钢构件施工工艺secret1.docx
《钢构件施工工艺secret1.docx》由会员分享,可在线阅读,更多相关《钢构件施工工艺secret1.docx(10页珍藏版)》请在冰豆网上搜索。
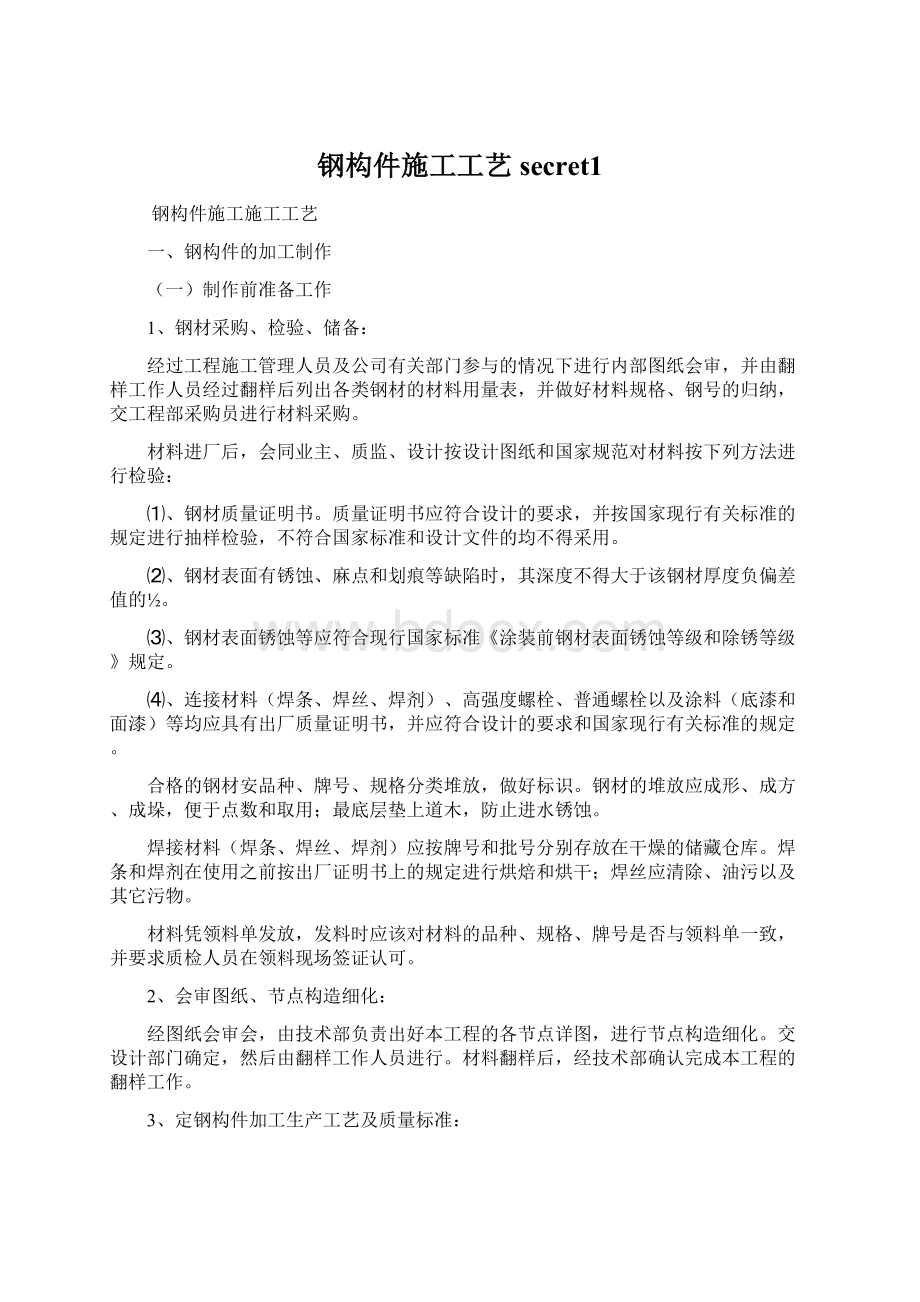
钢构件施工工艺secret1
钢构件施工施工工艺
一、钢构件的加工制作
(一)制作前准备工作
1、钢材采购、检验、储备:
经过工程施工管理人员及公司有关部门参与的情况下进行内部图纸会审,并由翻样工作人员经过翻样后列出各类钢材的材料用量表,并做好材料规格、钢号的归纳,交工程部采购员进行材料采购。
材料进厂后,会同业主、质监、设计按设计图纸和国家规范对材料按下列方法进行检验:
⑴、钢材质量证明书。
质量证明书应符合设计的要求,并按国家现行有关标准的规定进行抽样检验,不符合国家标准和设计文件的均不得采用。
⑵、钢材表面有锈蚀、麻点和划痕等缺陷时,其深度不得大于该钢材厚度负偏差值的½。
⑶、钢材表面锈蚀等应符合现行国家标准《涂装前钢材表面锈蚀等级和除锈等级》规定。
⑷、连接材料(焊条、焊丝、焊剂)、高强度螺栓、普通螺栓以及涂料(底漆和面漆)等均应具有出厂质量证明书,并应符合设计的要求和国家现行有关标准的规定。
合格的钢材安品种、牌号、规格分类堆放,做好标识。
钢材的堆放应成形、成方、成垛,便于点数和取用;最底层垫上道木,防止进水锈蚀。
焊接材料(焊条、焊丝、焊剂)应按牌号和批号分别存放在干燥的储藏仓库。
焊条和焊剂在使用之前按出厂证明书上的规定进行烘焙和烘干;焊丝应清除、油污以及其它污物。
材料凭领料单发放,发料时应该对材料的品种、规格、牌号是否与领料单一致,并要求质检人员在领料现场签证认可。
2、会审图纸、节点构造细化:
经图纸会审会,由技术部负责出好本工程的各节点详图,进行节点构造细化。
交设计部门确定,然后由翻样工作人员进行。
材料翻样后,经技术部确认完成本工程的翻样工作。
3、定钢构件加工生产工艺及质量标准:
根据《钢结构工程施工及验收规范》(GBJ205-83)、《港口工程质量检验评定标准》(JTJ221-98)、等国家规范及公司质量体系文件ISO90001-2002钢构件制作安装工艺规程编制本工程钢构件加工生产工艺及质量标准。
(二)钢构件加工制作流程
钢构件加工制作流程:
钢构件制作生产准备→放样、号料、切割→矫正、成型→边缘加工→组装→焊接(焊接结构矫正)→制孔→钢构件验收
(三)放样、下料和切割
1、按照施工图上的几何尺寸,以1:
1的比例在样台上放出实样以求出真实形状和尺寸,然后根据实样的形状和尺寸制成样板、样杆,作为下料、弯制、铣、刨、制孔等加工的依据。
放样和样板(样杆)允许偏差见下表:
放样和样板(样杆)允许偏差表
项目
允许偏差(mm)
平行线距离和分段尺寸
±0.5
对角线
1.0
长度、宽度
长度0~+0.5,宽度0~-0.5
孔距
±0.5
组孔中心线距离
±0.5
加工样板的角度
±20’
