超临界和超超临界机组问题.docx
《超临界和超超临界机组问题.docx》由会员分享,可在线阅读,更多相关《超临界和超超临界机组问题.docx(28页珍藏版)》请在冰豆网上搜索。
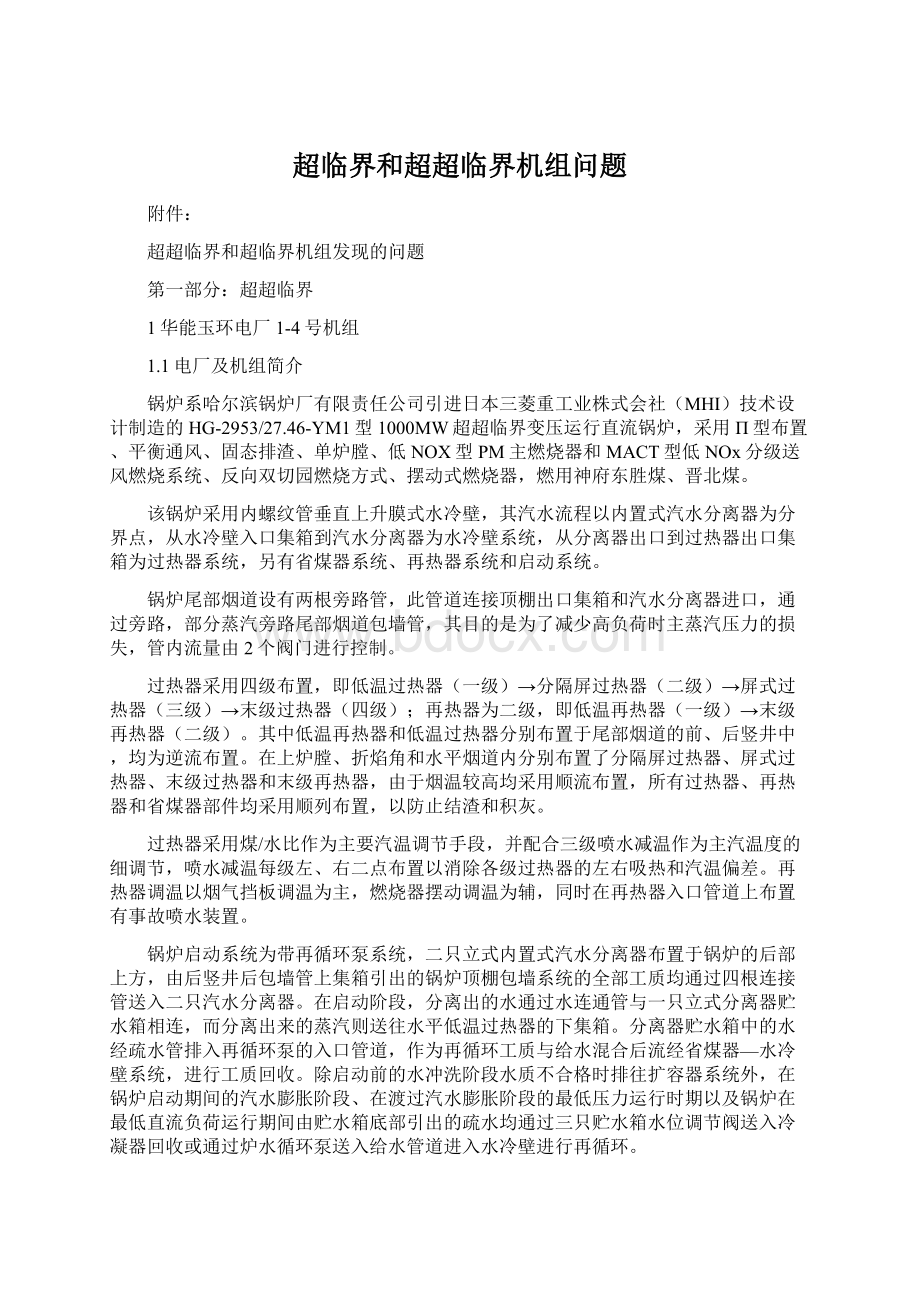
超临界和超超临界机组问题
附件:
超超临界和超临界机组发现的问题
第一部分:
超超临界
1华能玉环电厂1-4号机组
1.1电厂及机组简介
锅炉系哈尔滨锅炉厂有限责任公司引进日本三菱重工业株式会社(MHI)技术设计制造的HG-2953/27.46-YM1型1000MW超超临界变压运行直流锅炉,采用П型布置、平衡通风、固态排渣、单炉膛、低NOX型PM主燃烧器和MACT型低NOx分级送风燃烧系统、反向双切园燃烧方式、摆动式燃烧器,燃用神府东胜煤、晋北煤。
该锅炉采用内螺纹管垂直上升膜式水冷壁,其汽水流程以内置式汽水分离器为分界点,从水冷壁入口集箱到汽水分离器为水冷壁系统,从分离器出口到过热器出口集箱为过热器系统,另有省煤器系统、再热器系统和启动系统。
锅炉尾部烟道设有两根旁路管,此管道连接顶棚出口集箱和汽水分离器进口,通过旁路,部分蒸汽旁路尾部烟道包墙管,其目的是为了减少高负荷时主蒸汽压力的损失,管内流量由2个阀门进行控制。
过热器采用四级布置,即低温过热器(一级)→分隔屏过热器(二级)→屏式过热器(三级)→末级过热器(四级);再热器为二级,即低温再热器(一级)→末级再热器(二级)。
其中低温再热器和低温过热器分别布置于尾部烟道的前、后竖井中,均为逆流布置。
在上炉膛、折焰角和水平烟道内分别布置了分隔屏过热器、屏式过热器、末级过热器和末级再热器,由于烟温较高均采用顺流布置,所有过热器、再热器和省煤器部件均采用顺列布置,以防止结渣和积灰。
过热器采用煤/水比作为主要汽温调节手段,并配合三级喷水减温作为主汽温度的细调节,喷水减温每级左、右二点布置以消除各级过热器的左右吸热和汽温偏差。
再热器调温以烟气挡板调温为主,燃烧器摆动调温为辅,同时在再热器入口管道上布置有事故喷水装置。
锅炉启动系统为带再循环泵系统,二只立式内置式汽水分离器布置于锅炉的后部上方,由后竖井后包墙管上集箱引出的锅炉顶棚包墙系统的全部工质均通过四根连接管送入二只汽水分离器。
在启动阶段,分离出的水通过水连通管与一只立式分离器贮水箱相连,而分离出来的蒸汽则送往水平低温过热器的下集箱。
分离器贮水箱中的水经疏水管排入再循环泵的入口管道,作为再循环工质与给水混合后流经省煤器—水冷壁系统,进行工质回收。
除启动前的水冲洗阶段水质不合格时排往扩容器系统外,在锅炉启动期间的汽水膨胀阶段、在渡过汽水膨胀阶段的最低压力运行时期以及锅炉在最低直流负荷运行期间由贮水箱底部引出的疏水均通过三只贮水箱水位调节阀送入冷凝器回收或通过炉水循环泵送入给水管道进入水冷壁进行再循环。
锅炉采用正压直吹式制粉系统,配有六台上海重型机器厂生产的HP1163型中速磨煤机,每台磨煤机配有一台沈阳施道克电力设备有限公司生产的EG3690型给煤机。
