渗透检测三级考试工艺总结1.docx
《渗透检测三级考试工艺总结1.docx》由会员分享,可在线阅读,更多相关《渗透检测三级考试工艺总结1.docx(54页珍藏版)》请在冰豆网上搜索。
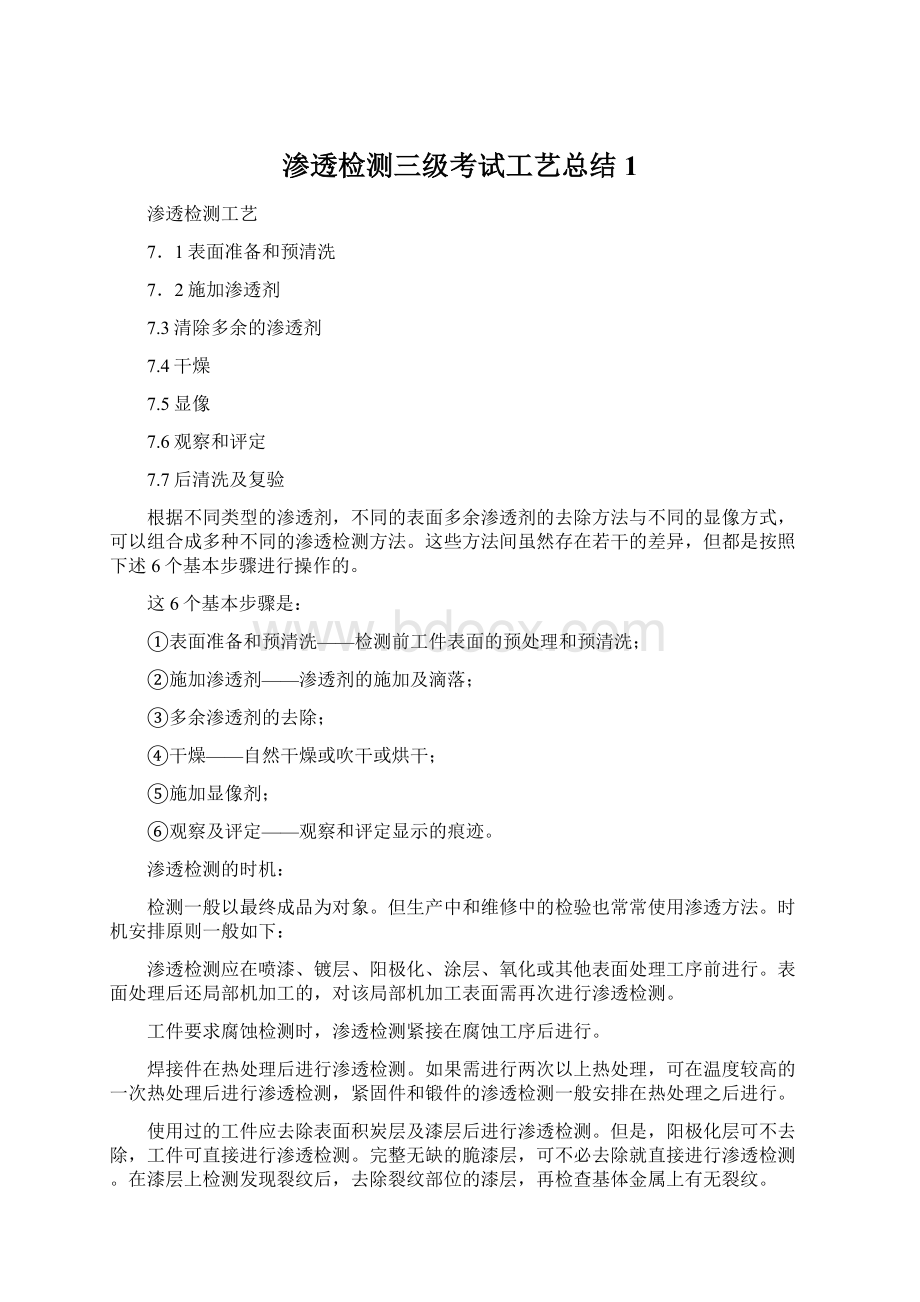
渗透检测三级考试工艺总结1
渗透检测工艺
7.1表面准备和预清洗
7.2施加渗透剂
7.3清除多余的渗透剂
7.4干燥
7.5显像
7.6观察和评定
7.7后清洗及复验
根据不同类型的渗透剂,不同的表面多余渗透剂的去除方法与不同的显像方式,可以组合成多种不同的渗透检测方法。
这些方法间虽然存在若干的差异,但都是按照下述6个基本步骤进行操作的。
这6个基本步骤是:
①表面准备和预清洗——检测前工件表面的预处理和预清洗;
②施加渗透剂——渗透剂的施加及滴落;
③多余渗透剂的去除;
④干燥——自然干燥或吹干或烘干;
⑤施加显像剂;
⑥观察及评定——观察和评定显示的痕迹。
渗透检测的时机:
检测一般以最终成品为对象。
但生产中和维修中的检验也常常使用渗透方法。
时机安排原则一般如下:
渗透检测应在喷漆、镀层、阳极化、涂层、氧化或其他表面处理工序前进行。
表面处理后还局部机加工的,对该局部机加工表面需再次进行渗透检测。
工件要求腐蚀检测时,渗透检测紧接在腐蚀工序后进行。
焊接件在热处理后进行渗透检测。
如果需进行两次以上热处理,可在温度较高的一次热处理后进行渗透检测,紧固件和锻件的渗透检测一般安排在热处理之后进行。
使用过的工件应去除表面积炭层及漆层后进行渗透检测。
但是,阳极化层可不去除,工件可直接进行渗透检测。
完整无缺的脆漆层,可不必去除就直接进行渗透检测。
在漆层上检测发现裂纹后,去除裂纹部位的漆层,再检查基体金属上有无裂纹。
磨削、焊接、矫直、机械加工和热处理等操作,如果可能产生表面缺陷,渗透检测则应在这些操作完成后进行。
对有延迟裂纹倾向的材料,至少应在焊接完成24h后进行焊接接头的渗透检测。
渗透检测通常在喷丸和研磨操作前进行,如果在其后进行,则应进行包括腐蚀在内的预清洗操作,使表面开口缺陷完全开口。
7.1表面准备和预清洗
检测部位的表面状况在很大程度上影响着渗透检测的检测质量。
任何渗透检测成功与否,在很大程度上取决于被检表面的污染程度及粗糙程度。
所有污染物会阻碍渗透剂进人缺陷。
另外,清理污染过程中产生的残余物反过来也能同渗透剂起反应,影响渗透检测灵敏度。
被检表面的粗糙程度也会影响渗透检测效果。
受检工件表面准备和预清洗的基本要求是,任何可能影响渗透检测的污染物必须清除干净;同时,又不得损伤受检工件的工作功能。
