橡胶工艺答案副本.docx
《橡胶工艺答案副本.docx》由会员分享,可在线阅读,更多相关《橡胶工艺答案副本.docx(17页珍藏版)》请在冰豆网上搜索。
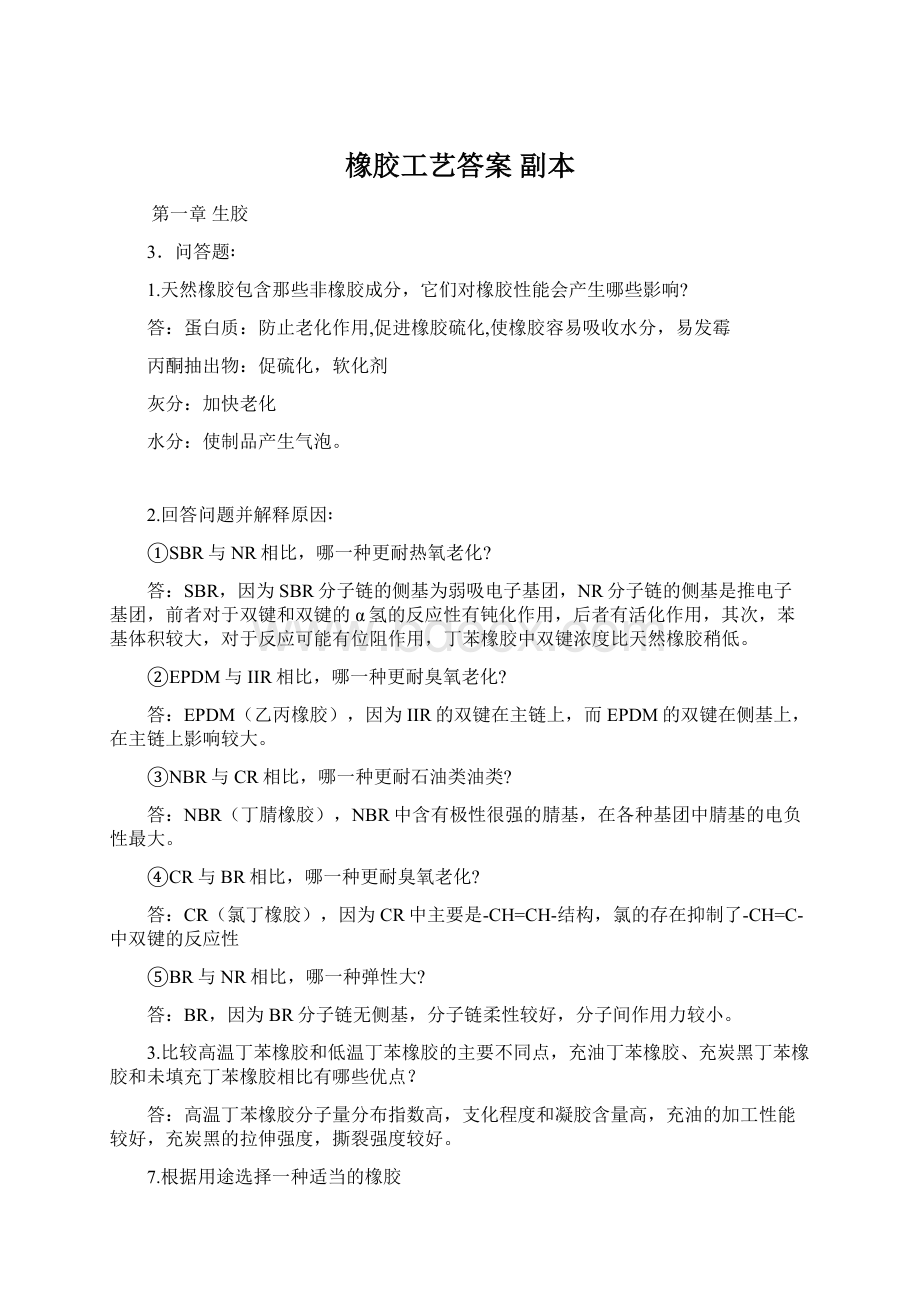
橡胶工艺答案副本
第一章生胶
3.问答题∶
1.天然橡胶包含那些非橡胶成分,它们对橡胶性能会产生哪些影响?
