Numeca涡轮级及叶轮流场计算规范要点.docx
《Numeca涡轮级及叶轮流场计算规范要点.docx》由会员分享,可在线阅读,更多相关《Numeca涡轮级及叶轮流场计算规范要点.docx(32页珍藏版)》请在冰豆网上搜索。
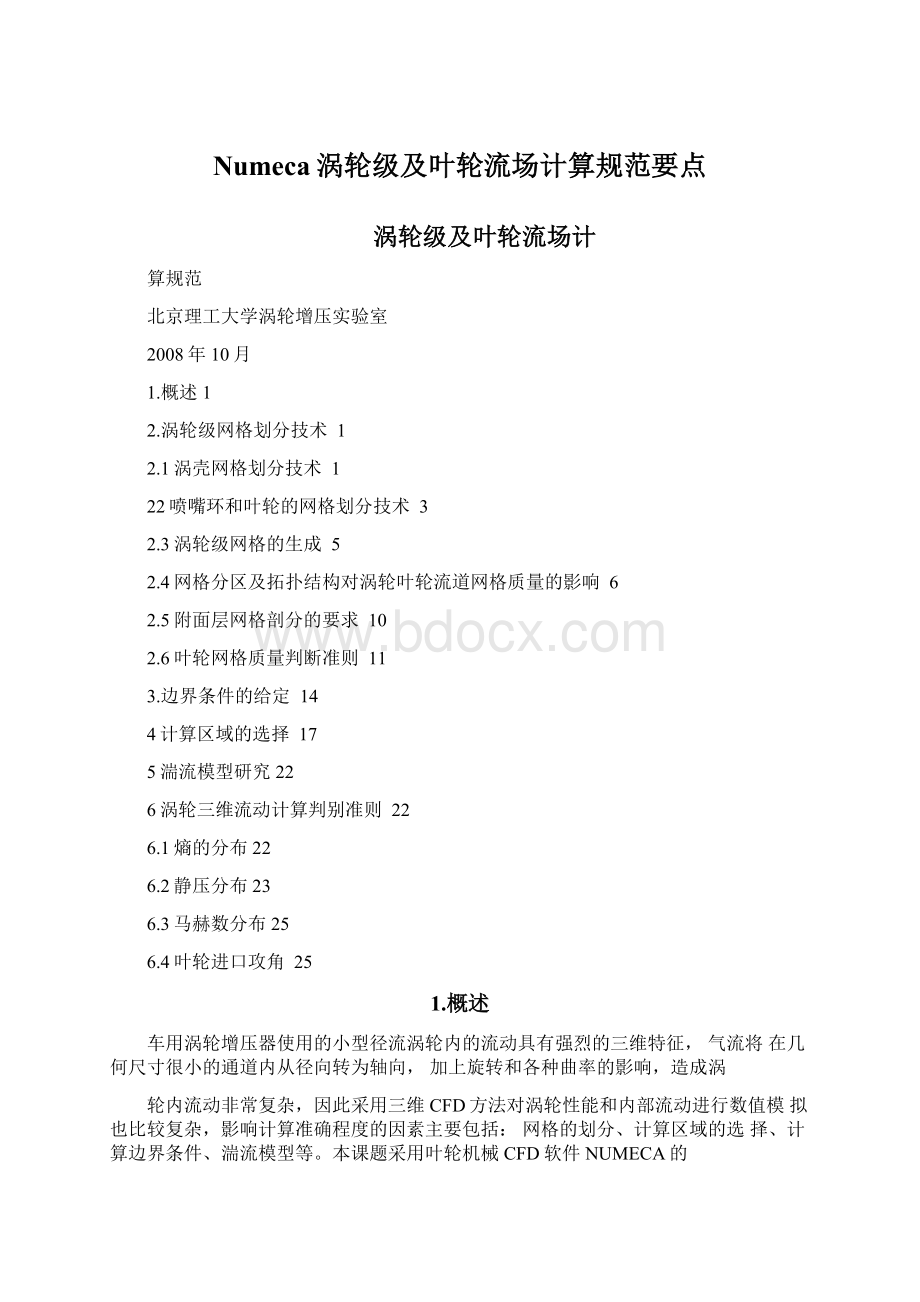
Numeca涡轮级及叶轮流场计算规范要点
涡轮级及叶轮流场计
算规范
北京理工大学涡轮增压实验室
2008年10月
1.概述1
2.涡轮级网格划分技术1
2.1涡壳网格划分技术1
22喷嘴环和叶轮的网格划分技术3
2.3涡轮级网格的生成5
2.4网格分区及拓扑结构对涡轮叶轮流道网格质量的影响6
2.5附面层网格剖分的要求10
2.6叶轮网格质量判断准则11
3.边界条件的给定14
4计算区域的选择17
5湍流模型研究22
6涡轮三维流动计算判别准则22
6.1熵的分布22
6.2静压分布23
6.3马赫数分布25
6.4叶轮进口攻角25
1.概述
车用涡轮增压器使用的小型径流涡轮内的流动具有强烈的三维特征,气流将在几何尺寸很小的通道内从径向转为轴向,加上旋转和各种曲率的影响,造成涡
轮内流动非常复杂,因此采用三维CFD方法对涡轮性能和内部流动进行数值模拟也比较复杂,影响计算准确程度的因素主要包括:
网格的划分、计算区域的选择、计算边界条件、湍流模型等。
本课题采用叶轮机械CFD软件NUMECA的
Fine/turbo软件包,对典型的车用增压器涡轮进行数值计算研究,分析上述因素对涡轮性能的影响,并确定涡轮内部流场的判别准则。
2.涡轮级网格划分技术
一个完整的径流涡轮级包含涡壳、喷嘴环和叶轮,涡轮级的网格划分研究选择JK90S增压器作为研究对象,它是径流有叶涡轮增压器,涡轮的主要几何参数和性能参数如表1所示。
表1JK90S增压器涡轮结构和性能参数
主要结构参数
设计点参数
叶轮进口直径mm
83
压比
2.28
叶轮出口轮缘直径mm
73
入口总温K
730
叶轮出口轮毂直径mm
26
流里kg/s
0.41
叶轮进口叶高mm
16
转速r/min
94000
叶轮轴向宽度mm
25
叶片数
12
涡壳入口面积cm2
34
喷嘴环入口直径mm
112
喷嘴环出口直径mm
91
喷嘴环叶片高度
14
喷嘴环叶片数
15
喷嘴环出口角度
25
涡轮级的网格划分是对涡壳、喷嘴环叶片和叶轮分别划分网格,然后进行整个级的网格生成。
2.1涡壳网格划分技术
JK90S增压器涡轮壳采用双通道梨形360度全周进气,其截面形状如图1所示,截面参数表如表2所示。
图1JK90S涡轮壳流道截面形状
表2JK90S涡壳流道截面尺寸表
截面
0s
30°
60°
90°
120"
150°
Rmm
57
53.5
50.5
47
43.5
40
rmm
11.4
10.7
10.1
9.4
8.7
8
截面
180°
210°
240“
270乜
300°
330°
Rmm
36
32
27.5
22.8
17.5
11.3
rmm
7.2
6.4
5.5
4.56
3.5
2.26
根据涡壳流道的几何尺寸,首先利用三维CAD软件建立涡壳流道的三维模型(如图2所示)。
