《数控加工编程及操作》前三章试题及答案.docx
《《数控加工编程及操作》前三章试题及答案.docx》由会员分享,可在线阅读,更多相关《《数控加工编程及操作》前三章试题及答案.docx(23页珍藏版)》请在冰豆网上搜索。
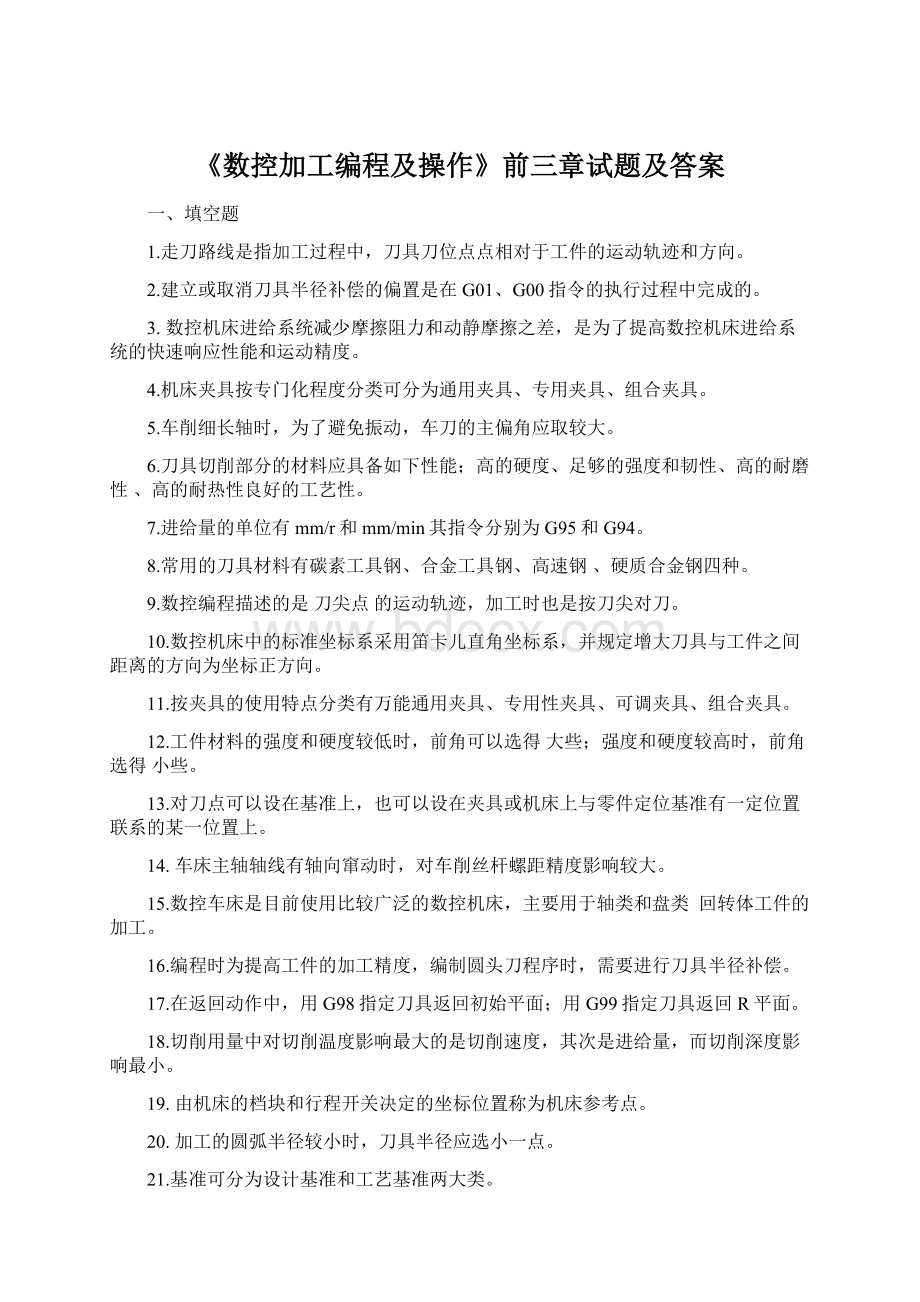
《数控加工编程及操作》前三章试题及答案
一、填空题
1.走刀路线是指加工过程中,刀具刀位点点相对于工件的运动轨迹和方向。
2.建立或取消刀具半径补偿的偏置是在G01、G00指令的执行过程中完成的。
3. 数控机床进给系统减少摩擦阻力和动静摩擦之差,是为了提高数控机床进给系统的快速响应性能和运动精度。
4.机床夹具按专门化程度分类可分为通用夹具、专用夹具、组合夹具。
5.车削细长轴时,为了避免振动,车刀的主偏角应取较大。
6.刀具切削部分的材料应具备如下性能;高的硬度、足够的强度和韧性、高的耐磨性、高的耐热性良好的工艺性。
7.进给量的单位有mm/r和mm/min其指令分别为G95和G94。
8.常用的刀具材料有碳素工具钢、合金工具钢、高速钢、硬质合金钢四种。
9.数控编程描述的是刀尖点的运动轨迹,加工时也是按刀尖对刀。
10.数控机床中的标准坐标系采用笛卡儿直角坐标系,并规定增大刀具与工件之间距离的方向为坐标正方向。
11.按夹具的使用特点分类有万能通用夹具、专用性夹具、可调夹具、组合夹具。
12.工件材料的强度和硬度较低时,前角可以选得大些;强度和硬度较高时,前角选得小些。
13.对刀点可以设在基准上,也可以设在夹具或机床上与零件定位基准有一定位置联系的某一位置上。
14. 车床主轴轴线有轴向窜动时,对车削丝杆螺距精度影响较大。
15.数控车床是目前使用比较广泛的数控机床,主要用于轴类和盘类回转体工件的加工。
16.编程时为提高工件的加工精度,编制圆头刀程序时,需要进行刀具半径补偿。
17.在返回动作中,用G98指定刀具返回初始平面;用G99指定刀具返回R平面。
18.切削用量中对切削温度影响最大的是切削速度,其次是进给量,而切削深度影响最小。
19. 由机床的档块和行程开关决定的坐标位置称为机床参考点。
20. 加工的圆弧半径较小时,刀具半径应选小一点。
21.基准可分为设计基准和工艺基准两大类。
22.切削用量三要素是指是切削速度,进给量,切削深度。
对于不同的加工方法,需要不同的切削用量,并应编入程序单内。
23.数控车床中,加工外圆通常采用机夹可转位车刀。
24.数控机床精度检验主要包括几何精度、定位精度和重复定位精度的检验。
25.数控机床实现插补运算较为成熟并得到广泛应用的是直线插补和圆弧插补。
26.在轮廓控制中,为了保证一定的精度和编程方便,通常需要有刀具长度、半径补偿功能。
27.为了提高加工效率,进刀时,尽量接近工件的切削开始点,切削开始点的确定以不碰撞工件为原则。
