CSR油船规范关于船舶极限强度研究.docx
《CSR油船规范关于船舶极限强度研究.docx》由会员分享,可在线阅读,更多相关《CSR油船规范关于船舶极限强度研究.docx(12页珍藏版)》请在冰豆网上搜索。
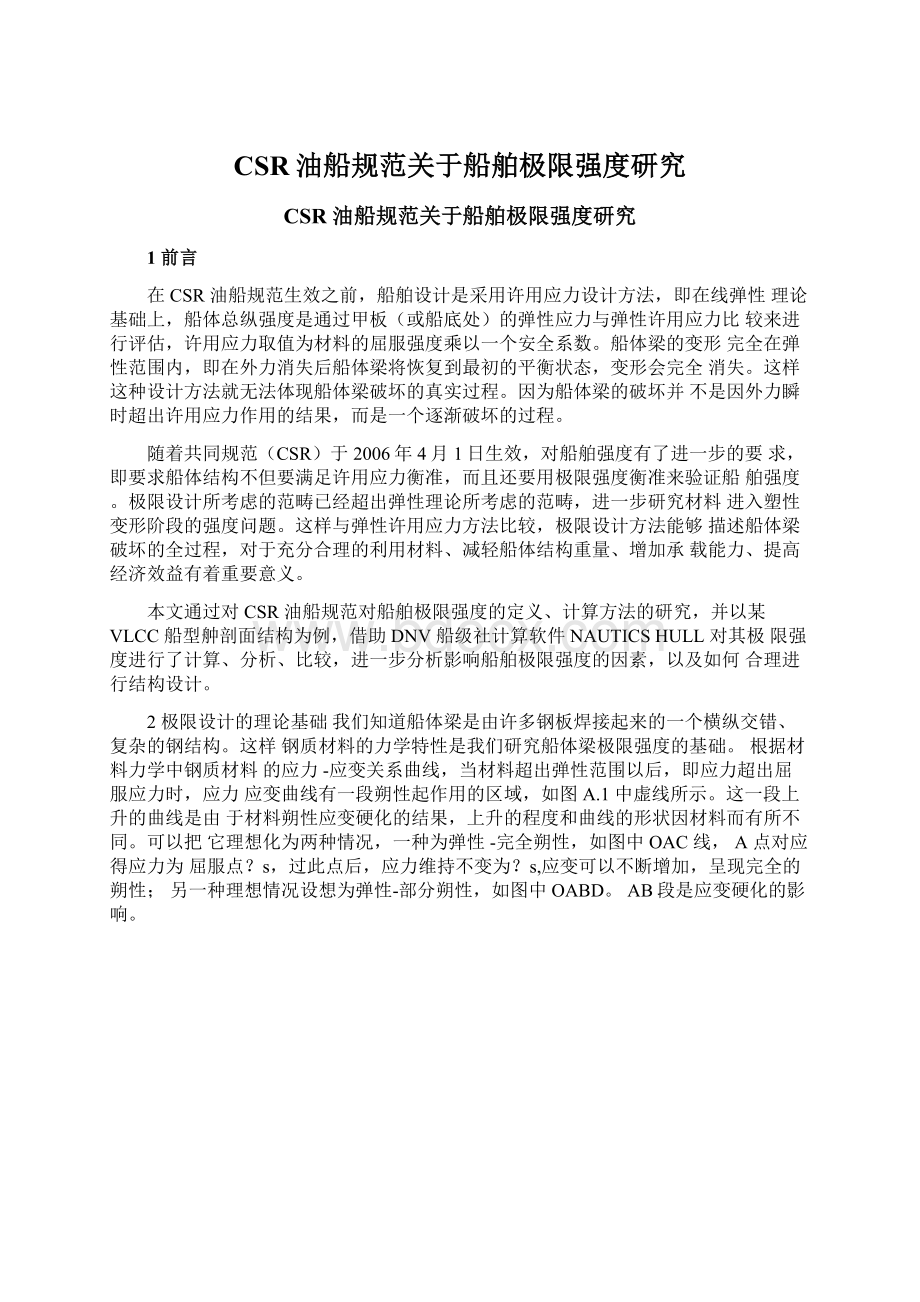
CSR油船规范关于船舶极限强度研究
CSR油船规范关于船舶极限强度研究
1前言
在CSR油船规范生效之前,船舶设计是采用许用应力设计方法,即在线弹性理论基础上,船体总纵强度是通过甲板(或船底处)的弹性应力与弹性许用应力比较来进行评估,许用应力取值为材料的屈服强度乘以一个安全系数。
船体梁的变形完全在弹性范围内,即在外力消失后船体梁将恢复到最初的平衡状态,变形会完全消失。
这样这种设计方法就无法体现船体梁破坏的真实过程。
因为船体梁的破坏并不是因外力瞬时超出许用应力作用的结果,而是一个逐渐破坏的过程。
随着共同规范(CSR)于2006年4月1日生效,对船舶强度有了进一步的要求,即要求船体结构不但要满足许用应力衡准,而且还要用极限强度衡准来验证船舶强度。
极限设计所考虑的范畴已经超出弹性理论所考虑的范畴,进一步研究材料进入塑性变形阶段的强度问题。
这样与弹性许用应力方法比较,极限设计方法能够描述船体梁破坏的全过程,对于充分合理的利用材料、减轻船体结构重量、增加承载能力、提高经济效益有着重要意义。
本文通过对CSR油船规范对船舶极限强度的定义、计算方法的研究,并以某VLCC船型舯剖面结构为例,借助DNV船级社计算软件NAUTICSHULL对其极限强度进行了计算、分析、比较,进一步分析影响船舶极限强度的因素,以及如何合理进行结构设计。
2极限设计的理论基础我们知道船体梁是由许多钢板焊接起来的一个横纵交错、复杂的钢结构。
这样钢质材料的力学特性是我们研究船体梁极限强度的基础。
根据材料力学中钢质材料的应力-应变关系曲线,当材料超出弹性范围以后,即应力超出屈服应力时,应力应变曲线有一段朔性起作用的区域,如图A.1中虚线所示。
这一段上升的曲线是由于材料朔性应变硬化的结果,上升的程度和曲线的形状因材料而有所不同。
可以把它理想化为两种情况,一种为弹性-完全朔性,如图中OAC线,A点对应得应力为屈服点?
s,过此点后,应力维持不变为?
s,应变可以不断增加,呈现完全的朔性;另一种理想情况设想为弹性-部分朔性,如图中OABD。
AB段是应变硬化的影响。
图A.1
由上图可以看出,当材料在外载荷作用下达到屈服强度时,材料并未立刻破坏。
而是进入了朔性变形阶段(这里只考虑弹性-完全朔性),即增大弯矩材料将保持屈服强度?
s大小不变而应变不断加大,直到材料本身均达到屈服强度为止。
由此可以看出朔性材料的朔性弯曲强度是大于其弹性弯曲强度的。
