供应商质量保证手册doc 39doc.docx
《供应商质量保证手册doc 39doc.docx》由会员分享,可在线阅读,更多相关《供应商质量保证手册doc 39doc.docx(33页珍藏版)》请在冰豆网上搜索。
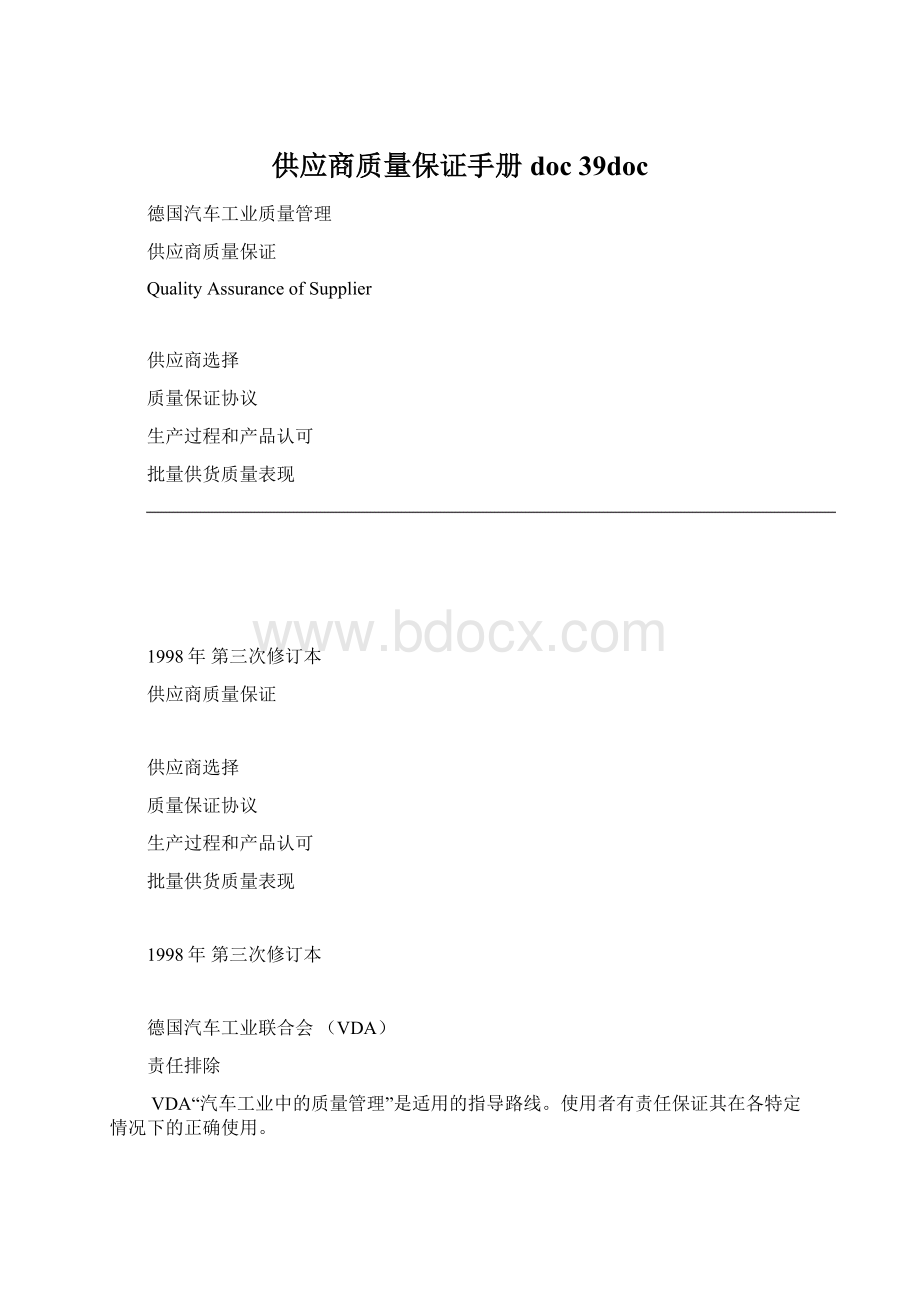
供应商质量保证手册doc39doc
德国汽车工业质量管理
供应商质量保证
QualityAssuranceofSupplier
供应商选择
质量保证协议
生产过程和产品认可
批量供货质量表现
1998年第三次修订本
供应商质量保证
供应商选择
质量保证协议
生产过程和产品认可
批量供货质量表现
1998年第三次修订本
德国汽车工业联合会(VDA)
责任排除
VDA“汽车工业中的质量管理”是适用的指导路线。
使用者有责任保证其在各特定情况下的正确使用。
VDA考虑工艺状况、发布时的现状。
根据VDA指导路线,任何人都要为自已的行为负责。
每个人的行为自负风险。
特此排除VDA以及发布VDA指导路线所涉及人员的责任。
在VDA指导路线应用过程中,发现错误或误译,立即通知VDA,使任何可能的错误可得到及时纠正。
参考标准
引用标准章节需得到DINDEUTSCHESINSTITUTFURNIRMUNGE.V(德国标准化协会)的许可,标准通过DIN编号和发布日期进行识别。
最新版本限定了标准的使用。
最新版本的获取途径:
出版商BEUTHVERLAGGMBH,10772BERLIN。
版权
整个出版物受版权保护。
任何末经VDA允许的超出版权法界限的使用,都是未经认可的、是非法的,这尤其适用于出版、翻译、电子系统的缩微拍摄、保管和处理。
前言
汽车工业中采购活动与生产定位的国际化需要相应的全球性质量管理标准。
使用方与供应商之间比较亲密的合作关系是进行全球竞争的必要前提。
使用方与供应商之间的亲密合作通过协议进行约定。
本书对这一项目有评论和建议。
“汽车工业质量管理”系列中VDA卷21975第1版,有如下内容:
评价供应商质量能力的指导路线,首件样品测试和进货环节的质量评价。
在VDA卷21995第2版中,以基本表格的形式描述了批量供货质量表现和首件样品测试的评价方法。
为与汽车工业的国际性质量管理标准达到同步,出现了现在的第三版本。
要对本卷进行摘要浓缩,在其他VDA出版物中详细说明的一些内容将不再提及。
本版本从根本上重新阐述供应商的选择、生产过程和产品认可(首件样品检验)、质量保证协议。
为符合最新的PPM评价,质量特性的评价程序有所调整。
准备期间,可参考如QS-9000、PPAP(生产部分认可程序)和EAQF中的要求及备注。
我们感谢下列公司及其员工参与本版本的准备工作:
