机械系毕业设计论文排版模版.docx
《机械系毕业设计论文排版模版.docx》由会员分享,可在线阅读,更多相关《机械系毕业设计论文排版模版.docx(12页珍藏版)》请在冰豆网上搜索。
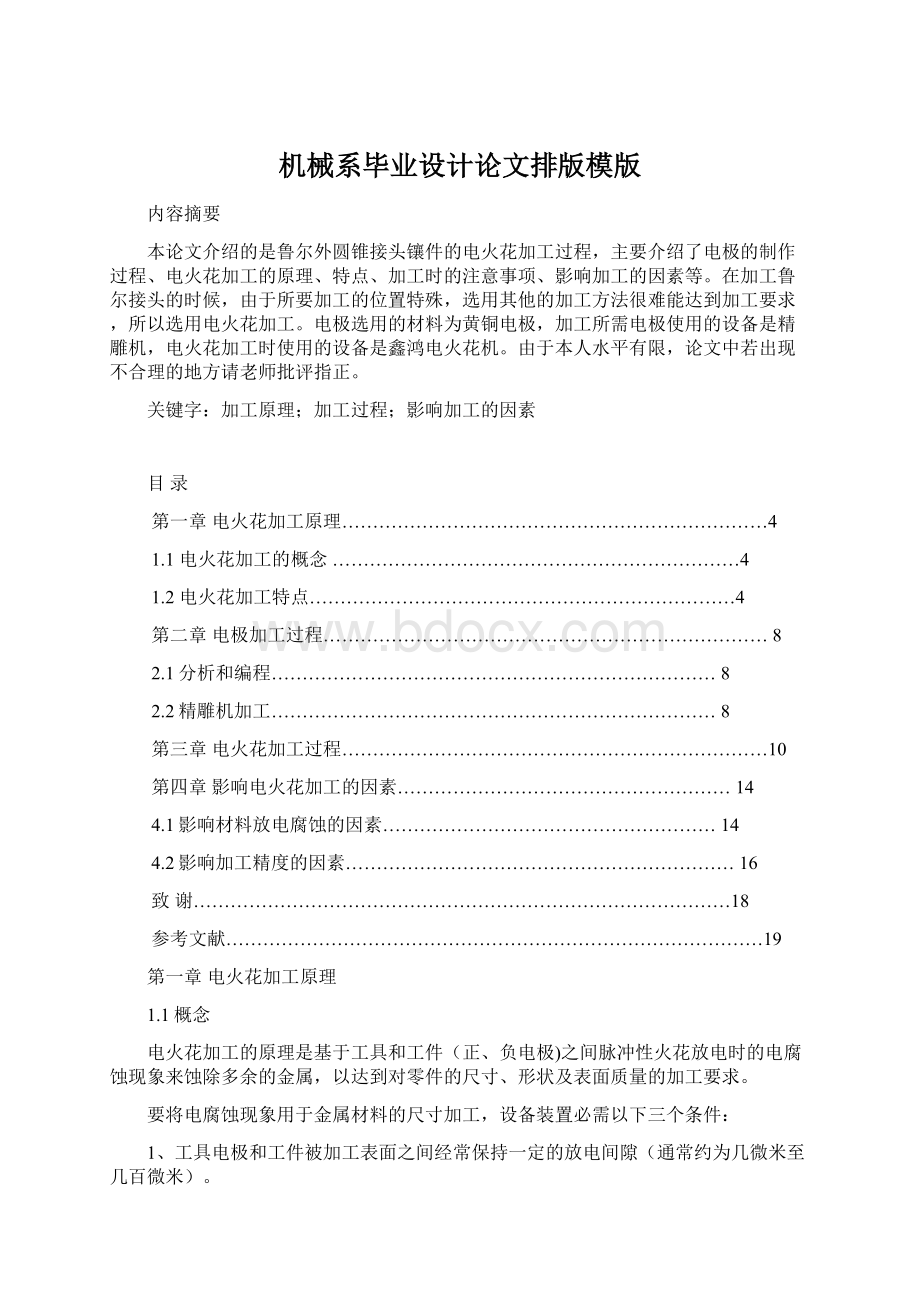
机械系毕业设计论文排版模版
内容摘要
本论文介绍的是鲁尔外圆锥接头镶件的电火花加工过程,主要介绍了电极的制作过程、电火花加工的原理、特点、加工时的注意事项、影响加工的因素等。
在加工鲁尔接头的时候,由于所要加工的位置特殊,选用其他的加工方法很难能达到加工要求,所以选用电火花加工。
电极选用的材料为黄铜电极,加工所需电极使用的设备是精雕机,电火花加工时使用的设备是鑫鸿电火花机。
由于本人水平有限,论文中若出现不合理的地方请老师批评指正。
关键字:
加工原理;加工过程;影响加工的因素
目录
第一章电火花加工原理……………………………………………………………4
1.1电火花加工的概念…………………………………………………………4
1.2电火花加工特点……………………………………………………………4
第二章电极加工过程………………………………………………………………8
2.1分析和编程………………………………………………………………8
2.2精雕机加工………………………………………………………………8
第三章电火花加工过程……………………………………………………………10
第四章影响电火花加工的因素………………………………………………14
4.1影响材料放电腐蚀的因素………………………………………………14
4.2影响加工精度的因素………………………………………………………16
致谢……………………………………………………………………………18
参考文献……………………………………………………………………………19
第一章电火花加工原理
1.1概念
电火花加工的原理是基于工具和工件(正、负电极)之间脉冲性火花放电时的电腐蚀现象来蚀除多余的金属,以达到对零件的尺寸、形状及表面质量的加工要求。
要将电腐蚀现象用于金属材料的尺寸加工,设备装置必需以下三个条件:
1、工具电极和工件被加工表面之间经常保持一定的放电间隙(通常约为几微米至几百微米)。
间隙过大,极间电压不能击穿极间介质,因而不会产生火花放电。
间隙过小,会形成短路,不能产生火花放电,而且会烧伤电极。
2、火花放电必须是瞬时的脉冲性放电,放电延续一段时间后,需停歇一段时间,放电延续时间一般为10-7~10-3s。
这样才能使放电所产生的热量来不及传导扩散到其余部分,把每一次的放电点分别局限在很小的范围内;否则,象持续电弧放电那样,使表面烧伤而无法用作尺寸加工。
为此,电火花加工必须采用脉冲电源
3、火花放电必须在有一定绝缘性能的液体介质中进行
例如煤油、皂化液或去离子水等。
