内凸缘矩形盒设计.docx
《内凸缘矩形盒设计.docx》由会员分享,可在线阅读,更多相关《内凸缘矩形盒设计.docx(22页珍藏版)》请在冰豆网上搜索。
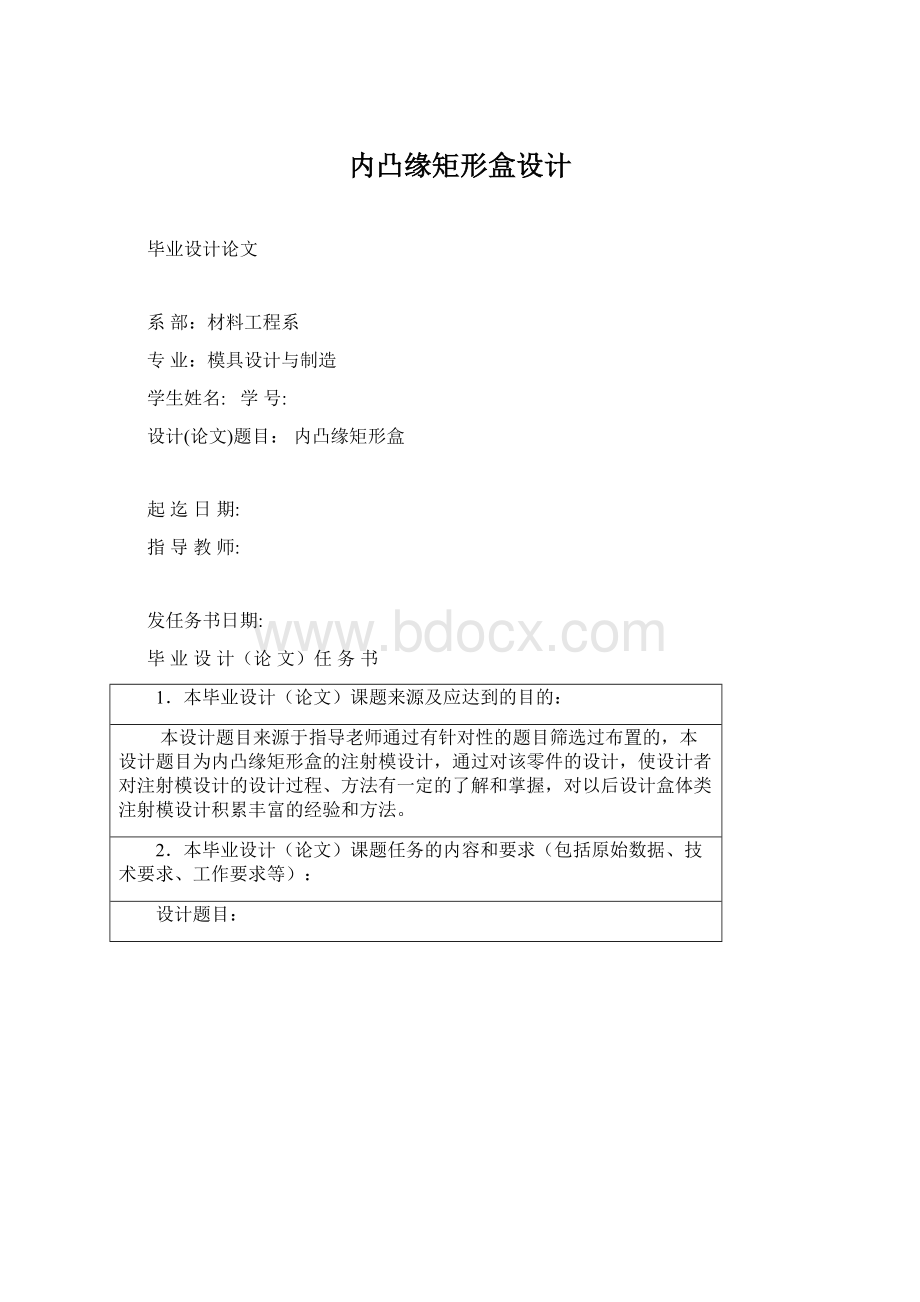
内凸缘矩形盒设计
毕业设计论文
系部:
材料工程系
专业:
模具设计与制造
学生姓名:
学号:
设计(论文)题目:
内凸缘矩形盒
起迄日期:
指导教师:
发任务书日期:
毕业设计(论文)任务书
1.本毕业设计(论文)课题来源及应达到的目的:
本设计题目来源于指导老师通过有针对性的题目筛选过布置的,本设计题目为内凸缘矩形盒的注射模设计,通过对该零件的设计,使设计者对注射模设计的设计过程、方法有一定的了解和掌握,对以后设计盒体类注射模设计积累丰富的经验和方法。
2.本毕业设计(论文)课题任务的内容和要求(包括原始数据、技术要求、工作要求等):
设计题目:
题目:
内凸缘矩形盒
材料:
HDPE
生产批量:
大批量生产
技术要求:
①未注圆角R2
②所有尺寸公差按SJ1372-78的4级精度
设计任务:
内容:
(1)完成矩形盒零件的工艺性分析及工艺方案制定
(2)矩形盒模具装配图及全部零件图的绘制
(3)完成模具主要工作零件的工艺规程编制
(4)编写设计说明书
题目:
内凸缘矩形盒设计
内容:
(1)内凸缘矩形盒的结构工艺分析;
(2)内凸缘矩形盒塑料注射模设计
(3)(3)绘制非标零件图;
(4)编写设计说明书;
(5)编制主要成型零件的加工工艺卡一份。
原始资料:
名称:
内凸缘矩形盒
材料:
聚乙烯
------------壳体
内凸缘矩形盒注塑模设计
前言
本设计根据从事塑料注塑模设计与制造的工程技术综合性应用型人才的实际要求,符合大专模具设计专业的毕业生毕业设计需要所编写的,对初学注塑模设计者有一定的参考价值。
本设计共分八章,分别对模塑工艺规程的编制、注塑模的结构设计、模具设计的有关计算、模具加热与冷却系统的计算、模具闭合高度的确定、注塑机有关参数的校核、注塑模主要零件加工工艺规程的编制等几方面进行了阐述。
本设计在设计过程中得到了翟德梅、杨占尧、原红玲等几位指导老师的大力支持和帮助,在此表示诚挚的感谢!
由于编者水平有限,收集技术资料困难,定有许多不尽人意的地方,恳请各位老师不吝赐教,提出改进意见。
以便使此设计进一步修正和完善。
绪论
一.模具在塑料成型中的地位
模具是工业生产中的重要工艺装备,模具工业是国民经济各部门发展的重要基础之一,塑料模具是指用语成型塑料制件的模具,它是型腔模具的一种,在现代塑料制件的生产中,合理的加工工艺、高效的设备,先进的模具是必不可少的三项重要因素,尤其是塑料模具对实现塑料加工工艺要求,满足塑料制件的使用要求,降低素件的成本起着重要的作用。
一副好的注射模具是可成型上百万次,一副优良的压缩模具大约可成型25万次,这与模具的是合计、模具材料及模具的制造有着很大的关系。
模具设计水平的高低、加工设备的好坏、制造力量的强弱、模具质量的优劣,直接影响着产品质量和经济效益能否提高,直接影响着许多新产品的开发和老产品的更新换代,工作能否顺利进行
俗话说:
