振膜复合模及工艺设计综述.docx
《振膜复合模及工艺设计综述.docx》由会员分享,可在线阅读,更多相关《振膜复合模及工艺设计综述.docx(30页珍藏版)》请在冰豆网上搜索。
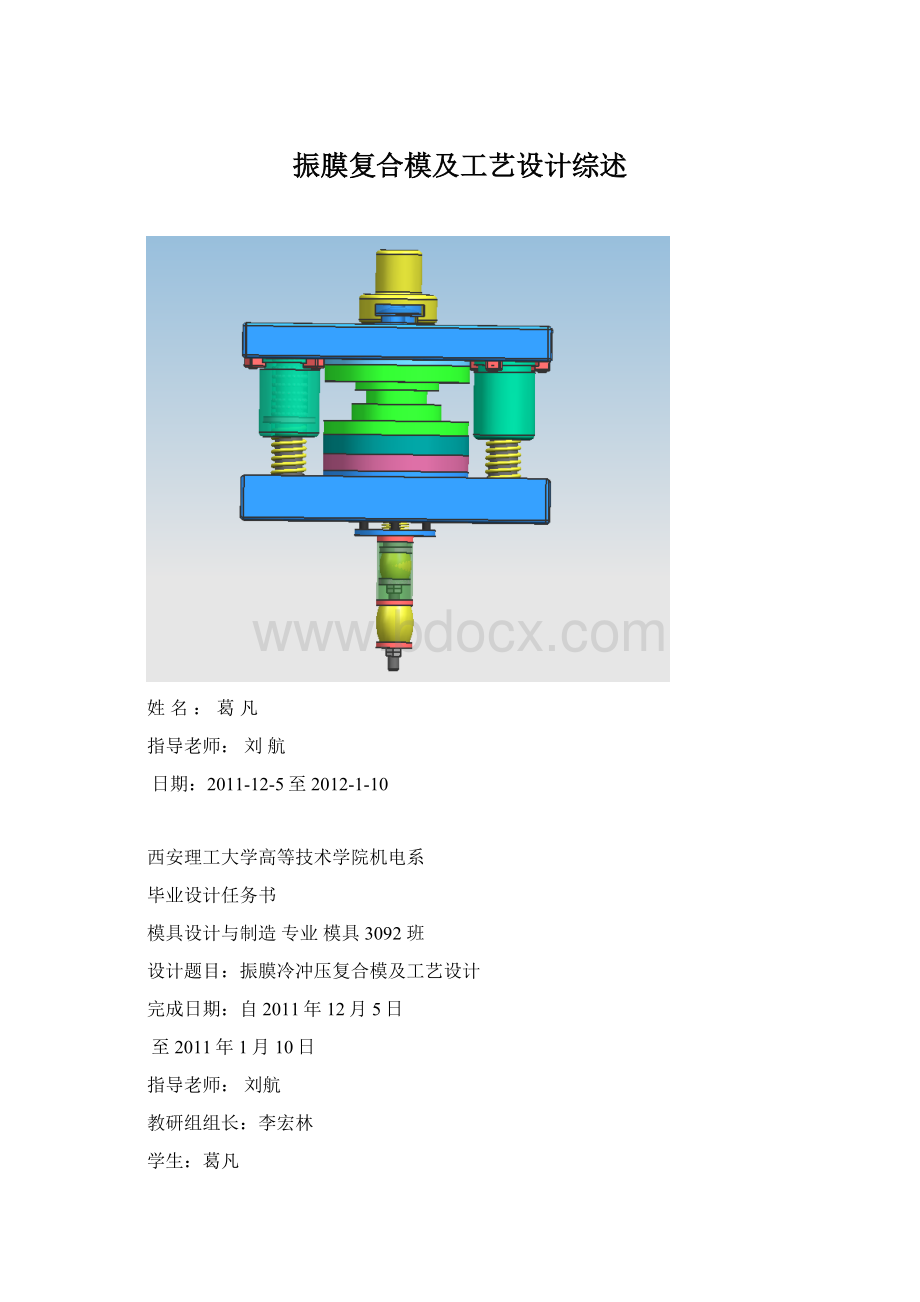
振膜复合模及工艺设计综述
姓名:
葛凡
指导老师:
刘航
日期:
2011-12-5至2012-1-10
西安理工大学高等技术学院机电系
毕业设计任务书
模具设计与制造专业模具3092班
设计题目:
振膜冷冲压复合模及工艺设计
完成日期:
自2011年12月5日
至2011年1月10日
指导老师:
刘航
教研组组长:
李宏林
学生:
葛凡
批准日期:
2011/11/5
接受任务日期:
2011/11/5
注:
任务书填写一式两份,一份留给教研室、一分发给学生,任务完成后附入说明书内。
设计进度计划表
序号
起止日期
计划完成内容
实际完成情况
检查日期检查人签名
1
第1周
分析制件,绘制其三维及二维图;完成制件图的修改工作,上交制件图,教师审查
2
第2周
选择成型工艺、成型设备,绘制该模具的装配草图,完成可行性分析,教师审查
3
第3周
完成该模具的装配图,上交模具装配图,教师审查
4
第4周
画出非标准零件的三维及二维图,教师审查
5
第5周
绘制所有非标准零件图的制造工艺,填写其综合工艺卡,教师审查。
整理设计说明书及其他资料,教师审查
6
第6周
答辩(全组教师参加)
指导老师批准,并签名:
刘航2011/12/3
一、设计内容和要求:
(说明书、专题、绘图、实验结果等)
1.设计振膜冷冲压复合模具与工艺设计
2.完成该模具的设计装配图及所有非标准零件图及制造工艺卡
3.上交资料有:
(1)制件图1张(A3、A4图)。
(2)制件的成型工艺一份。
(3)模具装配图一份(A1图)。
(4)该模具的所有非标准零件图及制造工艺卡若干份。
(5)该模具的详细说明书1份。
(6)答辩提纲1份。
4.可适量应用计算机辅助设计。
二、技术要求:
1.达到图纸的各项要求,使用第一角投影视图,使用国家标准。
2.生产纲领:
40000件/批
3.时间:
6周
三、主要参考资料:
1.«模具设计手册»
2.«工艺人员设计手册»
3.«模具加工手册»
4.«机械零件设计手册»
5.«模具制造手册»
6.«其它有关参考资料»
装配图(剖视图)
一.制件分析
1.超薄板冲裁技术···································6
2.振膜冲压面临的问题·······························9
3.振膜材料的分析及选择····························10
二.工艺分析··········································11
三.工艺方案的确定····································12
四.模具结构形式的确定································13
五.工艺设计··········································13
