5承压设备无损检测答疑.docx
《5承压设备无损检测答疑.docx》由会员分享,可在线阅读,更多相关《5承压设备无损检测答疑.docx(27页珍藏版)》请在冰豆网上搜索。
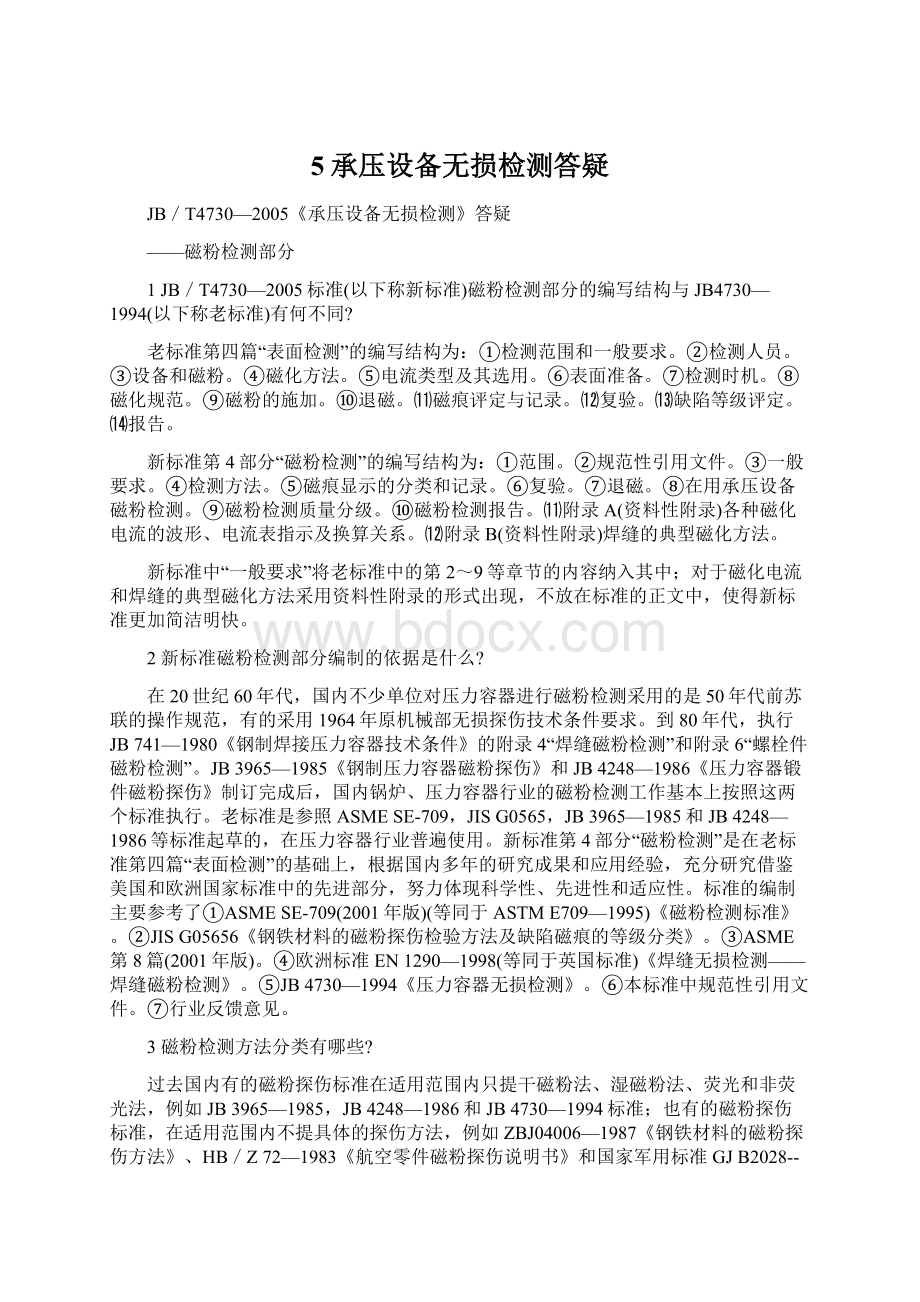
5承压设备无损检测答疑
JB/T4730—2005《承压设备无损检测》答疑
——磁粉检测部分
1JB/T4730—2005标准(以下称新标准)磁粉检测部分的编写结构与JB4730—1994(以下称老标准)有何不同?