“没有规矩不成方圆”世界上的许许多多东西都是从他们各具特色的“规矩”中诞生出来得。
东西-----产品,规矩-------模具。
模具:
是一种特殊的模型,用来塑造(制造)产品;从工艺的角度,模具是一种成型制品的特殊工艺装备。
模具技术:
研究模具设计、制造以及产品成型工艺的技术。
在现代化工业生产中,60%~90%的工业产品需要模具加工,模具工业已成为工业发展的基础,许多新产品的开发都依赖与模具,特别是汽车、电子电器、轻工、航空等行业。
因此,模具是工业生产的重要装备,是国民经济的基础工业。
模具被誉为工业之父,其技术集现代工业产品制造技术之大成。
世界各国给模具的称谓:
日本:
进入富裕社会的原动力。
德国:
金属加工业中的帝王。
罗马尼亚:
模具就是黄金。
欧美:
磁力工业
工艺先进的发达国家,其模具工业年产值早已超过机床行业的产值。
居20世纪90年代统计,日本模具工业已实现了高度的专业化、标准化和商品化,在全国一万多家模具企业中,生产塑料模具的企业占40%。
新近统计的韩国模具专业厂中,生产塑料模具的占43.9%,新加坡全国460多家模具企业中,60%生产塑料模具,由此可见,由于塑料成型工业的发展,塑料模具已处于同冲压模具并驾齐驱的地位。
二.我国塑料模具工业现状及今后的主要发展目标
我国各行业对模具工业的发展十分重视,国务院曾颁布过“当前产业政策要点的决定”。
在重点支持技术改造的产业、产品中,把模具制造列为机械工业技术改造序列的第一位。
它确定了模具工业在国民经济中的重要地位,也提出了振兴模具工业的主要任务,加入WTO后,在给我国机械行业尤其是模具工业带来严峻挑战的同时,也带来了巨大的机遇,我们必须尽快提高我国模具工业的整体技术水平并迎头赶上发达国家的模具技术水平。
本设计是注射模具设计,注射模具又称注塑模具,注射模具主要用语热塑性塑料制件的成型,近年来,热固性塑料注射成型的应用也在逐渐增加,世界塑料成型模具产量中的半数以上是注塑模具。
此外,反应注射成型、双色注射成型等特种注射成型工艺也正得到不断开发与应用。
三.设计目的及意义
本设计题目为内凸缘矩形盒的注塑模具设计,该课题的主要设计意义在于掌握注塑模设计的大体思路,懂得如何着手分析和考虑问题,能自己独立的设计出一套完整的模具体,且能将它应用于实际生产。
本设计对做毕业设计的毕业生有一定的设计意义,它概括了内凸缘矩形盒零件的设计要求、内容及方向。
通过对该零件模具的设计,进一步加强了设计者注塑模设计的基础,为设计更复杂的注塑模具做好了铺垫和吸取了更深刻的经验。
内凸缘矩形盒注射模设计
第一章
模塑工艺规程的编制
该塑件是一内凸缘矩形盒,,起零件图如下所示。
本塑件的材料初步选用HDPE,生产类型为大批量生产。
1.1塑件的工艺性分析
1.1.1塑件的原材料分析。
塑件的材料聚乙烯是指由乙烯单体自由基聚合而成的聚合物,英文名称为Polyethylene,简称PE。
PE的合成原料来自石油,因石油资源丰富,其产量自1965年一直高居第一。
聚乙烯是一种工业化年代较晚,但发展最快的塑料品种,最早实现工业化的品种为LDPE,于1951年首次实现万T级工业规模生产。