1.计算坯料尺寸·····································13
2.画排样图·········································15
3.计算材料利用率η·································15
4.计算冲压力·······································16
5.初选压力机·······································17
5.压力中心的计算···································17
6.凸、凹模刃口尺寸的计算···························18
六.填写工艺卡········································19
七.模具结构设计······································19
八.画装配图和零件图··································20
(零件图的二维和三维)
九.校核压力机安装尺寸································33
十.编写技术文献······································33
十一.心得体会········································33
一.制件分析
1.超薄板冲裁技术
超薄板冲裁面临的技术难题与挑战
超薄板冲裁件的线性尺寸精度要求高,而对冲切面一般均无要求。
因为料厚很小,冲切面平整、光洁,Ra为1.6-3.2μm。
但平面的线性尺寸精度与模具结构及其技术功能和状态、模具的制造精度等众多因素有关。
A.超薄料冲裁的难点与核心技术
(1)超薄料刚度小,送料易弯折变形和擦伤表面
厚度Τ为0.3-0.05mm的超薄料,多以带料、卷料供货刚度小,开卷展开送料入模很易折弯,拱弯变形及擦伤表面。
(2)必须用Ⅰ类小间隙冲裁
冲裁薄料及超薄料时,间隙稍大或不均匀,就会造成“弯边”、“啃边”,即在间隙大的部位材料沿凹模刃口弯边后切离或有压变痕迹,降低冲裁尺寸精度。
冲裁刃口磨钝,也会出现“弯边”。
因此,超薄料冲裁必须采用小间隙、锋利刃口剪切分离。
(3)超薄小间隙冲裁诱发的技术难题
超薄料冲裁间隙依料厚Τ为0.3-0.05mm,通常取C=4%t=0.012-0.002mm。
如此小的冲裁间隙不仅制模要求高,更主要的是要设计出好的冲模结构,确保凸模有高精度导向,不仅能消除压力机滑块导向误差大对冲模导向的影响,还能始终使冲模保持均匀的冲裁间隙,保证冲模有足够高的寿命。
(4)超薄板的高精度与超高精度冲裁
通常冲压的薄板多为各种牌号的热轧或冷轧钢板,有色金属较少。
而超薄板冲裁多为有色金属及以有色金属为基材,复以导电、导热、耐蚀、耐候性好的金、银、铂、铑、钯、铱等,贵重、稀有金属及其合金的厚度仅1-2μm至0.1-0.2mm的覆层,构成廉-贵双层或多层复合超薄板,冲裁过程中必须防止分层;公差为±0.001-±0.003mm超高精度的群孔群槽大面积,超薄板冲裁件,在高新技术领域中使用广泛。