图2JK90S涡轮涡壳三维模型
涡壳三维模型建立以后,将模型的iges文件输入到Numeca的Fine/turbo软件包中的网格生成模块IGG中划分网格。
由于涡壳流通区域几何形状复杂,在涡壳网格划分时采用分块的措施,即将涡壳流道划分为13个块,其中从入口到
0-0截面为1块,从0—0截面到360度截面按照每30度划分为1个块共计12块。
整个涡壳网格的质量通过对每一块网格质量的控制来达到。
在分别划分各个块网格的过程中,必须注意各个块的网格坐标及坐标方向一致,这是为了保证没有负网格出现。
进行涡壳和过渡段分块时,要保证二者相邻面的网格形状大小相同。
从涡壳入口段至0—0截面,采用蝶形网格。
从0—0截面到360度截面部分,将流道截面分为3部分如图3所示,其中1和2两部分由于形状比较复杂,采用蝶形网格。
最后完成的涡壳网格如图4所示。
涡壳总网格642874,分成14块,最小正交性12.99,最大网格长宽比714.3,最大网格延展比5.10。
图4JK90S涡轮涡壳网格
2.2喷嘴环和叶轮的网格划分技术
JK90S涡轮喷嘴环叶片采用气动叶型,其叶片形状和叶型数据分别见图5和表3。
叶片型线
图5JK90S喷嘴环叶片形状
表3喷嘴环叶片叶型数据
lmm
0
0.26
0.52
1.04
1.56
2.08
3.12
4.16
6.24
bmm
0
0.76:
1.04
1.42
1.67
1.85
2.09
r2.21
2.3
lmm
8.32
10.4
12.48
14.56
16.64
18.72
19.96
bmm
2.25
2.1
1.86
1.55
1.17
0.74
0.49
涡轮叶轮由于无法获得叶片的原始设计数据,因此首先采用三坐标测量测得叶轮的几何数据,然后根据叶轮的测量数据,利用三维CAD软件建立叶轮的几何模型(如图6)。
图6JK90S涡轮叶轮三维模型
喷嘴环叶片和叶轮的网格是利用Fine/turbo软件包中的Autogrid模块生成
的。
模型导入的方法为:
首先根据喷嘴环叶片和叶轮叶片的几何数据,分别建立
喷嘴环叶片的压力面、吸力面数据文件,以及叶轮叶片的压力面、吸力面、叶轮通道轮毂线和轮缘线,然后将它们导入Autogrid中进行网格划分。
在对喷嘴环和叶轮网格的划分过程中,为了研究喷嘴环间隙和叶轮叶背间隙对涡轮性能的影响,划分了3套网格:
第一种情况是不考虑喷嘴环上下两端的间隙,第二种情况是喷嘴环上下两端各加上0.2mm的间隙,第三种情况是在第二
种情况的基础上,再加上1mm的轮盘背面间隙。
叶轮的前缘和尾缘在shroud处给定间隙均为0.6mm。
带喷嘴间隙和叶背间隙的网格图见图7。
图7喷嘴环和叶轮网格的划分
三种情况下的网格质量如下:
第一种情况:
不带喷嘴间隙,总网格数487216,分成12块,最小正交性22.89,最大网格长宽比308.8,最大网格延展比2.6。
第二种情况:
带喷嘴间隙,总网格数555592,分成16块,最小正交性22.89,最大网格长宽比308.8,最大网格延展比2.6。
第三种情况:
带喷嘴间隙和轮背间隙,总网格数613650,分成18块,最小
