SMC片状模塑料的研究.docx
《SMC片状模塑料的研究.docx》由会员分享,可在线阅读,更多相关《SMC片状模塑料的研究.docx(14页珍藏版)》请在冰豆网上搜索。
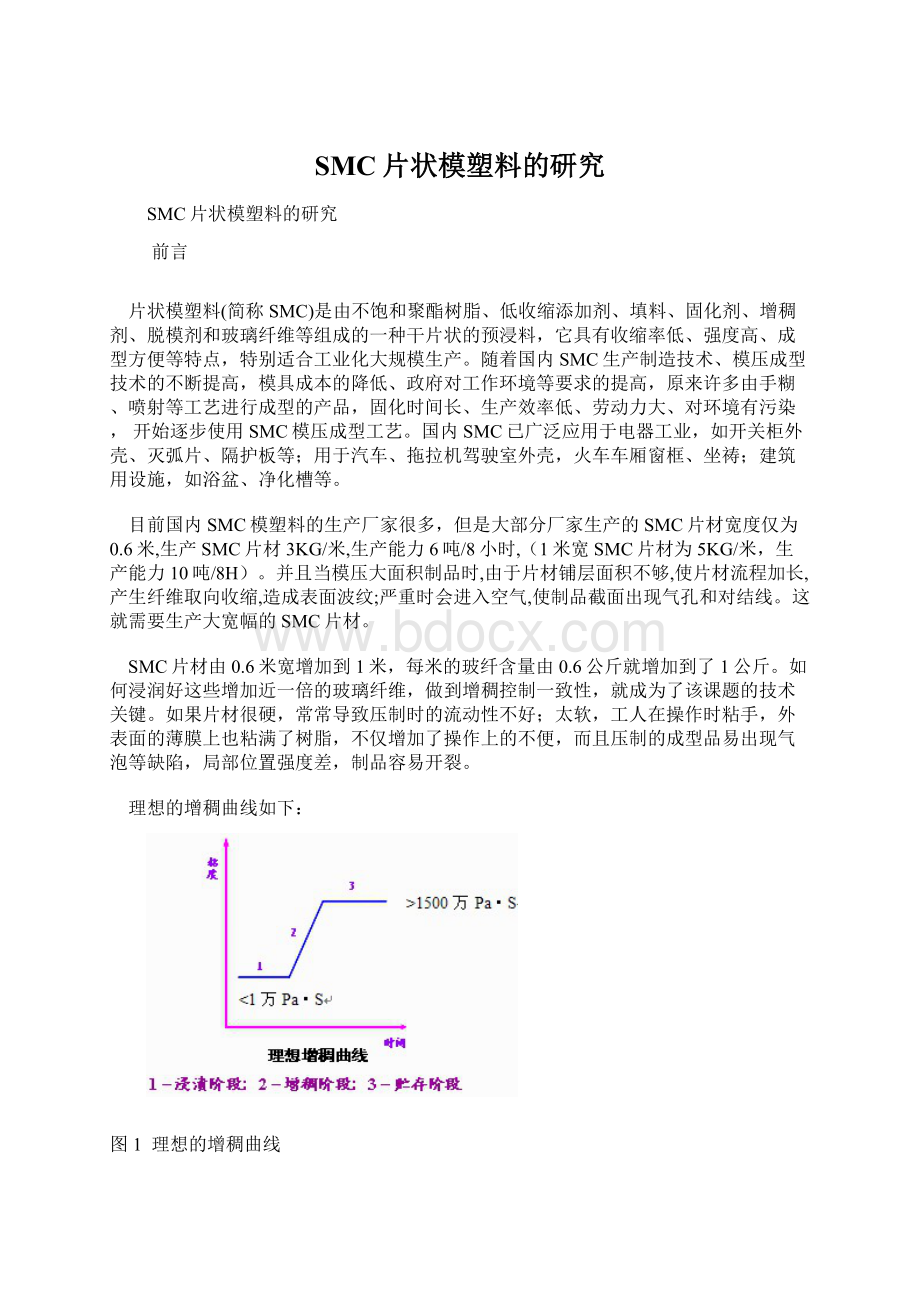
SMC片状模塑料的研究
SMC片状模塑料的研究
前言
片状模塑料(简称SMC)是由不饱和聚酯树脂、低收缩添加剂、填料、固化剂、增稠剂、脱模剂和玻璃纤维等组成的一种干片状的预浸料,它具有收缩率低、强度高、成型方便等特点,特别适合工业化大规模生产。
随着国内SMC生产制造技术、模压成型技术的不断提高,模具成本的降低、政府对工作环境等要求的提高,原来许多由手糊、喷射等工艺进行成型的产品,固化时间长、生产效率低、劳动力大、对环境有污染,开始逐步使用SMC模压成型工艺。
国内SMC已广泛应用于电器工业,如开关柜外壳、灭弧片、隔护板等;用于汽车、拖拉机驾驶室外壳,火车车厢窗框、坐祷;建筑用设施,如浴盆、净化槽等。
目前国内SMC模塑料的生产厂家很多,但是大部分厂家生产的SMC片材宽度仅为0.6米,生产SMC片材3KG/米,生产能力6吨/8小时,(1米宽SMC片材为5KG/米,生产能力10吨/8H)。
并且当模压大面积制品时,由于片材铺层面积不够,使片材流程加长,产生纤维取向收缩,造成表面波纹;严重时会进入空气,使制品截面出现气孔和对结线。
这就需要生产大宽幅的SMC片材。
SMC片材由0.6米宽增加到1米,每米的玻纤含量由0.6公斤就增加到了1公斤。
如何浸润好这些增加近一倍的玻璃纤维,做到增稠控制一致性,就成为了该课题的技术关键。
如果片材很硬,常常导致压制时的流动性不好;太软,工人在操作时粘手,外表面的薄膜上也粘满了树脂,不仅增加了操作上的不便,而且压制的成型品易出现气泡等缺陷,局部位置强度差,制品容易开裂。
理想的增稠曲线如下:
图1 理想的增稠曲线
1) 初期浸渍阶段,树脂增稠要足够缓慢,保证玻纤良好的浸渍。
一般要求半小时内粘度不超过6万厘泊。
2) 增稠阶段速度要足够快,能够尽快进入模压操作。
即树脂糊粘度大于1500万厘泊。
3) 模压料达到模压粘度时,粘度保持平稳,有较长的贮存寿命。
做好增稠粘度的控制,可以带来以下优点:
1) SMC片材表面不粘手,易于操作;
2) SMC成型时,玻璃纤维能够流向成型品的所有部分,保证成型品各部分物理、化学性能的稳定;
3) 使成型品具有好的外观。
当前,国家非常重视民用电器产品的防火安全问题所以,研究SMC配方及工艺,制定和控制增稠曲线,生产合格的1.0米宽阻燃SMC片材,是当前比较热门的课题。