超薄板的微间隙冲制高精度、超高精度冲裁件,需要设计并制造出结构优良、导向精准、冲压精度高的冲模。
这些都涉及冲压加工及冲模制造的关键核心技术。
B.开式压力机动态精度对冲裁模冲裁精度的影响
表一国产开式压力机出厂精度
检测项目
公差/mm
工作台板上平面的平面度
0.06(最大值)
滑块下平面的平面度
0.06(最大值)
滑块下平面对工作台板上平面的平行度
左右0.015-0.02
前后0.02-0.04
模柄孔对滑块下平面的垂直度
0.05/100(外露)
滑块行程对工作台板上平面垂直度
0.03-0.05
多数生产企业,用于生产中小型冲压件的开式压力机都已使多年,超期服役相当普遍。
其静态精度远低于表一中的数值,出厂精度早已丧失,实际运行的动态精度就更低了。
因此,Τ为0.3-0.05mm的超薄料冲裁用冲模的结构设计,必须排除压力机滑块导向精度低,机架弹性变形大而不均对冲模冲压精度的影响。
C.冲模导向装置的精度对冲模冲压精度的影响
用导柱模架的冲模靠模架的导向精度,摆脱压力机动态精度不高的影响。
滚动导向模架OⅠ和OⅡ两个公差等级,导柱与滚珠导套采用0.01-0.02过盈配合,能实现零误差导向。
表二滑动导向导柱模架导柱导套配合间隙/mm
配合形式
导柱直径
模架公差等级
说明
Ⅰ级
Ⅱ级
配合间隙
滑动配合
≤18
〉18-30
〉30-50
〉50-80
`≤0.01
≤0.01
≤0.014
≤0.016
≤0.015
≤0.017
≤0.021
≤0.025
导套导柱配合
Ⅰ级模架H6/h5
Ⅱ级模架H7/h6
根据以上分析和表二数据可得,冲裁t≤0.3mm超薄料较为合理的方案为:
采用滚珠导柱模架或采用Ⅰ级精度滑动导向导柱模架,配合弹压卸料板导向机构,以及设专门的工艺定位孔与导正销校准定位,提高冲模的冲压精度。
冲制超薄板、带料冲裁件的冲模结构设计
为了冲制t≤0.3mm的超薄料高精度冲裁件及一些虽料厚t〉0.3mm,但这些冲裁件有高精度小孔与群孔,其孔距与同轴度、孔形允差都在IT8级以上;为了使孔径d≤Φ3mm、d/t≤1及异型孔面积A≤7mm2的细长冲孔凸模,在其刃口工作段获得横向支承、加固的凸模杆部有更精确的导向,从而提高细长凸模的抗纵弯能力,对模架的结构都可按实际需要进行如下几方面的改进与细化。
1采用浮动模柄,进一步排除压力机滑块导向不准对模具的影响。
2模具的导柱配高精度导套,提高导向精度和寿命。
3加限位器(柱)控制上模下行位置。
4将模架导柱改为压装在上模座内,以便在用大行程压力机工作时,导板行程长,加大局部磨损并使卡模危险增多。
5薄料与超薄料冲裁,需要工作行程很小。
而且冲膜结构上也不允许凸模脱离导板,故可以将导柱长度控制在最小合适长度内,闭模时留在模座内。
2.振膜冲压面临的问题
如图一振模零件,材料为铝镁合金,料厚0.07mm。
零件成形后要求表面平整,不允许有划痕、皱褶、拉裂,成形处不允许有凹坑、塌陷等缺陷由于料薄且尺寸比较小,如果采用单工序模生产,由于多次定位会产生累积误差,且工件多次周转不可避免地会碰撞变形,生产率也很低。
振膜零件冲压面临的问题:
1振膜材料的选择。
2振膜的形状必须要有良好的的刚度。
