水泥生产设备及电气控制.docx
《水泥生产设备及电气控制.docx》由会员分享,可在线阅读,更多相关《水泥生产设备及电气控制.docx(17页珍藏版)》请在冰豆网上搜索。
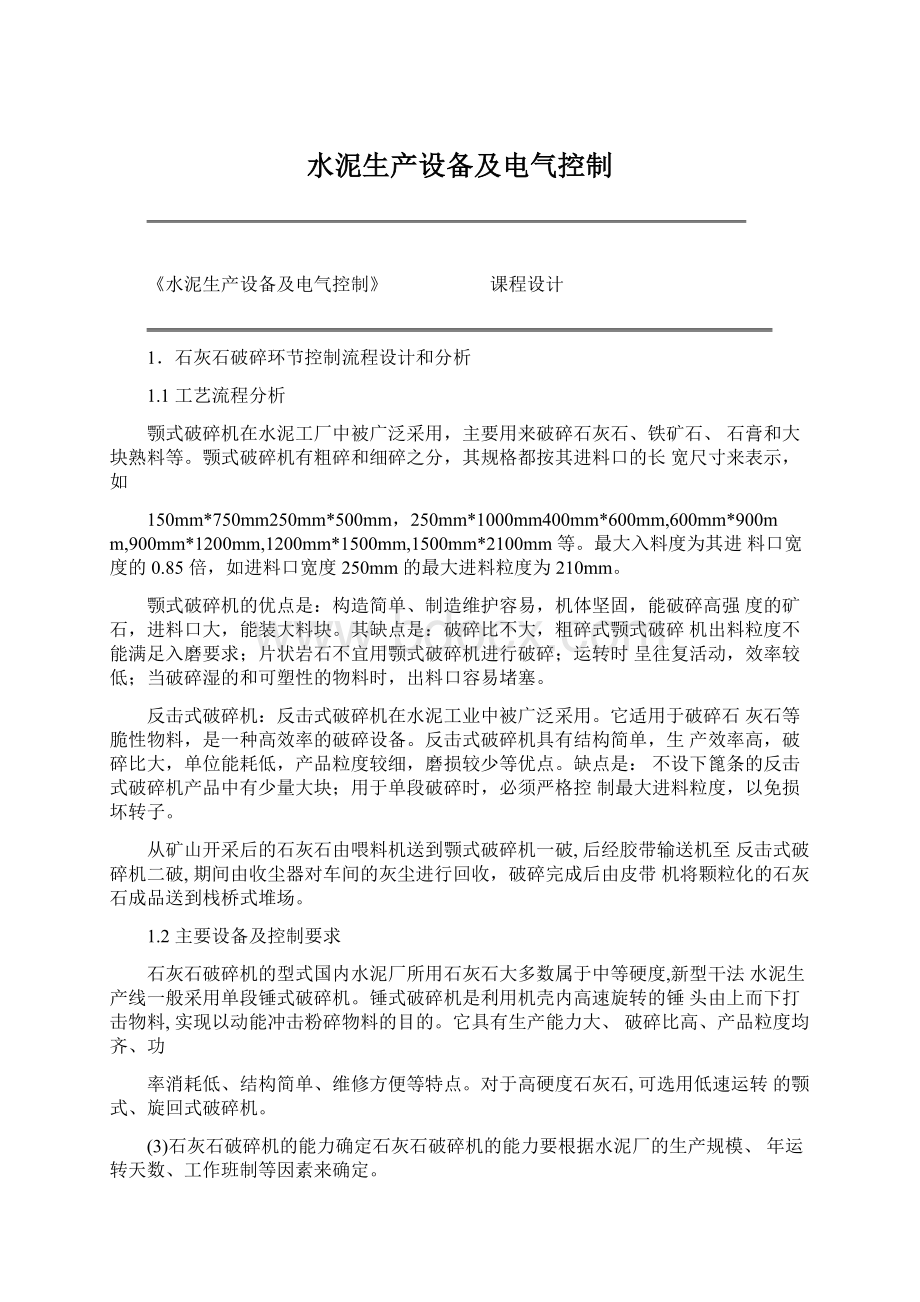
水泥生产设备及电气控制
《水泥生产设备及电气控制》 课程设计
1.石灰石破碎环节控制流程设计和分析
1.1工艺流程分析
颚式破碎机在水泥工厂中被广泛采用,主要用来破碎石灰石、铁矿石、石膏和大块熟料等。
颚式破碎机有粗碎和细碎之分,其规格都按其进料口的长宽尺寸来表示,如
150mm*750mm250mm*500mm,250mm*1000mm400mm*600mm,600mm*900mm,900mm*1200mm,1200mm*1500mm,1500mm*2100mm等。
最大入料度为其进料口宽度的0.85倍,如进料口宽度250mm的最大进料粒度为210mm。
颚式破碎机的优点是:
构造简单、制造维护容易,机体坚固,能破碎高强度的矿石,进料口大,能装大料块。
其缺点是:
破碎比不大,粗碎式颚式破碎机出料粒度不能满足入磨要求;片状岩石不宜用颚式破碎机进行破碎;运转时呈往复活动,效率较低;当破碎湿的和可塑性的物料时,出料口容易堵塞。
反击式破碎机:
反击式破碎机在水泥工业中被广泛采用。
它适用于破碎石灰石等脆性物料,是一种高效率的破碎设备。
反击式破碎机具有结构简单,生产效率高,破碎比大,单位能耗低,产品粒度较细,磨损较少等优点。
缺点是:
不设下篦条的反击式破碎机产品中有少量大块;用于单段破碎时,必须严格控制最大进料粒度,以免损坏转子。
从矿山开采后的石灰石由喂料机送到颚式破碎机一破,后经胶带输送机至反击式破碎机二破,期间由收尘器对车间的灰尘进行回收,破碎完成后由皮带机将颗粒化的石灰石成品送到栈桥式堆场。
1.2主要设备及控制要求
石灰石破碎机的型式国内水泥厂所用石灰石大多数属于中等硬度,新型干法水泥生产线一般采用单段锤式破碎机。
锤式破碎机是利用机壳内高速旋转的锤头由上而下打击物料,实现以动能冲击粉碎物料的目的。
它具有生产能力大、破碎比高、产品粒度均齐、功
率消耗低、结构简单、维修方便等特点。
对于高硬度石灰石,可选用低速运转的颚式、旋回式破碎机。
(3)石灰石破碎机的能力确定石灰石破碎机的能力要根据水泥厂的生产规模、年运转天数、工作班制等因素来确定。
石灰石破碎车间的位置石灰石破碎车间一般布置在矿山或在生产厂区内。
破碎车间的位置要充分考虑石灰石矿山和生产厂区的距离远近、重型车辆的运输条件、料流是否顺畅、适合破碎机高差布置的地形等因素来确定是否设置在矿山还是布置在厂区。
石灰石单段破碎车间的进、出料高差大,一般在6~12米左右,为了利用地形,高进低出布置紧凑,节省土建工程量,使用检修也方便,车间位置一般布置在斜坡上,这是目前石灰石破碎车间的主要布置型式———
0
台阶式布置,另一种是地坑式布置:
这种布置型式一般在无法满足破碎机高差要求的生产厂区内使用,破碎系统的主要设备设计在地坑内,土建工程量大,使用检修也不方便。
