煤基烯烃及其技术.docx
《煤基烯烃及其技术.docx》由会员分享,可在线阅读,更多相关《煤基烯烃及其技术.docx(12页珍藏版)》请在冰豆网上搜索。
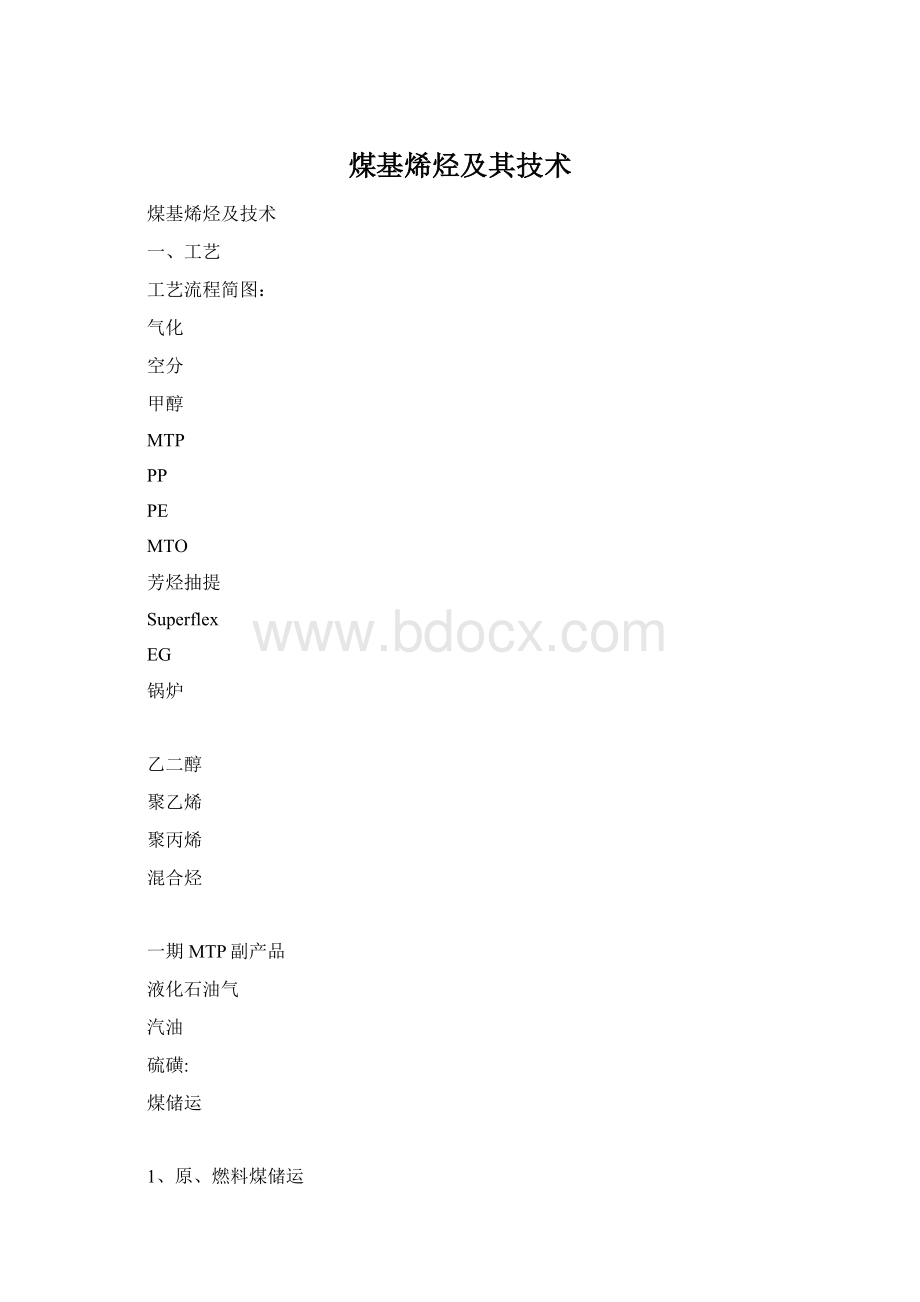
煤基烯烃及其技术
煤基烯烃及技术
一、工艺
工艺流程简图:
气化
空分
甲醇
MTP
PP
PE
MTO
芳烃抽提
Superflex
EG
锅炉
乙二醇
聚乙烯
聚丙烯
混合烃
一期MTP副产品
液化石油气
汽油
硫磺:
煤储运
1、原、燃料煤储运
以烟煤/无烟煤为原料,并将原煤制粉/水煤浆后,再被送入炉中加压气化的大型装置。
其原料采用有一定要求的烟煤/无烟煤,为了简化煤贮运系统的工艺流程,要求原、燃煤在配煤中心进行筛分破碎,原、燃煤(≤10mm的粒度)通过带式输送机送到装置区内。
2、气化工艺技术
目前世界上以煤为原料,用氧气及水/蒸汽作为气化剂生产以CO+H2为主要有用成分的煤气(粗合成气),再进一步生产甲醇和合成氨的工业化的气化工艺技术,有移动床、流化床和气流床三类。
现分别介绍其具有商业化业绩的煤气化方法如下:
2.1移动床(又称固定床)
该气化技术采用气体与块煤逆流接触模式,块煤向下移动,反应温度在600-1300℃之间,常用的有UGI间歇气化及鲁奇(Lurgi)加压气化,BGL加压气化(液态排渣)最近也有采用。
(1)UGI间歇气化
系在常压下操作,以块状优质无烟煤或焦炭为原料,先用空气吹入燃烧煤炭层,使其升温后,再送入蒸汽反应生成CO+H2,间断制气,由于吹风阶段放出的吹风气和造气废水对环境造成严重污染,且单炉产气量少,仅在我国中小型合成氨厂(含小型甲醇、联醇厂)中采用。
此造气技术在国外早已被淘汰;基于环境污染问题国内新项目也禁用此造气技术。
(2)鲁奇气化
在加压下采用5-50毫米的块状褐煤为原料,以氧气及水蒸汽作为气化剂。
此气化技术虽可连续加压气化,但气化温度仅~900℃,生成的粗煤气中含有大量甲烷,此气体用作城市煤气比较适合。
用于制合成氨,则在流程中经液氮洗涤后放出的大量甲烷馏份还要进行蒸汽转化及变换后才能作原料气使用。
因而流程复杂,加之因气化温度低,造气系统洗涤下来的废水中,含有大量的有机杂质——酚和氰等毒害物质,要回收及处理,但此处理难于达到环保要求,且又增加了生产成本。
我国在70年代,引进过一套日产千吨的氨厂,采用此气化技术;哈尔滨气化厂也引进过此气化技术联产城市煤气和甲醇。
此法引进后未获推广。
(3)BGL加压气化
BGL技术由英国煤气公司和鲁奇公司于二十世纪七十年代联合开发,开发出一种新炉型(BGL气化炉),BGL块煤/碎煤熔渣气化技术结合了熔渣气化和移动床加压气化技术的优点并克服了二者的不足,将鲁奇炉固态排渣改为熔融排渣,同时提高了气化反应温度,提高了块煤中粉煤的利用率,与鲁奇炉比BGL炉的气化效率和气体成分有了很大改进,废水排放量及组分有所减少,污染问题也有所改善。