这一特性对于提高材料
的弯曲强度、减小构件尺寸、减轻材料的重量有着重要意义。
材料的应力一应变曲线对于研究船舶的极限强度是至关重要的。
船体梁结构是由许多这样的朔性材料组成的复杂的结构,亦具有如此的力学性能,据此来进行船体梁极限强度的研究,可以更进一步、更清楚地了解船舶在其寿命期内遭受不同载荷作用后,船体梁的真实的破坏过程。
3规范中船舶极限强度的定义
在CSR规范中,极限强度即船体梁极限弯矩Mu,定义为船体梁的最大弯曲能力,超过此弯矩船体梁将发生崩溃。
船体梁的失效表现为纵向构件的屈曲、极限强度和屈服。
根据CSR油船的船型的特点,距离垂向中和轴较远的上甲板位置刚度和强度都要低于双壳结构的底部,所以无论是在中拱还是中垂状态下,甲板结构的屈曲、屈服是研究极限强度的关键点。
而材料的许用屈曲应力是小于等于屈服应力的,所以,船舶的极限强的应研究中垂状态下甲板结构的屈曲。
如图A.1.2所示。
当甲板
结构受压超出了其屈曲限度,其承载能力将降低。
为确定横框架之间的最弱失效模式,需考虑各个构件的所有失效模式,如:
板的屈曲、加强筋扭转屈曲、加强筋腹
板屈曲、加强筋侧向或总体屈曲以及它们的相互作用。
中垂状态下,船体梁剖面的船体梁极限能力定义为静态非线性弯矩-曲率曲线
M-K上的最大值,该曲线表示船体梁垂向弯曲时渐进破坏特性。
图A1.1弯矩一曲率曲线M—托
两个关键横框架剖面之间的曲率K,定义如下:
式中:
二一两相邻横剖面处的相对转角;
l—横框架间距,即纵骨跨距。
对中垂状态下的油船,仅考虑垂向弯矩,对切力、扭转载荷、水平弯矩侧向压力的影,均忽略不计。
图A+t2船舶在极端中垂下的框架之间的屈曲失效
4船体梁极限能力的计算方法
CSR规范中给出了两种计算船体梁极限强度方法,即一步法和多步法(亦称增量-叠代方法的简化方法)。
目前校核船舶极限强度基本上是利用这两种计算方法。
当然,在船舶结构设计中,应用极限强度概念对船体强度做出合理的评价不仅仅有此两种方法,可以利用其他有效的方法,如非线性有限元分析法、增量一叠代法。
如果采用其他的极限强度分析方法,应在开始前征得船级社同意。
应将其分析方法原理和计算的详细结果与船级社的计算流程及所得结果的比较编制文件,并提交船
级社审查和认可,这些方法的使用可能会要求需重新校准分项安全系数。
考虑到设计部门与船级社审图部门之间工作中的统一性,通常都采用船级社所推荐的计算方
法。
以下是对这两种方法的简单介绍:
A、一步法
该方法为在净厚度基础上计算中垂状态下船体梁极限弯曲能力的一种简化
方法,且基于船体梁弯曲刚度降低的甲板屈曲计算,其关键是确定甲板加筋板屈曲后有效面积,因为它决定了屈曲后甲板处的剖面模数大小。
如图A.2.1,船体
梁的极限弯矩Mu由下式求得:
Mu=Zred?
