抓斗制作工艺.docx
《抓斗制作工艺.docx》由会员分享,可在线阅读,更多相关《抓斗制作工艺.docx(10页珍藏版)》请在冰豆网上搜索。
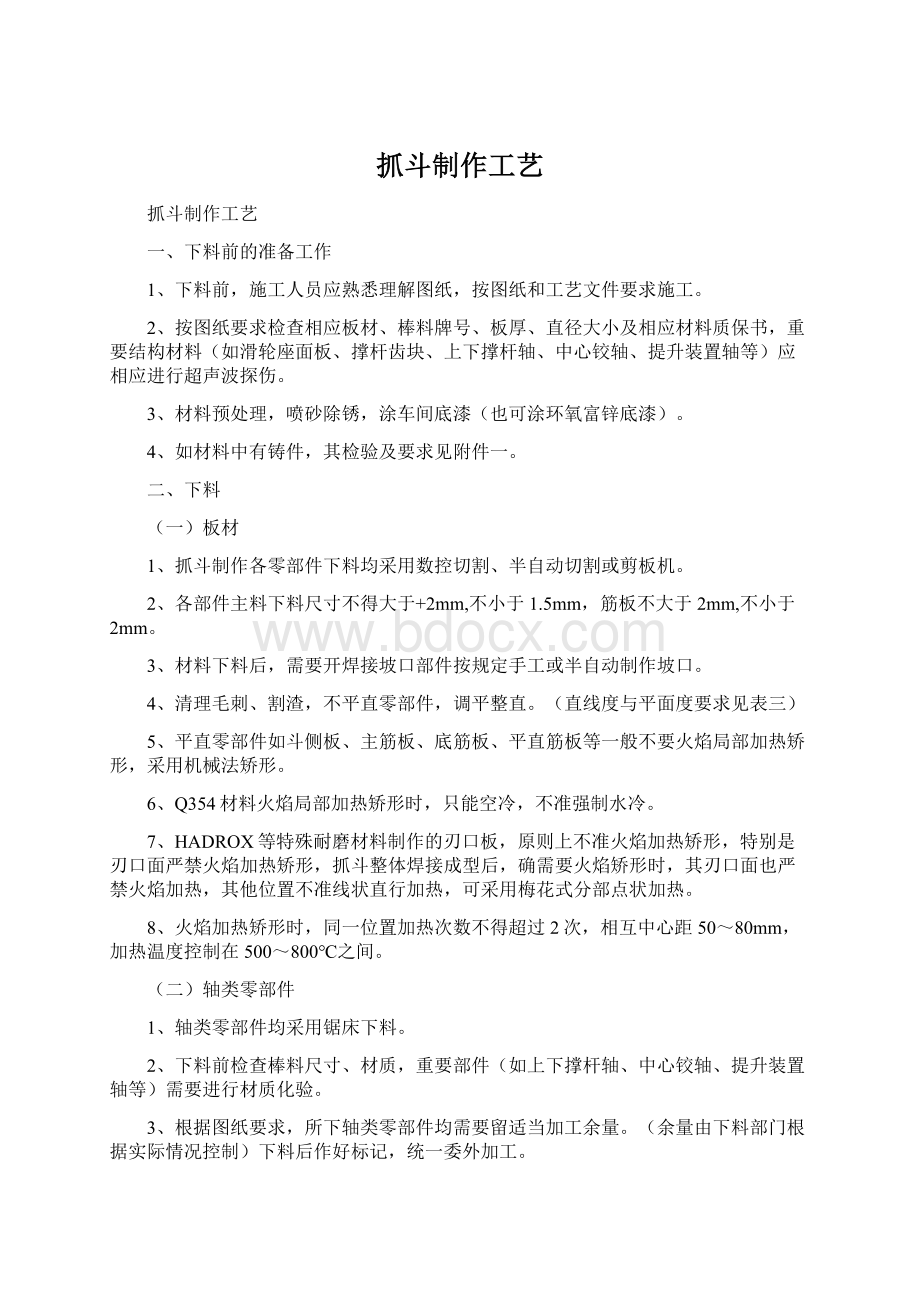
抓斗制作工艺
抓斗制作工艺
一、下料前的准备工作
1、下料前,施工人员应熟悉理解图纸,按图纸和工艺文件要求施工。
2、按图纸要求检查相应板材、棒料牌号、板厚、直径大小及相应材料质保书,重要结构材料(如滑轮座面板、撑杆齿块、上下撑杆轴、中心铰轴、提升装置轴等)应相应进行超声波探伤。
3、材料预处理,喷砂除锈,涂车间底漆(也可涂环氧富锌底漆)。
4、如材料中有铸件,其检验及要求见附件一。
二、下料
(一)板材
1、抓斗制作各零部件下料均采用数控切割、半自动切割或剪板机。
2、各部件主料下料尺寸不得大于+2mm,不小于1.5mm,筋板不大于2mm,不小于2mm。
3、材料下料后,需要开焊接坡口部件按规定手工或半自动制作坡口。
4、清理毛刺、割渣,不平直零部件,调平整直。
(直线度与平面度要求见表三)
5、平直零部件如斗侧板、主筋板、底筋板、平直筋板等一般不要火焰局部加热矫形,采用机械法矫形。
6、Q354材料火焰局部加热矫形时,只能空冷,不准强制水冷。
7、HADROX等特殊耐磨材料制作的刃口板,原则上不准火焰加热矫形,特别是刃口面严禁火焰加热矫形,抓斗整体焊接成型后,确需要火焰矫形时,其刃口面也严禁火焰加热,其他位置不准线状直行加热,可采用梅花式分部点状加热。
8、火焰加热矫形时,同一位置加热次数不得超过2次,相互中心距50~80mm,加热温度控制在500~800℃之间。
(二)轴类零部件
1、轴类零部件均采用锯床下料。
2、下料前检查棒料尺寸、材质,重要部件(如上下撑杆轴、中心铰轴、提升装置轴等)需要进行材质化验。
3、根据图纸要求,所下轴类零部件均需要留适当加工余量。
(余量由下料部门根据实际情况控制)下料后作好标记,统一委外加工。
三、焊接部件制作加工
(一)焊接零部件通用要求
1、组装前,核实需组装材料的尺寸是否符合图纸要求。
2、在平台上划中心线等主要定位尺寸线、轮廓线。
采用划针或石笔划线时偏差见表一:
表一
序号
项目
极限偏差(mm)
1
划针划线
+0.4
2
石笔划线
+0.8
3、组焊,组焊时严格控制尺寸,各尺寸误差均应控制在1mm以内。
4、焊接,焊接时清理好焊口周围油漆、油污、铁锈等物质。
应采用对称焊、反变形、退焊法等焊接方法,减小焊接变形;焊接完成后清理焊熘,药皮,并检查焊缝质量。
5、焊接完成后,振荡时效,减少分散焊接应力。
6、自检、互检、专检后,按公司工件转序制度转入下一工序;转序单中应注明工件名称及相关注意事项,并注明需完工时间。
7、机加工前,对照图纸对工件进行复核。
8、整体进行镗孔或钻孔,加工过程中应加强尺寸检查,防止因夹具变松、刀具磨损而造成工件尺寸超差。