2、钢材下料前先采用40×4000三辊卷板机进行矫正调平,矫正后的偏差值不应超过规范及设计规定的允许偏差值,以保证下料的质量。
3、利用样板计算出下料尺寸,直接在板料成型钢表面上画出零部件形状的加工界线。
采用剪切、冲裁、锯切、气割等工作过程进行下料。
下料与样杆(样板)的允许偏差见下表:
下料与样杆(样板)的允许偏差表
项目
允许偏差(mm)
零件外形尺寸
±1.0
孔距
±0.5
基准线(装配或加工)
±0.5
对角线差
1.0
加工样板的角度
±20’
4、放样和下料应根据工艺要求预留制作和安装时的焊接收缩余量及切割、刨边和铣平等加工余量。
5、零件的切割民下料线的允许偏差应符合下表规定:
手工切割
±2.0mm
自动、半自动切割
±1.5mm
精密切割
±1.0mm
6、割前应将钢材表面切割区域内的铁锈、油污等清除干净;切割后断口边缘熔瘤、飞溅物应清除,断口上不得有裂纹和大于1mm的缺棱,并应清除毛刺。
7、切割截面与钢材表面不垂直度不大于钢材厚度的10%,且不得大于2.0mm。
8、精密切割的零件,其表面粗糙度不得大开0.03mm。
9、机械剪切的零件,其剪切与号料线的允许偏差不得大于2.0mm。
机械剪切的型钢,其端部剪切斜度不得大于2mm。
(四)矫正和成型
1、普通碳素结构钢在高于-16℃采用冷矫正和冷弯曲。
矫正后的钢材表面不应有明显的凹面和损伤,表面划痕深度不大于0.5mm。
2、零件、部件在冷矫正和冷弯曲时,其曲率半径和最大弯曲矢高应按设计的规范要求进行加工。
3、当零件采用热加工成形时,加热温度宜控制在900~1000℃;碳素结构钢在温度下降到700℃之前、低合金结构钢在温度下降到800℃之前,应结束加工;低合金结构钢应缓慢冷却。
(五)边缘加工
对外露边缘、焊接边缘、直接传力的边缘,需要进行铲、刨、铣等再加工。
根据不同要求,一般采用风铲、刨边机、碳弧气刨、端面铣床等机具、设备进行。
(六)制孔
1、制孔根据情况分别采用冲孔、钻孔、气割割孔等。
2、梁端板的螺栓孔有风模钻孔,以保证螺栓孔位置、尺寸准确。
腹板及连接板上的螺栓孔采用划线法钻孔。
3、孔的允许偏差超过设计或规范时,不得采用钢块填塞,应采用与母材材质相匹配的焊条补焊后重新制孔。
(七)组装
1、板材、型材的拼接应在组装前进行;构件的组装在部件组装、焊接、矫正后进行。
2、组装顺序应根据结构形式、焊接方法和焊接顺序等因素确定。
连接表面及焊缝每边30~50mm范围内的铁锈、毛刺和油污必须清除干净。
当有隐蔽缝时,必须先预施焊,经检验合格方可覆盖。
3、布置拼装胎具时,其定位必须考虑预放出焊接收缩量及齐关、加工的余量。
4、为减少变形,尽量采取小件组焊,经矫正后再大件组装。
胎具及装出的首件必须经过严格检验,方可大批进行装配工作。
5、将实样放在装配台上,按照施工图及工艺要求预留焊接收缩量。
装配平台应具有一定的刚度,不得发生变形,影响装配精度。
6、装配好的构件应立即用油漆在明显部位编号,写明图号、构件号和件数,以便查找。
7、焊接结构组装按需分别选用以下工具:
⑴、卡兰或铁楔夹具:
可把两个零件夹紧在一起定位,进行焊接。
