FI 7步法培训.docx
《FI 7步法培训.docx》由会员分享,可在线阅读,更多相关《FI 7步法培训.docx(27页珍藏版)》请在冰豆网上搜索。
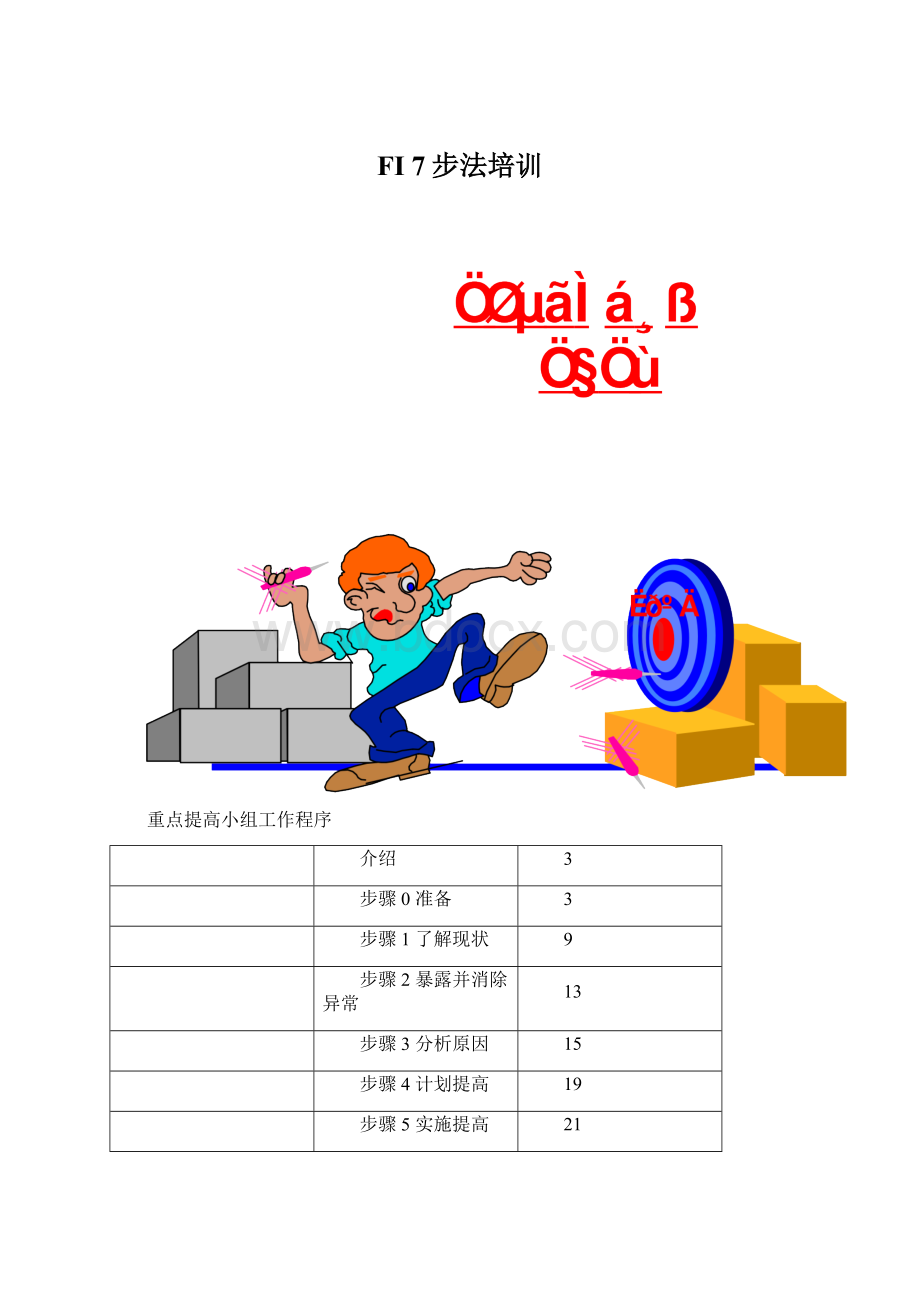
FI7步法培训
重点提高小组工作程序
介绍
3
步骤0准备
3
步骤1了解现状
9
步骤2暴露并消除异常
13
步骤3分析原因
15
步骤4计划提高
19
步骤5实施提高
21
步骤6检查结果
22
步骤7巩固成果
23
重点提高支柱项目
小组工作程序
F.I.项目小组工作程序是一个循序渐进的程序,随着小组项目进行,我们可逐渐看到公司的进步.以下将主要讨论成功执行F.I.工作程序的步骤0到步骤7的主要指导方针并描述每一步法主要的反馈,具体的行动和期望的目标。
一旦选择损耗消除或者问题主题,且.F.I.负责人同意它的优先权,区域经理或工厂领导Ð小组和一个F.I.小组会被授权消除损耗或解决此问题。
小组授权于一任命的组长,他对小组的发展和成功均负责任。
他通过F.I.工作程序7步法领导小组,并保证符合每一步的标准.本节中包括了小组的流程图,可在图中迅速浏览其中事宜。
这张图是以P&G的RayPayne创建的KUAE模式为基础。
小组的授权需要4个关键步骤,他们是:
小组发展
小组必须知道,理解和接受提出的计划。
区域经理对此问题的描述,一份规定完成内容的书面文件,与问题有关的数据和信息,都能小组对问题的理解起到很大帮助。
小组对这些知识的理解是非常必要的,它能够保证每一个员工能聚在一起,达成共识。
这个过程被叫做小组发展。
小组建设
小组中的每个人应根据其技能来担负不同的职责以能够通过更有效的方式来解决问题。
但这并不意味着小组会自动共同合作。
小组建设的目的在于为小组建立共同原则和确定共同的行为。
当然,如果所有组员都来自同一个组织,这或许会很简单。
然而,小组如何能协调地的工作却总是一个很重要的课题。
接受任务
一旦小组知道并弄清楚问题,他们必须证实地接受任务并对此作出相应的对策.另外,他们必须接受任务中给的指引方向或也可与任务组再确认.这种达到清晰明确和同意接受按要求去做的过程叫做接受任务。
初步计划
知道,理解并接受计划以后,就是执行计划.执行计划应慎重考虑。
小组能力的回顾和处理的问题为基础。
它应包括回顾每个人担当的责任以及小组如何共同运作。
一份更详细的任务过程将在IWS管理才能指导丛书或全球项目管理使用手册中涉及-CBA的5个图表。
F.I.小组登记主题并制定了一份用3-6月来完成所有步骤的项目日程.如果项目拖延太久,紫萑肜Ь城也钊耸慕峁.其次,小组准备了活动告示牌来跟进他们的进度,并向组织的其他成员展示他们的成绩。
步骤0的产品
1.同意授权
2.登记主题
3.初步活动板
工具和方法
子步骤
0.1
0.2
0.3
授权并开始
Ñ
Ñ
P&G小组效率榜样
Ñ
主题登记表
Ñ
Ñ
项目日程
Ñ
F.I.活动告示牌
Ñ
资源和登记CBA
Ñ
Ñ
授权示例
F.I.支柱小组的授权
目的:
消除23线的水平问题
成功衡量:
1.水平问题不再是23线的问题。
2.正在进行的活动将保证这已在23线获得成功。
3.向F.I.支柱小组提出再应用的建议。
4.在5天内完成这些!
产品:
1.应用于23线的解决方法;
2.再应用建议。