我国水泥厂所用石灰石大多属于中等硬度,因此可供选择的设备的类型也很多。
当石灰石中含有较多的粘性夹缝土时,如选用鄂式、
回旋式破碎机,则容易造成腔下部的堵塞,如选用锤式破碎机也容易造成下篦条的堵塞;反击式破碎机的防堵性能也不好。
若采用破碎兼烘干流程(向破碎机通入空气),用锤式、反击式破碎机来破碎粘性物料有良好效果。
对于片状石灰石,宜选用旋回式破碎机。
如选用鄂式破碎机,则片状石灰石容易从机腔中滑下而不能有效地受到压碎作用,根据设计原则和已计算的数据,可选用反击式破碎机,因其破碎比可达50以上,它就为单段破碎创造了条件,选用一台破碎机即可满足所需破碎比的要求,则以一段破碎为宜,一段较之两段或多段具有设备台数少,扬尘点小,生产流程简单、车间占地面积小、基建投资小、经营费用低,劳动生产率高等优点。
而且反击式破碎机比锤式破碎机更多地利用了冲击与反击作用,因此其破碎效果好、效率高、破碎比较大,产品较细、磨损较小。
传统的石灰石破碎系统多采用两段或一段破碎。
从矿山开采后的
石灰石先进入颖式破碎机进行一破碎之后由胶带输送机运至锤式破
碎机进行二破或者由PF1010反击式破碎机进行一段破碎后进贮库
供生产使用。
这样破碎后的石灰石粒度相差悬殊小粒径可在10毫米以下大粒径可达30-40毫米,由于粒度不均常影响生料磨台时产量的提高。
在同样的研磨时间内,常见大颗粒石灰石不易磨细而从磨尾甩出。
1.3水泥厂石灰石破碎及预均化流程图
图1-1石灰石破碎及预均化电机流程图
1
1.4电气控制流程图
图1-2石灰石粉碎工艺流程图
2.原料粉末和废气处理系统控制流程设计和分析
2.1工艺流程分析
原料配料设四个库,分别储存石灰石、砂岩、铝矾土、铁矿石;各种原料按生产品种要求进行配合,并经胶带输送机送至原料磨。
原料磨采用辊式磨,当入磨物料粒度≤80mm,水份≤10%,出磨生料细度为80μm筛筛余12%,水份为0.5%时,磨系统产量为220t/h。
各种原料在磨内进行粉磨、烘干后,经选粉机分选,粗粉返回磨盘重新粉磨,合格成品随出磨气流经旋风分离器收集。
收集下来的成品经空气斜槽、斗式提升机、空气输送斜槽入生料库储存、均化。
出旋风分离器的气体经循环风机,一部分气体作为循环风入磨,其余气体则通过袋收尘器净化后,经窑尾排风机和烟囱排入大气。
袋收尘器及增湿塔收下的粉尘经拉链机,汇同出磨生料一起经空气斜槽、胶带提升机及空气斜槽入生料均化库。
当增湿塔湿底时,增湿塔排出的湿灰经增湿塔下的可逆螺旋输送机、电动翻板阀进
2
入生料均化库。
当原料磨正常生产时,来自窑系统的废气经高温风机、增湿塔,全部进入原料磨作为烘干热源。
试生产或窑尾热源不足时,可利用辅助热风炉。
从原料磨排出的废气由循环风机送入废气处理系统。
为均化与储存生料,设有一座Φ18x62mNGF均化库,均化库的有效储量为11900t,储存期为1.55d。
均化库底部为倒锥体,出库生料经库底斜槽、流量控制阀、送至带有荷重传感器的生料搅拌仓,仓下设有两套流量控制阀和两台固体流量计,喂料仓下流量控制阀根据入窑生料量调节。