BMWAG,Munich
Daimler-BenzAG,Stuttgart
DelphiPackardElectricSystems,Wuppertal
MannesmannSachsAG,Schweinfurt
MannesmannVDOAG,Babenhausen
VolkswagenAG,Wolfsburg
我们特别感谢下列公司及其员工参与了“质量保证协议”和“PPM-评价”章节的准备工作:
AudiAG,lngolstadt
BMWAG,Munich
RobertBoschGmbH,Stuttgart
ContinentalAG,Hannover
Daimler-BenzAG,Stuttgart
DelphiPackardElectricSystems,Wuppertal
MannesmannSachsAG,Babenhausen
LucasAutomotiveLtd.,Koblenz
OpelAG,Russelsheim
PorscheAG,Zuffenhausen
VolkswagenAG,Wolfsburg
ZFGmbH,Saarbrucken
内容列表
前言
3
1
引言
7
1.1
目的
7
1.2
合作各方
7
1.2.1
概念方面
7
1.2.2
产品和过程开发阶段
7
1.2.3
批量供货阶段
7
2
供应商选择
8
2.1
质量能力
8
2.2
进一步选择的标准
9
3
质量保证协议(QAA)
10
4
生产过程和产品认可(PPA)
11
4.1
目的
11
4.2
应用范围
12
4.3
生产过程和产品认可的原则
12
4.4
PPA程序可能的导因
12
4.5
PPA程序
13
4.5.1
生产过程的评价
13
4.5.2
样品检测
13
4.5.3
基本的PPA过程
14
4.6
生产过程和产品认可的要求
17
4.7
提交等级的选择
17
4.8
保存期
18
4.9
认可情况
18
4.10
自身证明
18
4.11
报告/表格
20
5
批量供货质量表现
20
5.1
供应商评价
20
5.2
批量供货零件质量的评价
20
5.3
不合格的鉴定
21
5.4
不合格产品的处理
21
5.5
信息系统
22
5.5.1
信息来源
22
5.5.2
早期报警系统
22
5.5.3
顾客调查
22
5.6
不合格零件分类
22
5.7
PPM抱怨值调查
23
5.7.1
计算公式
23
5.7.2
计算方法
23
5.7.3
目标协议
23
5.7.4
特殊情况
23
6
术语定义
24
7
附录1
25
─质量保证协议(QAA)的核对清单
8
附录2
28
─首件样品测试报告表格
1.引言
汽车工业中顾客与供应商之间加强的合作关系对质量愈见重要.