锅炉在BMCR工况下运行时,五台磨煤机投运,一台磨煤机备用。
磨煤机出口的煤粉细度通过改变其顶部旋转分离器的转速来调节,燃用设计、校核煤种时,煤粉细度R90设计值为15.3%。
锅炉配有成都电力机械厂生产的两台AN42e6(V19+4°)型静叶可调轴流式引风机,上海鼓风机厂有限公司生产的两台FAF30-14-1型动叶可调轴流送风机和两台PAF-19-12.5-2型单吸轴流式一次风机。
1.2发生问题及解决办法
水冷壁壁温偏差问题是哈锅1000MW等级锅炉面临的重要问题,集中反映了引进技术与国内自主技术的矛盾性。
造成这种水冷壁壁温偏差问题的原因有以下2点:
1)水冷壁入口节流缩孔的堵塞问题
由于哈锅1000MW机组水冷壁下部选用的是垂直螺旋管,且本生流量为25%BMCR,为了保证水动力的安全性,水冷壁入口装设有节流缩孔以避免水动力多值性问题出现,但由此带来的问题是对于给水品质和系统的清洁度要求非常高。
系统内的任何杂质都可能堵塞节流缩孔,进而致使对应的管束流量大幅下降,管束金属得到的冷却能力大幅度也同步下降,水冷壁壁温测点示值大幅上升。
2)燃烧系统的投运顺序
哈锅1000MW超超临界锅炉引进的是三菱技术,而三菱原有的运行说明要求燃烧器的投入顺序是自上而下的。
如果首先投入最下层燃烧器,根据辐射换热特性,下部水冷壁吸热量太大,工质焓增太大。
由于汽液两相流动的阻力特性,必然加大了不同管束流动偏差,流动偏差和受热偏差重叠,直接结果是受热强的管子内工质流量更小,必然导致金属壁温偏差更大。
首先投入上层燃烧器,是为了使整个炉膛的辐射热负荷均匀,下部水冷壁和上部水冷壁都占有一定比例的吸热量,这样下部水冷壁的受热偏差和流动偏差都较小,并且通过混合联箱的混合,对上部水冷壁壁温偏差影响也很小。
解决办法
1)首先要通过规范水质,防止外部异物进入水冷壁入口联箱;而当停炉时间较长后,重新启动前,必须安排锅炉冷态冲洗和锅炉的热态冲洗,特别是锅炉起压后的全炉防水对反冲节流缩孔很有效果。
另外,在新建机组调试过程中要防止不同受热面节流缩孔混用、安装不符合规范,重视酸洗过程中的摸管和吹管后的拍片检查工作。
在玉环电厂2号炉试运过程中就发现了因缩孔孔径不符合设计值而发生的水冷壁超温问题。
2)锅炉启动可以以等离子形式投入最下层燃烧器,但投第二层及以后的燃烧器时应满足自上而下的要求,且锅炉带上中负荷后,应尽可能推出最下层燃烧器运行。
3)在锅炉湿态运行过程中,水冷壁壁温偏差大时,可以增大炉水循环泵出力,增大水冷壁入口流量,这有利于缓解水冷壁流动不均匀性,进而减小水冷壁壁温偏差。
甚至,可以进一步探索变水冷壁入口流量的控制思路。
2华电邹县电厂7、8号机组
2.1电厂及机组介绍
