把握生产准备的全过程 确保工厂投产一次成功.docx
《把握生产准备的全过程 确保工厂投产一次成功.docx》由会员分享,可在线阅读,更多相关《把握生产准备的全过程 确保工厂投产一次成功.docx(40页珍藏版)》请在冰豆网上搜索。
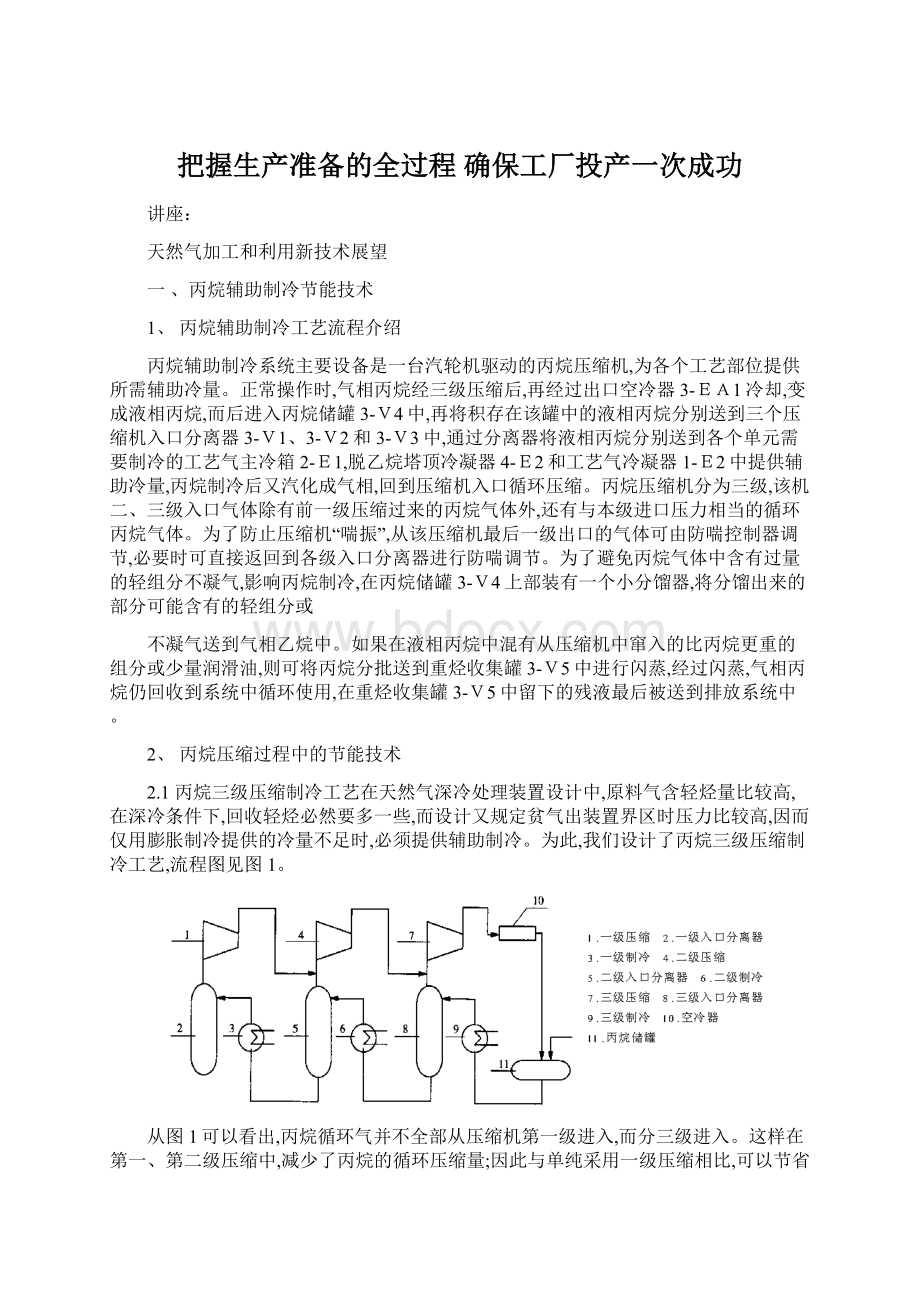
把握生产准备的全过程确保工厂投产一次成功
讲座:
天然气加工和利用新技术展望
一、丙烷辅助制冷节能技术
1、丙烷辅助制冷工艺流程介绍
丙烷辅助制冷系统主要设备是一台汽轮机驱动的丙烷压缩机,为各个工艺部位提供所需辅助冷量。
正常操作时,气相丙烷经三级压缩后,再经过出口空冷器3-EA1冷却,变成液相丙烷,而后进入丙烷储罐3-V4中,再将积存在该罐中的液相丙烷分别送到三个压缩机入口分离器3-V1、3-V2和3-V3中,通过分离器将液相丙烷分别送到各个单元需要制冷的工艺气主冷箱2-E1,脱乙烷塔顶冷凝器4-E2和工艺气冷凝器1-E2中提供辅助冷量,丙烷制冷后又汽化成气相,回到压缩机入口循环压缩。
丙烷压缩机分为三级,该机二、三级入口气体除有前一级压缩过来的丙烷气体外,还有与本级进口压力相当的循环丙烷气体。
为了防止压缩机“喘振”,从该压缩机最后一级出口的气体可由防喘控制器调节,必要时可直接返回到各级入口分离器进行防喘调节。
为了避免丙烷气体中含有过量的轻组分不凝气,影响丙烷制冷,在丙烷储罐3-V4上部装有一个小分馏器,将分馏出来的部分可能含有的轻组分或
不凝气送到气相乙烷中。
如果在液相丙烷中混有从压缩机中窜入的比丙烷更重的组分或少量润滑油,则可将丙烷分批送到重烃收集罐3-V5中进行闪蒸,经过闪蒸,气相丙烷仍回收到系统中循环使用,在重烃收集罐3-V5中留下的残液最后被送到排放系统中。
2、丙烷压缩过程中的节能技术
2.1丙烷三级压缩制冷工艺在天然气深冷处理装置设计中,原料气含轻烃量比较高,在深冷条件下,回收轻烃必然要多一些,而设计又规定贫气出装置界区时压力比较高,因而仅用膨胀制冷提供的冷量不足时,必须提供辅助制冷。
为此,我们设计了丙烷三级压缩制冷工艺,流程图见图1。
从图1可以看出,丙烷循环气并不全部从压缩机第一级进入,而分三级进入。
这样在第一、第二级压缩中,减少了丙烷的循环压缩量;因此与单纯采用一级压缩相比,可以节省功率。
另外,该压缩机虽分三级压缩,却没有级间冷却器,这是因为第二、第三级压缩机的入口气体中,除了前一级压缩出口的热气体,还有制冷后循环冷丙烷气,由于冷丙烷气的加入,使进入压缩机的丙烷气体温度降低,体积减小,压缩功率下降,这就是该流程的节能特点。
我们计算了在一定的冷冻负荷条件下,分别采用Ⅰ级、Ⅱ级、Ⅲ级压缩方案所需功率数值,见表1。
表1 丙烷冷冻中分级压缩效果对比级
从表1数据可以看出,在一定的冷冻负荷条件下,随着压缩级数的增加,所需要压缩的功率减少,能耗降低。
但设备费用却随着级数的增加而增加,所以最优化的选择应当是能耗减少、设备费用最少。
经过长时间的实践和总结,我们推荐采用一个确定冷冻级数优化值的一般规律图,见图2。
图中R表示压缩机的总出口压力与一级入口压力之比。
从图2可以看出,当R<3时,压缩机采用一级最经济;当3≤R≤5.5时,压缩机采用两级最经济;当R>5.5时,压缩机采用三级最经济。
