质量工程课设设计指导.docx
《质量工程课设设计指导.docx》由会员分享,可在线阅读,更多相关《质量工程课设设计指导.docx(35页珍藏版)》请在冰豆网上搜索。
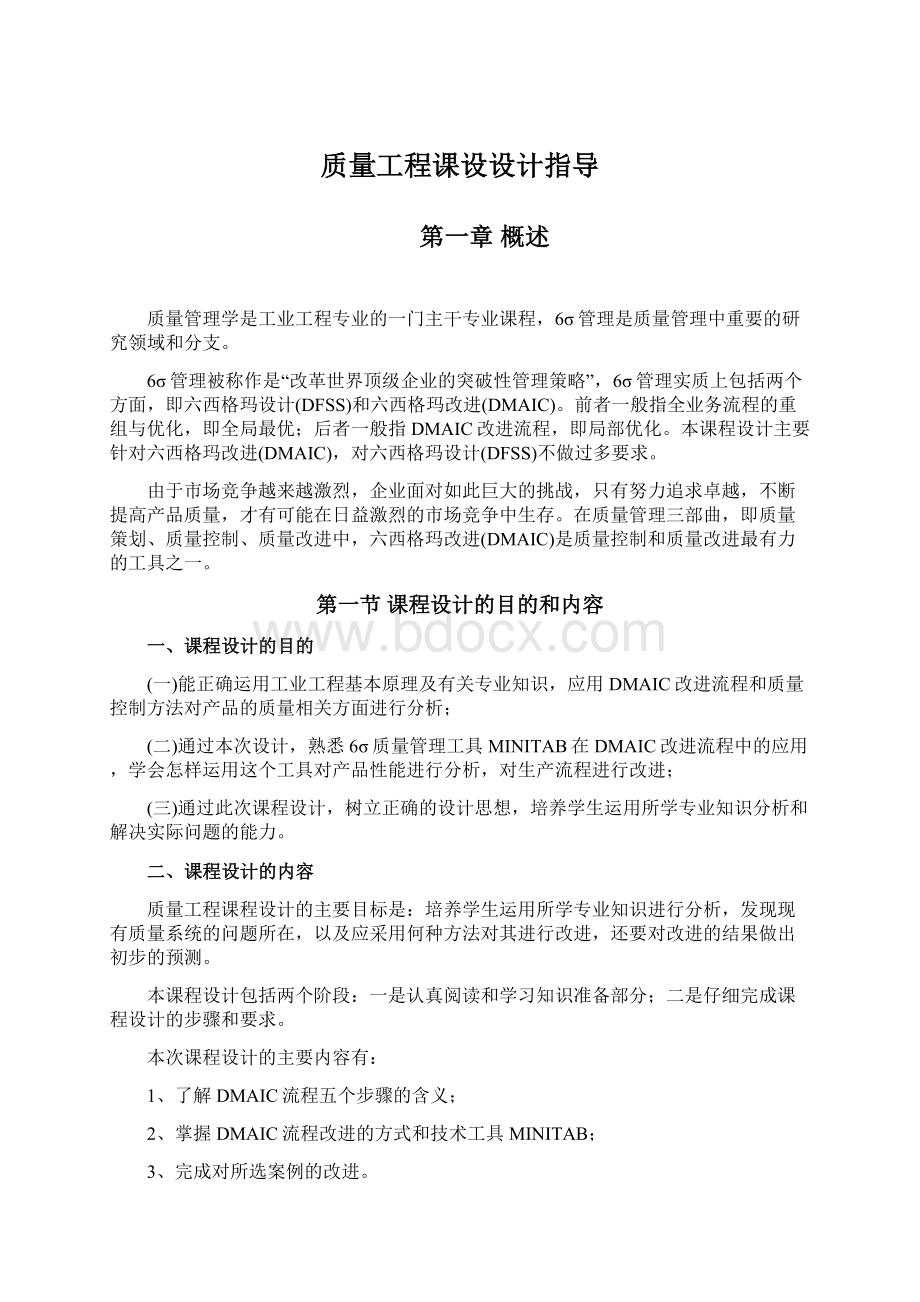
质量工程课设设计指导
第一章概述
质量管理学是工业工程专业的一门主干专业课程,6σ管理是质量管理中重要的研究领域和分支。
6σ管理被称作是“改革世界顶级企业的突破性管理策略”,6σ管理实质上包括两个方面,即六西格玛设计(DFSS)和六西格玛改进(DMAIC)。
前者一般指全业务流程的重组与优化,即全局最优;后者一般指DMAIC改进流程,即局部优化。
本课程设计主要针对六西格玛改进(DMAIC),对六西格玛设计(DFSS)不做过多要求。
由于市场竞争越来越激烈,企业面对如此巨大的挑战,只有努力追求卓越,不断提高产品质量,才有可能在日益激烈的市场竞争中生存。
在质量管理三部曲,即质量策划、质量控制、质量改进中,六西格玛改进(DMAIC)是质量控制和质量改进最有力的工具之一。
第一节课程设计的目的和内容
一、课程设计的目的
(一)能正确运用工业工程基本原理及有关专业知识,应用DMAIC改进流程和质量控制方法对产品的质量相关方面进行分析;
(二)通过本次设计,熟悉6σ质量管理工具MINITAB在DMAIC改进流程中的应用,学会怎样运用这个工具对产品性能进行分析,对生产流程进行改进;
(三)通过此次课程设计,树立正确的设计思想,培养学生运用所学专业知识分析和解决实际问题的能力。
二、课程设计的内容
质量工程课程设计的主要目标是:
培养学生运用所学专业知识进行分析,发现现有质量系统的问题所在,以及应采用何种方法对其进行改进,还要对改进的结果做出初步的预测。
本课程设计包括两个阶段:
一是认真阅读和学习知识准备部分;二是仔细完成课程设计的步骤和要求。
本次课程设计的主要内容有:
1、了解DMAIC流程五个步骤的含义;
2、掌握DMAIC流程改进的方式和技术工具MINITAB;
3、完成对所选案例的改进。
第二节课程设计的组织和进度
一、课程设计的组织
课程设计将把每班参加训练的学生分成6-7组,每组4人,要求在小组内分工协作、充分讨论、相互启发的基础上形成设计方案,课程设计结束要求各组提交相关资料和文件,必要时可要求各小组选出一个代表,进行课程设计方案演示和答辩,评出若干优秀设计成果。
具体要求为:
①设计过程以小组为单位,各组人员按职能划分,相关人员负责组织和协调本小组的讨论、任务分工等;
