铸造用呋喃树脂砂.docx
《铸造用呋喃树脂砂.docx》由会员分享,可在线阅读,更多相关《铸造用呋喃树脂砂.docx(13页珍藏版)》请在冰豆网上搜索。
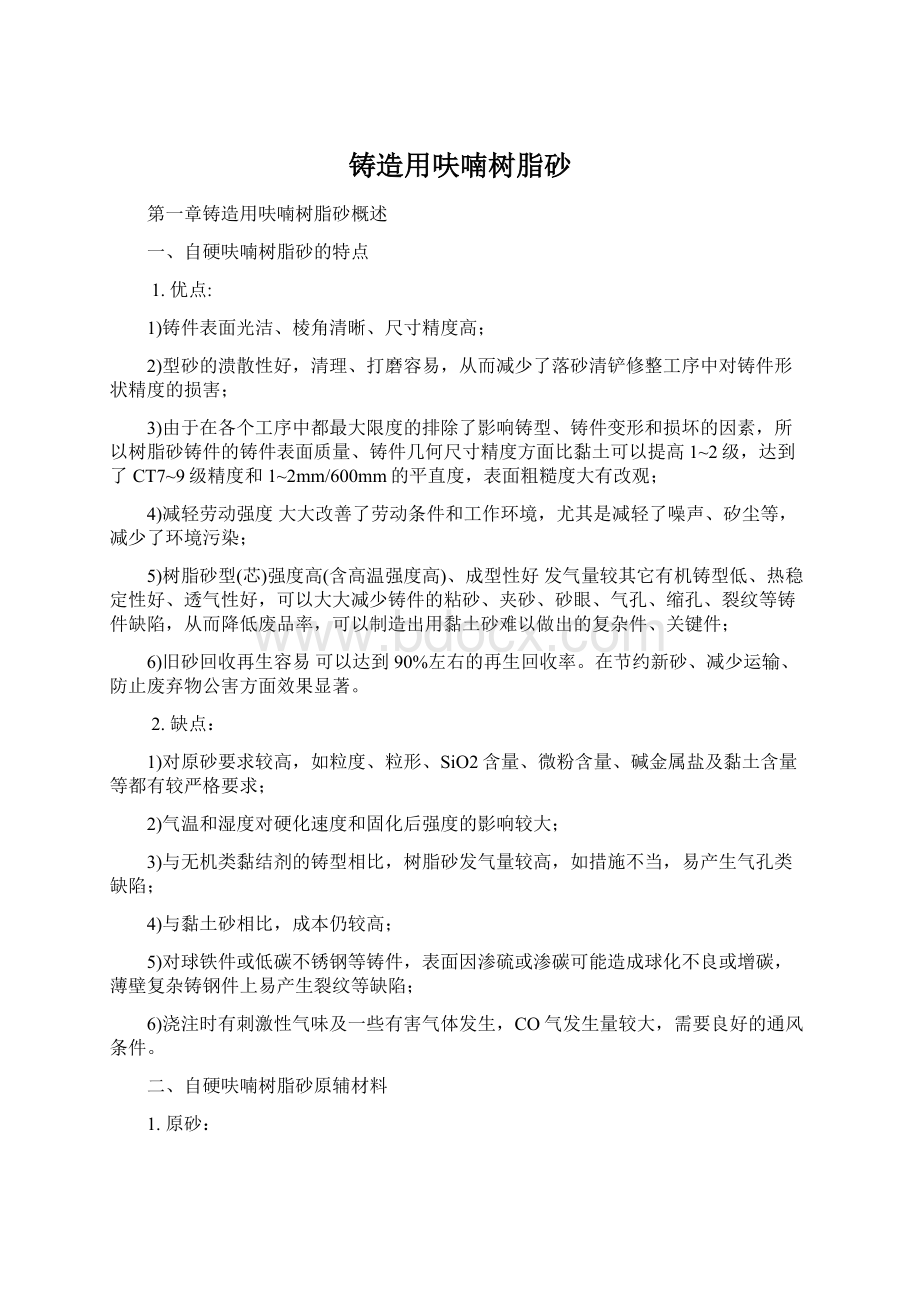
铸造用呋喃树脂砂
第一章铸造用呋喃树脂砂概述
一、自硬呋喃树脂砂的特点
1.优点:
1)铸件表面光洁、棱角清晰、尺寸精度高;
2)型砂的溃散性好,清理、打磨容易,从而减少了落砂清铲修整工序中对铸件形状精度的损害;
3)由于在各个工序中都最大限度的排除了影响铸型、铸件变形和损坏的因素,所以树脂砂铸件的铸件表面质量、铸件几何尺寸精度方面比黏土可以提高1~2级,达到了CT7~9级精度和1~2mm/600mm的平直度,表面粗糙度大有改观;
4)减轻劳动强度大大改善了劳动条件和工作环境,尤其是减轻了噪声、矽尘等,减少了环境污染;
5)树脂砂型(芯)强度高(含高温强度高)、成型性好发气量较其它有机铸型低、热稳定性好、透气性好,可以大大减少铸件的粘砂、夹砂、砂眼、气孔、缩孔、裂纹等铸件缺陷,从而降低废品率,可以制造出用黏土砂难以做出的复杂件、关键件;
6)旧砂回收再生容易可以达到90%左右的再生回收率。
在节约新砂、减少运输、防止废弃物公害方面效果显著。
2.缺点:
1)对原砂要求较高,如粒度、粒形、SiO2含量、微粉含量、碱金属盐及黏土含量等都有较严格要求;
2)气温和湿度对硬化速度和固化后强度的影响较大;
3)与无机类黏结剂的铸型相比,树脂砂发气量较高,如措施不当,易产生气孔类缺陷;
4)与黏土砂相比,成本仍较高;
5)对球铁件或低碳不锈钢等铸件,表面因渗硫或渗碳可能造成球化不良或增碳,薄壁复杂铸钢件上易产生裂纹等缺陷;
6)浇注时有刺激性气味及一些有害气体发生,CO气发生量较大,需要良好的通风条件。
二、自硬呋喃树脂砂原辅材料
1.原砂:
原砂品质对树脂用量,树脂砂强度以及铸件质量影响很大,某些工厂由于忽视对原砂质量的严格要求,给生产带来很多麻烦。
表1列举了不同大小和材质的铸件采用原砂的技术指标。
表1树脂自硬砂用原砂的技术指标(质量分数,%)
种类
粒度
(筛号)
SiO2
含泥量
含水量
微粉量①
酸耗
值/mL
灼烧
减量
适用范围
材质
铸件类型
特种砂
见其它特种砂为原砂的型砂和芯砂部分
特种钢
各类铸件
硅砂
30/50
>97
<0.2
<0.1~0.2
<0.5~1
<5
<0。
5
铸钢
重大型及大型热
节铸件
硅砂
40/70
>97
<0.2
<0.1~0.2
<0.5~1
<5
<0。
5
硅砂
40/70
>96
<0.2
<0.1~0.2
<0.5~1
<5
<0。
大中型热节铸件
硅砂
50/100
>96
<0.2~0.3
<0.1~0.2
<0.5~1
<5
<0。
5
中小型铸件
硅砂
40/70
>90
<0.2
<0.1~0.2
<0.5~1
<5
<0。
5
铸铁