答:
蛋白质:
防止老化作用,促进橡胶硫化,使橡胶容易吸收水分,易发霉
丙酮抽出物:
促硫化,软化剂
灰分:
加快老化
水分:
使制品产生气泡。
2.回答问题并解释原因∶
①SBR与NR相比,哪一种更耐热氧老化?
答:
SBR,因为SBR分子链的侧基为弱吸电子基团,NR分子链的侧基是推电子基团,前者对于双键和双键的α氢的反应性有钝化作用,后者有活化作用,其次,苯基体积较大,对于反应可能有位阻作用,丁苯橡胶中双键浓度比天然橡胶稍低。
②EPDM与IIR相比,哪一种更耐臭氧老化?
答:
EPDM(乙丙橡胶),因为IIR的双键在主链上,而EPDM的双键在侧基上,在主链上影响较大。
③NBR与CR相比,哪一种更耐石油类油类?
答:
NBR(丁腈橡胶),NBR中含有极性很强的腈基,在各种基团中腈基的电负性最大。
④CR与BR相比,哪一种更耐臭氧老化?
答:
CR(氯丁橡胶),因为CR中主要是-CH=CH-结构,氯的存在抑制了-CH=C-中双键的反应性
⑤BR与NR相比,哪一种弹性大?
答:
BR,因为BR分子链无侧基,分子链柔性较好,分子间作用力较小。
3.比较高温丁苯橡胶和低温丁苯橡胶的主要不同点,充油丁苯橡胶、充炭黑丁苯橡胶和未填充丁苯橡胶相比有哪些优点?
答:
高温丁苯橡胶分子量分布指数高,支化程度和凝胶含量高,充油的加工性能较好,充炭黑的拉伸强度,撕裂强度较好。
7.根据用途选择一种适当的橡胶
①制造水胎或硫化胶囊------乙丙橡胶
②制造内胎------丁基橡胶
③制造耐230℃在石油介质中连续工作的密封件------氟橡胶
④具有一定阻燃性、机械强度较高、耐酸碱的运输带覆盖胶------氯丁橡胶
8.试比较一下NR、SBR和BR的弹性、耐老化性与硫磺反应性等有何差异?
并从化学结构上加以解释。
答:
弹性比较:
BR>NR>SBR,因为BR主链上无侧基,NR主链上有侧甲基,SBR侧基是苯基及乙烯基,分子链柔顺性BR>NR>SBR
耐老性比较:
SBR>BR>NR,因为NR主链上侧基是推电子基团,SBR侧基是弱吸电子基团,前者对于双键及双键α氢有活化作用,后者有钝化作用,BR无侧基,介于两者之间。
硫磺反应性比较:
NR>BR>SBR,因为NR主链上侧基是推电子基团,SBR侧基是弱吸电子基团,前者对于双键及双键α氢有活化作用,后者有钝化作用,BR无侧基,介于两者之间。
13.什么是再生胶?
橡胶再生过程的实质是什么?
再生胶有何用途?
答:
再生胶的定义:
由废旧橡胶制品和硫化胶的边角废料、经粉碎、脱硫等加工处理制得的具有塑性和粘性的材料。
实质:
橡胶的再生是废胶在增塑剂(软化剂和活化剂)、氧、热和机械剪切的综合作用下,部分分子链和交联点发生断裂的过程。
应用:
(1)在轮胎工业中,再生胶主要用于制造垫带,另外也可用于外胎中的钢丝胶、三角胶条以及小型轮胎、力车胎中等。
(2)在工业用橡胶制品中也有应用,如胶管、胶板等橡胶制品中。
14.为什么丁苯胶的硫化速度比天然胶慢?
答:
因为NR有推电子的侧甲基,而丁苯橡胶有弱吸电子的苯基和乙烯基侧基 15.SBR在哪些性能上优于NR?