2. 实验部分
2.1 主要原材料
SMC的组成比较复杂,使用的原材料多达十多种,每种原材料的种类、性能、质量及其相互配比对SMC的生产工艺,成型工艺及最终制品的性能、价格都有很大影响。
常用原材料见表1。
表1 SMC生产用原材料
2.2 主要实验设备
SMC生产机组、高速分散机、BROOKFEILD粘度计、电子万能力学实验机、冲击实验机、200T模压压机及样条模具、树脂生产用制氮机和空压机。
2.3 SMC生产工艺
1) 生产阻燃SMC配方
表2 SMC生产用原材料
2) SMC生产设备
SMC生产设备分二部分:
一是配制树脂糊设备,一般使用立式高速分散机;二是SMC复台机,工艺流程如下图所示。
图2 SMC生产工艺流程
图3 SMC成型过程示意图
2.4 料脂糊制备
1) 树脂、低收缩剂和引发剂,在低剪切力下混合搅拌均匀。
2) 脱模剂和填料混合到温度达到32-37℃时为止。
3) 加入增稠剂MgO混合一分钟后,将树脂糊送到SMC机组刮料槽内。
2.5 SMC复合
将制好的树脂糊加入上下两个树脂糊槽中,开动复合机,下薄膜放卷,经下树脂刮刀后,薄膜被均匀地涂敷上一定厚度的树脂糊。
当其经过纤维沉降区时,粗纱经切割后均匀地沉降其上。
短切无捻粗纱长度为25mm,玻纤含量23%。
承按了短玻璃纤维的薄膜,在复合辊处与以同样方式涂敷树脂糊的上薄膜复合,将玻纤夹在中间,形成夹层结构。
夹层在浸渍区受到一系列压辊的滚压作用,使树脂糊浸透纤维。
最后由收卷装置收集成卷。
2.6 SMC增稠
送往熟化间增稠,直至不粘手,可剪裁、称量及模塑为止。
通常采用加速增稠。
加速增稠一般可在带有鼓风设备的熟化室内进行。
加速增稠,温度为35~40℃,时间约10小时。
但最后还应以增稠曲线判定增稠的程度和结果。
2.7 样条模压
用60T压机,模温为155℃,保压压力为15Mpa,保压时间为120s的条件下压制:
φ100X3的圆形试片15块,用于颜色、外观、收缩率、电气强度的测试;120X(10±0.2)X(4±0.2)试片用于冲击强度和弯曲强度的测试。
样条冷却24H后,方可进行检测。
3. SMC技术指标
阻燃SMC技术指标如下:
表3 SMC生产用原材料
4. 实验与讨论
1) 前期增稠速度的控制:
初始粘度控制采用丙烯酸丁酯-丙烯酸共聚物作为润湿分散剂
增稠速度选用合适酸值的树脂控制
最终模压粘度选用以色列进口MgO控制
2) 采用做正交表L9(34),对SMC配方进行优化
3) 研究水含量对SMC增稠的不良影响
按基本配方,配制SMC树脂糊,根据具体要求进行相关测试。
