第一章冲压变形的基本原理.docx
《第一章冲压变形的基本原理.docx》由会员分享,可在线阅读,更多相关《第一章冲压变形的基本原理.docx(18页珍藏版)》请在冰豆网上搜索。
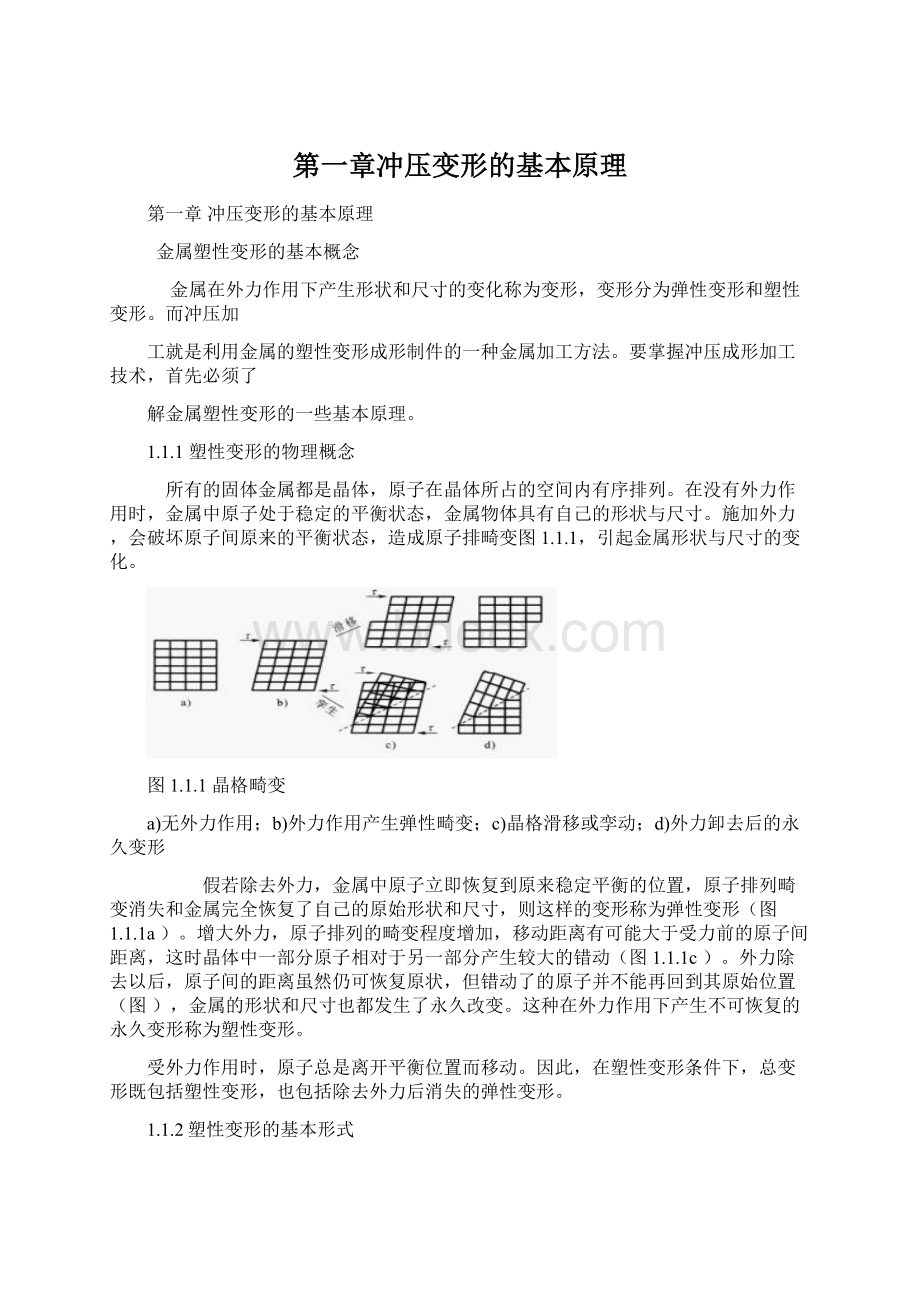
第一章冲压变形的基本原理
第一章 冲压变形的基本原理
金属塑性变形的基本概念
金属在外力作用下产生形状和尺寸的变化称为变形,变形分为弹性变形和塑性变形。
而冲压加
工就是利用金属的塑性变形成形制件的一种金属加工方法。
要掌握冲压成形加工技术,首先必须了
解金属塑性变形的一些基本原理。
1.1.1塑性变形的物理概念
所有的固体金属都是晶体,原子在晶体所占的空间内有序排列。
在没有外力作用时,金属中原子处于稳定的平衡状态,金属物体具有自己的形状与尺寸。
施加外力,会破坏原子间原来的平衡状态,造成原子排畸变图1.1.1,引起金属形状与尺寸的变化。
图1.1.1晶格畸变
a)无外力作用;b)外力作用产生弹性畸变;c)晶格滑移或孪动;d)外力卸去后的永久变形
假若除去外力,金属中原子立即恢复到原来稳定平衡的位置,原子排列畸变消失和金属完全恢复了自己的原始形状和尺寸,则这样的变形称为弹性变形(图1.1.1a)。
增大外力,原子排列的畸变程度增加,移动距离有可能大于受力前的原子间距离,这时晶体中一部分原子相对于另一部分产生较大的错动(图1.1.1c)。
外力除去以后,原子间的距离虽然仍可恢复原状,但错动了的原子并不能再回到其原始位置(图),金属的形状和尺寸也都发生了永久改变。
这种在外力作用下产生不可恢复的永久变形称为塑性变形。
受外力作用时,原子总是离开平衡位置而移动。
因此,在塑性变形条件下,总变形既包括塑性变形,也包括除去外力后消失的弹性变形。
1.1.2塑性变形的基本形式
金属塑性变形是金属在外力的作用下金属晶格先产生晶格畸变,外力继续加大时,产生晶格错动,而这种错动通常在晶体中采取滑移和孪动两种形式。
。
1.滑移
当作用在晶体上的切应力达到一定数值后,晶体一部分沿一定的晶面,向着一定的方向,与另一部分之间作相对移动,这种现象叫滑移,图1.1.1。
金属的滑移面,一般都是晶格中原子分布最密的面,滑移方向则是原子分布最密的结晶方向,因为沿着原子分布最密的面和方向滑移的阻力最小。
金属晶格中,原子分布最密的晶面和结晶方向愈多,产生滑移的可能性愈大,金属的可塑性就愈好。
晶格的滑移可通过位错理论来解释。
滑移时并不需要整个滑移面上的全部原子一齐移动,而只是在位错中心附近的少数原子发生移动。
2.孪生
孪动也是在一定的切应力作用下,晶体的一部分相对另一部分,沿着一定的晶面和方向发生转动的结果,已变形部分的晶体位向发生改变,与未变形部分以孪晶面对称,图1.1.1。
孪动与滑移的主要差别是:
①滑移过程是渐进的,而孪动过程是突然发生的;②孪动时原子位置不会产生较大的错动,因此晶体取得较大塑性变形的方式主要是滑移作用;③孪动后,晶体内部出现空隙,易于导致金属的破坏;④孪动所要求的临界切应力比滑移要求的临界切应力大得多,只有滑移过程很困难时,晶体方发生孪动。