9、未注公差尺寸公差,应符合GB1804-1992中m级的规定(见表二)
未注形位公差的机械加工零件的公差值,应符合GB1184-1996中下列公差值:
a.直线度、平面度未注公差按K级公差值;(见表三)
b.同轴度、圆度、圆跳度未注公差按H级公差值;(见表四)
c.对称度未注公差按L级公差(见表五)
d.平行度、垂直度未注明公差则按K级公差值。
(见表六)
线性尺寸未注公差值表二
公差等级
尺 寸 分 段
m(中等级)
>0.5-3
>3-6
>6-30
>30-120
>120-400
>400-1000
>1000-2000
>2000-4000
±0.1
±0.1
±0.2
±0.3
±0.5
±0.8
±1.2
±2
直线度和平面度未注公差值表三
公差等级
直线度和平面度基本长度的范围
H
~10
>10-30
>30-100
>100-300
>300-1000
>1000-3000
0.02
0.05
0.1
0.2
0.3
0.4
同轴度、圆度、圆跳度未注公差值 表四
公差等级
同轴度、圆度、圆跳度公差值
H
0.1
对称度未注公差值 表五
公差等级
对称度公差基本长度的范围
L
~100
>100-300
>300-1000
>1000-3000
0.6
0.1
1.5
2
平行度、垂直度未注公差值 表六
公差等级
平行度、垂直度基本长度的范围
K
~100
>100-300
>300-1000
>1000-3000
0.4
0.6
0.8
1
10、加工完成后,自检、互检、专检后,按公司工件转序制度转入下一工序;转序单中应注明工件名称及相关注意事项,并注明完工时间。
11、焊接坡口制备应符合国家相应焊接标准GB/T985-1988的有关要求。
图纸上有特殊要求,按图纸要求执行。
(二)提升装置
1、角焊缝,焊缝实行100%磁粉探伤,并应符合JB1965-85《钢制压力容器磁粉探伤》的I级规定。
2、部件质量检验按公司质量管理制度C级要求执行。
(不包含轴套类零件,下同)
(三)头部
1、头部吊耳角焊缝,实行100%磁粉探伤,并应符合JB1965-85《钢制压力容器磁粉探伤》的I级规定。
2、部件质量检验按公司质量管理制度B级要求执行。
(四)横梁
1、滑轮支撑板、横梁面板角焊缝,实行100%磁粉探伤,并应符合JB1965-85《钢制压力容器磁粉探伤》的I级规定。
2、部件质量检验按公司质量管理制度B级要求执行。
(五)撑杆
1、撑杆头进行粗加工,去除氧化皮,焊接在撑杆板上。
撑杆头焊缝100%超生波探伤并应符合JB411-94《锅炉和钢制压力容器对接焊缝》的I级规定。
2、撑杆分别整体镗孔。
杆中心距误差控制在±0.5mm,角度误差控制在±0.1°。
3、将啮合齿焊接在撑杆头上,焊接时采用对称焊等方法以减少变形;啮合齿应进行热处理,以提高齿的机械性能。
齿焊接完成后,两相配合撑杆应啮合灵活无卡齿现象。