目前聚乙烯的产量占合成树脂总量的20%左右,到2000年,全世界聚乙烯的年产量为4800万吨,中国聚乙烯的年生产能力323万t,实际生产275万t/a。
目前,聚乙烯的主要品种有:
低密度聚乙烯(LDPE)、高密度聚乙烯(HDPE)、线性低密度聚乙烯(LLDPE)、高分子量聚乙烯(UHMWPE)及氯化聚乙烯(CPE)等。
PE为线性聚合物,具有同烷烃相似的结构,属于高分子长链脂肪烃;分子对称无极性,分子间作用力小,力学性能不高、电绝缘性好、熔点低、印刷性不好。
PE分子链上含有短的甲基和长的烃基支链,并含有少量的双键和醚基,其耐候性不好,日晒、雨淋都引起老化,需加入抗氧剂和光稳定剂改善。
PE的结构规整、线性度高,因而易于结晶,晶型属于斜方晶系。
PE树脂为无味、无毒的白色粉末或颗粒,外观呈乳白色,有似蜡的手感,吸水率低,小于0.01%。
PE的膜透明,并随结晶度提高而下降。
PE膜透水率低但透气性较大,不适用于保鲜而适于防潮包装。
PE易燃,氧指数仅为17.4,燃烧时低烟,有少量熔融落滴,火焰上黄下蓝,有石蜡气味,PE的耐水性较好,制品表面无极性,难以粘合和印刷,经表面处理才可以改善。
PE的力学性能一般,其拉伸强度一般,抗蠕变性不好,只有耐冲击性能较好。
耐环境应力开裂性不好,但耐穿刺性好。
耐低温性不好,耐热性不好,线膨胀系数大,热导率较高。
PE无极性,介电损耗低,且随温度和频率变化较小,可用于高频绝缘,是少数年点晕性好的塑料品种,介电强度又高,因而可用于做高压绝缘材料。
PE属烷烃类惰性聚合物,具有良好的化学稳定性,PE常温下可耐酸碱、盐类水溶液的腐蚀,具体有稀硫酸、稀硝酸、任何浓度的盐酸、氢氟酸、磷酸、甲酸及乙酸等,但不耐强氧化剂如发烟硫酸、弄硫酸和络酸等。
PE在60℃以下不溶于一般溶剂,但与脂肪烃、芳香烃、卤代烃等长期接触会熔涨或龟裂。
温度超过60℃后,可少量溶于甲苯、乙酸戊酯、三氯乙烯、松结油、矿物油及石蜡中,温度超过100℃后可溶于四氢化萘
1.1.2塑件的结构和尺寸精度及表面质量分析
1.1.2.1结构分析。
从零件图上分析,该零件总体形状为一个无盖子的矩形盒。
在长度方向的两侧对称各对称分布了的一个长度为44mm,高度为4mm,宽度为5mm的凸缘。
凸缘距离边缘为8mm,相对来看就又出现了44mm
8mm
4mm的凹槽(对称分布),因此,模具设计时候必须考虑采用斜导柱内抽芯、斜顶杆顶出抽芯、斜滑块的内侧抽芯等方法把内凸缘成型出来,该零件属于中等程度。
1.1.2.2尺寸精度分析。
由制件可知,此制件为未注公差尺寸。
查《实用注塑模设计手册》中的表2-7塑料制件尺寸公差(SJ1372)和表2-8塑件推荐选用精度等级按一般精度等级选用公差等级为MT7级(GB/T14486—1993)。
具体尺寸取值如下400-0.72、210+0.56、50-0.36、40+0.36、340+0.72、240-0.56、80+0.40、500-0.80、440+0.80。
由以上的分析可知,该零件的尺寸精度中等,对应的模具相关零件的尺寸加工可以得到保证。
从塑件的壁厚上来看,壁厚最大处为5mm,最小处为3mm,壁厚差为2mm,较均匀,有利于成型。