现有一台工业示范炉在德国黑水泵厂运行,用于处理城市垃圾,所用原料为各种城市垃圾、废塑料和烟煤。
BGL炉气化废水主要来自炉内煤干燥干馏段,该气化废水中有机物含量高,处理难度较大,处理费用较高。
同时粗合成气中含有一定量的甲烷和苯及二甲苯等,不利于甲醇合成。
对于不联产燃料气的项目,甲烷等烃类合成气需进一步转化,将其再制成CO、H2,由此增加了消耗和投资。
2.2流化床
流化床的气化过程中,物料混合均匀,温度均一,常压温克勒炉气化炉及其改进型的(自朝鲜引进的)常压恩德气化炉,均属于此种炉型。
值得一提的是,1986年初在德国Berrenrath地方建成的加压高温温克勒炉,气化反应压力1.0MPa,温度900-950℃,粗煤气产量41667Nm3/h。
在国内常压恩德气化炉已在一些企业用于改扩建项目:
煤气化原料由焦改煤或由油改煤,以降低合成气成本;制取空气煤气做加热用燃料气。
常压恩德气化炉的不足之处在于常压气化,该煤气用于制取高压合成气(进一步制氨或甲醇)或氢气时,要多耗压缩功和中压蒸汽。
我国山西煤化所开发的灰熔聚流化床工艺,在流化床气化炉底部设计了中心射流管和环管。
通过中心射流管进入的高浓度氧形成局部高温使灰熔聚成球排出,此气化工艺尚未有大型工业化装置建成。
2.3气流床
国内大型煤气化装置一般采用气流床煤气化的技术,主要有水煤浆气化和粉煤气化技术。
粉煤气化技术包括壳牌(Shell)的多喷嘴干煤粉气化技术、GSP气化技术及PRENFLO等几种。
水煤浆气化技术有GE(德士古)的单喷嘴水煤浆气化技术、华东理工大学的多喷嘴水煤浆气化技术、西北化工研究院的单喷嘴多元料浆气化技术。
(1)粉煤气化技术
1)壳牌干煤粉加压气化法(荷兰Shell,SCGP气化技术)
SCGP气化技术是荷兰Shell公司多年开发的一种先进的气化技术,是第二代煤气化工艺之一。
该工艺采用纯氧、蒸汽气化,干煤粉进料,气化温度达1400~1600℃,碳转化率达99%,有效气体(CO+H2)达90%以上,液态排渣。
出气化炉的合成气温度1300—1500℃,用循环气体激冷冷却至900℃。
然后进入一个合成气冷却器(即废锅)进一步冷却,同时产生中压过热蒸汽,炉子采用了特殊的水冷壁结构。
2)(PRENFLO)粉煤气化工艺
德国克鲁伯-考柏斯公司与谢尔国际石油公司合作,在常压粉煤气化工艺基础上开发了加压粉煤气化工艺(加压K-T炉)。
在1981年以后,克鲁伯-考柏斯公司对该工艺又单独进行了开发,称为(PRENFLO)工艺。
1986~1992年在德国菲斯滕堡建立该工厂的示范厂,取得了成功;1992年在西班牙建设了采用该工艺气化技术的联合循环发电装置(IGCC),该装置目前正在进行商业化运行。
由于是用于发电,目前该工艺为干煤粉气化+废锅流程。
目前德国伍德公司着手改废锅工艺流程为激冷流程。
3)GSP气化技术
GSP气化技术原是德国未来能源公司开发的气化技术。