4、啮合齿焊缝100%超生波探伤并应符合JB411-94《锅炉和钢制压力容器对接焊缝》的I级规定。
其余角焊缝,焊缝实行25%磁粉探伤,并应符合JB1965-85《钢制压力容器磁粉探伤》的I级规定。
5、部件质量检验按公司质量管理制度A级要求执行。
(六)斗体
1、底板采用卷板机压弧,如底板需分两段压制而成,两板圆弧误差不得大于1mm;两板对接时其高低及相互错位不得超过0.5mm。
2、斗体组装时,两半斗体应相互找平,垂直;组装后,两半斗体相互错位不得超过0.5mm,各对角线误差不超过1mm。
3、组装横梁支撑,其中心铰轴位置及下撑杆轴位置平行度、垂直度对角线误差均执行表二要求。
4、焊接,焊接前将调整好的横梁支撑可靠封死。
焊接按图纸工艺要求进行。
5、对接焊缝实行25%超生波探伤并应符合JB411-94《锅炉和钢制压力容器对接焊缝》的I级规定。
角焊缝实行25%磁粉探伤,并应符合JB1965-85《钢制压力容器磁粉探伤》的I级规定。
6、部件质量检验按公司质量管理制度B级要求执行;中心铰轴孔及下撑杆轴孔按A级要求执行。
7、焊缝探伤检查要求,如图纸有特别要求的按图纸要求执行,如没有,按以上要求执行。
四、轴套类零件加工
1、加工前核对零件标识及相应材质,确保无误后方可工。
2、轴套零件粗车后,热处理。
(热处理按相应热处理规范进行,委外热处理厂家应对热处理质量负责)
3、热处理完成后应对零件硬度及表面淬火层厚度进行检验,淬火层厚度应考虑精加工后尺寸。
4、零件加工表面不应有沟痕,碰伤待损坏零件表面,降低零件强度和寿命的缺陷。
5、零件的尺寸公差,粗糙度等均应符合图样要求,未注公差应符合上表相关要求。
6、毛刺、飞边应除净,铣边、尖角应倒钝。
7、图样上未注形位公差者应符合上表相关要求。
8、如委外加工,提货时应由对方提供相应检验单,并全检或抽检。
9、所有轴套内零件质量检验按公司质量管理制度A级要求执行;
五、组装
(一)组装前准备工作
1、所有零部件须经检验合格,方可进行组装装配。
2、所有外购件须有合格证。
3、零部件装配,总体装配应由具有相当技术水平的熟练工人承担,并必须依照规定的工艺进行。
4、装配场地应整洁有序,不得任意堆放物件。
5、所有零部件的内外表面,在装配前必须清除毛刺、切屑、油污等脏物,互相配合表面应清洗干净,并涂上清洁的油、脂。
6、各零部件的配合面及摩擦面不允许有损伤情况。
如有轻微刻痕,必须修整,且不得影响使用性能。
7、装配前,必须复核相互配合零部件公差,并根据公差进行选配。
8、轴内润滑油孔不得有氧化皮、切屑等杂质,装配前须采用压缩空气法清理。
(二)装配要求
1、螺孔攻丝深度不得小于图纸规定,且不得歪斜,其垂直度误差按表六要求执行。
2、铰制孔的粗糙度应达到图纸规定,其圆度及圆柱度误差不得超过孔的直径公差。
3、各零部件上坚固件不得有松动现象,螺栓 、螺钉应对称地逐步拧紧。
4、螺母拧紧后,螺母及螺栓、螺钉头部与支承面不得有间隙或倾斜,螺栓末端应伸出螺母端面2~3螺距。
