压力容器制造工艺规程工艺文件.docx
《压力容器制造工艺规程工艺文件.docx》由会员分享,可在线阅读,更多相关《压力容器制造工艺规程工艺文件.docx(89页珍藏版)》请在冰豆网上搜索。
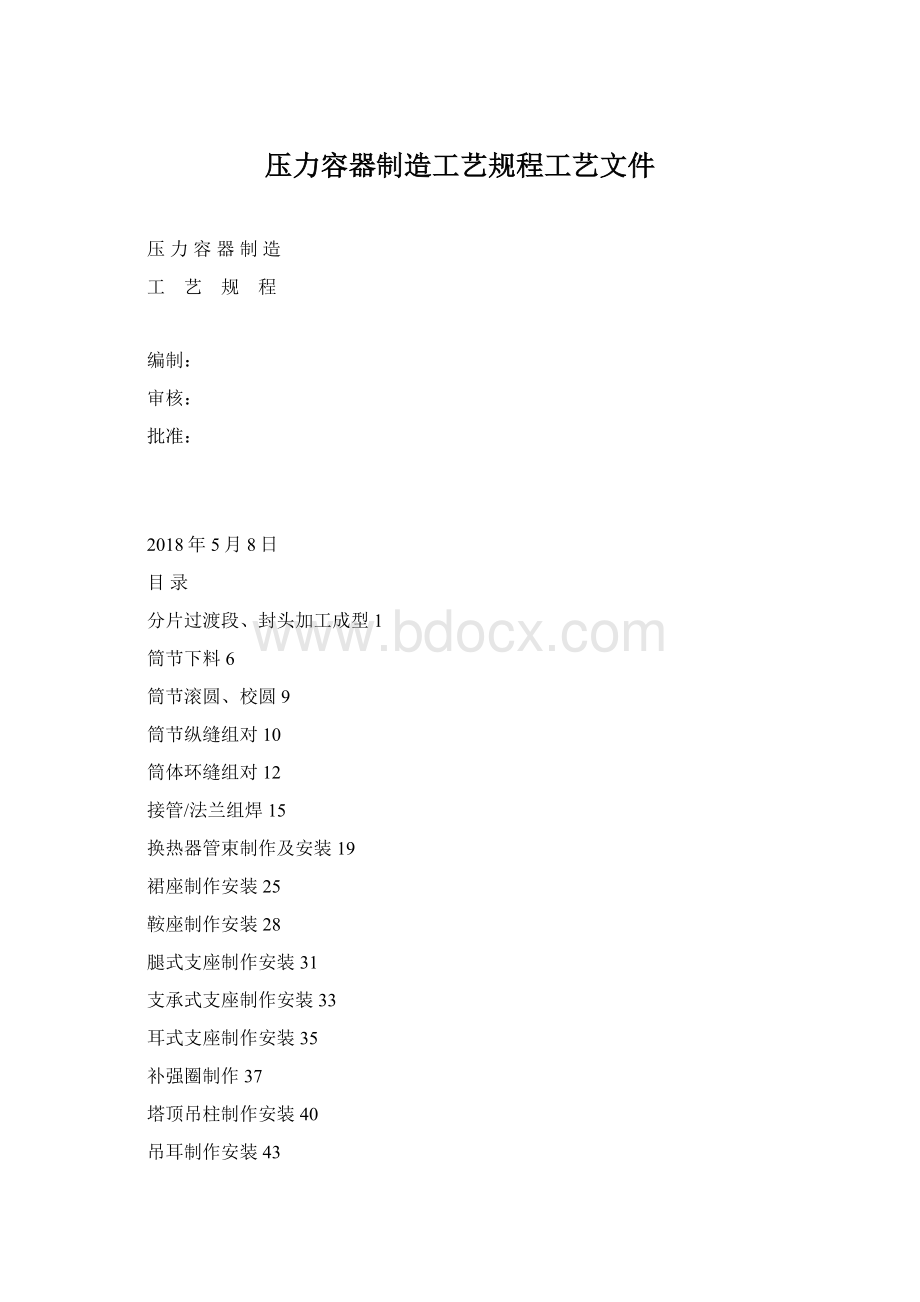
压力容器制造工艺规程工艺文件
压力容器制造
工 艺 规 程
编制:
审核:
批准:
2018年5月8日
目录
分片过渡段、封头加工成型1
筒节下料6
筒节滚圆、校圆9
筒节纵缝组对10
筒体环缝组对12
接管/法兰组焊15
换热器管束制作及安装19
裙座制作安装25
鞍座制作安装28
腿式支座制作安装31
支承式支座制作安装33
耳式支座制作安装35
补强圈制作37
塔顶吊柱制作安装40
吊耳制作安装43
塔盘固定件制作安装46
其它内、外件制作安装50
接管、补强圈安装53
空冷器管箱制作61
空冷器附件制作64
空冷器管束组装66
绕管换热器芯体制作69
绕管换热器组装75
水压试验81
气密性试验84
气压试验84
A法氨渗漏84
B法氨渗漏84
C法氨渗漏84
酸洗、钝化85
涂敷87
包装和运输90
零部件堆焊94
预后热及热处理99
分片过渡段、封头加工成型
工艺编号:
艺01
1、整体椭圆封头、分片椭圆封头执行GB/T25198-2010标准,旋压封头执行GB/T25198-2010标准,过渡段、锥形封头执行GB/T25198-2010标准,球形封头执行GB12337-2014《钢制球形储罐》标准,同时应符合GB/T150《钢制压力容器》、HG20584-2011《钢制化工容器制造技术要求》的有关规定。
2、椭圆封头、球形封头、锥段均至少自然加厚2mm,具体投料厚度与封头压制方确认,确保压制成形后的最小厚度不小于图纸技术要求给出的最小厚度或图样厚度。
3、封头切边后直边高度应符合图样规定,允差(-5%~10%)h,直边高度倾斜度:
h=25时,向外≤1.5mm,向内≤1.0mm;h=40时,向外≤2.5mm,向内≤1.5mm。
4、以外圆周长为基准的封头切边后,在直边部分端部用卷尺实测外圆周长,外圆周长公差应符合表1要求,外圆周长的设计值按π×Do或π(2δs+Di)计算,其中π取3.1416。
表1封头成型后外圆周长公差或内直径公差
单位:
mm
公称直径DN
钢材厚度δs
外圆周长公差
内直径公差
300≤DN<600
2≤δs<4
-4~+4
-1.5~+1.5
4≤δs<6
-6~+6
-2~+2
6≤δs<16
-9~+9
-3~+3
16≤δs≤22
-12~+12
-4~+4
600≤DN<1000
4≤δs<6
-6~+6
-2~+2
6≤δs<10
-9~+9
-3~+3
10≤δs<22
-9~+12
-3~+4
22≤δs≤40
-12~+18
-5~+6
1000≤DN<1600
6≤δs<10
-9~+9
-3~+3
10≤δs<22
-9~+12
-3~+4
22≤δs<40
-12~+18
-4~+6
40≤δs≤60
-15~+18
-5~+6
1600≤DN<3000
6≤δs<10
-9~+9
-3~+3
10≤δs<22
-9~+12
-3~+4
22≤δs≤60
-15~+18
