通用机加件检验作业指导书.docx
《通用机加件检验作业指导书.docx》由会员分享,可在线阅读,更多相关《通用机加件检验作业指导书.docx(10页珍藏版)》请在冰豆网上搜索。
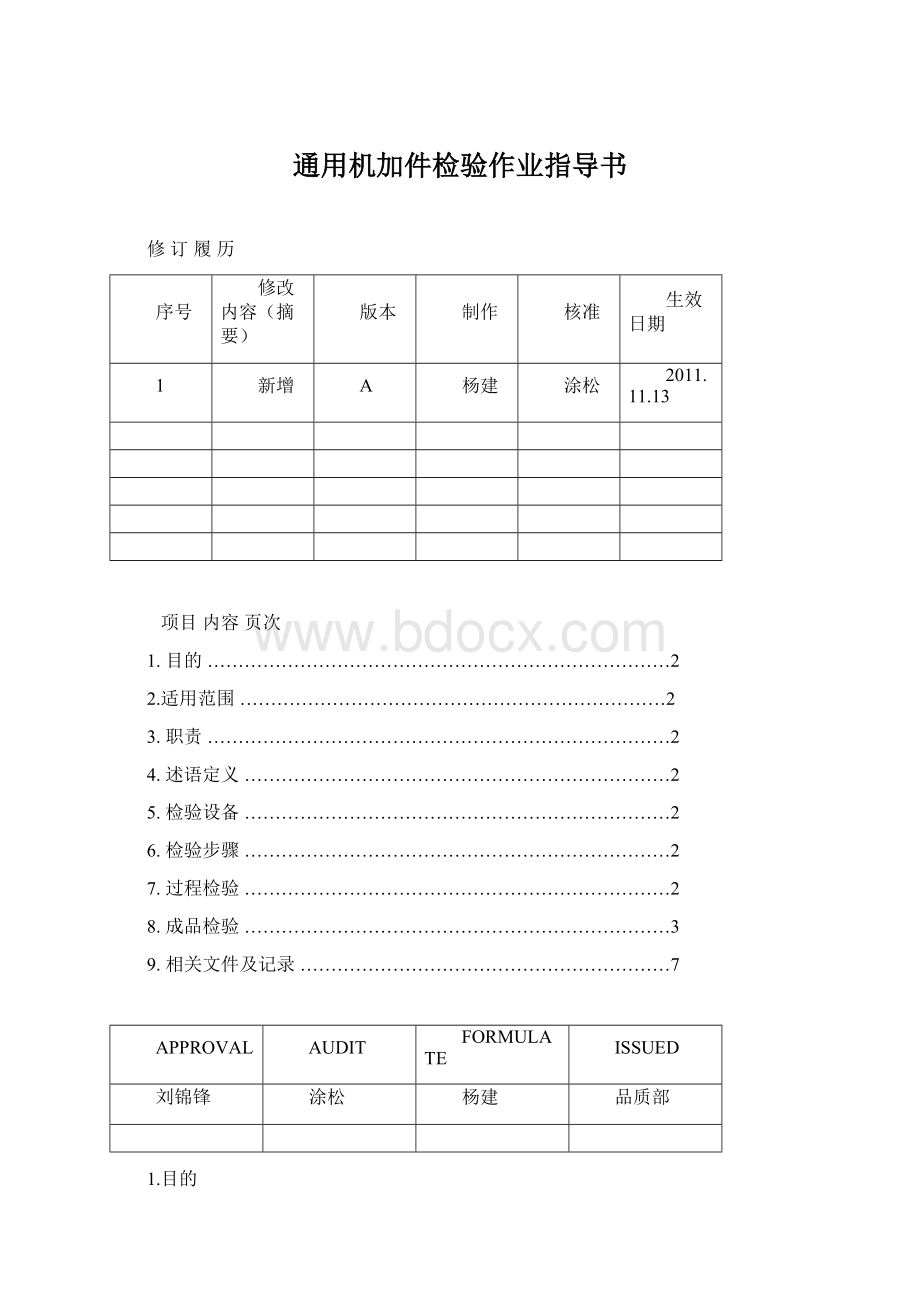
通用机加件检验作业指导书
修订履历
序号
修改内容(摘要)
版本
制作
核准
生效日期
1
新增
A
杨建
涂松
2011.11.13
项目内容页次
1.目的…………………………………………………………………2
2.适用范围……………………………………………………………2
3.职责…………………………………………………………………2
4.述语定义……………………………………………………………2
5.检验设备……………………………………………………………2
6.检验步骤……………………………………………………………2
7.过程检验……………………………………………………………2
8.成品检验……………………………………………………………3
9.相关文件及记录……………………………………………………7
APPROVAL
AUDIT
FORMULATE
ISSUED
刘锦锋
涂松
杨建
品质部
1.目的
为保证我司机加件产品的质量,又减少图纸对通用要求的描述,特制定通用检验标准,提供依据,做到检验标准明确且规范化、标准化。
2.适用范围
适用于本公司切削机加件,包括铸件、型材等的切削加工部分的加工过程控制及成品检验;
3.职责
3.1品质工程师:
负责制定和修订此检验规范适合本公司的适用性
3.2品质工程师:
根据此规范要求,制定来料、过程、成品检验作业指导书;
3.2品质主管:
对检验员的培训,及抽样作业监督
3.4检验员根据此规范进行来料、过程和成品的检验。
4术语定义
4.1A级表面:
在使用过程中经常被客户看见且被关注的部分;
4.2B级表面:
在使用过程中常常被客户看见的部分但不会过分关注;
4.3C级表面:
在使用过程中很少被客户注意到的表面部分。
5.检验设备
5.1检验设备和量具等精度、性能需要满足零件各检项目的需求。
6.检验步骤
6.1对照图纸要求之版本,是否与实物一致;
6.2清点图纸要求之数量,是否与实际相符;
6.3识别图纸要求之材料,是否与实物相符;
6.4审查图纸的尺寸、形位公差、外观、粗糙度等,选用合理检验方法和量具,保证检测数据的准确性。
6.5审查技术说明:
留意是否有对称件,不同类型的热处理、粗糙度等对特殊加工的要求。
6.6审查图纸上英文/日文的注解说明;
6.7按次序对工件进行检验,检完一个尺寸,作一个记号,不能漏检;