ydX103kN*m
式中:
Zred—甲板折减剖面模数(指甲板平均高度);
3
m
red
Z._1red
red-
zdmear?
_NA
Ired—船体梁折减惯性矩,m°。
计算时米用
对于所有的纵向有效构件,船体梁净厚度tnet50
甲板每个加筋板屈曲后的有效净面积代ff;
有效达到屈曲的部分;
Ahet50
yd
Aret50—甲板加筋板格的净面积;
二u—甲板加筋板格的屈曲强度,N/mm2。
对各加筋板分别计算。
使用高级屈曲方法及净厚度tnet50;
二yd—材料的最小屈服应力,用于确定船体梁剖面模数,N/mm2。
Zdk叩an—从基线处量至甲板平均高度的垂直距离,m,平均高度可按由基
线至甲板边线、及基线至甲板中心线的值来确定;
ZNA^ed—从基线处量至折减剖面中和轴的垂向距离m,折减剖面中和轴的
垂向距离的计算基于屈曲后甲板加筋板格的有效净面积;
yd
同时,在受拉的外底板处,极限弯矩Mu所给出的应力值应不超过屈服应力
故极限弯矩Mu应不大于:
Mu=ydIred103kN*m
ZNA_red
2
式中:
二yd—材料的最小屈服应力,用于确定船体梁剖面模数,N/mm;
Ired—船体梁折减惯性矩,mt
ZNA」ed—从基线处量至折减剖面中和轴的垂向距离,口;
图A.2.1船体梁一步法计算流程的弯矩一曲率曲线
该计算流程假定油船的极限中垂能力在甲板加筋板格达到极限能力时达到。
如果该假定对某结构形状无效,则应使用其他极限能力的计算方法计算其极限强度。
B、多步法
多步法是在净厚度基础上基于平断面、弹性-理想朔性、单元间无相互作用假设而建立船体结构逐步破坏的简化方法,其关键是确定各个结构单元在整个承载全过程的平均应力-平均应变关系曲线。
各个结构单元的应力一应变曲线由船级社规范相关的计算公式给出,这里不详细描述。
该方法定义船体梁的极限弯矩为弯矩曲率曲线M-k的极值,见图A.1.10以下是多步法的计算步骤:
步骤1将船体梁横剖面离散成结构单元,即纵向加筋板格(每个单元一根纵骨)、硬角
单元及横向加筋板格,见A.2.3
步骤2导出所有单元的应力-应变曲线(又称载荷-端缩曲线);
步骤3导出期望的最大要求曲率;
步骤4对各单元,计算其对于曲率的应变、对应的应力,及单元上的力;
步骤5通过检查剖面上的总轴向力来确定新中和轴的位置,调整中和轴的位置直到合
力为零;
步骤6将各单元力的贡献相加,得到相应的弯矩;
步骤7增加曲率,用当前中和轴位置作为下一步计算的初始位置并重复步骤4到6,直
至达到最大要求曲率,极限弯矩为M-k曲线的极值。
若曲线的极值没有出现,则增加曲率
至极值出现为止。
计算M-k曲线的流程图如下:
计算帰性剖而模数及中和Wiffz
■AM
初始化曲略*K尸由曲导出虽大婆求胎率升
根据气调赠中和轴的位究
~~~T~~-
对所冇结构单儿(序数“)
对中和轴位覽Z“计算曲率气引起的各单兀的应变「
对各单元计那相应应变£引起的应力竹
应丿j—应变
曲线0■-矽
增加曲率
i-i+l
JF—卩
乙葩・41
计算削面卜的总轴向力.F产2代&
将各瑕元的应力贡猷相加,得到曲率气卜的弯矩M
当中和轴的调整吐小十
0.0001m时跳出肺环
M-¥曲线的最大值即为丽看丽订
图A.2.2计算M-岸曲线的流程图
'nu-
时
图A2.3结构单元定買示例
締戦侧、内売朋伸板的咧CM忍览哗上水屮-拓的例子
5船体梁极限强度的计算衡准
根据规范要求,应对中垂状态下的船体梁极限弯曲能力予以评估和校核,以确保符合以下衡准。
此衡准适用于在极端海况下的完整的船舶结构,并不包括中拱、港内或破损情况。
对船中0.4L区域内的船体梁垂向极限弯曲能力应满足以下衡准:
式中:
Mwv^ag垂向中垂波浪弯矩,kNm;
Mu垂向极限弯曲能力,kNm;
S、W、R设计载荷组合的分项安全因子
根据静水弯矩的两种不同的取值,对应了两组不同的安全因子,这样该衡准应满足两种不同的设计载荷组合。
分项安全因子
设计工况组合
静水弯矩Msw的定义
S
V
W
R
a)
许用中垂静水弯矩Msw-perm-sea,Knm
1.0
1.2
1.1
b)
海上营运均匀满载时的最大中垂静水弯矩,Msw-full
1.0
1.3
1.1
表中:
S—中垂静水弯矩的分项安全因子;
W—涵盖环境和波浪载荷预报不确定性的中垂垂向波浪弯矩分项安全因子;
R—涵盖材料、几何及强度预报不确定性的中垂垂向船体梁弯曲能力的分项安全因子。
注:
最大中垂静水弯矩取自船舶均匀装载至最大吃水的离港工况和相应的到港工况及任何
航行途中工况。
对CSR油船而言,由于底部是双层底结构,距离水平中和轴较近,剖面模数要大于距离中和轴较远的甲板位置,故中拱状态下剖面极限弯矩值较中垂状态下的值大得多,这可以在下面的计算中得以验证,因此,油船只要求校核中垂状态下的极限强度,极限强度校核主要取决于中垂状态。
在初始设计阶段,中垂静水弯矩和波浪弯矩分别取CSR推荐值。
在此基础上分析中横剖面所需极限弯矩能力Mreq:
2
Msw』in」ea_mid一°.°5185CwvLB(C0.7)
(2)
2
Mwv_sag=-0.11CwvLB(Cb0-7)(3)
将⑵、(3)代入
(1)中得到
Mreq—0.05185CwvL2B(Cb0.7)0.11CwvL2B(Cb0.7)迪(4)
2
C
wv
300「L2
=10.75-()3,当150EL乞300时
100
Cwv=10.75,当300L<350时
2
Cwv=10.75-(上350)),当350L<500时150
对于油船而言,通常为肥大型船舶,方形系数Cb大多集中在0.76~0.83,其均
值在0.8左右。
公式(4)中CmCb、s、w均为常数,而对于VLCC船来说型宽
B基本上取值在0.5~0.6倍船长,这样公式中只有船长L是变量。
这样极限弯矩衡准值随着船长L的增加而变大。
所以,在设计初期合理的确定船型参数特别是船长能够有效的减小极限弯矩衡准,从而减轻因满足极限弯矩衡准而增加的结构重量。
6极限强度实例分析
根据CSR规范提供的计算极限强度的两种方法,依据DNVNAUTICS软件对
VLCC船进行极限强度分析。
计算船型的主要参数表1
垂线间长
/m
型宽
/m
型深
/m
结构吃水
/m
设计静水弯矩
设计波浪弯矩
中拱/kNm
中垂/kNm
中拱/kNm
中垂/kNm
316
60.0
29.7
21.5
6934969
6213550
9683972
10451643
极限强度分析结果如表2所示。
表2
极限弯矩分
析方法
分析
状态
剖面实际极限弯矩
M/KNm
最小要求极限弯
矩M/kNm
一步法
中垂
22618936
20631074
多步法
中拱
26667852
20411310
中垂
20737256
20631074
以上计算基于船体梁剖面模数满足许用应力衡准的前提下。
由上表可知,无论是一步法还是多步法,剖面的极限弯矩值均出现在中垂状态下,所以油船的极限强度对船体总纵强度要求主要体现在中垂状态。
应用两种不同的计算方法所得到的剖面极限弯矩值有所不同,在均满足极限强度衡准的前提下,多步法计算出来的剖面极限弯矩值偏小,比较保守,结构强度偏于安全;相比之下,一步法计算出来的剖面极限弯矩值较大,余量较大,还可以适当减小甲板构件尺寸,从而减轻结构重量,设计出来的结构比较经济。
由于船体梁的失效由纵向构件的的屈曲、极限强度和屈服强度控制,因而在中垂状态下,船体梁极限强度主要由甲板上加筋板的屈曲极限强度控制。