我厂丙烷压缩机R=10.2,因此采用三级压缩最经济和节能。
图2 压缩机级数优化选择图
2.2冷凝温度对压缩机功率的影响分析压缩机的功率不但受压缩机的级数影响,而且还受冷凝的温度影响。
为便于说明问题,我们计算了在单级丙烷冷冻系统中不同温度下压缩机所需的功率,详见表2。
表2 单级丙烷冷冻冷凝温度对压缩机功率的影响
从表2可以看出,随着冷凝剂的冷凝温度降低,不仅总压缩功率减少,冷凝负荷亦减少;因此,可以根据气温的变化通过调节驱动机而达到节能目的。
3
结束语冷冻压缩机的功率不仅和压缩级数有关,而且还和冷凝剂的温度有关。
因此,在设计制冷流程时,应合理选用压缩级数,以达到节能和减少投资的目的。
在运行中,可根据环境温度的变化,通过调整驱动机的输出功率达到节能的目的。
二、天然气脱硫脱水技术工艺探讨
含硫天然气中含有硫化氢、有机硫(硫醇类)、二氧化碳、饱和水以及其它杂质,因此需将其中的有害成分脱除,以满足工厂生产和民用商品气的使用要求。
各国的商品天然气标准不尽相同,主要是需满足管道输送要求的烃露点和水露点,同时对天然气中硫化氢、硫醇、二氧化碳的最高含量和低燃烧值有要求。
1、方案选择
原料天然气组成和商品天然气的要求不同,所选择的天然气净化工艺技术方案也是不同的,下面将结合哈萨克斯坦国某油气处理厂处理的天然气的组成和需输往国际管道中的产品天然气的要求,提出含硫天然气脱硫脱水工艺技术方案的选择方法。
⑴、原料天然气条件
哈萨克斯坦国某油气处理厂处理的油田伴生天然气主要条件为:
1)处理量600×104m3/d(标准状态为0℃,101.325kPa,以下同);
2)压力为0.7MPa,为满足管输压力和净化工艺需要,经增压站升压后进装置压力为6.8MPa;
3)主要组成
组分
组成(mol%)
C1
75.17
C2
9.44
C3
7.21
C4
3.35
C5+
1.06
CO2
0.71
H2O
0.51
H2S
36g/m3
硫醇硫
500mg/m3
⑵、商品天然气技术指标
该厂商品天然气将输往国际管道,需满足ОСТ51.40-93标准的要求,应达到的主要技术指标为:
1)出厂压力6.3MPa;
2)水露点≤-20℃;
3)烃露点≤-10℃;
4)硫化氢(H2S)≤7mg/m3;
5)硫醇硫(以硫计)≤16mg/m3;
6)低燃烧热值≥32.5MJ/m3。
⑶、工艺路线初步选择
根据原料天然气条件和商品天然气技术指标,工厂总工艺流程框图如下。
油田伴生天然气经增压站增压后,至天然气脱硫脱水装置进行处理,需脱除天然气中绝大部分的H2S和RSH,以满足产品天然气中硫化氢和硫醇硫含量的技术指标;同时需脱除天然气中绝大部分的水,以满足产品天然气水露点的技术指标,同时为回收更多的液化气和轻油产品,脱水深度还需满足后续的轻烃回收装置所需的水露点≤-35℃的要求。
而原料气中CO2的含量较低,为0.71%(mol),商品天然气的低燃烧热值≥32.5MJ/m3,可不考虑脱除。
经天然气脱硫脱水装置处理的干净化天然气经轻烃回收装置回收天然气中的轻烃(C3以上),生产液化气和轻油产品,并使商品天然气满足烃露点≤-10℃的技术指标。
