金天源4000TPD压榨厂日常故障培训交流会议记录文本.docx
《金天源4000TPD压榨厂日常故障培训交流会议记录文本.docx》由会员分享,可在线阅读,更多相关《金天源4000TPD压榨厂日常故障培训交流会议记录文本.docx(25页珍藏版)》请在冰豆网上搜索。
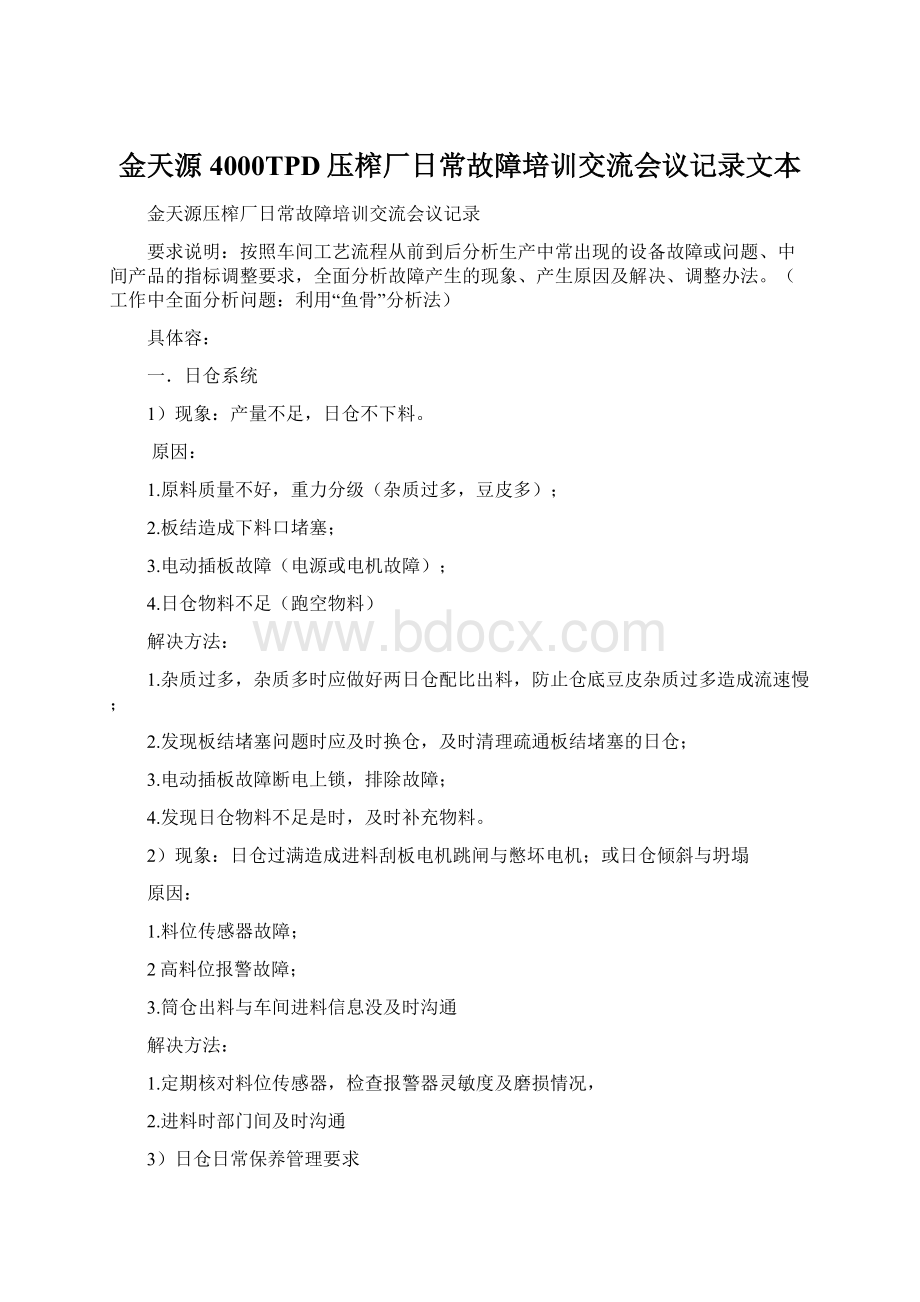
金天源4000TPD压榨厂日常故障培训交流会议记录文本
金天源压榨厂日常故障培训交流会议记录
要求说明:
按照车间工艺流程从前到后分析生产中常出现的设备故障或问题、中间产品的指标调整要求,全面分析故障产生的现象、产生原因及解决、调整办法。
(工作中全面分析问题:
利用“鱼骨”分析法)
具体容:
一.日仓系统
1)现象:
产量不足,日仓不下料。
原因:
1.原料质量不好,重力分级(杂质过多,豆皮多);
2.板结造成下料口堵塞;
3.电动插板故障(电源或电机故障);
4.日仓物料不足(跑空物料)
解决方法:
1.杂质过多,杂质多时应做好两日仓配比出料,防止仓底豆皮杂质过多造成流速慢;
2.发现板结堵塞问题时应及时换仓,及时清理疏通板结堵塞的日仓;
3.电动插板故障断电上锁,排除故障;
4.发现日仓物料不足是时,及时补充物料。
2)现象:
日仓过满造成进料刮板电机跳闸与憋坏电机;或日仓倾斜与坍塌
原因:
1.料位传感器故障;
2高料位报警故障;
3.筒仓出料与车间进料信息没及时沟通
解决方法:
1.定期核对料位传感器,检查报警器灵敏度及磨损情况,
2.进料时部门间及时沟通
3)日仓日常保养管理要求
1.配合其他部门做好日常保养及维护工作;
2.定期检查仓上物位计是否正常工作;
3.仓进料时,注意仓顶刮板的电流,定期记录刮板的空载、负载电流;
4.需定期检查筒仓仓顶是否渗漏(水),如有,及时维修;
5.操作中注意出料配比(不同原料的配比和仓底余料的配比);
6.同一原料生产时两仓交替使用,防止板结碳化;
7.计划停车要走空日仓存料;
8.日仓存料不宜超过2/3;
9.正常生产时日仓要保证一定料位,防止进豆砸仓底;
10.注意观察原粮豆有无霉变或碳化现象。
二.磁选问题
1)现象:
铁杂排放口漏豆
原因:
1.胶皮档板破损;
2.磁选器的磁筒磨损,导致运转时带料漏料
3.缓冲仓高报报警器故障造成料满溢流
解决方法:
1.定期检查胶皮磨损情况,即时更换;
2.定期检查磁筒的磨损情况,如磨坏,及时维修;
3.定期检查缓冲仓高位报警器,做好日常巡检。