②设计过程必须在本组内独立完成,不得跨组参考或抄袭,避免方案出现雷同;
③课程设计原则上在十天内做完;
④第十天进行课程设计的答辩与优秀设计方案评选,在各组推选代表进行方案介绍的基础上,推选出2-3个优秀设计方案。
二、课程设计的进度
本课程设计计划用10天(2周)的时间完成,其中有些任务安排在固定的时间进行,其余任务和进度由各小组以半天为单位自行安排。
第三节课程设计的考核和评分
一、考核
课程设计的考核方式为小组代表答辩。
学生按照设计任务书的规定要求完成设计任务,提交完整的技术资料,并经指导教师审核签字同意后,在规定的时间内进行答辩。
答辩小组由教研室组织,以指导教师为主,总人数不少于3人。
答辩时,学生自述主要设计内容不超过10min,然后回答答辩小组成员提出的问题。
每组学生的答辩时间一般控制在20min以内。
二、评分
按照每组学生在课程设计中的表现、相关资料质量及答辩情况,课程设计成绩按优、良、中、及格和不及格记分。
具体成绩评定标准如下:
优秀:
能全面完成课程设计任务,工作量较大,设计质量高,分析计算准确,观点和结论正确,能够提交完整的技术资料,课程设计报告不少于5000字,答辩表述正确,回答问题正确,答辩成绩为优秀以上。
良好:
完成规定的课程设计任务,设计质量好,分析计算正确,观点和结论正确,能够提交完整的技术资料,课程设计报告质量较高,答辩表述清楚,回答问题正确,答辩成绩为良好以上。
中等:
基本完成课程设计任务,设计质量好,分析计算基本准确,观点和结论基本正确,能够提交的技术资料,课程设计报告符合要求,答辩表述较清楚,主要问题回答正确,答辩成绩为中等以上。
及格:
尚能完成课程设计任务,工作量达到最低要求,分析计算一般,提交技术资料,课程设计报告符合质量基本要求,答辩表述基本清楚,主要问题回答基本正确,答辩成绩为及格以上。
不及格:
有下列之一者,评为不及格:
1)没有完成课程设计任务
2)工作态度马虎、潦草,设计质量差,不能达到专业课程设计任务书的基本要求
3)提交的技术资料有严重错误
4)答辩中概念模糊,主要问题回答错误
5)经常缺勤,严重违反纪律
6)答辩成绩为不及格
注意事项:
课程设计期间,学生可以以小组为单位组织讨论、分析,但不允许抄袭。
指导教师应按有关要求到设计现场指导和答疑。
第二章任务和要求
第一节课程设计任务书
一、设计题目
抛射器的性能设计与改进
二、设计依据
