自动焊技术在球罐焊接中的应用大会二等奖.docx
《自动焊技术在球罐焊接中的应用大会二等奖.docx》由会员分享,可在线阅读,更多相关《自动焊技术在球罐焊接中的应用大会二等奖.docx(10页珍藏版)》请在冰豆网上搜索。
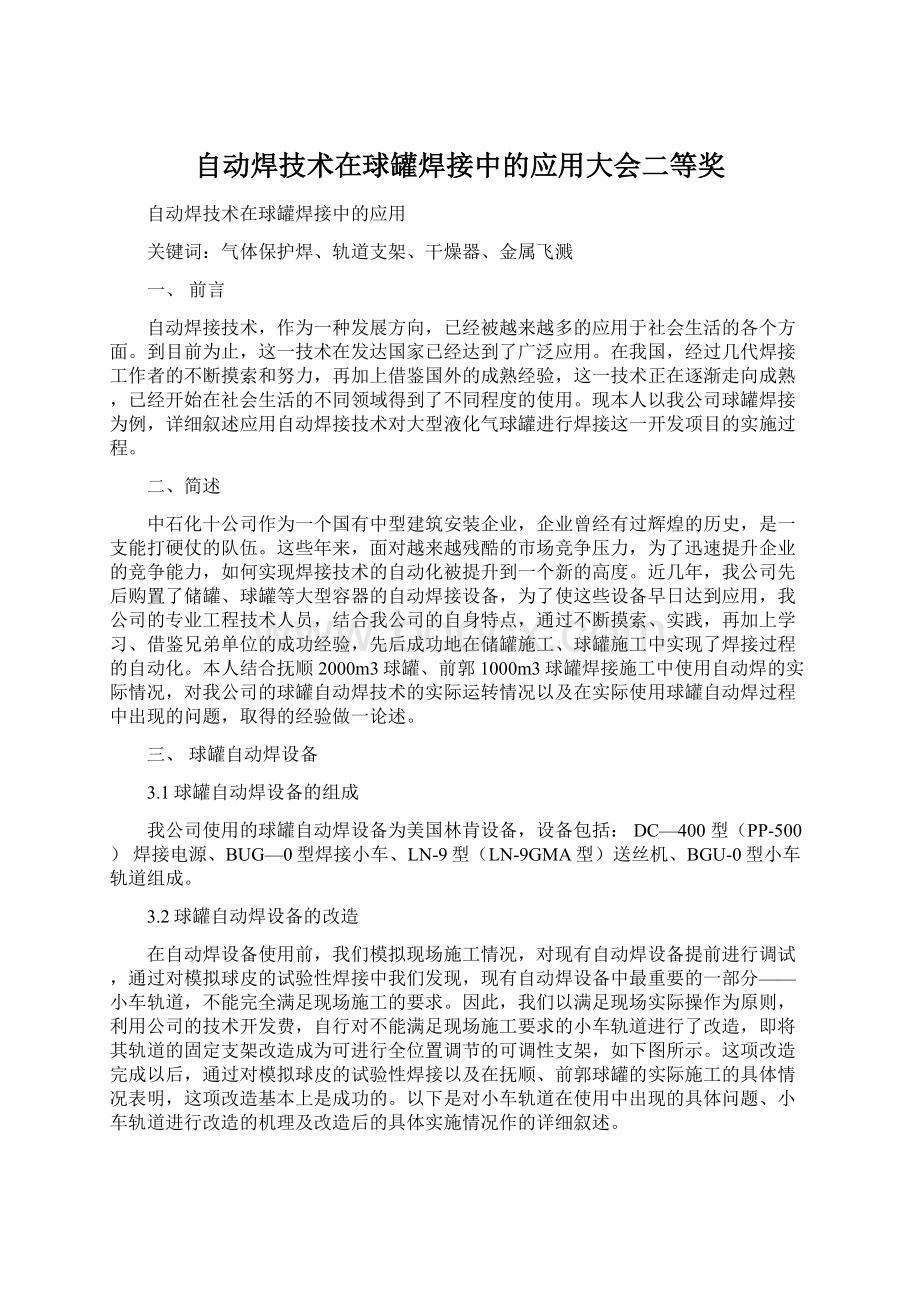
自动焊技术在球罐焊接中的应用大会二等奖
自动焊技术在球罐焊接中的应用
关键词:
气体保护焊、轨道支架、干燥器、金属飞溅
一、前言
自动焊接技术,作为一种发展方向,已经被越来越多的应用于社会生活的各个方面。
到目前为止,这一技术在发达国家已经达到了广泛应用。
在我国,经过几代焊接工作者的不断摸索和努力,再加上借鉴国外的成熟经验,这一技术正在逐渐走向成熟,已经开始在社会生活的不同领域得到了不同程度的使用。
现本人以我公司球罐焊接为例,详细叙述应用自动焊接技术对大型液化气球罐进行焊接这一开发项目的实施过程。
二、简述
中石化十公司作为一个国有中型建筑安装企业,企业曾经有过辉煌的历史,是一支能打硬仗的队伍。
这些年来,面对越来越残酷的市场竞争压力,为了迅速提升企业的竞争能力,如何实现焊接技术的自动化被提升到一个新的高度。
近几年,我公司先后购置了储罐、球罐等大型容器的自动焊接设备,为了使这些设备早日达到应用,我公司的专业工程技术人员,结合我公司的自身特点,通过不断摸索、实践,再加上学习、借鉴兄弟单位的成功经验,先后成功地在储罐施工、球罐施工中实现了焊接过程的自动化。
本人结合抚顺2000m3球罐、前郭1000m3球罐焊接施工中使用自动焊的实际情况,对我公司的球罐自动焊技术的实际运转情况以及在实际使用球罐自动焊过程中出现的问题,取得的经验做一论述。
三、球罐自动焊设备
3.1球罐自动焊设备的组成
我公司使用的球罐自动焊设备为美国林肯设备,设备包括:
DC—400型(PP-500)焊接电源、BUG—0型焊接小车、LN-9型(LN-9GMA型)送丝机、BGU-0型小车轨道组成。
3.2球罐自动焊设备的改造
在自动焊设备使用前,我们模拟现场施工情况,对现有自动焊设备提前进行调试,通过对模拟球皮的试验性焊接中我们发现,现有自动焊设备中最重要的一部分——小车轨道,不能完全满足现场施工的要求。
因此,我们以满足现场实际操作为原则,利用公司的技术开发费,自行对不能满足现场施工要求的小车轨道进行了改造,即将其轨道的固定支架改造成为可进行全位置调节的可调性支架,如下图所示。
这项改造完成以后,通过对模拟球皮的试验性焊接以及在抚顺、前郭球罐的实际施工的具体情况表明,这项改造基本上是成功的。
以下是对小车轨道在使用中出现的具体问题、小车轨道进行改造的机理及改造后的具体实施情况作的详细叙述。
我公司使用的自动焊设备为美国林肯设备,焊接前,在需要焊接的焊道旁,预先铺设小车轨道,小车轨道与焊道保持等距。
焊接过程中,联为一体的焊接行走机构、摆动机构沿着铺设在球皮上的轨道运行,焊接小车的行走速度等于焊接速度;与其一体的焊接摆动机构控制着焊枪的摆动方式及摆动幅度;焊枪摆动幅度的大小来决定着焊缝的熔宽;送丝机控制着焊丝的送进速度、焊接电流及电弧电压。