邹县电厂四期工程2×1000MW超超临界机组#7锅炉是东方锅炉(集团)股份有限公司(DBC)/东方日立锅炉有限公司(BHDB)与日本巴布科克-日立公司(BHK)联合设计、制造的DG3000/26.15-Ⅱ1型高效超超临界本生直流锅炉,为单炉膛,倒U型布置、平衡通风、一次中间再热、前后墙对冲燃烧、尾部双烟道,复合变压运行锅炉。
炉膛宽33973.4mm,深15558.4mm,高度69700mm。
炉膛四周为全焊式膜式水冷壁,由下部螺旋盘绕上升水冷壁和上部垂直上升水冷壁组成。
沿烟气流程依次布置屏式过热器、高温过热器、高温再热器。
竖井为双烟道结构,前/后烟道深分别为5486.4/9144mm,前烟道布置低温再热器、后烟道布置低温过热器和省煤器,其后布置三分仓回转式空气预热器。
每台锅炉配置2台成都电力机械厂生产的轴流式引风机,上海鼓风机厂有限公司生产的2台轴流式送风机和2台一次风机。
配置2台东方锅炉(集团)股份有限公司生产的回转式三分仓空气预热器。
由刮板捞渣机将炉渣先输送至渣仓,然后由汽车运输的方式除渣。
设置两台三室四电场干式静电除尘器,采用密相正压气力输送方式除灰。
2.2发生问题及解决办法
在邹县电厂7号炉试运过程中,多次发生一次风管煤粉沉积现象,特别是后墙燃烧器积粉更为严重。
经分析与以下因素有关:
1)煤粉颗粒偏粗
邹县电厂7、8号炉选用的是双进双出钢球磨煤机,分离器分离能力受到二次携带的影响,分离效率低下,大量煤粉粗颗粒被携带出来,容易在水平一次风管发生沉积。
2)一次风量小
由于上述的磨煤机分离器分离效率低下,维持磨煤机额定出力的一次风量大大减少,否则磨煤机料位无法保持。
一次风速的减小,使得一次风管内的流速低于积粉流速,甚至由湍流转为层流,层流的输送能力远小于湍流。
实测一次风管温度,发现温度上下偏差大,证实了管内分层流动的现象。
3)一次风管散热严重
由于1000MW锅炉尺寸大,一次风管较长且未保温,散热损失很大。
经测量,至燃烧器入口,温度下降达15~25℃。
在燃用水分大的煤种时,风粉混合物温度易低于露点温度,致使水蒸汽结露,煤粉容易粘结性增强,更容易在管道内沉积。
这也是后墙燃烧器对应一次风管积粉更严重的根本原因。
解决办法:
1)改造磨煤机分离器,提高分离器分离效率,最终改善了煤粉细度,
2)提高一次风量
3)外还通过煤粉管道保温,减少散热。
3上海外高桥电厂二期工程
3.1电厂及机组介绍
上海外高桥发电厂二期工程(2×900MW)机组为我国首次采用进口设备和技术的最大容量超临界机组。
锅炉岛为德国ALSTOM能源公司设计制造的塔式、超临界压力、一次中间再热、扩容式启动系统、平衡通风、单炉膛、四角切向燃烧、露天布置、固态排渣煤粉炉。
汽机岛为德国SIEMENS公司设计制造的超临界、一次中间再热、单轴、四缸四排汽、七级抽汽回热凝汽式汽轮机。
发电机为德国SIEMENS公司设计制造,型号为THDF125/67,采用水-氢-氢冷却方式,旋转整流器、无刷励磁系统、数字式电压调整器。
仪控岛采用日立HIACS-5000M分散系统,包括MCS、SCS、FSS、DAS等控制功能。