加筋板的屈曲极限强度破坏主要有以下几种形式:
梁柱屈曲、加强筋的扭转屈曲、翼板/折边型加强筋腹板局部屈曲、扁钢型普通加强筋的腹板局部屈曲、板材屈曲。
在设计开始阶段可能会出现船体梁剖面模数刚好满足许用应力衡准,但不满足极限强度衡准或
极限强度余度较大的情况,这时就需要对剖面结构进行优化。
(1)船体梁剖面模数满足许用应力衡准,但不满足极限强度衡准:
这样就需要增大甲板处的剖面模数,增大该处剖面模数的方式有很多,如增厚甲板、加大纵骨规格或两者的结和,以此来增大甲板处的剖面模数,达到满足极限强度的目的。
而增大剖面模数的最有效的方式是满足细长比要求的前提下,合理的加大纵向加强筋的规格,如增加加强筋腹板高度、增厚面板板厚等。
(2)船体梁剖面模数满足许用应力衡准,极限强度余度较大:
说明甲板纵骨的规格及甲板板厚取得不太合适,要适当减小纵骨规格,如减小腹板高度,增加腹板、面板板厚、加大面板宽度等。
当然,在为了满足极限强的同时,应注意尽量控制船体梁弹性剖面模数的增加,应以船体梁弹性剖面模数和极限强度均刚好满足相应衡准或略有余度为目标,以达
到减少因满足船体梁极限强度船体结构重量增加的目的。
由于受甲板剖面模数及侧向压力要求,甲板板厚取得都比较厚,因而加筋板发生板材屈曲的可能性较小,所以,甲板纵骨的屈曲破坏是所要考虑的重点,合理选用甲板纵骨的类型、规格增大加筋板格的屈曲强度起着重要作用。
表3所示为了满
足极限强度衡准,对甲板结构做的几种修改方式的比较,主要有比较了加厚甲板板厚、加大纵骨、增加纵骨间距、改变甲板纵骨形式等方式对剖面模数及船体梁横截面积的影响。
从表中数据可以看出,采用T型材或角钢是比较合理的,即满足剖面模数要求,又做到了结构重量最轻。
但考虑纵骨疲劳问题,T型材要优于角钢;而
采用扁钢则需要较大规格,纵向构件横截面积比较大,因而结构重量较重。
所以,甲板纵骨通常设计为T型材,而少用扁钢,可以有效减少因满足船体梁极限强度船体结构重量的增加。
表3
序号
修改方式
实际剖面模数
cm3
要求剖面模数
cm3
纵向构件截面积
cm2
1
加厚甲板
75.367
68.415
107613
2
加大纵骨(纵骨为T型材)
74.654
68.415
107467
3
加大纵骨间距,减少一根纵骨
75.363
68.415
107514
4
采用角钢
74.653
68.415
107431
5
采用扁铁
77.343
68.415
108235
6
增加一根纵骨,缩短纵骨间距
74.776
68.415
107523
表3中所对应的具体计算模型如下:
模型1:
主甲板板厚取19.5mm,甲板纵骨取T350X13+120X23。
模型2:
甲板板厚取18.5mm,甲板纵骨取T380X13+120X23。
模型3:
增加甲板纵骨间距,相应减少一根纵骨。
甲板板厚取20.0mm,甲板
纵骨取T380X13+120X23。
模型4:
甲板板厚取18.5mm,甲板纵骨采用角钢L400X13+120X23
模型5:
甲板板厚取18.5mm,甲板纵骨采用平铁FB360X25。
模型6:
增加一根纵骨,减小纵骨间距。
甲板纵骨采用T380X13+120X23。
7结束语
本文从极限强度的定义、计算方法等方面做了简要的分析,通过对极限强度计算公式的分析得到了船长与极限强度成正比关系,同时,借助DNV规范计算软件对改变甲板纵骨间距、纵骨类型而得到的数据进行比较,得知合理布置和确定甲板上的纵向构件,增加加筋板的屈曲极限强度,可以改善船体梁的极限弯矩,从而有效地降低因满足极限强度衡准而导致的船体剖面构件尺寸的增加,减少结构重量的增加。