1.1目的
本出版物作为汽车工业中组织顾客与供应商之间合作关系的辅助.
下面章节描述了程序:
─供应商选择
─质量保证协议
─生产过程和产品认可
─批量供货质量表现
应提供证明供应商能交付符合要求的合格产品的证据。
而且显示下述情况:
回避的可能性,不合格的确认和解决,供应商质量提高。
1.2合作各方
合作各方必须同时忠于对方,保守机密是基本要求。
(知道怎样保护,专利,等等)
顾客应该使合作类型与程序应用在基本状况下协调:
─产品的复杂性(产品/过程技术)
─供应商类型(例如:
工程供应商、制造商、服务供应商、贸易)
─交付范围(如:
原材料,零件,模块,系统)
─采购(如:
通用的,单一来源,垄断产品)
1.2.1概念方面
投标一种产品必须在所有条件相同时进行。
(相同的信息状态,相同时间,相同的评价标准)
顾客将预定用途、供货零件状况以及顾客产品告知供应商。
通过这样,供应商可以最好的建议顾客正确运用或使用供货零件,以避免顾客产品开发过程中出现错误。
因此,顾客列在文件中的要求应该容易理解、清楚和恰当。
供应商在报价前先要检查顾客要求的完整性和可行性。
确定文件的完整性,首要考虑经济方面、技术方面、服务方面以及组织方面的要求、质量管理方法和质量目标、要求协调协议。
这里如采购合约、交付计划、特性规范和质量保证协议起了辅助作用。
供应商的选择依据技术的、经济的、服务的和质量方面的标准。
1.2.2产品和过程开发阶段
提出项目计划,阐述从概念到开始批量供货的里程碑。
(见VDA4.3产品及其生产过程的项目计划和实施)
项目计划由顾客和供应商共同制订。
经协议才可变更。
产品和生产过程开发是否成功由生产过程和产品认可(首件样品测试)证明。
1.2.3批量供货阶段
在第一次批量供货前,必须进行生产过程和产品的认可。
批量供货完全有效的情况是供应商供给顾客的都是无缺陷产品。
顾客与供应商必须针对混乱和不合格产品的处理共同制定责任和程序。
(结合质量控制程序)
必须审核批量供货质量表现。
实现持续的产品进步以及生产最优化可参考相应数据、信息和经验。
图1-1合作的各个阶段
2.供应商选择
顾客根据所需购买的产品或服务来选择供应商。
通常,进行供应商的选择是
跨部门的,例如,是通过顾客的采购部,但涉及开发、生产、质量管理和服务。
供应商的选择应尽早进行,以使合作关系在开发的早期阶段便得以建立。
产品的复杂程度和技术要求越高,选择供应商时就要更小心、更仔细。
除技术、经济和服务方面,供应商的质量能力是最基本的选择标准。
2.1质量能力
对潜力进行综合评价后(根据技术、经济和服务方面等),必须通过对质量
体系和产品相关过程的认可来证实供应商总的质量能力。
(见图2-1)
证明可以是下述记录形式:
─顾客(第二方)对体系和过程的审核
─供应商其他用户对体系和过程的审核
─授权机构(第三方)的证明
特定情况下,顾客可决定不同形式。
根据体系审核或证书评价供应商的质量体系。
质量体系的评价透露供应商技术方面及组织方面的信息。
过程审核(如根据VDA卷6.3)评价产品的生产过程。
这里,对生产过程保证的提问是焦点。
综合质量能力是定购分配的前提。
产品特性质量能力的证明是生产过程和产品的认可(见第4章)。
这是批量供货认可的前提。
图2-1供应商选择程序
2.2进一步选择的标准
审核结果可供对供应商的条件进行比较,因而是进行供应商选择的基础。
选
择供应商的目的,首先是将风险降为最小,还有就是考察要求和进行进一步选择。
选择供应商时,可参考更深层次的标准,如:
·工程特性和潜力,可靠性,还有人事和技术装备。
·调度、开销纪律和价格,考虑内部调度、价格和开销结构的透明度,合理便利措施的系统实行。
·首件样品结论要参考首次采样的频率、首件样品测试报告(FSTR)的完整性以及样品零件、通讯、解决问题的能力、对投诉的反应。
·评价原材料接收时,还要考虑交付的可靠性和机动性、交付取消程序和控制。
·产品质量和质量意识,参考清洁、整齐、产品安全预防措施、员工资格、培训水平和进修。
·定购时的通讯与合作,生产计划和控制体系,通讯技术(内/外)。
