降低量的质量分级dB
等级
I
n
IV
V
底波降低量
BG/BF
<8
>8〜14
>14〜20
>20〜26
>26
注
:
本表仅适用于声程大于近场区长度的缺陷
9.9.4.衰减系数
9.10.质量分级等级评定
9.10.1.单个缺陷的质量分级见表6。
9.10.2.缺陷引起底波降低量的质量分级见表5。
9.10.3.缺陷密集区质量分级见表7。
9.10.4.表5、表6、和表7的等级应作为独立的等级分别使用
表6单个缺陷的质量分级mm
等级
I
n
IV
V
缺陷当
量直径
w©4
©4+(>
0dB-8dB)
©4+(>
8Db-12dE)
©4+(>
12Db-16dE)
>©
4+16dB
表7密集区缺陷的质量分级
等级
I
n
V
V
密集区缺陷占检测总面积的%
0
>0-5
>5-10
>10-20
>20
9.10.5.当缺陷被检测人员判定为危害性缺陷时,锻件的质量等级为V级。
10.钢制承压设备对接接头超声波检测和质量分级。
10.1.适用范围
10.1.1.本条规定了钢制承压设备对接接头的超声波检测和质量分级。
10.1.2.本条适用于母材厚度为8mm-120mm全熔化焊对接接头的超声波检测。
母材厚度为6mm-8mm全熔化焊对接接头的超声波检测应按JB/T4703-2005附录G(规范性附录)的规定进行。
承压设备有关的支承件和结构件焊接接头的超声波检测也可按本
条的规定进行。
10.1.3.如确有需要,壁厚为4mm-6mm的环向对接接头的超声波检测可参照JB/T4730.3-2005标准,6.1进行。
10.1.4.本条不适用于铸钢件对接接头、外径小于159mm的钢管环向对接接头、内径小于200mm的管座角焊缝的超声波检测,也不适用于外径小于250mm或内外径之比小于80%的纵向对接接头超声波检测。
10.2.超声检测技术等级
10.2.1.超声检测技术等级选择
超声检测技术等级分为A、B、C三个级别。
超声检测技术等级选择应符合制造、安装、在用等有关规范、标准及设计图样规定。
10.2.2.不同检测技术等级的要求
1022.1.“A”级仅适用于母材厚度为8mm-46mm的对接焊接接头。
可用一种K值探头采用直射波法和一次反射波法在对接焊接接头的单面单侧进行检测。
一般不要求进行横向缺陷的检测。
10.2.2.2.“B”级检测:
(a)母材厚度为8mm-46m时,一般用一种K值探头采用直射波法和一次反射波法在对接焊接接头的单面双侧进行检测。
(b)母材厚度大于46mn至120mm寸,一般用一种K值探头采用直射波法在对接焊接接头的双面双侧进行检测,如受几何条件限制,也可在焊接接头的双面单侧或单面双侧采用两种K值探头进行检测。
(c)应进行横向缺陷的检测。
检测时,可在焊接接头两侧边缘使探头与焊接接
头中心线成10°-20°作两个方向的斜平行扫查,见图12。
如焊接接头余高磨平,探头应在焊接接头及热影响区上作两个方向的平行扫查,见图13。
10.2.2.3.“C”级检测
采用C级检测时应将焊接接头的余高磨平,对焊接接头两侧探头扫查经过的母材区域要用直探头进行检测,检测方法见JB/T4730.3-2005标准5.1.4.4。
(a)母材厚度为8mm-46m时,一般用两种K值探头采用直射波法和一次反射波法在焊接接头的单面双侧进行检测。
两种探头的折射角相差应不小于10°,其中一个折射角应为45°。
(b)母材厚度大于46mmi120mm寸,一般用两种K值探头采用直射波法在焊接接头的双面双侧进行检测。
两种探头的折射角相差应不小于10°。
对于单侧坡口角度小于5°的窄间隙焊缝,如有可能应增加对检测与坡口表面平行缺陷的有效检测方法。
(c)应进行横向缺陷的检测。
检测时,将探头放在焊缝及热影响区上两个方向的平行扫查,见图13。
10.3.试块
10.3.1.试块的制作应符合JB/T4730.3-2005标准3.5的规定。
1032.采用的标准试块为CSK-IA、CSK-nA、CSK-川A和CSK