板料折弯液压系统设计解析.docx
《板料折弯液压系统设计解析.docx》由会员分享,可在线阅读,更多相关《板料折弯液压系统设计解析.docx(23页珍藏版)》请在冰豆网上搜索。
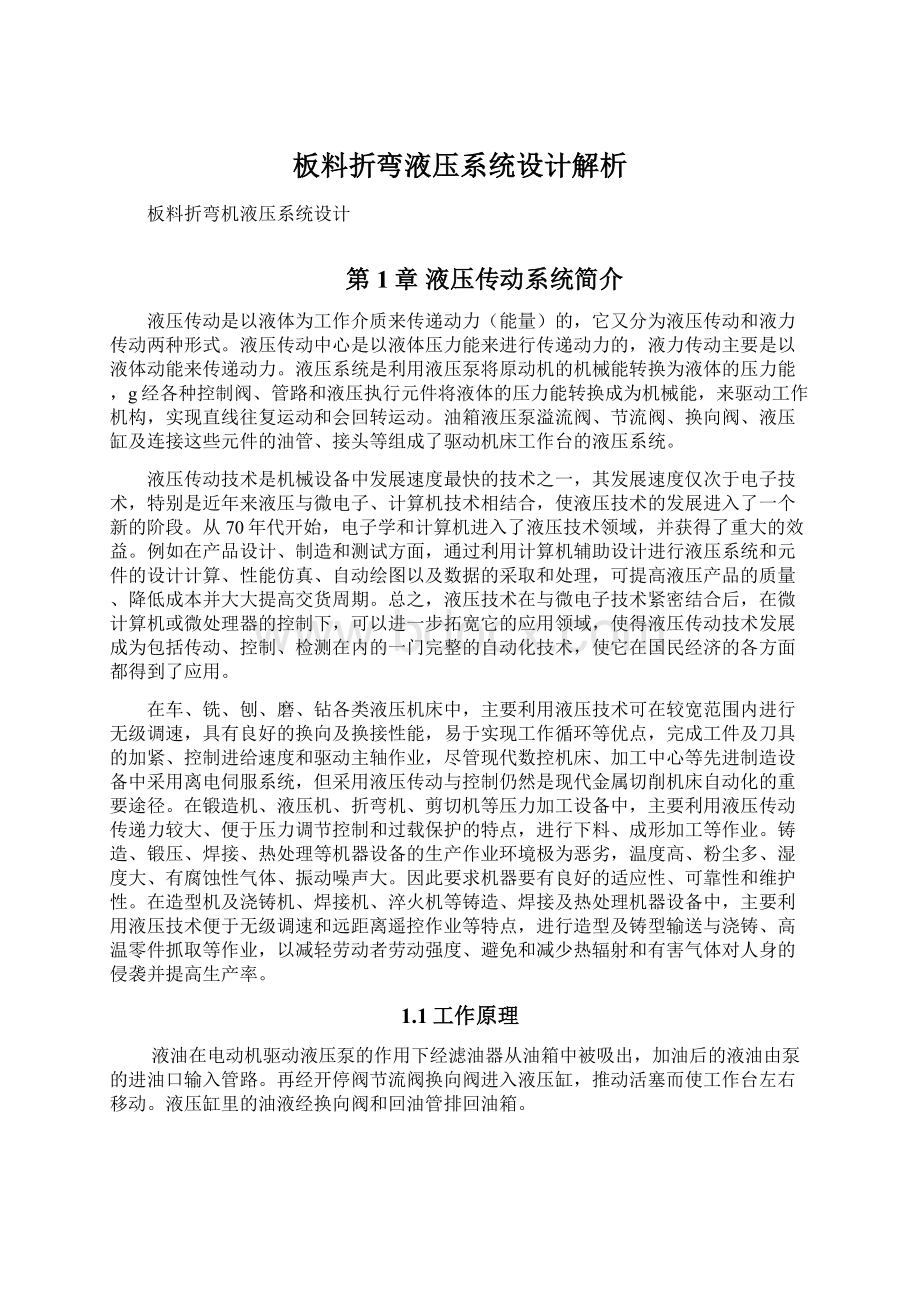
板料折弯液压系统设计解析
板料折弯机液压系统设计
第1章液压传动系统简介
液压传动是以液体为工作介质来传递动力(能量)的,它又分为液压传动和液力传动两种形式。
液压传动中心是以液体压力能来进行传递动力的,液力传动主要是以液体动能来传递动力。
液压系统是利用液压泵将原动机的机械能转换为液体的压力能,g经各种控制阀、管路和液压执行元件将液体的压力能转换成为机械能,来驱动工作机构,实现直线往复运动和会回转运动。
油箱液压泵溢流阀、节流阀、换向阀、液压缸及连接这些元件的油管、接头等组成了驱动机床工作台的液压系统。
液压传动技术是机械设备中发展速度最快的技术之一,其发展速度仅次于电子技术,特别是近年来液压与微电子、计算机技术相结合,使液压技术的发展进入了一个新的阶段。
从70年代开始,电子学和计算机进入了液压技术领域,并获得了重大的效益。
例如在产品设计、制造和测试方面,通过利用计算机辅助设计进行液压系统和元件的设计计算、性能仿真、自动绘图以及数据的采取和处理,可提高液压产品的质量、降低成本并大大提高交货周期。
总之,液压技术在与微电子技术紧密结合后,在微计算机或微处理器的控制下,可以进一步拓宽它的应用领域,使得液压传动技术发展成为包括传动、控制、检测在内的一门完整的自动化技术,使它在国民经济的各方面都得到了应用。
在车、铣、刨、磨、钻各类液压机床中,主要利用液压技术可在较宽范围内进行无级调速,具有良好的换向及换接性能,易于实现工作循环等优点,完成工件及刀具的加紧、控制进给速度和驱动主轴作业,尽管现代数控机床、加工中心等先进制造设备中采用离电伺服系统,但采用液压传动与控制仍然是现代金属切削机床自动化的重要途径。
在锻造机、液压机、折弯机、剪切机等压力加工设备中,主要利用液压传动传递力较大、便于压力调节控制和过载保护的特点,进行下料、成形加工等作业。
铸造、锻压、焊接、热处理等机器设备的生产作业环境极为恶劣,温度高、粉尘多、湿度大、有腐蚀性气体、振动噪声大。
因此要求机器要有良好的适应性、可靠性和维护性。
在造型机及浇铸机、焊接机、淬火机等铸造、焊接及热处理机器设备中,主要利用液压技术便于无级调速和远距离遥控作业等特点,进行造型及铸型输送与浇铸、高温零件抓取等作业,以减轻劳动者劳动强度、避免和减少热辐射和有害气体对人身的侵袭并提高生产率。
1.1工作原理
液油在电动机驱动液压泵的作用下经滤油器从油箱中被吸出,加油后的液油由泵的进油口输入管路。
再经开停阀节流阀换向阀进入液压缸,推动活塞而使工作台左右移动。
液压缸里的油液经换向阀和回油管排回油箱。
节流阀用来调节工作台的移动速度。
