日产10000水泥熟料新型干法水泥厂烧成系统工艺设计窑尾.docx
《日产10000水泥熟料新型干法水泥厂烧成系统工艺设计窑尾.docx》由会员分享,可在线阅读,更多相关《日产10000水泥熟料新型干法水泥厂烧成系统工艺设计窑尾.docx(55页珍藏版)》请在冰豆网上搜索。
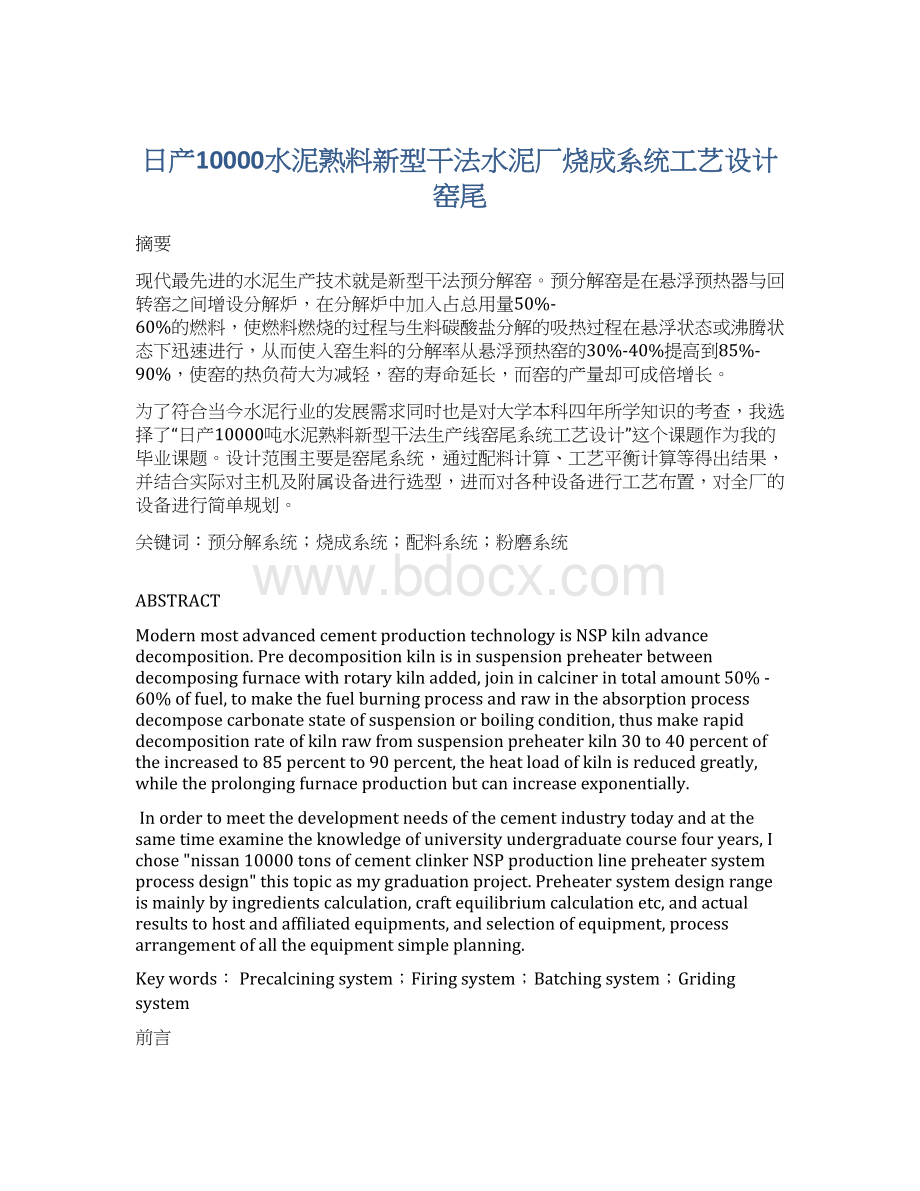
日产10000水泥熟料新型干法水泥厂烧成系统工艺设计窑尾
摘要
现代最先进的水泥生产技术就是新型干法预分解窑。
预分解窑是在悬浮预热器与回转窑之间增设分解炉,在分解炉中加入占总用量50%-60%的燃料,使燃料燃烧的过程与生料碳酸盐分解的吸热过程在悬浮状态或沸腾状态下迅速进行,从而使入窑生料的分解率从悬浮预热窑的30%-40%提高到85%-90%,使窑的热负荷大为减轻,窑的寿命延长,而窑的产量却可成倍增长。
为了符合当今水泥行业的发展需求同时也是对大学本科四年所学知识的考查,我选择了“日产10000吨水泥熟料新型干法生产线窑尾系统工艺设计”这个课题作为我的毕业课题。
设计范围主要是窑尾系统,通过配料计算、工艺平衡计算等得出结果,并结合实际对主机及附属设备进行选型,进而对各种设备进行工艺布置,对全厂的设备进行简单规划。
关键词:
预分解系统;烧成系统;配料系统;粉磨系统
ABSTRACT
ModernmostadvancedcementproductiontechnologyisNSPkilnadvancedecomposition.Predecompositionkilnisinsuspensionpreheaterbetweendecomposingfurnacewithrotarykilnadded,joinincalcinerintotalamount50%-60%offuel,tomakethefuelburningprocessandrawintheabsorptionprocessdecomposecarbonatestateofsuspensionorboilingcondition,thusmakerapiddecompositionrateofkilnrawfromsuspensionpreheaterkiln30to40percentoftheincreasedto85percentto90percent,theheatloadofkilnisreducedgreatly,whiletheprolongingfurnaceproductionbutcanincreaseexponentially.
