第五组套筒课程设计说明书.docx
《第五组套筒课程设计说明书.docx》由会员分享,可在线阅读,更多相关《第五组套筒课程设计说明书.docx(21页珍藏版)》请在冰豆网上搜索。
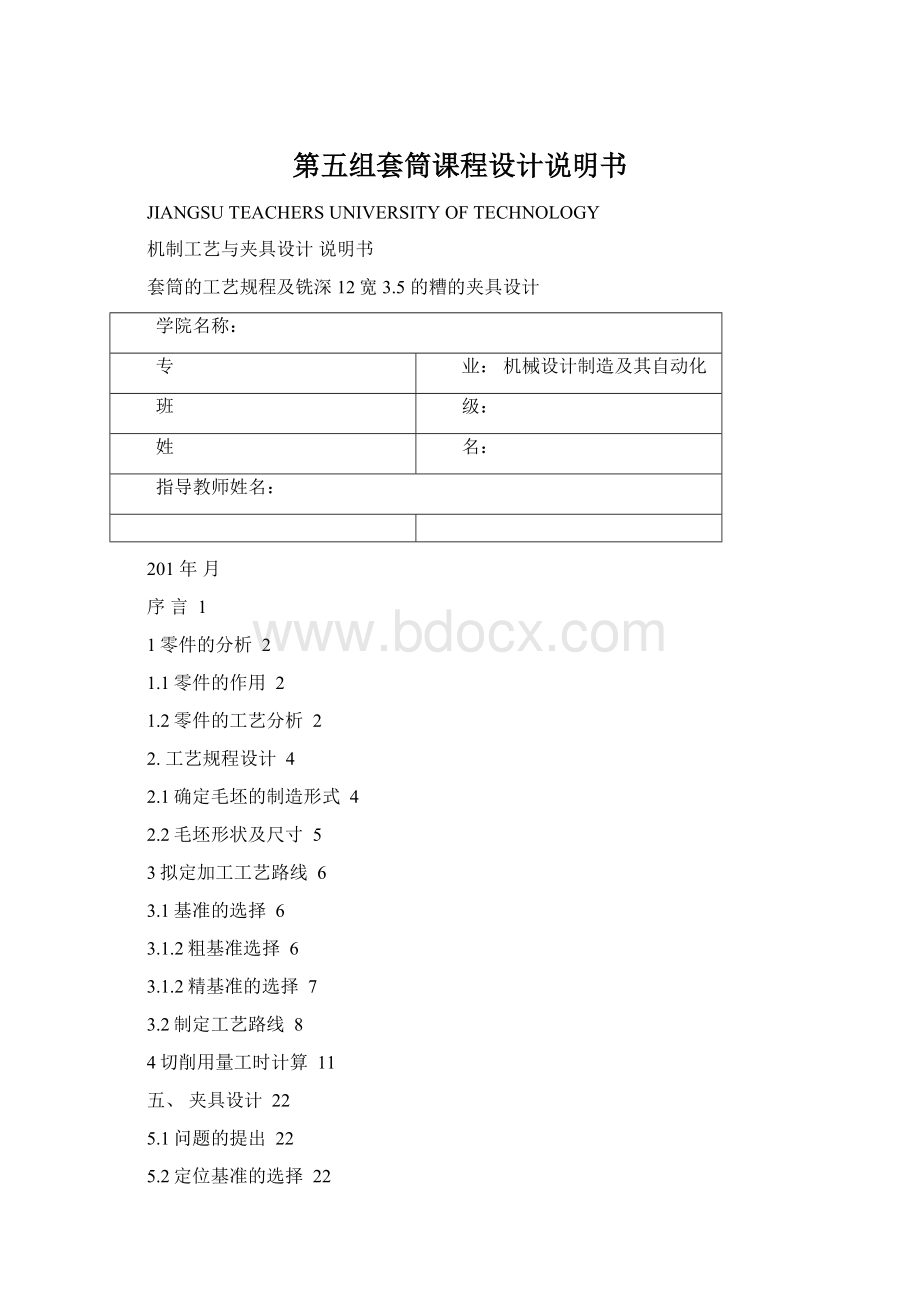
第五组套筒课程设计说明书
JIANGSUTEACHERSUNIVERSITYOFTECHNOLOGY
机制工艺与夹具设计说明书
套筒的工艺规程及铣深12宽3.5的糟的夹具设计
学院名称:
专
业:
机械设计制造及其自动化
班
级:
姓
名:
指导教师姓名:
201年月
序言1
1零件的分析2
1.1零件的作用2
1.2零件的工艺分析2
2.工艺规程设计4
2.1确定毛坯的制造形式4
2.2毛坯形状及尺寸5
3拟定加工工艺路线6
3.1基准的选择6
3.1.2粗基准选择6
3.1.2精基准的选择7
3.2制定工艺路线8
4切削用量工时计算11
五、夹具设计22
5.1问题的提出22
5.2定位基准的选择22
5.3切削力及夹紧力计算23
5.4定位误差分析26
5.5夹具设计及操作简要说明27
总结28
致谢30
参考文献31
机械制造业是制造具有一定形状位置和尺寸的零件和产品,并把它们装备成机械装备的行业。
机械制造业的产品既可以直接供人们使用,也可以为其它行业的生产提供装备,社会上有着各种各样的机械或机械制造业的产品。
我们的生活离不开制造业,因此制造业是国民经济发展的重要行业,是一个国家或地区发展的重要基础及有力支柱。
从某中意义上讲,机械制造水平的高低是衡量一个国家国民经济综合实力和科学技术水平的重要指标。
套筒的加工工艺规程及其铣槽的工装夹具设计是在学完了机械制图、机械制造技术基础、机械设计、机械工程材料等进行课程设计之后的下一个教学环节。
正确地解决一个零件在加工中的定位,夹紧以及工艺路线安排,工艺尺寸确定等问题,并设计出专用夹具,保证零件的加工质量。
本次设计也要培养自己的自学与创新能力。
因此本次设计综合性和实践性强、涉及知识面广。
所以在设计中既要注意基本概念、基本理论,又要注意生产实践的需要,只有将各种理论与生产实践相结合,才能很好的完成本次设计。
本次设计水平有限,其中难免有缺点错误,敬请老师们批评指正。
零件的分析
1.1零件的作用
套筒的作用,待查
1.2零件的工艺分析
工艺分析的目的,一是审查零件的结构形状及尺寸精度、相互位置精度、表面粗糙度、材料及热处理等的技术要求是否合理,是否便于加工和装配;二是通过工艺分析,对零件的工艺要求有进一步的了解,以便制订出合理的工艺规程。
该零件为大量生产的小型零件,在生产时要注意零件的:
1.便于装夹零件的结构应便于加工时的定位和夹紧,装夹次数要少。
2.便于加工零件的结构应尽量采用标准化数值,以便使用标准化刀具和量具。
同时还注意退刀和进刀,易于保证加工精度要求,减少加工面积及难加工表面等。
套筒有3组加工面他们有位置度要求。
套筒的工艺有2组加工面的分别为1,以外圆为基准的加工面,这组加工面包括粗车右端面、φ18
外圆表面至台阶面及φ38外圆表面,钻φ8内孔,粗铰φ8内孔,粗车左端面、φ18外圆表面至台阶面,扩φ12内孔,粗铰φ12内孔
2:
以端面和Φ12孔为基准的加工面,这组加工面主要是半精车右端φ18外圆及台阶面及φ38外圆,倒角,粗铣深槽,粗铣浅槽
2.工艺规程设计
2.1确定毛坯的制造形式
确定毛坯包括选择毛坯类型及其制造方法。
毛坯类型有铸、锻、压制、冲压、焊接、型材和板材等。
确定毛坯时要考虑下列因素:
1)零件的材料及其力学性能。
当零件的材料选定后,毛坯的类型就大致确定了。
例如,材料是铸铁,就选铸造毛坯;材料是钢材,且力学性能要求高时,可选锻件;当力学性能要求较低时,可选型材或铸钢。
2)零件的形状和尺寸。
形状复杂的毛坯,常用铸造方法。
薄壁零件,不可用砂型铸造;尺寸大的铸件宜用砂型铸造;中、小型零件可用较先进的铸造方法。
3)生产类型。
大量生产应选精度和生产率都比较高的毛坯制造方法,用于毛坯制造的昂贵费用可由材料消耗的减少和机械加工费用的降低来补偿。
如铸件应采用金属模机器造型或精密铸造;锻件应采用模锻、冷轧和冷拉型材等。
单件小批生产则应采用木模手工造型或自由锻。
4)生产条件。
确定毛坯必须结合具体生产条件,如现场毛坯制造的实际水平和能力、外协的可能性等。
有条件时,应积极组织地区专业化生产,统一供应毛坯。
5)充分考虑利用新工艺、新技术和新材料的可能性。
目前毛坯制造方面的新工艺、新技术和新材料的发展很快。
例如,精铸、精锻、冷轧、冷挤压、粉末冶金和工程塑料等在机械中的应用日益增加。
应用这些方法后,可大大减少机械加工量,有时甚至可不再进行机械加工,其经济效果非常显著。
套筒零件的材料20钢,20钢的可锻性好,因此可用锻造的方法因为是成批生产,采用模锻的方法生产锻件毛坯,既可以提高生产率,又可以提高精度而且加工余量小等优点。
2.2毛坯形状及尺寸
毛坯的形状及尺寸毛坯的形状和尺寸主要由零件组成表面的形状、结构、尺寸及加工余量等因素确定的,并尽量与零件相接近,以达到减少机械加工的劳动量,力求达到少或无切削加工。
但是,由于现有毛坯制造技术及成本的限制,以及产品零件的加工精度和表面质量要求愈来愈来高,所以,毛坯的某些表面仍需留有一定的加工余量,以便通过机械加工达到零件的技术要求。