液体介质又称工作液,它们必须具有较高的绝缘强度(103~107Ω·cm)以有利于产生脉冲性的火花放电,同时,液体介质还能把电火花加工过程中产生的金属小屑、碳黑等电蚀产物从放电间隙中悬浮排除出去,并且对电极和工件表面有较好的冷却作用。
1.2电火花加工特点
1、电火花属于不接触加工
工具电极和工件之间并不直接接触,而是有一个火花放电间隙,这个间隙一般是在0.05~0.3mm之间,有时可能达到0.5mm甚至更大,间隙中充满工作液,加工时通过高压脉冲放电,对工件进行放电腐蚀。
2、加工过程中没有宏观切削力
火花放电时,局部、瞬时爆炸力的平均值很小,不足以引起工件的变形和位移。
(1)可以“以柔克刚”
由于电火花加工直接利用电能和热能来去除金属材料,与工件材料的强度和硬度等关系不大,因此可以用软的工具电极加工硬的工件,实现“以柔克刚”。
(2)可以加工任何难加工的金属材料和导电材料
由于加工中材料的去除是靠放电时的电、热作用实现的,材料的可加工性主要取决于材料的导电性及热学特性,如熔点、沸点、比热容、导热系数、电阻率等,而几乎与其力学性能(硬度、强度等)无关。
这样可以突破传统切削加工对刀具的限制,可以实现用软的工具加工硬、韧的工件甚至可以加工聚晶金刚行、立方氮化硼一类的超硬材料。
目前电极材料多采用紫铜或石墨,因此工具电极较容易加工。
(3)可以加工形状复杂的表面
由于可以简单地将工具电极的形状复制到工件上,因此特别适用于复杂表面形状工件的加工,如复杂型腔模具加工等。
特别是数控技术的采用,使得用简单的电极加工复杂形状零件成为现实。
(4)可以加工特殊要求的零件
可以加工薄壁、弹性、低刚度、微细小孔、异形小孔、深小孔等有特殊要求的零件。
由于加工中工具电极和工件不直接接触,没有机械加工的切削力,因此适宜加工低刚度工件及微细加工。
图1-1内中心孔电极图
图1-2轴向电极图
图1-3镶件图
第二章电极加工过程
2.1分析和编程
一、分析零件图样和工艺要求
分析零件图样和工艺要求的目的,是为了确定加工方法、制定加工计划,以及确认与生产组织有关的问题,此步骤的内容包括:
1. 确定该零件应安排在哪类或哪台机床上进行加工。
2. 采用何种装夹具或何种装卡位方法。
3. 确定采用何种刀具或采用多少把刀进行加工。
4. 确定加工路线,即选择对刀点、程序起点(又称加工起点,加工起点常与对刀点重合)、走刀路线 、程序终点(程序终点常与程序起点重合)。
5. 确定切削深度和宽度、进给速度、主轴转速等切削参数。
6. 确定加工过程中是否需要提供冷却液、是否需要换刀、何时换刀等。
二、数值计算
根据零件图样几何尺寸,计算零件轮廓数据,或根据零件图样和走刀路线,计算刀具中心(或刀尖)运行轨迹数据。
数值计算的最终目的是为了获得数控机床编程所需要的所有相关位置坐标数据。
2.2选用精雕机加工电极
第一步:
清理工作台,工作台必须清理干净,确保无残渣。