我们在研究自动焊时发现,自动焊实现的焊缝实际上是一条与轨道完全平行的焊缝,焊缝的熔宽是通过控制焊枪摆动幅度来实现的,预先铺设在球皮上的轨道贴直了,自动焊焊接完成后的焊缝才是一条直线。
焊接过程中为了保证焊接电弧充分熔化到焊道两边,防止焊接缺陷的出现,小车轨道一定要与焊道保持完全等距。
换句话说,成功实现自动焊接的第一步就是:
预先在球罐表面上铺设一条符合要求的小车轨道,让小车轨道从头到尾都与焊道保持完全等距。
我们在实际铺设小车轨道时发现,我们现在使用的轨道是一种半柔性轨道,有一定的弯曲能力(图1示),为美国林肯焊接设备配套产品,轨道型号:
BUG-0型,它使用的轨道支架为等距固定支架,(图2示),使用这种轨道在球罐内外表面铺设时,我们发现最主要的问题就是铺设的轨道无法与焊道保持等距。
为何会出现这种现象呢,我们研究表明,这主要与现有轨道的设计有关。
即现在我们使用的轨道,轨道支架为等距固定式设计,这种设计,在轨道铺设时,轨道平面与铺设体永远保持水平,它产生的等距离线,只能是一条直线或展开线是一条直线,也就是说,轨道只有在平面及由平面围成的柱体表面铺设时,铺设的轨道可以与焊道保持等距,而在球形容器的内外表面铺设时,我们发现了固定支架轨道在设计上的问题。
因为球罐,作为一个球体,它上面的所有焊缝都呈一种曲线状态,在它上面铺设这种等距固定支架的轨道,由于轨道本身的设计局限,它产生的只能是一条直线或展开线是一条直线的等距离线,这种线永远不可能与曲线平行,所以铺设的轨道永远不可能与焊道保持等距。
轨道与焊道不能保持等距,那么在焊接过程中,在轨道上运行的焊接行走机构行走路线与焊道必然不能保持等距,既然焊接行走机构行走路线与焊道不能保持等距,那末在焊接行走机构上运行的焊接摆动机构,一定不可能自动摆动到位。
焊接摆动机构不可能自动摆动到位,实现焊接自动化比较困难。
为了使用这种轨道焊接球罐,我们对现有轨道的支架做了必要的改进,即由原来的固定支架,改为可全方位可调节支架(如图2示)。
这种轨道的设计原理就是:
以球罐焊缝曲率为基准,在离焊道300mm处,利用轨道可调性支架的上下调节,使半柔性轨道弯曲变形,最终在球罐表面铺设出一个柱体形轨道,柱体的曲率与焊缝曲率相同,焊接时,我们让焊接小车在柱体形状轨道上运行,此时在这种柱体轨道上运行的焊接摆动机构,它产生的等距离线,曲率与焊道的曲率完全相同,实际上就是产生了两条等距曲线,实际上也就解决了轨道与焊道不等距的问题。
设计图纸见下图:
原半柔性轨道
轨道固定支架图1
可调性轨道支架图2(改造后)
件1:
旋转件
件2:
固定件
件3:
上下调节件
改造后的可调性半柔性轨道,在可调性轨道支架旋转件、上下调节件的共同作用下,在球罐表面进行铺设时,可以轻易铺设出曲率与焊道的曲率完全相同柱状体,使轨道与焊道成为两条等距曲线,使焊接自动化成为了可能。
3.3球罐自动焊设备的添置
在焊接工作开始前,为了克服保护气体中杂质及水分含量超标对焊接质量的影响,我们在整个保护气体回路中添置了一个自制的CO2气体干燥器
球罐自动焊使用CO2气体做为保护气体。
CO2气体是一种无色、无味的气体,它有三种状态:
固态、液态和气态。
气态CO2只有受到压缩才能变成液态,当不加压冷却时,CO2气体将直接变成固态(干冰)。
固态CO2气体不适于焊接使用,因为空气中的水份会凝结在干冰的表面,当干冰气化时,产生的CO2气体中带有大量的水份,无法进行焊接使用。
我们焊接使用的通常是用钢瓶装的液态的CO2气体,常温下它自己就会气化。
球罐自动焊做为一种气体保护焊,其保护气体CO2的纯度对焊接质量的影响很大,对于焊接来说,CO2气体中主要的有害杂质是水份和氮气。
氮气一般含量较低,对焊缝金属的性能危害不大,对焊缝金属的性能影响最大的还是水份。
根据有关文献表明,同样是大于99.5%纯度的CO2气体,用其中含水量小于0.005%和等于0.05%的两种气体施焊后,前者焊缝金属的韧性比后者好,而且后者易于出现气孔.随着CO2气体中水份的增加,即露点温度的提高,焊缝金属中的含氢量亦增加,如图示。
同时必须注意,在焊缝质量要求较高的情况下,有时CO2气体中水份含量尽管没有高大使焊缝中出现气孔,但由于焊缝金属中含有相当多的氢,其塑性也显著下降。
所以,在使用CO2气体保护焊时,CO2气体的提纯是保证焊接质量的重要手段。
我们采用的手段为:
在二氧化碳气体回路中增加一套低压干燥器,利用干燥器中的干燥剂来减少二氧化碳气体中的杂质含量。
气体干燥器的制作图如下:
在此自制的气体干燥其中,为了便于更换过滤铜网和干燥剂,采用分体式结构,使用法兰进行连接。
同时,为了防止在使用过程中干燥器生锈,影响焊接质量,我们整个结构使用不锈钢来制作。
在件1中我们填充可重复使用的过滤网——200目的铜网
在件2中我们填充可重复使用的干燥剂——无水硫酸铜
1、过滤网2、干燥剂
气体干燥器
气体干燥器的使用原理是:
焊接前在球罐自动焊的焊接回路中加入此干燥罐,焊接开始时,工作气体通过进气嘴进入干燥器,先通过铜网的过滤使工作气体中的杂质被吸附,同时工作气体中的水分被无水硫酸铜吸附,使工作气体中的水分降低到规定范围内,最后,被干燥过的工作气体再次通过铜网的过滤作用将工作气体中夹杂的无水硫酸铜粉尘吸附,出出气嘴进入焊接回路。
此时进入焊接回路的工作气体杂质及水分的含量都非常的低,完全能满足焊接要求。
在使用气体干燥器时,我们必须注意的问题有:
1)无水硫酸铜的烘干
正常情况下,无水硫酸铜颜色为灰白色,具有很强的吸附水分的能力,是当前使用较为广泛的气体干燥剂。
当气体干燥器使用过一段时间以后,作为干燥剂的无水硫酸铜颜色由灰白色逐渐变为包含大量结晶水的颜色呈淡绿色硫酸铜固体。
此时,这种颜色呈淡绿色的硫酸铜固体已不具备吸附水分的能力,必须取出,通过使用350-400℃的高温进行2小时的烘干,将包含大量结晶水的硫酸铜固体中的结晶水烘干、蒸发,使淡绿色的硫酸铜固体重新变为颜色呈灰白色的、具有很强的吸附水分能力无水硫酸铜。
2)过滤铜网的清洗及更换
我们使用200目的铜网做过滤网,过滤铜网的主要作用就是:
吸附保护气CO2气体中存在的杂质、水分、硫酸铜粉尘等。
所以我们在使用干燥器时一定要注意,每隔10天左右,必须及时清洗过滤铜网,以保持其强的吸附杂志的能力。