·处理问题的质量,发生问题或顾客投诉时的产品传送,联络人的有效性,应急方案。
·对工作中的环境、健康影响、安全性的合法规定。
·环境意识,原材料的环境处理,产品,包装和损耗。
·可追溯性
这些标准应被纳入供应商评价体系。
(见第5章)
利用清单和数据处理可简化供应商的选择。
3.质量保证协议(QAA)
顾客在选定供应商后,应签订质量保证协议。
质量保证协议从产品策划开始,
特别是通过规定界面和促进加强的、平稳的合作,来确保顾客的质量要求得以实现。
还有一个边缘影响,就是合约各方的联合竞争力通常加强了。
由于现代的开发、生产和产品技术,广泛的制造质量保证措施是必需的。
质量保证协议旨在建立一般规则。
而且不该对合约任一方不利。
单方面改变成本、职责和责任是违背QAA的基本思想的。
指导思想:
质量保证协议的内容或措辞应是顾客和供应商双方都能接受的,即使在有冲突的地方。
质量保证协议为产品而定。
质量保证协议的内容原则上与质量有关。
有产品的特性和技术要求,举例来说,工程合约中性能规格、图样或其他说明。
还有商业内容,如在采购和供应合约中。
如果还未受控或其他合约中有比较接近的说明—如前面段落中的例子—质量保证协议的内容在其他合约中可以是:
—供应商质量体系要求
—质量相关责任的规定
—顾客与供应商之间界面的规定
—共有信息责任的规定
—顾客确定审核的权利
—关于质量数据、保留周期、报告的文件
—生产过程和产品认可程序(PPA)的规定
—产品更改程序的明确(见PPA)
—共同质量控制程序的规定
—测量,用于不合格的预防、确认、消除
—为评价问题供应商对顾客生产过程的参与
—对供应商分供方的要求的规定
—有关交付质量(PPM)和产品可靠性的协议
—检验和试验或检验和试验程序的调和
—材料接受检验的更改(以及JIT交付)
—技术和服务保证
—产品确认和可追溯性
—产品有效期
—供应商环境管理体系的要求
—保密协议
—合约期限
图3-1合约结构
备注:
QAA的内容可以独立拟定,也可以是其他协议(如供应合约)中的一部分。
质量保证协议中不同的措辞会影响产品责任和保证范围。
因此特别是针对错误会引起责任要求的产品,建议考虑责任承保人或进行法律咨询。
如果措辞违犯了当前的法律,则措辞或整个QAA在法律上是无效的。
对责任进一步的注解见VDA卷1(质量根据)。
4.生产过程和产品认可(PPA)
PPA程序确保具体产品满足顾客的要求。
至今,产品认可总是处于抽样的情况。
(VDA卷2,第2版)
新的生产过程和产品认可将生产过程特别考虑。
因此认可包含:
—过程(产品特定过程)。
通过过程能力分析和(或)过程审核
—产品。
通过首件样品测试
因此保证在受控的、有效的过程中制造出的产品满足指定要求。
PPA程序的基本思想是使供应商能向顾客宣布PPA程序成功完成。
4.1目的
在批量供货开始前,PPA程序提供图样和说明书中的质量要求被实现的证据。
完成的PPA证实顾客要求、规格、和其他要求(如法律、标准等等)被正确理解并实现,对生产过程也有效。
因此,生产过程和产品认可是产品和生产策划过程的最终确认,得到肯定的结论会导致批量供货认可(VDA卷4.3)。
生产过程和产品认可程序描述了允许顾客和供应商正确计划PPA的基本条件。
4.2应用范围
生产过程和产品认可程序适用于新的零部件或产品有技术修改和生产过程有变更时。
程序适用于具体的产品(整件、组件、零件、元件、开始材料),如:
—生产零部件
—维修或备用零部件
—间接材料,就象工具、润滑剂等等
—原材料
备注:
非具体产品(服务、软件等)应归入供应部分的资格测试框架中。
4.3生产过程和产品认可的原则
·PPA程序的实行必须符合顾客和供应商之间的协议。
·供应商考察顾客要求时,分清哪些要求基于PPA的考虑。
·协议在顾客与供应商间制订,在协议中包括PPA的已有规则,或加以补充或限制。
·有关PPA的协议被文件化并随后立档,举例来说,在要求说明中或在质量保证协议中(见VDA卷1)。
·顾客和供应商都可以创立PPA程序。
4.4章节阐明程序可能的导因。