3制件上Φ0.2的孔如何冲压有无废料?
若有废料,废料在哪?
若无废料,凸模取什么结构?
4材料的厚度Τ=0.07mm。
材料无法定位,应考虑如何进行定位以便顺利完成冲压过程。
5有所给任务可知,该制件为复合模冲压。
应该从制件的成型要求考虑复合模具结构。
6制件的排样图。
图一
制件图
3.振膜材料的分析及选择
材料:
铝镁合金牌号:
5A02(半冷作硬化)GB/T3618
材料状态
表三
半冷作硬化
抗剪强度τ
160-200MPa
抗拉强度σb
230-280MPa
屈服强度σs
210MPa
强性模量Ε
70000MPa
已退火
抗剪强度τ
130-160MPa
抗拉强度σb
180-230MPa
屈服强度σs
100MPa
强性模量Ε
70000MPa
概述:
5A02铝板为Al-Mg概述:
5A02铝板为Al-Mg系列铝合金,主要元素为镁,含镁量在3-5%之间。
主要特点为密度低、抗拉强度高、延伸率高,在相同面积下镁铝合金的重量低于其他系列。
与3A21相比,5A02铝板强度较高特别是具有较高的疲劳强度;3A21与相似,塑性与耐蚀性高;热处理不能强化,用接触焊和氢原子焊焊接性良好,氩弧焊时有结晶裂纹的倾向;5A02铝板在冷作硬化和半冷作硬化状态下可切削性较好,退火状态下可切削性不良。
可抛光。
用途主要用于要求高的可塑性,在液体或气体介质中工作的低载荷零件。
二.工艺分析
制件图如图一所示,材料为镁铝合金(5A02),料厚0.07mm,制件尺寸精度为IT14级,年产量4万件。
该制件形状简单规则,尺寸较小,厚度超薄,中批量生产,属于精密冲压件。
但是有几点问题应该注意:
(1)Φ0.2的小孔如何冲裁及该孔的废料的去向,同时还应考虑冲裁该孔的凸模如何加工和固定;(因为冲裁Φ0.2的孔没有公差要求,那么就按自由公差进行计算;该孔的孔径很小冲裁出的小孔几乎没有废料;考虑到凸模的加工,应该尽量选择组合凸模避免凸模难加工和纤细易损)
(2)铝镁合金的料厚仅为0.07mm属于超薄材料。
很易折弯,拱弯变形及擦伤表面,故如何定位是顺利冲裁该制件的关键;(采用无定位机构进行手工送料,尽量增大板料的搭边值)
(3)该产品为振膜,从制件的用途上考虑,制件的材料要求高的可塑性,在气体介质中工作的承受一定的低载荷。
(选取材料为5A02铝镁合金材料的性能已在《Ⅲ.振膜材料的分析及选择》中介绍)
(4)制件有3.80-0.3mm的拉伸高度,高度很小,如何控制拉伸高度是关键;(在拉伸凹模中采用可调节(带螺纹的)垫圈配合螺纹垫板的方式来控制拉伸高度)
(5)该制件为精密冲压件,模具的结构和压力机的动态精度是保证制件精度的关键要素。
(在模具结构上,采用浮动模柄和滚珠导套结构保证模具的导向精度;压力机的选择通过冲压力的计算尽量选择精度高的)
三.工艺方案的确定
该制件为复合模冲压成形。
其基本工序有落料、冲孔和拉伸三种。
按其先后顺序组合,可得如下的工艺方案:
拉伸——冲孔——落料,单件复合冲压
由于制件结构尺寸小,材料超薄,复合模装配较困难,强度也会受到一定的限制,寿命不高,正好符合该制件生产批量不高特点;制件上Φ0.2的孔是拉伸成形后冲制的,冲孔时,由于凸凹模的尺寸太小,料又很薄,冲孔后为了避免毛刺的出现,就必须使凸、凹模采用零间隙(或负间隙)的配合。