试从结构上解释之。
SBR的耐磨性、抗湿滑性、起始龟裂性能及使用温度上限都优于NR。
因为NR有推电子的侧甲基,而SBR有弱电子的苯基和乙烯基侧基,SBR分子链侧基是苯基及乙烯基,分子链不易内旋转。
第二章硫化体系
1.硫磺在NR、SBR、BR和NBR这几种橡胶中的溶解性怎样?
硫磺交联键的类型有哪几种?
答:
室温下,硫磺在NR和SBR中溶解较为容易,在BR和NBR中的溶解比较困难。
单硫键-C-S-C- 双硫键-C-S-S-C-:
耐热、耐老化性能较好,但张伸性能、耐疲劳性能较差 多硫键-C-Sn-C- 机械强度高,耐疲劳性好,但耐热、耐老化性能较差。
2.硫化剂的作用是什么,硫化在制品生产中有何意义?
答:
使之生成少量的低硫键,提高硫化胶的拉伸性能
5.传统硫化体系、有效硫化体系、半有效硫化体系对硫化胶结构与性能有何影响?
其应用范围怎样?
答:
常硫量硫化化体系用量:
S>1.5份促进剂一份左右
硫化胶结构:
以多硫键为主(占70%),低硫键较少
性能特点:
拉伸强度高,弹性大,耐疲劳性好;耐热,耐老化性较差, 此硫化体系使得胶料交工的安全性好,加工成本低,性能能满足一般要求。
有效硫化体系用量:
S 0.8-1.5份或部分给硫体代替,促进剂1-1.5份
硫化胶结构:
此硫化体系能使硫化胶形成占绝对优势的低硫键(90%)
性能特点:
耐热,耐老化性能较好,但拉伸强度、弹性、耐疲劳性较差 ,多用于在静态条件下使用的制品,如耐油密封圈。
半有效硫化体系用量:
低S 0.2-0.5份或部分给硫体代替促进剂2-4份
硫化胶结构:
多硫键,低硫键大体各占一半。
性能特点:
拉伸强度、弹性、耐疲劳性能适中;耐热,耐老化性能稍好, 此硫化体系多用于在动态条件下使用的制品,如轮胎胎侧。
6.CR适用的硫化剂是什么?
为什么不用硫磺硫化?
答:
CR适用的硫化剂是金属氧化物。
因为CR中主要是-CH=CCl-结构,氯的存在减弱了其中双键的反应性,所以其硫化反应活性比NR/SBR/NBR低,不能用硫磺硫化。
9.喷霜产生的原因是什么?
为避免喷霜应采取哪些措施?
答:
混炼胶产生喷霜的原因:
配合剂与橡胶的相容性差、配合剂用量过多、加工温度过高,时间过长、停放时降温过快,温度过低、配合剂分散不均匀。
硫化胶产生喷霜的原因:
与橡胶相容性差的防老剂或促进剂用量多了、胶料硫化不熟,欠硫、使用温度过高,贮存温度过低、胶料过硫,产生返原。
减轻喷霜的措施:
低温炼胶、使用不溶性硫黄、用硫载体取代部分硫黄、适当提高混炼胶的停放温度(25~30 ℃)、采用促进剂或防老剂并用,减少单一品种的用量、胶料中添加能够溶解硫黄的增塑剂如煤焦油、古马隆树脂、使用防喷剂
7.MgO在CR配方中的作用是什么?
答:
在高温(100℃以上)能提高硫化胶的定伸应力,并能吸收硫化过程中产生的HCl,在低温下具有稳定剂作用,能防止焦烧,但硫化时间长,且硫化程度不高。
8.在过氧化物硫化体系中,硫化有什么作用?
答:
可配用少量硫磺作辅助硫化,使之生成少量的低硫键,提高硫化胶的强伸性能。
9.哪些橡胶可用硫磺硫化,单用硫磺硫化有何缺点?