2)现象:
铁杂口堵料
原因:
长期不清理,铁丝类搭桥造成
解决方法:
定时清理,观察疏通
3)现象:
1.进料量小;
2.布料不均;
3.LEG-102提升机有回料
原因:
喂料口被杂质或料块堵塞,造成下料量小;料门开度小
解决方法:
检查清理,及时调整料门或维修气缸
三.斗秤问题:
设备故障:
1.压缩空气不足,气缸损坏
2.出料料位传感器故障,
3.电磁阀故障,
4.行进开关故障,
5.称重软件故障,
6.系统程序故障,信号故障(受电磁或其它影响)
1)现象:
计量不稳或不准
原因:
1.进料量变小(仓底有杂质或锥底料板结搭桥、磁选器堵料)
2.来料比重变小(杂质太多)
3.缓冲仓堵料(需及时清空)
4.散料称故障(LS故障、电磁阀故障、称重传感器故障、接近开关故障、压缩空气压力不足)
5.出料口堵塞
6.设备清洁度不好,称量斗积满灰尘(导致计量精度发生变化)
7.校秤不准;
8.料门关闭不严
9.称量循环周期时间可调(可以改变称量速度)
解决方法:
1.保持清洁度;校秤按厂家规做好;
2.定期做好计量器和料门的保养与维护
3.正常生产时,按照要求巡检
2)现象:
斗秤不进料和不出料(计量不连续)
原因:
1.原粮杂质或豆皮多,造成称重不够,不排料
2.下料斗高位报警故障,无法排料
3.下料溜槽满料,无法排料
4.放料装置故障,无法排料
5.进料装置故障,不进料
6.程序故障造成不进料或不排料
7.压缩空气不足造成不进料或不排料
解决方法:
1.定期维护保养散料秤所有仪器仪表,损坏件及时更换(气缸,传感器,电磁阀,行程开关等);
2.定期清空缓冲仓防止缓冲仓重力分级(每班一次,根据实际情况增加清理次数);
3.对清理筛及时清理,防止料堵上去。
四.大豆清理筛问题
1)现象:
大杂中含豆
原因:
1.筛板过脏堵塞,没有定时清理;
2.分料板破损造成分料不均;
3.产量过大
4.振幅过大;
5.传动皮带打滑或没有力;
6.弹性球损坏;
7.筛网网孔选型小。
解决方法:
定时清理筛板,定期检查筛板,弹性球,分料板,传动皮带及弹性板损坏程度,做好保养和更换。
2)现象:
豆中含杂(杂质含量<0.5%,尽可能少)
原因:
1.筛板破损;
2.筛网网孔选型过大;
3.进料短路;
4.杂质颗粒小
解决方法:
1.定期检查更换破损筛板;
2.选用合适网孔筛板;
3.分配好筛子进料量
3)大杂进入后续工序的危害
1.造成系统堵料(特别是调质塔上方);
2.进入调质塔部后会有安全隐患(着火)
