油罐内部防腐.docx
《油罐内部防腐.docx》由会员分享,可在线阅读,更多相关《油罐内部防腐.docx(7页珍藏版)》请在冰豆网上搜索。
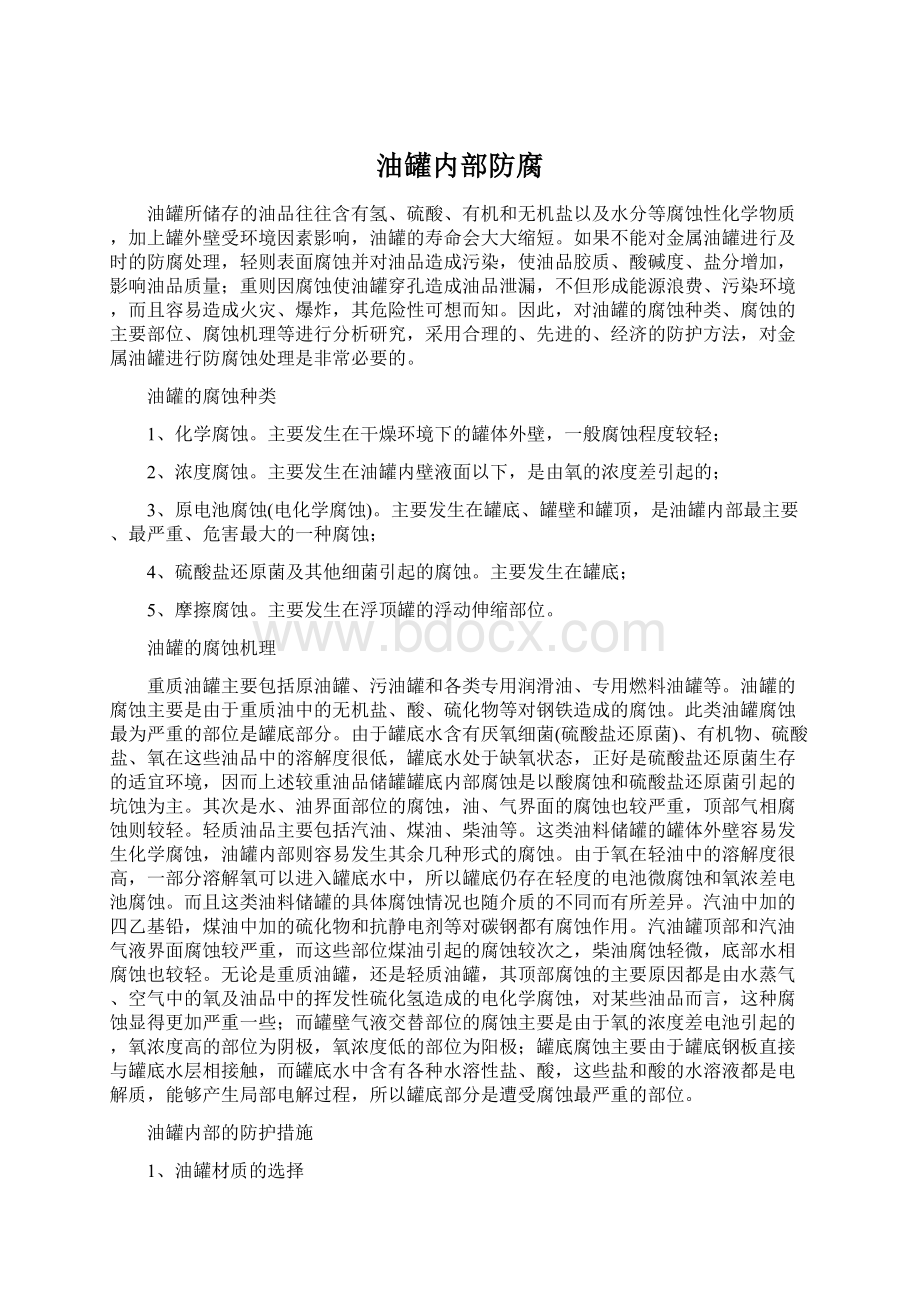
油罐内部防腐
油罐所储存的油品往往含有氢、硫酸、有机和无机盐以及水分等腐蚀性化学物质,加上罐外壁受环境因素影响,油罐的寿命会大大缩短。
如果不能对金属油罐进行及时的防腐处理,轻则表面腐蚀并对油品造成污染,使油品胶质、酸碱度、盐分增加,影响油品质量;重则因腐蚀使油罐穿孔造成油品泄漏,不但形成能源浪费、污染环境,而且容易造成火灾、爆炸,其危险性可想而知。
因此,对油罐的腐蚀种类、腐蚀的主要部位、腐蚀机理等进行分析研究,采用合理的、先进的、经济的防护方法,对金属油罐进行防腐蚀处理是非常必要的。
油罐的腐蚀种类
1、化学腐蚀。
主要发生在干燥环境下的罐体外壁,一般腐蚀程度较轻;
2、浓度腐蚀。
主要发生在油罐内壁液面以下,是由氧的浓度差引起的;
3、原电池腐蚀(电化学腐蚀)。
主要发生在罐底、罐壁和罐顶,是油罐内部最主要、最严重、危害最大的一种腐蚀;
4、硫酸盐还原菌及其他细菌引起的腐蚀。
主要发生在罐底;
5、摩擦腐蚀。
主要发生在浮顶罐的浮动伸缩部位。
油罐的腐蚀机理
重质油罐主要包括原油罐、污油罐和各类专用润滑油、专用燃料油罐等。
油罐的腐蚀主要是由于重质油中的无机盐、酸、硫化物等对钢铁造成的腐蚀。
此类油罐腐蚀最为严重的部位是罐底部分。
由于罐底水含有厌氧细菌(硫酸盐还原菌)、有机物、硫酸盐、氧在这些油品中的溶解度很低,罐底水处于缺氧状态,正好是硫酸盐还原菌生存的适宜环境,因而上述较重油品储罐罐底内部腐蚀是以酸腐蚀和硫酸盐还原菌引起的坑蚀为主。
其次是水、油界面部位的腐蚀,油、气界面的腐蚀也较严重,顶部气相腐蚀则较轻。
轻质油品主要包括汽油、煤油、柴油等。
这类油料储罐的罐体外壁容易发生化学腐蚀,油罐内部则容易发生其余几种形式的腐蚀。
由于氧在轻油中的溶解度很高,一部分溶解氧可以进入罐底水中,所以罐底仍存在轻度的电池微腐蚀和氧浓差电池腐蚀。
而且这类油料储罐的具体腐蚀情况也随介质的不同而有所差异。
汽油中加的四乙基铅,煤油中加的硫化物和抗静电剂等对碳钢都有腐蚀作用。
汽油罐顶部和汽油气液界面腐蚀较严重,而这些部位煤油引起的腐蚀较次之,柴油腐蚀轻微,底部水相腐蚀也较轻。
无论是重质油罐,还是轻质油罐,其顶部腐蚀的主要原因都是由水蒸气、空气中的氧及油品中的挥发性硫化氢造成的电化学腐蚀,对某些油品而言,这种腐蚀显得更加严重一些;而罐壁气液交替部位的腐蚀主要是由于氧的浓度差电池引起的,氧浓度高的部位为阴极,氧浓度低的部位为阳极;罐底腐蚀主要由于罐底钢板直接与罐底水层相接触,而罐底水中含有各种水溶性盐、酸,这些盐和酸的水溶液都是电解质,能够产生局部电解过程,所以罐底部分是遭受腐蚀最严重的部位。