3.晶间变形
滑移和孪动都是发生在单个晶粒内部的变形,称为晶内变形。
工业生产中实际使用的金属则是多晶体。
多晶体中的每个单晶体(晶粒)要受到四周晶粒的牵制,变形不如自由单晶体单纯,可塑性也不易充分发挥,会造成变形不均匀。
多晶体的变形方式除晶粒本身的滑移和孪动外,还有在外力作用下晶粒间发生的相对移动和转动而产生的变形,即晶间变形。
凡是加强晶间结合力、减少晶间变形、有利于晶内发生变形的因素,均有利于晶体进行的塑性变形。
当多晶体间存有杂质时,会使晶间结合力降低,晶界变脆,不利于多晶体进行塑性变形;当多晶体的晶粒为均匀球状时,由于晶粒界面对于晶内变形的制约作用相对较小,也具有较好的可塑性。
1.1.3金属的塑性与变形抗力
1.塑性及塑性指标
所谓塑性,是指固体材料在外力作用下发生永久变形而不破坏其完整性的能力。
塑性不仅与材料本身的性质有关,还与变形方式和变形条件有关。
所以,材料的塑性不是固定不变的,不同的材料在同一变形条件下会有不同的塑性,而同一种材料,在不同的变形条件下,会表现不同的塑性。
塑性是反映金属的变形能力,是金属的一种重要加工性能。
塑性指标是衡量金属在一定条件下塑性高低的数量指标。
它是以材料开始破坏时的塑性变形量来表示,它可借助于
一些实验方法测定。
常用的塑性指标有:
拉伸试验所得的延伸率:
(1.1.1)
断面收缩率:
(1.1.2)
式中:
L0,A0—拉伸试样原始标距长度(mm)和原始截面积(mm2);LK、AK分别为试样断裂后标距间长度(mm)和断裂处最小截面积(mm2);
除了拉伸试验外,还有爱力克辛试验、弯曲试验(测定板料胀形和弯曲时的塑性变形能力)和镦粗试验(测定材料锻造时的塑性变形能力)等。
需要指出,各种试验方法都是相对于特定的状况和变形条件下,承受的塑性变形能力,它们说明在某种受力状况和变形条件下,这种金属的塑性比那种金属的塑性高还是低,或者对某种金属来说,在什么样的变形条件下塑性好,而在什么样的变形条件下塑性差。
2.变形抗力
塑性成形时,使金属发生变形的外力称为变形力,而金属抵抗变形的反作用力,称为变形抗力。
变形力和变形抗力大小相等方向相反。
变形抗力一般用单位接触面积上的反作用力来表示。
在某种程度上,变形抗力反映了材料变形的难易程度。
它的大小,不仅取决于材料的流动应力,而且还取决于塑性成形时的应力状态、摩擦条件以及变形体的几何尺寸等因素。
塑性和变形抗力是两个不同的概念,前者反映塑性变形的能力,后者反映塑性变形的难易程度,它们是两个独立的指标。
人们常认为塑性好的材料,变形抗力低,塑性差的材料变形抗力高,但实际情况并非如此。
如奥氏体不锈钢在室温下可经受很大的变形而不破坏,说明这种钢的塑性好,但变形抗力却很高。
1.1.4影响金属塑性和变形抗力的主要因素
(一)影响金属塑性的主要因素
影响金属塑性和变形抗力的主要因素有两个方面,其一是变形金属本身的晶格类型,化学成份和组织状态等内在因素;其二是变形时的外部条件,如变形温度、变形速度和变形的力学状态等。
因此,只要有合适的内、外部条件,就有可能改变金属的塑性行为
1.化学成份和组织对塑性和变形抗力的影响