3.影响大豆调质的均匀性;
4.影响调质塔出料不均;
5.影响破碎机的喂料均匀性,从而影响破碎的粒度均匀性,影响产能
6.影响轧胚机的吃料和产能;
7.影响最终豆油的得率;
4)正产生产时需注意的事项
1.设备侧面漏料,由于安装时压条密封没有装好造成。
2.清理筛进料关风器可能容易被大块杂质卡死,生产中注意观察
3.注意进出料软连接情况,防止漏料
4.调整好吸尘风管风量,保证良好除尘效果
五.刹克龙风网系统
出现的现象:
1.除尘风管堵塞;
2.刹克龙出口大量粉尘飞出;
3.车间风网、设备漏灰严重,造成车间的环境卫生较脏
原因:
刹克龙的除尘工作效率降低
解决办法或影响因素:
1.风机选型和刹克龙的选型
2.刹克龙安装的垂直度以及固定情况
3.风管的进风速度
4.原料中粉尘的特型(颗粒、形状、大小、密度)
5.风网系统的密封(风管、关风器)
6.风网系统各点风压的平衡
7.风管、刹克龙部的清洁度
生产中注意事项:
1.每次停车及时检查和清理风管、刹克龙部的集料
2.开车、停车及时检查系统的密封情况
3.开车时,及时检查风网各吸点的压力是否平衡
4.开车时,及时检查各刹克龙的震动机固定情况
六.调质系统:
调质对原料起到升温软化(软化效果:
达到大豆无硬心),去水的作用;配合热风带去潮气,蒸发豆皮表面水分,为脱皮做初期处理。
(去水能力在1%~2%)
可能出现的现象:
1.调质后出料大豆水分偏高
2.调质后出料大豆的温度较低
3.调质出料大豆调质不均(部分豆子发现有白心)
1)影响调质塔去水的因素:
1.加热蒸汽的调节和各层蒸汽的分配调节
2.热风的温度(最高不能超过100℃)
3.热风总风量的调节以及各层热风的调配,和进出风的调整
4.风网系统的清洁度(风管无堵料)
5.疏水器的工作情况
6.产量的大小(在塔停留时间)
7.堵料搭桥,造成物料短路,局部流速过快
8.原粮豆的情况
9.上层料封
10.调质塔的整体保温
11.部加热列管漏
12.空气加热器漏
2)影响调质塔对大豆加温的因素:
1.加热蒸汽的调节和各层蒸汽的分配调节
2.热风的温度(最高不能超过100℃)
3.疏水器的工作情况
4.产量的大小(在塔停留时间)
5.堵料搭桥,造成物料短路,局部流速过快
6.原粮豆的情况
7.热风的进出风的调节
8.调质塔的整体保温
9.调质系统及风网系统是否漏气
10.豆子走自循环时间(刚开车)
3)影响调质塔调质不均因素:
1.出料速度不均(平衡分配出料速度,对于不同品种的原粮调整不同的速度)