答:
含双键多的可用硫磺硫化
缺点:
硫化时间长,硫磺用量多,硫化温度高,能耗大,硫磺利用率低,橡胶的工艺性能和物理机械性能比有促进剂和活化剂的硫化体系低
13.硫化曲线中的诱导期、硫化返原、硫化平坦期对一个企业的经济效益有何意义?
答:
硫化曲线中诱导期要足够长,充分保证生产加工的安全性,硫化速度要快,提高生产效率,降低能耗。
硫化平坦期要长,硫化胶具有较好的机械性能。
并不希望出现硫化返原,这会使硫化胶物理机械能能下降。
14.活性剂(氧化锌和硬脂酸)在硫磺硫化体系中的作用是什么?
答:
氧化锌和硬脂酸所组成活性剂课结合形成硬脂酸锌盐,硬脂酸锌盐有较大的溶解能力,可参与硫化反应个过程,减少多硫键的数目,从而改善了耐热、耐老化性能。
下列各种橡胶,哪些可以进行硫化反应?
①过氧化物 (NR、SBR、IIR、CR) ②硫磺(NR、BR、IIR、CR) ③金属氧化物(NR、CR、NBR、IIR)
16.试说明NR中不同硫磺用量和促进剂用量对硫化体系类型、交联结构及硫化胶性能的影响。
答:
NR的普通硫磺硫化体系,促进剂0.5-0.6份,硫磺2.5份,所得硫化胶网络70%以上为多硫交联键,硫化胶具有良好的初始疲劳性能,室温下有优良的动静态性能,但不耐热氧老化。
高促低硫(促进剂3-5份,硫化剂0.3-0.5份)或无硫,为有效硫化体系,交联结构中单、双硫键占90%,硫化橡胶有较高的抗热氧老化性能,但起始动态疲劳性差。
促进剂、硫磺用量介于以上两种之间,为半有效硫化体系,交联结构中多硫键与单双硫键相当,硫化胶有较好的动态性能,又有中等程度的耐热氧老化性能。
促进剂与硫等物质的量,为平衡硫化体系,交联结构有单硫、多硫、双硫,硫化胶有优良的耐热老化性和耐疲劳性。
22.已知有下列交联网络,请你说出与其相对应的硫化体系
① -C-C- ②-C-O-C- ③ -C-S1-C-和-C-S2-C- ④-C-S1-C-、-C-S2-C-和-C-SX-C-(其中以多硫交联键为主) ⑤-C-S1-C-、-C-S2-C-和-C-SX-C-(其中以单硫键和双硫键为主)
答:
依次是:
过氧化物硫化体系、酚醛树脂硫化体系、有效硫化体系、传统硫化体系、半有效硫化体系
25.橡胶的硫化过程可分为哪几个阶段?
试以硫化历程来加以说明。
答:
从化学反应角度看,第一阶段:
诱导期,各组分相互作用,生成有侧基的橡胶大分子。
第二阶段:
交联反应,带有侧基的橡胶大分子与橡胶大分子发生交联反应。
第三阶段:
网络熟化阶段,交联键发生短化、重排、裂解,趋于稳定。
从宏观角度看,分为焦烧阶段、热硫化阶段、平坦硫化阶段和过硫化阶段。
第三章橡胶的老化与防护
3.问答题∶
1.引起橡胶老化的内因,外因有哪些
答:
内因有橡胶分子链结构(双键、a-H)、橡胶内金属离子、橡胶中的配合剂 ;
外因有物理因素(热、光、电、应力、应变、辐射、水)、化学因素(O2、O3、SO2、H2S、酸、碱、金属离子)、生物因素(微生物(细菌、酶) 、昆虫(白蚁)
16.为什么IR、NR热氧老化后变软,BR、SBR和NBR热氧老化后变硬?
答:
因为IR、NR的化学结构主要是顺-1,4-聚异戊二烯,链稀烃发生a-H反应,a-H易于脱掉形成烯丙基自由基,分子链裂解,形成小的分子链,故热氧老化后变软。
BR、SBR、NBR结构中都含有丁二烯,在进行氧化后发生分子间的交联,所以热氧老化后变硬。
4.石蜡为何能防护静态使用条件下的橡胶臭氧化?