过滤铜网连续使用10-15次左右,由于其网眼尺寸很小,再通过进行清洗保持其强的吸附能力比较困难,此时可以考虑进行及时更换。
在焊接回路种添加气体干燥器,对工作气体进行干燥,通过抚顺、前郭球罐焊接的实践表明,效果显著,我们在自动焊所有施焊焊缝中,没有发现任何由于保护气体不纯产生的气孔等焊接缺陷。
四、球罐自动焊焊接工艺的改进
4.1采取工艺措施,减少焊接过程中的焊接飞溅
飞溅大是CO2气体保护焊最大的一个缺点,实际操作中我们发现,CO2电弧引燃以后,伴随着轻微的爆破声,大量的金属熔滴四处飞溅。
飞溅大,一方面影响焊件表面的质量,使焊件表面清理困难;同时,焊接过程中大量的金属熔滴的溅出,使焊缝金属的熔敷效率低,增加浪费。
另一方面,大量的金属飞溅极易堵塞焊枪喷嘴,使保护气体的流量降低,破坏保护气体的气体流态,影响保护效果。
为了降低飞溅大产生的这些不利影响,我们在施工当中采用以下措施来降低焊接飞溅。
4.1.1在保护气体CO2中加入氩气
CO2气体在电弧温度区间热导率较高,加上分解吸热,消耗电弧大量热能,引起弧拄及电弧斑点强烈收缩,即使增大电流,弧拄及电弧斑点也很难扩展,这是CO2电弧焊产生飞溅的最主要原因,是由CO2气体本身物理性质决定的。
研究表明,在CO2气体中加入一定数量的氩气,是减少金属飞溅的最有效的办法。
氩气为单原子分子,高温时不分解吸热,导热系数小,电弧热量损失少,电弧燃烧稳定。
但在实际使用过程中,由于氩气的造价比CO2气体高一倍以上,为了减少金属飞溅,无限度的增加氩气含量不是科学的办法。
人们通过实践发现了金属飞溅率与混合气体中氩气比例的关系。
由下表可以看出,随着氩气比例的增加,飞溅逐渐减少
CO2+Ar混合气体中不同比例混合气体飞溅率表
我们在施工中,在一般位置焊接时,本着即降低成本又降低焊接飞溅的目的,在保护气体中加入氩气,混合气体的比例:
50%CO2+50%Ar
4.1.2用药芯焊丝
药芯焊丝,由于在焊丝中部添加了大量的降低飞溅的物质,理论上其飞溅率只有实芯焊丝的1/3。
我们在施工当中,使用了美国林肯焊丝,焊丝牌号:
E712C。
此类焊丝是一种典型的CO2气保护焊焊丝,由合金卷成管状,中间填充焊剂。
实际使用情况表明,使用此类焊丝进行焊接,焊接过程非常平稳,产生的焊接飞溅只有实芯焊丝的一半左右。
4.2改变熔滴过渡形式,实现全位置焊
球罐自动焊在焊接过程中,在正常电流范围内,我们在研究其熔滴过渡形式时发现,它包含两种熔滴过渡形式,即:
短路过渡+大滴过渡组成的混合过渡形式。
使用这种混合熔滴过渡形式在焊缝容易成型的立焊及横焊位置焊接时,电弧燃烧稳定、焊缝成型美观,是一种比较合适的熔滴过渡形式。
虽然由于短路过渡的存在,使整个焊接过程飞溅较大,但我们可以通过使用药芯焊丝、在保护气体中加入适当氩气等措施来减少飞溅。
但是我们在焊接焊缝成型困难的仰脸位置焊缝时,我们发现,在焊接电弧热作用下,焊丝融化,形成液态熔滴,这些液态熔滴倒悬于焊丝端部,通过与仰脸位置的液态熔池金属发生接触,在表面张力及气体吹送力作用下来实现熔滴过渡,在熔滴过渡过程中我们发现,一方面,由于其熔滴尺寸较大,阻止熔滴向上过渡的重力较大,此时,促进熔滴过渡的力:
表面张力+气体吹送力不占明显优势,熔滴过渡困难;另一方面,过渡到熔池金属中的液态金属熔滴,在表面张力作用下,倒悬于熔池金属的表面,由于没有充分的结晶、冷却时间,在较大的重力作用下,极易下流,焊缝成型非常困难。
为了保证仰脸位置焊缝的焊接,我们采取的手段就是:
在仰脸位置焊缝焊接时,改变球罐自动焊的熔滴过渡形式;既由原来的短路过渡+大滴过渡,改变为现在的射滴过渡形式。
这种熔滴过渡形式的特点是:
熔滴尺寸非常小,过渡频率非常高,促进熔滴过渡的作用力非常大。
熔滴尺寸小,促进熔滴过渡的作用力非常大,那末在焊接过程中,熔滴过渡就非常容易,同时由于熔滴尺寸小,在熔池表面很快就能冷却结晶,焊缝成型非常容易。
通过分析表明,为了实现全位置焊接,球罐自动焊的熔滴过渡形式在仰脸位置焊接时必须改变为射滴过渡形式。
如何实现这种熔滴过渡形式的改变,关键就是在焊接过程中使焊接电流必须达到一个特殊的值:
射滴过渡临界电流。
换句话说,球罐自动焊在使用过程中,当其焊接电流达到或超过射滴过渡临界电流值时,出现射滴过渡,就可以实现仰脸位置的焊接。
我们在研究射滴过渡临界电流值时,发现该电流的大小与焊丝直径、焊丝材料、焊丝伸出长度、保护气体成分有关。
焊丝直径越小,射滴过渡临界电流值越低;焊丝材料电离电位越低,射滴过渡临界电流值越低;在保证电弧燃烧稳定的前提下,焊丝伸出长度越短,射滴过渡临界电流值越低;在焊丝直径、焊丝材料、焊丝伸出长度一定的前提下,对射滴过渡临界电流值影响最大的就是:
保护气体成分。
在通常情况下,在焊丝材料一定的前提下,焊接电流必须限制在一定范围内,否则电弧特性及材料都会发生变化,无法进行正常焊接。
射滴过渡临界电流值不能过高,临界电流值越高,实现射滴过渡越困难。
为了实现射滴过渡,我们采取最多的手段就是:
改变保护气体成分。
即向:
CO2气体中加入大量的氩气,形成富氩环境,大大降低射滴过渡临界电流值,使射滴过渡容易实现。
保护气体成分与射滴过渡临界电流值的关系曲线见下图:
保护气体成分与射滴过渡临界电流值的关系
在实际施工中我们使用的混合气体的比例为:
20%CO2+80%Ar
射滴过渡临界电流值:
210—220A。
在仰脸位置焊缝焊接过程中,在富氩的保护气体气氛中,当焊接电流调到规定数值时,就会出现非常明显的射滴过渡形式,此时,熔滴尺寸非常小,过渡频率非常高,形成的熔池金属熔深大,熔池体积小,焊缝金属成型非常美观。
五、球罐的焊接
在球罐施工中我们发现,球罐焊缝没有真正意义上的平、立、横、仰位置焊缝,其实都是一些非常规的属于变形状态的平、立、横、仰位置焊缝,在焊接这些非常规位置焊缝时,实践经验表明,单纯使用自动焊这一单一手段进行焊接有许多位置焊缝根本不能进行焊接,勉强进行的,实际效果也比较差。
通过分析、总结,我们得出结论:
在不同的焊缝位置上我们必须交叉使用自动焊、半自动焊、手弧焊等焊接方法,只有充分利用各种焊接方法的优点,才能保证我们在使用球罐自动焊接设备进行球罐焊接时,获得较为满意的结果。
5.1“丁”字焊缝的焊接。
球罐焊接前,一般先焊接立缝与环缝交界处的焊缝,这类焊缝又称“丁”字焊缝。