老标准第四篇“表面检测”的编写结构为:
①检测范围和一般要求。
②检测人员。
③设备和磁粉。
④磁化方法。
⑤电流类型及其选用。
⑥表面准备。
⑦检测时机。
⑧磁化规范。
⑨磁粉的施加。
⑩退磁。
⑾磁痕评定与记录。
⑿复验。
⒀缺陷等级评定。
⒁报告。
新标准第4部分“磁粉检测”的编写结构为:
①范围。
②规范性引用文件。
③一般要求。
④检测方法。
⑤磁痕显示的分类和记录。
⑥复验。
⑦退磁。
⑧在用承压设备磁粉检测。
⑨磁粉检测质量分级。
⑩磁粉检测报告。
⑾附录A(资料性附录)各种磁化电流的波形、电流表指示及换算关系。
⑿附录B(资料性附录)焊缝的典型磁化方法。
新标准中“一般要求”将老标准中的第2~9等章节的内容纳入其中;对于磁化电流和焊缝的典型磁化方法采用资料性附录的形式出现,不放在标准的正文中,使得新标准更加简洁明快。
2新标准磁粉检测部分编制的依据是什么?
在20世纪60年代,国内不少单位对压力容器进行磁粉检测采用的是50年代前苏联的操作规范,有的采用1964年原机械部无损探伤技术条件要求。
到80年代,执行JB741—1980《钢制焊接压力容器技术条件》的附录4“焊缝磁粉检测”和附录6“螺栓件磁粉检测”。
JB3965—1985《钢制压力容器磁粉探伤》和JB4248—1986《压力容器锻件磁粉探伤》制订完成后,国内锅炉、压力容器行业的磁粉检测工作基本上按照这两个标准执行。
老标准是参照ASMESE-709,JISG0565,JB3965—1985和JB4248—1986等标准起草的,在压力容器行业普遍使用。
新标准第4部分“磁粉检测”是在老标准第四篇“表面检测”的基础上,根据国内多年的研究成果和应用经验,充分研究借鉴美国和欧洲国家标准中的先进部分,努力体现科学性、先进性和适应性。
标准的编制主要参考了①ASMESE-709(2001年版)(等同于ASTME709—1995)《磁粉检测标准》。
②JISG05656《钢铁材料的磁粉探伤检验方法及缺陷磁痕的等级分类》。
③ASME第8篇(2001年版)。
④欧洲标准EN1290—1998(等同于英国标准)《焊缝无损检测——焊缝磁粉检测》。
⑤JB4730—1994《压力容器无损检测》。
⑥本标准中规范性引用文件。
⑦行业反馈意见。
3磁粉检测方法分类有哪些?
过去国内有的磁粉探伤标准在适用范围内只提干磁粉法、湿磁粉法、荧光和非荧光法,例如JB3965—1985,JB4248—1986和JB4730—1994标准;也有的磁粉探伤标准,在适用范围内不提具体的探伤方法,例如ZBJ04006—1987《钢铁材料的磁粉探伤方法》、HB/Z72—1983《航空零件磁粉探伤说明书》和国家军用标准GJB2028--1994《磁粉检验》;在GB/T15822—1995《磁粉探伤方法》的主题内容与适用范围中只笼统地提到“……磁粉探伤的一般方法和交叉磁轭探伤方法”。
征求意见时,少数单位提出要增加连续法和剩磁法;也有的要求增加周向磁化、纵向磁化和复合磁化法。
为了平衡这些意见,标准工作组参照日本JISG0565标准,考虑到锅炉、压力容器及压力管道的特点,把这些方法分类列人标准中(表1)。
表1磁粉检测方法分类
分类条件
磁粉检测方法名称
施加磁粉的载体
干法(荧光、非荧光)、湿法(荧光、非荧光)
施加磁粉的时机
连续法、剩磁法
磁化方法
轴向通电法、触头法、线圈法、磁轭法、中心导体法、交叉磁轭法
4新标准对磁粉检测人员有何要求?
磁粉检测人员应符合新标准第1部分第5.3节的要求,但要强调的是,磁粉检测人员未经矫正或经矫正的近距视力和远距视力应不低于5.0(小数记录值为1.0),测试方法应符合GB11533《标准对数视力》的规定。
并每年检查一次,不得有色盲。
医学上对色盲和色弱是这样定义的:
色盲是指全部或部分失去对颜色的分辨能力;色弱是指对颜色能正确认出,但表现出识别困难或辨认的时间较长。
由于磁粉有多种颜色,并且荧光磁粉检测时,在紫外线的照射下,其磁痕显黄绿色荧光,故要求磁粉检测人员不能是色盲,而色弱者可辨认简单的颜色,因此本标准不再象老标准那样强调“不得有色弱”。
5新标准对磁轭提升力指标有何规定?