调大节流阀,进入液压缸的油量增多,工作台的移动速度就增大;调小节流阀,进入液压缸的油量就减少,工作台的移动速度减少。
故速度是由油量决定的,液压系统的原理图见图2。
1.2液压系统的基本组成
(1)动力元件:
液压缸——将原动机输入的机械能转换为压力能,向系统提供压力介质。
(2)执行元件:
液压缸——直线运动,输出力、位移;液压马达——回转运动,输出转矩
转速。
执行元件是将介质的压力能转换为机械能的能量输出装置。
(3)控制元件:
压力、方向、流量控制的元件。
用来控制液压系统所需的压力、流量、方向和工作性能,以保证执行元件实现各种不同的工作要求。
(4)辅助元件:
油箱、管路、压力表等。
它们对保证液压系统可靠和稳定工作具有非常重要的作用。
(5)工作介质:
液压油。
是传递能量的介质。
第2章板料折弯系统工况分析计算
2.1技术要求
本板料折弯机液压系统设计要求液压系统完成滑块的快速下降→慢速加压→快速回程的工作循环。
要求生产效率高,功率损耗小,发热少,工作平稳,安全可靠,防止速度失控现象。
技术参数如下:
最大折弯力为8.5×105N。
滑块重力为1.35×104N,快速下降速度2.05×10-2m/s,慢速加压速度1.08×10-2m/s,快速上升速度4.9×10-2m/s。
快速下降行程0.175m,慢速加压行程0.025m,快速上升行程0.2m。
启动、制动时间为0.18s,忽略导轨摩擦力。
2.2负载分析和运动分析
由于折弯机为立式布置,行程较小(仅0.2m),且往复速度不同,故选用缸筒固定的立置单杆活塞缸(取缸的机械效率ηcm=0.91),作为执行元件驱动滑块及折弯机构对板料进行折弯作业。
根据技术要求和已知参数对液压缸各工况外负载进行计算,其计算结果如下:
工况
计算公式
液压缸负载F/N
说明
快速下降
启动加速
156.7
折弯时压头上的工作负载可分为两个阶段:
初压阶段,负载力缓慢的线性增加,约达到最大折弯力的5%,其行程为20mm;终压阶段,负载力急剧增加到最大折弯力,上升规律近似于线性,行程为5mm。
等速
0
慢速折弯
初压
42500
终压
850000
快速回程
启动
13875
等速
F=G
13500
制动
13125
根据已知参数持续时间计算结果如下:
工况
计算公式
时间/s
说明
快速下降
t1=L1/v1
8.54
折弯时压头上的工作负载可分为两个阶段:
初压阶段,其行程为L2=20mm;终压阶段,行程为L’2=5mm。
慢速折弯
初压
t2=L2/v2
1.85
终压
t3=L’2/v2
0.46
快速回程
启动
t4=L3/v3
4.08
利用以上计算数据做液压缸负载循环图和速度循环图
2.3确定液压缸参数,编制工况图
根据类比法按主机类型选择元件的设计压力,查询相关资料,初选液压缸的工作压力p1=23MPa。