-5~+6
3000≤DN<4000
10≤δs<22
-9~+12
-3~+4
22≤δs≤60
-15~+18
-5~+6
4000≤DN<5000
12≤δs<22
-9~+12
-3~+4
22≤δs≤60
-15~+18
-5~+6
5000≤DN≤6000
16≤δs≤60
-15~+18
-5~+6
5、以内径为对接基准的封头切边后,在直径部分实测等距分布的4个内直径,取其平均值。
内直径公差应符合表1规定。
6、封头切边后,在直边部分实测等距分布的4个内直径,以实测最大值与最小值之差作为封头的圆度,分头的圆度应不大于0.5%DN,且≤25mm,当δs/DN<0.005,且δs<12mm时,封头的圆度应不大于0.8%DN,且≤25mm。
7、封头切边后,在封头端面任意两直径上放置直尺或拉紧钢丝,在直尺或拉紧钢丝交叉处垂直的量封头总深度或封头总高度,其公差为(-0.2%~0.6%)DN。
8、整体封头用内样板检查封头内表面的形状偏差,最大间隙:
外凸不得大于1.25%Di,内凹不得大于0.625%Di。
9、椭圆封头瓜瓣(含整体供货带瓜瓣封头)、球形封头瓜瓣、折边过渡段瓜瓣(含整体供货带瓜瓣锥段)用全尺寸立体样板进行检查,其过渡区转角半径不得小于图样的规定值,形状偏差最大间隙≤3mm。
过渡段折边半径不得小于图样半径。
10、椭圆封头、球形封头瓜瓣弦长≥2000mm时,平面样板的弦长≮2000mm;瓜瓣弦长<2000mm时,平面样板的弦长≮瓜瓣弦长。
11、椭圆封头、球形封头瓜瓣几何尺寸允许偏差详见附图一。
12、椭圆封头、球形封头瓜瓣、锥段瓜瓣表面不得有裂纹、气泡、结疤、折叠、夹杂和分层。
13、分片封头、分片过渡段为净尺寸供货时,坡口由我方提供。
13.1分片过渡段分为正锥壳和偏心锥壳,为方便加工成型一般分成两半下料加工,成型后的过渡段需经预组装,预组装要求在刚性平台上进行,下口外基准圆直径确定时须考虑每道拼缝预留2~3mm收缩余量,预组装错边≤2mm,拼缝焊前棱角≤
mm。
13.2正锥壳放样方样方法如下:
(放样尺寸均以中径为准,同时放样尺寸应与封头加工单位确认)
13.2.1如下左图所示正圆锥大端直径为D、小端直径为d、高为H,圆锥顶角α=tg-1[(D-d)/2H]
L=D/(2*sinα)、l=L-H/cosα。
13.2.2正锥壳展开后其扇形中,△OAB为等腰三角形,OA=L、⌒AB=π*D/2,而在排板下料时需根据板料情况排料,上右图中θ=180°*D/L,则AB=2L*sin(θ/2).
13.2.3画AB的中垂线,使OA=L,则就找出圆心,再以O点为圆心L、l为半径画圆弧就可得到展开的两半正锥壳。
13.3偏心锥壳需用三角形展开法画出,偏心锥壳基本采用整体外委加工,验收时必需检查上下口平行度。
我公司偏心锥壳多用于釜式重沸器的制造,其采用的都是底平偏心,如下图:
三角形展开画法:
13.3.1在右边图的右(或左)半边两圆周上均分相同的等分,再在大圆周上每个点连接小圆周上相邻的两个点。
13.3.2画一直角三角形其高度为H,斜边为偏心锥壳的最长边。
13.3.3在直角三角形的底边上分别以垂足为圆心右图的连线为半径画上对应的点。