28.刀尖圆弧半径补偿有避免少切或过切现象的产生的作用。
二、选择题
1.数控机床切削精度检验(A),对机床几何精度和定位精度的一项综合检验。
(A)又称静态精度检验,是在切削加工条件下;
(B)又称动态精度检验,是在空载条件下;
(C)又称动态精度检验,是在切削加工条件下;
(D)又称静态精度检验,是在空载条件下。
2.大量粗车削外圆车刀之主偏角一般宜选用:
(C)
(A)0;(B)20;(C)30;(D)45度。
3.夹具的制造误差通常应是工件在该工序中允许误差的(B)。
(A)1~3倍;(B)1/3~1/5;
(C)1/10~1/100;(D)等同值。
4.切削用量是指(D)。
(A)切削速度;(B)进给量;
(C)切削深度;(D)三者都是。
5.选择切断车刀刃口宽度,是依被车削工件的(A)而定。
(A)外径;(B)切断深度;
(C)材质;(D)形状。
6.数控机床的F功能常用(B)单位。
(A)m/min;(B)mm/min或mm/r;(C)m/r。
7.在数控机床坐标系中平行机床主轴的直线运动为(C)。
(A)X轴;(B)Y轴;(C)Z轴。
8.程序中指定了(A)时,刀具半径补偿被撤消。
(A)G40;(B)G41;(C)G42。
9.三爪卡盘安装工件,当工件被夹住的定位圆柱表面较长时,可限制工件(B)个自由度。
(A)三;(B)四;(C)五;(D)六。
10.数控车床能进行螺纹加工,其主轴上一定安装了(B)。
(A)测速发电机;(B)脉冲编码器;
(C)温度控制器;(D)光电管。
11.数控系统所规定的最小设定单位就是(C)。
(A)数控机床的运动精度;(B)机床的加工精度;
(C)脉冲当量;(D)数控机床的传动精度。
12.后角较大的车刀,较适合车削何种材质:
(A)。
(A)铝;(B)铸铁;
(C)中碳钢;(D)铜。
13.减小表面粗糙度的方法是(B)。
(A)减少切削速度v;(B)减少转速n;
(C)减少进给量f;(D)减少背吃刀量ap。
14.精细平面时,宜选用的加工条件为(B)。
(A)较大切削速度与较大进给速度;(B)较大切削速度与较小进给速度;
(C)较小切削速度与较大进给速度;(D)较小切削速度与较小进给速度。
15.数控机床主轴以800转/分转速正转时,其指令应是(A)。
(A)M03S800;(B)M04S800;(C)M05S800。
16.执行下列程序后,镗孔深度是(A)。
G90G01G44Z-50H02F100(H02补偿值2.00mm)
(A)48mm;(B)52mm;(C)50mm。
17.用Φ12的刀具进行轮廓的粗、精加工,要求精加工余量为0.4,则粗加工偏移量为(C)。
(A)12.4;(B)11.6;(C)6.4。