第二步:
准备毛坯料,去除毛刺后装夹在工作台上。
第三步:
加工
1、装刀,选择8毫米刀具开粗,注意刀的长度不要撞到电极坯料。
2、对刀,按MDI,按T键,启动;清理刀具上残留废渣;按MDI,开转速,一万转。
S10000,M03。
切削电极上表面,削成平面。
(推平)
3、输入零点,分中。
Y轴,M88,M99。
X轴,M66,M77。
4、抬升刀具,停止转速,在电脑中选择程序。
5、用机器执行,串口2。
选中刚才所确定的程序,确定,启动。
6、按照程序加工,加工完成后按照程序要求换刀。
7、所有程序加工完成后,检查电极是否与所需电极有出入(是否有磨损、缺角等)。
图2-1电极图例
第三章电火花加工过程
第一步:
清理工作台。
确保工作台上没有渣滓,用手触摸没有粗糙的摩擦感。
图3-1空工作台
第二步:
装夹电极。
选用合适的夹具装夹电极,装夹时注意电极基准角方向应该于图纸一致。
图3-2装夹电极
第三步:
校正电极。
首先校核前后方向,确保误差在一个格(分度值1纳米)以内,其次校核X方向和Y方向,同样确保误差在一个格以内。
全部校核完成后再重复检查一次,确保电极装夹位置没有发生偏差。
图3-3校核电极前后方向图3-4校核电极X方向
图3-5校核电极Y方向
第四步:
校核模具。
本文中的模具即鲁尔接头,将鲁尔接头按照图示放在工作台上,模具基准与电极基准应对应。
校核鲁尔接头上的平面,校核完成后用六角匙吸紧工作台。
第五步:
分中。
用手摇动机床手柄(任选X/Y其中一个轴),先使电极基准平面与模具一侧碰触(碰触时机床蜂鸣器打开),靠近时减慢速度缓慢摇动,蜂鸣器报警说明已经接触,然后将两个轴归零。
用目测观察电极与模具接触时是否有缝隙或者渣滓,退出接触后用压缩空气枪清理接触面。
重复碰触检验,将所碰触的位置设置为该轴零点。
摇动手柄到该轴另一侧进行碰触,接触后记住数字,此数字即为模具在该轴方向上的长度。
重复碰触,检查数字是否一致,保证误差在5微米内,然后将该数字除以二,得到该轴中点。
另一轴也是用同样的方法分出中点,两个轴的交点就是模具的中心点。
图3-6两轴归零
图3-7碰触X轴
图3-8X轴除二
第六步:
定Z轴零点。
将Z轴抬高,摇动手柄使电极位置在模具正上方。
按照图纸,用电极基准面或者最高面与模具最高面进行碰触。
具体操作为:
按键“靠模放电”,电极自动下降去碰触模具,接触后在接触位置产生连续不间断的火花,停止放电,设置Z轴深度为0。
(或者抬升Z轴使电极位于模具正上方,按键“Z轴自动靠边”,Z轴接触模具后会自动归零。
)
第七步:
设定加工深度。
在机器上输入要加工的深度与电流等参数,具体操作为:
粗加工设置加工两段,电流为5A和3A,周率为120和70,放电间隙为1秒,抬升高度和积碳调整高度设置为抬高5毫米。
粗加工第一段应加工到距离所需加工深度0.3毫米,然后进行第二段粗加工。