13.3.4在钢板上以H为长度确定一条直线的两点,再以此两点为基准,直角三角形上顶点到底边的各对应点的距离及各自圆周上的弦长(这些长度尺寸均可用CAD方便的标出)为半径确定在展开图上的各对应点,圆滑的连接这些点即可。
14、带瓜瓣封头和锥段在制造方整体组焊时,需控制错边≤2mm,拼缝棱角≤
mm。
制造方应有相应工艺评定支持的焊接工艺,并由持证焊工施焊。
15、分片封头、分片过渡段的坡口须采用数控或半自动切割,坡口表面平整光滑,不得有任何沟槽、缺肉,精确保证坡口角度、深度。
材质为复合板、Cr-Mo钢及高强钢的坡口表面须经100%渗透检测,按NB/T47013《承压设备无损检测》Ⅰ级合格。
整体成形的球形、椭圆形封头的坡口须根据直径大小考虑采用精加工,精加工时须采用合理的工装夹具,将封头圆度调整至合格,保证沿周向坡口角度、钝边的均匀一致性。
16、所有先拼板后成形的椭圆形、球形封头拼缝,须在成形后进行100%射线探伤,按NB/T47013《承压设备无损检测》Ⅱ级合格。
17、制造方须提供的资料有:
17.1整体采购的:
合格证,板材、焊材质保书及复验报告,无损检测报告,焊接工艺评定报告,焊接记录,加热曲线,正火曲线,几何尺寸检查报告,监检报告,测厚报告,有预热、后热或焊后热处理要求的还须提供相应的曲线及热处理报告。
17.2外协加工的:
合格证,加热曲线,正火曲线,几何尺寸检查报告,监检报告,测厚报告,有预热、后热或焊后热处理要求的还须提供相应的曲线及热处理报告。
17.3非受压封头可适当放宽要求。
18、封头一般采用热冲压的方法成形,采有冷成形的封头应进行热处理。
当制造单位确能保证冷成形封头的性能符合设计、使用要求时,则不受此限。
冷成形的奥氏体不锈钢封头可不进行热处理。
19、封头、锥段瓜瓣齐口时,要求每道纵缝预留1.5mm~2mm收缩余量。
19.1瓜瓣切割后坡口表面不得有沟槽和缺肉,均匀光滑,不得有氧化铁等杂物。
坡口钝边允差为±1mm,角度允差为±2.5°。
20、不锈钢板、复合钢板瓜瓣切割
20.1尽量使用数控等离子切割机。
20.2切割后坡口表面不得有沟槽和缺肉,均匀光滑,将淬硬层打磨干净。
坡口钝边允差为±1㎜,角度允差为±2.5º。
坡口直线度小于等于切割长度的1‰,且小于等于2㎜。
若坡口质量及直线度达不到上述要求,可预留加工余量2~3㎜,划出直线,用磨光机(用不锈钢专用砂轮片)打磨出合格坡口。
21、封头、过渡段下料时必需按艺02的要求进行相关标记的移植。
图一
特殊技术要求:
Cr-Mo钢及σs≥490Mpa的高强钢坡口表面须作MT或PT。
本工艺规程适用于封头、过渡段锥壳加工验收
筒节下料
工艺编号:
艺02
1、领料:
1.1材料须具有合格质保书,标记齐全。
1.2钢板表面不允许存在有裂纹、气泡、结疤、折叠和夹杂等缺陷。
钢板不得有分层。
如有上述表面缺陷,允许清理,清理深度从钢板实际尺寸算起,不得超过钢板厚度公差之半,并应保证钢板的最小厚度。
缺陷清理处应平滑无棱角。
其他缺陷允许存在。
但其深度从钢板实际尺寸算起,不得超过钢板厚度公差之半,并应保证缺陷处厚度不超过钢板允许最小厚度。
1.3图样及标准规定进行超探的材料应检验合格。
1.4三类容器用材料须复验合格,母材抽样复验须合格,否则不得领料。