新标准规定,当使用磁轭最大间距时,交流电磁轭至少应有45N的提升力,直流电磁轭至少应有177N的提升力,交叉磁轭至少应有118N的提升力(磁极与试件表面间隙为0.5mm)。
磁粉检测标准规定的磁轭提升力指标反映了磁化规范的要求。
规定磁感应强度峰值Bm必须达到一定的大小,对于恒稳直流电或工频交流电通常可用磁轭平均吸力表达,其原理为,对于一定的设备与工件,磁轭平均吸力与铁素体钢板的磁导率、磁极间距、磁极间隙及运动状态等有关,当上述因素不变时,磁感应强度峰值Bm与磁轭平均吸力有一定的对应关系。
但如磁极间距变化,将使磁感应强度B、磁场强度H和相对磁导率μ变化,因此,提升力指标中应注明磁极间距。
新标准对交、直流电磁轭的提升力要求是参照ASME规范(2001年版)第五卷第7章“磁粉检测”中T-762的内容;对交叉电磁轭的提升力要求是基于对我国现有交叉电磁轭设备所进行的试验数据。
磁粉检测标准修改组做过交叉磁轭的提升力试验,在间隙为0.5~1mm且不考虑行走速度的情况下,要达到A1—7/50探伤灵敏度,交叉磁轭至少应有118N的提升力。
此提升力应注明间隙大小,因为间隙会降低被磁化工件的有效磁场强度,同时也降低了交叉磁轭的提升力。
因此新标准对交叉磁轭的提升力指标要求磁极与试件表面间隙为0.5mm。
6新标准对磁悬液载液有何规定?
新标准规定,湿法应采用水或低粘度油基载体作为分散媒介。
若以水为载体时,应加人适当的防锈剂和表面活性剂,必要时添加消泡剂。
油基载体的运动粘度在38℃时≤3.0mm2/s,使用温度下≤5.0mm2/s,闪点≮94℃,且无荧光和无异味。
以上规定主要取自ASMESE-709标准。
粘度指标主要是考虑在较低温度下载液应有较好的流动性,以保证探伤灵敏度。
高闪点指标主要是考虑安全性问题,无荧光是为了保证荧光磁粉探伤时不致干扰正常显示。
新标准以运动粘度作为油基载体粘度指标,纠正了老标准以动力粘度作为粘度控制指标的错误。
7新标准对磁悬液浓度有何规定?
新标准规定的磁悬液浓度有两种,一种是配制浓度,单位为g/L,用于新配制磁悬液时的浓度控制;另一种是沉淀浓度,单位为mL/100mL,利用梨形沉淀管测定,它既可用于回收磁悬液的浓度控制,又可用于新配制磁悬液时的浓度控制(表2)。
表2磁悬液浓度
磁粉类型
配制浓度/(g/L)
沉淀浓度/(含固体量,mL/100mL)
非荧光磁粉
10~25
1.2~2.4
荧光磁粉
0.5~3.0
0.1~0.4
承压设备磁粉检测实际工作中,绝大部分磁悬液均是一次性使用,若用体积沉淀法来确定磁悬液浓度则相当麻烦。
同时,由于磁粉用量不明确,配制磁悬液往往很长时间才能达到标准要求。
因此,新标准参考了JISG0565和国内压力容器行业多年来使用的经验采用g/L表示磁悬液的浓度,这样可使磁悬液的配制变得简单实用。
8除标准灵敏度试片以外,新标准还规定了哪些磁粉检测用灵敏度试件?
新标准还规定了磁场指示器(八角试块)和用于中心导体磁化方法的标准试块。
磁场指示器最早来自美国标准,由于它使用方便,经久耐用,在JB3965—1985标准中就开始采用。
由于磁场指示器刚性大,不可能与工件表面(曲面)很好粘合,同时其厚度为3.7mm,这些都使得磁场指示器无法模拟出工件表面状况,其磁痕显示与工件表面的磁场强度无严格对应关系,因此,新标准规定磁场指示器只能作为工件表面磁场方向是否正确的一种粗略校验工具,而不能作为工件表面磁场强度及其分布的定量指示。
新标准规定的中心导体法标准试块已列入JB/T6066—2004《无损检测磁粉检测用环形试块》中,它适用于中心导体法中估判磁化检测技术的全面性能及灵敏度的一种工具。
9JB/T4730—2005标准(以下称新标准)对标准灵敏度试片有何规定?
