某汽车总装车间物流系统优化研究概要.docx
《某汽车总装车间物流系统优化研究概要.docx》由会员分享,可在线阅读,更多相关《某汽车总装车间物流系统优化研究概要.docx(8页珍藏版)》请在冰豆网上搜索。
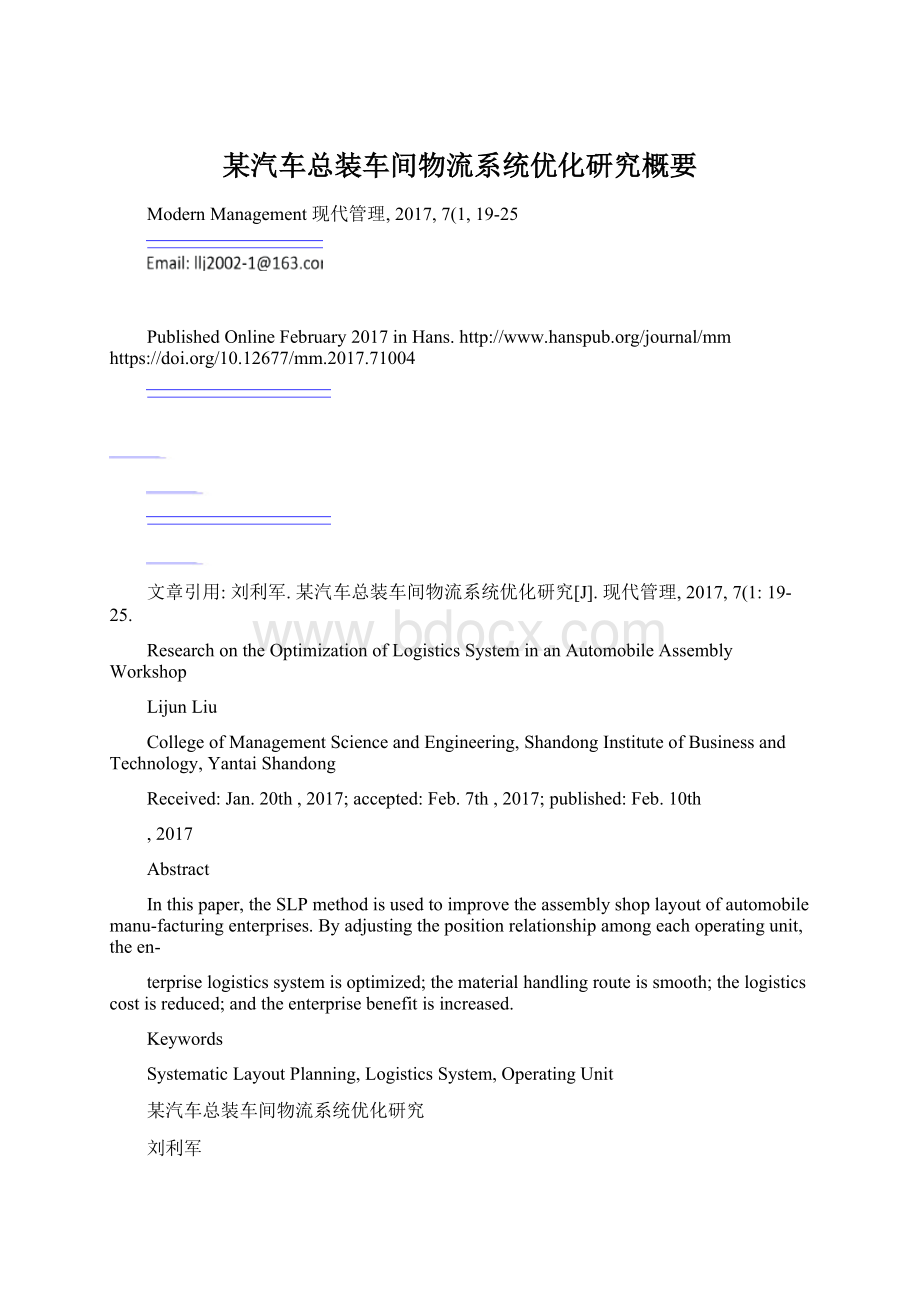
某汽车总装车间物流系统优化研究概要
ModernManagement现代管理,2017,7(1,19-25
PublishedOnlineFebruary2017inHans.http:
//www.hanspub.org/journal/mmhttps:
//doi.org/10.12677/mm.2017.71004
文章引用:
刘利军.某汽车总装车间物流系统优化研究[J].现代管理,2017,7(1:
19-25.