1.2.2.3表面质量分析。
该零件的表面除要求没有缺陷、毛刺,内部不得有杂质外,没有特别的表面质量要求,故比较容易实现。
综上分析可以看出,注塑时在工艺参数控制得较好的情况下,零件的成型要求可以得到保证。
1.2计算塑件的体积和质量
计算塑件的质量是为了选用注塑机及确定模具型腔数。
计算塑件的体积:
V=44
5
4
2+34
44
(24-21)+34
24
(50-44)/2
2+50
24
(40-34)
/2
2=18344
计算塑件的质量:
根据设计手册可查得低密度聚乙烯LDPE的密度为0.94~0.96g/cm3,取0.95g/cm3。
故塑件的质量为:
W=Vρ
=18344
0.95
10-3
=17.4268g
查《塑料制品及其成型模具设计》表0.1和《注塑模具典型结构100例》附表6得
塑料名称
聚乙烯(高压)
缩写
HDPE
注射成型类型
柱塞式
密度/g/cm3
0.94~0.96
计算收缩率/%
1.5~3.6
预热
温度/℃
70~80
时间/h
1~2
料筒温度/℃
后段
140~160
中段
170~180
前段
180~200
喷嘴温度/℃
160~180
注射压力/MPa
60~100
模具温度/℃
35~50
成型时间/S
注射时间
15~60
高压时间
0~3
冷却时间
15~60
总周期
40~130
1.3注塑机的选择
选择合适的注塑机是注塑加工正常进行的前提,本模具设计中初步决定采用一模两腔的结构,选择注塑机要以下列参数为依据
1.3.1最大注射量
注塑模一次成型的塑料重量(塑件与流道凝料之和)应在注塑机理论注射量的10%~80%之间;既能保证制品质量,又可充分发挥设备的能力,则选在50%~80%之间为好。
这里计算为粗略计算,视单个流道凝料重量为
则注射量在50%~80%中选择即
中选择。
1.3.2注射压力
注塑加工时所需注射压力与塑料品种、塑件的形状及尺寸、注塑机类型、喷嘴及模具流道的阻力等因素有关。
选择的注塑机注射压力必须大雨成型制品所需的注射压力。
根据经验,成型所需注射压力范围如下:
1.3.2.1塑件结构简单,熔体流动性好,壁后者,所需要注射压力一般小于70MPa;
1.3.2.2塑件形状一般,精度要求一般,熔体流动性好者,所需注射压力通常选70~100MPa;
1.3.2.3塑件形状一般,有一定精度要求,熔体粘度中等(如改性PE、PS),所需注射压力选100~140MPa;
1.3.2.4塑件壁薄、尺寸大,壁后不均,精度要求高,熔体粘度高者,注射压力选为100~140MPa。
1.3.3锁(合)模力
锁(合)力为注射机锁模装置用于夹紧模具的力。
所选注塑机的锁(合)模力必须大于由于高压熔体注入模腔压力的乘积。
即:
F锁>P腔
A/1000
这里P腔=25MPa;A≈2
40
50mm2
代入上式子中得到F锁>100KN
由以上分析考虑其塑件外形尺寸、注塑时所需压力和工厂现有设备的情况,初步选用注塑机为XS--Z--60型。
注塑机参数
XS--Z--60
额定注射量/CM3
60
柱塞直径/mm
38
注射压力/MPa
122
注射行程/mm
170