2.不同原料配比造成加热不均(在原粮配比过程中尽量的均匀混合配比)
3.加热蒸汽的调节和各层蒸汽的分配调节不均(尽量开大上层蒸汽,增加加热时间)
4.热风总风量的调节以及各层热风的调配,和进出风的调整不均(下层进出风调整大一些,因为下层去水能力强)
5.堵料搭桥,造成物料短路,局部流速过快(定期清理堵料搭桥)
6.由于风管堵塞造成风网系统不均(注意风网系统压力,对于堵塞的管道即时清理)
7.疏水器的故障造成受热不均(注意疏水器巡检,损坏的即时更换)
4)调质塔的一些问题故障及注意事项:
1.顶部进料段要保证一定的料封,防止风选系统和调质塔进出风的平衡
2.进料格栅板堵塞搭桥,在清理环节尽量保持良好的清理效果,需要定期对格栅板进行清理
3.对于部搭桥板结要及时清理防止物料短路,并预防火灾
4.出料辊的间隙调节好(不超过大豆直径的3/4),防止漏料。
如果有漏料现象,需要调整出料频率来调整正常产量
5.一旦出料系统故障或后续设备故障需要很长时间停车,我们可以通过调节出料辊间隙将料排除,防止着火和碳化板结。
6.调质的蒸汽安全阀保证安全可靠,灵活可用,压力不能超过1.2bar,(要经常检查校验安全阀的情况,尤其在开车送蒸汽的时候)。
调质塔列管最大承压1.5bar,超过会造成列管爆炸。
7.如果部加热列管漏,通过视镜观察,关闭相应蒸汽阀门,待维修更换
8.如果疏水器故障,关闭相应蒸汽阀门,及疏水前后阀门,打开舒服旁通,待管路无蒸汽和热水后进行维修更换
9.由于不同品种原料豆的直径不同,相同产量的出料频率不同,注意调整。
10.产量主要由出料绞龙控制,根据下料斗的料位情况控制好出料辊速度
11.蒸汽的使用上上层加热蒸汽尽量开大,保证充足的加热时间保证软化效果
七.破碎机环节
利用两只破碎辊锋对锋的方式将豆子进行咬合,利用两辊速度差进行剪切的过程。
实际情况下一次破碎至2~3瓣,二次破碎后达到4~6瓣。
可能出现的现象:
1.破碎豆种仍含有完豆
2.破碎后粉末度较大
3.豆瓣的均匀性较差
4.破碎豆的豆瓣太大
5.破碎机辊子不吃料
1)破碎后仍含整豆的原因
1.三尖档板磨损漏料
2.原料粒度不均,部分豆子颗粒度太小
3.车间漏料清理后返料造成
4.豆皮风网系统将豆吸走
2)破碎后粉末度较大的原因
1.豆子水分太低
2.调质不均匀,
3.辊子间隙过小;
4.速度差过大;
3)豆瓣均匀性较差?
1.喂料不均匀;
2.间隙不均匀;
3.原料的粒度不均匀;
4.辊子波纹磨损不均匀;
4)破碎后豆瓣太大?