答:
石蜡能防止静态变形橡胶的臭氧龟裂
9.影响臭氧老化的因素有哪些?
10.影响疲劳老化的因素有哪些?
11.防老剂为什么有适当的用量?
12.防老剂按结构可分为几类?
各有何特点?
15.试解释将防老剂D与防老剂TNP并用时会产生什么效果?
为什么?
18.试分析比较NR、CR、BR的耐臭氧老化性能
8.何谓防老剂的协同效应、对抗效应、加和效应?
什么情况下防老剂之间可能有协同效应?
答:
链终止型防老剂和破坏氢化过氧化物型防老剂并用会产生协同效应
6..不饱和碳链橡胶的吸氧曲线是什么形状的?
曲线可分为几个阶段?
每个阶段各有何特点?
根据下图三种橡胶吸氧动力学曲线判断它们的耐热氧化的顺序。
答:
不饱和碳链橡胶的吸氧曲线呈S型,可分为三个阶段。
第一阶段吸氧量小,吸氧速度基本恒定,此阶段橡胶性能虽有所下降但不显著,是橡胶的使用期。
第二阶段是自动催化氧化阶段,吸氧速度急剧增大,在此段后期,橡胶已深度氧化变质,丧失使用价值。
第三阶段是氧化反应结束阶段,吸氧速度先变慢后趋于恒速最后降至零,氧化反应结束
16.橡胶臭氧老化的物理防护方法有几种?
答:
四种,分别是橡胶并用、橡塑共混、表面涂层、加抗臭氧蜡。
21.选择合适的防老剂∶
(1)与食品接触的白色橡胶制品 ①防老剂D ②防老剂4010 ③防老剂264
(2)轮胎胎侧胶 ①防老剂MB ②防老剂4010NA ③防老剂2246S
(3)耐油抽出的橡胶 ①防老剂A ②防老剂NBC ③亚硝基二苯胺
第四章橡胶的补强与填充体系
3.问答题∶
5.炭黑聚集体的形态与炭黑结构程度高低有什么关系?
答:
①炭黑的一次结构(基本聚集体,聚熔体,永久结构) 炭黑在制造过程中,粒子间互相融结而形成的链枝状或葡萄状的聚集体叫一次结构。
它由化学键结合,炼胶过程中不受破坏,是炭黑在胶料中最小可分散的单位。
②炭黑的二次结构(次级聚集体) 指两个或两个以上,通过范德华力(物理吸附)而形成的疏松缔合物。
结合较弱,有些在造粒时被破坏,大多在炼胶时被破坏。
6.炭黑聚集体表面有什么基团?
炭黑的PH值与表面基团有什么关系?
答:
炭黑表面上有自由基、氢、含氧基团(羟基、羧基、内酯基、醌基)。
炭黑的PH值与表面的含氧基团有关,含氧基团含量高,PH值低,反之亦然。
10.什么是炭黑的表面粗糙度?
表面粗糙度是怎么形成的?
粗糙度影响橡胶的哪些性能?
11.炭黑的粒径、结构度、表面活性及表面含氧基团对胶料的混炼、加工工艺性能和焦烧性有何影响?
答:
对于混炼,粒径:
粒径小,吃料慢,难分散,生热高,黏度高;结构:
结构高,吃料慢,易分散,生热高,黏度高;活性:
活性高,生热高,黏度高,对吃料、分散影响不显著。
对于加工工艺(压延、挤出),炭黑粒径小、结构度高、用量大,压延挤出半成品表面光滑,收缩率低,压出速度快。
对于焦烧性,炭黑表面含氧基团多,pH值低,硫化速度慢;炭黑粒径小,结构高,易焦烧,硫化速度快。
22.什么是结合橡胶?
结合橡胶形成的途径有哪些?
哪些因素影响结合橡胶的生成量?