化学成份和组织对塑性和变形抗力的影响非常明显也很复杂。
下面以钢为例来说明。
①化学成份的影响在碳钢中,铁和碳是基本元素。
在合金钢中,除了铁和碳外还包含有硅、锰、铬、镍、钨等。
在各类钢中还含有些杂质,如磷、硫、氨、氢、氧等。
碳对钢的性能影响最大。
碳能固溶到铁里形成铁素体和奥氏体固溶体,它们都具有良好的塑性和低的变形抗力。
当碳的含量超过铁的溶碳能力,多余的碳便与铁形成具有很高的硬度,而塑性几乎为零的渗碳体。
对基体的塑性变形起阻碍作用,降低塑性,抗力提高。
可见含碳量越高,碳钢的塑性成形性能就越差。
合金元素加入钢中,不仅改变了钢的使用性能,而且改变了钢的塑性成形性能,其主要的表现为:
塑性降低,变形抗力提高。
这是由于合金元素溶入固溶体(α—Fe和γ-Fe),使铁原子的晶体点阵发生不同程度的畸变;合金元素与钢中的碳形成硬而脆的碳化物(碳化铬、碳化钨等);合金元素改变钢中相的组成,造成组织的多相性等,都造成钢的抗力提高,塑性降低。
杂质元素对钢的塑性变形一般都有不利的影响。
磷溶入铁素体后,使钢的强度、硬度显著增加,塑性、韧性明显降低。
在低温时,造成钢的冷脆性。
硫在钢中几乎不溶解,与铁形成塑性低的易溶共晶体FeS,热加工时出现热脆开裂现象。
钢中溶氢,会引起氢脆现象,使钢的塑性大大降低。
②组织的影响钢在规定的化学成份内,由于组织的不同,塑性和变形抗力亦会有很大的差别。
单相组织比多相组织塑性好,抗力低。
多相组织由于各相性能不同,使得变形不均匀,同时基本相往往被另一相机械地分割,故塑性降低,变形抗力提高。
晶粒的细化有利提高金属的塑性,但同时也提高了变形抗力。
这是因为在一定的体积内细晶粒的数目比粗晶数目要多,塑性变形时有利于滑移的晶粒就较多,变形均匀地分散在更多的晶粒内,另外晶粒越细,晶界面越曲折,对微裂纹的传播越不利。
这些都有利于提高金属的塑性变形能力。
另一方面晶粒多,晶界也愈多,滑移变形时位错移动到晶界附近将会受到阻碍并堆积,若要位错穿过晶界则需要很大的外力,从而提高了塑性变形抗力。
另外钢的制造工艺,如冶炼、浇铸、锻轧、热处理等都影响着金属的塑性和变形抗力。
2.变形温度对塑性和变形抗力的影响
变形温度对金属和合金的塑性有很大的影响。
就多数金属和合金而言,随着温度的升高,塑性增加,变形抗力降低。
这种情况,可以从以下几个方面进行解释。
①温度升高,发生回复和再结晶。
回复使金属的加工硬化得到一定程度的消除,再结晶能完全消除加工硬化。
从而使金属的塑性提高,变形抗力降低。
②温度升高,原子热运动加剧,动能增大,原子间结合力减弱,使临界剪应力降低,不同滑移系的临界剪应力降低速度不一样。
因此,在高温下可能出现新的滑移系。
滑移系的增加,提高了变形金属的塑性。
③温度升高,原子的热振动加剧,晶格中原子处于不稳定状态。
此时,如晶体受到外力作用,原子就会沿应力场梯度方向,由一个平衡位置转移到另一个平衡位置,使金属产生塑性变形。
这种塑性变形的方式称为热塑性,也称扩散塑性。
④温度升高,晶界强度下降,使得晶界的滑移容易进行。
同时,由于高温下扩散作用加强,使晶界滑移产生的缺陷得到愈合。