油罐内部的防护措施
1、油罐材质的选择
一般宜选用含碳量小于0.2%和硫、磷含量低于0.3%的钢材。
不同存储介质的油罐应选用不同的不锈钢材质。
2、适当增加腐蚀严重部位的钢材厚度
适当增加腐蚀严重部位如罐底和罐顶的厚度可以提高防腐能力,但不应超过钢板总厚度的20%。
3、采用阴极保护法
油品沉积污水介质中含盐量高,腐蚀性成分多,致使储罐底部受到严重的腐蚀,多年实践证明,牺牲阳极阴极保护可以减缓与沉积污水介质相接触部分表面的腐蚀。
一般采用压制带状阳极在罐底环状布置和罐壁下部均匀分布作牺牲阳
极。
在实际应用中通常牺牲阳极阴极保护与涂料联合使用,将更经济、取得更好的保护效果。
4、热喷涂复合防护层
把喷涂的金属原料在高温下熔化,用压缩气体或其他惰性气体将熔化的金属吹成雾状,迅速地喷射到预先准备好的金属物体表面上,这些细小的金属颗粒在飞射过程中是处于熔化状态,当撞到被喷射的物体表面后,立即变形、伸平并迅速冷却,紧紧地嵌附在被喷涂物体的表面,连续喷射便形成喷涂层。
在经过热喷后铝的钢基组织表面形成了0.1~0.3mm的喷涂层,该保护层可以经受住典型的工业大气及高温考验,能有效地隔绝腐蚀介质的渗透,防止钢基在介质中的电化学腐蚀,铝覆盖层还能不断地给钢基提供牺牲阳极保护,从而保护金属不受腐蚀。
5、涂料防护
从目前情况来看,对油罐内部防腐,国内外大都采用涂料进行防护。
要求涂料具有良好的耐油性,在-30~50℃范围内能耐原油、汽油、柴油、煤油、渣油、含油污水等介质的腐蚀。
同时涂料还应具有良好的抗静电性能,为此防腐涂料中往往需加入导静电填料,使涂料的体积电阻率降低。
除此之外,防腐涂料还应具有良好的物理机械性能,如附着力强、常温固化、不龟裂、施工方便等。
国外非常重视油罐防腐工作,日本通过对3042台油罐防腐调查,大部分采用环氧涂料、环氧煤焦油涂料、玻璃鳞片涂料、锌粉涂料用于油罐防腐,使用寿命7~10年,涂层厚度一般为0.4~0.7mm。
国内目前常用的储罐涂料主要有环氧树脂、聚氨酯、无机富锌、有机富锌、玻璃鳞片涂料等。
一般国内常用的油罐涂料品牌有:
8701环氧树脂防腐蚀涂料、TH一4硅酸锌耐油防锈涂料、H一99环氧抗静电涂料、环氧漆酚耐蚀抗静电涂料、聚氨酯抗静电涂料、EP一67环氧树脂玻璃鳞片防腐蚀涂料。
2.1涂料防护
从目前情况来看,对油罐内部防腐,国内外大都采用涂料进行防护。
要求涂料具有良好的耐油性,在-3O——5O℃范围内能耐原油、汽油、柴油、煤油、渣油、含油污水等介质的腐蚀。
但是,油品在贮运过程中,因摩擦而产生静电荷,石油制品易于积聚静电荷。
静电压随静电积累而升高,有可能高达1OKv以上,由于静电放电而引起火灾,爆炸事故。
因此,国家标准(GB13348)规定:
石油储罐内壁防腐蚀涂料必须具有良好的导静电能力。
涂料的体积电阻率应≤108欧姆米,并确定涂料对油品性质无害。