脱硫装置脱除的酸性气体,主要由H2S、RSH、CO2、H2O等组成,输往硫磺回收装置回收硫磺,经硫磺成型设施生产硫磺产品,硫磺回收装置尾气经尾气处理装置处理后经燃烧后排放大气。
本文以下部分主要讨论脱硫脱水装置如何选择合理的工艺技术方案,以使脱硫脱水装置的产品气中硫化氢、硫醇含量合格,水露点能满足商品天然气和后续的轻烃回收装置的要求。
⑷脱水工艺方案的初步选择
通常采用的脱水工艺方法有溶剂脱水法和固体干燥剂吸附法。
溶剂吸收法具有设备投资和操作费用较低的优点,较适合大流量高压天然气的脱水,其中应用最广泛的为三甘醇溶液脱水方法,但其脱水深度有限,露点降一般不超过45℃。
而固体干燥剂吸附法脱水后的干气,露点可低于-50℃。
由于本方案脱水装置产品天然气要求水露点≤-35℃,溶剂脱水法难以达到因此需采用固体干燥剂脱水工艺,如分子筛脱水工艺。
⑸脱硫脱硫醇工艺方案的初步选择
本方案需处理的伴生天然气中H2S含量为36g/m3,硫醇含量为500mg/m3,而且天然气处理量达到600×104m3/d,规模较大,目前国内单套脱硫装置最大处理能力仅为400×104m3/d。
通常采用的脱硫脱硫醇的方法有液体脱硫法和固定床层脱硫法。
如果采用单一的固定床层脱硫法,如分子筛脱硫脱硫醇工艺,根据本方案需处理的天然气的流量和含硫量,按10天切换再生一次计算,10天内需脱除的硫化氢量为2.16×106kg,约需要DN3000的分子筛脱硫塔500座,这显然是不可行的。
目前国内较为成熟可行的液体脱硫工艺方法为醇胺法,因为含硫天然气中同时存在硫醇,所以可选择砜胺法来脱除硫化氢和硫醇。
该工艺方法较为成熟,可把天然气中的硫化氢脱除至≤7mg/m3,同时对天然气中硫醇的平均脱除率为75%,则产品天然气中的硫醇硫含量为125mg/m3,尚不能达到硫醇硫≤16mg/m3的技术指标,此时可采用固定床层脱硫醇工艺,如分子筛脱硫醇工艺来脱除天然气中剩余的硫醇。
本方案还可以采用碱洗脱硫醇工艺来脱除天然气中的硫醇,为减少生产过程中碱的耗量和产生的废碱量,前面的醇胺法脱硫装置需采用一乙醇胺工艺,以脱除天然气中的大部分硫化氢和二氧化碳。
⑹脱硫脱水工艺方案的比选
由⑷和⑸所述,脱硫脱水工艺方案有以下两个较为可行的方案:
1)方案一:
砜胺法脱硫+分子筛脱水脱硫醇
该方案工艺框图见图2,经增压站升压的含硫天然气进入砜胺法脱硫装置脱除几乎全部的H2S和75%的硫醇,然后进入分子筛脱水脱硫醇装置脱除水分和剩余的硫醇,净化天然气经轻烃回收装置回收液化气和轻油产品。
脱水脱硫醇装置的分子筛再生气需增压后再返回至砜胺法脱硫装置进行脱硫,是一个循环的流程。
2)方案二:
一乙醇胺法脱硫+碱洗脱硫醇+分子筛脱水
该方案工艺框图见图3,经增压站增压的含硫天然气进入一乙醇胺法脱硫装置脱除几乎全部的H2S和CO2,然后进入碱洗脱硫醇装置脱除几乎全部的的硫醇,脱除硫化物后的天然气进入分子筛脱水装置脱水,净化天然气输往轻烃回收装置回收液化气和轻油产品。
脱水装置分子筛再生气需增压后返回脱水装置脱水,是一个循环的流程。
⑺、方案一工艺特点
1)砜胺法脱硫装置,采用环丁砜和甲基二乙醇胺水溶液作脱硫剂,溶液的主要组成包括甲基二乙醇胺、环丁砜和水,其重量百分比为45:
40:
15,兼有化学吸收和物理吸收两种作用,而且还能部分地脱除有机硫化物(对硫醇的平均脱除率达到75%以上),溶液中甲基二乙醇胺对H2S的吸收有较好的选择性,减少对CO2的吸收,大大降低了溶液循环量,减小了再生系统的设备如再生塔、贫富液换热器、溶液过滤器、酸气空冷器等的规格尺寸,从而减少了投资,同时减少了再生所需的蒸汽量和溶液冷却所需的循环水量,节能效果更加显著。
2)分子筛脱水脱硫醇装置是利用分子筛的吸附特性,有选择性地脱除天然气中的水和硫醇。
与传统的碱洗工艺不一样的是,分子筛工艺能有选择性地脱除硫化氢和硫醇,但不脱除CO2,这样可以使外输的天然气量比采用碱洗工艺时要增加2×104m3/d。
分子筛脱水和脱硫醇采用的分子筛是不同的,应用不同的两个分子筛床层,一般布置在同一座吸附塔内。
⑻、方案二工艺特点
1)—乙醇胺法脱硫,为典型的化学吸收过程,此法只能脱除微量有机硫,对H2S和CO2几乎无选择性吸收,在吸收H2S的同时也吸收CO2,因此净化气中CO2含量很小,有利于后续的碱洗脱硫醇装置减少废碱的产生,降低碱耗量。
但该方法溶液的酸气负荷较砜胺法低,因此所需的溶液循环量较大,溶液再生系统设备规格尺寸也较大,装置能耗也较高。
2)碱洗脱硫是一种比较传统的天然气脱硫工艺,MEROX法是目前运用较为广泛的碱洗脱硫技术,目前该技术多采用纤维膜技术来强化传质和分离过程。
碱液为NaOH水溶液,其和H2S、CO2以及硫醇(RSH)分别发生化学反应。
其中NaOH和H2S、CO2反应生成的Na2S、Na2CO3溶解在碱液中不能再生,增加了碱液的耗量。
而NaOH和RSH反应生成的硫醇钠(RSNa)可在催化剂的作用下和氧气、水反应转化为二硫化物和NaOH,完成碱液的再生,碱液只有很小部分的损耗。
因此必须在前面的脱硫装置将天然气中H2S和CO2的含量脱除至最低,以减轻碱洗装置的负荷,为此在本方案中脱硫装置采用—乙醇胺法脱硫。
另外,碱洗装置会有大量的废碱液(约250m3/a)需要处理,拟输送至工厂附近的废碱处理装置进行处理,否则工厂需增设废碱液处理装置。
3)分子筛脱水装置主要是应用分子筛床层脱水,和脱水脱硫醇装置相比,吸附塔减少了分子筛脱硫醇床层。
⑼、两方案的主要技术指标对比
1)装置规模及数量对比
两个方案的装置规模及数量对比见表1。
表1装置规模及数量对比表
项
目
序
号
脱硫装置
碱洗装置
分子筛装置
备注
装置公称处理能力
(104m3/d)
装置数量
(套)
装置公称处理能力
(104m3/d)
装置数量
(套)
装置公称处理能力
(104m3/d)
装置数量
(套)
方案二工厂还须增加一套废碱处理装置,投资约需420万美元
方案一
600
1
╱
╱
600
1
方案二
600
1
600
1
600
1
2)产品天然气对比
两个方案的产品对比见表2。
表2产品天然气主要指标对比表
项目
序号
产品数量
(104m3/d)
硫醇硫含量
(mg/m3)
水露点
(6.75MPa(a)下)
方案一
538
≤16
≤-35℃
方案二
536
≤16
≤-35℃
3)主要消耗指标和年操作费用对比
两个方案主要消耗指标见表3,年操作费用对比见表4。
