《炼钢工艺学》复习题.docx
《《炼钢工艺学》复习题.docx》由会员分享,可在线阅读,更多相关《《炼钢工艺学》复习题.docx(42页珍藏版)》请在冰豆网上搜索。
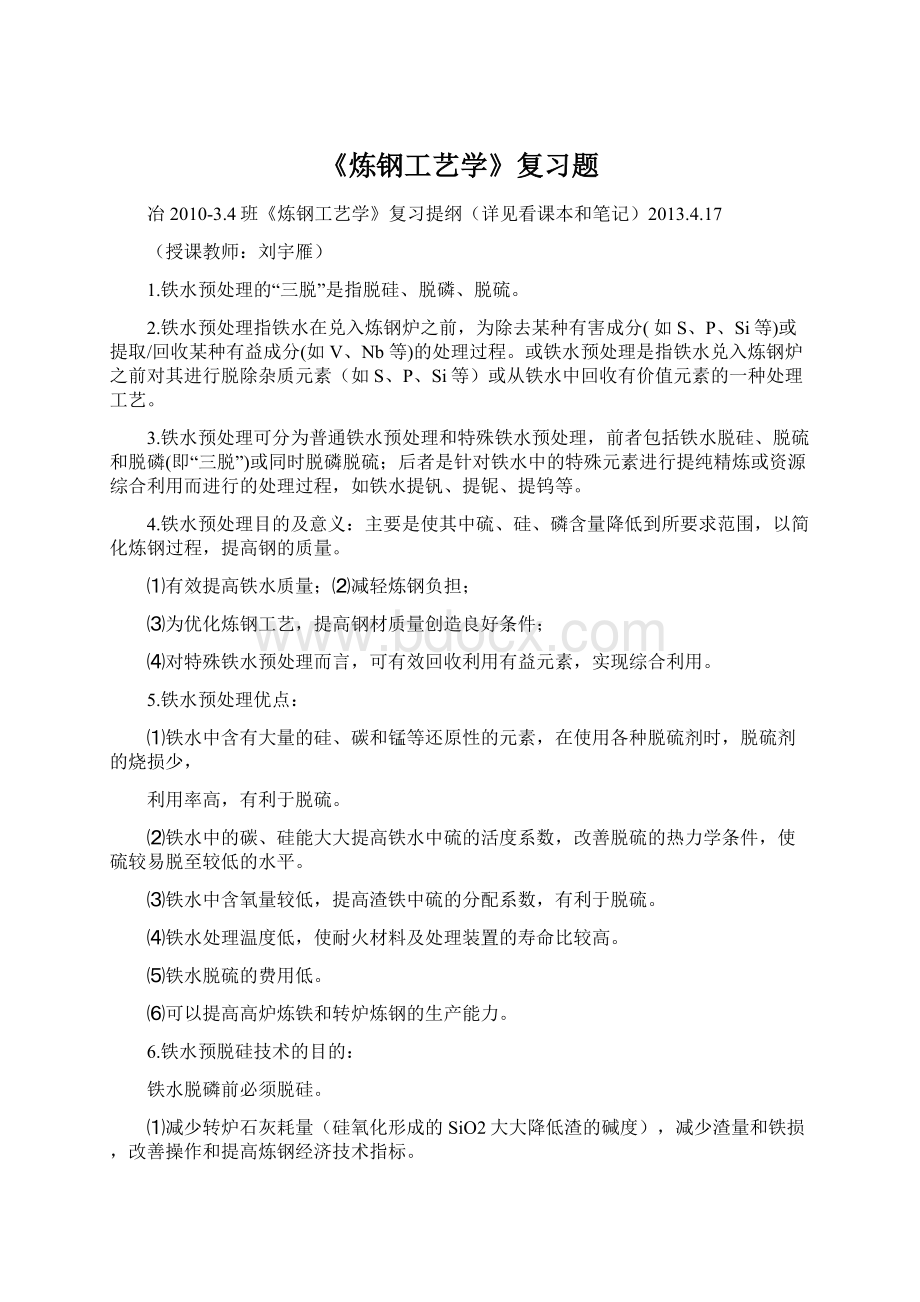
《炼钢工艺学》复习题
冶2010-3.4班《炼钢工艺学》复习提纲(详见看课本和笔记)2013.4.17
(授课教师:
刘宇雁)
1.铁水预处理的“三脱”是指脱硅、脱磷、脱硫。
2.铁水预处理指铁水在兑入炼钢炉之前,为除去某种有害成分(如S、P、Si等)或提取/回收某种有益成分(如V、Nb等)的处理过程。
或铁水预处理是指铁水兑入炼钢炉之前对其进行脱除杂质元素(如S、P、Si等)或从铁水中回收有价值元素的一种处理工艺。
3.铁水预处理可分为普通铁水预处理和特殊铁水预处理,前者包括铁水脱硅、脱硫和脱磷(即“三脱”)或同时脱磷脱硫;后者是针对铁水中的特殊元素进行提纯精炼或资源综合利用而进行的处理过程,如铁水提钒、提铌、提钨等。
4.铁水预处理目的及意义:
主要是使其中硫、硅、磷含量降低到所要求范围,以简化炼钢过程,提高钢的质量。
⑴有效提高铁水质量;⑵减轻炼钢负担;
⑶为优化炼钢工艺,提高钢材质量创造良好条件;
⑷对特殊铁水预处理而言,可有效回收利用有益元素,实现综合利用。
5.铁水预处理优点:
⑴铁水中含有大量的硅、碳和锰等还原性的元素,在使用各种脱硫剂时,脱硫剂的烧损少,
利用率高,有利于脱硫。
⑵铁水中的碳、硅能大大提高铁水中硫的活度系数,改善脱硫的热力学条件,使硫较易脱至较低的水平。
⑶铁水中含氧量较低,提高渣铁中硫的分配系数,有利于脱硫。
⑷铁水处理温度低,使耐火材料及处理装置的寿命比较高。
⑸铁水脱硫的费用低。
⑹可以提高高炉炼铁和转炉炼钢的生产能力。
6.铁水预脱硅技术的目的:
铁水脱磷前必须脱硅。
⑴减少转炉石灰耗量(硅氧化形成的SiO2大大降低渣的碱度),减少渣量和铁损,改善操作和提高炼钢经济技术指标。
⑵铁水预脱P的需要,可减少脱磷剂用量、提高脱磷、脱S效率。
当铁水[Si]>0.15%时,脱磷剂用量急剧增大。
因此,脱磷处理前需将铁水含[Si]脱至<0.15%,这个值远远低于高炉铁水的硅含量,也就是说,只有当铁水中的硅大部分氧化后,磷才能被迅速氧化去除。
所以脱磷前必须先脱硅。
铁水预脱P的最佳[Si]初始:
①苏打脱P:
[Si]初始<0.1%
②石灰熔剂脱P:
[Si]初始0.10~0.15%
⑶对含V或Nb等特殊铁水,预脱Si可为富集V2O5和Nb2O5等创造条件。
7.铁水预脱硫技术迅速发展的原因:
⑴用户对钢的品种和质量要求提高。
⑵连铸技术的发展要求钢中硫含量进一步降低,否则连铸坯容易产生内裂,铁水脱硫可满足冶炼低硫钢和超低硫钢种的要求。
⑶铁水中碳、硅、磷等元素的含量高,可提高硫在铁水中的活度系数,而有利于脱硫,同时铁水中的氧含量低,没有强烈的氧化性气氛,有利于直接使用一些强脱硫剂,如电石(CaC2)、金属镁等;故铁水脱硫效率高。
⑷铁水脱硫费用低于高炉、转炉和炉外精炼的脱硫费用。
其费用比值为:
高炉脱硫:
铁水预处理脱硫:
转炉:
炉外精炼=2.6:
1:
16.9:
6.10
⑸降低炼铁和炼钢炉脱硫负担;有利于降低消耗和成本,并增加产量。
⑹提高炼铁和炼钢经济技术指标;有效提高钢铁企业铁、钢、材的综合经济效益。
全程脱硫:
高炉-铁水炉外-炼钢炉(-精炼炉)→实现铁水深度脱硫,经济有效生产超低S高级优质钢;
⑺提高钢质、扩大品种、优化工艺(改善转炉炼钢操作);
8.铁水预脱硫优点(铁水脱硫条件比钢水脱硫优越的主要原因)
用优质铁水炼钢,是提高产品质量、扩大品种、增加效益和增强产品市场竞争力的重要条件之一,也是生产低硫洁净钢的基础。
铁水炉外脱硫有利于提高炼铁、炼钢技术经济指标。
通过比较各种脱硫工艺,铁水脱硫预处理工艺有如下优点:
⑴铁水中[C]、[Si]较高,fs↑,提高硫的反应能力;
⑵铁水中[O]较低,提高渣铁之间的硫分配比(Ls↑),脱硫效率高;
⑶搅拌充分,脱硫剂利用率高,脱硫速度快;
⑷铁水脱硫可提高炼铁炼钢的生产能力、节约工序能源、降低成本。
⑸故铁水脱硫费用费用比其他工序低。
9.铁水预脱硫技术的发展:
铁水炉外脱硫技术在20世纪60年代氧气顶吹转炉炼钢工艺发展后得到迅速推广,在国外已趋成熟,在实际生产中大量应用,处理工艺方法约数十种之多。
先后发明的工艺大致可分为分批处理法和连续处理法两大类,其中分批处理法又可分为铺撒法/投入法(含倒包法)、机械搅拌法、吹气搅拌法、喷射法、镁脱硫法等。
目前常用的方法有喷吹法和KR机械搅拌法。
目前生产中主要应用的铁水脱硫方法有KR搅拌法和喷吹法。
⑴KR机械搅拌法:
是将浇注耐火材料并经过烘烤的十字形搅拌头,熔池一定深度,借其旋转产生的漩涡,使氧化钙或碳化钙基脱硫粉剂与铁水充分接触反应,达到脱硫目的。