5、开口销穿好后,必须将尾部分开,伸出长度不小于开口销直径2倍,分开角度大于90°。
6、零部件装配后,各润滑点注入规定牌号和数量的润滑油、脂。
(三)滑轮装配
外购滑轮质量管理按公司外购件质量管理规定执行。
1、滑轮槽应光滑,装配后不得存在可能损坏钢丝绳的缺陷。
2、滑轮在装配时应注意使滑轮轴上的润滑油孔对准轴承隔套上的油槽,保证润滑状态良好。
3、轴承与滑轮轮毂采用过渡配合,安装时应先将轮毂内壁涂上清洁的润滑油,轴承装入时,应将内圈单挡边向里侧,装好后,轴承空腔2/3以上充满润滑脂。
4、轴承采用机械装置装配时,不得用锤直接击打轴承座圈。
特殊情况下必须用锤击打时,须用铜棒均匀地锤打被装配座圈,不许通过轴承滚动体传递打击力。
5、装配时若图纸无特别规定,则轴承座圈有标号面朝外,以便辩认轴承型号。
6、轴承正常工作情况下,其温升不得超过40℃,最高温度不得超过80℃。
7、轴承与滑轮轴采用间隙配合,装配时应先清除滑轮轴表面毛刺、切屑等,并用压缩空气吹净轴上油孔,然后涂上清洁的润滑油后再装入滑轮轴承。
8、装配好的滑轮,其槽内侧跳动(离槽顶10mm处)δ1和径向跳动δ2应满足δ1≤(3/1000)D;δ2≤(2/1000)D。
(D为滑轮名义直径)
9、滑轮安装时,滑轮外缘与滑轮罩的间隙,如图纸未作规定,一般取(1/3),且不大于10mm(Φ-钢丝绳直径)。
(四)套类零件装配
1、过盈配合的套类零件,在装配前应检查轴与孔尺寸是否符合图纸规定的公差范围。
2、套类零件装配时优先采用温差法装配,其装配应严格按相应工艺文件进行。
3、套类零件装配完成后,其头部不得突出端面。
(五)钢丝绳安装
1、钢丝绳的型号、规格和长度应按图纸要求查验,确认符合要求后方可使用。
钢丝绳禁止拉长使用。
2、钢丝绳开卷时,不允许打结或扭曲。
钢丝绳切断时不允许绳股散开。
3、钢丝绳应保持良好的润滑状态,所用的润滑剂应符合规定并不影响外观检查。
4、钢丝绳端部采用绳夹连接时应符合表七及图一要求:
绳夹数目 表七
钢丝绳直径(mm)
≤19
19~27
28~37
38~45
44~56
绳夹数量(个)
3
4
5
6
7
图一
5、绳夹夹紧程度以“U”型螺栓将钢丝绳直径压缩1/3为止,钢丝绳受力后再旋紧一次。
6、用楔套连接时,其连接方式如图二:
图二
(六)整体组装
1、各部件全部装配完成无误后,整体组装。
2、清理检查中心铰轴及油孔,清理横梁支撑孔并测量轴孔配合尺寸,确保轴孔在配合公差范围内;并在轴及孔内涂一层清洁油。
3、吊车配合将横梁吊至安装位置,仔细调整,将中心铰轴装配到位并用紧定螺钉紧固。
4、焊接限位块。
5、检查清理上下撑杆轴,测量相应轴孔尺寸,确保配合无误。
6、将撑杆装入头部铰座处,四根撑杆相互啮合转动应灵活,啮合齿之间应加入适当的润滑油。
7、吊车配合将头部吊至安装位置(撑杆应已装配完成),将撑杆分别装入斗部相应铰轴位置处,穿入下撑杆轴,撑杆头在下铰座位置两边间隙应相等。