在焊接“丁”字焊缝时,如果只使用自动焊,在焊接过程中我们就会发现,由于球罐自动焊焊枪的喷嘴尺寸较大,在焊接“丁”字口处焊缝时,由于坡口阻挡,焊枪根本不易摆动到位,焊枪摆动不到位,焊接电弧就熔化不到坡口边缘的母材金属,熔化不到母材金属就必然会形成大量的未熔合等焊接缺陷。
在焊接“丁”字焊缝时,我们可以充分利用手弧焊操作简便,易于控制摆动方式和焊条角度这一特点,在自动焊焊接焊接前,先用手弧焊将其“丁”字口处焊缝预先进行焊接,焊接长度300mm左右,并且每层都预先留出适合于自动焊接的接头。
这样一来,即解决了“丁”字口焊缝难焊接这一问题,又可以通过预先封闭焊缝两端,使焊接过程中焊肉易于开裂这一问题得以解决。
5.2赤道带立缝的焊接
以2000立球罐焊接为例,赤道带焊缝共20条,我们使用10台焊机对称进行焊接,我们采用从上向下分段退焊的方法进行焊接,一次性焊接长度为:
3米左右。
焊接顺序为:
先焊大坡口,后焊小坡口。
从打底到盖面,分10-12层焊接完成。
焊接前,在准备焊接的焊缝处画出位置相同的始焊线,打底焊接时,10台焊机从始焊线开始,同时对称进行焊接,从下向上一次性焊接3米,打底焊焊接完成以后,在进行2-12层的填充、盖面焊接时,焊接的每层与上一层之间留出:
20-30mm不焊,这样做的目的是在每层焊缝都为为下段焊缝的焊接留出接头。
10条焊缝焊接完成以后,10台焊机同步向另外对称的10条焊缝移动,焊接方法与开始10条焊缝的焊接完全相同。
大坡口焊接完成以后,小坡口进行气刨清跟,着色检验合格后再进行小坡口的焊接。
5.3碳弧气刨清根后的焊缝的焊接:
球罐自动焊是通过人工调节焊接小车上的摆动机构来控制焊丝摆动,来实现熔宽并确保焊接到位的。
因此它对焊道坡口的规整性要求很高,焊道坡口规整性太差,那么在焊接过程中焊接小车上的摆动机构就不容易摆动到位,摆杆摆动不到位,焊接电弧就熔化不了那部分的母材金属,母材金属不熔化或熔合不充分,那么在那块地方就会出现未熔合等焊接缺陷。
在球罐焊接过程中,正面焊缝焊接完成以后,背面使用碳弧气刨进行清根处理。
清根处理后的焊道坡口非常不规则,焊道底部很狭窄,并且凸凹不平。
焊接时,焊接小车上的摆动机构稍微摆动不到位,焊道底部金属就会出现熔合不好的现象,底部金属熔合不好必然会出现未熔合这一焊接缺陷。
抚顺施工实践证明,自动焊焊接完成以后,出现的最主要的焊接缺陷就是未溶合,出现缺陷的主要部位就是背面焊缝,缺陷深度大约在背面焊缝第一层打底焊位置。
所以如何焊接背面气刨清根后的焊缝是球罐自动焊必须解决的重要技术问题。
为了解决气刨清根后的焊缝的焊接问题,我们施工过程中、在施工结束以后可都进行了大量的实践、总结和研究。
最后得出结论是:
以使用手弧焊、自动焊交叉焊接的方法来达到提高焊接质量这一目的。
具体焊接顺序为:
1)使用手弧焊进行打底焊
焊缝背面清根以后,狭窄并且凸凹不平的第一层打底焊道,我们可以使用手弧焊的焊接方法,充分利用手弧焊易于调整焊条角度,易于摆动到位这一特点,来确保第一层打底焊道底部的母材金属能得到充分熔化。