1、六西格玛改进流程DMAIC步骤及要求(见第三章);
2、六西格玛改进流程DMAIC案例。
三、设计内容
根据给定的抛射器设计和制作要求,六西格玛改进流程DMAIC步骤及要求,及其相关案例,定义相关的性能指标,建立性能的测量方法,分析影响性能的原因,找出因素的最优设置,设计抛射器技术要求,对产品的质量进行抽样和控制评价。
第二节课程设计的要求
6σ流程DMAIC设计步骤及要求
预备阶段:
学习材料。
学习课程设计所提供指导书,理解并消化相关知识点的内容,仔细阅读相关的案例,仿照案例的步骤和格式进行课程设计工作,包括项目名称,日期,成员,分工,进度,目标等。
第一步:
定义阶段。
讨论并界定抛射器的主要性能指标及其评价标准,确定顾客的关键需求并识别需要改进的产品或过程,将改进的项目奠定在合理的基础上。
第二步:
量测阶段。
对于所界定的性能指标及其评价标准,设计出相关的测量方法。
测量现有过程,确定过程的底线与期望值,并对测量系统的有效性、重复性和再现性进行评价。
第三步:
分析阶段。
讨论可能影响性能指标的因素,并运用质量管理工具对这些因素进行分析,确定其中的关键因素。
第四步:
改进阶段。
对于确定的关键因素,使用质量管理工具找出并检验其最优水平,以减少过程的缺陷或变异,并设计抛射器技术要求;
第五步:
控制阶段。
按照设计的技术要求,对产品的质量进行抽样和控制评价。
第六步:
工作总结。
对上面所作的工作及其结果进行详细的分析和总结。
第三章六西格玛改进流程DMAIC
第一节概述
进行6σ管理本身就是一个过程的实现,它有自己明确的工作流程。
它包括6σ设计和6σ改进这两个基本流程。
6σ设计简记为DFSS(DesignForSixSigma),它是对一个新过程的实现步骤、方法等的全面规划。
6σ改进简记为DMIAC,是对已有过程的优化和保持,他具体包括五个流程,即界定(Define)、量测(Measure)、分析(Analyze)、改进(Improve)、控制(Control)。
过程6σ管理,从对过程的设计开始,通过界定、量测、分析、改进这四个流程,最终回到对过程的控制。
这是6σ管理活动的一个周期。
之后对过程的再设计,持续的过程改进,以及更高层次的过程控制。
一、界定阶段D
界定阶段(Define)是6σ项目DMAIC过程的第一个步骤,它确定顾客的关键需求并识别需要改进的过程。
要为项目正式启动做好工作,必须明确这些问题:
(1)如何选择与确定项目?
(2)如何分析项目?
(3)如何描述项目?