注射方式
柱塞式
锁模力/KN
500
最大成型面积/CM3
130
最大开模行程/mm
180
模具最大厚度/mm
200
模具最小厚度/mm
70
1.4塑件注塑工艺参数的确定
查找相关文献和参考工厂实际应用的情况,高密度聚乙烯(HDPE)的成型工艺参数可作如下选择:
(试模时,可根据实际情况做适当的调整)
注塑温度:
后段温度t1选用140~160/℃;
中段温度t1选用170~180/℃;
前段温度t1选用180~200/℃;
喷嘴温度:
选用160~180/℃;
注塑压力:
选用122MPa;
注塑时间:
选用40s;
保压:
选用78MPa;
保压时间:
选用15s;
冷却时间:
选用40s;
第二章
注塑模的结构设计
注塑模结构设计主要包括:
分型面选择、模具型腔数目的确定、型腔的排列方式、冷却水道布局、浇口位置设置、模具工作零件的结构设计、侧向分型与抽芯机构的设计、推出机构的设计等内容。
2.1分型面选择
模具设计中,分型面的选择很关键,它决定了模具的结构。
应根据分型面选择原则和塑件的成型要求来选择分型面,应以模具结构简单,分型容易,且不破坏已成型塑件为原则。
该塑件为内凸缘矩形盒,表面质量无特殊要求,但由于两内凸缘的作用使得分型面的选择现得有点困难了,此外该零件高度为24mm,且垂直于轴线的截面形状比较简单和规范,若选择下图示水平分型方式既可降低模具的复杂程度,减少模具加工困难又便于成型后出件。
故选用下图所示的分型方式较为合理。
2.2确定型腔的排列方式
本塑件采用一模两件,即模具需要两个型腔。
综合考虑浇注系统,模具结构的复杂程度等因素拟采取如下图所示的型腔排列方式
采用机喷嘴的有关尺寸:
喷嘴前端孔径:
d0=Ф4mm;
喷嘴前端球面半径:
R0=12mm;
根据模具主流道与喷嘴的关系:
R=R0+(1~2)mm
D=d0+(0.5~1)mm
取主流道球面半径R=13mm;主流道的小端直径d=Ф4.5mm。
为了便于将凝料从主流道中拔出,将主流道设计成圆锥形,其斜度为1˚~3˚经换算得主流道大端直径D=Ф8.5mm。
为了使溶料顺利进入分流道,可在主流道出料端设计半径r=5mm的圆弧过渡。
2.3.2分流道设计。
分流道的形状及尺寸,应根据塑件的体积、壁厚、形状的复杂程度、注塑速率、分流道长度等因素来确定。
本塑件的形状不算太复杂,溶料填充型腔比较容易。
根据型腔的排列方式可知分流道的长度较短,为了便于加工起见,选用截面形状为半圆形的分流道,查表得R=4mm。
2.3.3浇口设计。
根据塑件的成型要求及型腔的排列方式,选用侧浇口比较理想。
设计时考虑从壁厚为5mm处进料,料由厚处往薄处流,而且在模具结构上采用镶拼式型腔、
本设计的塑件内侧有两个对称的凸缘,它们均垂直于脱模方向,阻碍成型后塑件从模具脱出。
因此成型两凸缘的零件必须做成活动的型芯,即需要设置抽芯机构。
本模具采用初步决定采用斜滑块的内侧抽芯的方法。
2.4.1确定抽芯距。
抽芯距一般应大于成型凸台的高度,本设计中塑件两凸台高度相等,均为4mm,考虑到本设计塑件的型芯为斜角的特殊性故不用加抽芯安全系数塑件即可顺利脱模。
取抽芯距S抽=4mm。