其优点是动力学条件优越,有利于采用廉价的脱硫剂如CaO,脱硫效果比较稳定(由于搅拌能力强和脱硫前后能充分的扒渣,回硫少,可将硫脱至很低,即实现深脱硫),效率高(脱硫到≤0.005%),脱硫剂消耗少,适应于低硫品种钢要求高、比例大的钢厂采用。
其缺点是设备复杂,一次投资较大,脱硫铁水温降较大。
⑵喷吹法:
是利用惰性气体(N2或Ar)作载体将脱硫粉剂(如CaO,CaC2和Mg)由喷枪喷入铁水中,载气同时起到搅拌铁水的作用,使喷吹气体、脱硫剂和铁水三者之间充分混合进行脱硫。
目前,以喷吹镁系脱硫剂为主要发展趋势,其优点是设备费用低,操作灵活,喷吹时间短,铁水温降小。
相比KR法而言,一次投资少,适合中小型企业的低成本技术改造。
喷吹法最大的缺点是,动力学条件差,扒渣操作较难,易回硫(尤其是单喷法)有研究表明,在都使用CaO基脱硫剂的情况下,KR法的脱硫率是喷吹法的四倍。
10.叙述铁水镁基预脱硫工艺过程和工艺特点:
在出铁沟内向铁水中加入造渣料、保温剂等,使铁水从铁口至铁水罐的过程中,可以进行脱硅、脱硫,调整铁水成分。
铁水运到预处理车间,喷吹或加入金属镁、石灰脱硫剂。
脱硫后将铁水上面的渣除去,加入保温剂可以保持铁水温度、控制硫含量。
工艺特点:
充分发挥铁水氧势低的特点。
高炉:
炉渣碱度和焦比下降,有利于高炉顺行和提高生产率。
转炉:
减少石灰用量和渣量,提高金属收得率,冶炼超低硫钢。
11.铁水脱硫预处理的工艺方法:
⑴投掷(入)法:
将脱硫剂投入铁水中。
⑵喷吹法:
将脱硫剂喷入铁水中。
⑶搅拌法(KR法):
将通过中空机械搅拌器向铁水内加入脱硫剂,搅拌脱硫。
12.常用铁水预脱硫剂有石灰、碳化钙/电石、苏打、金属镁及复合脱硫剂等。
或生产中,常用的脱硫剂有苏打灰(Na2CO3)、石灰粉(CaO)、电石粉(CaC2)和金属镁。
13.提高铁水脱硫效果的措施:
1)热力学条件。
⑴fs↑([C]↑、[Si]↑);⑵降低氧位,即[O]↓、(O2-)↓(加入铝)
⑶脱硫剂用量↑(同时生产费用↑);⑷控制好温度。
2)动力学条件。
⑴根据铁水条件及钢种要求,选择适当主脱硫剂。
即要满足脱硫要求,又要尽量降低脱硫成本且操作方便。
脱硫要求一般时(轻脱硫),脱硫剂组成以石灰粉为主;生产低硫生铁时,以电石粉为主(深脱硫)。
⑵添加适当促进剂。
⑶适当减小脱硫剂粒度,增大反应界面,加快脱硫速度;
⑷强化熔池搅拌,增加逗留时间,减小扩散边界层厚度,提高混匀搅拌效率,均可加快脱硫反应速度;
