成型基础知识.docx
《成型基础知识.docx》由会员分享,可在线阅读,更多相关《成型基础知识.docx(23页珍藏版)》请在冰豆网上搜索。
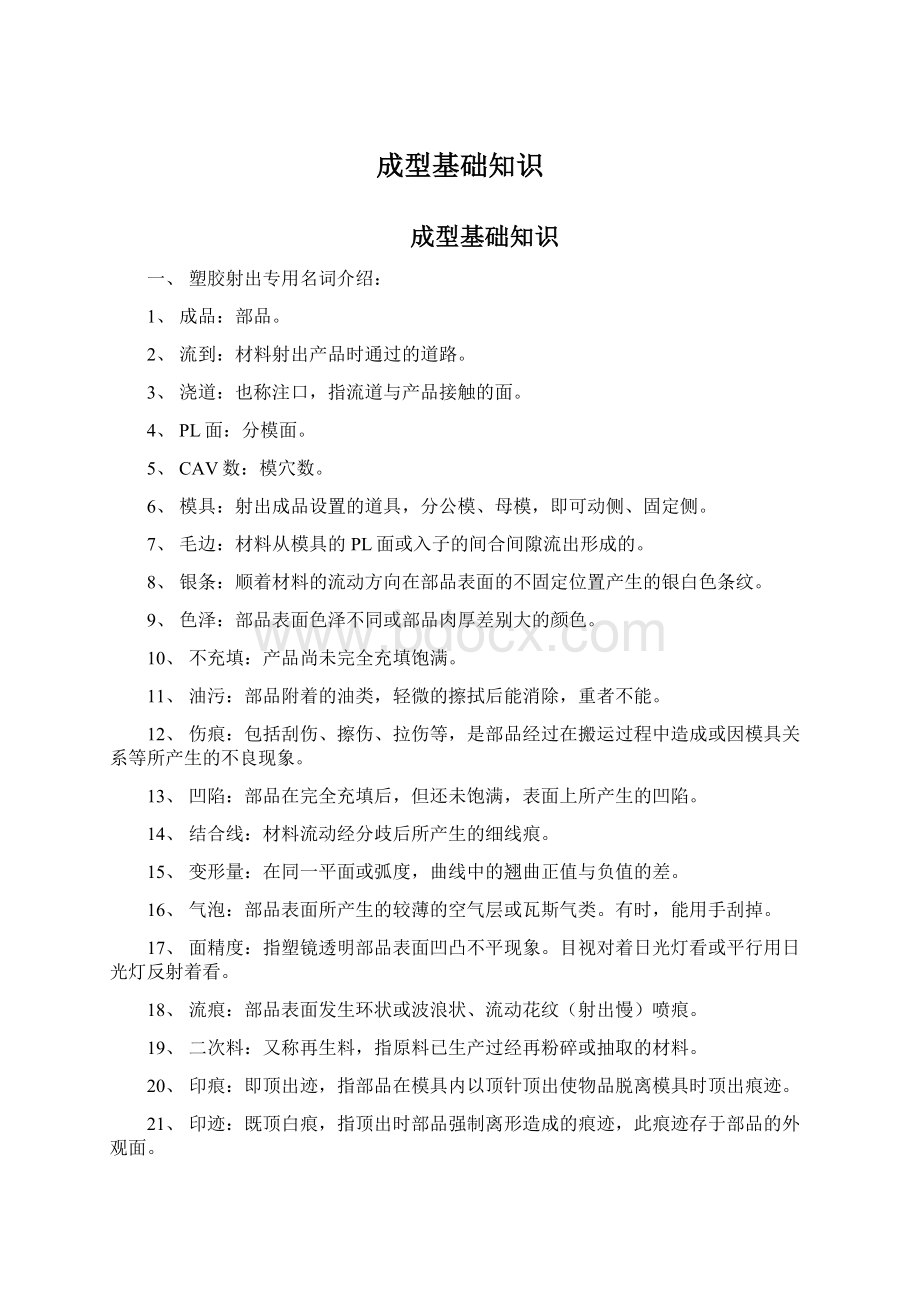
成型基础知识
成型基础知识
一、塑胶射出专用名词介绍:
1、成品:
部品。
2、流到:
材料射出产品时通过的道路。
3、浇道:
也称注口,指流道与产品接触的面。
4、PL面:
分模面。
5、CAV数:
模穴数。
6、模具:
射出成品设置的道具,分公模、母模,即可动侧、固定侧。
7、毛边:
材料从模具的PL面或入子的间合间隙流出形成的。
8、银条:
顺着材料的流动方向在部品表面的不固定位置产生的银白色条纹。
9、色泽:
部品表面色泽不同或部品肉厚差别大的颜色。
10、不充填:
产品尚未完全充填饱满。
11、油污:
部品附着的油类,轻微的擦拭后能消除,重者不能。
12、伤痕:
包括刮伤、擦伤、拉伤等,是部品经过在搬运过程中造成或因模具关系等所产生的不良现象。
13、凹陷:
部品在完全充填后,但还未饱满,表面上所产生的凹陷。
14、结合线:
材料流动经分歧后所产生的细线痕。
15、变形量:
在同一平面或弧度,曲线中的翘曲正值与负值的差。
16、气泡:
部品表面所产生的较薄的空气层或瓦斯气类。
有时,能用手刮掉。
17、面精度:
指塑镜透明部品表面凹凸不平现象。
目视对着日光灯看或平行用日光灯反射着看。
18、流痕:
部品表面发生环状或波浪状、流动花纹(射出慢)喷痕。
19、二次料:
又称再生料,指原料已生产过经再粉碎或抽取的材料。
20、印痕:
即顶出迹,指部品在模具内以顶针顶出使物品脱离模具时顶出痕迹。
21、印迹:
既顶白痕,指顶出时部品强制离形造成的痕迹,此痕迹存于部品的外观面。
22、型番迹:
成品型番号痕迹,用来区分各号码。
23、烧蚀:
部品上留下黑色的烧焦痕(热气经过压缩后分解)。
24、纤维浮:
材料的玻璃维浮出成品表面(纤维素)。
25、孔(穴)柱:
标示以¢,模具靠破(孔),立向增入(柱)直径。
26、静电:
摩擦生热后,所放出的电流(正离子),静电消除器放出(负离子)。
27、现合(实装):
与相对的部品嵌合。
28、荷姿:
防止部品碰伤、擦伤所装的包装盒。
二、成形不良的分类
成形不良大致分为三类
1、表面缺陷:
1).充填不足2).凹陷
3).变黄4).黑条纹
5).雾面6).银条纹
7).流痕8).熔合痕
9).激流痕10).异物
11).色泽不均12).颜色不均
13).污点14).擦痕
15).粘附性16).起泡
17).添加剂分离18).透明度不足
19).表面多孔性20).白点
21).影响外观的条痕22).毛边
2、成形与尺寸不良
1).翘曲、弯挠、扭转
2).尺寸安定性不够
3、龟裂
1).龟裂
2).白化
三、引起成形不良的原因及改善方法
1)充填不足
这是成形品的一部分缺少的现象,是成形不良的代表例,简称short。
充填不足是熔融塑胶流不到成形品的每一角落的结果,其原因主要有以下几种:
第1项原因是所谓L/T不足。
L/T是,塑胶流动的距离为L,成形品厚度为T时的比例。