重大及大型铸件
硅砂
50/100
>90
<0.2~0.3
<0.1~0.2
<0.5~1
<5
<0。
5
硅砂
50/100
>90
<0.2~0.3
<0.1~0.2
<0.5~1
<5
<0。
5
一般铸件
硅砂
100/200
>90
<0.3
<0.1~0.2
<0.5~1
<5
<0。
5
硅砂
70/140
>85
<0.2~0.3
<0.1~0.2
<0.5~1
<5
<0。
5
铸造非铁合金
各类铸件
硅砂
100/200
>85
<0.3
<0.1~0.2
<0.5~1
<5
<0。
5
①微粉:
对30/50、40/70筛号的原砂、140筛号以下为微粉;对50/100、70/140筛号的原砂,200筛号以下为微粉;对100/200筛号的原砂,270筛号以下为微粉。
酸自硬树脂砂除个别的、特殊要求之外,一般都采用硅砂,对硅砂的具体要求是:
1)原砂SiO2含量要高,一般铸钢件w(SiO2)≥97%,铸铁件w(SiO2)≥90%,非铁合金铸件w(SiO2)≥85%;
2)酸耗值应尽可能低,一般小于等于5ml;
3)含泥量越小越好,一般质量分数小于0.2%,颗粒表面应干净、不受污染,以保证砂粒与树脂膜之间有高的附着强度,因此应尽可能采用经过擦洗处理的擦洗砂;
4)原砂粒度适中,通常采用以70筛号为中心、主要部分集中在上下3或4个筛号上的原砂。
根据铸件大小,材质不同,原砂粒度大小应有所变化;
5)小于140筛号的细粉应尽量少,质量分数一般不得超过1%;
6)原砂应保持干燥,水的质量分数不大于0.2%;
7)角形因数要小,粒形越接近圆形越好。
角形因数最好在1.3以下,尽可能不用1.45以上的硅砂;
8)硅砂的灼烧减量质量分数不得超过0.5%。
2.再生砂
对浇注后的树脂砂经砂块破碎后的砂粒,通过机械摩擦等方法将其表面残留的固化树脂层去掉一部分的处理叫做树脂砂再生处理。
再生砂的质量直接影响着树脂的用量和型砂性能,因此控制再生砂质量指标很有必要。
指标见表2。
表2树脂砂再生质量控制指标
序号
树脂种类
铸造材质
灼减量/%(<)
酸耗值/ml(<)
PH
(<)
200目筛
的底盘/%(<)
底盘
量/%(<)
含水量/%(<)
含氮量/%(<)
1
酚醛脲烷
铸铁
3.0
—
8
3.0
0.5
0.2
—
2
呋喃树脂
铸铁
3.0
2.0
5
1.0
0.2
0.2
0.1
3
呋喃树脂
铸钢
1.5
2.0
5
1.0
0.2
0.2
0.03
4
呋喃树脂
铸铝
4.0
1.0
6
1.0
0.2
0.2
—
5
呋喃树脂
铸钢
2.5
1.0
6
1.0
0.2
0.2
—
6
多元醇脲烷类
铸铝
3.0
—
7
—
0.4
0.2
—
3.呋喃树脂
脲醛呋喃树脂具有强度高、韧性好、塑性好、价格便宜、应用范围广等特点,是应用量最大的一类树脂。
但是,在评价脲醛呋喃树脂时还应当注意随着含氮量增加,树脂游离甲醛的含量增加,水分增大。