1) 粘度采用BROOKFIELD粘度计测定
2) 水分含量用卡尔一费休尔法测定仪
4.1起始树脂糊粘度的控制
填料选用阻燃特性的Al(OH)3,在火焰下吸收热量释放结合水而产生自熄作用。
并能改善制品耐水性,电绝缘性和防止聚合物裂解。
但是,Al(OH)3比重大,吸油量多,加入到UP树脂中,如果不能被树脂很好的润湿分散,即会给体系带来如下问题:
1) 体系产生高粘度,直接影响玻纤的浸润
2) 无法润湿,出现干点
3) 几分钟后会絮凝甚至沉降分层
根据DLVO理论,填料相互接近絮凝,是因为填料分子相互吸引的范德华力。
如果能将一种带相同电荷和侧长链的分散剂分子吸附包裹在填料分子表面,就能使填料分子间产生静电排斥作用及空间位阻作用,抵消范德华力拉大分子间距离,有效起到解团聚作用。
为此,我们特别选择了丙烯酸丁酯-丙烯酸共聚物作为润湿分散剂。
聚丙烯酸已被证明在粉体表面吸附并产生较强的静电排斥,而丙烯酸丁酯的柔性非常好,其分子链在颗粒间产生空间位阻。
表4 不同润湿分散剂添加量对树脂糊初期粘度的影响
图4 不同润湿分散剂添加量对树脂糊初期粘度的影响
从上表可知,当填料全部选用有阻燃效果的Al(OH)3时,树脂糊的初始粘度比较高(26000厘泊),不利于玻璃纤维的浸渍。
通过加入偶联剂,可有效降低树脂糊粘度。
但当添加量超过0.15%时,效果不明显,说明碳酸钙粒子表面对分散剂吸附已趋于饱和。
4.2 不饱和聚酯树脂酸值对增稠过程的影响
不饱和聚酯树脂是关键,最根本的因素包括酸值、水分等。
其中水分的影响我们将在下面进行讨论,这里我们选择酸值不同的几种不饱和聚酯树脂进行比较。
表5不同酸值的不饱和聚酯树脂(同一类型)对增稠的影响
图5不同酸值的不饱和聚酯树脂(同一类型)对增稠的影响
从增稠速度上来看,基本上是按酸值越大,增稠越快,即PS-520>P701>P801的顺序进行的。
为了保证初期玻璃纤维的充分浸渍(初期粘度8800),以及熟化后最终能达到模压的粘度(终点粘度164e5),选用酸值适中的P801为SMC专用树脂。
4.3 终点模压粘度的控制
以往的SMC增稠选用氢氧化物增稠,增稠时间需要1星期。
根据增稠机理,我们选用高活性以色列进口MgO,增稠只需10H,大大缩短熟化时间,同时用量也比前者少。
增稠机理:
两个阶段 先成盐反应,然后配位络合反应
第一阶段 金属氧化物与聚酯端基-COOH进行酸碱反应,生成碱式盐。
第二阶段 碱式盐与聚酯分子中的酯基(氧原子)以配位键形成络合物
表6不同氧化镁含量对增稠稳定的影响
表6不同氧化镁含量对增稠稳定的影响