未来能源公司的前身是原民主德国的德意志燃料研究所DeutschesBrennsoffinstiuFreiberg(DBI),是当时东德从事与煤气化有关的各种技术研发最高研究机构,1956年成立于Freiberg,涉及的领域有煤的洗选、气体的生产、工艺气体的输送、储存气的综合利用及核技术。
1991年,DBI的气体生产部被NoellGMBH公司收购。
1999年,诺尔公司被BabcockBorsingPowerGMBH收购。
2002年9月1日BabcockBorsingPowerGMBH(巴巴高克能源公司)申请破产。
2002年未来能源公司成立并收购了巴巴高克能源公司。
目前,在Freibergde1的试验装置已气化了80多种气化原料其中包括了30多种不同的煤种(几乎涵盖了从褐煤到无烟煤的所有煤种),25种市政或工业方面的废渣、石油焦、油类、浆料以及20种液体废料。
气化试验在反应器压力4.0MPa条件下进行,使用纯氧作为气化剂。
该公司在Freiberg建有3MW气化装置(投煤量为7.2t/d)和5MW气化装置(投煤量12t/d,内径0.6m)的中试气化装置,至今设备完好。
1984年在德国黑水泵建成了130MW气化装置(投褐煤量720~750t/d,设计压力为3.0Mpa,工作压力2.5Mpa,产气量为50000Nm3/h,气化炉内径1.9m,压力容器外壳内径2.4m)。
气化原料是德国东部的褐煤,产品煤气与其它24台固定床加压气化炉(PKM)生产的煤气用作城市煤气。
到1990年,东西德合并后,城市煤气被改用天然气,PKM固定床气化炉部分停车,另一部分还在生产,因此该气化炉改烧液体焦油等原料,生产的煤气与其它气化炉产生的煤气用于生产12万吨/年甲醇,发电7.5MW。
改变气化原料后,采用该水冷壁气化炉一直运行至今。
与其他同类气化技术相比,该技术因采用气化炉顶干粉加料与反应室周围水冷壁结构,因而在气化炉结构以及工艺流程上有其先进之处,但工业化经验比较少。
(2)水煤浆加压气化
1)GE(德士古)水煤浆加压气化
GE(德士古)水煤浆加压气化法为目前世界上先进成熟的气化技术之一,它由GE(德士古公司)开发的,属气流床加压气化法。
是将煤(和/或石油焦)磨成水煤(焦)浆,掺入添加剂、助熔剂等形成粘度为800-1000CP,煤(焦)浆浓度为60-70%wt.的浆状流体,经加压后送入喷嘴,与纯氧一起经喷嘴喷入气化炉进行燃烧和部分氧化反应,气化反应温度为1300-1400℃。
炉子上部气化生成的热粗煤气,经用水激冷后,煤气被水蒸汽饱和并冷却,煤渣积存在气化炉底部水浴中间歇排出。
2)多喷嘴对置式水煤浆气化技术
该技术是由华东理工大学和兖矿集团共同开发,具有完全自主知识产权,已授权16项发明专利、11项实用新型专利。
经过二十多年的不懈奋斗与研究,目前,本项技术已经成熟,工艺指标先进,规模易于大型化。
3)多元料浆气化技术(MCSG)