18.数控系统的报警大体可以分为操作报警、程序错误报警、驱动报警及系统错误报警,某个程序在运行过程中出现“圆弧端点错误”,这属于(A)。
(A)程序错误报警;(B)操作报警;
(C)驱动报警;(D)系统错误报警。
19.为加工相同材料的工件制作金属切削刀具,一般情况下硬质合金刀具的前角(C)高速钢刀具的前角。
(A)大于;(B)等于;(C)小于;(D)都有可能。
20.车削细长轴时,要用中心架或跟刀架来增加工件的(A)。
(A)刚性;(B)强度;(C)韧性;(D)硬度。
21.G00指令与下列的(C)指令不是同一组的。
(A)G01;(B)G02,G03;(C)G04。
22.刀尖半径左补偿方向的规定是(D)。
(A)沿刀具运动方向看,工件位于刀具左侧;
(B)沿工件运动方向看,工件位于刀具左侧;
(C)沿工件动方向看,刀具位于工件左侧;
(D)沿刀具运动方向看,刀具位于工件左侧。
23.圆弧插补指令G03XYR中,X、Y后的值表示圆弧的(B)。
(A)起点坐标值;
(B)终点坐标值;
(C)圆心坐标相对于起点的。
24.数控机床的运动配置有不同的形式,需要考虑工件与刀具相对运动关系及坐标方向,编写程序时,采用(D)的原则编写程序。
(A)刀具固定不动,工件相对移动;
(B)铣削加工刀具只做转动,工件移动;车削加工时刀具移动,工件转动;
(C)分析机床运动关系后再根据实际情况;
(D)工件固定不动,刀具相对移动。
25.一般钻头的材质是:
(A)
(A)高碳钢;(B)高速钢;(C)高锰钢;(D)碳化物。
26.液压夹头夹持不同材质的工件,其夹持压力应:
(A)
(A)不同;(B)相同;
(C)保持最大压力;(D)任意夹持压力。
27.夹持工件时,下列那项可不予考虑:
(D)
(A)车削方式;(B)进给方向;
(C)工件直径;(D)切削液。
28.车削用量的选择原则是:
粗车时,一般(C),最后确定一个合适的切削速度Vc。
(A)应首先选择尽可能大的吃刀量ap,其次选择较大的进给量f;
(B)应首先选择尽可能小的吃刀量ap,其次选择较大的进给量f;
(C)应首先选择尽可能大的吃刀量ap,其次选择较小的进给量f;
(D)应首先选择尽可能小的吃刀量ap,其次选择较小的进给量f。
29.切削脆性金属材料时,材料的塑性很小,在刀具前角较小、切削厚度较大的情况下,容易产生(A)。
(A)带状切屑;(B)挤裂切屑;
(C)单元切屑;(D)崩碎切屑。
30.车削窄槽时,切槽刀刀片断裂弹出,最可能的原因是:
(C)。
(A)过多的切削液;(B)排屑不良;
(C)车削速度太快;(D)进给量太小。
31.影响数控车床加工精度的因素很多,要提高加工工件的质量,有很多措施,但(A)不能提高加工精度。
(A)将绝对编程改变为增量编程;(B)正确选择车刀类型;
(C)控制刀尖中心高误差;(D)减小刀尖圆弧半径对加工的影响。