1.5不锈钢及复合板复层表面下料前应有防污染措施。
2、号料
2.1按排板图号料,一般同材料,同焊接方法的筒体纵缝加工一组产品试板。
2.2划线、号料时须考虑卷制管马鞍口形状和接管焊接型式(内伸10mm或平齐),并预留3~8mm机加工余量,按理论最长点尺寸保证。
注意图纸中接管外伸高度、内伸高度的解释。
注意设计对标准人孔组合件的特殊备注,如锥段上人孔接管须加长。
2.3筒节板长、宽号料允差为±1mm,对角线允差≤1.5mm,刨削余量为2mm(若需)。
2.4号料后板面各项标记应齐全,如筒节编号、产品编号(见排板图)。
2.5如超出滚制能力,根据筒节直径和壁厚,板两端合理预留200-450的带头板,一般是直径越小壁厚越厚预留的带头板越长。
2.6卷制接管、虾米弯接管由技术人员在CAD上放样后,按等分法分成若干份,然后将基准线至双线弧线的尺寸标注出来后(见上图所示接管马鞍口)交班组放样。
3、标记移植
3.1按附图二、三标移统一内容,包括材质、质保书自编号。
不锈钢、Cr-Mo钢、高强钢、低温钢材料表面不得打制钢印。
3.2标移时如焊接工艺为内坡口,则需标移在画线一面的反面,此时必需在画线一面用记号笔写上相关标记。
4、下料
4.1不锈钢板下料采用数控等离子切割机放水切割或用剪板机剪切,复合钢板下料可用普通等离子或数控等离子切割。
4.2其余板材下料采用数控或小车式氧-乙炔切割,但当钢板较薄、余量不多切割后易产生变形时也采用数控等离子切割机放水切割。
4.3剪切、切割后相对于检查线偏差为±1mm。
4.4采用剪切下料后剪切面允许有深度≤1mm的磕痕和厚度≤0.5mm的毛刺。
5、坡口切割
5.1Q345R、Q245R、Q235等钢板可用氧-乙炔切割坡口。
5.2板切割后坡口表面不得有沟槽和缺肉,不得有氧化铁等杂物。
应均匀光滑,坡口钝边允差为±1mm,角度允差为±2.5°。
5.3筒节板长宽度允差为±2mm,对角线允差≤2.5mm。
5.4切割的坡口必须磨去氧化层、渗碳层、淬硬层,直至露出金属光泽。
6、刨边
6.1不锈钢板、复合钢板、Cr-Mo、低温钢板坡口均采用刨边机。
6.2需削薄处理的筒节钢板不得在钢板未圈圆的情况下采用刨边机削薄。
6.3板刨边后坡口表面不得有挤压或鱼鳞状痕迹,粗糙度不得低于
坡口钝边允差为±1mm,角度允差为±2.5°。
6.4筒节板长宽度允差为±2mm,对角线允差≤2.5mm。
6.5需进行坡口探伤的板料其坡口探伤前,须进行表面打磨,直至露出金属光泽。
图二
附图三
L、B尺寸具体见试板工艺
特殊技术要求:
1.Cr-Mo钢及σs≥490Mpa的高强钢坡口表面须作MT或PT。
复合钢板坡口加工时一般要求在复层与基层之间刨出一台阶以利于焊接。
2.换热器壳程筒体内直径允许偏差可通过外圆周长加以控制,其外圆周长允许上偏差为10mm,下偏差为零。
3.此工艺规程同时适用于筒体、裙座筒体、锥段、卷制接管。
筒节滚圆、校圆
工艺编号:
艺03
1、确认钢板经压头、卷圆后坡口在筒体的内外侧是否与焊接工艺一致。
2、压头时根据钢板材质、焊接变形量合理控制反变形量;若筒节焊接采用内部先焊外部清根后焊接压头,曲率要求稍大于筒节曲率,而采用外部单面焊双面成形焊接工艺时曲率可与筒节相同。