1.辊间间隙太大;
2.辊子波纹磨损严重;
3.产量太大
5)破碎辊吃料下降(或辊子间料堆积严重)
1.辊子间隙太小
2.来料流量太大;
3.破碎辊磨损严重;
4.破碎辊的齿形不对
6)影响破碎效果的因素
1.来料的水份和温度
2.原粮的质量(品种大小不同和杂质的多少)
3.铁杂对破碎辊的损伤
4.破碎辊安装的水平度
5.破碎辊间隙调整情况
6.破碎辊的磨损情况
7.布料的均匀程度
8.三尖档板的情况
9.传动皮带情况
10.产量的大小
6)破碎辊轴承容易损坏的因素:
1.喂料不均,导致受力不均
2.安装时轴承座水平度的的调整
3.皮带打滑
4.润滑油不足造成损伤或润滑油过多不利于散热(加油原则:
少量分多次加油)
5.喂料中铁器的影响
7)开停破碎机的原则:
1.开启破碎的时候需要先开主电机(分辊状态下启动)从下往上开启,先开二破再开一破。
2.开启主电机后再喂料,根据产量,破碎机电流和破碎情况调整辊间距,要有安全间隙不能出现撞辊现象
3.停止破碎机的时候需要走空料箱并对喂料辊进行人工清料,待没有物料进入破碎辊后分辊停止破碎机电机,先清一破后清二破,由上往下停止。
八、CCC,CCD系统
要求:
在在保证豆皮残油的情况下尽量低的条件下多脱皮
出现的现象:
1.脱皮豆仁中含皮量较高
2.皮种含豆仁、粉较高,豆皮残油较高
1)影响CCD、CCC脱皮效果的因素:
1.循环总风量的大小以及各台CCD、CCC的风量、风压的平衡
2.循环风的温度
3.循环风的进出风配比
4.原粮的品质(水分和豆皮含量)
5.调质效果(温度和水分)
6.破碎效果(破碎粒度和粉末度)
7.进出料的稳定性,进出需平衡并有一定料封
8.布料是否均匀
9.部列管搭桥堵料,造成原料短路
10.CCC,CCD的密封性(密封不好造成风压不稳)
11.空气加热器漏造成循环风湿度大
2)如何检查CCC,CCD的密封
1.利用U型计在落料口检测风压
2.打开取样门利用手感触负压
3)在CCD、CCC操作中的要求
1.在喂料阶段要保证来料的稳定性
2.保证进出料段有一定的料封保证系统密闭性
3.风量调整要保证不能吸入豆粒
4.定期维修要清理列管搭桥堵料,确保部清洁度
5.CCC,CCD有一定的出水能力,注意水分和热风的控制
6.及时检查和巡检系统风压的稳定性
7.及时检查和巡检各台CCC、CCD的风量、风压平衡
九.轧胚环节:
通过两辊对破碎豆粒的挤压及辊间速度差的剪切作用达成轧胚作用,胚片厚度控制在0.25~0.35mm之间。
过薄或过厚都不利于油的浸出。
如何检测胚片厚度的方法:
对轧胚机辊划分5(3)个区域(今后要做好标识)进行取样存放;然后对每个区域的胚片进行四分法,在每一份中随机取出4~5片进行叠加测量并算出平均值,再对4份的平均值核算平均值,得出一个区域的胚片厚度;最后把5点(3点)的厚度平均,即得出该台轧胚机的胚片厚度。
(在读取数据时误差在±0.01mm)
出现的现象:
1.轧胚机胚片厚度不均匀;
2.胚片中有破碎豆仁
3.轧辊不吃料,辊间堆积物料
4.轧辊间碰闯
5.轧胚机轴承温度升高
6.轧胚机皮带打滑
1)防止轧胚机撞辊现象的方法
1.合辊的间隙要调整合适的安全间隙