改善方法有两方面:
a)成形方面改善塑胶的流动性,即选择流动性良好的塑胶,提升加热料筒的温度,以使熔融塑胶尽速流进模具内的每一末端。
b)模具方面则应尽量减少注道、浇道、浇口的阻力,尤其是浇口的阻力。
第2项原因是由于从浇道到浇口的阻力不同,致使熔融塑胶在浇口的压力产生差距所造成的,属这种原因的充填不足多发生在多模穴模具上。
因此,多模穴模具至浇口的距离须相等,而成对模穴的模具原则上采用尺寸及重量较接近的。
修改方法是加大发生充填不足的模槽的浇口,若是具有多段射出功能的射出成形机,可在通过浇口以前将射出速度减低,而通过浇口后才加快射出速度,便可改善充填速度。
第3项原因是模具内瓦斯气残留。
为避免这种充填不足,模具的合模线,顶出销或嵌件周边须有让空气逃出的间隙,同时在射出过程的最后段应放慢射出速度,使得空气有充分时间逃出。
此外,在常发充填不足部位形成空气逃出用沟,沟深在模槽一端应为0.02mm以下。
2)凹陷
射出成形品的不良中,凹陷是出现机率相当高的缺陷。
在射出成形过程,被射出的熔融塑胶,与模具表面接触则固化。
这时,因固化塑胶与熔融塑胶的密度不同,于是其厚度比模具间隙小,其程度与收缩率成比例,而成形品的厚部与薄部的缩小程度是不相同的,且固化时间也不甚相同,这样就容易发生凹陷。
其二,熔融塑胶要承受压缩力,而在薄部前方的厚部,在薄部固化后不再受压力,则其收缩程度将较薄部为大,于是凹陷产生。
另外,收缩率比较大的结晶性塑胶也较易发生凹陷。
防止凹陷的方法:
在成形上,持续保持压力至熔融塑胶完全固化为止,在固化初期的保压压力应较大,后段的保压压力需降低;在模具方面,把浇口设于成形品厚部,以及加大浇口都是防止凹陷的方法。
3)毛边
模具在成形时,由于密合不良而使熔融的塑胶进入模腔后产生泄漏物,冷却后粘附于部品上,就是我们所指的毛边。
按照模具结构来分,社内通常把毛边分为:
靠破毛边,擦破毛边,配合毛边,型合毛边,PL面毛边等。
产生毛边的原因主要有以下几种:
a)锁模力不够;b)模具本身PL面或入子靠破,插破不良;c)成形条件设置压力过大,射速过快;d)成形材料温度设定过高(料管温度)或滞留时间过长,材料过火分解;e)PL面或入子间异物附着,合模不紧。
4)烧焦
发生烧焦现象的原因主要是模具内有空气存在,当空气受压缩时会放热造成塑胶烧焦。
成形上,如烧焦部位在塑胶流程的末端,可减少最后一段的射出速度,如是融合痕部位的烧焦,可把熔融塑胶流过发生溶合痕部位时的速度降低;模具上,可形成让空气逃离的小沟。
5)黑条线
这是成形品上的从浇口向塑浇流动方向出现黑线的现象,是塑胶分解变黑色的部分,混进成形时产生的。
这种分解,主要是由塑胶温度过高而引起,但添加的难燃剂的分解也是原因之一。
6)雾面
是成形品的表面光泽不佳的现象。
大部分原因是离型剂用量过多或模具研磨不足所引起起的。
7)银条纹
成型品表面,顺着塑胶流动方向出现银白色条文的现象。
这是存在於熔融塑胶中的水分或挥发物,在缸套内因受压缩呈液状的,挤出注嘴后由同於压力降低蒸发气体,当塑胶固化时成为细泡的。
因此,完全去除原料中水分,或防止原料分解则可预防这种不良。
8)流痕