国内从1990年代后期相继推出抗静电耐油防腐蚀涂料,基本上属掺合型导静电涂料。
国内目前常用的储罐涂料主要有环氧树脂、聚氨酯、无机富锌、有机富锌、玻璃鳞片涂料等。
一般国内常用的油罐涂料品牌有:
8701环氧树脂防腐蚀涂料、TH-4硅酸锌耐油防锈涂料、H-99环氧抗静电涂料、环氧漆酚耐蚀抗静电涂料、PU-91聚氨酯抗静电涂料、EP-67环氧树脂玻璃鳞片防腐蚀涂料。
除此之外,防腐涂料还应具有良好的物理机械性能,如附着力强、常温固化、不龟裂、施工方便等。
国外非常重视油罐防腐工作,日本通过3052台油罐防腐调查,大部分采用环氧涂料、环氧煤焦油涂料、玻璃鳞片涂料、锌粉涂料用于油罐防腐,使用寿命7-lOa,涂层厚度一般为0.4-0.7mm。
其中玻璃鳞片涂料40.2%,环氧涂料占27.7%;环氧煤焦油涂料占10.1%;锌粉涂料占10.3%,其他涂料占11.7%。
美国石油学会(API)1991年发布的APIRP652-地面石油储罐防腐蚀涂层技术标准,经过对30家涂料厂家近50个产品进行试验室加速试验评价,选出25个适用产品,作为推荐使用产品,薄层(厚度在500微米以内):
主要环氧煤焦油涂料、环氧酚醛涂料、环氧-胺、环氧-聚酰胺等涂料系统。
厚层涂料(厚度大于500微米)的有:
玻璃鳞片加强的乙烯基树脂涂料、环氧树脂以及间苯二甲酸酯涂料等。
对于新建油罐进行内防腐处理时推荐厚度为900-1400微米,而出现腐蚀的旧油罐建议厚度2000-3000微米。
中国石油储罐防腐剖析
索双富等
引言
十几年来我国的许多港口及炼油厂建立了大量的储油设施,这些设施的可靠运行对高效 生产及环境安全有直接关系。
而油罐的腐蚀使油品中掺入铁锈等杂质,这些杂质加速了内燃机和其它机械摩擦副的磨损。
因此油罐防腐越来越受到重视。
由于中国地域广阔,气候环境存在巨大差异,一年四季中气温、空气的湿度、太阳的辐射强度、工业化程度等也有巨大差别,各地炼油厂的中小型储油设备采用了多种多样的防腐措施,各种常用的防腐措施几乎均能在我国的储油设施中见到。
下面首先分析储油罐的腐蚀机理,然后综述中国储油罐常用的防腐技术,最后介绍电弧喷涂长效防腐技术,这种复合涂层可为油罐提供20年以上的有效保护。
一、油罐腐蚀现象及腐蚀机理
1.油罐的腐蚀现象
中国某石油基地,自1976年投产以来,先后建成各类油罐95座,总容积60万m3,大部分油罐投入使用前内壁用红丹粉、外壁用调和漆进行防腐处理,经测试,各种油罐不同部位的腐蚀速率见表1。
由表1可以看出,轻质油罐的腐蚀速率一般大于中、重质油罐的腐蚀速率;轻质油罐顶部气液相交界处腐蚀速率大于
表1油罐不同部位的腐蚀速率
mm/a
油罐部位油罐类别
罐底
(内表面)
油相罐壁
油气或油水
两相交界处
油罐顶部
轻油油罐
0.1~0.2
≤0.1
0.3~0.5
0.3~0.4
重油油罐
0.2
0.1
0.3~0.5
0.3~0.4
石脑油罐
≤0.1