⑸控制好温度。
提高铁水温度,增大硫的传质系数;
⑹选择适当的喷吹参数,以取得最佳喷吹效果。
14.选择脱硫方法的原则(铁水脱硫方案的选择)
⑴铁水条件供应条件;⑵冶炼钢种要求;
⑶处理规模(处理能力,作业率)、工艺流程(铁水运输方式)及总图布置(布置位置);⑷脱硫效率及脱硫剂消耗;⑸处理成本(设备和基建费用);
⑹铁水温降;⑺预留铁水三脱的可能性;⑻环境污染
15.转炉的内衬由绝热层/隔热层、永久层、工作层组成。
炼钢用耐火材料按化学性质可分为:
碱性耐火材料、酸性耐火材料和中性耐火材料。
碱性耐火材料是指以CaO和MgO为主组成的耐火材料。
耐火度:
是使耐火材料软化到一定程度的温度。
抗渣性:
耐火材料在高温下抵抗炉渣侵蚀的能力。
16.转炉炉衬损坏原因主要为机械作用、高温作用、化学侵蚀、炉衬剥落。
或机械冲击和磨损、耐材的高温溶解、高温溶液渗透、高温下气体挥发。
转炉出钢口采用耐冲蚀性好、抗氧化性高的镁碳砖。
炉龄:
转炉从开新炉到停炉,整个炉役期间炼钢的总炉数。
转炉炉龄:
是指转炉大修后投入生产直到下次停炉大修期间所炼钢的炉数。
经济炉龄即为最佳炉龄,也就是要获得最好的生产率和最低的成本。
17.炼钢的基本任务:
脱碳、脱磷、脱硫、脱氧,去除有害气体和非金属夹杂物,提高温度和调整成分。
采用的主要技术手段为:
供氧,造渣,升温,加脱氧剂和合金化操作。
或“四脱”(脱碳、脱氧、脱磷和脱硫),“二去(去气和去夹杂)”,“两调整”(调整温度和成分)。
或脱碳、脱磷、脱硫、脱氧,去气(去除有害气体)和非金属夹杂物,升温及脱氧合金化(提高温度和调整成分)。
1)脱碳:
把铁水中的碳氧化脱除到所炼钢种的范围内。
2)脱磷脱硫:
通过造出成分合适的炉渣,去除铁水中的磷、硫。
3)脱氧和合金化:
加入脱氧剂和铁合金,降低钢液中的氧和使钢液达到钢种要
求的合金成分。
4)脱气(氢、氮)和脱夹杂物:
把溶解在钢液中的气体和来不及上浮排除的非
金属夹杂物,通过一定的方法去除。
5)升温:
把冶炼过程的金属液温度升高至出钢温度。
6)浇注:
将成分和温度合格的钢水浇注成坯。
18.熔渣的物理化学性质
炼好钢首先要炼好渣,所有炼钢任务的完成几乎都与熔渣有关。
熔渣的结构决定着熔渣的物理化学性质,而熔渣的物理化学性质又影响着炼钢的化学反应平衡及反应速率。
因此,在炼钢过程中,必须控制和调整好炉内熔渣的物理化学性质。
15.炉渣在炼钢中起着什么作用?