ResearchontheOptimizationofLogisticsSysteminanAutomobileAssemblyWorkshop
LijunLiu
CollegeofManagementScienceandEngineering,ShandongInstituteofBusinessandTechnology,YantaiShandong
Received:
Jan.20th,2017;accepted:
Feb.7th,2017;published:
Feb.10th
2017
Abstract
Inthispaper,theSLPmethodisusedtoimprovetheassemblyshoplayoutofautomobilemanu-facturingenterprises.Byadjustingthepositionrelationshipamongeachoperatingunit,theen-
terpriselogisticssystemisoptimized;thematerialhandlingrouteissmooth;thelogisticscostisreduced;andtheenterprisebenefitisincreased.
Keywords
SystematicLayoutPlanning,LogisticsSystem,OperatingUnit
某汽车总装车间物流系统优化研究
刘利军
山东工商学院管理科学与工程学院,山东烟台
收稿日期:
2017年1月20日;录用日期:
2017年2月7日;发布日期:
2017年2月10日
摘要
本文利用SLP方法对汽车制造企业总装车间布局进行改善,通过调整各作业单位间的位置关系,使企业物流系统得到优化,物料搬运路线顺畅,物流成本降低,企业效益增加。
刘利军
关键词
系统布置设计,物流系统,作业单位
Copyright©2017byauthorandHansPublishersInc.
ThisworkislicensedundertheCreativeCommonsAttributionInternationalLicense(CCBY.
http:
//creativecommons.org/licenses/by/4.0/
1.引言
随着中国汽车制造业的发展,市场竞争日益激烈,已经从卖方市场转变为买方市场,以卡车制造企业为例,竞争格局从当初的“一汽解放”与“东风汽车”两雄争霸,发展到现在的一汽解放、东风汽车、北汽福田、中国重汽、陕汽集团、上汽红岩、北奔重卡、安徽江淮等群雄逐鹿的局面。
面对着复杂多变的个性化市场需求,各汽车制造企业都感受到前所未有的巨大的竞争压力。
企业之间的竞争也不再是单纯的价格竞争,而是表现为以产品设计、质量、成本、交货时间、对顾客需求的反应速度、售后服务、供应链等为中心的综合实力的竞争。
这就需要企业从自身实际情况出发,按照高效益、低成本的要求,迅速改变企业目前的物流运作模式,不断持续改进物流系统,提高企业的竞争力[1],获得更好的生存与发展的空间。
汽车制造企业物流系统快速、高效的运作能够有效降低物流成本,帮助企业改善内外部工作环境,提升企业市场竞争地位,增加市场份额,获得更大经济效益。
合理的工厂布局设计是优化企业物流系统,提高工作效率,降低运作成本的先决条件。
本文以某汽车制造有限公司总装车间布局为背景,利用系统布置设计(SystematicLayoutPlanning,简称SLP法[2]对其进行优化,意在改善其物流运作环境,降低物流成本。
2.车间布局及物流概况
该总装车间承担中重型车二类底盘及整车装配、驾驶室内饰、前桥分装、后桥分装、平衡轴弹簧分装、发动机与变速器合装、车轮总成装配及充气,整车检测等任务。
年产中重型卡车2万辆。
汽车装配生产工艺流程如图1所示。
汽车整车装配需要的分装合件主要包括:
平衡轴合件、后桥、前桥、发动机总成、轮胎等部件。
总装车间布局及物流动线如图2所示。
从上图中的物流动线可以看出,总装车间存在底盘件存放区域、分装区域及人员活动区域布置不合理现象,造成物流路线交叉,人员及物料移动路线较长,导致物料搬运时间增加,物流成本上升,影响了总装流水线的生产效率。
针对上述问题采用SLP法对车间布局进行优化。
3.车间布局优化
3.1.作业单位划分
根据总装车间现有设施划分作业单位如表1所示。
3.2.物流分析
SLP中将物流强度划分为超高物流强度、特高物流强度、较大物流强度、一般物流强度和可忽略搬
OpenAccess
刘利军
Figure1.Automobileassemblyprocessflowchart
图1.汽车装配工艺流程图
Figure2.Layoutandlogisticsroadmapbeforeimproving
图2.改善前布局及物流路径图
刘利军
运5个等级,分别用符号A、E、I、O、U来表示,其物流强度逐渐减小,其对应的物流路线比例分别为10%、20%、30%、40%、0%,所承担的物流量比例分别为40%、30%、20%、10%、0%。
主要作业单位对及物流强度如表2所示,表中未列出作业单位对物流强度等级为U级。
3.3.非物流分析
划分作业单位间的相互关系密切程度及非物流影响因素(理由如下表3所示。
3.4.综合相互关系分析
首先,确定物流与非物流相互关系的相对重要性比例取m:
n=1:
2。
其次,量化物流强度等级和非物流的密切程度等级如表4(部分数据所示。