表3主要消耗指标对比表
序号
项目
单位
方案一
方案二
1
循环水
104t/a
446
1028
2
新鲜水
104t/a
2.2
2.6
3
电力
104kW·h/a
1265
1970
4
蒸气
104t/a
31.5
61.5
5
燃料气
104m3/a
505
474
6
化学品及催化剂
T/a
环丁砜60
甲基二乙醇胺22
分子筛95t/5a
一乙醇胺70
氧化催化剂0.6
NaOH193
分子筛75/5a
表4年操作费用对比表
方案
方案一
方案二
年操作费用(美元)
130
180
4)投资对比
两个方案的投资对比见表5。
表5投资对比表
项目
序号
脱硫装置
(万美元)
碱洗装置
(万美元)
分子筛装置
(万美元)
总计
(万美元)
方案一
1015
╱
560
1575
方案二
1235
750
490
2475
5)两方案优缺点对比
现把两个方案的主要优缺点对比见表6。
表6主要优缺点对比表
序号
方案一
方案二
优点
1、总工艺流程简单。
2、工程量较小,需要一套脱硫装置和一套分子筛脱水脱硫醇装置。
3、外输的产品天然气量较方案二多2×104m3/d。
4、年操作费用较低。
5、投资较低。
1、不需要脱硫醇的专用分子筛。
2、燃料气消耗较小。
缺点
1、需用复合床分子筛吸附器,且需要脱硫醇专用分子筛。
2、脱硫醇的分子筛再生温度较高,消耗燃料气较多。
1、工艺流程较为复杂。
2、工程量较大,需要一套脱硫装置、一套碱洗装置和一套分子筛脱水装置。
3、如每年250m3废碱液无法处理,则还须增加一套废碱液处理装置。
4、外输的产品天然气量较方案一少2×104m3/d。
5、涉及国外的纤维膜反应器专利技术,年操作费用较高。
6、投资较高。
⑽、结论
脱硫脱水工艺方案是油气处理厂总工艺流程的核心部分,需根据原料天然气组成和商品天然气的技术指标要求,通过工艺方法特点、总工艺流程以及工程量、投资、能耗等技术经济指标进行对比确定。
方案一和方案二相比,总工艺流程较为简单,工程量较小,一次投资较省,主要消耗指标及年操作费用较低,而且不产生废碱液,有利于环保,所以本工艺技术方案采用方案一工艺路线,即砜胺法脱硫+分子筛脱水脱硫醇。
2、常温精脱硫在天然气中的应用
天然气用作化工生产原料气时,一般要求总硫<05×10-6,满足转化催化剂对原料气的要求,而传统精脱硫采用湿法脱除H2S,然后再用钴钼加氢串高温氧化锌工艺,由于湿法脱硫运行费用高,钴钼加氢串高温氧化锌存在能耗高、开车时间长、价格贵等缺点,国家气体净化剂重点工业基地,湖北省化学研究院气体净化中心开发了低成本的精脱硫剂。
经过十多年努力,k开发生产的T703特种氧化铁和DS1复合氧化物等十几种常温精脱硫剂和新工艺已在多个厂家应用,获得了较好的应用效果。
例1
在大港油田中的应用
天津大港油田天然气处理站液化气回收装置1994年引进美国PROQUIP公司技术,投运后硫化物对设备的腐蚀和管道堵塞等问题日趋严重,这不仅降低了该装置的运营效率,同时也严重威胁着该装置的安全运行。
为了解决天然气中硫化物对生产装置的腐蚀等问题,1997年该公司新上一套常温精脱硫装置,选用了我中心开发生产的T703特种氧化铁精脱硫剂。