6.8检验出来的不合格品,记录并标识清楚交由上级领导进行确认和处理。
7.过程检验:
7.1材料检验
原材料符合图纸要求,达到本公司原材料检验标准。
7.2设备检验
加工设备及各项参数应能保证加工零件的精度。
7.3尺寸检验:
7.3.1图纸上标注公差的,按标注值检验;
7.3.2图纸上未注公差的,按技术要求中的未注公差检验;
7.4形位公差检验:
7.4.1图纸上标注公差的,按标注值检验;
7.4.2图纸上未注公差的,按技术要求中的未注形位公差检验;未注形位公差由加工工艺保证,
常规情况不检,有争议时进行检验
7.5粗糙度检验
7.5.1使用样块比较法,以表面粗糙度比较样块工作面上粗糙度值为准,用目视法与被测表面进行比较
判定、被测表面的粗糙度值,需要时可用显微镜比较法,有争议时可用粗糙度仪检测,图纸有特殊
要求时按图纸要求检验,用样块比较时,样块和被测表面材质、加工方法应一致,有电镀、喷涂等
表面处的零件,图中粗糙度默认是表面处前的加工粗糙度。
7.6螺纹检验:
7.6.1图纸标注螺纹公差等级的,按图纸要求检验,图纸未标注时,按下述原则
7.6.2普通螺纹黙认公差等级:
内螺纹6H,外螺纹6g例如:
(M8);
7.6.3统一螺纹黙认公差等级:
内螺纹2B,外螺纹2A例如:
(1/4-20UNC);
7.6.4加工过程中必须用校对合格螺纹塞规/环规检验,要求“通规通、止规止”;
7.7.外观检验:
7.7.1表面不可有划伤、碰伤、刀伤、刀纹平整无段差台阶等;
7.7.2去毛刺要求:
用手沿零件加工边角的任何位置及方向触摸均无刮卡现象;
7.7.3螺纹倒角:
内螺纹倒角至大径,外螺纹倒角至小径;
7.7.4机加件锐边(角)倒钝:
常规情况下不检验倒钝值,存在有争议时以此为检验标准;
7.7.4.1最短直壁大于2mm,倒0.5mm以下倒角或圆角,不刮手;
7.7.4.2最短直壁小于或等于2mm,倒不超过0.2倍直壁倒角或圆角,不刮手;
8成品检验
8.1检验方案定义:
8.1.1抽检:
所谓抽检是指从一个批次中抽出N个作为样本,进行全部的特性检验。
抽取的数量可以根据
《AQL抽样检验作业指导书》文件执行,确定有代表性即可。
抽检一般是随机的,也就是从所有
产品中随便拿取一定数量的单件作为样本来进行检验。
并以这些样本的检验结果来判定这些样本
所代表的整批次产品的性能或质量。
8.1.2全检:
所谓全检是指根据某种标准对被检查产品进行全部的特性检验
8.1.3抽检&全检相互结合:
根据我司客户产品质量需求采用的抽检与全检相互结合的检验方式进行验。
8.2一致性:
同批来料、外观、颜色、表面光洁度、加工工艺、表面处理、互换性、字唛、包装等.