方法:
1.F.I.程序的7步法
关键岗位:
1.小组负责人:
RickyMathews
2.客户:
23线和分步
3.组员:
4.协助人:
PedroEscudero
区域经理日期F.I.支柱负责人
登记表示例
F.I.主题登记表
工厂:
部门:
F.I.小组
题目:
离心塞
批准日期:
3/15/95
主要影响:
PQCDSM
登记号:
015
需要的改进:
离心塞每班造成0.5小时的停机时间.除去离心塞是一件脏且具危险性的工作。
小组负责人:
HardyToreach
-部门经理
圈其中一个
组员:
DeeFect
-工程师
A级
ConnieTamination
-维护人
B级
TommyNogo
-供应商
C级
(基于定级程序)
计划时间:
两个月到步骤5
成果衡量
每天塞的数量
(期望不超过3个月)
初始价值
3.5/天
目标价值
0
里程碑
目标日期
Notes
步骤0:
准备
3/18/95
步骤1:
了解现状
3/20/95
步骤2:
暴露并消除异常
步骤3:
分析原因
步骤4:
计划提高
步骤5:
执行改进
5/20/95
步骤6:
检查结果
步骤7:
巩固结果
F.I.活动板示例
这步集中在清楚了解问题所在,哪些是真正的损耗,哪些是急需解决的问题.(过程,产品,等)在左表中已展示了总的流程主要活动是从所有来源包括现场勘察来收集数据核实真正的损耗.通常用术语“Gemba,Genbutsu”来描述现场的勘察.这是取自3GE能GEN的方法发展这种理解。
这种原则的关键是你决定要用的信息应是你已经在现场勘察证实的信息,你了解出现问题的设备的部分或零部件.另外,描述的问题遵循物理定律。
在发展小组的理解过程中,一个关键的工具是线或流程图表的发展.这些图表并不要很复杂,但它应该能描述线或流程的关键信息.另外,它也可用来解释说明生产系统的损耗和热点。
下面展示了一张简单的生产线图.如果你的问题集中于一个单元,那么,在小组了解情况时,一张一段时期内的图表会非常有用
不管用了何种工具,都需将现款分为几步来解决。
其他的TQ工具和技巧为理论上理解现况提供了工具。
Pareto揭示了瓶子标签上的各种问题.标签位置不正确,占标签问题中的44%.这44%的问题症状在第二张Pareto已标出.它表明瓶身前部标签位置不对是主要的原因.这又可分支成另一个Pareto.它表明瓶身前部的标签位置不对是主要的原因.这又可以分解成另一个Pareto。
这些问题可以从投入的精力和物力,物料损耗,总的影响或总成本来评估。
小组也能通过速度-标签问题的相关线来决定标签问题是否与速度有关。
小组能够明确问题导致的所有影响,并鉴定它是否带来部分或所有的问题,这是至关重要的.这将帮助小组决定全面完善的影响及优先性.在理解问题中,决定不同问题之间的相互联系或决定某一程序是否失去控制,这都是非常重要的。
这种理解很紧要。
小组必须将注意力集中在F.I.上.这就是步法1.3.的含义.小组在标签线上开始可能授权消除标签质量问题,他们可能发现多种多样的问题.他们也可以决定将左右偏移前部标签问题降低。
这也许会引起许多新的问题。
小组将回到他们的组织中并对初步的F.I.达成共识.接着,他们可能被告知去跟进新增的标签问题,这种举措是非常必要的。
小组必须明确他们对所做的项目灵活敏捷.他们必须制定重点问题的阐述并将目标设定高得几乎无法达µ(0缺陷)。
