数控车技能考核试题和加工操作规范.docx
《数控车技能考核试题和加工操作规范.docx》由会员分享,可在线阅读,更多相关《数控车技能考核试题和加工操作规范.docx(16页珍藏版)》请在冰豆网上搜索。
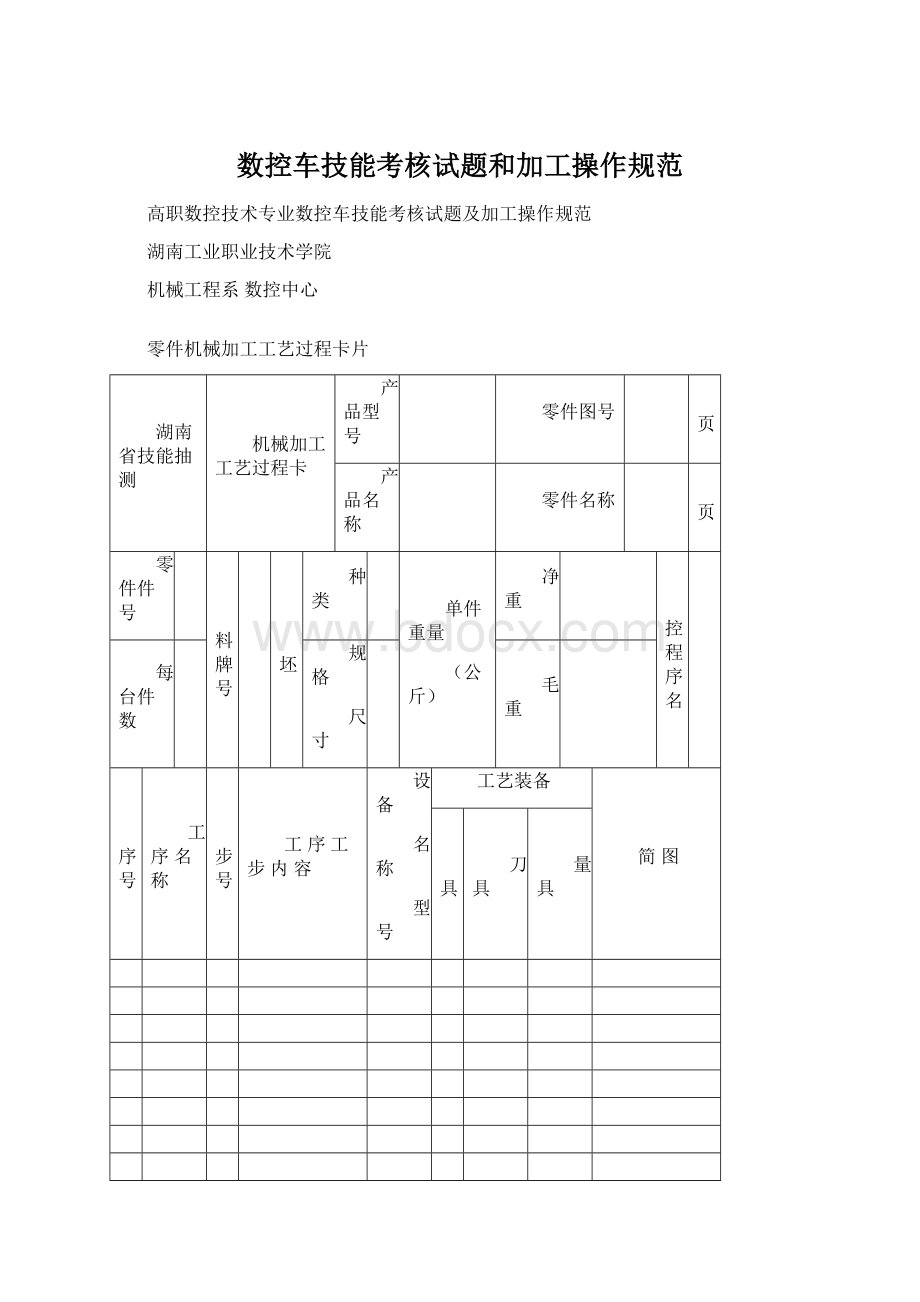
数控车技能考核试题和加工操作规范
高职数控技术专业数控车技能考核试题及加工操作规范
湖南工业职业技术学院
机械工程系数控中心
零件机械加工工艺过程卡片
湖南省技能抽测
机械加工工艺过程卡
产品型号
零件图号
共页
产品名称
零件名称
共页
零件件号
材料牌号
毛坯
种类
单件重量
(公斤)
净重
数控程序名
每台件数
规格
尺寸
毛重
工序号
工序名称
工步号
工序工步内容
设备
名称
型号
工艺装备
简图
夹具
刀具
量具
零件检测评分表
学校名称
姓名
零件名称
数控车零件1
工件编号
序
号
考核
项目
检测位置
配
分
评分标准
检测
结果
扣分
1
形状(10分)
外轮廓
4
外轮廓形状与图形不符,每处扣1分
螺纹
3
螺纹形状与图形不符,每处扣1分
内孔
3
内孔与图形不符,每处扣1分
2
尺寸精度(40分)
Φ34
6
每超差0.01mm扣2分
Φ34
4
每超差0.01mm扣2分
Φ34
4
超差不得分
Φ26±0.2
3
超差不得分
Φ22±0.2
3
超差不得分
螺纹M30×2-6g
5
超差不得分
槽4×3(±0.1)
3
超差不得分
C2(45°±30′)
1
超差不得分
R5±0.5
1
超差不得分
70±0.3
2
超差不得分
35±0.3
2
超差不得分
27±0.2
2
超差不得分
25±0.2
2
超差不得分
20±0.2
1
超差不得分
16±0.2
1
超差不得分
3
表面粗糙度(15分)
Ra1.6
5
降一级不得分
Ra3.2
6
降一级不得分
其余Ra6.3
4
降一级不得分
4
形状位置精度(5分)
同轴度0.03
5
每超差0.01mm扣2分
5
碰伤、划伤
每处扣3-5分。
(只扣分,不得分
合计
70
零件得分
检测老师签字
一、试题分析
1、毛坯确定:
零件最大外径Φ46、长度70,材料45号钢;选用45号钢棒料,毛坯直径尺寸为Φ50mm,长度尺寸为72mm。
2.特征分析:
外圆特征:
台阶、凸圆弧、槽、螺纹、倒角
内圆特征:
台阶
3.尺寸分析:
外圆精度要求较高,尺寸精度以Φ34
为例,尺寸公差范围为0.025mm,容许最大直径尺寸Φ34,最小直径尺寸Φ33.975,其它未标注长度和内径公差按GB01804-m,具体极限偏差见下表。
GB01804尺寸偏差数值表
公差等级
基本尺寸分段
0.5-3
>3-6
>6-30
>30-120
中等m
±0.1
±0.1
±0.2
±0.3
4.形位公差:
右端Φ34外圆处与左端A处Φ36处同轴度要求为Φ0.03;
5.螺纹底径计算:
M30X2-6g:
30代表螺纹最大径;2代表螺纹螺距,用P符号代替;6g代表螺纹公差。
公式:
底径=大径-1.3XP
底径=30-1.3X2=27.4
6.量具准备
0-200游标卡尺;25-50、50-75千分尺;通规、止规。
7.加工经验