同时为了便于填充、盖面焊继续使用自动焊,打底焊的焊肉应达到5mm左右,这样一来,既可以使不规则的焊道底部充分熔化,保证底部所有不规则位置都能被手弧焊熔合好,又可以为接下来自动焊填充、盖面焊提供了一个较好的焊接条件。
2)使用自动焊进行填充、盖面焊
手弧焊打完底以后,此时焊道底层较为平整,已经满足于自动焊的施焊要求,但此时坡口两侧母材金属仍然是凸凹不平,不利于自动焊焊接,所以,在使用自动进行填充焊接时,为使焊道两侧的母材金属熔合好,可以使用分层、分道的焊接手段来进行焊接,所谓分层、分道焊接就是指在焊接过程中调整焊枪角度,让焊枪直接对准坡口一侧金属进行焊接,让焊接电弧直接、充分的熔化坡口一侧的母材金属,以杜绝电弧熔化不到位的问题出现。
也就是说:
分层、分道的焊接手段可以保证坡口内侧的所有位置都能被焊接电弧充分熔化,从而达到彻底消除未熔合这一焊接缺陷的目的。
5.4上下极带的小环形焊缝的焊接:
上下极带的小环形焊缝在焊接位置上处于环焊缝与立焊缝位置之间,在焊接过程中,纯粹使用环缝或立缝的焊接手法都不合适,在抚顺球罐的施工过程中,在这个位置上实验性质的使用过自动焊的多种摆动方式包括使用横焊操作手法,实际效果都不明显。
我们专门为此研究了手弧焊在这个位置上进行焊接时的焊接操作特点,发现手弧焊在这一特殊位置上焊接时,使用的是:
压道焊接加上斜拉式摆动方式进行焊接,这一特殊焊接方式正好涵盖了焊立缝、焊环缝两种摆动方式的特点。
手弧焊在这一位置焊接时使用的特殊摆动方式在球罐自动焊上根本无法实现。
在小环形这一特殊焊接位置上进行焊接时,可以考虑使用球罐自动焊上的半自动焊这一功能,让自动焊工手持焊枪,开启半自动开关使用先进行压道焊接,再进行斜拉摆动方式进行焊接。
这样即保证了焊接小环形焊缝需要的特殊操作手法,又能实现自动焊的焊接高效率,还能降低焊工的劳动强度。
5.5横焊焊缝的焊接:
使用球罐自动焊进行横焊焊缝焊接的最大问题就是环形轨道无法铺设。
为此,施工前我们利用公司技术开发费专门进行了轨道支架的可调性改造,改造后的轨道可以很轻易的在任何焊接位置上进行铺设。
也就是说:
在设备上我们为球罐环焊缝焊接做好了必要的准备。
在球罐环焊缝焊接过程中,我们可以在预先铺设好的环形轨道上,利用压道技术进行焊缝的焊接。
5.6仰脸焊缝的焊接:
在仰脸位置焊缝焊接时,我们可以通过气体配比器向保护气体中添加Ar气,大大降低临界电流,改熔滴过渡形式由短路过渡到射滴过渡,使仰脸位置焊缝易于焊接成型。
六、结束语
抚顺2000m3球罐、前郭1000m3球罐使用自动焊进行焊接的实际情况表明,自动焊技术在球罐焊接中的使用,可以大大降低施焊焊工的劳动强度,提高球罐焊接的速度和质量,是以后应当大力提倡、推广的新型技术。
参考文献
1、《焊接方法及设备》姜焕中主编机械工业出版社1981
2、《气体保护焊工艺及设备》王震征主编国防工业出版社1982
3、《气体保护焊》张修智主编电力工业出版社1982
4、《关于熔化极气体保护焊熔滴过渡的分类与名称问题》焊接学报1983
5、《熔化电焊设备》西安交通大学中国工业出版社1961
6、《气体保护焊译文集》哈儿滨焊接研究所1975
7、《熔焊原理》苏A.A叶罗欣主编赵裕民译机械工业出版社1980