2.4.2确定斜楔倾角。
斜楔和活动镶件的倾斜角α是斜滑块内抽芯的主要数据之一,它与抽拨力以及抽芯距有直接关系。
一般取α=15˚~25˚,本例选取α=20˚。
2.4.3确定斜楔的尺寸。
斜楔的直径取决于抽拨力及其倾斜角度,可按设计资料的有关公式进行计算。
本设计经验估值,取斜楔的直径d=Ф20mm。
斜楔的长度根据固定板的厚度、抽芯距、斜楔直径及斜角大小确定,这里取37mm。
2.4.4滑块与导滑槽设计。
本设计中侧向抽芯机构主要是用于成型零件的侧向槽和侧向凸台,由于侧向槽和侧向凸台的尺寸较小,考虑到型芯强度和装配问题,采用组合式结构。
型芯与滑块的连接采用镶嵌方式;本设计中为使模具结构紧凑,降低模具装配复杂程度,拟采用整体式滑块和整体式导向槽的形式。
由于侧抽芯距较短,故导滑长度只要符合滑块
在开模时的定位要求即可。
2.5成型零件结构设计
2.5.1凹模的结构设计。
本设计中模具采用一模两件的结构形式,考虑加工的难易程度和材料的价值利用等因素,凹模拟采用镶嵌式结构。
2.5.2凸模结构设计。
凸模主要是与凹模相结合构成模具的型腔。
其凸模与侧型芯的结构形式如下图
第三章
模具设计中的有关计算
本设计中成型零件工作尺寸计算时候均采用平均尺寸、平均收缩率、平均制造公差和平均磨损量来计算。
查表高压聚乙烯的收缩率为S=1.5%~3.6%,故平均收缩为
SCP=(1.5+3.6)/2%=2.55%,模具制造公差取δZ=Δ/3。
3.1型腔和型芯工作尺寸计算
3.1.1定模型腔直径(宽)。
定模型腔直径(长)。
定模型腔深度:
活动镶块长度:
活动镶块高度:
槽宽;
槽深:
3.2型腔侧壁厚度和底板厚度计算
3.2.1定模型腔镶件侧壁厚度计算
定模镶件型腔为组合式矩形型腔,根据组合式矩形型腔侧壁厚度计算公式进行计算:
式子中P为型腔压力(MPa)这里取25MPa;
a=8mmA=21mm(初选值)
(根据上面型腔工作尺寸计算得长宽尺寸分别为40mm和
50mm,取大值进行计算)
E:
为模具材料的弹性模量取
δ:
刚度条件,即允许变形量,在0.025~0.04中选取
这里选取δ=0.035mm。
代入公式计算得h=6.325mm
3.2.2定模型腔镶件底板厚度计算
根据组合式型腔底板厚度计算公式进行计算:
式子中P=25MPa;
b=8mm;
L=85mm(初选值);
B=160mm(根据模具初选外形尺寸确定);
[δ]=160MPa(底板材料选定为45刚);
代入公式计算得
H=6.51mm
考虑到模具的整体结构协调,取H=25mm。
第四章
模具加热与冷却系统的计算
本塑件在注射成型时不要求有太高的模温,因而在模具上可不设加热系统。
是否需要冷却系统可作如下设计计算:
设定模具平均工作温度为65℃,用20℃得常温水冷却,其出口温度为
45℃,产量为(初算每两分钟一套)0.51kg/h。
4.1求塑件在硬化时每小时释放的热量Q3。
查有关文献得聚乙烯的单位热流量为
4.2求冷却水的体积流量V。
由体积流量V查表可知所需的冷却水管直径非常小。
由上述计算可知,因为模具每分钟所需的冷却水体积流量很小,故可不设冷却系统,依靠空冷的方式冷却模具即可。