多元料浆气化技术是由西北化工研究院开发的大型煤气化技术,其研究开始于20世纪60年代后期,经历了实验室探索研究和基础研究、技术开发等不同阶段,在完成中间试验和工业化示范试验基础上,于2001年实现工业应用。
该技术采用湿法气流床气化概念,以煤、石油焦、石油沥青等含碳物质和油(原油、重油、渣油等)、水等经优化混配形成多元料浆,料浆与氧通过喷嘴混合后瞬间气化,具有原料适应性广、气化指标先进、技术成熟可靠、投资费用低等特点,整套工艺以及料浆制备、添加剂技术、喷嘴、气化炉、煤气后续处理系统等已获得8项国家专利。
3、CO变换工艺技术
生产甲醇时煤气中的部分CO需经变换制氢,调控H2/CO,以满足甲醇合成时对合成气中的H2/CO要求。
CO变换反应式CO+H2O=CO2+H2
配合煤气化技术的CO变换系统,国内外均采用耐硫变换技术。
目前国内外得到较为广泛应用的钴钼系耐硫变换催化剂(国内又称为宽温变换催化剂),既耐硫又有很宽的活性温区,低温活性也很好。
使用该催化剂可将含硫煤气直接进行变换,使流程简化、热回收率高,可显著地降低能耗。
同时钴钼系耐硫变换催化剂可将煤气中COS等有机硫转化成易于脱除和回收的H2S,提高硫回收率、减少硫化物对环境的污染。
4、酸性气体的脱除工艺技术
本工段的任务是将变换气中的H2S、COS、CO2等酸性气体在气体进工段的压力条件下,进行脱除。
脱除变换气体中H2S、COS、CO2等杂质的方法很多,从工艺方法可分为化学吸收、物理吸收及物理-化学双吸收型,这三种方法在国内外均有工业化的生产实践。
化学吸收方法主要优点是:
吸收速度快,流程简单。
它是按化学反应计量进行的,故吸收压力对溶剂的吸收能力影响不大。
由于它吸收放热和解吸的吸热不能相互抵偿,所以它的能耗高。
物理吸收法主要优点与化学吸收正好相反,它的吸收机理是利用溶剂分子的官能团对分子(极性和非极性)的亲合力不同,而有选择性吸收气体。
溶剂吸收溶质(气体)时,一般遵循“亨利定理”;吸收能力只与被溶气体分压成比例的增加,而不受化学计量限制,因此在变换气中CO2等较多的情况下(即酸性气分压高的情况下)被广泛的采用。
物理-化学吸收法的特点则是将两种不同性能的溶剂混合,使溶剂既有物理吸收的功能又兼有化学吸收的功能,如Amisol法。
物理吸收法中按吸收温度的不同,一般分为热法和冷法,热法中以Selexol(如国内的NHD法)工艺最为著称,冷法则以低温甲醇洗法为代表。
5、硫回收
生产过程中原料煤含有的硫通过气化、变换,绝大部分进到低温甲醇洗装置分离出的酸性气体中并予以浓缩,浓缩气中的H2S含量≥25%,浓缩气送入硫回收装置回收硫。
含硫气体回收硫的方法比较多,有回收硫磺、也有回收硫酸。
在回收硫磺的各种不同工艺中,以克劳斯硫回收工艺(含尾气处理工艺)为好。
6、甲醇合成及精馏(含氢回收)
甲醇的工业生产始于1923年,德国BASF公司首先建成一套以CO和H2为原料,年产300吨的高压法甲醇合成装置,在全世界开拓了以合成气作为一种工业合成原料的生产史。
从20世纪20年代到60年代中期,世界各国甲醇合成装置都用高压法,采用锌铬催化剂。