炉渣不仅是炼钢生产的废弃物,又是冶炼过程中不可缺少的主要物质,所谓“炼钢就是炼渣”,炉渣在炼钢过程中所起的主要作用有:
⑴炉渣能有效的去除铁水中的有害元素S和P。
⑵炉渣是炼钢过程中氧的重要传递媒介,特别是对电炉、精炼炉更是如此。
⑶炉渣可以搜集从金属液中上浮的各种反应产物及非金属夹杂物。
⑷炉渣对熔池的传热有重要作用,可以减少熔池的散热损失。
⑸炉渣对金属的收得率有重要影响,炉渣的物理性质控制不当就会造成喷溅或是增加渣中夹铁量而造成更多的金属损失。
⑹炉渣可以保护炉衬,溅渣护炉(炉渣是使炉衬侵蚀的主要物质,因此炉渣的化学成分及物理性质对炉衬的使用寿命有重要影响)。
或炉渣的作用:
脱除磷硫、向金属熔池传氧、减少炉衬侵蚀等。
或熔渣在炼钢过程中的作用主要体现在以下几个方面:
⑴去除铁水和钢水中的磷、硫等有害元素,同时能将铁和其他有用元素的损失控制在最低限度内。
熔渣还能吸收铁水中的钒、铌等有用元素的氧化物,而成为钒渣或铌渣,然后再从中提取钒或铌,可以说熔渣是炼钢去除杂质的精炼剂;
⑵炼钢熔渣覆盖在钢液表面,保护钢液不过度氧化、不吸收有害气体,保温,减少有益元素烧损;
⑶防止热量散失,以保证钢的冶炼温度;
⑷吸收钢液中上浮的夹杂物及反应产物。
熔渣在炼钢过程中也有不利作用,主要表现在:
⑴侵蚀耐火材料,降低炉衬寿命,特别是低碱度熔渣对炉衬的侵蚀更为严重;
⑵熔渣中夹带小颗粒金属及未被还原的金属氧化物,降低了金属的收得率。
因此,造好渣是炼钢的重要条件。
要造出成分合适、温度适当并具有适宜于某种精炼目的的炉渣,发挥其积极作用,抑制其不利作用。
有利作用:
⑴通过调整熔渣成分氧化还原钢液,使钢液中硅、锰、铬等元素氧化或还原的硫、磷、氧等元素;
⑵吸收钢液中的非金属夹杂物;
⑶防止炉衬的过分侵蚀;
⑷覆盖钢液,减少散热和防止二次氧化和吸氢。
其他作用:
在不同炼钢方法中,熔渣还有其独特的作用。
如:
①氧气顶吹转炉炼钢过程→熔渣-钢液滴-气泡形成高度的乳化相→钢渣接触面积↑→
加速吹炼过程。
②电弧炉炼钢时→稳弧(稳定电弧燃烧)和传热→良好的泡沫渣能包围住弧光→弧光对炉衬的辐射侵蚀↓
③电渣重熔时→作电阻发热体→可重熔和精炼金属(电渣炉)
④出钢时→钢液的二次氧化↓
⑤浇注时→作保护渣,可减少氧化,防止散热,并改善铸坯表面质量等。
不利作用:
①侵蚀耐火材料,降低炉衬寿命,特别是低碱度熔渣对炉衬的侵蚀更为严重。
②熔渣中夹带小颗粒金属及未被还原的金属氧化物,降低了金属的回收率。
③严重泡沫化熔渣会引起喷溅。
(转炉)
19.炼钢炉渣的来源,主要有三个方面:
①炼钢过程有目的加入的各种造渣材料(石灰、萤石、粘土砖等)。
②钢铁材料(生铁或废钢)中所含元素Si、Mn、P、Fe等元素的氧化产物。
炼钢过程中化学反应的产物,即金属炉料、脱氧剂及合金中的各元素被氧化后所生成的氧化物(SiO2、MnO、P2O5、FeO、Fe2O3);还有少量硫化物(CaS、MnS)。
③冶炼过程被侵蚀的炉衬耐火材料。
或炼钢过程中炉渣来自何处?
炉渣的来源主要有:
⑴钢铁料(铁水、废钢)所含的各种杂质元素(如Si、Mn、P等)被氧化生成的氧化物;
⑵为去除铁水中的硫、磷而加入的造渣材料(石灰等)及助熔剂(萤石等);
⑶作为氧化剂或冷却剂加入的矿石、烧结矿、氧化铁皮等材料带入的杂质;
⑷被侵蚀或冲刷下来的炉衬耐火材料;
⑸由各种原材料带入的泥沙杂质。
20.熔渣的氧化性(熔渣的氧化能力):
是指在一定的温度下,单位时间内熔渣向钢液供氧的
数量(在单位时间内从渣相向金属相供氧的数量);是熔渣的一个重要性质,决定了脱磷、
脱碳,以及去除夹杂物等。
通常用渣中氧化铁含量的多少表示熔渣氧化能力的强弱。
生产中
常用渣中∑(%FeO)表示渣的氧化性。
21.熔渣氧化性对操作过程有何影响?