例如:
不得用钢丝刷打磨铝、镁、钛等软合金,密封面不得进行酸蚀处理等。
被检工件经过机加工的被检表面一般要求粗糙度R。
≤12μm;非机加工表面粗糙度可以适当放宽,但不得影响渗透检测结果。
对受检工件表面进行局部检测时,也应在渗透检测前,进行表面准备和预清洗。
一般渗透检测工艺方法标准规定:
渗透检测准备工作范围应从检测部位四周向外扩展25mm。
通常情况下,焊缝、轧制件、铸件、锻件的表面状态,是可以满足渗透检测要求的。
当焊缝、轧制件、铸件、锻件表面的不规则外形,影响渗透检测效果;或铁锈、型砂、积炭等;物,可能遮盖拒收缺陷迹痕,或对检验效果产生干扰时,必须用打磨方法或机械加工方法进行表面处理。
打磨方法或机械加工方法可能堵塞表面缺陷的开口,降低渗透检测效果。
特别是对铝、镁、钛等软合金。
因此,打磨、机械加工后,应进行酸蚀处理;喷丸后,也应进行酸蚀处理。
在渗透检测的表面准备和预清洗中,要防止由于清理和清洗方法的不当,造成缺陷的堵塞。
人们往往忽视清洗方法的正确运用。
例如,采用化学方法和溶剂去除方法时,应尽量避免浸泡或刷洗法,杜绝压力水喷的方式。
在不得已采用浸泡、刷洗或压力水喷法的场合,必须注意随后的干燥,防止可能造成的浸润堵塞。
这是因为,任何残余的液体都会阻碍渗透剂的渗入。
因此,必须采取相应措施,例如,烘烤或吸附方法,使缺陷重新暴露,其问只充满空气。
7.1.1污染物类别及其对渗透检测的影响
被检工件常见的污染物包括:
铁锈、氧化皮、腐蚀产物;
焊接飞溅、焊渣、铁屑、毛刺;
油漆及其他有机防护层;
发蓝层、阳极化层及磷酸盐、铬酸盐转化的涂层。
预清洗是渗透检测的第一道工序,用于清洗受检工件表面以下液体污物:
防锈油、机油、润滑油及含有有机组分的其他液体;
水和水蒸发后留下的化合物;
强酸、强碱及包括卤素在内的有化学活性的残留物。
应当指出,不仅要清除被检面上原来的污物,而且要清除表面准备过程中所产生的残余物。
所有污染物对渗透检测的影响
至少有如下几点:
①妨碍渗透剂对受检工件的润湿,妨碍渗透剂渗入缺陷,甚至完全堵塞缺陷。
②妨碍显像剂对缺陷中的渗透剂的吸附,影响缺陷迹痕显示的效果。
③缺陷中的污染物,会与渗透剂混合,甚至发生作用,降低渗透剂的灵敏度及其性能;
有些污染物,例如酸和铬酸盐,会影响荧光染料发光。
④有些污染物,会引起虚假显示;有些污染物,会掩盖显示;所有污染物,都会污染渗透剂、显像剂等渗透检测剂。
7.1.2清除污染物的方法
进行表面准备和预清洗前,选择合适的方法是非常重要的。
常用的方法有:
机械清理、化学清洗、溶剂清洗。