因此,供应商通常有责任向顾客说明PPA程序是否必须以及到什么程度。
·如顾客免除PPA程序,不意味着解除供应商进行内部认可的责任。
(见4.6章节)
·供应商承担PPA实行的全部责任。
·为达到顾客对产品的要求,供应商对其分供方的全部元件、部分整件和服务的认可负责。
·PPA程序必须与顾客在协议中制定,以使PPA在批量生产前进行。
·订购和预定交付日期如有要求,顾客仅接收样品零部件。
·认可根据双方间的协议进行,如将已签字的首件样品测试报告送还给供应商。
·如果顾客和供应商双方同意,可提出并认可首件样品测试报告以限定产品范围。
·顾客的认可不减轻供应商对其产品质量负的责任。
·应单独建立无PPA时顾客取消供应的协议。
PPA本身不能代表或取消一个供应合约。
4.4PPA程序可能的导因
合约成员在产品有修改以及产品相关过程有变化时必须通知对方。
下列情况是实行PPA程序的可能的原因:
─使用新的零部件
─设计、规格或材料有变化
─使用有选择性的材料或结构
─引进新的工具,或修改工具,或替换工具
─损失变化或保持后
─制造方法或生产过程有变更
─生产变化或引进新的生产设备后
─产品或服务的供应商变化了
─由于质量问题引起的交付停顿后
─生产设备已闲置12个月或更长时间
(用于备用件市场的产品可以排除)
图4-1批量供货认可
4.5PPA程序
生产过程和样品测试的评价是生产过程和产品认可的基础。
4.5.1生产过程的评价
开始新的或更改的产品或过程,受控并可行的过程的计划、开发和引进是活动的必要部分。
PPA过程中这些活动的执行通过文件和记录证实。
这包括:
FMEA过程,过程流程图,生产、检验、试验计划和得自过程能力分析的结论。
记录传送或委托给顾客以符合PPA要求。
(见4.6章)
顾客可另外进行一次过程审核(见VDA6.3章)。
审核在供应商处进行。
4.5.2样品测试
样品是产品试样,通过它可以测试与规定要求的一致性。
区分“首批样品”和“其他样品”。
样品测试,也称样品检验,理解为样品的确认。
通过样品,回顾协商同意并加以规定的要求,样品评价的结果被载入文件。
首批样品是完全在批量生产条件下采用批量生产资源制造的产品和材料。
生产过程和产品认可的抽样必须用首批样品。
首批样品的抽样被称作“首件样品测试”。
首批样品预定用于检验、测试并发送给顾客,应该在批量生产条件下从生产线随机抽样。
顾客和供应商对不同类型产品协商决定尺寸范围。
也适用于抽样数目。
其他样品(DIN5535015部分)是指不完全在批量生产条件下制造的产品和材料。
其他样品绝对不可以用于生产过程和产品认可。
但是,其他样品若满足规格要求,可供给顾客。
其他样品的认可,例如顾客工程部或开发部尝试并适合的样品,并不同时意味着批量供货认可,也不是免除PPA程序的原因。
如果顾客特别要求其他样品的抽样。
那么抽样目的,以及抽样范围和承诺应该商定,被记入文件。
这种情况下,VDA表格中必须有相应的备注。
图样和规范中包含的所有产品特性都要被抽样。
包括可行的、有用的以及什么时候不接受。
─尺寸
─材料
─性能
─可靠性
─视感
─重量
─触感
─声感
─气味
备注:
CAD图样要求关于参考点、测试剖面和测试表面的细节。
样品被明确鉴定,对应各个测量数值。
如果必须的话,鉴定中包括来源。
明确的鉴定所有的特性,单独记录名义值、极限值和实际值。
实际值与各个样品相对应。
4.5.3基本的PPA程序
图4-2中描述了基本的PPA程序。
因此,下面各点供参考:
·PPA程序按顾客要求策划,使认可可在批量供货开始前进行。
·供应商提出完整的全套PPA文件和图样(包括CAD数据)以及规格,这对进行产品的检查、测量和测试是必须的。
·供应商测定测量系统的能力并记录结论。
提供所有必需的产品特性检验、测试和测量用的设备(联系相关的产品修改状态)。
·顾客和供应商应该一起限定产品特性,以进行能力分析。
·供应商为实现要求,规定必须的过程特征。
·测定上述特征的过程能力并载入文件(见VDA卷4,第1部分)。
检查类型和能力特征值应该由顾客和供应商商定。