经计量后的生料,由斜槽、提升机送入窑尾预热器二至一级旋风筒上升管道。
2.2主要设备及控制要求
1.增湿塔出口气体温度的控制
通过调节增湿塔的喷水量,控制增湿塔出口气体温度。
2.磨机出口气体温度的控制
通过调节增湿塔的喷水量、循环风阀门开度、调节冷风阀门(尽量不用)控制入磨风温,稳定磨机出口气体温度。
3.磨机风环压差的控制
原料磨内物料量的多少,反映在磨机风环压差上,通过调整喂入磨内的物料量,可稳定磨机风环压差。
4.生料的质量自动控制
通过调节各原料喂料装置的比例,自动控制生料化学成分。
2.3电气控制流程图
图2-1原料粉磨和废气处理流程图
二、原料粉磨和废气处理系统控制流程设计和分析
(一)原料粉磨控制流程设计和分析
1.工艺流程
原料磨采用辊式磨,当入磨物料粒度≤80mm,水份≤10%,出磨生料细度为80μm筛筛余12%,水份为0.5%时,磨系统产量为210t/h。
各种原料在磨内进行粉磨、烘干后,经选粉机分选,粗粉返回磨盘重新粉磨,合格成品随出磨气流经旋风分离器收集。
收集下来的成品经空气斜槽、斗式提升机、空气输送斜槽入生料库储存、均化。
出旋风分离器的气体经循环风机,一部分气体作为循环风入磨,其余气体则通过袋收尘器净化后,经窑尾排风机
3
和烟囱排入大气。
袋收尘器及增湿塔收下的粉尘经拉链机,汇同出磨生料一起经空气斜槽、胶带提升机及空气斜槽入生料均化库。
当增湿塔湿底时,增湿塔排出的湿灰经增湿塔下的可逆螺旋输送机、电动翻板阀进入生料均化库。
当原料磨正常生产时,来自窑系统的废气经高温风机、增湿塔,全部进入原料磨作为烘干热源。
试生产或窑尾热源不足时,可利用辅助热风炉。
从原料磨排出的废气由循环风机送入废气处理系统。
3.原料粉末控制流程图
4
(二).废气处理控制流程1.用电设备表
序号
名称
电压
功率
控制要求
备注
1M
收尘器控制
器
380V
27KW
送电
2M1
回转下料器
1
380V
1.1KW
恒速
2M2
回转下料器
2
380V
1.1KW
恒速
2M3
回转下料器
3
380V
1.1KW
恒速
2M4
回转下料器
4
380V
1.1KW
恒速
2M5
回转下料器
5
380V
1.1KW
恒速
2M6
回转下料器
6
380V
1.1KW
恒速
2M7
回转下料器
7
380V
1.1KW
恒速
2M8
回转下料
器8
380V
1.1KW
恒速
3M1
拉链机1
380V
3M2
拉链机1
380V
4M
排风机
690V
调速
变频
5
控制流程图:
三、简述烧成系统的组成环节
3.1系统简介
熟料煅烧系统作为水泥生产过程中的一个环节,承担着将生料烧成熟料的重要作用,人们形象的称之为水泥厂的心脏。
近几十年来,水泥工业窑的发展非常迅速,尤其是现在以窑外分解技术的迅速崛起,它在提高生产效率有效降低熟料单位热耗方面的巨大优势,使之成为目前水泥行业的主要技术。
3.2系统生产工艺过程
生料喂入一级旋风筒进风管道开始,经预热、预分解后入回转窑煅烧成水泥熟料,通过倾斜推动篦式冷却机的冷却、破碎并卸到链斗输送机输入熟料库为止。