8、中心铰轴、下撑杆轴安装时,不允许对相应轴、孔进行打磨处理;撑杆安装应在自然状态,不允许在受力犯别状态下安装。
9、相应螺栓安装紧固后,将抓斗打开,焊接相应限位块。
10、各润滑点加注润滑油。
11、组装完成后,斗体相互错位不得超过2mm,刃口间隙在抓斗闭合时不得大于2mm;抓斗重心应与提升中心一致,各位置不得出现相互干涉现象。
12、开合试验,试验前应仔细检查,确保安全后方可进行;试验时,抓斗应能顺利开合无异响;试验应进行不少于10次。
六、涂装
1、清理焊口及破损部位铁锈,清理油污。
2、焊口及破损部位补涂环氧富锌底漆。
3、补涂底漆干透后,涂环氧云铁底漆,两遍底漆干膜厚度不少于80μm。
4、喷涂氯化橡胶桔红面漆。
5、涂装完成后,干膜总厚度不少于130μm。
6、以上为公司生产抓斗涂装要求,如用户有特殊要求,按用户要求执行。
附件一:
铸造件检验及质量控制标准
一、铸造材料应符合GB11352-1989《一般工程用铸造碳钢》的规定,检验试样按相应国标规定执行。
二、如铸造件图样没有标准尺寸公差时按表一、表二执行:
毛坯件未注尺寸公差 表一 mm
毛坯件基本尺寸
公差
≤100
±2.5
>100~160
±3.5
>160~250
±4
>250~400
±6
>400~630
±7
>630~1000
±8
>1000~1600
±9
>1600~2500
±10.5
铸件未注壁厚尺寸公差 表二 mm
壁厚基本尺寸
公差
>20~40
±3
>40~80
±5
>80~160
±6
>160~315
±8
注:
表一、表二中基本尺寸包括加工余量、拔模斜度。
三、铸件铸造完成或粗加工后应进行检查,不允许有超过表三所列许用值,如超过应进行修补以排除缺陷。
表三
夹砂
当长度≤2mm时,在直径为50mm的圆内不得超过2个,在20mm间距内无其它缺陷。
渣眼
气孔
缩孔
当长度≥2<4mm时,在直径为50mm的圆内不得超过1个,当长度<2mm时,在直径为50mm的圆内不得超过2个。
收缩裂缝
不允许
结疤
<15mm且在直径为50mm的圆内不得超过1个。
错箱
当铸件重量<50kg,不大于1mm;当铸件重量>50~500kg,不大于2mm;当铸件重量>500kg,不大于3mm
四、如发现铸件有超过规定缺陷,可用砂轮打磨或把缺陷完全清除后,用同母材强度相等的焊条补焊,经确认无缺陷后,退火处理。
五、铸件机加工后,加工面不允许有裂纹、气孔、针孔、夹砂。
如发现有以上缺陷,确认不影响使用的可采用如下方法进行修补:
1、用砂轮进行修补,修补后表面粗糙度必须达到图样规定要求。
2、修补缺陷深度不得超过0.05t(t为直径或壁厚),最大不得超过2mm;修补的凹坑半径应为缺陷深度2倍以上;凹坑应平滑过渡不得呈尖棱状。
修补后须经磁粉探伤或液体渗透法对铸件进行检验,确认缺陷已完全排除后方可使用。