1966年,英国ICI公司研制成功甲醇低压合成的铜基催化剂,并开发了甲醇低压合成工艺,简称ICI低压法。
1971年,德国Lurgi公司开发了另一种甲醇低压合成工艺,简称Lurgi低压法。
20世纪70年代以后,高压法因其自身的缺点已逐渐被淘汰,各国新建与改造的甲醇装置几乎全部用低压法。
低压合成法主要有Davy、Lurgi、Topsφe等方法,前两种被认为是当今较为先进的甲醇技术,技术都比较成熟,约80%的甲醇装置采用这两种方法生产。
低压合成法主要区别在于各种工艺所采用的反应器不同,反应热回收的方式也不同。
总的发展趋势是向生产能力大、单程转化率高、副产中压蒸汽、投资省、操作方便的方向发展。
较常用的合成反应器有冷激式反应器、管式反应器。
氢回收工艺技术方案以甲醇合成弛放气为原料获取高纯氢气工艺技术方案比较多,常用的有变压吸附PSA法、深冷分离法、膜分离法。
深冷分离法适合于规摸大、要求氢气纯度高的项目,但对于中、小规模装置投资大。
变压吸附PSA法适合于要求氢气高纯度的项目,规摸大、中、小均可,投资适中。
变压吸附(PSA)获取高纯氢的工艺技术成熟可靠,且其设备、材料国内已可成套供应。
膜分离法适合于投资要省,要求氢气纯度不高的项目。
7、MTO装置、MTP装置
乙烯和丙烯是现代化学工业中的重要基础原料,其需求量将越来越大。
制备乙烯和丙烯的传统方法是采用轻油(石脑油、轻柴油)裂解工艺,但石油储量有限,所以世界各国开始致力于非石油路线制乙烯和丙烯类低碳烯烃的开发。
其中,以煤或天然气为原料制甲醇,再由甲醇制低碳烯烃的工艺受到越来越多的重视。
目前石油价格高,今后石油价格也难于有大的降低,对于缺油少气的中国来说甲醇制低碳烯烃的工艺更为重要。
甲醇转化制低碳烯烃技术包括两种工艺:
甲醇转化以制乙烯和丙烯为主(MTO);甲醇转化以制丙烯为主(MTP)。
美国美孚石油公司(Mobil)对采用ZSM-5系列分子筛催化剂将甲醇转化为乙烯和较低级烃做了大量初始研究,Mobil的甲醇生产汽油(MTG)工艺已工业化。
在1985年Mobil在新西兰Montonui公司的甲醇制汽油(MTG)生产厂就已经投产。
甲醇转化为较低级烯烃的研究后来被用来制备C3烯烃(它易于聚成汽油和馏份油产品),Mobil的甲醇制烯烃(MTO)以及烯烃制汽油和馏份油(MOGD)工艺已经得到证明。
由于烯烃是甲醇制汽油反应的中间产物,所以甲醇制汽油技术的成功开发推动了后来甲醇制烯烃(MTO)、甲醇制丙烯(MTP)等工艺的开发。
甲醇制取烯烃的工业化研究也已进行了多年,国际上的一些著名的大石油和化学公司如美孚公司(Mobil)、巴斯夫公司(BASF)、埃克森石油公司(Exxon)、环球油品公司(UOP)、海德罗公司(NorskHydro)等都投入了大量的力量。
甲醇制烯烃的研究工作主要集中在催化剂的筛选和制备技术方面。