32.断屑槽愈(B),愈容易断屑。
(A)窄;(B)宽;(C)深;(D)浅。
33.切断时防止产生振动的措施是(A)。
(A)适当增大前角;(B)减小前角;
(C)增加刀头宽度;(D)减小进给量;
34.数控车床在加工中为了实现对车刀刀尖磨损量的补偿,可沿假设的刀尖方向,在刀尖半径值上,附加一个刀具偏移量,这称为(B)。
(A)刀具位置补偿;(B)刀具半径补偿;(C)刀具长度补偿。
35.钻削时,切削热传出途径中所占比例最大的是:
(B)
A、刀具B、工件C、切屑D、空气介质
36.车削时切削热传出途径中所占比例最大的是:
(C)
A、刀具B、工件C、切屑D、空气介质
37.通过当前的刀位点来设定加工坐标系的原点,不产生机床运动的指令(D)
A、G54B、G53C、G55D、G92
三、判断题
1.直线控制系统和点位控制系统相同,都是保证点到点之间的路径是直线。
(X)
2.判断刀具磨损,可借助观察加工表面之粗糙度及切削的形状、颜色而定。
(V)
3.内孔车刀的刀柄,只要能适用,宜选用柄径较粗的。
(V)
4.切削中,对切削力影响较小的是前角和主偏角。
(X)
6.数控车床的刀具补偿功能有刀尖半径补偿与刀具位置补偿。
(V)
7.恒线速控制的原理是当工件的直径越大,工件转速越慢。
(X)
8.当数控加工程序编制完成后即可进行正式加工。
(X)
9.程序段的顺序号,根据数控系统的不同,在某些系统中可以省略的。
(V)
10.非模态指令只能在本程序段内有效。
(V)
11.数控机床适用于大批量生产。
(X)
12.数控机床的重复定位精度比定位精度高,是为了使加工零件的精度更高。
(X)
13.精车削应选用刀尖半径较大的车刀片。
(X)
14.在数控车床上钻削中心孔时,若钻头静点偏离中心,即无法钻削。
(X)
15.恒线速控制的原理是当工件的直径越大,工件转速越快。
(X)
16.数控机床的编程方式是绝对编程或增量编程。
(X)
17.于XY平面执行圆弧切削的指令,可写成G17G02X_Y_R_F_;。
(V)
18.程序指令G90G28Z5.0;代表Z轴移动5㎜。
(X)
19.工件的六个自由度只有全部被限制,才能保证加工精度。
(X)
20.数控车床当启动电源后,最好作机械回零操作。
(V)
21.在工具磨床上刃磨刀尖能保证切削部分具有正确的几何角度和尺寸精度及较小的表面粗糙度。
(V)
22.数控加工中,最好是同一基准引注尺寸或直接给出主标尺寸。
(X)
23.切削用量中,影响切削温度最大的因素是切削速度。
(V)
24.数控车床适宜加工轮廓形状特别复杂或难于控制尺寸的回转体零件、箱体类零件、精度要求高的回转体类零件、特殊的螺旋类零件等。
(X)
25.一个主程序中只能有一个子程序。
(X)
26.能进行轮廓控制的数控机床,一般也能进行点位控制和直线控制。