加工螺纹M30X2-6g,6g为螺纹大径公差,图纸标注最大径是Φ30,实际加工中为了使螺纹配合更好,利用G71编程切削外圆,在切削螺纹大径直径时编程为Φ29.8mm,使螺纹大径直径减小0.2 mm;螺纹加工以环规检测为准。
二、制定工艺
湖南省技能抽测
机械加工工艺过程卡
产品型号
零件图号
C1
共页
产品名称
零件名称
数控车零件1
共页
零件件号
材料牌号
45
毛坯
种类
棒料
单件重量
(公斤)
净重
数控程序名
O0001
O0002
O0003
O0004
每台件数
规格
尺寸
Φ50X72
毛重
1.16Kg
工序号
工序名称
工步号
工序工步内容
设备
名称
型号
工艺装备
简图
夹具
刀具
量具
1
下料
1
下Φ50X72棒料
锯床
2
热处理
1
调质
3
检验
1
毛坯检验
4
车右端外圆
1
粗精车零件右端部分外圆轮廓至尺寸
数控车CAK6135
三爪卡盘
93°外圆车刀
千分尺
2
加工退刀槽,车削零件右端部分外圆螺纹退刀槽
数控车CAK6135
三爪卡盘
外圆槽刀
游标卡尺
3
螺纹加工,车削零件右端部分外圆螺纹至尺寸
数控车CAK6135
60°外圆螺纹刀
通规止规
5
车左端外圆
1
调头装夹,打表
百分表
2
平端面,控制总长70mm
数控车CAK6135
93°外圆车刀
千分尺
6
3
粗精车零件左端部分外圆轮廓
数控车CAK6135
93°外圆车刀
千分尺
7
检验
1
成品检验
三、刀具选择与切削参数设置
1.刀具选择:
刀具选择根据所要加工的特征选择刀具类型
①外圆特征:
台阶、凸圆弧、倒角:
选择主偏角93°外圆车刀
槽:
选择槽刀,刀宽小于图纸要求的宽度
螺纹:
选择螺纹刀加工,刀尖角度为60°
②内圆特征:
台阶选择:
麻花钻、内镗刀,主偏角93°
麻花钻内镗刀
2.切削参数的选择
表一切削参数的选择
93°外圆车刀
槽刀
螺纹刀
镗刀
粗车转速
500r/min
400r/min
800r/min
500r/min
粗车进给速度
120mm/min
30mm/min
100mm/min
粗车背吃刀量
1mm
见表二
1mm
精车转速
1200r/min
800r/min
精车进给速度
120mm/min
80mm/min
精车背吃刀量
0.3mm
0.3mm
表二螺纹刀的背吃刀量(直径值)
背吃刀量
实际尺寸
第一刀
0.5
第二刀
0.5
第三刀
0.4
第四刀
0.4
第五刀
0.3
第六刀
0.3
第七刀
0.2
第八刀
重复第七刀尺寸
四、对刀和精度补偿
1.对刀:
X轴
①主轴正转,转速600r/min。
②用手轮方式,倍率X10,沿Z轴切削工件外圆,切削距离离工件端面小于10mm,切削深度小于0.5mm。
③用手动方式,使沿Z轴快速退出,移动过程中X轴不允许动,将主轴停止。
④用游标卡尺测量已加工外圆表面,记下测量直径尺寸。
⑤按面板功能键F10切换显示,找到F4刀具补偿功能键,按F1刀具补偿,将光标移动到1号刀补试切直径处,按ENTER键,输入记下测量直径尺寸,再按按ENTER键。
Z轴
①主轴正转,转速600r/min。
②用手轮方式,倍率X10,沿X轴切削工件端面,切削距离离工件端面小于0.5mm,切削深度过零件回转中心位置。
③用手动方式,使沿X轴快速退出,移动过程中Z轴不允许移动,将主轴停止。