≤0.1
0.3~0.5
0.3~0.4
汽油罐
≤0.1
≤0.1
0.3~0.5
0.3~0.5
柴油罐
0.1
<0.1
0.1~0.2
0.12
渣油罐
0.1~0.2
0.1
0.1~0.2
0.2
重油罐
0.1~0.2
≤0.1
0.1~0.2
0.2
原油罐
0.2~0.3
0.1
0.2~0.3
0.1~0.2
罐壁。
另外,油罐气相部位的腐蚀一般为均匀腐蚀,而罐底则为不均匀的点蚀;油罐内壁比外壁的腐蚀速度高;当油罐所处环境空气湿度大,四季温差大,空气中氯离子、二氧化碳、硫化物含量高时,则油罐腐蚀速率大。
2.油罐的腐蚀机理
(1)油罐气相部位以化学腐蚀为主,气相部位基本上均匀腐蚀,这是因为油料中挥发出的酸性气体H2S、HCI,外加通过呼吸气阀进入罐内的水分、氧气、二氧化碳、二氧化硫等腐蚀气氛在油罐上凝结成酸性溶液,导致化学腐蚀的发生。
(2)油罐储油部位该部位腐蚀速率低,一般不会造成特殊危险。
但是应指出气相、液相交界处,即干湿交界处环境潮湿富氧,具备电化学腐蚀的两大基本要素。
(3)罐底内表面其腐蚀形貌为点蚀,主要原因是罐底积聚了酸性沉淀,酸性水中含有大量富氧离子,成为较强的电解溶液,产生化学腐蚀;加上油中固体杂质和油罐腐蚀产物大量沉积于罐底,它们与油罐罐底有不同的电极电位,这就形成了腐蚀电池,产生了电化学腐蚀。
罐底外表与土壤电解质接触,其腐蚀速率约为0.8mm/a。
二、油罐常用的防腐方法
油罐的防腐可以分为两类,一类是新建油罐的防腐;另一类是旧油罐的修复防腐。
这里仅讨论新建油罐的防腐问题。
由于油罐内部与外部的腐蚀机理有一定的差异,因而采取的防腐措施也不一样,理想的设计是各个部位同寿命;但由于具体情况差异很大,一般对油罐的内壁分为三部分,即底部、中部和顶部;罐体外部可分为两部分,既罐地板与底部及罐体侧
部与顶部。
油罐外壁常用防腐方法主要有:
(1)石油沥青防腐涂层。
(2)硬质聚胺脂泡沫塑料制作的防腐保温层,介质温度<100℃。
(3)塑料胶粘带防腐层,温度<70℃,涂层为一层底胶+两层塑料胶粘带+一层外保护层的复合结构。
(4)环氧沥青防腐涂层。
用于油罐内壁防腐方法很多,如表面镀、渗相应的耐腐蚀材料、水泥沙浆衬里、喷刷防腐涂料等。
近年油罐内壁制备喷铝复合涂层技术也已成熟,受到了用户欢迎。
但当前中国油罐内壁多采用防腐涂料。
因为成品油是有机高绝缘性物质,油料在流动、过滤、搅拌、喷射、灌注等过程中,可能产生静电荷,携带静电荷的流体进入储罐后,则发生电荷的积聚,引起电位的升高,该电位是否会上升到超过安全极限值,取决于油料中静电荷是否能够迅速释放,否则由于静电荷的积聚,可能发生火灾或爆炸事故。
因此,所选涂料除应具有良好的耐油、耐水性,附着力强,柔韧性好,抗冲击,抗老化等性能外,还必须满足GB13348-92《液体石油产品静电安全规程》及中国石化总公司(91)生字224号文件对油罐《内壁防腐涂料应低于108Ωm》的要求。