是在成型品表面,以浇口为中心发生各格纹状花纹的现象。
造成这种现象的主要原因是被射出的塑胶固化时,有时与模具接触,有时离开而引起的。
防止不良的具体方法是放慢射出速度或提高塑胶温度及模具温度。
在易出现流痕的部分放慢射出速度,往后则把射出速度提高到不发生充填不足的程度,也是有效方法。
9)熔合痕
这现象是成型品有孔洞部分,或成型品的厚部中央部有薄部分,或采用2个以上浇口成型时发生的。
当熔融塑胶在射出成型机内流动时,塑胶流尖端部分的温度难免稍微下降,因此,在塑胶再会合部位将形成互不溶合的痕线,这就是溶合痕。
因应方法是:
使用流动性良好的塑胶,把出现溶合痕部位的塑胶温度易升高,避免空气阻挡塑胶流动等。
另一种造成明显的溶合痕的原因:
是离型剂,用过量的离型剂时,当射出的塑胶流动时,把离型剂推向尖端而滞留於此部位,一旦发生这种情况,离型剂则被夹住,防碍塑胶的溶合,而造成明显的溶合痕。
另外,排气不良也是造成溶合痕的原因之一。
10)激流痕
在成形表面产生以浇口为起点的蚯蚓状条痕的现象。
这是通过浇口的塑胶以带状接触模具表面固化,与后续的射出塑胶熔合产生的。
这是塑胶一带状从浇口流出的侧浇口模具才发生的不良,此外交叠浇口也会发生。
用针孔形浇口,潜入式浇口或薄膜浇口成形时不会发生这种不良。
11)异物
这是异物掺进的现象,通常清除作业不充分,或再生品中有异物时发生,但射出成形机本身有损伤时也会发生。
12)光泽不均
是成形品表面光泽不均,部分光泽不均的现象。
模具温度过低,模具研磨不均匀或离型剂用量过多时容易发生这种现象。
13)颜色不均
是成形品的颜色不均的现象。
引起颜色不均的原因是,塑胶与着色剂的混合不均匀,或着色的安定性不佳在缸套中分解等。
另一原因是换色时的清理工作不周到。
14)擦伤
是成形品表面受模具擦伤,留下擦痕的现象。
制作模具的疏忽或电镀时,或在坡度小的部位形成细纹而造成与成形品脱模方向相反的反斜度时,易发生擦伤。
但是顶出稍不够,或顶出稍偏于成形品的一方时,脱模不顺而形成反斜度时也会发生擦伤。
15)龟裂
指部品周边的放射状裂痕。
造成原因主要为部品内应力残留。
造成内应力残留主要有以下几种原因:
a.压力过剩b.部品肉厚不均或冷却管道设计不常
c.成形时或冷却过程中,成形品内部残留内应力
改善措施有:
a.提升熔胶温度
b.提升模温
c.减小保压压力
四、射出成形五大因素:
1.温度:
熔胶温度、干燥温度、模具温度、料管温度、作动油温度、环境温度
2.压力:
射出压力、保压压力、锁模力、开关模压力、顶出压力
3.速度:
射出速度、回转速度、开关模速度、顶出速度
4.时间:
射出时间、保压时间、开关模时间、冷却时间、干燥时间
5.量:
计量、开模及关模位置、注射及保压切换位置、前后松退位置
五、塑胶成型方法:
1.射出成型:
设内采用,注射成型机
2.压出成型:
电线电缆被覆、管材押出
3.真空成型:
瓶类
4.输压成型:
皮革
5.热成型:
冰箱内箱、容器
六、成型条件基本设定方法:
1、以材料性质:
a、流动状况差速度宜快
b、流动性好速度宜慢
2、依部品外观需求:
a、外观部品速度宜慢
b、机构部品速度宜快
※总结:
以最小的成型压力成型出达到尺寸外观需求的部品。
七、常见加工工具及其使用
1、笔刀
分类:
大(黄)笔刀,小(黑)笔刀。
用途:
用于加工部品毛边、段差、多肉等,使用时用力需均匀,不可使重力而导致笔刀折断。
刀片削不动时,需要换刀片。
2、斜口钳
分类:
大剪钳,小剪钳
用途:
用于加工部品的灌口(使产品脱离流道),各灌口需据各部品的限度要求加工,不可高(低)於限度。
注:
加工时,若注口过硬,应特别小心,防止钳口破缺,斜口钳只能用于加工塑胶部品,其余一律不予使用。
3、顶针
分类:
据其直径尺寸分
用途:
部品小孔内出现毛边或“水口”过高,则需使用顶针钻孔(顶住口)。
4、镊子
用途:
用於选别小部品。
如:
绝缘粒或加工外观部品,如SB盖等电镀品
成型技术研讨
一、目的:
使用最适当的成型条件,在最小的成型压力下调试出最优良的品质,最稳定的产品。
二、成型条件(此设定时成型技术中主设订)
1.成型五大要素
A.温度:
料管温度、模温、干燥温度、油温、环境温度。
B.压力:
射娅、保压、顶出压、开关模压力、锁压力。
C.时间:
射出时间、保压时间、冷却时间、计量时间、干燥时间。
D.速度:
射速、回转速、型开闭、顶出速度。
E.量:
计量、顶出量、开闭模量。
2.名词解释
A.射出压力:
将熔融树脂充填于模穴内的压力。
B.射出速度:
将熔融树脂充填于模穴内的压力。
C.射出时间:
将熔融树脂充填于模穴内的压力。
D.冷却时间:
填充与模具的树脂冷却固化为热变形温度以下至可取出成型品的时间。
E.背压:
螺杆回转时,对于后退螺杆施以阻抗,使之后退困难的阻力,普通为3-20Kg/c㎡
功用:
1、增加螺杆对熔融树脂所做的功。
2、提高熔融温度及其均匀程度。
3、消除未熔融颗粒。
4、增加料管内原料及均匀度。
5、消除料管内熔融材料瓦斯起排放。
三、成型工程循环
成型原料
熔化加压流动、成型
漏斗螺丝熔射保压成品成
供给化混合出冷却取出品
开模高压锁杆模具密闭区间
四、料管分为三大部分:
(如图A)
(图A)
50~70%15~30%20~25%
供给区压缩区计量区
压力
(图B)
浇口冷却时间
压力与时间之关系
计量区:
使熔融树脂混合搅拌均匀依加热保温设定温度为高温。
压缩区:
依外部加热与内部的作用,施行可塑化,设定温度为中间温。
入料区:
为供给材料软化树脂并施行熔融的区域设定温度较低。
五、射出成型中塑料流动之压力变化分为三大阶段(如图B)
第一阶段:
塑料进入模穴,直到充满整个模穴。
第二阶段:
当模穴充满后,流动速度减慢,此时塑料继续被挤入模穴,密度提高,压力也急速上升,通常约10~20%的塑料在此时进入模穴。
第三阶段:
塑胶渐渐凝固,压力也随之下降。
1、成型条件要素如次:
温度:
料管温度,模型温度,树脂温度,干燥温度,油温度,周围温度。
压力:
填充压力,保持压力,回转,开模(型)压力,模型紧束压力。
时间:
填充时间,保持时间,冷却时间,干燥时间。
量:
计量、突出量、开模(型)量。
在成型中此要素互相关联,不能各自任意社定,又与成型品形状、树脂种类、模型构造互相复杂关系,成型条件应依实际成型而设定。
2、热可塑性树脂:
1)料管温度
料管的设定温度依树脂种类而有差异,又依树脂制造商、
树脂品级也有关系,如有错误设定料管温度,不但会使成型不良,有时因树脂引起分解发生有毒瓦斯对人体有不良影响,又有爆炸性树脂,对于料管温度的设定,应先充分掌握适当温度再设定。
A后部:
此为供给材料,软化树脂并施行熔融的区域,设定温度宜稍低,但耐论系有时稍高设定后部温度。
B中部:
此为材料压缩区,依外部加热与内部的剪断的作用施行可塑化,设定温度在中间温度左右。
C前部:
此为计量区,使熔融树脂混合搅拌均匀化,依加热保温,设定温度为高温。
D喷嘴:
依成型周期,前部温度,喷射的动用方式,树脂种类而设定,热稳定性良好时设定稍高温度。
2)射出压力
将融树脂填充于模型,设出压力过分高低均不宜,浇口冷固完了以后,宜加以2次压力(保压),浇口冷固不完全时,重量或尺寸参差不齐或发生短缺射出。
PS、PE等树脂对压力敏感,而PC、PMMA等树脂较为
钝感,对于PC等树脂可提高温度,藉以改善流动性。
3)射出速度
此为熔融脂往模型的填充速度,一般对于外观、尺寸精密度及物性而言,射出速度宜快,但对于加厚或加深成型品,并顾虑过烧,银条痕等不良成型,则宜较迟缓,最近采用多假设定射出温度使树脂流动国最合适状态施行成型。
4)射出时间
射出时间包括模型填充时间(浇口为冷却固话时间)保
压时间过短则在浇口部末固化,模腔内树脂被退回螺杆侧,致使尺寸精密度或外观不良,为避免短射或消除氮泡,宜采取较长保压时间。
5)冷却时间
填充模型的树脂却固化为热变形温度以下,至可取出成
型品的时间,虽可依成型品厚度、树脂温度、模具温度、树脂特性等,但一般根据经验决定,冷却时间较长,成型品的变形较小,成型品的变形较小,但因成型品收、枞模型的拔出的不容易,而成型周期拖长。
计量时间超出冷却时间时,也有因此延长冷却时间。
6)计量
依螺杆回转计量并储存在料管前部,计量时间(螺旋回
转时间)设定比冷却时间为短,普通计量行程包括缓衡决定、缓衡量为避免填充不足,使成型品重量不均匀减少,宜采取3~5mm左右(小型机)为缓衡量。
7)螺杆回转数
因螺赣回转,树脂受到剪断作用以至内部发热,回转速
越快,树脂的发热越多,过快时使树脂温度升高发生过热或分解,在不发生过烧或分解的范围内,尽可能提高设定回转速度。
8)背压
螺杆回转时,对于后退螺旋加以阻抗,使为后退困难的
阻力稍为背压,普通为3~20Kg/c㎡左右,其效果如次:
A、防止重量不均匀
B、防止空气混入
C、挥发分的脱气效果
D、使熔融均匀并使色分散良好
9)模型温度
模型从填充的高温树脂去除热量
模型表面温度均匀,每次成型均须稳定,依成型品种类,
有强制冷却模型,或反而提高模型温度,对于强制冷却,可
改善树脂的流动性,加速成型品的冷却,缩短成型周期。
对于提高模型温度,为流动性不良的树脂所需要措施,可依模型温度调节,使模型内的树脂流动性改善。
模型温调有使用冷却水与热媒体两种,使用冷却水进出口温度差调整为5~6℃,对于高粘力的树脂(压力、温度依存性较高的树脂、PC、PMMA等),模型温度设定为稍高温度,在洁晶性树脂,结晶化度受到模型温度可使结晶化度上升且可提高强度改善外观,但尺寸收缩增大,对于非洁晶性树脂在不变形范围内,模型温度提高,而以低于热变形温度约10℃为理想的模型温度。