(V)
27.刀具前角越大,切屑越不易流出,切削力越大,但刀具的强度越高。
(X)
28.用中等切削速度切削塑性金属时最容易产生积屑瘤。
(V)
29.黄铜硬度低,车削时车刀的前角应选大些。
(V)
30.外圆粗车循环方式适合于加工棒料毛坯除去较大余量的切削。
(V)
31.通常在命名或编程时,不论何种机床,都一律假定工件静止刀具移动。
(V)
32.程序G01X40.0Y20.0F100.0.,刀具进给到(40,20)点,X、Y两轴均以每分钟100㎜的进给率进给。
(X)
33.指令G43、G44、G49为刀具半径左、右补正与消除。
(X)
34.对几何形状不复杂的零件,自动编程的经济性好。
(X)
35.数控车床与普通车床用的可转位车刀有本质的区别,其基本结构、功能特点都是不相同的。
(X)
四、简答题
1.数控加工工序顺序的安排原则是什么?
答:
(1)同一定位装夹方式或用同一把刀具的工序,最好相邻连接完成;
(2)如一次装夹进行多道加工工序时,则应考虑把对工件刚度削弱较小的工序安排在先,以减小加工变形;
(3)道工序应不影响下道工序的定位与装夹;
(4)先内型内腔加工工序,后外形加工工序。
2.数控加工工艺分析的目的是什么?
包括哪些内容?
答:
在数控机床上加工零件,首先应根据零件图样进行工艺分析、处理,编制数控加工工艺,然后再能编制加工程序。
整个加工过程是自动的。
它包括的内容有机床的切削用量、工步的安排、进给路线、加工余量及刀具的尺寸和型号等。
3.车削圆柱形工件时,圆柱形工件的锥度缺陷与机床的哪些因素有关?
答;造成工件产生锥度缺陷的有关的因素有:
(1)溜板移动相对主轴轴线的平行度超差;
(2)床身导轨面严重磨损;
(3)工件装夹在两顶尖间加工时,由于尾座轴线与主轴轴线不重合而产生锥度;
(4)地脚螺栓松动,使机床水平发生变动。
4.数控机床加工与普通机床加工相比有何特点?
(1)数控加工工艺内容要求更加具体、详细;
(2)数控加工工艺要求更严密、精确;
(3)数控加工的工序相对集中。
5.什么叫粗、精加工分开?
它有什么优点?
答:
在确定零件的工艺流程时,应将粗精加工分阶段进行,各表面的粗加工结束后再进行精加工,尽可能不要将粗、精加工交叉进行,也不要在到机床上既进行粗加工以进行精加工,这就是粗精加工分开。
这样加工可以合理使用机床,并使粗加工时产生的变形及误差在精加工时得修正,有利于提高加工精度,此外,还可提早发现裂纹、气孔等毛坯缺陷,及时终止加工。
6.何谓机床坐标系和工件坐标系?
其主要区别是什么?
答:
机床坐标系又称机械坐标系,是机床运动部件的进给运动坐标系,其坐标轴及方向按标准规定。
其坐标原点由厂家设定,称为机床原点(或零件)。
工件坐标又称编程坐标系,供编程用。
7.在数控加工中,一般固定循环由哪6个顺序动作构成?