而同时这些问题也正是界定阶段的基本任务。
1.选择项目
(1)项目的来源
外部信息来源,包括:
顾客意见,市场调查,竞争对手。
内部信息来源,包括:
质量分析报告,质量审核报告,财务分析报告,企业方针目标诊断报告。
(2)项目的分布规律
质量缺陷类项目,资源效率类项目,顾客抱怨类项目。
2.项目确定
(1)项目选择原则
三“M”原则:
Meaningful(有意义的),Manageable(可管理的),Measurable(可测量的)。
SMART原则:
S,Simple(简单明了);M,Measurable(可量化的);A,Agreedto(达成一致意见);R,Reasonable(合理考虑先进性和成功的可能性);T,Time-based(在一定时间内完成)。
(2)项目评价标准
顾客满意;过程能力;劣质成本;增值能力。
(3)确定项目
项目选择矩阵,项目选择过程中使用的评价因素表(表2-6),使用此表可以增加对6σ项目选择的正确性。
表2-6评价因素表
项目评估矩阵
资料可利用性
资源可利用性
项目时间
质量定义
投资回报
成功机会
目标CTQ
合计
重要性评分
1-5级
1-5级
1-5
1-5
1-5
1-5
1-5
顾客满意过程能力劣质成本增值能力
合计
(4)项目评估
好项目的特征:
是一个重复发生的事件或过程;问题范围相对集中;能够量化为测量指标;过程处于受控状态,需要提高过程能力;项目对顾客有一定影响;与公司战略目标紧密相连;项目的积极效益比较客观;突破性的改进——减少70%的缺陷。
不作为项目的特征:
项目范围太广;十分简单并且知道答案的问题;技术难度很大,完成把握很小;长期发展项目。
1.项目分析
项目的选择和确定必须建立在分析的基础上,一般从顾客需求分析,流程分析,劣质成本分析进行分析。
(1)顾客需求分析
a.顾客需求:
产品和服务需求;输出需求
b.确定关键质量特性
c.SIPOC分析:
SIPOC是供方,输入,过程,输出和顾客的第一个英文字母的缩写,它可以表示一个业务过程或产品实现过程中主要活动或子过程,以此来确定关键输入变量和关键输出变量。
(2)流程分析
掌握过程是构建向顾客传递价值的竞争优势的途径。
利用流程图来说明产品(服务)形成全过程,为了说明过程所有可能的波动偏差,应把所有人力资源、文件、程序方法、设备、零部件和测量一起都包括在过程的说明中。
(3)劣质成本分析
每个企业都有成本核算,从这个意义上说,只要项改进业绩,不断减少质量成本占销售额的比率,6SIGMA管理就是一个务实、有效的途径。
劣质成本包括:
预防成本(不增值部分),鉴定成本(纠正措施等),故障(损失成本)(内部故障+外部故障)。
2.项目描述
问题的陈述原则:
具体的,明确地解释有什么不对;可观察的,描述问题可见的迹象;可测量的,以定量的术语指明问题的范围;可控的,问题的影响有多大。
二、量测阶段M
通过现有过程的评估确定问题分析的焦点和范围(称为基线评估),识别影响过程输出y的几个重要的输入xi,并对量测系统的有效性进行评价。
这一阶段有两个主要目的:
一是收集数据,确认问题和机会并进行量化;二是梳理数据,为查找原因提供线索。
它的基本任务是:
选择评价指标;确定测量对象并策划数据收集方案;验证测量系统。
1.评价指标有DPU(单位产品缺陷数)、DPMO(百万机会缺陷数)、RTY(流通合格率)和过程能力指数。
2.在数据收集的策划过程中应该注意:
样本量;时间范围;其他因素,批次、抽样频率、班次、班组、机器等。
3.一个好的测量系统的基本要求:
有足够的分辨力;在规定的时间内要保持统计稳定性;要具有线性性。
三、分析阶段A
通过数据分析确定影响输出y的少数几个重要的输入xi。