零件的切边在拉伸和冲孔后进行,为了使切边后边缘不出现毛刺,切边凸、凹模也只能采用零间隙的配合。
又因为Φ0.2的孔为自由公差,不用考虑凸模插入材料和凹模内进行落料时因材料的切向流动压力造成孔的微变形;又因为材料超薄造成拉伸力的大小无法准确确定而造成拉伸变形或开裂的现象,采用可调节的拉伸装置。
四.模具结构形式的确定
(1)考虑到安装、调整及导向精度高的特点,上、下模采用双导柱滚动模架导向;
(2)为了消除压力机导向误差对模具导向精度的影响,采用了浮动模柄。
(3)为了控制压料、拉伸、冲孔、切边、顶出的先后次序,采用了双弹顶机构。
(4)为了使零件成形后表面平整,无划痕、皱褶、拉裂、凹坑、塌陷等缺陷及为了提高制件的表面质量,在拉伸凹模与板料的接触表面采用镀Cr处理。
(5)为了防止合模后制件的拉伸高度不足,采用了螺纹垫板和橡胶圈利用浮动模柄易拆卸的特点及时方便的通过螺纹垫板上的内六孔进行调整。
综上所述,由文献【中国模具工程大典】中表5.1-52(P1058)选用中间导柱模架,由文献【模具设计指导】中表5-5(P122)选用复合模圆形厚凹模典型组合尺寸形式
五.工艺设计
1.计算坯料尺寸
(R5)相对弯曲半径为
R/t=5/0.07=71.43>0.5
式中R——弯曲半径(mm)
t——料厚(mm)
可见,制件属于圆角半径较大的弯曲件,应先求出弯曲变形区中性层曲率半径ρ(mm)。
由文献【冲压设计资料】(P131)中性层的位置计算公式
ρ=R+χt
式中χ——有实验测定的应变中性层位移系数
由文献【冲压设计资料】(P131)表3-6中性层位移系数χ值,查出χ=0.5
ρ=(5+0.5×0.07)mm=5.035mm
(R45)相对弯曲半径为
R/t=45/0.07=642.8>0.5
式中R——弯曲半径(mm)
t——料厚(mm)
可见,制件属于圆角半径较大的弯曲件,应先求出弯曲变形区中性层曲率半径ρ(mm)。
由文献【冲压设计资料】(P131)中性层的位置计算公式
ρ=R+χt
式中χ——有实验测定的应变中性层位移系数
由文献【冲压设计资料】(P131)表3-6中性层位移系数χ值,查出χ=0.5ρ=(45+0.5×0.07)mm=45.035mm
由文献【冲压设计资料】(P131)圆角半径较大(R〉0.5t)的弯曲件毛料长度计算公式l0=Σl直+Σl弯;l弯=(1800-α)πρ/1800
式中l0——弯曲件毛料展开长度(mm)
Σl直——弯曲件
各直线段长度总和(mm)
Σl弯——弯曲件各弯曲
部分中性层展开长度之和(mm)
图二几何关系图
由图二可知
Σl直=14.5mm
l弯=(1800-α)πρ/1800
Σl弯=l弯1+l弯2=157.2mm
l0=Σl直+Σl弯=171.7mm
2.画排样图
由文献【冲压设计资料】(P39)表2-14冲裁金属材料的搭边值可查出,因为本套模具无定位装置采用手工送料的方式,故
a=1.5mma1=1.5mm
图三排样图
由冲裁金属材料的搭边值可得条料的宽度尺寸B(mm)的值为46mm