正交性20.5,最大网格长宽比307.59,最大网格延展比2.6。
2.3涡轮级网格的生成
喷嘴环和叶轮三部分(如
整个涡轮级的CFD计算,计算区域需要包括涡壳、图8所示)。
IGG中生成整个涡轮级
IGG,然后设定转/静叶的
在涡壳、喷嘴环和叶轮的网格划分完成后,需要在的网格。
将已划分好的涡壳、喷嘴环和叶轮网格导入
交接面参数即可。
在涡轮级中存在两个交接面,一个是涡壳与喷嘴环的交接面,另一个是喷嘴环与叶轮的交接面,其中涡壳与喷嘴环之间的交接面设在距涡壳出口3.5mm,而喷嘴环与叶轮的交接面由软件自动设定。
为了使给定边界条件和试验过程中的更接近,在涡壳的入口加了一段直管,最后生成的整个涡轮级网格如图9所示。
图9JK90S涡轮级网格
如前所述带不带喷嘴环间隙、带喷嘴环间隙、带叶轮叶背间隙三种情况下的涡轮级网格情况如下:
第一种情况:
不带喷嘴间隙,总网格数1309916,总共32块,最小正交性
12.99,最大网格长宽比714.3,最大网格延展比5.1。
第二种情况:
带喷嘴间隙,总网格数1378292,总共36块,最小正交性12.99,最大网格长宽比714.3,最大网格延展比5.1。
第三种情况:
带喷嘴间隙和轮背间隙,总网格数1436350,总共38块,最
小正交性12.99,最大网格长宽比714.3,最大网格延展比5.1。
2.4网格分区及拓扑结构对涡轮叶轮流道网格质量的影响
由于涡轮叶轮三维几何形状相对较为复杂,应用结构化网格进行网格划分时,为了保证网格划分的质量并便于控制网格的分布,一般采用分块划分的方式,并以一定的方式将几个块进行连接并可进行数据上的传递。
计算区域内网格块的
划分方法及其连接方式构成了网格的拓扑结构。
拓扑结构的形式对网格的质量有直接的影响,合理的拓扑结构不仅可以提高网格的质量,还可使网格生成的过程简化。
在本节中,将对JK90S涡轮叶轮进行不同拓扑结构形式的网格划分,并进行对比,以选定进行涡轮叶轮网格生成的推荐方法。
网格划分采用的基本拓扑结构采用的是HCH型网格,即叶轮流道共采用5个网格块分区(不考虑叶顶间隙内的网格块),其中四个网格块为H型拓扑结构,叶片前缘上游及尾缘下游各有一个H型网格块,叶片通道之间各有一个H型块,另外一个网格块为C型拓扑结构包络近叶片区域,又称SkinMesh。
所谓SkinMesh结构是指为了保证绕叶片区域的网格质量及分布以满足附面层内流动特征捕捉的需求,将近叶片区域单独进行网格包络式网格划分的结构。
需要指出的是,
由于本节所研究的JK90S涡轮叶轮为钝尾缘结构,因此其SkinMesh的结构为C型,对于非钝尾缘结构(圆形、椭圆形、尖形等),则对应的SkinMesh为O形
结构,完全包络整个叶片,但对总的网格块数目没有影响。
图10为基本的网格
拓补结构和网格参数。
a网格拓扑结构b网格参数
图10网格拓补结构和参数
在HCH基本网格拓补结构的基础上,叶轮内部网格可以采用匹配和非匹配的连接方式,匹配连接方式指相邻两个网格块之间交接网格面上的网格点一一对应,而非匹配连接方式,即两个相邻网格块之间的网格点非一一对应,图11即