均应有良好的一致性。
8.3尺寸检验:
8.3.1图纸上标注公差的,按标注值检验;
8.3.2图纸上未注公差的,按技术要求中的未注公差检验;
8.4形位公差检验:
8.4.1图纸上标注公差的,按标注值检验;
8.4.2图纸上未注公差的,按技术要求中的未注形位公差检验;未注形位公差由加工工艺保证,
常规情况不检,有争议时进行检验
8.5粗糙度检验
8.5.1使用样块比较法,以表面粗糙度比较样块工作面上粗糙度值为准,用目视法与被测表面进行比较
判定、被测表面的粗糙度值,需要时可用显微镜比较法,有争议时可用粗糙度仪检测,图纸有特殊
要求时按图纸要求检验,用样块比较时,样块和被测表面材质、加工方法应一致,有电镀、喷涂等
表面处的零件,图中粗糙度默认是表面处前的加工粗糙度。
8.6螺纹检验:
8.6.1图纸标注螺纹公差等级的,按图纸要求检验,图纸未标注时,按下述原则
8.6.2普通螺纹黙认公差等级:
内螺纹6H,外螺纹6g例如:
(M8);
8.6.3统一螺纹黙认公差等级:
内螺纹2B,外螺纹2A例如:
(1/4-20UNC);
8.6.4成品检验时按照客户要求选择实配或经螺纹塞规/环规检验合格的螺母/螺钉检验螺纹,能顺畅通过
或装配即合格。
8.7.外观检验:
8.7.1外观检视条件及方法:
--视力:
校正视力1.0以上;
--目视距离:
检查物距离眼睛A级面约40cm,B、C级面约70cm远;
--目视角度:
45度~90度(检查时产品应转动);
--目视时间:
A级面10秒/面,B、C面6秒/面;
--灯光:
大于500LUX的照明度或公司车间正常照明度。
8.7.2表面光滑、平整、无毛刺、变形、锈蚀、裂纹、压折、夹渣、气孔等;预埋件、铆接件应牢靠、
无松动,螺纹无缺损、无腐蚀等;不允许有加工遗留物存留在物件上;
8.7.3去毛刺要求:
用手沿零件加工边角的任何位置及方向触摸均无刮卡现象;
8.7.4螺纹倒角:
内螺纹倒角至大径,外螺纹倒角至小径;
8.7.5机加件锐边(角)倒钝:
常规情况下不检验倒钝值,存在有争议时以此为检验标准;
8.7.5.1最短直壁大于2mm,倒0.5mm以下倒角或圆角,不刮手;
8.7.5.2最短直壁小于或等于2mm,倒不超过0.2倍直壁倒角或圆角,不刮手;
8.7.6零件的喷塑、喷漆层应均匀、连续,无缩孔、起泡、开裂、剥落、粉化、流挂、露底
(局部无涂层或涂料覆盖不严)、指印等缺陷;
8.7.7热处理方法应符合有效版本图纸要求,热处理后不应有过烧、氧化、脱碳、热裂、变形、斑点、翘曲、
及表面晶粒不均不良现象。
8.7.8表面处理:
8.7.8.1表面处理方法应符合有效版本图纸要求,处理后表面光滑平整、无斑点、烧焦、起泡、水纹、镀层
脱落、镀层不全以及电镀酸性渗渣物等存在;
8.7.8.2表面处理后,零件表面允许有不可避免的轻微夹具印痕和轻微的水印;在不影响装配的情况下,边、
棱角处允许有轻微的粗糙;非重要表面允许有轻微的水纹或个别的斑点;
8.7.9其余外观缺陷要求请参见下表:
外观缺
陷类型
缺陷所处
表面类型
允许范围
A级表面
B级表面
C级表面
基材花斑
金属表面
不允许
不允许
S总≤被测面积的5%
浅划痕
所有表面
不允许
L≤50×0.4,P≤2
P≤5
深划痕
所有表面
不允许
不允许
不允许
凹坑
非拉丝和
喷砂面
不允许
直径≤0.5,P≤2
不限制
凹凸痕
所有表面
不允许