新标准规定的标准试片有A1型、C型、D型和M1型。
与JB4730—1994标准(以下称老标准)相比,新标准增加了D型和M1型试片内容。
A型试片最先由日本标准提出,A型试片分A1和A2型,A1型为退火材料制成,其磁导率各向异性很小,而A2型为不作热处理的冷轧材料,在不同方向上磁特性有差异,因此新标准特别注明A1型试片,使之与日本标准中术语相对应。
C型试片主要应用于由于被检工件尺寸原因导致Al型标准试片使用不便的场合,如焊缝坡口等狭小部位的检测。
D型试片内容主要参照了JB/T6065标准,适用于探伤面窄小或工作表面曲率半径较小的场合。
M1型试片由铁道科学研究院金化所生产,它是由三个不同深度而间隔相等的人工刻槽以同心圆形式做在同一试片上,一片多用,观察磁痕显示差异直观,能更准确地推断出被检工件表面状态。
日本无损检测学会曾进行过连续法检测时A型标准试片磁痕显示与磁场强度对应关系的试验。
结果表明,用连续法探出的A型标准试片的磁痕,几乎不受被检材质的影响,而仅与被检物表面的磁场强度有关。
用剩磁法时,A型试片显示磁痕与被检件的剩磁通密度有关,但由于后者受试件的材质、A型试片与探伤面的接触状态以及试件产生的磁极的较大影响,故不能利用A型试片直接测试试件的剩磁通。
所以A型试片仅适用于连续法,不适用于剩磁法。
在连续法中使用标准灵敏度试片可以了解被检工件各部位表面有效磁场强度和方向,确定有效检测区,确认磁化方法是否正确,还可检查探伤装置,磁粉、磁悬液的性能,以及检测操作是否正确等,具有使用简单、直观、方便等优点。
10新标准中对确定磁场强度方法作了哪些规定?
磁粉检测应有适当的磁场强度,为了使磁痕显示一致,磁场强度必须控制在合理的范围内,通常是±25%,影响磁场强度的因素是工件的尺寸、形状、材质以及磁化技术等,这些因素的变动范围广泛,所以很难制定严格的磁场强度规则以适用于每种工件。
标准中规定了四种方法来确定磁场强度:
(1)用磁化电流表征的磁场强度按新标准第4部分中3.8.6.1~3.8.6.3款所给出的公式计算。
(2)用材料磁特性曲线,确定合适的磁场强度。
(3)磁场强度计测量工件表面的切线磁场强度,连续法为2.4~4.8kA/m,剩磁法为14.4kA/m。
(4)用标准试片(块)来确定磁场强度是否合适。
对于工件形状规则的磁化规范可用经验公式计算,但对于形状复杂的工件,很难用经验公式计算出每个部位的磁场强度,此时可以用仪器来测量表面磁场强度。
用连续法检验,工件表面的切向磁场强度为2.4~4.8kA/m,其下限值为标准规范要求,上限值为严格规范要求,用剩磁法检验,工件表面切向磁场强度应达14.4kA/m,使工件饱和磁化。
对常规工程材料来说,在相应的磁场强度下其相对磁导率均可在240以上,用经验公式计算或仪器测量表面磁场强度确定的磁化规范均可得到所需的检测灵敏度,但对与常规工程材料磁特性差别较大的钢材,最好是在测绘其磁特性曲线后制定磁化规范,方可获得理想的检测灵敏度。
标准试片方法对于异型工件和尺寸变化较大形状复杂的工件具有快速直观的优点,对工件局部的探伤灵敏度也能够实施控制,但对于小型工件磁化规范的确定比较困难,对剩磁法不适用,也不能反映工件的磁特性,试片上能够发现的规定大小的缺陷不能说明在工件上也能发现同样的缺陷,因此在使用标准试片之前,应了解工件的磁特性,如工件的磁特性与试片相差较大,应进行适当修正。
ll直接通电法和中心导体法有哪些特点?
在新标准中这两种方法的磁化规范是如何规定的?