1.1 工艺过程和操作参数
该装置的工艺示意流程如下:
混合天然气气水分离器T703净化气处理的天然气组成见表1,处理量为48000m3/h,操作压力3.0MPa,温度30~40℃,进口H2S含量≤20×10-6,出口要求H2S<1×10-6。
表1 大港油田天然气组成
脱硫工艺主要设备及脱硫剂用量见表2。
表2 主要设备及精脱硫剂的装填量
1.2 运行效果
从1997年该精脱硫装置投运以来,运行状况一直良好,精脱硫运行数据见表3。
表3 精脱硫装置运行结果
从以上数据看,精脱硫出口H2S<0.01×10-6,T703的精脱硫容大于20%,完全消除了H2S腐蚀造成的管道堵塞和停车检修,每年可为该公司减少1000多万元的经济损失,同时大大提高了该液化气回收装置的生产能力,每年可增加效益335万元。
例2在江汉油田中的应用
江汉油田钟市压气站和王场压气站是专门处理油田伴生气和拔顶气的净化站,伴生气中H2S含量800×10-6左右,拔顶气中H2S200×10-6左右,两种气源在球罐中混合,然后进入精脱硫系统将H2S脱除,以解决设备腐蚀和后工段液化石油气的铜片腐蚀问题。
以下介绍的是在钟市应用的例子。
2.1 工艺过程和操作参数
该脱硫工艺选用DS-1脱硫剂,其示意流程如下:
处理的伴生气和拔顶气组成见表4,处理气量700Nm3/h,压力0.4MPa,温度70~80℃,入口H2S含量230×10-6。
表4 钟市压气站伴生气和拔顶气组成
主要设备及脱硫剂用量见表5。
表5 主要设备及脱硫剂的装填量T
2.2使用效果
该系统自2002年6月运行至今,精脱硫出口H2S≤0.03×10-6,远远低于设计要求,石油液化气铜片腐蚀小于1b级,省掉了液化气脱硫,经济效益显著。
例3在泸天化中的应用
泸天化是以天然气为原料生产合成氨的大型企业,原来采用湿法脱H2S工艺,年操作费用高。
为降低成本,厂家决定在高温脱硫前采用干法脱硫将原料气中总硫脱至<5×10-6,经过考察,国内多个使用普通氧化铁脱硫剂的厂家,多因普通氧化铁硫容低而更换频繁造成脱硫费用高,例如四川某厂先后使用了4个厂家的氧化铁脱硫剂,使用寿命均在3个月以内。
中心根据泸天化工艺条件及过去一些天然气为原料的化肥厂采用氧化铁脱硫剂不理想的教训,在技术上采取了一些有效的措施,采用了T703型特种氧化铁精脱硫剂,于2003年12月已投入运行,取得了明显的效果。
3.1 工艺过程和操作参数
工艺示意流程如下:
天然气气水分离器T703T703处理的天然气组成见表6,处理量60000Nm3/h,操作压力1.0MPa,操作温度35℃,进口H2S含量20×10-6。
表6 泸天化天然气组成
主要设备及精脱硫剂用量见表7。
表7 主要设备及精脱硫剂的装填量
3.2 运行效果
该精脱硫装置于2003年12月投入运行至今,运行平稳,精脱硫塔出口H2S<0.03×10-6,运行数据见表8。
表8 泸天化精脱硫系统运行数据
注:
采用湖北省化学研究院生产的HC2型微量硫分析仪。
结语
实际应用情况表明,与普通脱硫剂相比,T703和DS1脱硫精度高,出口H2S≤0.03×10-6,完全达到了设计要求。