粗加工应为精加工留10个丝(0.1毫米)的余量。
精加工设置加工电流为2A和1.5A,周率为50和30,放电间隙为0.5秒,抬升高度与积碳调整高度不变。
精加工第一段打7个丝,第二段打3个丝。
(周率在机器上默认是电流的30倍,可以按照要求考虑加工情况进行设置)。
图3-9粗加工参数
图3-10精加工参数
第八步:
加工。
按照设置好的参数进行加工,开切削液,冲洗加工位置。
第九步:
清理工作台。
加工完成后清理机床工作台,拆卸电极和模具,用切削液将废渣等冲洗干净,然后摇动手柄将机床主轴移动到中间的位置。
注意事项:
1、注意机床主轴位置应适当,不要太高或太低。
2、电极有两种,四个,分粗精工。
3、切削液的冲洗位置应注意,尽量不要产生大量火花,切削液的流量应适中避免产生明火。
第四章影响电火花加工的因素
4.1影响材料放电腐蚀的主要因素
1.极性效应
能量在两极上的分配对两个电极电蚀量的影响是一个极为重要的因素,而电子和正离子对电极表面的撞击则是影响能量分布的主要因素,因此,电子撞击和离子撞击无疑是影响极性效应的重要因素。
但是,近年来的生产实践和研究结果表明,正的电极表面能吸附工作液中分解游离出来的碳微粒,形成碳黑膜(覆盖层)减小电极损耗。
由此可见,极性效应是一个较为复杂的问题。
除了脉宽、脉间的影响外,还有脉冲峰值电流、放电电压、工作液以及电极对的材料等都会影响到极性效应。
从提高加工生产率和减少工具损耗的角度来看,极性效应愈显著愈好,加工中必须充分利用极性效应,最大限度地降低工具电极的损耗,并合理选用工具电极的材料,根据电极对材料的物理性能、加工要求选用最佳的电规准,正确地选用加工极性,达到工件的蚀除速度最高,工具损耗尽可能小的目的。
当用交变的脉冲电流加工时,单个脉冲的极效应便相互抵消,增加了工具的损耗。
因此,电火花加工一般都采用单向脉冲电源。
2.电参数
电参数主要是指电压脉冲宽度ti、电流脉冲宽度te、脉冲间隔to、脉冲频率ƒ、峰值电流ie、峰值电压μ和极性等。
提高电蚀量和生产率的途径在于:
提高脉冲频率,增加单个脉冲能量或者说增加平均放电电流(对矩形脉冲即为峰值电流)和脉冲宽度;减小脉冲间隔并提高有关的工艺参数。
在实际生产时要考虑到这些因素之间的相互制约关系和对其它工艺指标的影响,例如脉冲间隔时间过短,将产生电弧放电;随着单个脉冲能量的增加,加工表面粗糙度值也随之增大等等。
3.金属材料热学常数
所谓热学常数,是指熔点、沸点(气化点)、热导率、比热容、熔化热、气化热等。
常见材料的热学常数可查相应手册。
每次脉冲放电时,通道内及正、负电极放电点都瞬时获得大量热能。
而正、负电极放电点所获得的热能,除一部分由于热传导散失到电极其它部分和工作液中外,其余部分将依次消耗在:
(1)使局部金属材料温度升高直至达到熔点,而每克金属材料升高1°C(或1K)所需之热量即为该金属材料的比热容;