但是,不论选择哪种方法,都不是万能的。
例如,溶剂清洗剂不能清洗锈蚀产物、氧化皮、焊瘤、飞溅物以及普通无机物;蒸气去油不能清洗无机型污物(夹渣、腐蚀、盐类等),也不能清除树脂型污物(塑料涂层、清漆、油漆等)。
选择预清洗方法时,必须考虑如下几点:
①必须了解污染物的类别,有针对性地选用合适的预清洗方法。
因为,没有一种预清洗方法是万能的。
应注意,溶剂蒸气除油、超声清洗及水基清洗剂在内的溶剂洗涤,是用于去除油脂及蜡等污染物的方法。
碱清洗、酸蚀处理等化学清洗是用于清除油漆、釉子、锈皮、积炭或用溶剂清洗法去不掉的其他污染物的方法。
机械清理与表面修整是用于清除焊渣、飞溅、泥土或用溶剂清洗和化学清洗不能清除的其他污染物的方法。
②必须了解选用的预清洗方法,对被检工件的影响。
选用的预清洗方法,不得损伤被检工件的工作功能。
例如,前已叙述,密封面不得进行酸蚀处理。
应该注意,为个别部位选择的清洗用物质,例如化学清除剂、溶剂及腐蚀剂等,应与被清除的污染物相容,而且应不损伤被检工件表面及其预期功能。
③必须了解选用的预清洗方法的实用性。
例如:
被检大工件不能放在小型除油槽中去进行除油。
几种常用的表面准备和预清洗的方法。
1.机械清理与表面修整
包括振动光饰、抛光、干吹砂、湿吹砂、钢丝刷、砂轮磨等。
振动光饰适用于去除轻微的氧化皮、毛刺、锈蚀、铸件型砂或模料等,不能用于铝镁、钛等软金属材料。
抛光适用于去除被检工件表面的积炭、毛刺等。
干吹砂适用于去除氧化皮、熔渣、铸件型砂、模料、喷涂层和积炭等。
湿吹砂可用于清除比较轻微的沉积物。
如果不会使金属表面硬化或使表面缺陷被磨料封堵或污染的话,可以用吹砂打磨来清理金属表面。
钢丝刷和砂轮磨用于去除氧化皮、溶渣、铁屑、铁锈等。
应注意,涂层必须用化学法去除,不能用打磨法去除。
用机械方法清除污物时产生的金属细末、砂末等可能堵塞缺陷。
所以,经过机械处理的受检工件,渗透检测前一般应进行酸洗或碱洗。
焊接件和铸件吹砂后可不酸洗或碱洗而进行渗透检测;精密铸造的关键受检工件,如涡轮叶片等,吹砂以后必须酸洗方能渗透检测。
喷丸法处理后的被检工件也应进行酸洗或碱洗。
渗透检测通常安排在喷丸前进行。
2.碱洗及蒸汽清洗
碱洗适用于去除油污、抛光剂、积炭等,多用于铝合金。
碱洗液是一种不易燃的水溶液,含有经过特别选择的洗涤剂。
该洗涤剂能够对各类污物起润湿、渗透、乳化及皂化作用。
热的碱洗液还可用来除锈和除垢,清除掩盖表面缺陷的氧化皮。
碱洗液应按照制造厂的建议使用。
注意,采用碱洗工艺清洗后的被检工件,必须把清洗剂冲洗干净;并在渗透检测前,将其整体加热干燥;施加渗透剂时,被检工件温度一般不得超过50℃。