小组已经清楚他们项目的重点并已发展了他们的理解后,此时,他们非常有必要回顾在小组的技巧并重新评估他们解决手上问题的能力。
如果他们需要帮助,他们应作出相应的决定。
一旦设定目标,小组可以准备第二步了。
上述的示例显示且利用了以下的技巧:
Pareto分析,3Gen-2Gen,流程图表,现场勘察.小组也可用鱼刺法和5M分析法.所有的TQ工具应牢记在心.当小组在下一阶段发掘问题中,还会有更详细的分析.
步骤1的产品
1.生产线/流程表,或设备草图,时间表
2.问题相关分析
3.改善的目标
工具和方法
子步骤
1.1
1.2
1.3
程序流程
Ñ
瓶颈CBA
Ñ
3Gen和2Gen
Ñ
现场观察CBA
Ñ
鱼骨图
Ñ
5M分析
Ñ
Pareto分析
Ñ
以往的经验表明大部分损耗来自于缺陷或不能建立或维持基本现状。
(如加固、润滑和清洁)在应用F.I.工作程序更加复杂的分析技巧之前,应建立基本条件(相当于步法1-3的AM),来小心地消除所有的小缺陷和缺陷的影响.这将有助于为设备和程序建立一张最佳状况表,以及完善的方向和具体目标.通过这些举措,你可以理解到还有哪些存在的问题有助于集中于消除问题的必要所在.如果基本状况已经存在,那么步骤2能够快速达到或跳过去。
步法2中,有的放矢的重要性已得到阐释.越不关注问题,小组将会做越多的工作,因为他们将做一整套设备来代替做具体的零部件.你可以想象以下手头的工作量,如果小组在大设备上或大的方面需要做与步法1,2相当的AM来代替在一个零部件的工作量。
注:
步骤2非常关键.在这步中,F.I.项目的主要部分已经解决了他们着手纠正的问题。
这里讲述了设备或程序达到基本条件的重要性.它也强调授权F.I.小组之前作A.M.的重要性。
步骤2的产品
1.F.I.回到基本状况,消除缺陷及污染源
2.遵循标准会维护改善
3.重要方面的文件更新
理想条件下的流程图
技术信息
工具和方法
分步骤
2.1
2.2
2.3
2.4
程序流程
Ñ
Ñ
Ñ
机器周期图
Ñ
5M程序控制
Ñ
安全图
Ñ
AM问题表
Ñ
Ñ
QIDW-工作程序流程
Ñ
Why-Why分析
Ñ
清洁、检查和润滑标准
Ñ
如果你有足够的数据,那么最好在分析原因前进行评估.如果小组通过步法2已经采取了自己的方法,但问题仍然存在,收集其他的数据是非常必要的。
能够识别根本原因的清晰的分析方法是取得进步的关键.步法1中使用的工具能被再次应用,且与这步的中间一步联系.Why-Why分析
一个综合的鱼骨图,4M问题识别方法可以用来鉴别所有造成根本原因的问题.需要分析的问题在鱼刺法中被识别.Pareto分析能够用来决定哪些问题需先做Why-Why分析。
那我们还需做Why-Why分析。
本页中的WhyWhy格式综合了用信息检测的分析和处理根本原因的具体标准的定义.这加强了标准的使用并保证根本原因消除活动传递了日常管理方法。
大多数问题将使用Why-Why分析法。
可以通过Why-Why分析法来说明许多采取的行动.如果采取这些行动以后,原来的问题还为解决,或还为达到既定的目标,那么应采用更有力的工具
这些工具是
错误树分析(FTA)
这是一种详细推理分析技巧,也利用了Boolean逻辑来描述某一具体的失败事例.这种途径在以下方面有用:
1.为定量和定性可靠分析提供选择