美孚公司(Mobil)提出了一种使用ZSM-5催化剂,在列管式反应器中进行甲醇转化制烯烃的工艺流程,并曾于1984年进行过9个月的中试实验,试验规模为100桶/天。
在工艺过程中,甲醇扩散到催化剂孔中进行反应,首先生成二甲基醚,然后生成乙烯,反应继续进行,生成丙烯、丁烯和高级烯烃,也可生成二聚物和环状化合物,以碳选择性为基础,乙烯收率可达60%(重),烯烃总收率可达80%(重),大体相当于采用常规石脑油/粗柴油管式炉裂解法收率的两倍,但催化剂的寿命尚不理想。
巴斯夫公司(BASF)采用沸石催化剂,1980年夏季在德国路德维希港建立了一套日消耗30吨甲醇的中试装置。
此法反应温度为300-450oC,压力为0.1-0.5MPa,用各种沸石做催化剂,初步试验成果是C2-C4烯烃的重量收率为50-60%,收率太低。
环球油品公司(UOP)筛选出的催化剂称作MTO-100,其主要成分是SAPO-34(即硅、铝、磷),SPAO-34虽然是理想的催化材料,但对流化床操作不是坚固耐用的材料。
因此,MTO催化剂是SAPO-34与一系列专门选择的黏合剂材料之结合体。
据推测,MTO-100中所采用的黏合剂是处理过的二氧化硅和氧化铝。
这种催化剂的选择性高于ZSM-5类催化剂。
于1995年6月和海德罗公司(NorskHydro)合作建设了一套粗甲醇加工能力为0.75吨/天的示范装置,装置连续运转了90天,各系统的操作都正常、顺利,打通了工艺的全流程,这套工艺称作MTO(MethanoltoOlefine)工艺。
在90天运转中催化剂经过450次反应-再生循环,其性能仍然非常稳定,反应后通过取样分析,催化剂的强度也满足要求,而且可以改变操作条件调节乙烯和丙烯的产出比例。
乙烯和丙烯的纯度均在99.6%以上,可直接满足聚合级丙烯和乙烯的要求。
1995年11月环球油品公司(UOP)和海德罗公司(NorskHydro)在南非第四次天然气转化国际会议上首次公布了他们联合开发的天然气经合成甲醇进一步生产烯烃(乙烯、丙烯及丁烯)的MTO过程及示范装置的运行数据,并称该过程已可以实现年产50万吨乙烯的工业化生产,可从环球油品公司(UOP)、海德罗公司(NorskHydro)获得建厂许可证,这套技术称作UOP/HydroMTO工艺。
环球油品公司和道达尔公司已在比利时建成一MTO示范装置,装置规模为原料甲醇1万吨/年,产品为聚合级乙烯和聚合级丙烯等,装置将在2008年年底投产。
该工艺将在尼日利亚推向商业化应用。
尼日利亚的天然气化工联合企业将采用UOP/Hydro公司开发的MTO工艺,建设7500吨/天甲醇装置,甲醇用作MTO进料,MTO设计生产40万吨/年乙烯和40万吨/年丙烯,乙烯和丙烯再用于生产40万吨/年HDPE和40万吨/年PP。
该联合装置原定于2006年投产,后因种种原因而修改为2012年投产,装置规模修改为10000吨/天甲醇(350万吨/年)、乙烯和丙烯为130万吨/年,目前该联合装置已进入详细工程设计阶段。