答:
固定循环由以下6个顺序动作组成:
①X、Y轴定位;
②快速运动到R点(参考点);
③孔加工;④在孔底的动作;
⑤退回到R点(参考点);
⑥快速返回到初始点。
8.刀具切削部分的材料包括什么?
答;目前用于制造刀具的材料可分为金属材料和非金属材料两大类:
金属材料有碳素工具钢、合金工具钢、高速硬质合金。
非金属材料有人造金刚石和立方氮化硼及陶瓷。
其中碳素工具钢和合金工具钢的红硬性能较差(约200°C~400°C),已很少用来制造车刀。
9.采用夹具装夹工件有何优点?
答:
由于夹具的定位元件与刀具及机床运动的相对位置可以事先调整,因此加工一批零件时采用夹具工件,即不必逐个找正,又快速方便,且有很高的重复精度,能保证工件的加工要求。
10.简述刀位点、换刀点和工件坐标原点。
答:
(1)刀位点是指确定刀具位置的基准点;
(2)带有多刀加工的数控机床,在加工过程中如需换刀,编程时还要设一个换刀点;换刀点是转换刀具位置的基准点。
换刀点位置的确定应该不产生干涉;
(3)工件坐标系的原点也称为工件零点或编程零点,其位置由编程者设定,一般设在工件的设计、工艺基准处,便于尺寸计算。
11.按照基准统一原则选用精基准有何优点?
答:
按此原则所选用的精基准,能用于多个表面的加工及多个工序加工,可以减少因基准变换带来的误差,提高加工精度。
此外,还可减少夹具的类型,减少设计夹具的工作量。
12.什么叫车床的几何精度和工作精度?
答:
(1)机床的几何精度是指机床某些基础零件本身的几何形状精度、相互位置的几何精度、其相对运动的几何精度。
(2)机床的工作精度是指机床在运动状态和切削力作用下的精度。
机床在工作状态下的精度反映在加工后零件的精度上。
13数控车床的编程特点。
答:
(1)在一个程序段中,根据图样上标注的尺寸可以釆用绝对编程的相对值编程,也可混合使用;
(2)被加工零件的径向尺寸在图样上测量时,一般用直径值表示,所以釆用直径尺寸编程更为方便;
(3)由于车削加工常用棒料作为毛坯,加工余量较大,为简化编程,常釆用不同形式的固定循环;
(4)编程时把车刀刀尖认为是一个点;
(5)为了提高加工效率,车削加工的进刀与退刀都釆用快速运动。
14、数控机床的机床坐标系与工件坐标系的含义是什么?
答:
(1)机床坐标系是机床固有的坐标系,机床坐标系的原点也称为机床原点或机床零点在机床经过设计制造和调整后这个原点便被确定下来,它是固定的点。
数控装置上电时并不知道机床零点每个坐标轴的机械行程是由最大和最小限位开关来限定的;
(2)工件坐标系是编程人员在编程时使用的,编程人员选择工件上的某一已知点为原点称编程原点或工件原点工件坐标系一旦建立便一直有效直到被新的工件坐标系所取代。
15、为什么要进行刀具长度补偿?