(2)每熔化1g材料所需之热量即为该金属的熔化热;
(3)使熔化的金属液体继续升温至沸点,每克材料升高1°C所需之热量即为该熔融金属的比热容;
(4)使熔融金属气化,每气化1g材料所需的热量称为该金属的气化热;
(5)使金属蒸气继续加热成过热蒸气,每克金属蒸气升高1°C所需的热量为该蒸气的比热容。
当脉冲放电能量相同时,金属的熔点、沸点、比热容、熔化热、气化热愈高,电蚀量将愈少,愈难加工;热导率较大的金属,会将瞬时产生的热量传导散失到其它部位,因而降低了本身的蚀除量。
当单个脉冲能量一定时,脉冲电流幅值愈小,脉冲宽度愈长,散失的热量也愈多,从而使电蚀量减少;若脉冲宽度愈短,脉冲电流幅值愈大,由于热量过于集中而来不及传导扩散,虽使散失的热量减少,但抛出的金属中气化部分比例增大,多耗用了气化热,电蚀量也会降低。
因此,电极的蚀除量与电极材料的热导率以及其它热学常数、放电持续时间、单个脉冲能量等有密切关系。
4.其它因素
加工过程不稳定将干扰以致破坏正常的火花放电,使有效脉冲利用率降低。
随着加工深度、加工面积的增加,或加工型面复杂程度的增加,都将不利于电蚀产物的排出,影响加工稳定性和降低加工速度,严重时将造成结炭拉弧,使加工难以进行。
如果加工面积较小,而采用的加工电流较大,也会使局部电蚀产物浓度过高,放电点不能分散转移,放电后的余热来不及传播扩散而积累起来,造成过热,形成电弧,破坏加工的稳定性。
电极材料对加工稳定性也有影响。
用钢电极加工钢时不易稳定,用纯铜、黄铜电极加工钢时则比较稳定。
脉冲电源的波形及其前后沿陡度影响着输入能量的集中或分散程度,对电蚀量也有很大影响。
4.2影响加工精度因素的主要因素
与传统的机械加工一样,机床本身的各种误差,工件和工具电极的定位、安装误差都会影响到电火花加工的精度。
另外,与电火花加工工艺有关的主要因素是放电间隙的大小及其一致性、工具电极的损耗及其稳定等。
电火花加工时工具电极与工件之间放电间隙大小实际上是变化的,电参数对放电间隙的影响非常显着,精加工放电间隙一般只有0.01mm(单面),而粗加工时则可达0.5mm以上。
目前,电火花加工的精度为0.01~0.05mm。
电火花加工时,可以通过修正电极的尺寸对放电间隙进行补偿,以获得较高的加工精度。
然而,放电间隙的大小实际上是变化的,影响着加工精度。
1.表面粗糙度
电火花加工表面的粗糙度取决于放电蚀坑的深度及其分布的均匀程度,只有在加工表面产生浅而分布均匀的放电蚀坑,才能保证加工表面有较小的粗糙度值。
为了控制放电凹坑的均匀性,需要采用等能量放电脉冲控制技术,即检测间隙电压击穿下降沿,控制放电脉冲电流宽度相等,用相同的脉冲能量进行加工,从而使加工表面粗糙度微观上均匀一致。
2.加工间隙(侧面间隙)的影响
加工间隙的大小及其一致性直接影响电火花成形加工的加工精度。