3、滚圆后用弦长≥Di/6且不小于300mm的内或外样板和直尺检查,检查筒节曲率,其与样板间隙≤2mm。
4、
锥段在卷圆时如用小三辊,需在机架上加上保护罩,在大三辊上必须分段卷制,此时在划线时就需划好各等分的射线。
小口径锥段使用千斤顶或采用锤击的方法分段压制,压制时可采用如下图所示的胎具:
成型时钢板(图中双点划线)是边前移边转动的,压制(或锤击)部位在放样时就以辐射状画出。
如超出滚制能力,根据预留压头板尺寸合理控制直边段,并使起弧段200mm范围内的曲率略大于筒节曲率。
滚圆前,上、下辊表面及钢板表面必须清理干净,复合钢板、不锈钢板滚圆前卷板机上辊表面需用丙酮擦洗,同一规格的筒节要求滚动、下压次数及油压相同,以保证其延伸量一致。
5、筒节纵缝焊完后根据棱角度和圆度情况确定是否校圆。
6、校圆前筒节上的试板、(熄)引弧板必须采用切割方法取下,不得用锤击方法取下,校圆时控制圆度:
对于普通容器、塔器其圆度≤筒体内径的1%,且≤25mm(卷制接管≤1%Di,且≤3mm),对于刚性不大的筒节只需对棱角度进行校正(棱角≤1/10δs+2mm,且≤5mm)。
对于换热器壳体,要求其圆度≤0.5%Di且当Di≤1200mm时圆度≤5mm、Di≥1200mm时圆度≤7mm。
特殊技术要求:
1.此工艺规程同时适用于筒体、裙座筒体、锥段、卷制接管。
筒节纵缝组对
工艺编号:
艺04
1、组对时,坡口间隙、错边量、棱角度等应符合规定。
具体尺寸允差见附表一。
2、组对时尽量使用F枪、手位葫芦等,少用工卡具,以避免机械损伤。
不锈钢、Cr-Mo钢、低温钢及σs≥490Mpa的高强钢所用工卡具拆除后,母材经补焊后打磨平滑用永久记号笔做好标记,以进行磁粉或着色检测。
3、工卡具、吊耳、引熄弧板等须统一设置,与筒体同材质,引(熄)弧板的长度要求不短于150mm其厚度要求为筒节厚度的2/3并保证外表面平齐以免造成焊缝两端与整条焊缝的不一致性。
4、组对时须严格控制错边、间隙,并保证错边、间隙的均匀一致性。
5、立位焊接的筒体及分片到货的锥段、椭圆封头、球形封头纵缝组对须在经找正水平的平台上(或拼接的钢板)上进行,以保证圆度及端面不平度。
锥段组对纵缝间隙允许有2mm的不一致性。
6、封头组对时,保证瓜瓣下口平齐,控制理论拱高,组对间隙均匀2~3mm。
7、严禁强力组对,点固焊缝间距和厚度要符合规定,严禁对材料表面进行烧烤。
8、焊接接头拘束度大时,推荐采用抗裂性能更好的焊条施焊。
9、点固焊缝不得有裂纹,否则应清除重焊。
如存在气孔、夹渣时亦应去除。
10、熔入永久焊缝内的定位焊缝两端应便于接弧,否则应予修整。
11、有预后热要求时,严格执行工艺。
纵缝点焊预后热采用氧—乙炔火焰加热,时间不得少于3min,保证温度,保证点焊焊缝长度≥150mm和厚度12mm~16mm,间距400mm~500mm,防止焊前开裂。
12、无法或回床困难的筒体纵缝组对时须预留反变形。
13、临时工卡具、吊耳的焊接须采用和筒体相同的焊接工艺及焊材。
附表一
壳体
项目
φ×δs
样板弦长
≥1/6Di,且不小于300mm
错边量
纵缝
δs<12mm,错边量≤1/4δs
12mm≤δs<50mm,错边量≤3mm