答:
结合橡胶,也称为炭黑凝胶(bound- rubber),是指炭黑混炼胶中不能被它的良溶剂溶解的那部分橡胶。
形成途径有两个,一是化学吸附,二是物理吸附。
影响结合橡胶的因素炭黑的因素,炭黑的比表面积(比表面积增大,结合橡胶增加)、混炼薄通次数、温度(温度升高结合胶量升高)、橡胶性质(不饱和度高,分子量大的橡胶生成的结合胶多)、陈化时间(时间增加,结合胶量增加,约一周后趋于平衡)。
12.炭黑的基本性质对硫化胶的拉伸强度、定伸应力、扯断伸长率、耐磨性有何影响?
答:
①炭黑粒径的影响:
粒径小,撕裂强度、定伸应力、硬度均提高,而弹性和伸长率下降,压缩永久变形很小,耐磨性好。
②炭黑结构的影响:
定伸应力随结构度的升高而明显提高。
结构对磨耗的影响小于炭黑比表面积的影响,而且它的影响只有在苛刻磨耗条件下才明显化。
③炭黑表面活性的影响:
炭黑粒子表面的活性及结晶尺寸对补强作用有一定影响,微晶尺寸增大,炭黑的补强作用下降。
炭黑粒子的表面粗糙度对橡胶补强不利。
14.白炭黑分为几类?
各有何特点?
白炭黑表面有什么基团?
气相法白炭黑和沉淀法白炭黑结构上有什么不同?
根据制造方法不同分为 ①干法白炭黑(气相白炭黑) ②湿法白炭黑(沉淀白炭黑) 气相法白炭黑的补强性好,但价格贵,产量低。
沉淀白炭黑主要用作天然橡胶和合成橡胶的补强剂、牙膏摩擦剂等。
白炭黑表面上有羟基、硅氧烷基。
气相法的粒子内部为无规则的三元体型结构,呈紧密填满状态;沉淀法白炭黑内部有无规则的二元线性结构,因而有毛细孔内表面。
17.分析下列化合物中哪一种可能在表面含羟基的白炭黑与二烯烃橡胶之间起偶联剂的作用?
哪些能起到对碱性无机填料与二烯烃橡胶之间的偶联作用① CH2=CH-(CH2)15-COOH ② CH3-CH2-(CH2)15-CH2OH ② CH3-(CH2)15-CH=CH2④ CH2=CH-CH2-Si-(OCH3)3
答:
①/②④
18.炭黑在橡胶中为何有最大填充量?
若实际用量超过该最大值后会怎样?
答:
过多则出现硬化效应,但对热裂法炭黑则不限。
19.计算HAF在BR中的最大填充量∶ 条件∶①HAF的DBP吸油值为120ml/100g,比表面积为76m2/g,结合橡胶厚度为45埃 (并假设是平面的),比重1.86g/cm3,②BR比重为0.92g/cm3。
20.根据用途选择一种填料∶
①制造矿山地区砂石路面上使用的载重车胎面胶 :
HAF-HS,SRF,HAF,MT,沉淀法碳酸钙,陶土
②某胶硫化速度快,要求选一种对硫化速度有减缓作用的补强剂:
ISAF ,HAF,EPC,FEF ,FT
③药用瓶子的瓶塞:
CaCO3,SRF,BaSO4
④乙丙橡胶与天然橡胶并用做白色胎侧胶:
白炭黑,沉淀法CaCO3,GPF,陶土
24.通常所说的硬质炭黑和软质炭黑各包括哪些品种,有何特点?
答:
硬质炭黑:
粒径在40nm以下,补强性高的炭黑如超耐磨,中超耐磨,高耐磨炭黑等。
软质炭黑:
粒径在40nm以上,补强性低的炭黑,如半补强炭黑,热裂法炭黑等。
25.可用哪些方法来提高白色填料的补强性?
答:
一半可用表面改性的方法来提高白色填料的补强性。
具体包括:
亲水基团偶联剂或表面活性剂改性、离子表面接枝、离子表面离子交换、粒子表面聚合物胶囊化。
第五章弹性体共混 二.
问答题∶
1.什么叫塑炼?
其目的意义何在?
是否每种生胶都要塑炼?