不允许
直径≤2.0,P≤5
抛光区
金属表面
不允许
不允许
S总≤被测面积的5%
烧伤
拉丝面
不允许
不允许
不限制
水印
电镀、氧化
不允许
S≤3.0,P≤2
不限制
露白
镀彩锌
不允许
不允许
S≤4.0,P≤3
修补
喷塑、电泳漆
不允许
S≤3.0,P≤1
S总≤被测面积的5%
颗粒
所有表面
不允许
直径≤1.0,P≤2
直径≤3.0,P≤5
挂具印
所有表面
不允许
不允许
不限制
图文损伤
印刷图文
不允许
不允许
不允许
色点
所有表面
不允许
S≤0.5,P≤3L≤50
S总≤被测面积的2%
露底
电镀、喷涂
不允许
不允许
不允许
注
S为单个缺陷面积(mm2),P为缺陷数量(个),L为缺陷长度或间距(mm)
8.8.0说明:
a、基材花斑:
电抛光、电镀或氧化前因基体材料腐蚀、或者材料中的杂质、材料微孔等原因所造成的、与
周围材质表面不同光泽或粗糙度的斑块状花纹外观;
b、浅划痕:
膜层表面划伤,但未伤及底层(即底层未暴露);对其它无膜层表面则为:
目测不明显、手指甲
触摸无凹凸感、未伤及材料本体的伤痕;
c、深划痕:
膜层表面划伤,且已伤至底层(即底层已暴露出来);对其它无膜层表面则为:
目测明显、手指
甲触摸有凹凸感、伤及材料本体的伤痕;
d、凹坑:
由于基体材料缺陷,或在加工过程中操作不当等原因而在材料表面留下的小坑状痕迹;
e、凹凸痕:
因基材受撞击或加工不良等而呈现出的明显变形、凹凸不平的现象,手摸时有不平感觉;
f、抛光区:
对基材上的腐蚀、划伤、焊接或铆接等部位进行机械打磨抛光后表现出的局部高光泽、光亮区域;
g、烧伤:
拉丝、电抛光、电镀处理时因操作不当、造成零件表面过热而留下的烧蚀痕迹;
h、水印:
电镀、氧化或电抛光后因清洗水未及时干燥或干燥不彻底所形成的斑纹、印迹;
i、露白:
镀彩锌钝化膜因磨擦而被去除、露出新层,或因缝隙截留溶液导致的无钝化膜现象,呈现为区别于
周围颜色的白色;
j、修补:
因膜层损伤而用涂料所作的局部遮盖;
k、颗粒:
因材料夹杂物或外来物的影响而在表面形成的、颜色与正常表面一致的凸起现象;
l、挂具印:
指电镀、电抛光、氧化、喷涂等表面处理生产过程中,因装挂用辅助工具的遮挡而使其与零件
相接触的部位产生局部无膜层的现象;
m、图文损伤:
印刷图文因局部脱落或擦伤、附着不良、污染等所造成的图形、字迹不完整不清晰的现象;
n、色点:
由材料、模具、环境或设备中的灰尘或夹杂物等影响在涂层中形成的不同色的斑点;
o、露底:
电镀层或喷涂层未能完全覆盖而露出基层表面;
8.8.1对机加件的非喷漆(粉)表面可允许有下列缺陷:
8.8.1.1A级表面每100mm×100mm范围内允许有数量不超过一个且直径不超过0.50mm的轻微麻点、轻微的
小划伤、极轻微的压痕及不可避免的轻微夹具伤痕;
8.8.1.2B、C级表面允许有:
局部的轻微麻点、压坑(压坑深度不大于板材厚度公差的一半,直径不超过1.0mm且须保证板材的最小厚度,且每100×100mm内不得超过5个);个别的轻微擦划伤(划痕长度不大于50mm);局部轻微的氧化色或顺轧制方向的暗色;
8.8.1.3使用材料应符合有效版本图纸的要求,材料本身应无变形、划伤、氧化、变色等;
8.8.1.4丝印颜色符合图纸要求,文字规范,图案清晰,直线平直、弧线规则,粗细均匀,无重影、无毛边