毛坯尺寸与零件图样上的尺寸之差称为毛坯余量。
锻件公称尺寸所允许的最大尺寸和最小尺寸之差称为锻件尺寸公差。
毛坯余量与毛坯的尺寸、部位及形状有关。
3拟定加工工艺路线
3.1基准的选择
基面的选择是工艺规程设计中的重要工作之一。
基面选择的正确合理,可以使加工质量得到保证,生产率得到提高。
否则,加工工艺过程中会问题百出。
3.1.2粗基准选择
粗基准选择应当满足以下要求:
(1)粗基准的选择应以加工表面为粗基准。
目的是为了保证加工面与不加工面的相互位置关系精度。
如果工件上表面上有好几个不需加工的表面,则应选择其中与加工表面的相互位置精度要求较高的表面作为粗基准。
以求壁厚均匀、外形对称、少装夹等。
(2)选择加工余量要求均匀的重要表面作为粗基准。
例如:
机床床身导轨面是其余量要求均匀的重要表面。
因而在加工时选择导轨面作为粗基准,加工床身的底面,再以底面作为精基准加工导轨面。
这样就能保证均匀地去掉较少的余量,使表层保留而细致的组织,以增加耐磨性。
(3)应选择加工余量最小的表面作为粗基准。
这样可以保证该面有足够的加工余量。
(4)应尽可能选择平整、光洁、面积足够大的表面作为粗基准,以保证定位准确夹紧可靠。
有浇口、冒口、飞边、毛刺的表面不宜选作粗基准,必要时需经初加工。
(5)粗基准应避免重复使用,因为粗基准的表面大多数是粗糙不规则的。
多次使用难以保证表面间的位置精度。
基准的选择是工艺规程设计中的重要工作之一,他对零件的生产是非常重要的。
先选取外圆和端面为定位基准,利用V型块为定位元件。
3.1.2精基准的选择
精基准的选择应满足以下原则:
1)为了保证零件各个加工面都能分配到足够的加工余量,应选加工余量最小的面为粗基准。
2)为了保证零件上加工面与不加工面的相对位置要求,应选不加工面为粗基准。
当零件上有几个加工面,应选与加工面的相对位置要求高的不加工面为粗基准。
3)为了保证零件上重要表面加工余量均匀,应选重要表面为粗基准。
零件上有些重要工作表面,精度很高,为了达到加工精度要求,在粗加工时就应使其加工余量尽量均匀。
4)为了使定位稳定、可靠,应选毛坯尺寸和位置比较可靠、平整光洁面作粗基准。
作为粗基准的面应无锻造飞边和铸造浇冒口、分型面及毛刺等缺陷,用夹具装夹时,还应使夹具结构简单,操作方便。
5)粗基准应尽量避免重复使用,特别是在同一尺寸方向上只允许装夹使用一次。
因粗基准是毛面,表面粗糙、形状误差大,如果二次装夹使用同一粗基准,两次装夹中加工出的表面就会产生较大的相互位置误差。
以错误!