汽机本体的DEH、MEH、ETS的控制采用德国西门子TELEPERM-XP分散控制系统实现其功能,其中DEH还涉及密封油、真空、防进水、氢油水辅助系统等控制。
化水系统由业主委托国内设计、采购,二台机组公用。
主要系统包括:
净水系统、补水系统、废水系统、反渗透、循环水加药系统。
每台机组各配置一套凝结水精除盐系统、取样系统和加药系统,采用进口设备,由西门子配套。
3.2发生问题及解决办法
3.2.1吹管临时系统故障
1)临时管道的管径和壁厚偏小,三通叉角度不合理,使得吹管过程中,临时管道内流速太大(最大处蒸汽流速达到音速),且叉管流量分配不均,导致管道局部产生共振爆管;
2)临时管道的支撑设计上,支撑点设计不合理,不利于管道的自由膨胀,部分临时管道相互支撑、悬吊,使管间的振动加剧,引起支撑点的变形损坏。
解决办法:
增大临时系统通径;加强临时系统管道的支撑
3.2.2空气预热器在调试过程中多次发生故障,曾一度制约机组带负荷运行,当机组负荷增加,排烟温度增加到一定值时,空气预热器电流增加,严重时空气预热器过电流跳闸。
内部检查发现传热部件外壳焊缝开裂,传动带局部变形。
锅炉采用直径较大的回转式空气预热器,且烟道结构造成烟速分布状态较差,空气预热器内部受热不均,致使运行过程中,存在着较大的内外温差,从而产生了内外组件之间的胀差,引起预热器内部罩壳发生胀裂和传动带损坏。
因此,设计上考虑不足是预热器故障的最根本原因。
解决办法:
1)在预热器进口烟道加装导流板;
2)改变传动带与空气预热器传热部件的连接方式,由原来的径向支撑改为悬吊支撑,避免了传动带因内部传热部件径向膨胀而引起的损坏;
3)对开裂部分焊缝进行加固和修复。
4)在设备改造过程中,从设计上着手,改变内部结构,解决或消除胀差,才能从根本上解决问题。
4大唐国际宁德电厂二期工程
4.1电厂及机组介绍
福建大唐国际宁德发电有限责任公司二期工程设计2×660MW超超临界燃煤汽轮发电机组。
锅炉为东方锅炉(集团)股份有限公司生产的超超临界参数变压直流炉,采用一次再热、平衡通风、露天布置、固态排渣、全钢构架、全悬吊结构Π型锅炉,型号为DG2060/26.15-II1。
锅炉配有14只全启式弹簧安全阀,其中屏式过热器进口4只,末级过热器出口2只,再热器进口6只,再热器出口2只,过热器出口还装有2只电磁释放阀。
锅炉设计采用前后墙对冲燃烧方式,每台锅炉装设旋流式HT-NR3型燃烧器。
前、后墙各布置18只,分、上、中下三层,每层布置6只,共36只。
锅炉采用低NOx煤粉燃烧器及分级配风方式,在BMCR工况下,炉膛出口NOx含量不大于300mg/Nm3。
制粉系统采用冷一次风正压直吹式制粉系统。
每台锅炉设有6台上海重型机器厂生产的HP1003型弹簧变加载中速磨,5台运行,1台备用,每台磨煤机引出的6根煤粉管道连接到锅炉前墙或后墙同一层燃烧器。
锅炉炉膛风烟系统为平衡通风方式。