(1)用直接通电法检测筒形工件不能检查其内表面不连续性,因为内表面磁场强度为零。
(2)用中心导体法能检测筒形工件内外表面与电流方向平行的纵向缺陷和端面的径向缺陷。
(3)中心导体法对筒形外表面检测时应尽量使用直流电或整流电,用交流电进行外表面检测时,会在筒形工件内产生涡电流,因此工件的磁场是芯棒中的传感电流和工件内的涡电流产生的磁场叠加,由于涡电流有集肤效应,由此导致工件内外表面的检测灵敏度相差很大,对磁化规范确定带来困难。
国内有资料介绍,对一内径为φ80mm,厚2mm钢管通交直流电磁化,为达到管内、外表面相同大小的磁场,通直流电时二者相差不大,而通交流电时,检查外表时的电流值将是检查内表面时电流值的2.7倍。
因此用中心导体法进行外表面检测时,一般不用交流电而尽量使用直流电和整流电。
(4)使用中心导体法如电流不能满足检测要求时可用偏置芯棒法,芯棒应靠近内壁放置,导体与内壁接触时应采取绝缘措施。
老标准中棒与内壁间距10~15mm以及按空心工件厚度来确定磁化电流值的表11—4被删去。
(5)新标准对轴向通电法和中心导体法的磁化规范按表3中公式计算。
表3轴向通电法和中心导体法磁化规范
检测方法
磁化电流I的计算公式
交流电
直流电、整流电
连续法
(8~15)D注1)
(12~32)D
剩磁法
(25~45)D
(25~45)D
注:
1)D——工件横截面上最大尺寸,mm
根据通电导体的磁场公式计算,连续法检验时工件表面的切向磁场强度为2.4~4.8kA/m,所要求的交流电磁化电流I=(7.5~15)D,三相全波整流电磁化电流I=(12~32)D,下限值对应于标准规范,上限值对应于严格规范;因此新标准根据标准规范和严格规范的要求确定磁化电流值的大致范围,交流电连续法I=(8~15)D;直流电(整流电)连续法I=(12~32)D,与ASMESE-709标准一致。
12新标准中对触头法的磁化规范是如何规定的?
新标准中对触头法的磁化规范规定与ASME规范大致相同(表4)。
其中个别数值微小差别的调整是为了便于记忆,而且也在误差范围内。
另外,触头法产生畸变的周向磁场,除按经验公式选择磁化规范外,还应用标准试片实测结果来校正磁化电流值。
表4触头法磁化规范
标准号
工件厚度T/mm
电流值I/A
JB/T4730—2005标准
<19
(3.5~4.5)倍触头间距
≥19
(4~5)倍触头间距
ASME规范
<19
(3.5~4.3)倍触头间距
≥19
(4~5)倍触头间距
13采用磁轭法进行检测时应注意哪些问题?
JB4730—1994标准(以下简称老标准)中磁轭的磁极间距控制在50~200mm,由于磁极附近会产生漏磁场吸附磁粉形成非相关显示,为排除漏磁场干扰,所以新标准将最小磁极间距扩大到75mm,这一规定与ASME规范一致。
交流电磁场具有集肤效应,因此对表面缺陷有较高的灵敏度。
此外,由于交流电方向不断的变化,使得交流电磁轭的磁场方向也不断变化,这种方向变化可搅动磁粉,有助于磁粉的迁移,从而提高灵敏度。
而直流电磁轭由于其磁场深人工件表面较深,有助于发现较深层的缺陷。
因此在同样的磁通量情况下,磁场深度大,磁力线可穿过面积也大,所以单位面积上的磁感应强度就低,从而降低了检测灵敏度。
有资料表明,直流电磁轭在>6mm的钢板上进行磁粉检测时,尽管电磁轭的提升力满足标准要求(≥177N),但用A型灵敏度试片测试,表面磁场强度往往达不到要求。
一般来说,承压设备表面及近表面缺陷的危害程度较内部缺陷要大。
如果表面和近表面缺陷的检出率高,对于承压设备的安全则比较有利,所以对锅炉、压力容器的焊缝进行磁粉检测时以采用交流电磁轭为好。
而对薄壁压力管道来说,采用直流电磁轭由于其磁场深入工件表面较深,有助于发现较深层的缺陷,可以弥补内部缺陷的检测真空,因此用直流电磁轭为好。
14JB/T4730--2005标准(以下简称新标准)为什么删去平行电缆法?