⑵、槽钢夹紧器:
可用于装配板结构的对接接头。
⑶、矫正夹具及拉紧器:
矫正夹具用于装配钢结构;拉紧器是在装配时有来拉紧两个零件之间的缝隙。
⑷、正后丝扣推撑器:
用于在装配圆筒体的调整焊缝间隙和矫正筒体形状之用。
⑸、液压油缸及手动千斤顶。
8、定位点焊所用的焊接材料的型号,应与正式焊接的材料相同,并应由有合格证及上岗证的焊工点焊。
9、焊接结构组装工艺:
⑴、无论翼缘板,腹板,均应先进行装配焊接矫正,与钢柱连接的节点板等,应先小件组焊,矫正再定位大组装。
⑵、放组装胎时放出收缩量,一般放至上限(L≤24m时放5mm,L≥24m时放8mm)。
⑶、上翼缘节点板的槽焊深度与节点板的厚度关系见下表:
节点板厚度(mm)
6
8
10
12
14
槽焊深度(mm)
5
6
8
10
12
10、无论翼缘板、腹板,均先单肢装配焊接矫正后进行大组装。
组装前先进行基本定位,以确保在进行交叉施焊时结构不变形。
11、构件的隐蔽部位经焊接、涂装,并经检查合格后方可封闭;完全密闭的构件内表面可不涂装。
(八)成品检验
1、焊接全部完成,焊接冷却24小时后,全部做外观检查并做出记录。
2、按照施工图要求和施工规范规定,对成品外形几何尺寸进行检查验收,做好记录。
(九)成品保护
1、堆放构件时,地面必须垫平,避免支点受力不均。
构件的吊点、支点应合理;
构件一般均立放,以防止由于侧面刚度差而产生下挠或扭曲。
2、钢结构构件均涂防锈底漆,编号不得损坏。
(十)保证质量措施
1、防止构件运输、堆放变形:
必须采取措施,防止出现由于运输、堆放时的垫点不合理,或上、下垫木不在一条垂直线上,或由于场地沉陷等原因造成变形。
如发生变形,应根据情况采用千斤顶、氧-乙炔火焰加热或用其它工具矫正。
2、防止构件扭曲:
拼装时节点处型钢不吻合,连接处型钢与节点板间缝隙大于3mm,则需矫下,拼装时用夹具夹紧。
长构件应拉通线,符合要求后再定位焊接固定。
长构件翻身时由于刚度不足有可能发生变形,这时应事先进行临时加固。
3、防止焊接变形:
采用合理的焊接顺序及焊接工艺(包括焊接电流、速度、方向等)或采用夹具、胎具将构件固定,然后再进行焊接,以防止焊接后翘曲变形。
4、防止尺寸不准确:
制作、吊装、检查应用统一精度的钢尺。
严格检查构件制作尺寸,不允许超过允许偏差。
(十一)钢构件的焊接
1、材料
⑴、电焊条:
按照设计及规范要求选用焊条,焊条须具有出厂合格证明。
如须改动焊条型号,必须征得设计部门同意。
严禁使用过期药皮脱落、焊芯生锈的焊条。
焊接前将焊条进行烘焙处理。
⑵、作业条件
a、审阅施工图纸,拟定焊接工艺。
b、准备好所需施焊工具,焊接电源。
c、在钢结构车间施焊区施焊。
d、焊工经过考试,并取得合格证后才可上岗,如停焊超过半年以上时,则重新考核后才准上岗。
e、施焊前焊工复查组装质量和焊缝区的处理情况,如不符合要求,修整合格后方能施焊。
2、操作工艺
(1)焊条使用前,必须按照质量证明书的规定进行烘焙,低氢型焊条经过烘焙后,应放在保温箱内随用随取。