最后,建立综合相互关系图,如图3所示。
Table1.Operatingunit
表1.作业单位
序号作业单位名称备注
1底盘件存放区主要存放各工位装配所需零部件
2车头内饰板、车架存放区总装线所需车架、驾驶室装配所需内饰板
3转向器合件分装区12工位安装所需转向器合件的分装
4传动轴存放区8工位装配所需传动轴存放区
5平衡轴分装区2工位所需平衡轴、钢板弹簧库存及分装区
6后桥分装区7工位所需后桥及钢板弹簧存放及分装区
7前桥分装区9工位所需前桥及钢板弹簧存放及分装区
8内饰线驾驶室内饰装配线
9总装线2工位总装线关键工位
10总装线7工位
11总装线8工位总装线关键工位
12总装线9工位
13总装线12工位总装线关键工位
Table2.Logisticsintensityofmainoperatingunits
表2.主要作业单位对物流强度
序号作业单位对物流强度物流强度等级序号作业单位对物流强度物流强度等级
11--96.603E105--104.931I
21--101.812O116--106.605A
31--110.709O127--127.219A
41--120.583O1310--116.103E
51--130.012O1410--123.988I
62--82.493O1510--132.016O
72--94.458I1611--126.532E
83--124.967I1711--132.998O
94--116.458E1812--134.968I
刘利军
Table3.Non-logisticsintensitysummarysheet表3.非物流强度汇总表
序号作业单位对(物流关系
非物流密切程度等级
理由代码序号作业单位对(物流关系
非物流密切程度等级
理由代码编码及理由
11-
2I7125-9I1、91工艺衔接要求2作业性质相似3使用同种工位器具4使用相同的加工设备5同一组人员操作6工作联系频繁程度7便于监督和管理
8使用的频繁和紧急程度9使用同种文件档案
21-9I6、71
36-7O2、331-10O6、71
46-10E1、741-11O6、71
57-12E1、751-12O6、71
610-11A1、961-13O6、
71710-12I7、972-7O5、61
810-13I7、
982-8I6、81911-12A5、992-9I6、82011-13O5、9103-13E1、72112-13O5、911
4-11
E
1、7
Figure3.Comprehensivecorrelationdiagramofoperatingunit图3.作业单位综合相互关系图
刘利军Table4.Operatingunitcomprehensivecorrelationcalculationtable表4.作业单位综合相互关系计算表关系密切程度序号作业单位对综合关系非物流关系(加权值:
2等级121-21-3IU分值20……76777811-1211-1312-3AOO411EOI3121134AOI物流关系(加权值:
1等级UU分值00分值40等级IUTable5.Rankingtableofcomprehensiveproximitydegreeforoperatingunit表5.作业单位对综合接近程度排序表作业单位代号综合接近程度排序19427833104311531266977783139851013111132121331386928101112564113Figure4.Theoperatingunitpositiondiagram图4.作业单位位置相关图3.5.车间作业单位位置相关图根据综合相互关系级别高低按照综合接近程度分值高低进行排序(如表5所示,确定不同级别作业单位间的位置关系。
得到作业单位位置相关图如图4所示。
据此对总装车间布局进行调整,得到图5所示的改善后布局图。
24
刘利军更衣室工艺办公室楼梯车架存放区男浴女浴室室质量办公室技能培训洗手间室看板底盘件存放处驾驶室内饰大板块2工位平衡轴分装区处放存件盘底车架装配线内饰装配线7工位内饰仓库8工位9工位前桥分装区传动轴存放处后桥分装区驾驶室库存12工位转向器合件分装区发动机分装区变电供电处内饰班组活动区分装一班活动区分装二班活动区洗手间Figure5.Improvedlayoutchart图5.改善后布局图4.小结本文利用系统布置设计(SLP法对总装车间进行布局优化,结果表明,改善后的车间布局使工艺过程更具柔性,缩短了平衡轴、转向器合件、前桥以及后桥的装配作业周期,使物流运作更加顺畅,减少了物料搬运距离,降低了物流成本,提高了生产效率,同时也使总装作业现场环境得到极大的改善。
基金项目山东省自然基金资助项目,项目编号:
ZR2014GL007。
参考文献(References[1][2]易铎楠,辛清,赵鸿文.汽车制造企业精益供应链物流系统研究[J].企业改革与管理,2016(8:
147-151.方庆琯,王转.现代物流设施与规划[M].北京:
机械工业出版社,2009:
162-177.25
期刊投稿者将享受如下服务:
1.2.3.4.5.6.7.投稿前咨询服务(QQ、微信、邮箱皆可为您匹配最合适的期刊24小时以内解答您的所有疑问友好的在线投稿界面专业的同行评审知网检索全网络覆盖式推广您的研究投稿请点击:
http:
//www.hanspub.org/Submission.aspx期刊邮箱:
mm@hanspub.org