稍高设定模型温度,可是流动良好,定向或留歪曲减少,外观鲜艳靓丽,且可提高合线(WELDLINE)强度,但因尺寸收缩变大,成型品因短射发生缩水或气泡,又有周期延长的负面结果。
成型理论试模技术讲解
(一)试模之前需对所有之材质作如下了解
塑材大致有三种原料所提炼而成:
1.PC主要是由石油提炼而成
2.ABS主要是由焦煤提炼而成
3.POM主要是由汽油提炼而成
针对各种材质之性能,在成型上之化学效应,我们应要求对我们现使用之材质有充分了解,以便对下一动作有一个充分得把握,保证成型试模时,材料过高温加热后顺利成型,不易造成不必要的后果。
(二)模具之结构性能上确认:
1、模具因刚制作完成,它所本身之结构及性能上需多确认,特别是新规第一次试模。
2、模具作动需认真确认(具体详见试模注意事项)
3、所模立志调整,直接关系到模具后续之量产状况,它设定之大于小,也直接关系到模具寿命的长于短,因此模具锁模力之设定也是成型试模关键的一环。
锁模力换算公式(tf)
F:
锁模力(tf)F=A×P×1.2/1000
A:
产品的投影面积(c㎡)
P:
模内平均树脂压力(kgf/c㎡)
(三)成型条件之确认
1、部品加织之成形手法
温度设定时间设定高速度低压力
2、部品不加织之成形手法
温度先设定时间设定低速度高压力
3、部品成形切换方式之确认
根据部品之大小,结构性能以及机台本身之切换方式,作对应的选择(压力切换、位置切换、时间切换等)。
(四)、条件设定的方式
1、首先以一速一压于不充填到充填教条件,条件一个一个的加上去,直到整个部品已成形出一个85-95%的部品,但部品之外观仍有凹陷或轻微的外观不良时,再使用保压之功能,使得整个部品在外观与尺寸上有一个完整的外表及精确的寸法。
因此当你设定保压时,需根据部品本身之结构,设定合适的保压,否则将会影响模具后续的作业寿命,以及直接影响模具内压,导致应力残留,部品屁裂现象。
2、其实在成形条件调整的同时,大部分机械都有几速几压之性能,但是我们之设定,也是根据部品形状及结构,对于成形条件设定时能简易的射出成形。
如果说使用一速一压有些部品是难以达成我们所要的成形效果,以及优良的部品。
因此大部分外观之部品,都用多段式射出成形。
以便我们根据自己成形所需,选择自己最佳的成形条件。
因此在我们成形试模时,开始使用之方式仍是最简单、最容易的设出成形。
因为模具第一次试模并没有对结构及寸法上作管制。
3、温度、压力、时间、速度、位置的设定
1、温度在成形调试以前,必须设定完成。
因为成形温度在射出占为最重要的一位。
如果说在成形温度上无法得到掌控,那么后续的射出成形就难以成形,塑胶部品因为对热之效应最为敏感,对热能产生的化学反应也是最为强烈。
例如:
ABS熔胶温度180-240度。
如果在你射定的175度那么对一后续之成形胶不易射出,射出时压力过大,材料流动不良等。
若设定225度,那成形时部品容易变形,材料易过火,成形之部品
2、压力之设定:
在成形设定时,以一主一副先射后保,
时间之设定:
各条件之设定需根据部品本身之结构及