平行电缆法虽然有与工件非电接触、容易实施磁化的优点,但该方法存在磁力线方向不沿工件切向;磁力线的一部分在空气中通过,使被检工件中的磁场被大大减弱;磁场分布不均匀;磁化规范难以确定等缺点。
由于采用平行电缆法进行磁粉检测时的结果不可靠,故新标准将老标准中列人的平行电缆法删去。
15新标准中对线圈法的有效磁化区是如何规定的?
各种标准对线圈法的有效磁化区的规定是:
(1)老标准规定,线圈法的有效磁化区在线圈端部0.5倍线圈直径的范围内。
(2)ASTME1444—1994a标准规定对于低充填因数线圈法,有效磁化区在线圈中心向两侧延伸0.5倍线圈直径范围,对高充填因数线圈法,磁化有效区是从线圈中心向两侧分别延伸200mm。
(3)美国ASME规范第V卷第7章“磁粉检验”中T-774.2中规定,如果线圈磁化范围扩大到超过线圈任一边150mm(6in)时,其适当的磁场应由T-753的磁场指示器来确定。
为确定线圈法的有效磁化范围,用以下条件进行试验,对材质为35CrMo的两种不同规格工件(φ90mm×760mm和φ52mm×400mm),采用湿连续法油磁悬液,电缆与工件紧密缠绕(高充填因数),中档灵敏度试片C-15/50。
试验结果表明,试片无论是放在电缆中还是放在距电缆端部200mm处,C15/50灵敏度试片上人工缺陷均能清晰显示。
(4)新标准根据试验结果,参照ASME规范,作出相对保守的规定,即线圈法有效磁化区是从线圈端部向外延伸到150mm范围内。
这样规定可以确保磁化强度足够。
另外还规定,对超过150mm以外区域的磁场强度可以采用标准试片确定。
16关于线圈法的磁化规范的规定,新标准与老标准相比有何改变?
(1)ASTME1444—2001标准中对低充填因数线圈纵向磁化的条件是,线圈的横截面积是被检零件横截面积的10倍或更多倍时,即线圈与被检零件横截面积之比y≥10使用公式:
NI=45000/(L/D)
式中:
N—线圈匝数,I—施加在线圈上的磁化电流(A),L—工件长度(mm),D—工件直径或横截面上最大尺寸(mm)
ASMESE-709标准(2001版)中规定的条件为,线圈的内径大大超过零件的内径尺寸(<10%的线圈内径),即y≥100。
在2005年3月新标准定稿会上决定,低、中、高充填因数全部定义为线圈横截面积与工件横截面积比,所以新标准中对低充填因数线圈纵向磁化的条件采用了ASTME1444—2001标准的规定,即y≥10。
(2)老标准中没有中充填因数线圈磁化电流公式,使得应用范围不完整。
新标准中采用了ASMESE-709中列出的磁化电流公式
NI=
式中:
(NI)h——由高充填因数线圈公式计算出的安匝数,(NI)1——由低充填因数线圈公式计算出的安匝数
(3)在低、高充填因数线圈应用公式中的L/D,当计算空心工件时,工件直径应由有效直径Deff代替。
ASMESE-709标准规定,对圆筒形工件:
Deff=
式中:
D0——圆筒外直径,Di——圆筒内直径
对非圆筒形工件
Deff=
式中:
At——零件总的横截面积,Ah——零件中空腔横截面积
(4)老标准中,线圈法的计算公式不适于(L/D)≤3的工件,对于(L/D)≥10的工件,公式中(L/D)取10。
新标准按ASTME1444-2001标准规定,(L/D)最小为2,当(L/D)≥15时取(L/D)=15。
(5)本行业中剩磁法很少使用,也不用(或很少使用)线圈法对工件作剩磁法检验,因此这部分内容就未列入。
17新标准中“质量控制”一节的描述参考了哪些国外标准?
质量控制内容是参照ASMESE-709和JISG0565标准的要求而制订的,国内有些单位在该方面做得不够,因此在标准中专门列一节强调这个问题。
表5为ASMESE-709标准中建议的设备保养和校验时间间隔。
18新标准中对被检工件表面准备有何新的要求?