脲醛呋喃树脂会出现混浊沉淀等现象,使树脂性能变差。
4.固化剂
磺酸固化剂都是由铸造树脂生产厂与树脂配套供应的。
表3为国产常用的几种磺酸固化剂,按季节划分品种,通过调整固化剂的种类和加入量可以调节自硬砂的硬化速度。
表3国产磺酸固化剂技术指标
指标型号
密度/(g/cm3)
黏度/mPa·s(20℃)
总酸度(质量分数)/%
游离酸(质量分数)/%
适用范围
GS03
1.20~1.30
10~30
24.0~26.0
7.0~10.0
春天、秋天
GS04
1.20~1.30
10~30
18.0~20.0
0.0~1.5
夏天
GC08
1.20~1.40
170~200
29.0~31.0
4.5~7.5
严冬
GC09
1.20~1.40
60~80
24.5~27.5
2.5~4.5
冬天
5.添加剂
为了改善酸自硬树脂砂的某些性能,有时在配比中加入一些添加剂,常用的添加剂见表4。
表4树脂自硬砂用添加剂
序号
名称
加入量
(质量分数)/%
作用
1
硅烷
0.1~0.3
偶联剂,提高强度,降低树脂加入量
2
氧化铁粉
1~1.5
防冲砂
3
氧化铁粉
3~5
防止气孔
4
甘油
0.2~0.4
增加砂型(芯)韧性
5
苯二甲酸二丁酯
约0.2
增加砂型(芯)韧性
6
邻苯二甲酸二丁酯
约0.2
增加砂型(芯)韧性
硅烷能增加树脂与原砂的附着强度,从而使树脂耗量降低1/3左右。
同时,硅烷还可以使树脂砂的抗湿性得到明显改善。
硅烷会水解,并变成高聚物沉淀出来,因而其增强作用随时间延长而减弱,因此最好在使用前加入硅烷,搅拌均匀放置4h后立即使用。
6.涂料
表5铸铁树脂砂型用醇基涂料的配方
序号
配料/%
鳞片状石墨粉
土状石墨粉
叶腊石粉
石英粉
锂基膨润土
有机膨润土
膨胀石墨粉
钠基膨润土
PVB
树脂
乌洛托品
酒精
备注
1
100
4~5
0.8~1
适量
2
100
7~9
0.3~0.5
1~1.25
适量
3
30
70
6~8
0~0.2
4~6
适量
4
100
4~5
0.2~0.5
1~1.5
适量
5
100
10~15
2~5
适量
6
30
70
10~15
2~5
适量
膏状
7
10
80
10
4~8
0.2~0.5
3~6
适量
膏状
8
10
65
25
5
3
适量
浅色
涂料
表6涂料的工艺性能
性能
水基涂料
醇基涂料
密度ρ/(g/cm3)
1.4~1.5
1.25~1.35
黏度(6#涂料杯)/s
7~8
6~7
悬浮性
24h
99%
—
2h
—
97%
涂刷性
滑爽,不把砂型(芯)表面砂粒带起
流平性
涂覆后砂型(芯)涂层表面能自动清除刷痕
不流淌性
垂直表面涂刷,涂料不往下流淌,不形成滴痕、不堆积
渗透性
渗入砂层深度2~3倍涂料直径
涂层强度
涂刷后不剥落损坏,浇注时耐冲刷
抗裂纹性
涂层在烘干和浇注时都不产生裂纹
贮存性
能贮存3~6个月,仍能保持规定的性能