如果没有其他限定,则维持下列数据:
检查类型描述能力
短期过程能力MFUCmk≥1.67
初步过程能力PFUPpk≥1.67
长期过程能力PFUCpk≥1.33
·进行尺寸检查并记录结果。
来自认可的外部机构的测试结果被承认。
将测试结果与要求相比较。
·测试材料并记录结果。
来自认可的外部机构的测试结果被承认,将测
试结果与要求相比较。
·进行性能测试以及顾客和供应商商定的其他测试,记录结果。
将测试结果与要求相比较。
·首件样品测试报告的封面表格必须填完整。
供应商的授权代表必须审核报告并在封页签名。
4-2PPA程序
4.6生产过程和产品认可的要求
提交等级决定哪些文件、记录以及样品必须传送给顾客用于生产过程和产品认可。
提交也可针对供应商的工作。
如果没有另外商定,根据提交等级2的文件和样品被传送给客户。
要求:
提交等级
1
2
3
1.首件样品测试报告封页(FSTR)
×
×
×
2.测试结果(如尺寸、材料性能、性能、视感、重量、可靠性、
触感、声感、气味、过程能力数据等等)
√
√
3.样品(传送的数量或质量根据协议)
A
A
A
4.文件(如顾客图样、CAD数据、规范、认可的设计更改等)
√
√
5.设计和开发认可
×
×
6.FMEA
E
7.过程流程图表(生产和测试步骤)
×
×
8.生产、检查、测试计划
E
9.检查、测试和测量设备清单(产品-特性)
×
10.产品和测试设备能力分析(结论)
√
11.对顾客要求依从的证据,针对与顾客商定的范围(如环境、
安全性、再循环)
×
×
×对各个提交级别的要求
√个别情况,范围与顾客商定
A样品数(≥0)与顾客商定
E仅用于检验
与提交等级无关,供应商必须进行自己的内部认可并记录结果。
这时他必须针对上表中1至11点作出陈述。
如果样品提交得到同意,那么顾客在适当的时候要求样品,与给出预定交付日期的订货分开。
符合所有规范,才进行文件、记录和样品的提交。
如果不符合有背离,供应商必须获得顾客的书面认可(偏差许可),并将其附于提交。
4.7提交等级的选择
提交等级1的判断标准:
─供应商是知名的,首次抽样和批量供货过程没有发生问题。
─容易生产的产品或一次简单的更改
─产品家族:
一个项目的数量根据提交等级2或3进行抽样,其余项
目的数量根据等级1。
提交等级2的判断标准:
─新的供应商
─知名供应商发生质量问题
─制造过程类似的产品发生问题
─新的生产过程(新的产品)
提交等级3的判断标准:
─顾客无适用的测量设备
─新的生产过程(质量能力评价)
─产品制造是复杂的、困难的,生产过程难以控制(以专业水平判断
问题)
─有专门档案的文件(部分)(DWSPA),见VDA卷1
4.8保存期
考虑到PPA程序,产品的和相关过程的文件、记录、以及生产过程和产品认可组成部份的数据必须保留,保留的时期至少为:
产品供应合约有效期加1年或根据专门协议。
当前有效的参考和界限模式由供应商保留相同的时间期限。
因此,顾客和供应商间应该就有特殊性能的产品建立明白的协议。
(如大部分产品,货架寿命)
备注:
如果产品的文件必需存档,可以要求更长的保留期。
如果众所周知程序的合法性还有待决定,相应文件既不允许被调动也不允
许被毁坏。
4.9认可情况
顾客将评价提交的文件,可能的话还有样品,完成首件样品测试报告的封页,填写单独的和综合的认可状况,如果没有另外商定,将它传送给供应商。
认可状况可以是:
·认可
这意味着不违背交付取消规定的产品得到认可。
·附条件的认可
这意味着产品的发送仅在特定的限制时期或特定件数得到许可(背离特许)。
条件由顾客和供应商个别商定。
再次抽样可能是必需的。
·否决,必须再次抽样
这意味着产品的发送未被允许,必须再次抽样。
4.10自身证明
顾客和供应商间可以商定由供应商进行自身证明。
这意味着供应商向顾客出具提交文件,但顾客的反应不是必需的。
如果已经商定自身证明,供应商可将它连同承诺文件提交,同时保持产品的认可状态“认可”。
要减少正式费用和过程时间,选择这一步骤。
当顾客确信供应商的可靠性且本步骤