制件的排样图如图二所示,选择条料的规格在保证条料宽度的前提下以获得最高的材料剪裁利用率为准。
3.计算材料利用率η
由文献【模具设计指导】(P10)材料利用率通用计算公式
η=A。
/A×100%=77.2%
式中A。
——得到制件的总面积(mm2)
A——一个步距的条料面积(L×B)(mm×mm)
得
η=3.14×21.252/46×46×100%=67%
4.计算冲压力
完成本制件所需的冲压力由冲裁力、压边力和拉伸力组成,不需要计算卸料力和推料力。
(1)冲裁力F冲——由冲孔力、落料力两部分组成
由文献【模具设计指导】(P10)冲裁力F冲(N)的计算公式
F冲=KLtτ0或F冲=Ltσb
式中K——系数,K=1.3;
L——冲裁周边长度(mm);
τ0——材料的抗剪强度(MPa);
σb——材料的抗拉强度(MPa)。
有本书表三得
σb=280MPa
F冲=Ltσb=280×0.07×42.5≈2.7KN
(2)压边力F压——由于在直边的上下接触面采用电火花的方法打出花纹再根据模具合模时的压力,因此该制件压边力远小于压边圈的摩擦力。
故压边力F压可以忽略不计。
(3)拉伸力F拉——控制拉伸高度
拉伸力F拉由双弹顶机构来提供根据簧丝的弹力来实现拉伸。
(4)卸料力F卸和推料力F推和顶件力F顶
——由文献【模具设计指导】(P11)卸料力、推料力和顶件力的计算公式
F卸=K卸F冲
F推=K推F冲n
F顶=K顶F冲
式中K卸、K推、K顶——系数,查文献【冲压设计资料】(P59)卸料力、推料力、顶件力的系数,得K卸=0.07K推=0.1K顶=0.14
n——卡在凹模直壁洞口内的制件(或废料)件数,因为冲裁该孔为无废料冲孔,故本书取n=1
F卸=K卸F冲=0.07×2.7=0.189KN
F推=K推F冲=0.1×2.7=0.27KN
F顶=K顶F冲=0.14×2.7=0.378KN
故F=F冲+F卸+F推+F顶
=2.7+0.189+0.27+0.378
=3.537KN
5.初选压力机
考虑本套模具采用浮动模柄装置,而浮动模柄与模柄孔的尺寸关系
查文献【模具设计指导】(P107)表4-35国产多工位压力机主要技术参数,初选压力机型号规格为Z81-40。
详细参数如下表所示
表四
压力机型号
Z81-40
标称压力/kN
400
滑块行程/mm
150
工位数/个
7
滑块行程次数/(次/min)
40
最大装模高度/mm
300
装模高度调节量/mm
40
工位距/mm
150
夹板纵向送料行程/mm
150
夹紧时夹板内侧距离/mm
130-210
送料线高度/mm
180
模柄孔尺寸(直径/mm×深度/mm)
Φ32×55
垫板尺寸(孔径/mm×厚度/mm)
Φ110×60
打料行程/mm
30
6.压力中心的计算
本制件由于图形规则,为圆形中心对称,故压力中心为制件的几何中心。
压力中心的位置如图四所示:
图四压力中心
故求得压力中心位置为XG=0YG=0
7.凸、凹模刃口尺寸的计算
采用配作法计算冲孔落料复合模工作零件的刃口尺寸,可增大制造误差。
(1)落料凹模刃口尺寸计算:
由文献【冲压模具及设备】(P97)查取磨损系数χ,由文献【公差配合与测量技术】(P14)查取公差Δ。