为获取理想的油罐内壁涂料,近十几年来,中国许多科研生产单位进行了大量研究工作,取得了丰硕的成果,现已研制出近20种抗静电涂料,如1900聚氨脂导电漆、PU-91-2弹性导静电防腐涂料、036-3导静电耐油防腐涂料、SFZ-909导静电防腐涂料、HE52-5耐油防静电防腐涂料。
三、电弧喷涂复合涂层
油罐的设计寿命一般为20年,采用漆类防腐不能达到防腐层同油罐的设计寿命相一致,在我国的重腐蚀区,这类涂层的寿命仅为3~5年,甚至更短。
因此近年能长效防腐的电弧喷涂复合涂层得到了广泛的应用,采用这种涂层可以做到防腐层同油罐的设计寿命相一致,大大节约油罐的维护费用,提高设备的利用率,减小由于设备维护造成的减产或停产。
电弧喷涂复合保护层能够有效地保护储油罐的内壁,特别是阴极保护不能实现的部位,在油罐的内壁气相腐蚀部位,采用电弧喷涂锌做基础,外部涂覆抗静电封闭剂,在海洋大气及工业大气复合污染的环境下,采用铝基复合涂层,能够使外壁获得长效抗腐蚀保护。
1.电弧喷涂复合涂层的保护机理
在电弧喷涂的锌、铝涂层上再涂覆封闭涂层(有时为了外观效应,可增涂任何色彩的油漆),形成的复合保护涂层对机体有双重保护作用,一方面可以像涂料那样把机体同腐蚀环境隔离开,另一方面锌、铝的电解电位比钢铁低,因此涂层对机体有阴极保护作用。
锌、铝涂层有如下三个特点:
(1)锌、铝涂层与钢铁在同一腐蚀环境中,其腐蚀速率比钢铁低,这样在钢铁机体上喷涂较薄的一层Zn、Al,其耐腐蚀性比钢铁年限长许多。
(2)锌、铝涂层在一定腐蚀环境下稳定性良好,如九个月海水中浸泡实验表明,锌的电极电位波动仅±30mV,纯铝的电极电位变化要大一些,但纯铝表面能形成一层牢固的氧化物薄膜,阻止腐蚀的进一步进行。
(3)锌、铝涂层较钢铁有更低的腐蚀电位,对油罐内壁钢铁机体起到阴极保护作用。
2.电弧喷涂复合保护涂层的设计
电弧喷锌涂层、喷铝涂层、喷锌铝合金涂层均可应用于油罐的防腐保护,但在海洋大气中以铝涂层为好。
在综合实验数据的基础上,得出喷铝涂层寿命经验公式为
T=(0.64W)/(D)
式中T——设计寿命,a
W——涂层的厚度,μm
D——裸露钢铁面积的百分数
裸露钢铁面积的百分数与涂层的孔隙率有关,电弧喷铝的孔隙率一般为15%,因为不是所有孔隙均暴露出钢铁,所以D要小于15%,它与涂层厚度及喷涂参数有关,一般为4%~6%。
涂层加封闭剂后则D变得更小,综上所述,一般喷铝涂层厚度为180μm~220μm。
3.封闭涂层设计
封闭涂层既可以延长金属涂层的寿命又具有装饰作用。
除了应具备油罐内壁涂料性能要求外,封闭剂的渗透能力也是其重要指标,其粘度必须进行有效控制,粘度大的封闭剂渗透能力差;封闭剂的颗粒尺寸对渗透效果也有影响,用于油罐内壁的封闭剂应采用小尺寸颗粒、具有抗静电能力的为好,同时现场使用时加入稀释剂,提高封闭渗透效果。