未找到引用源。
φ12孔为定位精基准,加工其它表
面及孔。
主要考虑精基准重合的问题,当设计基准与工序基准不重合的时候,应该进行尺寸换算,这在以后还要进行专门的计算,在此不再重复。
3.2制定工艺路线
制订工艺路线的出发点,应当是使零件的几何形状、尺寸精度及位置精度等技术要求能得到合理的保证。
通过仔细考虑零件的技术要求后,制定以下两种工艺方案:
铸造
时效
涂底漆
10
车
粗车右端面、φ18外圆表面至台阶面及φ38外圆表面
20
钻
钻φ8内孔
30
铰
粗铰φ8内孔
40
车
粗车左端面、φ18外圆表面至台阶面
50
钻
扩φ12内孔
60
铰
粗铰φ12内孔
70
车
半精车右端φ18外圆及台阶面及φ38外圆,倒角
80
铣
粗铣深槽
90
铣
粗铣浅槽
100
铰
精铰φ8内孔
110
车
半精车左端φ18外圆,车沟槽,倒角
120
车
精车左端φ18外圆,保证粗糙度0.8
130
铰
精铰φ12内孔
140
钻
钻3个沉孔
150
锪
锪3个沉孔
160
铣
精铣深槽,保证表面粗糙度3.2
170
检查
1
锻造
锻造
2
正火
处理
正火处理
3
钻
钻2-Φ7孔
4
车
车R17.25孔
5
铣
铣下端面
6
铣
铣左右端面
7
铣
铣前后端面
8
车
车2-M14螺纹孔
9
钻
钻6xM6螺纹孔
10
钻
钻2xΦ5孔
11
检验
检验
工艺方案一和方案二的区别在于方案二先钻孔,车孔再铣端面,违背了先面后孔的原则,并且工序安排过于简单,不具体,而方案一先粗加工后精加工,工序安排紧凑合理,遵循了安排工艺的基本原则,可以更好地保证了工件的加工精度,综合考虑我们选择方案一。
具体的工艺路线如下
铸造
时效
涂底漆
10
车
粗车右端面、φ18外圆表面至台阶面及φ38外圆表面
20
钻
钻φ8内孔
30
铰
粗铰φ8内孔
40
车
粗车左端面、φ18外圆表面至台阶面
50
钻
扩φ12内孔
60
铰
粗铰φ12内孔
70
车
半精车右端φ18外圆及台阶面及φ38外圆,倒角
80
铣
粗铣深槽
90
铣
粗铣浅槽
100
铰
精铰φ8内孔
110
车
半精车左端φ18外圆,车沟槽,倒角
120
车
精车左端φ18外圆,保证粗糙度0.8
130
铰
精铰φ12内孔
140
钻
钻3个沉孔
150
锪
锪3个沉孔
160
铣
精铣深槽,保证表面粗糙度3.2
170
检查
4零件加工工序设计
4.1粗车右端面、
18外圆表面至台阶面及φ38
外圆表面
1)切削深度单边余量为Z=2mm
2)进给量根据《机械加工工艺手册》取f=0.2mm/r
C
3)计算切削速度vcmCxvykv
T
mxvyvapvfv
其中:
Cv=342,xv=0.15,yv=0.35,m=0.2。
kMv=1.44,ksv=0.8,kkv=1.04,kkrv=0.81
kBv=0.97。
0.151.440.81.040.810.97=96m/min
600.20.30.150.10.35v
4)确定机床主轴转速
ns=1000vc
100096
π38
804r/min
与804r/min相近的机床转速为800r/min。
现选取
nw=800r/min。
所以实际切削速度
dnsπ38800
vc==95.45m/min
c10001000
5)切削工时,按《工艺手册》表6.2-1
tm=ll1l2i=29=0.4833(min)
nwf6000.1
4.2钻φ8内孔
确定进给量f:
根据参考文献Ⅳ表2-7,当钢的
b800MPa,d08mm时,f0.39~0.47m/r。
由于本零件在加工Φ8孔时属于低刚度零件,故进给量应乘以系数0.75,则
f0.39~0.470.750.29~0.35mm/r
根据Z525机床说明书,现取f0.25mm/r
切削速度:
根据参考文献Ⅳ表2-13及表2-14,查得
切削速度v18m/min所以
根据机床说明书,取nw750r/min,故实际切削速度为
切削工时:
l100mm,l19mm,l23mm,则机动工时为
4.3粗铰φ8内孔
根据参考文献Ⅳ表2-25,f0.2~0.4mm/r,
v8~12m/min,得
ns169.8~254.65r/min
查参考文献Ⅴ表4.2-2,按机床实际进给量和实际转速,取f0.35mm/r,nw198r/min,实际切削速度
切削工时:
l100mm,l19mm,l23mm,则机动
v9.33m/min。
工时为
ll1l2nwf
10093
1980.35
4.4粗车左端面、φ18外圆表面至台阶面
1)切削深度单边余量为Z=2mm。
2)进给量根据《机械加工工艺手册》取f=0.2mm/r
C
3)计算切削速度vcmCxvykv
Tapvfv
其中:
Cv=342,xv=0.15,yv=0.35,m=0.2。
kMv=1.44,ksv=0.8,kkv=1.04,kkrv=0.81