这个阶段是最难预见的阶段,在这一阶段不仅仅是寻找原因,在罗列原因的基础上,还要确认关键原因以及这些原因如何被证实。
我们把分析阶段的主要流程和使用的工具用一个循环图(图2-2)来表示,连续进行循环分析,不断地确认或拒绝原因假设,直到识别出关键的原因并被数据证实为止。
以下的这些统计工具在后面将会介绍如何使用,有些在其他课中已经有所了解了。
主要的流程主要使用的统计工具
寻找问题的原因
————————
头脑风暴法,因果图
确定关键原因
————————
排列图,散布图,FMEA
验证分析原因
————————
假设检验,方差分析
图2-2分析阶段的循环图
四、改进阶段I
通过几个重要的输入xi的改进,寻找优化过程输出y的方案,是过程的缺陷或变异降低。
改进阶段的步骤:
(1)寻找解决问题的改进措施,提出改进建议、目标和方法,应用头脑风暴法集思广益,并充分应用统计技术、方法,提高解决问题的效率和效果。
(2)对改进方案进行综合比较分析,从中挑选优化的方案。
(3)对改进方案进行验证,确认有效性后努力实施取得成效。
(4)精心设计策划,估计可能出现的困难和阻力并加以克服。
五、控制阶段C
对改进的过程程序优化,并采用有效的监控方法保持过程改进的成果,使过程持续运行在新的高水平上。
控制阶段常用的工具和技术有过程控制计划、标准操作程序、防错法、过程能力分析、控制图等。
这些工具需要结合使用,已达到最好的效果。
通过一段时间的控制,可以发现过程中的新问题,对这些新发现的问题需要寻找过程异常的原因。
消除异常原因的最佳方法是进行新的过程改进。
所以过程控制与过程改进是密切相关的,过程控制即是过程改进的结果,也同时是过程改进的起因。
控制阶段的基本任务:
(1)证实结果是真实的,确实是通过努力,消除了缺陷的根本原因,而不是转嫁矛盾;
(2)证实改进是值得的,应考察其财务效果;(3)保持过程长期稳定,通过运用控制图方法和防差错技术,监控过程,预防差错,使改进后的过程处于受控状态,保持长期稳定;(4)巩固项目成果实现持续改进,建立文件化和标准化的控制体系,有效实施现场管理,实现持续改进;(5)关闭项目,提交报告。
第二节寻找质量问题的几个直观工具
一、调查表(CheekSheet)
调查表又叫检查表,是用来系统地收集数据,发现过程的缺陷,以便做量化分析的工具。
常用的调查表有记录调查表、分布调查表、缺陷位置调查表和缺陷原因调查表(本设计对记录调查表、缺陷调查表和分布调查表进行详细介绍,其他的内容请参阅参考书目)。
(一)记录调查表
记录调查表也称为不合品项目调查表。
它可以记录一段时间内某几项特征出现的频数,或者是抽查的几批同型产品中各种缺陷出现的频次。
例2-1表2-7是某印刷厂成品臭氧检验中对书籍装订印刷不合格项目的累计值的调查表,装订印刷错误主要集中在字迹不清、页面有污点和纸张折叠上,在提高书籍印刷质量、降低不合格频率的过程中应优先考虑解决这些问题。
表2-7装订印刷错误记录调查表
错误类别
时间
合计(n=23164)
1
2
3
……
封皮破损
1
0
2
……
15
装订松脱
2
1
0
……
8
字迹不清
10
9
7
……
89
色泽不均
1
3
2
……
10
页面污点
4
6
3
……
40
纸张折叠
2
2
3
……
31
有缺页
1
1
0
……
7
合计
21
22
17
……
200
(二)分布调查表
分布调查表有时也被称为质量分布调查表或生产工序检验表,用以记录产品的某一项质量特性值的分布情况。
分布调查表根据历史资料,将数据分布范围分成若干等距的区间并作为横轴,同时纵轴以5为间隔制成表格,供调查记录时使用。