蒸汽清洗是一种改进的热碱清洗方法,在容器内进行。
适用于大型被检工件。
能够清除被检工件表面的无机污物和各种有机污物,但无法清除较深缺陷底部的污物。
此时,可采用溶剂浸泡法。
3.酸洗处理
(1)酸洗处理的作用
①酸洗处理可以清除被检表面的锈蚀。
②酸洗处理可以清除可能掩盖表面缺陷,并且可能妨碍渗透剂渗入表面开口缺陷的氧化反。
③被检工件经打磨、机械加工后,进行酸洗处理时,可以清除封闭表面开口缺陷的金属量束JJ。
喷丸后,进行酸洗处理,可以清除由于喷丸形成的封闭表面开口缺陷的细微金属物。
例如:
经过机加工的软金属经过酸洗后,可以去除可能掩盖开口缺陷的金属粉末。
(2)酸洗处理时的注意事项
①酸和铬酸盐将会影响荧光染料的发光作用。
因此,酸洗处理后的被检工件必须清洗干净,使被检表面呈中性;并且在施加渗透剂前,充分干燥。
②被检工件被酸洗液作用后,可能发生氢脆。
因此,酸洗处理后的被检工件应进行去氢处理;并且在施加渗透剂前,将被检工件冷却至50℃以下。
例如:
高强度钢酸洗时,容易吸收氢气,产生氢脆现象。
因此,应进行去氢处理。
去氢条件一般为,在200℃左右温度下,烘烤3h。
去氢应在酸洗后尽快进行。
③酸洗时,要严格控制时间,防止被检表面腐蚀严重。
强酸溶液用于去除严重的氧化皮,中等强度的酸溶液用于去除轻微氧化皮,弱酸溶液用于去除被检表面薄层金属。
④酸洗后要进行中和处理,然后在流动水中进行彻底的清洗。
清洗后要烘干越检工件,以去除被检表面上可能渗入缺陷中的水分。
⑤酸洗处理,应按制造厂推荐意见进行。
4.溶剂去除
包括溶剂蒸气除油和溶剂液体清洗。
溶剂蒸气除油通常为三氯乙烯蒸气除油。
溶剂液体清洗通常用酒精、丙酮或汽油、三氯乙烯等溶剂清洗或擦洗,常用于大工件局部区域的清洗。
有许多溶剂能有效地用来溶解油脂、油膜、蜡、密封胶、油漆及普通有机污物等。
溶剂应无残留物,尤其是在采用手动、液浸法时更应特别注意。
溶剂不能去除锈蚀、氧化皮、焊瘤、飞溅物以及普通无机物。
有些溶剂是易燃物质,有些则可能还有毒,所以,应按照制造厂说明书和注意事项进行操作使用。
溶剂蒸气除油是清除受检工件表面和开口缺陷处的油和油脂类污染物的较好方法。
但它不能清除无机型污染物(如夹渣、腐蚀、盐类等),也不能清除树脂类(例如,塑料、涂层、清漆、油漆等)。
三氯乙烯是一种无色、透明的中性有机化学溶剂,沸点86.7℃,比汽油溶油能力强,蒸气密度可达4.54g/L,容易形成蒸气区。
三氯乙烯蒸气除油操作十分方便,只需将受检工件放人蒸气区中,蒸气便迅速在受检工件表面冷凝,而将受检工件表面的油污溶解掉。