2.轧辊常检查,由于磨损造成的凹凸不平要进行磨辊
3.要定期对倒角进行磨辊保养
4.在生产中调整好喂料启动与合辊时间
2)影响轧胚效果的因素
1.液压系统压力(总压,单机辊压,压力传感器,液压油箱有无空气,液压油的油量)
2.布料的均匀度和喂料的稳定性
3.原料的品种和品质
4.来料水份和温度
5.破碎的粒度
6.刮刀位置的调整
7.三尖挡板的磨损度
8.轧胚辊的磨损情况以及辊的温度
9.整体轧胚的进料分配(8台)
10.干燥风的温度和风量
3)轧胚机的轧辊不吃料(吃料条件:
啮入角小于摩擦角)
1.破碎豆仁颗粒太大
2.豆粕豆中杂质含量影响落料
3.喂料辊喂料不均,局部料大多
4.豆软化过度,豆仁表面出油
5.轧辊间隙太小
6.轧辊表面有潮汽、油
7.加工产能过大
4)胚片中有碎豆仁原因
1.三尖挡板磨损严重
2.轧辊磨损严重,导致轧辊是椭圆或锥状
5)轧胚机轴承温度升高原因
1.轴承缺润滑脂
2.加注润滑脂过多,导致热量无法散失
3.轧胚机的加工产能过大
4.轧胚机的轧辊吃料不均匀(导致局部吃料)
5.轧胚机的四只轴承座的平面度(标准小于1.6mm)
6.轧胚机的轴承游隙不对(过小)
6)轧胚机皮带打滑
1.皮带比较松弛
2.喂料中含铁器(特别是大的铁器)
3.皮带或皮带轮表面有油
十.膨化环节:
膨化就是利用蒸汽对物料进行加温加湿加压的作用,利用出腔压力差破坏细胞壁结构的过程。
出现的现象:
1.膨化料的温度不够
2.膨化料不松散,硬心、实心
1)如何判断膨化效果的好坏:
1.出料表面有游离的油,接出后看看是否有回吸效果
2.吹:
将条状料握于手中进行吹气,用手感觉透气性
3.掰:
将料掰开,查看断面中心是否有硬心
4.搓:
将料用手心进行一次碾压,查看散料的形状和粉末度
2)影响膨化效果的因素:
1.来料的温度和水份
2.蒸汽压力和质量
3.液压模头的压力和模头形状
4.蒸汽的压力分配
5.蒸汽喷头堵塞
6.传动皮带打滑
7.膨化温度的设定
3)膨化蒸汽的分配
1.喂料段少用蒸汽,防止蒸汽过大造成不吃料和堵料,起到一定的物料润滑即可
2.蒸汽重要加于加压段,充分与物料接触,进行加温加湿加压的作用,利用剪切销的作用充分糊化物料,并起到润滑防止电机电流过高作用
3.排料段少用或不用,只起到润滑物料作用,对物料的作用不大,有利于节能。
十一、冷却器环节
通过利用空气与物料充分接触进行能量交换,去除物料水份并降低物料温度。
(传质传热)
1)影响冷却器调解水份的因素:
1.物料的均匀分布(360°旋转布料器起到均匀分布料的作用)
2.来料的质量(水份和温度)
3.料层高度的控制(停留时间的控制)
4.出料速度的控制(利用翻版限位开关控制)
5.系统的风量
6.热风风温的控制(温度<100℃,最好控制在90℃以下)
7.体壁整体的密封度
8.空气加热器漏
2)冷却器着火的危害性大,应注意几点:
1.热风温度<100℃
2.系统的积存料要即时清理
3.空气加热器定期清理防止粉尘着火
4.在开停机中要按照安全操作去做
十二、浸出系统
利用适量溶剂(正己烷/6号溶剂油)对胚片/膨化料采取逆流浸出提取物料中的油脂过程。
出现的现象:
1.栅板堵料
2.喷淋沥干效果较差