安全性
对人体和环境不产生有害影响
7.脱模剂和胶黏剂
三、呋喃树脂砂硬化特性
1.树脂加入量为型砂量的1%;
固化剂加入量为型砂量的0.5%。
2.可使用时间和脱模时间与硬化特性的关系
这是自硬树脂砂也是所有化学黏结剂砂的很重要的性能指标。
可使用时间是指自硬树脂砂(其它化学黏结剂也相同)混砂后能够制出合格砂芯的那一段时间。
脱模时间是指从混砂结束开始,在芯盒在内制的砂芯(或未脱模的砂型)硬化到能满意地将砂芯从芯盒中取出(或脱模),而不致发生砂芯(或砂型)变形所需的时间间隔。
实际生产中,砂芯的脱模时间要根据砂芯的尺寸和复杂程度确定。
只要脱模后,砂型和砂芯不会变形、塌箱,就应脱模,决不可随意延长。
否则,会使脱模困难,甚至使模样、芯盒破坏,影响生产率。
从有利于生产着眼,希望混好的砂的可使用时间长,但生产中可使用时间与脱模时间之比最理想的还只能达到0.8,一般为0.35~0.6。
影响可使用时间、脱模时间的因素很多。
实验表明,所采用的原砂、树脂、催化剂的类型、质量和加入量、混砂工艺、环境温度和湿度,均对可使用时间和脱模时间有明显的影响,影响最大的为环境温度和催化剂的加入量。
当催化剂量相同,室温不同时,温度低则可使用时间长;温度高则可使用时间短。
其趋势是温度每增加10℃可使用时间缩短1/3~1/2。
室温相同时,催化剂加入量减少,可适用时间明显增长;催化剂增多,可适用时间缩短。
但是催化剂加入量超过一定范围内,可适用时间变化不大,但对脱模时间影响显著。
温度变化也明显影响脱模时间,其趋势是每增加5℃,脱模时间约缩短1/3~1/2。
四、呋喃树脂砂制备工艺
1.混制工艺:
为了使树脂、固化剂、偶联剂能在最短的时间里均匀覆盖在砂粒表面,需利用混砂机混制。
呋喃树脂砂不宜用碾轮式混砂机,大多用以搅拌为主的连续式混砂机或碗形混砂机。
混制树脂砂两种方法如下:
(1)
(2)
需要指出的是,当树脂加入已混合有固化剂的砂中后,应该在数秒钟至半分钟内混好,尽快出砂造型,不可在混砂机内混制时间过长。
2.旧砂再生工艺流程
旧砂再生工艺流程为:
第二章呋喃树脂铸造工艺设计
一、工艺特点:
1.呋喃树脂砂使用呋喃树脂和酸固化剂,在常温下硬化。
铸型的强度高,尺寸准确。
在浇注金属液时,呋喃树脂受热分解,燃烧,发气量大而且集中,逐渐容易形成气孔缺陷;
2.呋喃树脂砂在造型时,以干砂方式灌入砂箱,它的流动性好,可以不用大力舂砂。
砂粒之间间距比黏土砂大得多,透气性好;
3.呋喃树脂砂性采用快速、平稳的浇注系统,使铸型内的金属液迅速充满或达到一定高度,金属液的压力可以防止树脂砂中的气体进入铸件,迫使气体从透气性良好的砂型内排出;
4.呋喃树脂砂型导热慢,铸件不容易冷却,设计冒口时适当考虑铸型冷却后,溃散性很好,清砂方便,铸件的表面粗糙度和尺寸准确程度高于黏土砂铸件。
二、浇注位置的确定
1.保证铸件的大平面,重要加工面或主要受力面的质量。