国内一些研究机构(如西南化工研究院、大连化学物理研究所、上海石油化工研究院等)也于上世纪90年代开始进行甲醇转化制低碳烯烃技术开发研究。
工作取得了与UOP接近的结果,为甲醇转化制低碳烯烃技术的国产化作了准备。
大连化学物理研究所等开发的DMTO甲醇转化制低碳烯烃技术取得了国国家专利,对于流化床反应系统的自主开发和工程放大也做了很多工作,其示范装置于2006年夏季取得了阶段性成果,并得到国家鉴定和认可。
国内第一套神华包头煤基烯烃项目的MTO工艺前面反应部分采用DMTO工艺,后面分离部分采用ABBLummus分离工艺。
Lurgi公司基于由德国南方化学公司(Sud-Chemie)提供的改性ZSM-5分子筛催化剂,开发了一种甲醇转化为丙烯的工艺(MTP)。
开发的甲醇制丙烯工艺采用固定床反应器。
2002年Lurgi公司的甲醇转化为丙烯工艺(MTP)示范装置已在挪威国家石油公司(Statoil)的甲醇装置上运行,Lurgi公司使它运转8000h以确认催化剂的稳定性,然后将建设工业规模的甲醇制丙烯装置。
2003年9月,Lurgi公司在该甲醇制丙烯示范装置上证实了该工艺的可行性,为进一步工业化放大和工艺流程的优化提供了可靠保证。
甲醇制丙烯工艺所用催化剂已经实现工业化生产,并且结炭量小,催化剂可进行原位间歇再生,再生温度较低(在反应温度下再生),对催化剂要求低,因此甲醇制丙烯工艺采用固定床反应器生产丙烯。
8、PE
聚乙烯(LLDPE/HDPE)的工艺技术根据反应条件的不同可以分为三大类:
气相工艺——在气相工艺中乙烯气体在流化床反应器(如Unipol工艺和BP工艺)或搅拌床反应器(如BASF工艺)中直接聚合生成固体聚合物。
淤浆法工艺——在淤浆法工艺中乙烯聚合形成悬浮在烃类稀释剂中的聚合物粒子。
淤浆法工艺又有四种反应器类型,即搅拌釜反应器(如Hoechst、旭化成);两段反应的搅拌釜工艺(如日产、三井);用异丁烷稀释剂的连续流动的环管反应器(Phillips工艺)及用C6或更重的稀释剂的连续流动的环管反应器(如Solvay工艺)。
溶液法工艺——在溶液法工艺中,溶解的乙烯聚合,形成也能溶解在反应溶剂(一般为环己烷或脂肪烃)中的聚合物。
有三种反应器类型,即中压(10.3MPa)反应器(如Nova)、低压(2.76MPa)冷却型反应器(如道化学)和低压绝热反应器(如DSM)。
聚合技术的进展主要归功于催化剂的进展,十多年来催化剂的活性及活性中心的控制手段已有明显的改进。
目前用于生产全密度聚乙烯的催化剂主要有三种类型;一种为铬基催化剂,是在硅胶或硅铝胶载体上浸渍铬络合物;另一种是钛基催化剂,是用化学键结合在含镁载体上的钛化合物;第三种是近年来开发的茂金属催化剂。
茂金属催化剂生产的聚乙烯具有分子量分布窄且分布均匀,加工性好等特点,其强度、透明性、低温热封性优于其他产品。
9、PP
聚丙烯(Polypropylene,缩写为PP)是以丙烯为单体聚合而成的聚合物,是通用塑料中的一个重要品种。