第五章
模具闭合高度的确定
在支承与固定零件的设计中,根据经验确定:
定模座板:
H1=16mm;
上固定板:
H2=40mm;动模固定板:
H3=20mm;支承板:
H4=20mm;垫块:
H5=50mm;
动模座板:
H6=16mm。
因而模具的闭合高度:
H=H1+H2+H3+H4+H5+H6
=16+40+20+20+63+16
=165mm
第六章
注塑机有关参数的校核
本模具的外形尺寸为
XS--Z--60型注塑机模板最大安装尺寸为350mm
280mm,故能满足模具的安装要求。
由上述计算模具的闭合高度H=152mm,XS--Z--60型注塑机所允许模具的最小厚度Hmin=71mm,最大厚度Hmax=200mm,即模具满足安装条件。
经查资料XS--Z--60型注塑机的最大开模行程S=180mm,满足式顶出塑件要求
S
H1+H2+(5~10)mm
=16+32+10
=58mm
此外,由于侧分型抽芯距较短,不会过大增加开模行程距离,注塑机的开模行程足够。
经验证,XS--Z--60型注塑机能满足使用要求,故可采用。
第七章
绘制模具总装图和非标零件工作图
本模具的工作原理:
模具安装在注塑机上,定模部分固定在注塑机的定模板上,动模固定在注塑机的动模板上。
合模后,注塑机通过喷嘴将熔料经流道注入型腔,经保压,冷却后塑件成型。
开模时,塑件包在型芯10和活动镶件8上随动模部分向左移动而脱离定模座,分型到一定距离后,脱出机构开始工作,设置在活动镶件8上的顶杆11将活动镶件连同塑件一起推出型芯脱模。
合模时,顶杆在弹簧13的作用下复位,顶杆复位后动模板停止移动,然后人工将活动镶件重新插入镶件定位孔中,再合模后进行下一次的注塑过程。
技术说明:
动模型芯镶件10大端为带台阶的圆柱,中间高出与活动镶件齐平。
两活动镶件插入件10的左、右两矩形孔内,靠件10两矩形孔的侧壁定位。
脱模时靠顶杆11将活动镶件,连同制品一同顶出型腔。
同理,须先复位,靠弹簧13实现。
复位杆件20实际上仅仅是为了安装复位弹簧而已,并未起到复位作用。
顶杆件11的尖头部位应稍长些,安装活动镶件才方便。
其长度不应小于顶杆件9厚度的1/2。
件11尖头部分的尖角为10˚~15˚的小斜面不可忽视,此斜面使镶件插入并正确定位方便。
第八章
注塑模主要零件加工工艺规程的编制
在此仅对成型零件型芯的加工工艺进行分析。
8.1型芯的加工工艺
型芯的加工工艺过程见表8-1。
机械加工工艺过程卡
机械加工工艺过程卡片
产品型号
零(部)件图号
01
产品名称
活动镶件
型芯
共( )页第( )页
材料牌号
40Cr
毛坯
种类
锻造毛坯
毛坯外型尺寸
每个毛坯可制件数
1
每台
件数
备注
工序号
工序名称
工序内容
车间
工段
设备
工艺装备
工时
准终
单件
1
下料
下料:
Ф50mm×55mm
备料车间
锯床
2
锻造
锻至尺寸15mm×40mm×50mmm
锻造车间
空气锤C41—250加热炉
3
退火
退火
锻造车间
加热炉
4
刨
刨六面尺寸至12mm×38mm×45mm
模具车间
刨床
5
刨
一端尺寸不边,另一端刨成11mm×37