液压缸无杆腔为主工作腔,根据液压缸下行时滑块自重采用液压方式平衡,则计算液压缸无杆腔有效面积
活塞直径
按GB/T2348-1993,取标准值D=250mm。
根据快速下行与快速上升的速度比确定活塞杆直径d:
求的d=190mm,取标准值d=180mm
计算无杆腔有效面积
有杆腔有效面积
工作循环中液压缸压力流量计算如下:
工况
计算公式
液压缸负载F/N
工作腔压力p/Pa
输入流量q
cm3/s
L/min
快速下降
启动加速
;
156.7
3510
1005.8
60.35
等速
0
0
-
-
慢速折弯
初压
;
42500
0.952×106
530
31.8
终压
850000
19×106
530→0
31.8→0
快速回程
启动
;
13875
0.645×106
-
-
等速
13500
0.628×106
1157.8
69.5
制动
13125
0.61×106
-
-
工作循环中功率计算如下:
快速下降(启动)阶段:
P1=p1q1=3.53W
快速下降(恒速)阶段:
P1、=0
慢速加压(初压)阶段:
P2=p2q2=504.56W
慢速加压(终压)阶段,压力由0.952MPa增至19MPa,其变化规律
流量由530cm3/s减小至零,其变化规律为
从而得功率
计算得当t=0.218s时功率最大P3=Pmax=2648W,此时p=9.5MPa,q=278.8cm3/s=16.73L/min
快速回程阶段:
P4=p4q4=727W
根据以上分析和计算数据绘制液压缸工况图如下:
功率图
流量图
压力图
第3章拟定液压系统图
3.1确定液压传动系统的类型
液压传动系统的类型究竟采用开式还是采用闭式,主要取决于它的调速方式和散热要求。
一般的设计,凡具备较大空间可以存放油箱且不另设置散热装置的系统,要求尽可能简单的系统,或采用节流调速或容积---节流调速的系统,都宜采用开式。
在开式回路中,液压泵从油箱吸油,把压力油输送给执行元件,执行元件排出的油则直接流回油箱。
开式回路结构简单,油液能得到较好的冷却,但油箱的尺寸大,空气和赃物易进入回路;凡容许采用辅助泵进行补油并通过换油来达到冷却目的的系统,对工作稳定和效率有较高要求的系统,或采用容积调速的系统都宜采用闭式。
在闭式回路中,液压泵的排油管直接与执行元件的进油管相连,执行元件的回油管直接与液压泵的吸油管相连,两者形成封闭的环状回路。
闭式回路的特点是双向液压泵直接控制液压缸的换向,不需要换向阀及其控制回路,液压元件显著减少,液压系统简单,用油不多而且动作迅速,但闭式回路也有其缺点,就是回路的散热条件较差,并且所用的双向液压泵比较复杂而且系统要增设补、排油装置,成本较高,故应用还不普遍。
3.2液压回路的选择
液压机械的液压系统虽然越来越复杂,但是一个复杂的液压系统往往是由一些基本回路组成的。
液压基本回路就是由有关液压元件组成,能够完成某一特定功能的基本回路。