kBv=0.97。
所
vc600.20.30.150.10.35v
1.440.81.040.810.97=96m/min
4)
确定机床主轴转速
与1698r/min相近的机床转速为1700r/min。
现选取
nw=1700r/min。
所以实际切削速度
dnsπ181700
vc==96m/min
c10001000
5)切削工时,按《工艺手册》表6.2-1。
ll1l2
tm=12i;其中l=21mm;l1=4mm;l2=0mm;
nwf
lll29
tm=12i=29=0.4833(min)nwf6000.1
4.5扩φ12内孔
根据有关手册规定,扩钻的切削用量可根据钻孔的切削用量选取
f1.2~1.8f钻1.2~1.80.650.75
0.585~0.87mm/r
根据机床说明书,选取f0.57mm/r
v1~1v钻1~1126~4m/min
23钻23
则主轴转速为n51.6~34r/min,并按车床说明书
dwnw12168
v6.33m/min
10001000
切削工时:
l100mm,l16mm,l23mm,则机
动工时为
tmll1l2100631.138minnwf1680.57
4.6粗铰φ12内孔
根据参考文献Ⅳ表2-25,f0.2~0.4mm/r,
v8~12m/min,得
ns169.8~254.65r/min
查参考文献Ⅴ表4.2-2,按机床实际进给量和实际转速,
取f0.35mm/r,nw250r/min,实际切削速度
v12m/min。
切削工时:
l100mm,l19mm,l23mm,则机动工时为
ll1l210093
tm121.245min
4.7半精车右端φ18外圆及台阶面及φ38外圆,
倒角
1)切削深度单边余量为Z=1mm
2)进给量根据《机械加工工艺手册》取f=0.8mm/r
3)计算切削速度
Cv
vcmxvyvkv
Tmaxpvfyv
其中:
Cv=342,xv=0.15,yv=0.35,m=0.2。
修正系数kv见
切削手册》表1.28,即
kMv=1.44,ksv=0.8,kkv=1.04,kkrv=0.81
kBv=0.97。
342
0.20.150.35
600.22.20.80.35v
所以
1.440.81.040.810.97=89m
/min
4)确定机床主轴转速
与753r/min相近的机床转速为750r/min。
现选取
nw=750r/min。
所以实际切削速度vc=dns=πx3875094m/min
5)切削工时,
tm=ll1l2i;其中l=25mm;l1=4mm;l2=0mm;
nwf
tm=ll1l2i=29x2=0.966(min)nwf7500.8
4.8粗铣深槽
1.选择刀具
刀具选取不重磨损硬质合金套式面铣刀,刀片采用YG8,ap1.5mm,d03.5mm,v12m/min,z4。
2.决定铣削用量
1)决定铣削深度因为加工余量不大,一次加工完成ap1.5mm
2)决定每次进给量及切削速度
根据X51型铣床说明书,其功率为为7.5kw,中等系统刚度。
根据表查出fz0.2mm/齿,则
1000v100012
ns1091r/min
sd3.5
按机床标准选取nw=1000r/min
当nw=1000r/min时
fmfzznw0.241000800mm/r
按机床标准选取fm800mm/r
3)计算工时
切削工时:
l12mm,l19mm,l23mm,则机动工时为
4.9粗铣浅槽
切削用量计算同上
计算工时
切削工时:
l1mm,l19mm,l23mm,则机动工时为
ll1l2193tm120.065min
nwf1000x0.2
4.10精铰φ8内孔
切削用量和工时计算同工序30
4.11半精车左端φ18外圆,车沟槽,倒角
切削用量和工时计算同工序40
4.12精车左端φ18外圆,保证粗糙度0.8
切削用量和工时计算同工序40
4.13精铰φ12内孔
切削用量和工时计算同工序60
4.14钻3个沉孔
机床:
Z525立式钻床
刀具:
根据《机械加工工艺手册》表10-61选取高速钢麻花钻Φ4.5
1)进给量
2)切削速度
取f=0.13mm/r
V=24~34m/min.取V=25m/min
3)确定机床主轴转速
ns=1000vc
100025
π4.5
1769r/min
与1769r/min相近的机床转速为1750r/min。
现选取nw=1750r/min。
所以实际切削速度vc=10d0n0s=π41.5000175024.73m/min
5)切削工时,按《工艺手册》表6.2-1
4.15锪3个沉孔
根据有关资料介绍,利用钻头进行扩钻时,其进给量与切削速度与钻同样尺寸的实心孔时的进给量与切削速度之关系为f(1.2~1.8)f钻
11
v(~)v钻
23
式中的f钻、v钻——加工实心孔进的切削用量.