选用两台成都电力机械厂生产型号为AN33e6入口静叶可调轴流式引风机;两台上海鼓风机厂有限公司生产型号为FAF25-14-1的动叶可调轴流式送风机,两台上海鼓风机厂有限公司生产型号为PAF17.5-12.5-2的双动叶可调轴流式一次风机。
锅炉还配有炉膛火焰电视摄像装置、炉膛出口烟温探针、炉管泄漏检测装置等安全保护装置。
每台锅炉设置二台福建龙净环保股份有限公司生产的双室五电场静电除尘器(保证效率99.8%),采用正压气力除灰系统,除渣系统采用干式除渣方式。
4.2发生问题及解决办法
4.2.1无炉水泵启动
本锅炉设计有一套带炉水循环泵的启动系统,炉水循环泵置于储水箱与省煤器入口之间,使得机组在启动初期的湿态下运行条件下,汽水分离器的疏水通过炉水循环泵,能够再次进入省煤器的锅炉给水管道,从而在省煤器→下降管→水冷壁→汽水分离器→储水罐→炉水循环泵→省煤器入口间,形成类似汽包炉的控制循环;此运行方式能够保证启动初期锅炉水动力安全,有效减少给水外排,减少热量损失,缩短机组启动时间。
受炉水循环泵供货进度的影响,锅炉点火吹管及整套启动期间,炉水循环泵无法到货。
考虑工期进度要求,我们准备采用无炉水泵启动方式。
通过查阅锅炉厂有关设计资料,前往广东粤电靖海发电厂、浙江玉环电厂进行调研,并且经过相关理论计算,我们认为本锅炉无炉水泵启动可行,其关键点即是如何保证锅炉水冷壁系统的水动力安全。
在实际的锅炉点火吹管和机组启动初期,我们将水煤比控制在合理范围内,约在13左右,保证给水系统最低流量始终在水冷壁水动力安全值之上。
通过对水冷壁系统各个壁温测点的检测,没有发现水冷壁受热面超温现象,且各个水冷壁受热面壁温均匀,无明显过高或过低壁温值,这充分说明锅炉水冷壁系统各个水冷壁管流量分配较均匀。
点火初期采用等离子方式启动前墙B制粉系统,汽温无明显偏差,说明带内螺纹的螺旋水冷壁+垂直水冷壁系统设计结构,能明显减小水冷壁出口汽温偏差,也是有利于无炉水泵启动的。
点火启动初期过程中无法转化为蒸汽的大量疏水外排,进入开式循环水系统或者在水质合格的情况下进入凝汽器回收。
虽然启动初期给水大量外排,使得锅炉点火至汽机冲车时间加长,机组启动初期的经济性有所下降,但是对于新建机组尽快改善炉水品质,保证机组按时投产发电,提早转入商业运行,还是有很大的实际意义。
4.2.2省煤器泄漏事故
机组启动后带满负荷试运期间,发生一次省煤器系统爆管泄露。
事故发生后,我们及时停炉处理缺陷,经过仔细排查,泄漏是由厂家焊口漏焊,造成高压给水外泄并吹损相邻管道,经过更换受损破裂管道,问题已解决。
4.2.3制粉系统问题
4.2.3.1磨煤机运行中要注意及时排放石子煤,同时要控制合适的一次风量,维持磨煤机入口和出口一定的风压;
4.2.3.2磨煤机试运中磨煤机入口气动快关风门及出口门经常发生反馈故障现象,除个别门是由于安装角度不合适,系统带粉后造成门板卡涩开关不到位,多数是开关反馈的限位开关位置不合适,通过重新调整限位开关位置,并在出入口门通入密封风,减少粉尘进入插板门,问题基本解决;