分布调查表与直方图很相似,所不同的是直方图是根据已有数据合理分组,然后制图,而分布调查表是根据经验事先分组并制好表格,然后供现场记录。
例2-2表2-8是某零件直径的分布调查表。
该零件直径的合格范围是0.97cm~1.04cm,此次共抽检了142个零件的直径,将其逐一记录在所在区间,如图所示。
根据质量分布调查表的显示,很容易判断抽检的142个零件的直径服从正态分布,其中有3个不合品,不合格品率为2.11%。
表2-8零件直径分布调查表
规格(cm)
下公差线
2
上公差线
5
5
5
4
5
5
5
5
5
5
1
5
5
5
5
3
5
5
5
5
5
4
2
5
5
5
5
5
5
5
1
频数
0
2
8
11
24
37
30
20
9
1
累计频数
0
2
10
21
45
82
112
132
141
142
(三)缺陷原因调查表
缺陷原因调查表也被称为矩阵调查表,用来查明缺陷产生的原因。
该调查表也要求是先确定好缺陷的种类和代表符号,然后把生产过程对应的设备、操作人员和工作时间等分别作为横栏和纵栏的标题,调查时在交叉栏上记录出现的各种缺陷及其数量。
例2-3表2-9是某玻璃制品厂的两个生产小组生产的玻璃杯的质量缺陷原因调查表。
对某星期连续五个工作日生产的玻璃杯的抽检中,这两个小组分别出现的错误种类及数量如调查表所示。
可以看出小组1生产的玻璃杯常出现的缺陷是有气泡,而小组2的设备清洁工作做得不好。
用调查表收集到的是最原始的数据,有些数据要对其进行整理、加工,以得到更直观有效的信息。
绘制统计图是对数据进行加工的一种简单方式,好的统计图可以让使用者直观、快速、准确地得到有用的信息。
下面将会介绍几种寻找质量问题时常用到的统计图。
表2-9玻璃杯缺陷原因调查表
小组
工作日
1
2
3
4
5
1
○Х☆○
○Ⅹ○
◇☆☆○
○○Ⅹ●
☆○●○
◇○☆○
Ⅹ○○
◇○☆●
○○
●◇○○
○◇○
2
●ⅩⅩ
◇○●○
●☆
◇☆○●
○●●
●◇●
●☆○●
●
○气泡●色斑◇外形不整Х刮痕☆裂痕
二、排列图(ParetoChart)
排列图是寻找“关键的少数”缺陷的有效工具,是“二八原理”在质量管理中的应用。
多数的质量损失是有少数几种缺陷造成的,因而改进质量的最重要的工作就是减少“关键的少数”缺陷。
排列图也称为帕雷托图、巴雷特图、柏拉图,在质量管理过程中被用来发现多种缺陷中的“关键的少数”缺陷,以便抓住主要问题,优先解决。
一般的情况时,把发生率高的缺陷减少一半要比把发生率低的项目完全消除更为容易。
例如装订图书可能会发生缺页和错页两种缺陷,统计表明,缺页出现的频率为80%,而错页出现的频率只占20%,作为质量主管,你有两种方案选择。
第一方案:
致力于减少缺页;第二方案:
致力于消除错页。
你可能会想,错页出现的频率少,更容易解决,所以选择第二方案,但是这是一个错误的决策。
正确的决策应该是选择第一方案,你会发现这是一个事半功倍的方式。
(一)排列图的结构
排列图由一个横坐标轴、两个纵坐标轴、一系列由高到低相邻排列的长方形和一条累计百分比的折线组成。
其中,横坐标是缺陷种类,是按缺陷出现的频次高低由左到右依次排列的,左纵坐标轴是缺陷出现的频数,右纵坐标轴为0~100的百分比刻度。
也可以把左纵坐标轴取作质量损失,这时横坐标轴的缺陷顺序是按各种缺陷总损失的大小从左到右依次排列的。
根据用途,排列图可以分为分析现象用排列图和分析原因用排列图。
(1)分析现象用排列图与不良结果有关,用来发现主要现象,但是并不能解释现象出现的原因,需要进一步分析。
不良结果主要出现在质量、成本、交货期和安全等方面,比如可以据排列图确定产品的哪些不合格现象更经常发生,或确定顾客抱怨的主要方面是什么。