答:
数控车床的刀具装在回转刀架上,加工中心、数控镗铣床、数控钻床等刀具装在主轴上,由于刀具长度不同,装刀后刀尖所在位置不同,即使是同一把刀具,由于磨损、重磨变短,重装后刀尖位置也会发生变化。
如果要用不同的刀具加工同一工件,确定刀尖位置是十分重要的。
为了解决这一问题,我们把刀尖位置都设在同一基准上,一般刀尖基准是刀柄测量线(或是装在主轴上的刀具使用主轴前端面,装在刀架上的刀具可以是刀架前端面)。
编程时不用考虑实际刀具的长度偏差,只以这个基准进行编程,而刀尖的实际位置由G43、G44来修正。
五、编程题
1.编制简单回转零件(如图所示)的车削加工程序,包括粗精车端面、外圆、倒角、倒圆。
零件加工的单边余量为2mm,其左端面25mm为夹紧用。
%1406
N0010T0101M03S500
N0020G00X100Z10
N0030G81X0Z1F80
N0040X0Z0.4
N0050X0Z0F60
N0060G73U2W2R2P10Q20X0.4Z0.1F150
N0070N10G01X44Z2F80
N0080X50Z-1
N0090Z-57
N0100G02X56Z-60R3
N0110G01X88
N0120Z-85
N0130G00X100Z120
N0140M05
N0150M02
零件加工的单边余量为2mm,其左端面25mm为夹紧用。
2、在华中世纪星系统数控车床上加工下图所示零件,材料PC棒,请编辑该零件的加工程序刀具:
1号外圆刀;2号螺纹刀;3号切断刀;4号内孔刀。
O0001
N010 G92G90X25Z0
N020 G00X40Z90
N030 M06T0101
N040 M03S600F100
N050 G00X30Z2
N060 G71P070Q170U2R2X0.4Z0.2F100
N070 G00X27Z2
N080 G01X16Z0C-2
N090 Z-20
N100 X20C-2
N110 Z-40
N120 G04X2
N130 X15Z-50
N140 G02X25Z-65R20
N150 G01Z-80
N160 G04X2
N170 G00X30
N180 X40Z90
N190 G70P070Q170
N200 G00X40Z90T0100
N210 M06T0303
N220 G00X30
N230 Z-20
N240 G01X12F10
N250 G04X2
N260 G00X30
N270 X40Z90T0300
N280 M06T0202
N290 G00X16Z2
N300 G82X15.2Z-18F1.5
N310 G82X14.6Z-18F1.5
N320 G82X14.2Z-18F1.5
N330 G82X14.04Z-18F1.5
N340 G00X30
N350 X40Z90T0200
N360 M05
N370 M02
3、加工形状如图所示的零件,采用手工编程方法。
以西门子802S数控系统,应进行如下操作。
图1零件图
(1)确定加工路线
按先主后次,先精后粗的加工原则确定加工路线,采用固定循环指令对外轮廓进行粗加工,再精加工,然后车退刀槽,最后加工螺纹。
(2)装夹方法和对刀点的选择
采用三爪自定心卡盘自定心夹紧,对刀点选在工件的右端面与回转轴线的交点。
(3)选择刀具
根据加工要求,选用四把刀,1号为粗加工外圆车刀,2号为精加工外圆车刀,3号为切槽刀,4号为车螺纹刀。
采用试切法对刀,对刀的同时把端面加工出来。
(4)确定切削用量
车外圆,粗车主轴转速为500r/min,进给速度为0.3mm/r,精车主轴转速为800r/min,进给速度为0.08mm/r,切槽和车螺纹时,主轴转速为300r/min,进给速度为0.1mm/r。
(5)程序编制
确定轴心线与球头中心的交点为编程原点,零件的加工程序如下:
主程序
JXCP1.MPF
N05G90G95G00X80Z100 (换刀点)
N10T1D1M03S500M08 (外圆粗车刀)
-CNAME=“L01”
R105=1R106=0.25R108=1.5 (设置坯料切削循环参数)
R109=7R110=2R111=0.3R112=0.08
N15LCYC95 (调用坯料切削循环粗加工)
N20G00X80Z100M05M09
N25M00
N30T2D1M03S800M08 (外圆精车刀)
N35R105=5 (设置坯料切削循环参数)
N40LCYC95 (调用坯料切削循环精加工)
N45G00X80Z100M05M09
N50M00
N55T3D1M03S300M08 (切槽车刀,刀宽4mm)
N60G00X37Z-23
N65G01X26F0.1
N70G01X37
N75G01Z-22
N80G0