δs>50mm,错边量≤1/16δs,且≤10mm
环缝
δs<20mm,错边量≤1/4δs
20mm≤δs<40mm,错边量≤5mm
40mm≤δs<50mm,错边量≤1/8δs
δs>50mm,错边量≤1/8δs,且≤20mm
棱角(焊前/焊后)
焊前≤1/10δs,焊后≤2+1/10δs,且不大于5mm
端面不平度
≤1‰Di,且≤2mm
圆度
≤1%Di,且≤25mm(卷制管≤1%Di,且≤3mm)
相邻筒节周长偏差
≤6mm
特殊技术要求:
1.此工艺规程同时适用于筒体、封头、裙座筒体、锥段、卷制接管。
2.复合钢板纵缝组对错边量要求在1mm以内,焊接时基层全部焊接到位,过渡层与面层焊接时在两端各留出约50mm不焊,待环缝复层焊接时一并施焊。
筒体环缝组对
工艺编号:
艺05
1、引弧板、引出板、产品焊接试板不应锤击拆除。
2、组对时,纵缝布置方位按排板图给出的方位,坡口间隙、错边量、棱角度等应符合规定。
具体尺寸允差见附表二。
附表二
壳体
项目
φ×δs
样板弦长
≥1/6Di,且不小于300mm
错边量
纵缝
δs<12mm,错边量≤1/4δs
12mm≤δs<50mm,错边量≤3mm
δs>50mm,错边量≤1/16δs,且≤10mm
环缝
δs<20mm,错边量≤1/4δs
20mm≤δs<40mm,错边量≤5mm
40mm≤δs<50mm,错边量≤1/8δs
δs>50mm,错边量≤1/8δs,且≤20mm
棱角(焊前/焊后)
焊前≤1/10δs,焊后≤2+1/10δs,且不大于5mm
端面不平度
≤1‰Di,且≤2mm
圆度
≤1%Di,且≤25mm(卷制管≤1%Di,且≤3mm)
相邻筒节周长偏差
≤6mm
3、组对时尽量少用工卡具,确需点焊码铁等工卡具时,应尽量避免机械损伤。
不锈钢、Cr-Mo钢、低温钢及σs≥490Mpa的高强钢所用工卡具拆除后,母材经补焊后打磨平滑用永久记号笔做好标记,以进行磁粉或着色检测。
4、必需焊接工卡具、吊耳时须统一设置,与筒体同材质,不锈钢筒体组对用工卡具可用碳钢,但必需在筒体与工卡具间加薄不锈钢板,减少对母材的损伤。
5、组对前须找正筒节圆度,对刚性较差的筒节,尽量采用专用撑圆组对夹具,并测量端口周长,根据周长进行修复、调整。
组对时须严格控制错边、间隙,并保证错边、间隙的均匀一致性。
撑圆组对夹具安装时需保证夹具轴线相对筒节轴线的同心度,如下图所示:
安装时确保夹具宽度方向一半左右伸出筒节端口,且要使6个撑脚顶开高度基本一致。
6、筒节经找正后,以排板图上焊缝所在位置为基准画出0°、90°、180°、270°中的任一条基准线,再用盘尺按筒节的外圆周长等分四个点分别用样锪或记号笔做好标记。
7、对于内件较多的容器和塔器,组对封头端的筒节一端需将外部四条心线用角尺引入筒节内部并用样锪或记号笔做好标记。
8、塔体封筒环缝组对时,选用滚胎必需一致,滚胎上同一位置的轮子保持在同一水平面及同一直线上,若组对至某一部位发现刚性特别大时不可强行组对,需检查塔体直线度及滚轮架的水平度及直线度,并进行调整后再行组对。
9、浮头式换热器壳体上两大法兰平行度偏差为±2mm,方位以两大法兰眼心对中为准。