④按面板功能键F10切换显示,找到F4刀具补偿功能键,按F1刀具补偿,将光标移动到1号刀补试切长度处,按ENTER键并输入0,再按ENTER键。
2.精度补偿
精度补偿是对已采用试切法对刀的刀具进行精度校验和补偿。
具体操作方法:
①编写校验程序,切削工件,然后测量工件是否达到所要求尺寸,如果有偏差,即对偏差进行补偿。
%0001
T0101
调用1号刀具1号刀具补偿
M03S1000
主轴正转,转速采用精车
G0X53Z3
刀具快速到下刀点位置
G01X49.7F100
移动要切削的X轴位置,切削深度与精车参数一致,这里输入的数值,比我们试切法对刀时候的直径值小0.3mm。
即切削深度为0.3mm。
Z-10
Z轴移动10mm,移动距离够量具测量即可
G0X150Z150
快速将刀具移开工件位置
M05
主轴停止
M30
程序停止并返回程序起始位置
注:
所使用的进给速度,主轴转速,切削深度均为零件精车时所使用的参数,这样才能在精车环境下,测量出正确的加工数值。
公式:
(补偿值)=(程序设定值)-(实际测量值)+(原有磨损尺寸)
②根据程序,程序设定值所要求的尺寸为49.7mm,经过测量实际测量值尺寸为49.76mm,将数值代入公式求补偿值,原有磨损尺寸为默认为0:
补偿值=49.7-49.76+0=-0.06,在对应刀具的X磨损处输入-0.06mm,这样使刀具将未切到的0.06mm切掉。
③验证补偿值是否正确,将程序中的49.7改成49.4,切削深度为0.3mm,与精车时候使用的切削深度参数一致,再一次运行校验程序。
测量工件,如果尺寸为49.4,则刀具精度补偿成功。
如果测量的数值为49.36,比要求的尺寸小了0.04mm,上一步骤输入磨损尺寸为为-0.06:
将数值代入公式求补偿值,补偿值=49.4-49.36+(-0.06)=-0.02
五、数控加工程序编制格式
工序一:
下料
工序三:
平端面,钻通孔
1.将尾座移动到合适位置
2.用MDI方式将主轴转动,转速为400r/min
3.利用Φ18钻花将毛坯钻成通孔
工序五:
外圆轮廓加工(见下图)
最粗实线为卡爪;
虚线方块为毛坯形状;
A→E点为走刀路径;
工步1:
粗精车零件右端部分外圆轮廓至尺寸
1.准备(A点):
在A点我们完成刀具加工零件前的准备工作,包括主轴转动,调用刀具和刀具补偿,冷却液开启。
T0101;
M03S500;
M08;
2.刀具快速移动到循环程序起点(B点):
将刀具从A点快速移动到B点下刀点位置;方法是以对刀建立的工件坐标系为原点,X轴:
毛坯直径+3mm,Z轴:
所加工轮廓Z轴起点坐标+3mm。
此题毛坯为Φ50mm,,X轴下刀点为50+3=53,Z轴为0+3=3。
G0X53Z3
3.编写循环G71,循环中包括几个模块:
①循环主体G71:
G71U1R0.5P1Q1X0.3Z0F120
②刀具移动到需要切削轮廓起点位置(C点)
N1G01X26Z0
③编写所需要加工轮廓形状的程序(C点→D点),D点Z向坐标为-45,实际加工中走刀到-47(E点)这样避免调头车削的时候,产生连接痕迹。
N1G01X29.8Z-2F100S1000
Z-20
X34
Z-35
X46
N2