只有掌握每个规准的加工间隙和表面粗糙度的数值,才能正确设计电极的尺寸,决定收缩量,确定加工过程中的规准转换。
3.加工斜度的影响
在加工中,不论型孔还是型腔,侧壁都有斜度,形成斜度的原因,除电极侧壁本身在技术要求或制造中原有的斜度外,一般都是由电极的损耗不均匀,以及“二次放电”等因素造成的。
(1)电极损耗的影响。
电极由于损耗而形成锥度,这种锥度反映到工件上,就形成了加工斜度。
(2)工作液脏污程度的影响。
工作液越脏,“二次放电”的机会就越多,同时由于间隙状态恶劣,电极回升的次数必然增多。
这两种情况都将使加工斜度增大。
(3)冲油或抽油的影响。
采用冲油或抽油对加工斜度的影响是不同的。
用冲油加工时,电蚀产物由已加工面流出,增加了“二次放电”的机会,使加工斜度增大。
而用抽油加工时,电蚀产物是由抽吸管排出去,干净的工作液从电极周边进入,所以在已加工面出现“二次放电”的机会较少,加工斜度也就小。
(4)加工深度的影响。
随着加工深度的增加,加工斜度也随着增加,但不是成比例关系。
当加工深度超过一定数值后,被加工件的上口尺寸就不再扩大了,即加工斜度不再增加。
不同的加工对象对加工斜度的要求也不同。
在型腔加工中,由于本身要求有一定的拔模斜度,则对加工斜度的要求并不严格。
对于直壁冲模,则要求加工斜度比较严格。
只要掌握影响加工斜度的规律,即可达到预定的要求。
4.楞角倒圆的原因及规律
电极尖角和楞边的损耗,比端面和侧面的损耗严重,所以随着电极楞角的损耗导致楞角倒圆,加工出的工件不可能得到清楞。
而且,随着加工深度的增加,电极楞角倒圆的半径增大。
但超过一定加工深度,其增大的趋势逐渐缓慢,最后停留在某一最大值上。
楞角倒圆的原因除电极的损耗外,还有放电间隙的等距离性。
凸尖楞电极由于尖角放电的等距离性,必然使工件产生圆角;凹尖楞电极的尖点根本不起放电作用,但由于积屑也会使工件凸楞倒圆。
因此,既使电极完全没有损耗,由于间隙放电的等距离性仍然不可能得到完全的清楞。
如果要求倒圆半径很小,必须要缩小放电间隙。
致谢
经过这几天的努力,我完成了这篇论文,在此特意向帮助过我的人们致以诚挚的感谢。
首先我要感谢指导我写这篇论文的XX老师,是X老师为我指明了方向,让我知道了应该怎么去写。
其次,我要感谢翟靖宇同学,他为我详细讲解了电极的制作过程。
然后,我要感谢在我学习过程中与我一起成长的同学们,我们一起学习共同进步。
最后,我要感谢我的母校——天津轻工职业技术学院,是学校为我提供了良好的学习环境,让我学到了很多知识,才能写出这篇论文。
参考文献
[1]杨占尧主编,《塑料注射模结构与设计》,高等教育出版社,2008.7
[2]韩瑞云主编,《塑料成型工艺与模具设计》,天津轻工职业技术学院,2011.4.1
[3]邹继强主编,《塑料制品及其成型模具设计》,清华大学出版社,2005.2
[4]塑料模具技术手册编委会,《塑料模具技术手册》,机械工业出版社,1997