本系统分为:
生料预热与分解、三次风管、熟料煅烧、熟料冷却破碎及输送熟料四大部分。
6
系统的组操作
系统的启动是要依一定的顺序进行的,否则会对设备造成伤害的。
1组启动顺序:
窑中稀油站系统→窑头一次风机→油泵→间歇辅传翻窑→窑头喂煤空压机组→窑头喂煤螺旋泵组→窑头喂煤秤→熟料库顶收尘组→熟料输送组→窑头电收尘组→冷却机干油泵→冷却机拉链机锤破组→冷却风机(组)→窑尾收尘回灰及增湿塔回灰系统→启动高温风机稀油站及液力偶合器加油站→窑尾收尘后排风机→连续慢翻窑→启动高温风机→称重仓收尘组→喂料风机组(空压机组)→喂料组→入称重仓→生料库底风机组→分解炉喂煤组→用主传连续翻窑→分解炉喂煤→启动冷却机→窑头(窑尾)收尘高压送电→启动冷却机
2组传顺序止料、止分解炉后的顺序基本与组启动顺序相反。
停车操作
系统停车前先把停车计划通知到原料粉磨、煤粉制备等车间,使其做好充分的准备,并随时联系,以便相互配合。
原则上希望系统停车后,能做到窑空,煤粉仓空,运输设备空但主要还是应当根据生产需要。
另外,原料粉磨、煤粉制备系统需要关闭热风阀或使热风改向时,一定要与中控操作员联系并征得准许后方可进行有关设备的操作。
注意:
不要没有准备而造成烧成系统的气流突然变化,干扰窑的工作状况。
系统停车时,有自动调节回路的设备一般都应切换成手动位置,正常停车的顺序是:
炉、窑减煤、减料;先停炉、停料、后停窑。
窑尾旋风预热器
一、新型干法水泥生产线均采用旋风预热器,(其结构如右图)物料从上一级下料管下来后,被下一级管道上来的热气流吹上去,在管道内迅速换热,然后进入旋风筒内进行气固分离,气体从内筒上升到上一级管道,物料则被分离下来,进入下一级。
二、它的热交换主要发生在管道中,而分离则完全是在旋风筒内。
众多的资料表明,气固间80%以上的热交换是在入口管道内进行的,热交换方式以对流换热为主。
物料在转向被加速的起始区段内完成换热。
7
物料与气体完成换热后,必须进行气固分离,分离出的物料向高温区(下一级预热器,分解炉或回转窑)运动,进行进一步的预热、分解或煅烧。
否则,物料将随气流一起流向低温区,使预热效果降低,甚至起不到预热作用。
窑中及窑头
将生料煅烧成熟料经过冷却后送人熟料库。
主要设备:
窑中拖动电机调速范围和调速精度要求高,选择调速方式时要慎重。
篦冷机
一、篦冷机工作原理是:
高温熟料和空气的充分热交换,以达到高效冷却熟料
和热回收的效果。
二、冷却机主要完成的任务:
1.尽可能多的把熟料中
的显热(1200~1500KJ/Kg熟料)回收进烧成系统,加热二、三次空气,提高二、三次风温,尽可能的将烧成系统的燃料消耗降至最低。
2.选择适当的熟料冷却速度,以提高熟料质量和易磨性,由窑口卸出的熟料(温度
1300~1400℃)进入冷却机后,吹以冷风(等于环境温度),熟料受到急冷,熟料中的液相来不及完成结晶,一部分呈玻璃相,另一部分即使结晶也比普通冷却速度得到的晶粒更细,这种熟料可以制成标号更高的水泥。
3.最后将熟料冷却到尽可能低的温度,以满足熟料输送、贮存和水泥粉磨的要求。