除油过程中,受检工件表面温度不断上升,达到蒸气温度时,除油也就结束了。
三氯乙烯在使用过程中易受热、光、氧的作用分解成酸性,因此,在使用过程中要经常测量酸度值。
若需要将深缺陷中的油脂全部清除干净时,建议采用溶剂浸泡法。
钛合金被检工件容易与卤族元素作用,产生应力腐蚀裂纹,因此,钛合金应采用添加特殊抑制剂的三氯乙烯进行除油,并且在除油前必须进行处理,以消除应力。
橡胶、塑料及涂漆被检工件不能使用三氯乙烯蒸气除油,因为这些被检工件会受到三氯乙烯的破坏。
也不得使用会对其产生有害影响的溶剂除油。
必要时,应通过试验,确认所使用的溶剂是否会对被检橡胶、塑料工件产生有害影响。
另外,还应注意温度对其的影响。
铝、镁合金被检工件在除油后,容易在空气中锈蚀,应尽快浸人渗透剂中。
5.洗涤剂清洗
洗涤剂清洗液是一种不易燃的水溶液,含有特殊的表面活性剂,能够对各类污染物(如油脂、油膜、切削加工润滑油等)起润湿、渗透、乳化及皂化作用。
洗涤剂清洗液可分为碱性、中性和酸性三类,选定的清洗液对被检工件应无腐蚀作用。
采用洗涤剂清洗,可以很容易地将被检工件表面和缝隙内的污染物清除干净。
清洗时间一般应为10~15rain。
清洗温度一般可为75~95℃。
浓度应按照制造厂的推荐值(一般为45~60kg/m。
)。
清洗时应作适当搅动。
6.超声波清洗
超声波清洗利用超声波的机械振动,去除被检工件表面的油污。
它常与洗涤剂或有机溶剂配合使用。
这样可提高清洗效果、减少清洗时间,便于大批量小工件检测。
如果是清除无机污物,例如,清除锈蚀、夹渣、盐类、腐蚀物等,则应辅以水和洗涤剂。
如果是清除有机污物,如油脂、油膜等,则应辅以有机溶剂。
超声清洗后,施加渗透剂前,应加热被检工件,以去除溶剂或洗涤剂。
然后,将被检工件冷却至50℃以下。
7.去漆处理
根据油漆的化学成分,有针对性地选择的去漆剂,能够有效地去除被检表面的油漆膜层。
一般情况下,去除漆层时,可以采用热的碱洗液清洗,还可采用特殊的去漆剂。
油漆膜层必须完全除掉,直至露出金属表面。
去漆后,应使被检工件表面充分干燥。
:
8.陶瓷的空气焙烧
空气焙烧法适用于去除陶瓷被检工件的水分或有机污染物。
一般在低于1000℃的清洁的氧化环境中加热陶瓷,是去除水分和有机污染物的有效方法。
加热的最高温度应不降低陶瓷的性能。
吹砂对裂纹显示的影响:
试样上的原始裂纹经吹砂后,显示非常模糊。
酸洗处理后,显示变得清晰。
试样经过去毛刺抛光处理后,原始裂纹数量明显减少,酸洗处理后,原始裂纹显示非常清晰.