速度之设定:
模具材料之性能组合一起,以不充填慢
位置之设定:
慢的调试,以达到我们的部品品质水准。
3、试模时成形程序:
锁模:
锁模力是否正常
设定:
条件(适当)
短射:
不设定保压
调整:
渐进式
主要之不良成形及其原因
成形不良之影响
关连成形机者
关连模具者
关连成形材料者
充填不足
(1)射出压力不足
(2)加热缸温度太低
(3)加热缸或喷嘴阻塞
(4)喷嘴太小
(5)材料供给不足
(6)漏斗阻塞
(7)射出速度太低
(1)浇口位置不当
(2)模具构造不良
(3)流道太小
(4)模具温度太低
(5)冷料对流道及浇口阻塞
(6)成形品部肉厚不均或太满
(7)成形空间内之气体未能顺利排出
(1)流动性不良
(2)润滑剂不足
毛边过剩
(1)射出压力太高
(2)合模力不足
(3)材料供给过多
(4)保压时间太长
(5)加热缸温度太低
(6)射出速度太慢
(1)模具无法紧密配合
(2)模具中有异物及毛头等附着,而无法完全合模.
(3)模具构造不良
(1)流动性太好
收缩下陷
(1)射出压力不足
(2)加热缸温度太高
(3)射出速度太低
(4)材料供应不足
(5)成形机能量不足
(6)保压时间太短
(7)喷嘴口径太小
(8)成形循环过快
(1)模具温度过高,及温度不均
(2)浇口太小
(3)流道太小
(4)成形品厚度不均
(1)材料过软
(2)收缩率大
气泡
(1)射力压力不足
(2)射出速度太低
(3)射出中形成断续
(4)保压时间不足
(5)加热缸温度太高
(1)浇口位置不当
(2)模具构造不良
(3)成形品厚度不均
(4)流道太小
(5)浇口太小
(6)成形品在模具中受冷却时间过长
(7)成形空间内之气体未能顺利排出
(1)流动性不良
(2)有吸湿性
(3)含有挥发性物质
燃烧的难易
火焰拿掉是否继续燃烧
火焰之颜色
燃烧的状态
气味
成形的特征
PF
慢慢燃烧
熄灭
黄色
膨胀缺裂颜色变深
碳酸臭味酚味
黑色或
UF
难
熄灭
黄色尾端青绿
膨胀缺裂白化
尿素味、甲醛味
颜色大多美丽
MF
难
熄灭
淡黄色
膨胀缺裂白化
尿素味、胺味、甲醛味
表面很硬
UP
易
不熄灭
黄色黑烟
微膨胀缺裂
苯乙烯气味
成品大多以玻璃纤维补强
PMMA
易
不熄灭
黄色尾端青绿
软化
压克力气味
和玻璃一样声音,可弯曲
PS
易
不熄灭
橙黄色黑烟
软化
苯乙烯气味
敲击是有金属性的声音,多为透明成形品
PA
慢慢燃烧
熄灭
先端黄色
熔融落下
特殊味
有弹性
PVC
难
熄灭
黄色下端绿色
软化
氯气味
软质者类似橡胶,可调整各种硬度
PP
易
不熄灭
黄色(蓝色火焰)
快速完全燃掉
特殊味(柴油味)
乳白色
PE
易
不熄灭
先端黄色下端青色
熔融落下
石油臭味(石蜡气味)
淡乳白色,大多为半透明
ABS
易
不熄灭
黄色黑烟
熔融落下
橡胶味、辣味
聚
易
熄灭
略白色火焰
微膨胀缺裂
硫磺味
硬且声脆
PC
稍难
熄灭
黄色黑烟
软化
特殊味
淡黄色,透明或不透明,耐冲击
POM
易
不熄灭
先端黄色下端青色
边滴边燃
福而马林的气味
乳白色,不透明
CN
极易
不熄灭
黄色
完全迅速燃烧
特殊味
透明或不透明
CA
易