自20世纪50年代发明了聚丙烯Ziegler-Natta(Z-N)聚合催化剂并实现工业化以后,聚丙烯的生产、应用和工艺技术都得到快速的发展,聚丙烯逐渐成为最重要的热塑性产品之一,工艺技术也由最初的浆液法发展到了气相法。
目前,根据反应介质状态和反应器构型的不同,聚丙烯生产工艺主要有浆液法、液相本体法和气相法三大类。
浆液法工艺用溶剂作稀释剂,将丙烯和催化剂加入到几个串联的反应器中,在50-80℃、1-2MPa下进行聚合反应,生成的聚合物呈粉粒状悬浮在稀释剂中。
反应结束后的浆液经闪蒸脱除未反应的单体、催化剂残渣和无规物等,然后经干燥造粒得到成品。
主要生产工艺有Hoechst、Mitsui、BP、Shell和solvay等工艺。
目前世界上仍有使用浆液法工艺的装置在运行,用来生产高质量的产品,但新建聚丙烯装置一般不采用浆液法。
液相本体法工艺是在反应体系中不加任何溶剂,将催化剂直接分散在液相丙烯中,在50-80℃、2.5-3.5MPa条件下进行丙烯液相本体聚合反应。
以催化剂颗粒为中心的聚丙烯粉末在液相丙烯中不断生长,悬浮在液相丙烯中,随催化剂停留时间增长,聚丙烯颗粒在液相丙烯中的浓度增高。
作为连续生产工艺,催化剂连续计量加入反应器。
聚丙烯颗粒随液相丙烯(浆液)从反应器中不断流出,经闪蒸回收未聚合的丙烯单体,即得到粉末聚丙烯产品。
按照反应器形式液相本体工艺主要有液相釜式反应器工艺和液相环管反应器工艺,最典型的液相本体法工艺是LyondellBasell公司的Spheripol工艺,该工艺是目前世界上应用最广泛的工艺之一。
气相聚合工艺是丙烯在气相聚合反应器中直接气相聚合生成固相的聚合物产品。
该工艺工业化实现得最晚,但发展的很快,被认为是最有前景的工艺。
该工艺按反应器类型不同分为气相搅拌床工艺和气相流化床工艺,气相搅拌床工艺又分为立式搅拌床和卧式搅拌床两种工艺。
气相搅拌床工艺与流化床气相聚合工艺的差别是,反应器内气相单体的流动速度保持在流化速度以下,因此时空产率要比流化床气相聚合工艺高。
搅拌床工艺向反应器内通入液相丙烯,令其吸收聚合热后气化,可以有效取出聚合热。
Lummus公司的Novolen工艺为典型的立式搅拌床工艺,Ineos公司的Innovene工艺则是卧式搅拌床工艺的代表;流化床工艺主要有DowChemical公司Unipol工艺和LyondellBasell公司的Spherizone工艺。
这几种工艺在世界上都有广泛的应用,并且将会是未来采用最多的工艺。
二、产品用途及市场
聚乙烯和聚丙烯主要用于生产各种塑料制品,如薄膜、农膜、型材、板材、片材、管材、管件、编织袋、容器、泡沫制品、合成革、日用塑料品等等;乙二醇主要用于生产聚酯,进而生产涤纶纤维、饮料瓶等制品。
1、聚乙烯(简称PE)
聚乙烯是乙烯最重要的下游产品,聚乙烯消费量占世界聚烯烃消费量的70%,消耗了世界乙烯产量的52%。
聚乙烯可分为三大类,即低密度聚乙烯(LDPE)、高密度聚乙烯