答:
指把具有弹性的生胶转变成可塑性胶料的工艺过程 塑炼的目的:
1、使生胶获得一定的可塑性,满足加工的要求;2、使生胶的可塑性均匀化,以便制得质量均匀的胶料。
门尼粘度60以下的不用塑炼。
如软丁苯胶、软丁腈胶
4.氧对生胶塑炼起到什么样的作用?
答:
①低温塑炼机械力为主,也称冷塑炼。
②高温塑炼氧化裂解为主,也称热塑炼。
5.温度对生胶塑炼有何影响?
为什么NR在110℃下塑炼效果最差?
答:
低温机械塑炼效果随温度升高而减小,高温机械塑炼效果随温度升高而急剧增大,在110℃左右的温度范围内,机械塑炼效果最小。
当温度在110℃附近时,机械力的破坏作用和氧的直接氧化裂解作用都很小,故总的机械塑炼效果最小。
6.开炼机塑炼时的操作方法有哪些?
各有何优点?
答:
1)薄通法:
生胶不包辊,通过0.5—1毫米的辊距,然后让其自然地落到开炼机的低秀盘上,再将底盘上的胶拿起扭转90°投入辊筒上,反复多次,直到可塑性达到要求为止。
薄通法对各种橡胶的塑炼都普遍适用。
而且塑炼效果好,胶料质地均匀。
2)包辊塑炼,将生胶包在前辊上让其自然反复过辊塑炼,直至规定的时间为止。
这种方法由于辊距较大(5—10毫米)胶料不易散热,温度容易升高。
塑炼效果较差,塑炼胶质量不大均匀。
但劳动强度较小,易于操作。
3)爬架子法:
将生胶在炼机上过辊后即引上一个装有运输带的架子上,运行一段距离再返回塑炼。
特点是胶料散热较好。
塑炼效果比包辊法好。
4)机组连续塑炼法:
将几如开炼排列组成机组,用运输带连接进行连续塑炼。
此法塑炼效果高,生产能力大,可连续法地操作。
但需用的设备多。
7.用开炼机和密炼机塑炼各有何优缺点?
答:
开炼机:
存在机械自动化程度低,劳动强度高,操作危险性大,配合剂飞扬损失大,工作环境条件差,混炼质量较差等缺点,不适于现代化大规模生产。
但机台容易清洗,变换配方灵活方便,适合于胶料配方多变,批量少的生产和实验室加工,炼胶温度较低,适于某些特殊配方。
密炼机:
塑炼效率高,胶料的可塑性比较均匀一致,而且其自动化稳度高,劳动强度和卫生条件都得以改善,但胶料会受到高温和氧化裂解作用,硫化胶物机性能有所下降,且设备造价高,一般只适于大型工厂使用
8.用开炼机塑炼应控制的工艺条件有哪些?
它们对塑炼有何影响
答:
容量大小:
取决于生胶品种和设备规格,为提高产量,可适当增加容量,但若过大会使辊筒上的堆积胶过多,难以进入辊距使胶受不到捏炼,且胶料散热困难,温度升高又会降低塑炼效果。
辊距:
减小辊距有利于增大机械剪切作用,胶片厚度剪薄有利于冷却和提高机械塑炼效果。
辊速和辊比:
提高辊筒的转速和速比都会提高塑炼效果,但辊速和速比的增大,辊距的减小都会加大胶料的生热升温速度,为保证机械塑炼效果,必须同时加强冷却措施。
辊温:
辊温低,胶料黏度高,机械塑炼效果增大,辊温过低会使设备超负荷而受损害,并增加操作危险性。
塑炼时间:
每次塑炼的时间在15-20min以内,不仅塑炼效率高,最终获得的可塑度也大。
化学塑解剂:
可塑度在0.5以内时,胶料的可塑度随塑炼时间增加而呈线性增大。
9.用密炼机塑炼应控制的工艺条件有哪些?
它们对塑炼有何影响?