4.2.3.3个别制粉系统在启动初期,出现原煤斗膨煤堵煤现象,对机组运行造成一定扰动,通过在给煤机出入口落煤管加装振打装置,堵煤现象大大减少。
4.2.4有关风机的问题
4.2.4.1一次风机喘振问题
二期工程在设计初期,取消了设置在一次风机出口的联络风道,在风机启动和运行期间,只发生过一次喘振失速现象,较一期工程已经大大减少。
分析发生喘振原因,系点火初期一次风压自动设定母管压力定值偏高,而制粉系统运行和通风的磨煤机较少,一次风压自动抗扰性差造成。
通过优化一次风压自动参数设置,并尽量增加点火初期的通风量,问题解决。
4.2.4.2一次风机动叶执行器死区偏大问题
A、B两台一次风机在并列运行时,在两侧动叶开度一致情况下,风机出力不同,且在小开度下,动叶死区大,影响自动投入效果。
经过多次试验检查,确认一次风机液压缸存在制造问题,引起液压油流量不一致,造成一次风机出力不同。
通过厂家返厂更换液压缸后,问题解决。
4.2.4.3B引风机轴承温度偏大问题
试运期间发现,在相同风机出力下,B引风机所有轴承温度比A引风机对应点偏高8~10℃。
当环境温度接近在25℃时,个别轴承温度达到70℃报警值;当环境温度和排烟温度降低时,两台风机轴承温度随之明显降低,B引风机最低达到40℃。
分析现象可以看出,B引风机轴承温度受外界环境条件变化影响比A引风机大,并非轴承本身设备问题。
怀疑风机内部中心筒密封不严,导致过量热烟气漏入中心筒,加热轴承至温度偏高;停机后进入内部检查,找到漏点并加堵,问题得以解决。
4.2.5凝汽器内部滤网堵塞问题
在机组整套启动调试期间,发生过两次凝汽器内部滤网堵塞问题。
第一次发生在2008年12月22日,堵塞的滤网为凝泵入口管道凝汽器热井侧吸入口处滤网。
表现现象为凝结水泵出力异常。
机组停机后检查该滤网处堵塞物为保温棉。
该处滤网设计偏细,大概为25mm2的孔径。
现场决定更改滤网形式,更换为格栅式粗滤网。
原滤网堵塞情况见下图:
第二次滤网堵塞发生在2008年12月23日,堵塞的滤网为凝汽器A侧至B侧凝结水联通管滤网(厂家图纸未表明该处设有滤网)。
现象为凝汽器A侧真空值(-83.3KPa)与B侧相差较大(-92KPa),现场通过点温枪测量,发现凝汽器A侧水位过高(该侧未设计有水位磁翻板,变送器也只设计有1个且当时处于故障状态)。
停机后检查该处滤网结构和堵塞情况基本同于第一次热井吸入口处滤网状况。
处理方案为取消该处滤网。
综合分析两次滤网堵塞原因为现场工期紧张,部分管道保温工作与整套启动试运同步进行。
机组设计的真空破坏阀位于6m处对空,且未设有滤网。
在机组的几次真空破坏过程中,从真空破坏阀处吸入大量的保温棉絮是造成滤网堵塞的直接原因。
4.2.6凝结水泵出口压力偏高问题
在凝结水泵试运过程中发现凝结水泵出口压力高于厂家给定的设计值。