⑵、首次采用的钢种和焊接材料,必须进行焊接工艺性能和物理性能试验,符合要求后才采用。
⑶、多层焊接应连续施焊,其中每一层焊道焊完后应及时清理,如发现有影响焊接质量的缺陷,必须清除后再焊。
⑷、要求焊成凹面的巾角焊缝,可采用船位焊接使焊缝与母材间平缓过渡。
⑸、焊缝出现裂纹时,焊工不得擅自处理,须申报焊接技术负责人查清原因,订出修补措施后才可处理品。
⑹、严禁在焊缝区以外的母材上打火引弧。
在坡口内起弧的局部面积应熔
焊一次,不得留下弧坑。
⑺、重要焊缝接头,要在焊件两端配置起弧和收弧板,其材质和坡口型式应与焊件相同。
焊接完毕用气割切除并修磨平整,不得用锤击落。
⑻、要求等强度的对接和丁字接头焊缝,除按设计要求开坡口外,为了确保焊缝质量,焊接前采用碳弧气刨刨焊根,并清理要部氧化物后才进行焊接。
⑼、为了减少焊接变形与应力和公司常采取如下措施:
a、焊接时尽量使焊缝能自由变形,钢构件焊接要从中间向四周对称进行。
b、收缩量大的焊缝先焊接。
c、对称布置的焊缝由成双数焊工同时焊接。
d、长焊缝焊接可采用分中逐步退焊法或间跳焊接。
e、采用反变形法,在焊接前,预先将焊件在变形相反的方向加以弯曲或倾斜,以抵消焊后产生的变形,从而获得正常形状的构件。
f、采用刚性固定法:
用夹具夹紧被焊零件能显著减少焊件的残余变形及翅曲。
g、锤击法:
锤击焊缝及其周围区域,可以减少收缩应力变形。
⑽、焊接结构变形的矫正。
见矫正和成型中的“H型矫正机矫正原理图”和“油压机调形原理图”。
(十二)磨擦面加工处理
1、磨擦面加工:
本工程使用的是磨擦型高强螺栓连接的钢结构件,要求其连接面具有一定的抗滑移系数,使高强度螺栓紧固后连接表面产生足够的磨擦力,以达到传递外力的目的。
2、喷丸方式处理磨擦面:
喷丸粒径选用1.2~3mm,压缩空气压力为0.4~0.6MPa(不含有水份和任何油脂),喷距100~300mm,喷角以90°±45°。
处理后基材表面应达Sa2½级,呈均匀一致的金属本色。
喷丸表面粗糙50~70µm可不经生锈期即可施拧高强度螺栓。
3、经处理好的磨擦面,不能有毛刺(钻孔后周边即应磨光焊疤飞溅,油漆或污损等),并不允许再行打磨或锤击、碰撞。
处理后的磨擦面应妥善保护,磨擦面不得重复使用。
4、高强度螺栓连接的板叠接触面需平整(不平度<1.0mm。
当接触面有间隙时,其间隙不大于1.0mm可不处理;间隙为1~3mm时应将高出的一侧磨成1:
10的斜面,打磨方向与受力方向垂直;间隙大于3.0mm时则应加垫板,垫板面的处理要求与构件相同。
5、出厂前作抗滑移系数试验,符合设计值要求。
(十三)钢构件的安装
构件在安装前再进行检查,保证质量,除锈、涂漆等工作要作好,把准备工作搞好,用仪器放样以使位置准确,同时注意安全。
钢构件安装时应按施工图进行,安装前对临时支架,支承、吊机等临时结构和钢构件本身的不同受力状态下的强度、刚度及稳定性进行验算。
1、安装前应对构件的明细表核对。
2、钢构件在工地安装过程中矫正、制孔、组装、焊接和涂装等工序的施工质量符合要求。
3、杆件宜采用预先组拼,栓合或焊接,扩大拼装单元进行安装。