3.溶剂蒸汽倒流至预处理
4.混合油中粉末度较高
5.浸出器正压
6.胚片残油较高
7.浸出器爬行
1)溶剂蒸汽倒流至预处理的原因
针对此原因从以下三方面考虑
A、首先防止大量溶剂气体的产生
1.入浸料温度的控制
2.溶剂温度的控制
3.新鲜溶剂、混合油循环量的控制
B、尽量排除浸出器的溶剂蒸汽
1.尾气风机风量的控制调整(风量的大小)
2.浸出器冷凝器的良好工作状态(换热管是否结垢、堵塞)
3.循环水的量、温度
4.DT正压太高,蒸汽倒串至浸出器
C、如有溶剂气体,采取措施尽可能减少溶剂通入DRG132刮板的可能性
1.浸出器进料箱的料封
2.入浸密封绞龙配重门良好的工作状态
3.安全风机FAN201的运行
4.停车时密封插板GAT201是否关闭
2)浸出器喂料密封绞龙、喂料刮板堵塞或故障原因
1.来料水份过大
2.误入杂物将绞龙卡死(DRG-132掉刮板或回填料杂物)
3.来料量过大(产量过大或瞬时来料过大)
4.浸出器喂料箱堵(板结块料)
5.浸出器进料料位传感器,报警器故障,造成料位过高
6.密封绞龙配重门故障
7.设备尾轮失速报警故障
8.设备自身故障(电机,联轴器,减速机,传动链条)
9.浸出器转速过慢(手动状态没有调整好)
10.DT正压蒸汽倒串进浸出器造成绞龙出口料过湿造成堵料
3)浸出器混合油喷淋、沥干效果较差原因
1.入浸料的情况(水份,温度,粉末度,膨化效果)
2.溶剂喷淋量过大
3.溶剂含水
4.溶剂温度过低
5.混合油循环量过大或没有调整好
6.料层与油斗的气象压力平衡不好
7.筛板堵塞
8.油格液位过高
9.浸出器转速过快
10.产量过大
11.物料豆皮的含量
12.DT蒸汽倒串进浸出器,造成系统气象压力不好
13.消防蒸汽漏
4)混合油中粉末度较高原因
1.来料自身的粉末度高和水份低(水份过低浸出过程也会造成粉末度高)
2.筛板的间隙大或筛板有漏点
3.喷淋量过大,料层上液位过高,从平衡管溢流进油格
4.开停车或故障停车时料层过低,直接被冲进油格
(注:
油格椎体部分有个冲洗管,利用涡流作用使沉积的料悬浮,正常生产时冲洗管道的阀门开启)
5)浸出器正压原因
1.来料温度过高
2.溶剂温度过高
3.溶剂喷淋量过大
4.渗透效果不好(来料的水份,粉末度,膨化效果等)
5.尾气风机风量不足
6.尾气系统的吸收塔液位过高尾气进口堵塞
7.浸出器冷凝器效果较差(换热管结垢、循环水量不足、循环水温度较高)
8.气密性不好
9.DT蒸汽倒串
10.消防蒸汽漏或误开
6)胚片残油较高的原因
1.来料情况(全面分析入浸料杂质、水份,温度,粉末度,膨化效果等)
2.溶剂质量(正己烷含量、界点常数)
3.溶剂温度
4.溶剂含水
5.溶剂含油(液泛造成)
6.溶剂与物料的配比
7.产量过大
8.混合油循环量的调节
9.混合油溢流进湿粕刮板
10.浸出器进料段豆粕塌陷飘入刮板DRG208
11.浸出器料层不均匀
12.喷淋槽堵塞造成溶剂短路
13.物料中有碎豆(轧胚漏料或回填料)
14.浸出器转速的调整
15.取样代表性和准确性
16.浸出器输送刮板链条摩擦静电会影响溶剂的极性
8)浸出器爬行原因
1.链条紧度不好(链条松)