一般放在铸型的下面或侧面;
2.满足铸件的凝固方式要求;
3.尽量减少泥芯数量,尽量使泥芯头支撑稳定,定位准确,下芯组装方便,出气通畅;
4.复杂铸件泥芯数量多,应优先考虑在下泥芯时,尺寸容易检查,尺寸精度容易保证。
第三章铸件缺陷分析及防止
呋喃树脂砂生产的铸件表面质量好,尺寸精度高,废品率低。
但在生产过程中仍会出现不少缺陷,甚至造成批量报废。
(1)气孔
①产生原因
a.树脂或固化剂加入过多,发气量增大。
b.涂料中水分太高,涂料过多,干燥不充分。
c.旧砂灼减量和微粉超标,发气量大,透气性降低。
d.造型制芯未考虑排气。
泥芯通气设置不理想,与外形出气孔未贯通。
e.上涂料时局部有堆积,不能彻底干燥。
f.浇口小,浇注速度慢,铸件高,金属液上升速度低;
g.浇注温度过低,铁水氧化,钢液脱氧不够等。
②防止方法
a.降低树脂和固化剂加入量,选用发气量小的树脂,树脂中加入硅烷(占树脂重量2%)。
b.控制涂料中的含水量<5%,控制酒精含水量。
砂型及泥芯充分干燥后,再刷上涂料,合箱前用喷灯烘烤。
c.加强旧砂再生和防尘,铸铁用砂灼减量≤3%,铸钢用砂灼减量≤2%,微粉含量(200目+底盘)≤0.8%。
d.重视外模及泥芯的气孔设置,保证浇注时顺利排气。
e.清除局部涂料堆积。
f.大孔出流,保证金属液充型快速、平整、分散浇注。
高的铸件用阶梯形浇口,使用浇口杯提高压力头。
(2)粘砂
①产生原因
a.砂粗,粒度过于集中。
砂粒间隙大,金属液易渗入空隙形成粘砂。
b.涂料层太薄或者漏涂,涂层渗透太浅,涂料耐火度不高。
c.砂型、砂芯紧实度不够,铸型表面疏松、强度低。
d.砂型、砂芯中新砂比例太高。
浇注温度过高。
e.型砂超出其可使用时间,砂温太高。
②防止方法
a.选用多筛砂,铸钢或铸铁厚部可使用铬砂或锆英砂。
b.涂料层要有一定的渗透深度和涂层厚度,涂料质量要好。
c.提高砂型、砂芯的紧实度,采用振实台造型。
必须注意凸台下、活块下部砂的紧实程度,提高凹沟、转角处砂的紧实度。
d.多用旧砂。
用高温出铁、低温浇注的原则,控制合理的浇注温度。
e.控制砂温,安装砂温调节装置。
控制型砂的可使用时间满足造型需要。
(3)裂纹
①产生原因
a.呋喃树脂砂高温退让性差,特别是铸钢件容易产生裂纹。
b.合金钢材料容易裂。
c.铸件结构复杂,收缩阻力大。
d.树脂砂中,固化剂受热分解,铸件表面渗硫,产生微裂纹,成为表面龟裂的起纹。
e.砂芯未倒圆角,型砂在浇注中尖角高温,产生热量集中,容易拉裂。
f.泥芯骨过大,妨碍收缩。
②防止方法
a.提高型砂退让性,在砂中加入木粉,EPS珠粒,泥芯做空心。
b.在裂纹容易产生的部位,使用铬铁砂或铣英砂代替石英砂。
c.设防裂筋,与需方协商,修改铸件结构。
d.使用灼减量低的旧砂,减少固化剂加入量,用含硫低的黏结剂。
e.砂芯刮出铸造圆角,防止尖角砂结构,可以加大铸型圆角。
f.芯骨减少,芯骨应简单。