Inordertomeetthedevelopmentneedsofthecementindustrytodayandatthesametimeexaminetheknowledgeofuniversityundergraduatecoursefouryears,Ichose"nissan10000tonsofcementclinkerNSPproductionlinepreheatersystemprocessdesign"thistopicasmygraduationproject.Preheatersystemdesignrangeismainlybyingredientscalculation,craftequilibriumcalculationetc,andactualresultstohostandaffiliatedequipments,andselectionofequipment,processarrangementofalltheequipmentsimpleplanning.
Keywords:
Precalciningsystem;Firingsystem;Batchingsystem;Gridingsystem
前言
本计的目的、意义、范围和技术性能要求:
通过三年的专业学习,在毕业设计时运用所学的专业知识来设计论文,培养我们综合运用所学的基础理论、专业知识和基本技能,提高分析、解决实际问题能力;提高查阅文献和收集资料的能力,计算机技术和外语应用能力;使我们系统而又熟练地掌握水泥厂工艺流程,具有进行水泥厂主要车间初步设计计算、编写设计说明书等工作能力;进而培养学生创新精神和实践能力,为今后的实际工作打基础。
通过本设计对大学所学知识进行系统应用,培养自己综合运用所学的基本理论、基本知识和基本技能分析解决实际问题的能力,帮助自己建立正确的设计思想和严谨的科学作风。
本次的设计是设计日产10000吨水泥熟料水泥厂新型干法工艺烧成系统窑尾工艺设计,在降低电耗、提高产品煅烧质量的指导思想下进行设计。
主要设计在预热系统、预分解系统、烧成系统,设备的选型如何能在达到生产能力的要求下还能提高产品的质量。
本次设计的设计主要内容是水泥生产的工艺流程,水泥厂区及车间布置和烧成系统主要设备的计算选型等。
因此有必要对烧成系统的设备及其发展进行了解。
当前国内外水泥工业发展现状和存在的问题:
由于我国水泥行业起步比较晚,在国外技术都基本成熟的情况下,我国还是用立窑生产,不仅产量低,而且污染重,耗能高,水泥质量差,所以我国水泥行业起步时,就准备吸收借鉴外国技术,当时中国建材部英明决定同日本三家主要水泥机械制造商进行技术交流。
首先决定冀东水泥厂引进石川岛的SF分解炉预热器窑4000t/d熟料生产线,然后宁国水泥厂引进了三菱的MFC分解炉预热器窑4000t/d熟料生产线等。
之后国内各大水泥行业设计院在引进消化吸收的基础上相继成功开发出自己的预热预5分解系统。
从此中国的水泥新技术如雨后竹笋,迅猛发展。
如像海螺水泥厂现在都已经淘汰所有落后的水泥生产技术,全部是新型干法生产技术,不仅节约了能源,还提高了产量,现在国家大力扶持新技术,逐步关闭落后产能高、污染重的小型水泥厂,我相信中国水泥以后必将走在世界的前列。