2.筛板的安装问题(栅板接头处最好不要有阶梯,如有最好沿输送链条运行方向降低)
3.传动链条和链条轮故障(咬合不好)
4.不同料段的物料比重不平衡(来料不均或水份因素)
十三、DT、DC蒸脱、干燥冷却系统
利用直接蒸汽、间接蒸汽蒸脱除湿粕里面的溶剂以及调整豆粕中的抗营养因子;利用热风、冷风对豆粕进行干燥、冷却,达到储藏、运输的要求。
出现现象:
1.DT气相温度过高、过低
2.DT气相压力较高
3.DT出料温度较低
4.DT出料残溶较高
5.DT、DC部物料接团严重
6.DC出料水分较高、较低
7.DC出粕中含有黑点(颜色不正常)
1)影响DT气相温度的因素
1.来料的温度(刮板、浸出器的保温效果;浸出物料)
2.来料产量稳定性
3.来料含溶情况
4.DT料层的控制(特别是DT第四层料位的控制)
5.直接蒸汽量
6.直接蒸汽的质量(温度和含水量)
7.间接蒸汽量、疏水系统是否正常
8.零排放的蒸汽稳定性
9.直接蒸汽孔是否堵塞
10.蒸汽阀门的实际开度(有效工作开度)
11.DT顶层气象温度的设定值
2)影响DT气相压力的因素
1.来料含溶情况
2.来料温度情况
3.料层高度(特别是DT第四层料位)
4.间接气不足或疏水器故障
5.间接蒸汽法兰或管漏
6.直接蒸汽过大
7.气相温度设定过高
8.沙克龙堵塞
9.DT气密性不好(特别是管道、视镜、人孔、温度计接口、压力计接口等接口密封)
10.DT冷凝器堵塞或结垢
11.循环水量不足、温度高
12.尾气风机风量不足
13.DC进料关风器漏风
3)影响DT出料温度的因素
1.来料温度低
2.来料含溶高
3.来料不稳定
4.料层控制过低(滞留时间不足,特别是第四层,开停车注意)
5.间接汽不足或疏水器故障
6.直接蒸汽不足
7.气相温度设定过低
8.直接蒸汽孔是否堵塞,造成蒸汽短路
4)影响DT出料粕残溶的因素
1.来料含溶高
2.来料的稳定性
3.整体的产量大小
4.料层的控制(物料滞留时间)
5.间接气不足或疏水器故障
6.直接蒸汽质量和压力流量
7.气相温度设定过低
8.沙克龙捕集器溶剂喷淋过大
9.打入油脚量(包括质量和流量)
10.DT冷凝器堵塞或结垢
11.循环水量不足、温度高
12.尾气风机风量
5)DT、DC部物料接团因素
1.打入油脚量和含水量
2.直接蒸汽含水大
3.零排放供直接蒸汽含水
4.间接蒸汽漏
5.溶剂含水
6.回填料中含块多或水份大
6)影响DC出料水分的因素
1.风机的风量(正常生产风量一般不要调节)
2.热风的温度(最高温度不要超过140℃)
3.来料的水份情况(预处理来料、溶剂含水情况)
4.来料的稳定性和料层的控制
5.物料的产量不稳定
6.DT部间接蒸汽管、法兰连接处漏蒸汽
7.空气加热器漏
7)DC出料中含有黑点(颜色不正常)
1.原粮豆有碳化现象(黑豆或赤豆)
2.DC中豆粕的长期堆积烤糊
3.DT,DC绞刀根部堆积烤糊
4.设备故障扒料会有碳化料的回填(特别是DT故障)
十三、蒸发系统
在真空条件下,利用热源(蒸汽)把混合油里面的溶剂蒸发掉。
出现的现象
1.蒸发系统真空较低
2.蒸发系统/汽提塔液泛
3.毛油残溶较高
1)蒸发系统真空较低原因
1.蒸发系统的气密性(法兰、泵机械密封、视