现已知
f钻=0.36mm/r(《切削手册》)表2.7
v钻=42.25m/min(《切削手册》)表2.13
1)给量取f=1.5×0.36=0.51mm/r按机床选取0.5mm/r
2)削速度v=0.4×42.25=16.9m/min.
3)定机床主轴转速
1000vc100016.9
ns=c=633r/min
πdWπ8.5
与633r/min相近的机床转速为600r/min。
现选取
nw=600r/min。
所以实际切削速度
dnsπ8.5600
vc==16m/min
c10001000
5)削工时,按《工艺手册》表6.2-1。
ll1l2
tm=i;其中l=4mm;l1=6mm;l2=0mm;
nwf
m=ll1l2=10=0.072(min)nwf2750.5
4.16精铣深槽,保证表面粗糙度3.2
切削用量工时计算同工序80
4.17检验
五、夹具设计
为了提高劳动生产率,保证加工质量,降低劳动强度,需要设计专用夹具。
由指导老师的分配,决定设计第80道工序粗铣深12,宽3.5的糟的铣床夹具。
5.1问题的提出
在机械制造中,用以装夹工件(和引导刀具)的装置,称为夹具。
它是用来固定加工对象,使之占有正确位置,接受施工或检测的装置。
在机械加工过程中,为了保证加工精度,首先要使工件在机床上占有正确的位置,确定工件在机床上或夹具中占有正确的位置的过程,称为工件的定位。
定位后将其固定,使其在加工过程中始终保持定位位置不变的操作称为夹紧。
工件在机床或夹具上定位、夹紧的过程称为工件的装夹。
用以装夹工件的装置称为机床夹具,简称夹具。
本夹具主要用于粗铣深12,宽3.5的糟,本道工序加工精度要求不高,为此,只考虑如何提高生产效率上,精度则不予考虑。
5.2定位基准的选择
拟定加工路线的第一步是选择定位基准。
定位基准的选择必须合理,否则将直接影响所制定的零件加工工艺规程和最终加工出的零件质量。
基准选择不当往往会增加工序或使工艺路线不合理,或是使夹具设计更加困难甚至达不到零件的加工精度(特别
是位置精度)要求。
因此我们应该根据零件图的技术要求,从保
证零件的加工精度要求出发,合理选择定位基准。
此道工序后面
还有精加工,因此本次铣没有较高的技术要求,也没有较高的平
行度和对称度要求,所以我们应考虑如何提高劳动效率,降低劳
动强度,提高加工精度。
我们采用端面和内孔为定位基准,为了提高加工效率,缩短辅助时间,决定用简单的螺母作为夹紧机构。
5.3切削力及夹紧力计算确定夹紧力就是确定夹紧力的大小、方向和作同点。
在确定夹紧力的三要素时要分析工件的结构特点、加工要求、切削力及其他外力作用于工件的情况,而且必须考虑定位装置的结构形式和布置方式。
夹紧力的三要素对夹紧结构的设计起着决定性的作用。
只有夹紧力的作用点分布合理,大小适当,方向正确才能获得良好的效益。
1.夹紧力方向的确定
(1)夹紧力方向应垂直于主要定位基