新型干法水泥生产技术发展的第一阶段为20世纪50年代初到70年初,是悬浮预热技术诞生和发展阶段,第二阶段是20世纪70年代初至今,是预热分解技术诞生和发展阶段。
50年代德国洪堡公司将世界第一台预热器投入生产,洪堡型旋风预热窑,是把生料的预热和部分分解由预热器来完成,代替回转窑部分回转筒体功能,达到缩短回转窑长度,使生料在回转窑外与气体充分混合,提高换热效率,从而提高窑系统生产效率。
1959年伯力鸠斯公司开时建造第一代多波尔旋风预热器,由于它是双旋风筒的系统,对于很高产量的窑系统很适应,不需要采用几条平行工作预热器系统,又能达到个报告稿的分离效率。
这种多波预热器窑的生产能力可达7200t/d。
之后克虏伯——伯力鸠斯公司发明克波尔逆流悬浮预热器。
窑外分解技术是1971年以来发展起来的一种水泥熟料煅烧新技术,窑外分解锻烧技术就是在悬浮预热器与回转窑之间增设一个分解炉,在其中加人约60%的燃料,与生料紧密混合,使燃料的燃烧过程和生料的吸热分解过程同时在悬浮状态下极其迅速地进行,导致生料在入回转窑时已基本上完全(90~95%)分解。
关于在回转窑后面加一把火,提高生料分解率的设想早在1960年以后就已出现在外国刊物和专利上。
例如1965年一篇文章提出,这里不需要高温,故可利用劣质燃料。
以后不久一份捷克专利建议把熟料锻烧过程分成三个阶段.预热、分解和烧成,分别在不同的设备内进行。
在回转窑后面增设一个专门的装置,加人燃料进行燃烧,使经过预热器预热的生料分解,再人回转窑烧成熟料。
但这些设想都未付诸实现。
1971年日本石川岛公司首先在日本水泥公司进行预分解技术实验获得成功,而后把该公司Φ3.9m×53.5m立波尔窑改建为带SF分解炉的悬浮预热窑,使该窑日产量提高一倍,达到2000t/d。
分解炉的优点使日本小野田公司在1972年先建Φ1.8m×25mRSP实验窑,随后,日本川崎重工业公司和小野田水泥公司分别研制了带KSV型和RSP型分解炉的回转窑,并投人了工业生产。
近两三年西德的伯力鸡斯公司、丹麦的史密斯公司和西德的洪堡公司也相继研制了自己的分解炉型式。
最近几年实现的各种分解炉,如与早期提出的设想对比,明显地有一个共同的特点,就是燃料和生料紧密混合,燃料的燃烧过程和生料的吸热分解过程是在悬浮状态下在同一个空间内迅速地同时进行的,而早期的想法一般都专设一个燃烧炉,燃料在其中燃烧,然后用燃烧废气将热量带人预热器,传给生料,使之分解。
但是最近几年,国际水泥界在工艺方面并未取得新的突破性进展,新技术绝大部分是在上世纪几大创新技术的基础上开发或发展的,这些新技术包括降低热耗、提高自动化程度、扩大生产规模、废物利用、环境保护、产品深加工等方面,都是对原有创新技术的完善和提高,总体上还未出现重大的技术创新。
大量的工作主要还是对新型干法生产工艺全过程进行优化和完善提高方面。
利用以信息技术为主的一大批高新技术对传统的水泥工业进行改造,使其成为可持续发展的绿色产业。