8
四、水泥粉磨系统的控制流程设计和分析
粉磨过程是水泥生产过程中的重要环节,被应用于水泥生产的多个工序中,如生料工序中生料粉磨、孰料煅烧工序中煤粉粉磨及最后成品水泥的粉磨。
水泥粉磨是水泥生产的最后一个环节,水泥粉磨质量的好坏直接影响着成品水泥质量。
水泥粉磨是指生产水泥用的孰料、石灰石、粉煤灰和石膏四种混合物在粉磨设备内经挤压、研磨,颗粒逐渐减小,最终达到一定细度的物理过程。
由于水泥粉磨过程复杂,生产设备种类、数量众多,且生产环境恶劣,影响粉磨效果的因素很多,为达到理想的粉磨效果,需对粉磨设备和粉磨控制技术提出了更高的要求。
4.1水泥磨生产流程及设备简介
水泥粉磨即将水泥粉磨原料熟料、石灰石、粉煤灰及石膏在配料站经配料后用胶带输送机输送至水泥磨,胶带输送机上设置除铁器。
混合料水泥磨内进行粉磨、烘干后,经选粉机分选,粗粉返回磨盘重新粉磨,合格成品随出磨气流经收尘器收集。
收集下来的成品经斜槽、斗式提升机输送到矿水泥库中储存;粉磨过程中产生的粗渣(粗料)经由胶带输送机,斗式提升机,管道除铁器,锁风下料阀返回磨内继续粉磨,胶带输送机上设置除铁器;出磨气流经过袋收尘器净化后,经排风机一部分从烟囱排入大气,另一部分作为循环风与热风炉出来的热风混合后一起入水泥磨,烘干入磨的混合料。
最终合格水泥成品经斜槽,斗式提升机输送到成品库中进行储存,供后续包装及发运工序使用,如图4-1所示。
图4-1立磨生产流程图
立磨是水泥生产中主要的粉磨设备,它主要应用于生料粉磨工序、煤粉粉磨工序和水泥粉磨工序。
相对于球磨机来说,立磨设备相对较少,且生产能耗也低。
本项目使用的为我公司自主研发的立磨具有价高的性价比。
水泥配料环节
1.工艺过程分析
9
库顶:
送料皮带机
库底:
配料称大皮带、废底皮带机皮带机要调速
2物料配比:
由中控室控制,设计时不向用电设备供电。
主要设备:
辊压机:
两台变压电机及辅助设备。
V型选粉机:
恒速
称料仓:
称重
提升机
两个小皮带机
辊压机粉磨系统的工艺流程
辊压机的粉磨工艺系统有预粉磨、混合粉磨、联合粉磨、半终粉磨和终粉磨方式,其中采用联合粉磨方式较为普遍。
1、预粉碎经辊压后料饼直接喂入后续球磨机,磨成成品。
球磨机可开路也可闭路。
2、混合粉磨辊压机和球磨机串联,出球磨机经选粉机选出成品,粗粉返回辊压机。
3、联合粉磨辊压机和球磨机各自承担不同粒度阶段的粉磨作业,如同磨机的粗、细仓,辊压机将物料粒度粉磨至3-5mm,球磨机则从3-5mm再磨到合格细度。
4、半终粉磨部分成品是由辊压机产生的,即分级设备从挤压的料饼经打散后选出成品,选粉后粗料再喂入后续磨机磨细,然后经分级设备选出成品。
5、终粉磨不带后续磨机,全部粉磨作业有辊压机完成,要求辊压机生产高细粉磨。
该系统需配打散机和高效选粉机,流程简单,能耗低。
4.2系统设备控制要求
水泥生产现场各种设备是实现既定生产工艺的基础,生产过程中各种工艺参数的调整也需要现场专门的设备来实现,因此对现场设备的控制质量,很大程度上决定了产品质量的好坏,进而影响了水泥企业经济效益的好坏。