7.2施加渗透剂
7.2.1渗透剂施加方法
渗透剂施加方法应根据被检工件大小、形状、数量和检查部位来选择。
所选方法应保证被检部位完全被渗透剂覆盖,并在整个渗透时间内保持润湿状态。
具体施加方法如下:
喷涂:
静电喷涂、喷罐喷涂或低压循环泵喷涂等。
适用于大工件的局部或全部检查。
刷涂:
刷子、棉纱、抹布刷涂。
适用于局部检查、焊缝检查。
浇涂(流涂):
将渗透剂直接浇在受检工件表面上。
适用于大工件的局部检查。
浸涂:
把整个被检工件全部浸入渗透剂中。
适用于小工件的表面检查。
7.2.2渗透时间及温度
1.渗透时间
渗透时间指施加渗透剂到开始去除处理之间的时间。
采用浸涂法施加时,还应包括排液所需的时间。
这时它是施加渗透剂时间和滴落时间之和。
被检工件浸涂渗透剂后,应进行滴落,以减少渗透剂的损耗。
滴落时,排除被检工件表面流淌的渗透剂所需的时间称滴落时间。
因为渗透剂在滴落过程中仍在继续往缺陷中渗透,所以滴落时间是渗透时间的一部分。
滴落过程中,渗透剂中的挥发物质被挥发掉,使渗透剂中的染料浓度相对提高,即提高了渗透检测灵敏度。
渗透时间又称接触时间或停留时间。
被检工件不同,要求发现的缺陷种类和大小不同,被检表面状态不同及所用渗透剂不同,渗透时间的长短也不同。
一般渗透检测工艺方法标准规定:
在10~50℃的温度条件下,施加渗透剂的渗透时间一般不得少于10min。
对于怀疑有缺陷的被检工件,渗透时间可相应延长,或者额外施加渗透剂,以保证缺陷内渗入足够的渗透剂。
应力腐蚀裂纹特别细微,渗透时间需更长,甚至长达2h。
2.渗透温度
渗透温度一般控制在10~50℃范围内。
温度太高,渗透剂易干在被检工件上,给清洗带来困难;温度太低,渗透剂变稠,动态渗透参量受影响。
为提高检测细小裂纹的灵敏度,可将渗透温度控制在10~50~C范围的上限。
当渗透检测不可能在10~50~C的标准温度范围内进行时,则应用铝合金淬火试块作对比试验,对操作方法进行修正。
图7~3所示,为两种不同温度下的着色渗透检测试验结果。
A型试块左边的渗透温度为120℃,右边为30℃。
7.3去除多余的渗透剂
本步骤要求去除被检工件表面上多余的渗透剂,又不将已渗入缺陷中的渗透剂清洗出来。
水洗型渗透剂直接用水去除,后乳化型渗透剂经乳化后再用水去除,溶剂去除型渗透剂用有机溶剂擦除。
去除渗透剂时,要防止过清洗或过乳化;同时,为取得较高灵敏度,可使荧光背景或着色底色保持在一定的水准上。
但是,也应防止欠洗,防止荧光背景过浓或着色底色过浓。
这一步骤完成得如何,在一定程度上取决于操作者以往取得的经验。
7.3.1水洗型渗透剂的去除
水洗型渗透剂可用水喷法清洗。
一般渗透检测工艺方法标准规定:
水射束与被检面的夹角以30。
为宜,水温为10~40℃,冲洗装置喷嘴处的水压应不超过0.34MPa。
水洗型荧光渗透剂用水喷法清洗时,应使用粗水柱,喷头距离受检工件300mm左右,并注意不要溅人邻近槽的乳化剂中。
应由下而上进行,以避免留下一层难以去除的荧光薄膜。
水洗型渗透剂中含有乳化剂,所以水洗时间长,水洗压力高,水洗温度高。
这便有可能把缺陷中的渗透剂清洗掉,产生过清洗。
在得到合格背景的前提下,水洗时间越短越好。
荧光渗透剂的去除,可在紫外灯照射下边观察边进行。
着色渗透剂的去除应在白光下控制进行。
除水喷洗外,去除方法还有手工水擦洗、空气搅拌水浸洗方法。
7.3.2后乳化型渗透剂的去除
后乳化型渗透剂的去除方法因乳化剂不同而不同。
施加亲水性乳化剂的操作方法是先用水预清洗,然后乳化,最后再用水冲洗。