如①杂质的去除程度;②钢水含氧量;③石灰溶化速度;④熔渣的泡沫程度;⑤喷溅;⑥炉衬寿命;⑦金属和铁合金的收得率。
22.熔渣与熔融金属之间应有足够大的表面张力,以有助于渣壳分离,防止熔渣卷入金属内;而熔渣与非金属夹杂物之间的表面张力越小越好,以利于熔渣对非金属夹杂物的浸润、吸附和溶解。
炉渣碱度:
是指炉渣中的碱性氧化物与酸性氧化物的数量之比,一般用R=%CaO/%SiO2来表示。
溶渣粘度代表溶渣内部相对运动时各层之间的内摩擦力。
影响炉渣粘度的主要因素是:
炉渣成分、温度、悬浮于渣中固态微粒的尺寸和数量。
23.氧气顶吹转炉的传氧机理主要可分为直接传氧和间接传氧两种形式。
炼钢时向钢液供氧的方式有直接供氧和间接供氧。
硅的直接氧化反应式为:
[Si]+{O2}=(SiO2)和[Si]+2[O]=(SiO2)。
24.炼钢脱磷的有利条件有哪些?
答:
脱磷反应:
2[P]+5(FeO)+4(CaO)=(4CaO·P2O5)+5[Fe]
或脱P化学反应式为:
2[P]+5(FeO)+3(CaO)=(3CaO·P2O5)+5[Fe]+Q
由去磷反应式可知,高碱度、高氧化铁炉渣有利于去磷。
脱磷有利条件:
高碱度、高(FeO)/氧化性、良好流动性熔渣、充分的熔池搅拌、适当的温度和大渣量。
氧化脱磷的有利条件:
⑴较高的炉渣碱度(3~4);⑵氧化铁较高(15%~20%);
⑶良好流动性熔渣;⑷充分的熔池搅拌;⑸适当的温度(1450~1550℃);
⑹渣量要大,可利用多次放渣和造新渣去磷。
氧气顶吹转炉炼钢过程中,去除[P]的任务主要是在吹炼中前期完成。
脱磷工艺的热力学和动力学条件和炼钢过程中脱磷特点及脱磷的必要性:
2[P]+5(FeO)+3(CaO)=3CaO.P2O5+5[Fe]或2[P]+5(FeO)+4(CaO)=4CaO.P2O5+5[Fe]
磷使钢产生冷脆,磷含量越高越易在结晶边界析出磷化物,降低钢的冲击值,含碳高时[C]促进凝固过程中磷的偏析。
2[P]+5[O]+3(O2-)=2(PO4-)
①T↓有利脱P,放热反应
②R↑有利脱P,CaO与P2O5结合,降低γ;R↑↑粘度↑不利
③FeO↑有利脱P,必要条件,促进P2O5[O]↑
④渣量↑有利脱P,稀释
⑤[Si][Mn][Cr][C]↑不利脱P[O]↓
⑥提高LP,能扩大钢渣界面提高传质系数的因素有脱碳速度、氧枪位置、供氧强度等,都能促进脱磷。
转炉和电炉炼钢过程R↑有利于脱磷。
但出钢脱氧后钢水中[O]↓,带入的转炉渣中的P要回到钢水中,如何解决炉外精炼过程回磷是炼钢脱磷课题。
25.回磷:
就是磷从熔渣中又返回到钢中,也是脱磷的逆向反应;或成品钢中磷含量高于终点磷含量也属回磷现象。
或磷自炉渣返回钢液的现象。
26.减少回磷的措施:
为了抑制“回磷”现象,在生产中常用的办法是:
在出钢前向炉内加入石灰,使炉渣变稠以防止出钢时下渣。
⑴冶炼中期,保持∑(FeO)>10%,防止因炉渣“返干”而产生的回磷;控制终点温度不要过高,并调整好炉渣成分,使炉渣碱度保持在较高水平。
⑵出钢时,①适当提高脱氧前的炉渣碱度;②挡渣出钢,尽量避免下渣;
⑶出钢后,向钢包渣面加一定量石灰,增加炉渣碱度;脱氧合金化时,尽可能采取钢包脱氧,而不采取炉内脱氧。
27.炼钢脱硫的有利条件有哪些?