为叶轮内部采用匹配和非匹配连接方式的网格形式。
b两个通道之间采用匹配网格情况
图11两种连接方式的涡轮叶轮内部网格
采用以上这两种连接方式的网格拓扑结构,都可以对涡轮叶轮进行正常的网
格分区和网格剖分,并形成最终的三维计算网格,但由于其网格连接方法有所不同,因此最终所生成网格的质量也会有所不同。
以下将主要针对采用这两种不同
拓扑结构所生成的Blade-to-Blade截面网格正交性进行对比分析,以阐述这两种网格拓扑结构的差异及特点。
图12~14给出了三种不同拓扑结构所对应的叶轮0%、50%及100%叶高截面网格单元及网格质量分布图。
左列为对应截面的网格单元及其正交性分布云图,左列柱图为其网格正交性从0-90度对应的网格单元数及占整个截面的网格总数百分比分布。
对于正交性,网格单元的角度越接近90度则说明网格质量越好,
越接近0度则说明网格质量越差。
而图15为采用匹配和非匹配连接方式的叶轮总的网格正交性的分布,可以评价整个叶轮通道内部网格质量。
a非匹配拓扑结构
b匹配拓扑结构
图120%叶高截面网格及其正交性分布
a非匹配拓扑结构
b匹配拓扑结构
图1350%叶高截面网格及其正交性分布
a非匹配拓扑结构
b匹配拓扑结构
图14100%叶高截面网格及其正交性分布
a匹配网格正交性b不匹配网格正交性
图15两种连接方式总的网格正交性分布
由图可以明显看出,采用非匹配连接方式的网格质量可以显著改善叶轮内部的网格质量,表现在:
非匹配连接方式中网格单元正交性角度处于54度以上的
网格明显多于匹配连接方式,在正交性较差的区域(小于36度),非匹配连接方式的网格数量明显少于匹配方式,这说明匹配方式未能很好的控制正交性较差的网格单元数目。
另外,从两种拓扑结构对应的截面上的正交性分布来看,非匹配
连接方式对应的网格正交性分布较均匀,没有出现较大的梯度,而对于匹配连接方式,这种不均匀性明显加剧,这将对后期的计算过程中的差分格式精度造成一定的影响。
基于以上分析,采用SkinMesh形式的网格拓扑结构可以达到相当的网格质量及网格光顺性,并且在采用了非匹配的网格连接方式后,可以大幅度提升网格质量。
因此,涡轮叶轮的网格划分,推荐采用HHCHH(钝尾缘或/与钝前缘结构)结构或者HHOHH结构(非钝尾缘及前缘结构),并在网格的连接方式上米用非匹配连接方式。
2.5附面层网格剖分的要求
对于涡轮内部的三维粘性流动数值模拟,在保证计算网格数目的前提下,所得到的计算结果可信度主要决定于边界层内的流动模拟及损失预测。
而决定边界
层内流动特征模拟精度的最主要因素便是壁面网格的y+及边界层内的网格数目。
为无量刚网格尺度,其定义为:
+严P小
y
yv卩
式中y为实际的网格尺度,"为湍流粘性系数,、为动力粘性系数,「为运动粘性系数,[为工质密度。
图16给出了靠近固体壁面区域的边界层内速度形分布与y+的关系。
由图可
以看出,边界层分为三个子层:
粘性底层、过渡层及对数率层。
由于求解控制方程为雷诺平均Navier-Stokes问题,因此方程组的封闭需要借助与湍流模型。
常用的湍流模型分为低雷诺数模型和高雷诺数模型两类,这两类湍流模型对于边界