4、安装过程中,每完成一节间应测量其位置、标高和预拱度。
及时矫正。
5、钢构件工地焊缝分全焊连接和焊缝与高强度螺栓的合用连接。
6、连接时按设计规定的顺序进行。
7、工地焊接时设部分防风设施,遮盖全部焊接处,雨天不得焊接。
(十四)钢构件防腐涂装
1、施工准备
⑴、根据设计图纸要求,选用底漆及面漆。
⑵、准备除锈机械,涂刷工具。
⑶、涂装前钢结构、构件已检查验收,并符合设计要求。
⑷、防腐涂装作业在公司油漆厂区内进行,油漆厂区具有防火和通风措施,可防止发生火灾和人员中毒事故。
2、工艺流程
基面清理→底漆涂装→面漆涂装
3、涂装施工
⑴、基面清理:
a、钢结构工程在涂装前先检查钢结构制作,安装是否验收合格。
涂刷前将需涂装部位的铁锈、焊缝药皮、焊接飞溅物、油污、尘土等杂物清理干净。
b、为保证涂装质量,采用自动喷丸除锈机进行除锈。
该除锈方法是利用压缩空气的压力,连续不断地用钢丸冲击钢构件的表面,把钢材表面的铁锈、油污等杂物清理干净,露出金属钢材本色的一种除锈方法。
这种方法效率高,除锈彻底,比较先进的除锈工艺。
⑵、底漆涂装:
a、调合防锈漆,控制油漆的粘度、稠度、稀度、兑制时充分的搅拌,使油漆色泽、粘度均匀一致。
b、刷第一层底漆时涂刷方向应该一致,接搓整齐。
c、刷漆时采用勤沾、短刷的原则,防止刷子带漆太多而流坠。
d、待第一遍干燥后,再刷第二遍,第二遍涂刷方向与第一遍涂刷方向垂直,这样会使漆膜厚度均匀一致。
e、涂刷完毕后在构件上按原编号标注;重大构件还需要标明重量、重心位置和定位标号。
⑶、面漆涂装:
a、面漆涂装大部分构件在厂内完成,少数构件需待现场安装结束后才进行。
同样在涂装面漆前需对钢结构表面,尘土等杂物进行处理。
b、面漆调制选择颜色一致的面漆,总制的稀料合适,面漆使用前要充分搅拌,保持色泽均匀。
其工作粘度、稠度应保证涂装时不流坠,不显刷纹。
c、面漆在涂装过程中应不断搅和,涂刷方法和方向与底漆涂装相同。
4、涂层检查与验收
⑴、表面涂装施工时和施工后,对涂装过的工件进行保护,防止飞扬尘土和其他杂物。
⑵、涂装后处理检查,应该是涂层颜色一致,色泽鲜明,光亮,不起皱皮,不起疙瘩。
⑶、涂装漆膜厚度的测定,用触点式漆膜测厚仪测定漆膜厚度,漆膜测厚仪一般测定3点厚度,取其平均值。
5、成品保护
⑴、钢构件涂装后加以临时围护隔离,防止踏踩,损伤涂层。
⑵、钢构件涂装后,在4小时之内遇有大风或下雨时,则加以覆盖,防止粘染尘土和水气,影响涂层的附着力。
⑶、涂装后的构件需要运输时,要注电防止磕碰,防止在地面拖拉,防止涂层损坏。
涂装后的钢构件勿接触酸类液体,防止咬伤涂层。
6、应注意的质量问题
⑴、涂层作业气温应在5~38˚C之间为宜,当天气温度低于5˚C时,选用相应的低温涂层材料施涂。
⑵、当气温高于40˚C时,停止涂层作业。
经处理后再进行涂层作业。
⑶、当空气湿度大于85%,或构件表面有结露时,不进行涂层作业,或经处理后再进行涂层作业。
⑷、结构制作前,对构件隐蔽部位,结构夹层难以除锈的部位,提前除锈,提前涂刷。