(4)夹渣
①产生原因
a.浇注时扒渣、挡渣不力,渣随金属液进入型腔。
b.浇注系统集渣能力不足,溢流措施不足。
c.浇注时间过长。
d.金属液浇注不平稳,特别对易氧化的金属如铝、铝青铜、球墨铸铁,产生二次氧化夹渣。
e.金属液温度低,渣不易从金属液中清除。
②防止方法
a.金属表面扒渣,洒集渣剂,球铁应数次搅拌,扒渣。
b.浇注系统设过滤网或集渣包。
横浇口要高一些,在铸件内浇口对面或顶面设立溢流冒口。
c.快浇,平稳充型。
使用大孔出流理论,增大内浇口尺寸及数量。
(5)硬度不足
①产生原因
a.树脂砂导热性差,铸件在型内高温时间长,冷却速度低。
b.化学成分波动,浇注温度太高。
c.内浇口开在要求硬度高的部位,延长冷却时间。
②防止方法
a.缩短开箱时间,使用冷铁。
b.选择合适的化学成分,添加增加硬度的微量合金,降低浇注温度。
c.内浇口离开要求硬度高的地方。
(6)渗碳、渗硫及球化不良
①产生原因
a.树脂、固化剂都是有机物,在浇注冷却过程中,低碳钢及低碳不锈钢的表面会渗入一层碳,厚度2~3mm。
b.固化剂对甲苯磺酸对不锈钢或球铁表面渗碳可达1~3mm。
c.由于渗硫,使球铁表面会产生球化不良。
②防止方法
a.砂型和涂料中可加入氧化铁粉,也可用铬铁砂砂型上两层铬英粉涂料。
b.在涂料中加入强烈脱硫的物质。
c.球化处理时,增加一点球化剂。
(7)缩孔和缩松
①产生原因
a.铸铁凝固时,液态补缩不足,产生缩孔或缩凹。
在工艺上表现为冒口太小,冒口径太小,冒口数量不足。
b.冒口颈和内浇口截面积大,与铸件接触处增大了接触热节。
在工艺上表现为内浇口太厚,冒口径尺寸太大,放置位置不对。
c.化学成分变化对收缩产生影响。
d.浇注温度过高。
e.冒口处金属液温度太低。
f.型砂强度低,铸铁石墨化膨胀利用率低,铸件缩松。
②防止措施
a.增大冒口体积,增大冒口颈尺寸,增加冒口数量,在铸件厚大处设置冷铁。
b.减薄加宽内浇口,增加内浇口数量,内浇口开在铸件薄处。
减小冒口颈尺寸,在冒口径旁边设置冷铁,这样就可以开大冒口颈,增加缩补量,又可以及时封死冒口,消除接触热节增大现象。
c.充分考虑化学成分对铸件凝固的影响,调整铸件凝固方式。
d.适当降低浇注温度。
e.冒口中冲入热金属液或放发热冒口圈(保温冒口)。
f.砂型要捣紧,对于重大型铸件,应选择高强度树脂作黏结剂。
(8)砂孔
①产生原因
a.配模时砂未吹净,或者砂吹到死角吸不出来。
b.砂型、砂芯强度不高,局部疏松,砂易剥落、配模磕碰落砂。
c.内浇口进的金属液有冲刷力,能将砂粒冲下。
d.安放浇冒口圈时,防止砂粒落入型腔。
e.直浇口没有耐火陶管,浇注时冲砂。
②防止方法
a.合箱仔细,清除浮砂和堆积砂。
b.造型与制芯时用棒捣固砂型,表面疏松处用涂料可修补。
c.内浇口开宽,数量增加,金属液流量大,流速小,平稳充型。
d.安放浇口杯(盆)和冒口圈要小心。
e.直浇口可安耐火陶管。