0.5%的Ca(OH)2在10天左右粘度可以到达1500万厘泊,但后期仍处于粘度上升阶段,增稠不稳定,不利于此时进行模压。
选用MgO进行增稠,前期增稠速度快,后期因为反应完全粘度容易趋于稳定,并且当MgO用量为0.3%时,可以做到熟化10H粘度达到1500万,实现1天内生产,1天内成型。
不过,MgO用量的稍微变化,对粘度的影响很大。
当用量为0.2%时,片材熟化达不到模压要求。
当用量为0.4%时,树脂糊增稠太快,不利于玻璃纤维的浸渍,甚至最终太硬不能模压。
因此生产时因严格控制称量MgO,这点比Ca(OH)2麻烦。
4.4 SMC配方的优化
以SMC模压样条的收缩率(间接表示光泽度)和冲击强度为参考值优化配方,做正交表L9(34),如下:
表7 不同用量MgO对增稠影响
以上数据均为质量百分比,玻璃纤维含量为23%
由正交表可以看到,
●以收缩率(光泽度)为参考值优化配方为:
表8 以收缩率为参考的配方
由表可知,影响SMC收缩率的最主要因素是LSA。
图7 LSA对收缩率的影响
随着LSA值的增大,SMC收缩率总和的值也随之减少,且趋势明显。
这是由于片状模塑料在模压温度升高后热塑性LSA在UP树脂中热膨胀,部分弥补了由于树脂固化收缩的原因。
另外,模压温度越高,LSA膨胀越大,也对收缩率有影响。
● 以冲击强度为参考值优化配方为:
表9 以冲击强度为参考的配方
图8 模压温度对冲击强度的影响
140-150℃阶段,冲击强度模压温度的升高而增大。
说明固化约完全,强度越大。
但从150-160℃,冲击强度开始下降,可能是因为过多热量集中在制品内部,冷却后UP与LSA界面间形成空的微孔,造成收缩内应力的缘故。
●综合两组配方,得到优化配方
表10优化后配方
根据以上配方,在155℃模压温度,保温时间3min,压力15 MPa下压制样条,测得其收缩率0.14%,冲击强度为100MPa.
4.5水分对增稠的影响
按配方配制树脂混合物,通过卡尔-费休水含量测定仪、添加适量的水来调整混合物的水分含量。
表11优化后配方
图9水含量对初期增稠影响
图10水含量对增稠后期的影响
当水分含量增加到0.2%,初期增稠的速度快,不利于玻璃纤维的浸润;并且最终增稠粘度却下降,导致模压时树脂混合物与玻璃纤维的离析而影响产品的最终质量。
所以,含水量要控制在0.15%以内。
5 结论
(1)生产SMC片材,对树脂糊的粘度控制很重要。
(2)采用正交实验法对配方进行优化,制得合格的阻燃SMC片材。
(3)模压温度建议在155℃,制品的表面光泽度和冲击强度最佳。
(4)含水量的控制必须在0.15%。