2.推理性发展对系统失败的理解
3.指出与失败率有关的重要系统方面
4.提供洞察系统行为的分析
F.T.A与MECA不同,因为它只注重于识别那些导致失败或缺陷类型的系统因素或事肌
故障模式,效应及关键性分析(FMECA)
这是一种评估单个故障事件及它对系统影响的工具.许多失败的影响能够被考虑并优先化.唯一的注意事项是FMECA并没有多种多样的相互关联的故障.通常说,做一次FMECA需要以下步骤:
1.将欲分析的系统,具体单位或零部件根据功能分开.(用流程表,技术图纸等)
-将待分析的系统等按功能分开
-决定主要功能
-识别会影响每个作用的可能故障
2.列出各种已列出的故障模式的原因.(每种故障可能不止一种原因)
3.明确每种故障模式对操作的影响
步法1-3弥补了FMECA
4.制定关键指数(风险优先数)
-theRPN=紧急程度*可能系数*发现率
-每一项系数对应一种原因
因此,FMECA能被用来优化已识别的根本原因的顺序.它也能用来评估与促进计划相联的风险.这意味着小组不仅仅在推理上应用FMECA。
PM分析
现象分析是一判别所有可能因素的严格分析途径.与FMECA不同的是,优先化是特意列入日程的,从而保证所有的因素,不管其影响的程度,都能被识别,检查及纠正
PM分析应该用在已消除缺陷不断扩大的环境中.(完成步法1-3的AM)另外,它通常跟在Why-Why分析之后,来阐明需致力达到0缺陷的遗留问题.
PM分析的基本方法
1.严格遵循“Genbn敿皵Genbutsu數脑蚶疵枋鱿窒
2.用物理原理及定律来分析产生这种现象的机理
3.了解程序,设备和零部件的作用与结构
4.利用4M分析来调查现象.
5.先不定优先原则,不急于草率下结果,需集中消除通过推理得出的可能原因
工作点分析
这是设备及产品之间相互作用的分析。
它集中研究这些相互作用来判定是否出现这种缺陷现象。
一旦发现这种缺陷,就会细查原因。
这就是用来定义及检查原因的Genba,Genbutsu方法。
b这些工具的每一种都有自己的CBA或可提供的培训,这里将不再细加讨论.EachofthesetoolshavetheirownCBAortrainingavailableandwillnotbedealtwithinanymoredetailhere.
这些分析技巧是用于从大量复杂的,相互关联的现象中提高了解并确切找出故障和质量问题原因的工具.他们可能以需要某一高水平的工程技术来结束.然而,小组必须保证他们根据“三实斣---实际地点,实物,及实际现象,将问题发生地收集的信息进行分析。
在本步骤的最后部分,你将知道产生你欲解决问题的根本原因。
步骤3的产品
1.清楚定义的根本原因
-通过推理过程的清晰路径
-适当时候,一份细致的Why-Why分析或PM分析
工具及方法
分步骤
3.1
3.2
3.3
3.4
质量控制方法
Ñ
Ñ
Pareto分析
Ñ
KT问题分析
Ñ
Ñ
Ñ
Ñ
工作点分析
Ñ
错误树分析
Ñ
IE技巧
Ñ
PM分析
Ñ
在拟定及发展选项时,你应该考虑几种变化.在此阶段,不要下任何定论.为了最佳效果,应考虑技术人员及专家的适当参与。
每一种可能的选择都决定了所需的资源.评估寿命周期费用.最终对PQCDSM优化顺序。
注意这是如何渗入以下的行动事例中.在评估一节中,用评估寿命周期费用来决定成本影响.