尺寸Ad1【制件尺寸R50-0.3】,取χ=0.5,Δ=0.3
Ad1=(Amax-χΔ)+Δ/40=(5-0.5×0.3)+0.3/40=4.85+0.0750
尺寸Ad2【制件尺寸R450-0.62】,取χ=0.5,Δ=0.62
Ad2=(Amax-χΔ)+Δ/40=(45-0.5×0.62)+0.62/40=44.69+0.1550
尺寸Ad3【制件尺寸280-0.52】,取χ=0.5,Δ=0.52
Ad3=(Amax-χΔ)+Δ/40=(28-0.5×0.52)+0.52/40=27.74+0.130
尺寸Ad4【制件尺寸42.50-0.62】,取χ=0.5,Δ=0.62
Ad4=(Amax-χΔ)+Δ/40=(42.5-0.5×0.62)+0.62/40=42.19+0.1550
尺寸Ad5【制件尺寸3.80-0.3】,取χ=0.5,Δ=0.3
Ad5=(Amax-χΔ)+Δ/40=(3.8-0.5×0.3)+0.3/40=3.65+0.0750
凸模尺寸按凹模配作加工,保证合理间隙0.012-0.016
(2)冲孔凸模刃口尺寸计算:
尺寸d【Φ0.2+0.250】取χ=0.5,Δ=0.25
dp=(dmin+χΔ)0-Δ/4=(0.2+0.5×0.25)0-0.25/4=0.3250-0.0125
凹模尺寸按凸模配作加工,保证合理间隙0.012~0.016
(3)凹模孔口及尺寸
因为制件的厚度为超薄所得的合理间隙非常的小为了保证制件的精度制件的外形尺寸采用软模结构即零间隙(或负间隙)获得从而使模具顺利完成冲裁过程。
其余孔的公差采用IT14级精度进行冲裁。
(4)拉伸高度及尺寸
拉伸高度的获得是通过调节螺纹垫板和增加橡胶圈的方法逐步的进行调节。
六.填写工艺卡
按表四要求,将以上有关结果、数据填入。
时间定额一栏可不要求填写。
七.模具结构设计
冲孔落料拉伸复合模
因制件形状简单,虽有Φ0.2的小孔,但总体结构稳定,选用整体式凹模较为合理。
因生产批量不大,选用T10A为凹模材料。
(1)确定凹模厚度H值:
由文献【模具设计指导】(P13)凹模厚度的计算公式
H=3√——F冲≈14mm
(2)确定凹模周界尺寸L×B:
由文献【冲压设计资料】(P61)表2-40凹模厚度H和壁厚C查得C=26H=20
L=B=94.5
通过对凹模周界的计算选取标准模架
由文献【中国模具工程大典】中表5.1-52(P1058)选用中间导柱模架100×100×135-0ⅡJB/T7182.3,技术条件按JB/T7183-1995。
虽然此模架能够满足制件的精度要求但是其余各部分的零件均按文献【模具设计指导】(P122)表5-5复合模圆形厚凹模典型组合尺寸选取标准件。
其余的一些零件按照冲孔落料拉伸复合模的需要自行进行设计和选择材料。
模具的零件通过表五进行选取:
八.画装配图和零件图
按照任务书的要求绘制装配图和零件图。
图
(1)
装配图(a)
图
(二)
装配图(b)
装配图(c)
零件图(冲孔凸模)
零件图(凸凹模)
零件图(拉伸凹模)
零件图(切边凸模)
零件图(切边凹模)
零件图(顶出器)
零件图(可调节垫板)
零件图(垫板)
零件图(空心垫板)
零件图(凸模固