在本设计中选择五种回路,分别为调压回路、调速回路、平衡回路、换向回路和卸荷回路。
1)调压回路
调压回路的功用在于调定或限制液压源的最高工作压力,也就是说能够控制系统的工作压力,使它不超过某一预先调定好的数值,或使工作机构在运动过程中的各个阶段具有不同的工作压力。
调压控制回路包括连续调压回路、多级调压回路、恒压控制回路等。
液压源工作压力级的多少,压力在调节、控制或切换方式上的差异,是这种回路出现多种结构方案的原因,也是对它进行评比、选择时要考虑的因素。
该设计选择溢流阀单级调压回路,溢流阀开启压力可通过调压弹簧调定,如果调定溢流阀调压弹簧的顶压缩量,便可设定供油压力的最高值。
系统的实际工作压力有负载决定,当外负载压力小于溢流阀调定压力时,溢流阀处无溢流流量,此时溢流阀起安全阀作用。
图示2-1油路可靠,价格便宜。
图2-1调压回路
2)调速回路
调速阀调速回路由调速阀、溢流阀、液压泵和执行元件等组成。
它通过改变调速阀的通流面积来控制和调节进入或流出执行元件的流量,从而达到调速的目的。
这种调速回路具有结构简单、工作可靠、成本低、使用维护方便、调速范围大等优点。
用流量控制阀实现速度控制的回路有三种基本方式,节流调速回路分为进油节流调速回路、回油节流调速回路、旁路节流调速回路等。
本设计选用单向进油节流调速回路。
用溢流阀和串联在执行元件进油路上的调速阀调节流入执行元件的油液流量,从而控制执行元件的速度。
基本回路如图2-2所示:
图2-2调速回路
3)平衡回路
平衡回路的功用在于防止垂直或倾斜放置的液压缸和与之相连的工作部件因自重而自行下落。
下图是一种使用单向顺序阀的平衡平很平衡回路。
由图可见,当换向阀左位接入回路使活塞下行时,回油路上存在着一定的背压;只要将这个背压值调得使液压缸内的背压能支承得住活塞与之相连的工作部件,活塞就可以平稳的下落。
当换向阀处于中位时,活塞就停止运动,不在继续下移。
这种回路在活塞向下快速运动时功率损失较大,锁住时活塞和与之相连的工作部件会因单向顺序阀和换向阀的泄漏而缓慢下落;因此它只使用于工作部件重量不大、活塞锁住时定位要求不高的场合。
图2-3平衡回路
4)换向回路
往复直线运动换向回路的功用是使液压缸和与之相连的主机运动部件在其行程终端处迅速、平稳、准确地变换运动方向。
简单的换向回路只须采用标准的普通换向阀。
5)卸荷回路
卸荷回路的功用是在液压泵驱动电机不须频繁启闭的情况下,使液压泵在零压或很低压力下运转,以减少功率损失,降低系统发热,延长液压泵和电机的使用寿命。
图2-4卸荷回路
3.3拟定液压系统回路图
根据上述原则,考虑到折弯机工作时所需功率较大,故采用容积调速方式。
为满足速度的有级变化,采用压力补偿变量液压泵供油。
即在快速下隆时,液压泵以全流量供油,当转换成慢速加压折弯时,泵的流量减速小在最后5mm内,使泵流量减到零。
当液压缸反向回程时,泵的流量恢复到