T703和DS1精脱硫剂具有硫容高,机械强度好,遇水不粉化,操作简单,使用方便等特点。
T703型精脱硫剂脱硫精度能满足天然气转化催化剂的要求。
DS1型精脱硫剂在无氧天然气中很好地解决了设备腐蚀和液化气铜片腐蚀问题,经济效益显著。
3、壳牌公司的天然气、炼厂气和液体的处理技术
⑴、 慨 述
从气体和轻烃中脱除硫化物和其他痕量化合物的气液处理技术,包含了各种各样的技术。
一般认为这一技术已相当成熟,可以改进和革新的机会不大。
但是,由于进料气体的不断变化且种类繁多,除了来自炼厂和酸性气储源的这些传统的气体来源,还有煤或渣油气化项目中产生的需处理的气体、开采石油时的伴生气体、生物气以及钻井平台上的天然气;这些进料气体的温度和压力很不相同,尤其是在组成上差别更大;同时最终产品规格也对处理工艺提出了各种不同的要求。
因此工艺设计者面临着如何用现有的技术知识来丰富设计,发展工艺的问题。
这里介绍的是壳牌公司所拥有的处理技术,包括近两年之内的主要发展。
壳牌公司在研发领域所做的努力使得壳牌的处理技术能尽可能多的满足工业领域对处理工艺的需要。
⑵、脱硫及CO2的气体和液体可再生处理技术
通常当仅仅(大)部分硫和CO2需要脱除时,称其为大部分脱硫工艺。
因在此脱硫后,已可满足销售指标的要求,剩余部分会继续留在过程气中。
如果(几乎)全部硫和CO2都被脱除了,则称为深度脱硫。
2.1ADIP和Sulfinol工艺
壳牌的ADIP工艺是一个可再生的胺工艺,用碱性胺如DIPA和MEDA做溶剂。
因为此工艺用的是胺的水溶液,因此对烃类、硫醇和有机硫的吸收很少。
如果要达到对H2S相对于CO2的高选择性吸收,一般选用MDEA做溶剂。
对于一般炼厂,通常使用DIPA,因为它能很好地抵抗原料气中微量化合物的有害降解和热降解。
其它用于炼厂的胺溶剂还有DEA、MEA、DGA和各种称其为MDEA系列的溶剂,即通常的MDEA溶液加入适当的添加剂以增强其选择性及动力学性能和稳定性。
ADIP工艺可用于以下情况:
从炼厂气和天然气中脱除H2S和CO2;
从含有CO2的气流中选择性的脱除H2S;
从LPG和LNG中脱除H2S和COS;
从气体中大部分脱除CO2。
除了胺的水溶液工艺,壳牌还发展了壳牌的Sulfinol工艺。
因为这一工艺使用水、环丁砜和胺溶剂的混合物作为溶剂,使得脱除COS、硫醇和有机硫化合物成为可能,其原因是加强了这些化合物在溶剂中的物理溶解性。
另外,对CO2溶解能力的增加可以提高H2S和CO2溶解的动力学性能。
Sulfinol-D工艺应用DIPA做胺溶剂,来达到H2S和CO2的深度脱除。
Sulfinol-M用MDEA做胺溶剂,被选择用来脱除H2S和实现CO2的大部分脱除。
当要求选择性脱除H2S或部分CO2时,则选择使用MDEA的Sulpinol-M做溶剂。
Sulfinol-M较之ADIP-M有两个优点:
可以脱除有机硫;再生时蒸汽消耗量较低。
对ADIP和Sulfinol装置的整体优化包括:
设计优化;整体工艺监控;溶剂的整体工艺化学分析;对溶剂质量控制的建议,如回收、过滤、活性炭床等。
其中整体工艺监控提供了对操作条件和工艺控制的建议。
目前世界上共有超过500套ADIP装置和超过200套Sulfinol装置正在运行