答:
容量:
容量过小不仅降低机械塑炼效果和生产效率,塑炼胶质量也不均匀,容量过大,塑炼质量不均匀,且密炼室散热困难使胶温过高。
上顶栓压力:
增加设备对胶料的摩擦和剪切作用,提高塑炼效果。
转子速度:
同样条件下,胶料达到相同的可塑度要求所需要的塑炼时间与转速成反比。
随着转速的提高又必然会加大胶料的生热升温速度,应加强冷却措施,防止过炼。
塑炼温度:
塑炼效果随温度升高急剧增大,但温度过高有可能出现过炼而损害硫化胶物理机械性能。
塑炼时间:
排胶温度一定,密炼机塑炼效果最初随着塑炼时间线性增大,然后渐趋缓慢。
化学塑解剂:
不仅能充分地发挥其增塑效果,而且在同样条件下还可降低排胶温度,提高塑炼胶质量。
12.为什么对各种制品用的塑炼胶都规定有一定的可塑度?
其可塑度过大或过小有什么不好?
答:
生胶的可塑度是关系到制品整个制造过程进行的难易,直接影响到硫化胶的物理炼胶机机械性能及制品使用性能的重要性质。
若生胶可塑度过高,会使硫化胶的物理机械性能降低。
而生胶可塑度过低,则会造成下工艺加工的困难,使胶料不易混炼均匀,压延,压出时半成品表面不光滑,收缩率大,不易掌握半成品尺寸,在压延时胶料也难于擦进织物中,造成挂胶帘布掉皮等现象,大大降低布层间附着力
14.试分析为什么合成橡胶塑炼效果不如NR明显,且不容易出现过炼现象?
答:
这是因为多数丁二烯类合成橡胶的分子链中不具备天然橡胶分子中的甲基共轭效应,因为没有键能较低的弱键存在;其次是合成橡胶的平均分子量一般都比较低,初始黏度较低,机械力作用下容易发生链之间的滑动,降低了机械力的有效作用;多数合成橡胶在机械力作用下不能结晶或结晶性很小,这些都使合成橡胶分子链难以被机械力破坏;另外,低温下丁二烯类合成橡胶分子链被机械力破坏生成的大分子自由基化学稳定性较NR低,缺氧时容易发生再结合而失去机械塑炼效果或发生分子间活性传递,产生支化和凝胶而不利于塑炼;当有氧时一方面发生氧化裂解,另一方面也产生支化和凝胶,故合成橡胶低温机械塑炼效果不如NR好,在机械塑炼时应尽可能降低辊温,减小辊距并减小容量。
第七章混炼
2.问答题∶
1.什么叫混炼?
混炼的目的意义何在?
混炼:
通过适当的加工将配合剂均匀混合在一起,制成质量均一的混合物,完成这一加工操作的工艺过程叫做胶料的混炼工艺。
意义:
混炼胶质量对胶料的后续加工性能、半成品质量和成品性能具有决定性硬相,所以混炼工艺是橡胶加工中最重要的基本工艺过程之一。
2.在开炼机上混炼时一般会出现哪几种包辊状态?
如何才能取得适合于混炼的最好包辊状态?
1)生胶不能进入混距,不能包辊,原因是辊温较低或胶料硬度大,弹性高。
如硬丁晴胶或塑炼等,在这种情况下不能进行混炼。
2)生胶能包前辊,一般橡胶都能出现这种情况,这是正常混炼的包辊状态
3)生胶通过辊缝后不能紧包前辊上,表现有脱辊(或称出兜)的现象。
在温度稍高时,混炼顺丁胶或三元乙丙橡胶等会出现这种情况,此时使混炼操作发生困难。
4)呈粘流包辊,在高温下混炼塑性较大的胶料会出现这种情况,这种情况下混炼可正常进行,但对配合剂的分散下利。
在混炼时,一般应控制在第二种和第四种情况,而避免出现第一种和第三种情况。
为了取得第二种情况,在操作中必须根据各种生胶的特性来选择适宜的温度,如顺丁胶的包辊性较差,适宜的混炼温度范围较窄当辊温超过时,由于生胶的结晶溶解,变得无强韧性,就会出现第三种状态。
天然胶和丁苯胶的包辊性较好,适宜的