层内参数的模拟采用不同的方法。
高雷诺数模型直接应用对数关系式来求解边界层内的参数,没有对粘性底层进行特别处理,,因此对y+的要求比较宽,允许其值在20-50之间,但通过图可以看出,边界层内的分离流动不满足对数律关系,因此高雷诺数湍流模型在边界层内分离流动的捕捉方面存在着缺陷;而低雷诺数
模型求解粘性底层内的流动参数,可以较准确的捕捉边界层内的流动信息,因此
在进行全三维粘性流动数值模拟中推荐使用低雷诺数模型。
由于直接对粘性底层
进行求解,因此要求其y+比较小,应控制在10以下。
而为了达到更准确的粘性底层流动信息的捕捉,应当在粘性底层内布置至少3-5个网格,这就要求近壁面的应该控制在5以下,推荐值为2-3。
根据此推荐的y+值,可以根据下述公式来预测近壁面第一层网格的法向尺寸:
式中ywaii为近壁面第一层网格尺度(即AutoGrid中所要求输入的FirstCellWidth),Vref为参考速度,可取为叶轮尾缘处线速度,'•为工质动力粘性系数,Lref为参考长度,可取为叶轮进口叶尖直径。
图16边界层内速度形分布
需要注意的是,上述公式仅仅为用于预测,实际的壁面y+应当根据最终的三维计算结果输出值为准。
如果三维计算结果输出的y+实际值与推荐的2-3存在较大差别,则可根据差别的比例返回重新修改网格生成过程中的第一层网格尺度,并重新生成网格完成计算。
一般情况下,第一层网格尺度的修正仅需要一次便可以达到满足要求的网格。
2.6叶轮网格质量判断准则
延展比、长宽比,其具体几何
评价网格质量的因素主要包括网格的正交性、含义如下所示:
正交性:
如右图所示,图中对应的实线所构成的区域为一网格单元,该网格单元相邻两条网格边的的夹角表示网格单元的正交性角度,该角度范围为0-90度,如该角度为钝角,这对应的正交性角度为其余角。
该网格单元的最小正交性角度则为角度中最小的角度。
该正交性角度是网格质量中最重要的指标,计算收敛性有着明显的影响,因此应当尽可能的提高计算网格正交性角度。
受实际几何形状等因素的影响,使计算网格正交性角度普遍接近90度无法实现,但对于一个高质量的计算网格而言,应当使得全局网格的最小正交性角度不小于20度,并需尽可能保证大正交性角度的网格占据总网格数的比例。
昨畑血=陛疸型
mrMx,V)
长宽比:
如由图所示,图中a、b、c、d四条边构成一个网格单元。
取任意相邻的两条网格边的均值及另两条相邻边的均值之间的最大值与最小值之比值即为网格的长宽比。
长宽比的大小影响着网格单元的形状,其值越接近1,则网格单元的形状越接近正方形,网格质量越高,对应的计算精度也就越高。
因此,应当尽可能的降低全局网格的长宽比。
但对于全三维粘性湍流计算,为了捕捉边界层内部的流动信息,需要对固体壁面区域进行网格加密以满足边界层内网格数目及分布的要求,因此在限定网格数目的情况下,无法大幅度降低网格的长宽比。
基于此原因,对于粘性网格,应使得全局最大网格长宽比不大于1000,并应使长宽比大于100的网格单元数目比例不高于10%。
延展比:
右图给出了两个相邻的网格单元,每个网格单元有6条网格边构成。