施加乳化剂时,只能用浸涂、浇涂或喷涂(喷涂浓度不超过5%)。
不能刷涂,因为刷涂不均匀。
预水洗的目的是尽量多地洗去工件表面多余的渗透剂,减少渗透剂对乳化剂的污染。
预水洗可用压缩空气水喷枪喷洗或浸入搅拌水槽中清洗。
要注意清洗工件上的凹槽、盲孑L和内腔等容易残留渗透剂的部位。
预水洗温度不高于40℃,预水洗时间控制在尽量短的时间范围内。
’
施加亲油性乳化剂的操作方法是直接用乳化剂乳化,然后用水冲洗;施加乳化剂时,只能用浸涂法或浇涂法,不能用刷涂法或喷涂,而且也不能在被检工件上搅动。
乳化工序是后乳化型渗透检测工艺中最关键的步骤。
必须严格控制乳化时间,防止过乳化。
在保证达到允许的着色背景及荧光背景的前提下,乳化时间应尽量短。
工件从乳化槽中取出后,均需进行滴落。
滴落时间是乳化时间的一部分。
即乳化时间等于浸人乳化剂中的时间与滴落时间之和。
乳化时间的影响因素包括工件表面粗糙度、乳化剂浓度、乳化剂温度、乳化剂被污染程度和后乳化型渗透剂种类。
需对具体工件,通过试验选择最佳乳化时问。
并且要根据乳化剂被污染,乳化能力不断降低现象,修正乳化时间。
当乳化时间增加到新配制乳化剂乳化时间的2倍以上,还达不到乳化效果时,应更换乳化剂。
一般渗透检测方法标准对乳化时间作了原则上的规定:
亲油性乳化剂的乳化时间在2min内,亲水性乳化剂的乳化时间在5min以内。
乳化剂温度太低,会使乳化能力下降。
一般规定,乳化温度在20~30℃范围较好。
环境温度太低,可将乳化剂加温使用。
乳化结果后,即施加乳化剂后需将工件立即浸入温度不超过40℃的搅拌水中清洗,以迅速停止乳化剂的乳化作用。
亲水后乳化型渗透检测法最终水洗及亲油后乳化型渗透检测法施加乳化剂后水洗,需在白光或黑光灯下进行,以控制清洗质量。
若在白光或黑光灯下发现清洗不干净,说明乳化时间不足。
此时,应将工件烘干,重新对工件进行渗透检测,并增加乳化时间,以达到合格的清洗背景。
当检验要求不太严格时,可直接将工件再次浸入乳化剂中补充乳化,以减少背景。
只要乳化时间合适,即不过乳化,最终水洗时间就不像水洗型渗透检测工艺那样严格,但也应在尽量短的时间内清洗干净。
7.3.3溶剂去除型渗透剂的去除
溶剂去除型渗透剂用清洗/去除溶剂去除。
除特别难清洗的地方外,一般应先用干燥、洁净不脱毛的布依次擦拭,直至大部分多余渗透剂被去除后,再用蘸有清洗/去除溶剂的干净不脱毛布或纸进行擦拭,直至将被检表面上多余的渗透剂全部擦净。
但应注意,不得往复擦拭,不得用清洗/去除溶剂直接冲洗被检面。
7.3.4去除方法与缺陷中渗透剂被去除可能性的关系
图7—4表示采用不同的去除表面多余渗透剂的方法与从缺陷中去除渗透剂的可能性。
从该关系图中可以看出,用不沾有机溶剂的干布擦除时,缺陷中的渗透剂保留最好;后乳化型渗透剂的乳化去除法较好;水洗型渗透剂的水洗去除法较差;有机溶剂清洗去除法最差,缺陷中的渗透剂被有机溶剂清洗掉很多。
在去除操作过程中,如果出现欠洗现象,则应采取适当措施,增加清洗去除,使荧光背景或着色底色降低到允许水准上;或重复处理,即从预清洗开始,按顺序重新操作,渗透、乳化、清洗/去除及显像全过程。
如果出现过乳化过清洗现象,则必须进行重复处理。
7.4干燥
7.4.1干燥的目的和时机
干燥的目的是除去被检工件表面的水分,使渗透剂充分地渗入缺陷或回渗到显像剂上。
干燥的时机与表面多余渗透剂的去除方法和使用的显像剂密切相关。
原则上,溶剂去除法渗透检测时,不必进行专门的干燥处理,应在室温下自然干燥,不得加热干燥。