现场的主要设备均设有中控控制和手动控制两种控制方式。
在设备现场设置按钮盒或控制箱,并装有带统一钥匙的控制方式选择开关,设有中控、零位、手动三种选择方式。
1)中控控制时,在中控室操作员可对设备进行启动或停止操作;
2)手动控制时,现场人员可对设备进行启动、停车等操作;
3)零位方式时,在检修时使用,中控及手动均不能对设备进线启动,以确保人员安全;
4)故障时,中控室及现场均可紧急停车。
同时,要求在中央控制室监控画面上能够以某种方式提示操作员,此设备当前处于那种工作状态,可以进行那种操作。
在本项目中将监控画面上的设备状态以不同颜色状态来区分:
1)绿色代表有备妥,设备满足中控启动条件,中控可以启动设备;
2)绿色闪烁代表设备由控制室启动,正在运行中;
3)灰色表示设备没有备妥,设备有故障或正处于手动控制中;
4)红色闪烁代表设备有故障,需要处理。
10
立磨系统的组连锁如图4-2所示,其共8分组,启动顺序如下,停机顺序相反。
图4-2水泥磨分组及启动顺序示意图
4.3系统控制方案
生产线上的设备均采用计算机控制系统控制,根据生产流程和设备特点,控制系统设一个中控室,以实现从原料进场至水泥出库的生产线的计算机控制,构成一个主工艺流程的计算机控制网络系统,完成对现场设备的控制、现场信息采集与交换、生产信息汇总等。
由于本项目设备数量较大、且工艺布置较远,因此需要根据现场环境、工艺要求对控制系统进行分组控制,分区时要遵循以下原则:
(1)在生产流程上联系紧密的设备、数字、模拟量,要分配到同现场控制站中,以便于系统的布置;
(2)尽量把距离控制站较近的设备放在同一控制站下,以减少材料消耗及对采集信号的影响;
(3)依据控制站带载能力。
设备布置时应考虑控制器的处理能力和输入输出模块的合理使用。
本系统采用浙江中控ECS-700系统,系统设置1个控制域,控制域下设3个控制站,分别为水泥磨控制站、矿渣磨控制站;设置1个操作域,操作域下
11
设置5个操作站。
水泥磨立磨系统自身带有一套AB公司PLC控制系统,本系统通过支持PROFIBUS协议的主站通信模块COM763,来实现整个ECS-700系统与水泥磨控制系统的信息交换,并实现必要的控制功能。
系统的整体结构采用标准DCS分层,分为:
现场设备层、过程控制层、集中操作监视层。
它们通系统通信网络构成配合紧密的整体。
4.3.1主要控制回路及参数
1)配料站配料控制
通过配料站各原料定量给料机给料量的控制,实现磨喂料量的控制。
2)磨机进风口气体温度的控制
通过调节热风炉供煤量、电动配风阀的开度、冷风阀的开度与循环风阀门的开度实现磨机进风温度的调节。
3)磨机出口气体温度的控制
通过调节磨内的喷水量、电动配风阀的开度、循环风阀门开度、调节冷风阀门控制入磨风温,实现稳定磨机出口气体温度。
4)磨机内物料量的控制
水泥磨磨内物料量的多少,反映在磨机风环压差上,通过调整喂入磨内的物料量,研磨压力,可稳定磨机风环压差。
5)水泥成品细度控制
主要通过调节选粉机转速和磨内气流量来实现。