(2)分析原因用控制图与过程因素有关,这些过程因素包括操作者、机器、原材料和作业方法等。
两种排列图只是在用途上稍有不同,在原理和绘制方法上完全相同。
例2-4图2-3是根据表2-7“装订印刷错误记录调查表”绘制的,由排列图可以得到比记录调查表更详细的信息。
从图中可知,最主要的错误是字迹不清,占全部错误的44.5%;其次是页面污点错误,占20%;再次是纸张折叠问题,这三项错误共占全部错误的80%。
图2-3书籍装订印刷错误排列图
用排列图发现主要的缺陷后,再根据因果图寻找产生这种缺陷的原因,消除或控制住这种原因,就能把这种原先的主要缺陷出现的频数大幅度降低,这时它的出现频率已经降低到第二位甚至更低。
然后对改进后的过程重新收集数据做记录调查表,并按照新的缺陷排列顺序制作新的排列图,使前后两张排列图左纵坐标轴刻度保持一致,这样就可以通过比较两张排列图得出改进所提高的效率。
如例2-5印刷厂运用因果图等方法后发现,造成字迹不清的原因是纸张湿度过高和印刷机保养不当等,采取措施改进后,对产品再次抽检,记录错误类别及发生频次。
为便于比较,前后抽检的样本量要相等。
根据新得到的数据做新的排列图,并通过调整使纵坐标轴与改进前的相同,从而得到改进后的排列图(图2-4)。
图2-4修改前后的排列图比较
比较观察两张排列图的累计折线图,即可得知采取的改进措施对提高装订印刷质量的确有帮助,消除的缺陷数目大约是改进前缺陷总数的30%。
Minitab软件绘制排列图的方法:
首先将表2-7的错误类别和合计值输入到Minitab表格中去,然后按Stat>QualityTools>ParetoChart…的顺序打开ParetoChart对话框;单选ChartDefectsTable,然后在LabelsIn栏目中选择错误类别变量,在FrequenciesIn中选择频次值,根据需要在CombineDefectsAfterTheFirst-%IntoOne中键入80或者90等,表示当累计错误百分比达到该要求后,其他错误因素就计入Other项;最后在Title中输入排列数的名字,点击OK键即可得到排列图。
三、因果图(Cause-and-Effect)
因果图又叫鱼刺图、树枝图、石川图,是1953年日本东京大学教授石川馨提出来的,用于系统地寻找产生某种过程缺陷的各种可能的影响原因,从而寻找质量改进的措施。
因果分析图能把问题的可能原因整理为清晰的逻辑组合。
在绘制因果图之前,有一组熟悉问题的成员使用头脑风暴法共同探讨,尽可能全面的搜集影响因素,然后将其分门别类并做图,进行系统的分析。
由于因果分析是小组的共同工作,因此组长的作用很重要。
组长要给小组提供必要的、关于所要解决问题的信息,指导小组按规定的程序分析问题,指导小组进行自由讨论直到所有可能的原因都被提出,鼓励成员结合别人的意见提出进一步的设想,激励小组成员的创造性思维等等,最重要的是要鼓励成员提出自己的观点,而不能批评任何不可思议的设想。
因果分析的基本程序为:
1、叙述问题;
2、确定主要分支;
3、自由讨论;
4、确认最有可能的原因;
5、确定最有可能/最易证明的原因;
6、采取改正措施;
7、用实验证明。
因果图的结构:
因果图由一个主轴和几个分支组成,当原因很多且可以归纳为几大类时,也可以在主要分支下再画分支。
主轴指向是待分析质量问题,几个分支则代表几类可能的影响因素。
过去把影响因素归结为人、机、料、法、环五大因素。
Minitab中归结为人为、设备、材料、方法、量测和环境。
6σ质量管理中将主要影响因素归为六大类,称为6M,即人力、机械、物料、方法、量测和环境。
例2-6某银行发现其各营业网点的顾客人数都在不断地减少,为了增加顾客流量,提高其在行业中的竞争能力,该行成立6σ质量管理小组来寻找