新标准规定,被检工件表面不得有油脂、铁锈、氧化皮或其它粘附磁粉的物质。
表面的不规则状态不得影响检测结果的正确性和完整性,否则应作适当的修理。
如进行打磨,则打磨后被检工件的表面粗糙度Ra≤25μm。
如被检工件表面残留有涂层,当涂层厚度均匀且≯0.05mm,不影响检测结果时,经合同各方同意,可以带涂层进行磁粉检测。
关于涂层去除问题,ASMESE-709标准(2001版)规定,薄的非导电涂层(数量级约为0.02~0.05mm)一般可能不会干扰显示,检测区及附近非导电涂层或覆盖层>0.05mm时,必须验证证明对最厚涂层处亦能探测出缺陷。
国内也有资料介绍,当涂层厚度为0.5mm时,可以发现A-30/100灵敏度试片上的人工缺陷显示。
因此当涂层厚度≯O.05mm时,可以带涂层进行磁粉检测,但应用触头法时工件和电极接触部分必须清除干净。
新标准送审稿原有“如果涂层更厚,必须证明整个存在最厚涂层的地方能够不妨碍磁粉检测,否则应该去除”,为保守起见,在新标准的最终稿中将此段话删去。
被检工件表面打磨应根据实际情况,表面粗糙度要求由老标准Ra≤12.5μm放宽到Ra≤25μm。
为了增加对比度,允许使用反差增强剂。
19磁粉检测时机应如何选择?
常用的低合金高强钢属于易淬火钢一类。
在焊接过程中,焊缝容易产生冷裂纹。
其中延迟裂纹是常见的一种形式,它不是焊后立即产生,而是在焊后几小时至十几小时或几天后才出现。
若磁粉检测安排在焊后立即进行,就有可能使容易产生延迟裂纹的焊缝的检测变得毫无意义。
因此新标准规定,对于那些有可能产生延迟裂纹的材料,其磁粉检测应安排在焊后24h进行。
应注意的是,焊后24h是《压力容器安全技术监察规程》的最低要求,对于某些产品来说有可能采用更长的时间,这时应按较严格的要求执行。
如GB12337《钢制球形储罐》就明确规定对有可能产生延迟裂纹的材料,其磁粉检测应安排在焊后36h进行。
此外对有再热裂纹倾向的材料在热处理后还应增加一次无损检测。
20使用交叉磁轭式旋转磁场磁粉探伤仪进行检测时,为什么要限制行走速度?
对连续法探伤,磁化时间一般要求1~3S,目的是使缺陷有足够的时间形成磁痕。
同样道理,如果交叉磁轭的行走速度过快,就等于缺陷磁痕的形成时间过短,还没来得及形成缺陷磁痕交叉磁轭已经离开了缺陷位置,从而造成漏检。
21为什么旋转磁场磁粉探伤仪不能用于剩磁法?
用剩磁法检测的首要条件是能够获得足够的剩磁。
因此,当采用交流设备磁化工件时必须配有断电相位控制器。
因为交流电产生的磁场强度在不断的变化,如果不采用断电相位控制,让它能在达到最大剩磁的时限内停止磁化,就不能确保获得最大的剩磁。
而旋转磁场磁粉探伤仪是由两相正弦交变磁场形成的旋转磁场,不仅其磁场的大小在不停的变化,而且其方向也在360°范围内不断地改变。
所以,无论在何时断电,磁场的大小和方向都是未知的,更无法保证获得稳定的最大剩磁。
因此,旋转磁场磁粉探伤仪只能用于连续法,而不能用于剩磁法。
22当采用交叉磁轭式旋转磁场磁粉探伤仪进行检测时,为什么对间隙要加以限制?
磁轭式磁粉探伤仪(包括交流磁轭和交叉磁轭)的工作原理是通过磁轭把磁通导人被检测工件来达到磁化工件的目的。
而磁极与工件之间的间隙越大,等于磁阻越大,从而降低了有效磁通。
当然也就降低工件的磁化程度,结果必然造成检测灵敏度的下降。
此外由于间隙的存在,将会在磁极附近产生漏磁场,间隙越大所产生的漏磁场就越严重。
而间隙产生的漏磁场会干扰磁极附近由缺陷产生的漏磁场,有可能无法形成缺陷磁痕,即使形成磁痕也会被破坏掉。
因此,为了确保检测灵敏度和有效检测范围必须限制间隙,而且越小越好。
对于承压设备,当被检工件表面为一曲面时,它的四个磁极不能很好地与工件表面相接触,会产生某一磁极悬空(在球面上时),或产生四个磁极以线接触方式与工件表面相接触(在柱面上时),这样就在某一对磁极间产生很大的磁阻,其表现为很强的噪声,从而降低了某