设计的凝泵关断压力为4.2MPa,但实际运行中在系统只走再循环调阀管线时流量为580t/h,凝泵出口压力为4.6MPa远高于此值。
为此特意通过超声破流量计现场重新测量凝泵出力曲线。
测量方法为控制凝泵再循环调门和调门旁路手动门开度。
数据如下:
凝泵出口压力(MPa)
测得凝泵流量
(t/h)
凝泵电流
(A)
4.1
997
218
4.2
947
214
4.3
861
211
4.4
767
205
4.6
570
199
5.0
129.4
184
这种情况造成凝泵出力与精处理承压等级有一定冲突。
精处理设计的正常运行压力为4.2MPa,压力高保护定值为4.5MPa。
目前在启机过程中,通过开启再循环调门旁路手动门缓解这一矛盾。
业主应考虑对此系统进行改造。
4.2.7高加正常疏水手动门盘根泄露问题
在整套试运过程中,#1高加正常疏水调门前手动门盘根出现过几次泄漏情况。
在第一次泄漏发生后,现场利用停机消缺机会更换过同型号的盘根,但在后续的大负荷运行中又发生同样的泄漏问题,综合分析怀疑此批量盘根不能满足#1高加正常运行需要。
应用其它型号质量可靠的盘根替换。
4.2.8汽轮机#1、#2轴瓦磨损问题
在2009年2月1日机组第二次冷态启动过程中,发生了#1瓦磨瓦事故。
对比第一次冷态启动,进行简要对比说明。
第一次冷态启动过程中各项参数均正常。
启动步骤根据制造厂说明书要求,启动前暖缸至160℃、暖阀至220℃。
冲车根据启动曲线,升速率100rpm/m至200rpm摩擦检查,转速降至100rpm以下后投入高压缸预暖方式升速至400rpm锁定高调开度,然后依据曲线暖机升速。
第二次启动操作完全同第一次。
启动前盘车电流14A,暖缸至171℃,暖阀至180℃。
于2009年2月1日22:
20挂闸升速,目标值200rpm,升速率100rpm/min。
在升速过程中发现#1瓦温度明显高于首次启动同转速状态。
定速200rpm后#1瓦温度持续上升,到80℃后下令远方打闸,打闸后#1瓦温度最高至145℃。
机组于22:
30转速惰走至0,盘车投入,盘车电流14A,偏心20um。
在出现磨瓦情况后,汇同业主、监理、安装、制造厂各方对事故进行分析。
结合2008年11月~2009年1月在某电厂发生的两台同型号机组先后出现的#1瓦多次磨损事故,制造厂认为事故原因为#1瓦、#2瓦的可倾瓦瓦块曲率半径设计偏小,高压缸预暖后机组在低转速下轴颈与下可倾瓦块完全贴死,造成进油困难轴瓦磨损。
制造厂的处理方案为#1瓦、#2瓦更换新瓦,新瓦的曲率半径比原瓦加大3mm。
在更换新瓦后机组与2009年2月10日重新启动定速,启动过程中各项参数正常。
但是,在轴瓦改造后机组目前只经历过一次启动,这次改造是否彻底解决了磨瓦问题还有待检验。
#2机组在今后的启停过程中,尤其是在低转速下要重点监视#1、#2瓦瓦温变化趋势。
4.2.9高压旁路减压阀问题
高压旁路减压阀在整套试运过程中表现的极不稳定,多次出现阀门摆动无法控制情况。