脱硫的有利条件:
高温、高碱度、低氧化铁(FeO),良好流动性熔渣、充分的熔池搅拌和大渣量。
氧气顶吹转炉脱[S]效果比较理想的条件是在吹炼后期。
28.碳氧浓度积:
在一定的温度和压力下钢液中的碳氧反应达到平衡时,碳和氧的质量百分浓度之积是一个常数。
29.脱碳反应对炼钢过程的作用/碳氧化在炼钢中的作用:
炼钢熔池中脱碳反应基本形式为:
[C]+[O]=CO↑和[C]+(FeO)=[Fe]+CO↑。
①脱碳,将熔池中的碳氧化脱除至所炼钢种的终点要求;
②放热升温,加速传质传热;③均匀熔池成分、温度;
④加大钢-渣界面,加速反应的进行,也有利于熔渣的形成;
⑤去气去夹杂(有利于非金属夹杂的上浮和有害气体的排出)。
⑥爆发性的脱碳反应会造成喷溅。
或氧气顶吹转炉炼钢脱碳反应的意义:
⑴氧化铁水中的碳至少种要求终点碳的范围内;
⑵均匀钢水温度、成分促进各种化学反应进行;
⑶去除钢中气体,促进钢中非金属夹杂物碰撞上浮;
⑷为转炉炼钢提供大部分热源;
⑸使炉渣形成成泡沫,有利于炉渣与金属滴间的化学反应。
30.碳氧反应发生的必要条件是:
必须存在过剩氧,即[O]实际>[O]平衡。
31.钢中氧的危害性主要表现在以下方面
(1)产生夹杂;
(2)形成气泡;(3)加剧硫的危害。
32.脱氧任务:
炼钢炉内氧的存在形态有气态氧、溶解在渣中的氧、溶解在钢中的氧。
⑴按钢种要求降低钢液中溶解的氧;⑵排除脱氧产物;⑶控制残留夹杂的形态和分布。
炼钢生产常用的脱氧方法有沉淀脱氧、扩散脱氧和真空脱氧。
33.炼钢脱氧的方法有哪几种?
它们各有什么特点?
答:
按脱氧原理及脱氧反应发生的地点不同,脱氧方法分为沉淀脱氧﹑扩散脱氧和真空脱氧。
1)沉淀脱氧
定义:
把脱氧剂加入钢液中,脱氧产物以沉淀形态产生于钢液之中的脱氧方法就叫沉淀脱氧,又叫直接脱氧,是目前广为采用的脱氧方法。
或把块状脱氧剂加入到钢液中,脱氧元素在钢液内部与钢中氧直接反应,生成的脱氧产物上浮进入渣中的脱氧方法称为沉淀脱氧。
或是把块状脱氧剂直接加入到钢水中,脱除钢水中氧的一种脱氧方法。
或将脱氧剂加到钢液中,它直接与钢液中的氧反应生成稳定的氧化物,即直接脱氧。
或将块状脱氧剂沉入钢液中,熔化、溶解后与钢中氧反应生成稳定的氧化物并上浮进入炉渣,以降低钢中氧的脱氧方法。
或直接向钢液中加入脱氧剂,以夺取溶解在钢液中的氧,并生成不溶于钢液的氧化物或复合氧化物而排至炉渣中。
特点:
优点:
脱氧效率比较高,耗时短,合金消耗较少((沉淀脱氧反应在钢液内部进行,效率高,脱氧反应速度快,对冶炼时间无影响),操作简便,成本较低,因而在生产中广泛采用。
缺点:
脱氧产物容易残留在钢中会造成内生夹杂物。
当脱氧产物不能清除时将增加金属液中杂质的含量,易污染钢液(生成的脱氧产物有可能难以完全上浮而成为钢中非金属夹杂;沉淀脱氧的脱氧程度取决于脱氧剂能力和脱氧产物的排出条件)。
应用:
转炉炼钢普遍采用沉淀脱氧法,出钢过程的预脱氧,钢水喂线(如铝线、Ca5i线等)终脱氧都属沉淀脱氧。
常用的脱氧剂有:
锰铁、硅铁、铝和复合脱氧剂等。
2)扩散脱氧
原理:
是根据氧分配定律建立起来的,随着钢液中氧向炉渣中扩散,炉渣中(FeO)逐渐增多,为了使(FeO)保持在低水平,需在渣中加脱氧剂来还原渣中的(FeO),这样可以保证钢液中的氧不断向渣中扩散。