在同一网格方向上,取两相邻网格单元各自的四条网格边的均值中的最大值与最小值的比值即为网格延展比。
由于数值计算过程中,网格单元的参数信息存储在格子中心,两相邻网格的的尺度变化过大会引起网格之间参数信息传递的较大数值误差,因此应当严格控制全局网格延展比。
对于一三维粘性网格,应当限制全局最大网格延展比不大于5,并且应使90%以上的网格单元延展比小于3。
图17给出了JK90S涡轮叶轮的计算网格及三种网格质量判别准则的网格数
目分布图。
由图可以看出,网格正交性最小值为19.34,接近最佳的网格正交性
最小值的标准,且正交性角度大于54度的网格数目占全部网格的93.4%以上;
网格长宽比最大值306,且值小于200的网格数目占据全部网格的99.8%以上;网格延展比最大值2.6,其中延展比小于2的网格数目占全部网格的比例为99.7%以上,完全满足以上所述的计算网格质量要求。
(a)叶轮网格
(b)网格正交性
129.G192.4256.2m
(b)网格长宽比
654W
1LG41.SG2,292.6
(c)网格延展比图17网格质量检查
3.边界条件的给定
涡轮进口的边界条件包括温度、压力和速度。
温度和压力的给定比较简单,分别给定总温和总压即可。
速度的给定需要由涡轮壳进口的方向确定,JK90S增压器涡壳图如图18所示,其进口方向为切线方向,因此进口径向和轴向速度方向为零,只需通过计算点流量、进口气体密度和进口截面积计算出速度大小即可给定。
如果涡壳设计为进口与涡壳中心线有一定角度,需要根据角度计算出切向
和径向的速度分量给定。
图18JK90S涡轮涡壳
涡轮出口的边界条件有两种给定方法:
第一种方法是出口给定质量流量,压力自适应;第二种方法是出口给定平均静压。
为了考察这两种出口边界条件对计算结果的影响,对JK90S涡轮进行了计算研究,计算所选工况为:
喷嘴环叶片角度为25度、相似转速为3200。
计算中保持进口条件一致,按照试验中该相似转速下实测各工况点的参数给定出口静压和流量进行计算。
计算所用网格为喷嘴
环叶片不带间隙,计算结果如图19所示。
图19两种出口边界条件计算结果
从流量-压比图可以看出,出口给定平均静压的计算结果与试验结果更接近。
计算点和试验点相比较,当出口给定质量流量时,对应的工况点质量流量大致相等,而计算点的膨胀比比试验值减小;当出口给定静压时,对应的工况点膨胀比大致相等,而计算点的流量比试验值增大。
由于试验时是采用孔板流量计测量流量,其测量精度受孔板前压力、孔板压差和孔板前温度三个测量量精度的影响,而出口静压测量只受一个测量量精度影响,出口静压的测量精度高于流量测量的精度。
因此出口给定静压的方法可以更好地将计算结果与涡轮特性试验结果进行比较。
两种出口条件对计算收敛特性也有比较大的影响,NUMECA中的收敛标准
一般为:
1)全局残差下降三个数量级以上;每一块中的残差下降三个量级以上;
2)进出口流量出口流量相对误差小于0.5%,且流量不再发生变化。
3)对于有大分离涡的流动(尤其在进出口处),流量收敛曲线会发生振荡,此时由于迭代中分离涡的位置和强度都会发生不同程度的变化,呈现非定常特性,因此流量也会随之发生变化(但这种变化近似为周期性)。