直接造成反馈连杆断裂,汽缸损坏等多起事故。
在CCI厂家指导下对高旁减压阀进行了改造,改造方案包括定位器加固,更换强度更高执行器连杆,在高旁减压阀芯增开导气孔和导流锥等,均未解决实际问题。
从2008年12月21日高旁第一次出现故障时的主汽压力14MPa,到改造完成后的2009年2月11日主汽压力3.79MPa时高旁阀即不可控。
高旁阀工作能力越来越恶化。
业主应联系厂家彻底解决高旁阀问题,建议考虑更换其他结构形式的阀组。
4.2.10机组运行过程中#1、#2瓦瓦温偏高问题
在机组的正常运行中,#1瓦、#2瓦温度一直偏高。
但是我们发现在高负荷下,#1、#2瓦温度对高调门开度变化非常敏感。
维持负荷不变的工况下,改变主蒸汽压力,调门开度随之改变,#1、#2瓦温度也随之变化。
尤其是在进行机组最大出力试验时,伴随着综合阀位的增加,负荷增长的同时#1、#2瓦瓦温出现明显下降。
具体参见下图
4.2.11高厂变故障问题
机组12月21日首次并网后,12月22日完成厂用电切换后,取主变、高厂变油样化验,发现高厂变C2H2含量超标,12月23日通过再次取样化验C2H2含量仍超标(7.52μL/L),确定高厂变内部有放电现象,退出运行,改启备变带2#机厂用电。
最终倒出高厂变油、滤油,12月31日机组停运后,进高厂变内部检查,确定因分接头结合不到位导致内部放电,处理完毕后,1月6日再次机组启动,取油样化验正常。
第二部分:
超临界机组
1大唐国际乌沙山电厂
1.1电厂及机组简介
浙江大唐乌沙山发电厂1~4号锅炉为哈尔滨锅炉厂有限公司引进三井巴布科克能源公司(MitsuiBabcock)技术生产的HG-1890/25.4-YM4型超临界参数变压运行、直流、单炉膛、一次中间再热、前后墙对冲旋流燃烧方式、平衡通风、固态排渣、全钢悬吊结构、Π型露天布置燃煤锅炉。
锅炉设计煤种为神府东胜煤,校核煤种山西大同塔山煤。
锅炉主要技术数据见下表。
编号
项目
单位
设计煤种
BMCR工况
TRL工况
1.
过热蒸汽流量
t/h
1890
1799
2.
过热蒸汽压力
MPa(g)
25.4
25.28
3.
过热蒸汽温度
℃
571
571
4.
再热蒸汽流量
t/h
1606
1525
5.
再热蒸汽进口压力
MPa(g)
4.64
4.39
6.
再热蒸汽出口压力
MPa(g)
4.45
4.21
7.
再热蒸汽进口温度
℃
319.7
313.8
8.
再热蒸汽出口温度
℃
569
569
9.
给水温度
℃
283.7
280.1
10.
空预器进口一/二次风温
℃
20/20
20/20
11.
空预器出口一/二次风温
℃
294.7/318.8
290.8/313.7
12.
锅炉排烟温度(修正后)
℃
120
117
13.
锅炉保证效率(LHV)
%
93.84
94.08
14.
空预器漏风率(1年后)
%
≤8
≤8
15
NOX(折