选粉机转速可通过调节变频器频率来实现,而磨内气流量可通过电动执行器调节阀门开度来实现。
4.3.2电力拖动方案
1)电动机选型及电控设备选择
电动机的容量、型式和调速方式由工艺专业在设备选型中确定。
交流电机容量大于等于200kW时选用10kV电动机,容量小于200kW时选用380V电机。
低压电机主回路采用自动空气开关作短路保护,热继电器作过负荷保护,交流接触器作失压保护。
对于10m以上胶带输送机设拉绳开关,以后每隔40m增设一拉绳开关。
在提升机底部设置带钥匙检修按钮,确保检修时人身安全。
2)电动机的调速及调速电动机的控制
一般要求调速的电动机采用交流电动机,少数调速电动机采用直流电动机。
交流调速电动机采用全数字式变频调速控制装置进行控制,直流电动机采用全数字式可控硅直流调速控制装置进行控制。
3)车间用电设备供电
高压电机和变压器由总降压站供电。
低压配电采用一级配电方式。
所有低压用电设备由电气室MCC柜统一配电及控制。
照明及杂动力电源与主用电设备电源分开,分别由总降压站照明变及各电气室供电。
4)低压回路保护
12
电动机的保护:
采用低压断路器的电磁脱扣器作为短路保护;三相热继电器作为过负荷保护;接触器线圈作为失压保护。
配电线路的保护:
采用低压断路器的复式脱扣器作为短路和过负荷保护。
4.3.3控制系统配置
本工程全线采用集散控制系统。
根据工艺生产流程、生产车间总图布置,结合实际生产操作的需要,设置中央控制室及三个现场控制站。
本项目设三个控制站:
水泥磨控制站、矿渣磨控制站和包装及发运控制站,各种控制功能包括过程控制、顺序控制等均由电气室内的现场控制站独立完成。
现场控制站与中央控制室内的操作站通过高速数据通讯网络进行通讯,从而形成一个完整的集散型控制系统。
五、简述水泥输送与包装系统的工艺流程
5.1水泥包装及发运工序简介
水泥包装和发运是水泥生产的最后一环节,它将水泥生产的最终产品运送至用户手中。
本工序共分为水泥散装和水泥袋装两个部分。
来自水泥粉磨系统的水泥经斗式提升机、空气输送斜槽送入水泥库内。
水泥库底设有减压锥及充气装置,由罗茨鼓风机供气。
水泥经库底卸料装置、空气输送斜槽送至水泥包装系统和水泥散装系统。
1)水泥散装
来自成品水泥库的水泥首先进入散装系统2个水泥汽车散装库,每个库设两若干套水泥汽车散装机。
库下设有散装智能发运系统,随时计量装车量,避免多装或少装。
13
图5-1水泥散装流程图
2)水泥袋装
水泥袋的主要设备是包装机,它将散装水泥装入标准袋中。
来自成品水泥库的散装水泥经输送装置首先储存在包装机上部储存仓中,仓下设给料机,仓内的水泥
在压缩空气的作用下具有较好的流动性,在物料重力作用下,进入包装机,再通过出料嘴灌入水泥袋内。
包装机一般都具有自动称量控制,即在水泥袋内质量达到设定值使,会自动停止下料,直至下一水泥袋安放到位。
本项目设置1台八嘴回转式包装机,单台包装机的能力为90t/h。
包装好的袋装水泥(50kg标准袋),经卸袋输送系统送入汽车装车机进行装车发运,主要工艺流程如图。
14
图5-2水泥包装流程图
15
16