在这种情况下,也可认为计算收敛
4)计算迭代收敛时,流场处每一点处的参数值不再发生变化,或者对于有分离涡情况,涡内某一点的参数应当为周期性变化。
5)对于定常计算,所有的总体性能(效率、转矩、推力等)都应当变为恒定值,不再随迭代步数而发生变化。
对于有大分离的情况,这些参数则会呈现周期性变化,这两种情况下都可认为计算收敛。
对该计算工况线上的4个计算工况点的收敛特性进行了比较,其质量流量和效率的收敛曲线的对比如图20所示,由图可以看出,出口给定质量流量时,计算400多步后,进出口质量流量的误差依然大于0.5%,并且最终的计算结果进出口质量流量并不相等;而出口给定平均静压时,计算200步后,进出口质量流量的误差为0.05%,表明计算结果已经收敛,且进出口流量相等。
从以上的分析可以得出结论:
涡轮的CFD计算出口边界条件采用平均静压,计算更容易收敛,并且计算结果与试验结果对比更可信。
^0^77179
1
创旳电Qi2SDe^newOPtODOMoutO.27828.re5500cycles
iI
massfl&wensrirVoul:
0.929^
I1
Slagfl_Qi_25l&*gi_nfiw_OP1_QClCl_Mu————
mjssfiowenorin/oul:
0.845%
—SIjfle_QI_25P#9_new_&P-Wig.rss=500cyclH
7心4rt甩
i
5Uge_Qi_25D*j_new.OP1wDOO_M-ocH.47Mg.res500*yclei
ii
mm对I脚jan^r口卓静整
ii
in.0471493
&jtgJdiSgll
in0.^0962
in039966B
outD.377603
OUt0.^0307
in:
0.373996
C*l歸
出口给定质量流量的质量收敛曲线
200
300
出口给定平均静压的质量收敛曲线
出口给定质量流量的效率收敛曲线
出口给定平均静压的效率收敛曲线图20两种出口边界条件流量和效率的收敛曲线
4计算区域的选择
对于整个涡轮级,涡轮进口气流分布比较均匀,但在涡轮出口,沿叶高气流参数有较大变化,并且出口气流存在旋流,因此研究涡轮出口计算区域气流参数的变化规律,对于提高计算的准确度有比较重要的意义。
涡轮出口区域的计算研究选择K27型增压器作为研究对象,该增压器涡轮是径流无叶涡轮,涡轮的主要几何尺寸和性能参数如表4所示。
表4K27增压器涡轮结构和性能参数
主要结构参数
设计点参数
叶轮进口直径
mm
76
压比
1.8
叶轮出口轮缘直径mm
64
入口总温K
767
叶轮出口轮毂直径mm
25
流量kg/s
0.235
叶轮进口叶高
mm
11.5
转速r/min
100000
叶轮轴向宽度
mm
25
叶片数
12
涡壳入口面积
cm2
20
涡壳网格和叶轮网格的划分方法和前述JK90S增压器涡轮方法一样,不同的是,为了对涡轮出口后的截面进行计算,因此需要在叶轮出口处接上一段出口段,最终生成的涡轮级网格如图21所示。
图21K27涡轮级计算网格
为了与计算结果比较,进行了K27增压器涡轮的性能试验,试验是