10、虾米弯环缝组对前可用放地样的方法进行预组对,由于需组对的焊缝形状为椭圆形,因此在组对时必须确保错边量≤1/4δ且不大于2.5mm,尤其是弯头的内圆周尚有壁厚增加的因素。
预组对过程中进行必要的修整后,再行打磨坡口,组对焊缝间隙要保证均匀一致。
11、严禁强力组对,点固焊缝间距和厚度要符合规定,严禁对材料表面进行烧烤。
12、焊接接头拘束度大时,推荐采用抗裂性能更好的焊条施焊。
13、点固焊缝不得有裂纹,否则应清除重焊。
如存在气孔、夹渣时亦应去除。
14、熔入永久焊缝内的点固焊缝两端应便于接弧,否则应予修整。
15、有预后热要求时,严格执行工艺。
环缝点焊预热采用氧—乙炔火焰加热,时间不得少于3min,保证温度,保证点焊焊缝长度≥150mm和厚度12~16mm,间距400~500mm,防止焊前开裂。
16、点焊及临时工卡具的焊接须采用和筒体相同的焊接工艺及焊材。
特殊技术要求:
1、换热器壳程筒体直线度允差为L/1000(L为圆筒总长),当L≤6000mm时,其值不大于4.5mm;当L>6000mm时,其值不大于8mm。
2、塔式容器直线度:
任意3000长度筒体直线度偏差≤3;筒体总长度L≤30000时,总偏差≤L/1000;L>30000时,总偏差≤0.5L/1000+15。
3、此工艺质量要求同时适用于筒体、封头、裙座筒体、锥段、卷制接管。
接管/法兰组焊
工艺编号:
艺06
1、领料
1.1接管法兰必须有材料确认标记,并经材料质检员验收合格,方可领料。
1.2管材须具有合格质保书,标记齐全。
1.3图样及标准规定进行超探的材料应检验合格。
1.4三类容器用材料须复验合格,母材抽样复验须合格,否则不得领料。
1.5法兰订货前必须考虑设计的特殊备注,如法兰内径B,以保证和SCH系列薄壁、厚壁接管相匹配。
1.6不锈钢管表面下料前应铺设保护膜。
2、号料
2.1按图纸规定的伸出长度减去法兰厚度进行接管划线、号料,接管须考虑马鞍口形状和接管焊接型式(内伸10mm或平齐),并预留3~8mm机加工余量,按理论最长点尺寸保证。
注意图纸中接管外伸高度、内伸高度的解释。
注意设计对标准人孔组合件的特殊备注,如锥段上人孔接管须加长。
2.2内伸式接管端部采用气割下料时需预留3mm的余量待切割后再用打磨等方法去除。
3、标记移植
3.1按附图四标移接管统一内容,包括材质、质保书号。
4、下料
4.1锯床切割或上车床加工接管。
4.2不锈钢接管下料切割须采用等离子切割机进行。
5、坡口加工
5.1切割或上车床加工接管坡口。
5.2不锈钢接管坡口切割须采用等离子,再上车床加工或用不锈钢专用砂轮片打磨。
5.3切割的坡口必须磨去氧化层、渗碳层、淬硬层,直至露出金属光泽。
附图四
6、环缝组对
6.1法兰领料进后,要用石棉板将法兰密封面保护好。
人孔、大型卷制接管等安装过程人须频繁出入的管口法兰,石棉板内圆直径比密封面内径小20㎜,石棉板外圆直径比法兰外径大20㎜;其余管口法兰用整圆板,外圆直径比法兰外径大20㎜。
6.2引弧板、引出板不应锤击拆除。
6.3组对尺寸允差见附表三。
6.4组对时尽量少用工卡具,以避免机械损伤。
不锈钢、Cr-Mo钢、低温钢、σs≥490Mpa的高强钢所用工卡具拆除后,母材经补焊后打磨平滑,并用永久记号笔做好标记,以进行磁粉或着色检测。
6.5工卡