本设计的指导思想和设计路线:
是旋风预热器加预分解炉的窑尾工艺设计,具有生产能力大、产量高、熟料热耗低、环境污染少、预热得到充分利用等技术优势外,还具有熟料煅烧温度高、煅烧均匀、冷却速度快的技术冼势,从而使熟料质量更好。
窑尾预热分解系统:
预分解系统是热工系统,是高温烟气与物料完成换热分离的装备,主要功能是充分利用回转窑和分解炉排出的废气余热加热生料,使生料预热及部分碳酸钙分解。
因此应根据各个工厂不同的海拔、气候、地理优势等自然条件,以及不同的原燃料条件,如成分、运输等.对系统进行最优化的设计。
预热器系统1)推广五级预热器。
通过对预热器系统阻力和分离效率的优化以及热量的综合利用.可以使用五级预热分解系统的综合节热效果投资会节省很多.操作运行也简单许多。
虽然投资成本加大,但具有更高的生产效益,在各各方面都有小号的收益,例如熟料热耗约可以降低20~30kcal/kg熟料.一条5O00t/d的熟料生产线.年节约标煤约4400t~6600t。
2))减小预热器直径,这会带来设备、耐火材料、窑尾框架基建投资降低等一系列好处。
3))预热器分离效率匹配,保证其高效率,.既对降低系统热耗有好处,还能够明显减轻废气处理系统的负担.利于环保减排。
4))预热器的阻力,降阻的关键是优化预热器系统的工艺参数,关键是涡壳、内筒结构及尺寸的优化,5)通过对对适应生料放粗的要求,进行对生料磨针对性设计。
分解炉系统1)一台设计合理的在线型(窑气与炉气混合)燃烧炉对低质煤粉燃烧的适应性强于离线型燃烧炉.因此得出离线型燃烧炉对煤粉适应性好的结论.在线型燃烧炉底具备高温窑气条件,煤粉能够首先喷入高温烟气中快速升温并烘干水分(具备了高温条件).然后随高温烟气上升遇到三次风(具备了氧气条件),使低质煤得以迅速起燃。
所以选择在线型燃烧炉。
2)设计中提高分解炉的用煤比例,减少窑头的用煤比例,其喷煤量占60%,窑头喷煤管处喷40%.总体降低燃料的使用量。
3)分解炉的结构形式力求简单可靠,能最大限度降低生产成本,提高产量。
4)重视料、风、煤人炉位置上的合理匹配,提高碳酸钙的分解,保证碳酸钙的分解率达到90%-95%。
5)降低分解炉的阻力,提高换热效率。
4)主要分解炉介绍:
日本川崎重工KSV炉,主要由下部喷腾层和上部涡室组成。
DD型分解炉,主要由四个区组成,包括还原区、燃料分解和燃烧区、主要燃烧区、完全燃烧区,根据工艺性能分四个区:
流化区、供气区(涡流区)、稀薄流化区、悬浮区。
对于分解炉的选型有;单纯旋流:
虽然能增加物料在炉内的停留时时,但旋流强度过大易造成粉料贴壁运动,对均匀不利。
单纯喷腾:
有利分散和纵向均布,但会造成疏密两区,同时会引起部分物料短路。
单纯流态化:
由于气固参数相一致,降降低传递和反应的推动力,若要反应程度高,对炉温要求相应较高,且阻力损失过大。
简单的湍流:
设备高度过高。
因此,实践结果表明,原来不同类型和结构的分解炉有目趋接近