用水清洗的被检工件,若采用干粉显像或非水湿式显像时,则在显像之前,必须进行干燥处理;若采用水湿式显像剂应在施加后进行干燥处理;若采用自显像,则应在水清洗后进行干燥。
7.4.2常用的干燥方法
干燥的方法有干净布擦干、压缩空气吹干、热风吹干、热空气循环烘干等。
实际应用中是将多种干燥方法组合进行,例如,被检工件水洗后,先用干净布擦去表面明显的水分,再用经过过滤的清洁干燥的压缩空气吹去表面的水分,尤其要吹去盲孔、凹槽、内腔部位及可能积水部位的水,然后放进热空气循环干燥装置中干燥。
另一种方法是在室温下使用环流风扇。
使用这种方法的渗透检测,其灵敏度通常不及使用加热的干燥法。
只有当被检工件由于尺寸或质量等原因,不能使用烘箱时,才使用环流风扇吹干方法。
为加快干燥速度,也可以采用“热浸”技术,即被检工件洗净后,短时间地在80~90℃的热水中浸一下,可提高工件的初始温度,加快干燥速度。
由于“热浸”对被检工件具有一定的补充清洗作用,故一般不推荐采用。
为确保不因“热浸”造成过洗,“热浸”时间严格控制在20s之内。
光洁的机加工面不允许进行“热浸”。
7.4.3干燥温度和时间
干燥温度不能太高,干燥时间不能太长。
否则会将缺陷中渗透剂烘干,不能形成缺陷显示。
过度干燥还会造成渗透剂中染料变质。
允许的最高干燥温度与所用渗透剂种类及被检工件材料有关。
正确的干燥温度需经试验确定。
一般规定:
金属被检工件干燥温度不宜超过80℃,塑料被检工件通常用40℃以下的温风吹干。
干燥时间越短越好,一般规定不宜超过10min。
一般渗透检测工艺方法标准常作总体规定:
干燥时被检工件表面的温度不得大于50℃;干燥时间5~10min。
干燥时间与被检工件材料、尺寸、被检工件水分的多少、工件初始温度和烘干装置的温度等因素有关,还与每批被干燥的工件的数量有关。
为控制最短干燥时间,应控制每批放进烘干装置中的工件数量。
另外,薄截面被检工件或高导热性被检工件不应与干燥速率缓慢的被检工件放在一起干燥,否则,干燥温度及干燥时间很难控制。
干燥时,要防止被检工件筐、吊具上的渗透检测材料及操作者手上的油污对被检工件造成污染,而产生虚假显示或遮盖缺陷显示。
为防止污染,应将干燥后的操作与干燥前的操作隔离开来,例如在自动线上采用分离的两条流水线,第一条线进行除油、渗透和水洗,第二条线进行干燥和显像。
在只有一条线操作的情况下,从干燥工序开始,换一种干净被检工件筐,用于干燥以后的工序,这样效果也很好。
7.5显像
显像的过程是在被检工件表面施加显像剂,利用毛细作用原理将缺陷中的渗透剂吸附至被检工件表面,从而产生清晰可见的缺陷显示图像。
显像时间不能太长,显像剂不能太厚,否则缺陷显示会变模糊。
7.5.1显像方法
常用的显像方法有干式显像、非水基湿式显像、湿式显像和自显像等。
①干式显像:
干式显像也称干粉显像,主要用于荧光渗透检测法。
使用干式显像剂时,须先经干燥处理,再用适当方法将显像剂均匀地喷洒在整个被检工件表面上,并保持一段时间。
多余的显像剂通过轻敲或轻气流清除方式去除。
干粉显像可将被检工件埋人显像粉中进行,也可用喷枪或喷粉柜喷粉显像,但最好采用喷粉柜进行喷粉显像。
喷粉柜喷粉显像是将被检工件放入显像粉末柜中,用经过过滤的干净干燥的压缩空气或风扇,将显像粉末吹扬起来,使呈粉雾状,将被检工件包围住,在被检工件表面上均匀地覆盖一层显像粉末,滞留的多余显像剂粉末,应用轻敲法或用干燥的低压空气吹除。
②非水基湿式显像:
也称溶剂悬浮显像。
非水基湿式显像主要采用压力喷罐喷涂。
喷涂前应摇动喷罐中的弹子,使显像剂重新悬浮,固体粉末重新呈细微颗粒均匀分散状。
喷涂时要预先调节好,调节到边喷边形