扩散脱氧时,脱氧剂加到熔渣中,通过降低熔渣中的(FeO)含量,使钢水中氧向熔渣中转移扩散,达到降低钢水中氧含量的目的。
定义:
扩散脱氧又叫间接脱氧。
它是将粉状的脱氧剂如C粉﹑Fe-Si粉﹑CaSi粉﹑Al粉加到炉渣中,降低炉渣中的氧含量,使钢液中的氧向炉渣中扩散,从而达到降低钢液中氧含量的一种脱氧方法。
或通过不断减低炉渣中(FeO)含量来相应降低钢液中氧含量的方法。
或是在液态金属与熔渣界面上进行的,利用熔渣中的FeO与钢液中的FeO能够互相转移,趋于平衡时符合分配定律的机理进行脱氧。
特点:
优点:
钢中残留的有害夹杂物较少。
脱氧反应在钢渣界面上进行,脱氧产物不会污染钢液(扩散脱氧的产物存在于熔渣中/在渣相内形成,不在钢中生成非金属夹杂物,这样有利于提高钢液的洁净度)。
缺点:
钢水平静状态下扩散脱氧的时间较长(脱氧速度较慢),脱氧剂消耗较多。
由于扩散脱氧是在钢-渣界面上进行,钢液中的氧需要向渣中转移,完全靠氧的扩散,因此速度很慢/脱氧时间长,可以通过吹氩搅拌或钢渣混冲等方式加速脱氧进程;另外,进行扩散脱氧操作前,需换新渣,以防止回磷。
应用:
一般用于电炉还原期,或钢液的炉外精炼。
合成渣洗、LF白渣精炼均属扩散脱氧,脱氧效率较高,但必须有足够时间使夹杂物上浮。
配有吹氩搅拌装置,效果非常好。
3)真空脱氧:
原理:
将钢包内钢液置于真空条件下(如RH精炼),通过抽真空打破原有的碳氧平衡,促使碳与氧的反应,达到通过钢中碳去除氧的目的。
定义:
利用降低系统的压力来降低钢液中氧含量的脱氧方法。
它只适用于脱氧产物为气体的脱氧反应如[C]-[O]反应。
特点:
优点:
不消耗合金,脱氧比较彻底,脱氧产物为CO气体,易于排除,不污染钢液(不会对钢造成非金属夹杂的污染),而且在排出CO气体的同时,还具有脱氢、脱氮的作用,故这种脱氧方法的钢液洁净度高。
局限:
需要有专门的真空设备。
应用:
随着炉外精炼技术的应用,根据钢种的需要,钢水(转炉或电炉)也可采用真空脱氧。
34.促使脱氧产物上浮的措施:
⑴上浮速度↑;⑵形成液态的脱氧产物。
⑶形成与钢液间界面张力大的脱氧产物。
30.合金元素加入一般的原则:
⑴脱氧元素先加,合金化元素后加;
⑵脱氧能力较强、且比较贵重的合金,应在钢水脱氧良好的情况下加入,以提高合金收得率。
⑶熔点高,不易氧化的元素,可加在炉内。
35.钢中气体来源及其对钢质的影响:
钢中气体主要指氢和氮,一般来说氮的含量较高,且较难去除。
2)钢中氢、氮的来源及它们对钢质量的影响
1)钢中氢的来源及其对钢性能的影响
⑴来源:
炉气、原材料、冶炼和浇注系统。
①钢中氢主要来源于炼钢用原材料。
例如,石灰通常含有4—6%的水分,铁合金中也有少量水分。
炉衬和浇注设备(如未烘干的炉衬、钢包等)也是氢的来源之一。
②氢也可来自大气中的水分,尤其在雨季,空气湿度大,钢中往往有较多的氢。
⑵对钢质量的影响:
“白点”、氢脆、发纹、“鱼眼”、层状断口。
①钢中氢危害性极大,随着钢中含氢量的增加,钢的强度特别是塑性和韧性将显著下降,使钢变脆,称为“氢脆”。
②氢还是钢中“白点”产生的根本原因。
所谓“白点”,就是存在于热轧钢坯和大锻件内部的小裂缝,因其在钢试样的纵向断口上,多呈圆形或椭圆形的银白色斑点,故称“白点”。
但在其酸浸后的横向切上,却呈细小裂缝