改善过程中,密切注意可能会产生新的问题.例如,生产量加大,会引起次品.当计划改进时,需慎重考虑新原料的使用可能性.有时,你必须进行在线测试来评估改进(DOE,EO,PEO)的影响.在此步的最后部分,你将发送出完善计划,它应包括行动计划示例中所示的一切。
步骤4的产品
1.行动计划
工具和方法
具体分步骤
4.1
4.2
4.3
4.4
4.5
4.6
4.7
潜在问题分析
Ñ
Ñ
Ñ
决策分析
Ñ
Ñ
PQCDSM矩阵
Ñ
优先性矩阵
Ñ
Ñ
Ñ
寿命周期成本
Ñ
紧急故障标准
Ñ
测试计划
Ñ
试验产品CBA
Ñ
在开始推行改进之前,你应估计合适的工具,模具,零部件及原料是否可用。
从一开始,就应有技工的参与,向他们解释要做的变动,并估计是否培训在新条件下的操作或收集数据来跟踪改进.在对设备改良以前,如果所有参与的员工需要的话,一定要做安全培训.必须跟进CQV程序,确保在部门管理层或是初步管理支柱小组的参与下,能收集CQV标准的输入.在此步法最后,你必须肯定操作工理解这种改进或变动,他们已被培训过如何在新的条件下操作以及如何收集/跟踪新的操作条件。
步骤5的产品
1.对改进计划的行动
工具及方法
具体分步骤
5.1
5.2
5.3
5.4
5.5
执行计划
Ñ
Ñ
检查表
Ñ
Ñ
Ñ
安全培训
Ñ
培训计划
Ñ
Ñ
I.M.支柱的接受
Ñ
CQV
Ñ
当检查结果时,必须保证已取得对时间和改进目标的结果评估.分析并了解差距所在,以及它们产生的原因.在工厂内用活动牌展示这些信息,能够帮助以后小组成员学习你的推理方法.
如果结果不如预期那样,你应该回到步法3再重新考虑,或再细致些或使用更有力的分析工具做进一步的分析.
步骤6的产品
1.结果评估
2.可成立的决定
工具和方法
具体分步骤
6.1
6.2
结果一览表
Ñ
基准点(提高和基准点)
Ñ
计划跟踪
Ñ
Ñ
差距分析
Ñ
Ñ
如果改进不用定时的操作和维护标准来巩固住,那么它就会轻易失去使用的价值。
提高工作方法后,需要将之标准化,以防员工又不小心回到以前的旧习惯中,这一点是非常重要的。
通过编写培训资料(一点教材及检查表)来教授及培训员工这些标准,从而可以预防问题重复发生。
核实一种提高之后,应作出一份再应用的建议,并与区域业务经理及F.I.支柱小组分享。
²
步骤7的产品
1.标准、程序等使生产线维持改进
2.培训一线生产员工
3.再应用建议
工具及方法
具体分步骤
7.1
7.2
7.3
7.4
7.5
7.6
流程图
Ñ
Ñ
再应用矩阵
Ñ
过渡计划
Ñ
再应用建议
Ñ
一点教材
Ñ
Ñ
支柱回顾表
Ñ
F.I.小组工作程序
步骤0:
准备工作
1.授权有指定负责人的小组
2.F.I.小组登记主题并制定项目日程安排
3.F.I.小组利用工作簿或活动板来跟进工作进展
步骤1:
了解现状
1.从所有来源包括现场观察收集数据来确认真正的损耗
2.将现状设定到可操作的水平
3.制定某一具体问题的陈述和实际目标
步骤2:
暴露并消除异常
1.所有的缺陷均被发现
2.污染源已从根本上得到解决
3.正在维护的设备已有清洁,检查和润滑的标准
4.制定理想条件下的流程表
步骤3:
分析原因
1.用各种工具分析数据
2.分析理想条件和当前条件
3.找出根本原因
4.确认根本原因
步骤4:
计划提高
1.为改善提高提供多种选择
2.用PQCDSM矩阵来确定解决措施的优先性
3.选择一种建议
4.评估寿命周期成本
5.确定资源和责任
6.进行在线测试,并评估提高
7.制定改进计划
步骤5:
Ö实施提高
1.核实改进执行的目标和程序
2.检查物料,工具及应急情况
3.进行安全培训
4.执行改进工作
5.进行提高方面的培训
步骤6:
检查结果
1.评估实际结果与目标
2.决定继续或返回到步骤3
步骤7:
巩固成果
1.更新文件程序
2.制定标准化的检查表
3.编写结果总结
4.编写培训资料
5.变更和文件管理的培训
6.与F.I.支柱小组进行最后的回顾