无断线、无偏移、无异物、无油墨堆积及凸起、鼓泡、凹陷现象;
8.8.1.5热处理方法应符合有效版本图纸要求,热处理后不应有过烧、氧化、脱碳、热裂、变形、斑点、翘曲、及表面晶粒不均等不良现象;
8.8.1.6喷砂和拉丝的目数按图纸要求,图纸未作要求时喷砂和拉丝均按100目的标准;喷砂后零件表面不得有明显变形;拉丝后整个表面纹路均匀,拉丝方向按图纸要求,图纸未作要求时与零件长边方向一致,拉丝后表面不得有烧伤痕迹;
8.8.2喷漆(粉)件表面外观要求:
8.8.2.1喷漆或喷粉件颜色、纹理参照有效的颜色样板及签样检验;
8.8.2.2颜色检验:
标准要求△E≤1.0;检验时以目视检验为主,不得有明显色差。
比对标准色板,以一致或极接近为合格;对目视有异议时用色差仪检测;
8.8.2.3漆层或粉层应均匀、连续,无缩孔、起泡、针孔、开裂、剥落、粉化、颗粒、流挂、露底
(局部无涂层或涂料覆盖不严)、刮伤、划痕、色斑、色点、指印等缺陷;
8.8.2.4粉层或漆层厚度符合图纸要求,否则粉层为0.05~0.15mm,漆层为0.03~0.06mm;
8.8.2.5A级表面每100mm×100mm范围内允许有数量不超过一个且直径不超过0.30mm的黑点、麻点,表面
不得有划伤,凹坑等缺陷;B、C级表面每100×100mm内允许有数量不超过3个且直径不超过0.5mm的黑点、麻点,允许有个别的轻微擦划伤(划痕长度不大于10mm)、局部轻微的氧化色或顺轧制方向的暗色及压坑(压坑深度不大于板材厚度公差的一半,直径不超过1.0mm且须保证板材的最小厚度);
8.8.2.6A级表面不允许有深浅划痕、挂具印及漆(粉)层夹杂异物;B、C级表面允许漆层有微量的夹杂物,在过渡面上允许有轻微的皱纹或凹陷及轻微的挂具印;任何表面喷粉或喷漆后都不得有预埋件头部的痕迹。
8.8.2.7喷粉或喷漆附着力检验:
用百格刀(或介刀)在供应商提供的样板(同批表面处理)或同批试样工件表面划1mm×1mm格子100个,格子深度以见到基材为准,把3M600#测试胶纸贴在格子上,用手指按压排除里面的空气,使胶纸充分贴紧被测表面,以45°方向向上快速拉起,在同一个位置上重复做10次,每次用的胶纸要更新;
判定:
A级面格子不应有脱落;其他面允许有5%以内掉落为合格。
8.8.2.8丝印附着力检验:
用3M600#测试胶纸粘贴于丝印表面,每次覆盖面积不小于150㎡(如该丝印表面面积小于150㎡时,则将其全部覆盖住即可),并用手压平,使胶纸与丝印表面完全结合,然后,迅速而连续地以垂直于丝印表
面方向的力撕掉胶纸,丝印表面不得有任何丝印脱落现象(重复检测三至五次)。
8.8.2.9丝印耐化学试剂性检验:
用纯净水浸过的擦布擦拭丝印15秒,再用甲基化酒精(或纯度95%以上工业酒精)浸过的擦布擦拭15秒,最后用异丙醇(99%)浸过的擦布在同一位置擦拭15秒,然后距离40cm~60cm处目视,不允许有丝印字迹脱落、丝印油墨扩散及变色等现象发生。
(擦拭方法:
用擦布包裹在500g砝码头部(砝码头部直径为10mm),手握砝码,沿水平方向来回推行,每秒一个来回)。
8.8.3.0供应商提供的性能检验报告可以作为我司检验的记录,但需仔细确认供应商提供报告所检项目是否与我司要求相符并确认其品质符合性。
9相关文件及记录
9.1相关文件
QC-WI-23-001《品质检验步骤作业流程图》
QC-WI-23-002《AQL抽样检验作业指导书》