由于金属和合金的种类繁多,上述一般的结论并不能概括各种材料的塑性和变形抗力随温度的变化情况。
可能在温升过程中的某些温度间,往往由于过剩相的析出或相变等原因,而使金属的塑性降低和变形抗力增加(也可能降低)。
3.变形速度对塑性和变形抗力的影响
所谓变形速度是指单位时间变形物体应变的变化量,塑性成形设备的加载速度在一定程度上反映了金属的变形速度,它对塑性有两个方面的影响。
①变形速度大时,要同时驱使更多的位错更快地运动,金属晶体的临界剪应力将提高,使变形抗力增大;当变形速度大时,塑性变形来不及在整个变形体内均匀地扩展,此时,金属的变形主要表现为弹性变形。
根据虎克定律,弹性变形量越大,则应力越大,变形抗力也就越大。
另外,变形速度增加后,变形体没有足够的时间进行回复和再结晶,而使金属的变形抗力增加,塑性降低。
②在高变形速度下,变形体吸收的变形能迅速地转化为热能(热效应),使变形体温升高(温度效应)。
这种温度效应一般来说对塑性的增加是有利的。
常规的冲压设备工作速度都较低,对金属塑性变形的性能影响不大。
考虑变形速度因素,主要基于零件的尺寸和形状。
对大型复杂的零件成形,变形量大且极不均匀,易局部拉裂和起皱,为了便于塑性变形的扩展,有利于金属的流动,宜采用低速的压力机或液压机。
小型零件的冲压,一般不考虑变形的速度对塑性和变形抗力的影响,主要从生产效率来考虑。
冲压成形时变形毛坯的力学特点与分类
1.3.1变形毛坯的分区
板料在进行各种冲压成形时,可以把变形毛坯分为变形区和不变形区。
变形区是正在进行特定变形的部分;不变形区可能是已经经历了变形的已变形区,或尚未参与变形的待变形区,也可能是在冲压成形的全过程中都不参与变形的不变形区,还有在变形过程中起传递变形力作用的传力区。
图1.3.1示出了基本冲压成形工序拉深、翻边和缩口变形过程中的毛坯各区的分布,具体划分情况见表。
图1.3.1毛坯各区划分举例
a)拉深b)翻边c)缩口
表1.3.1冲压变形毛坯各区划分情况
冲压方法
变形区
不变形区
已变形区
待变形区
传力区
拉深
A
B
无
B
翻孔
A
B
无
B
缩口
A
B
C
C
从本质上看,各种冲压成形过程就是毛坯变形区在其主应力作用下产生应变的过程。
所以,毛坯变形区的受力情况和变形特点是决定各种冲压成形根本性质的主要依据。
1.3.2变形区的应力应变特点
绝大多数板料冲压变形都是平面应力状态。
一般在板料表面上不受力或受数值不大的力,所以可以认为在板厚方向上的应力数值为零。
使毛坯变形区产生塑性变形应力是在板料平面内相互垂直的两个主应力。
除弯曲变形外,在大多数情况下都可以认为这两个主应力在厚度方向上的数值是不变的。
因此,可以把所有冲压变形方式按毛坯变形区的受力情况(应力状态)和变形特点从变形力学的角度归纳为以下四种情况。
1.冲压毛坯变形区受两向拉应力的作用
在轴对称变形时,可以分为以下两种情况:
σr>σθ>0,且σt=0
σθ>σr>0,且σt=0
这两种情况在冲压应力图(图1.3.2)中处于GOH和AOH(第Ⅰ象限)范围内,而且在冲压变形图(图中则处于AON及AOC范围内,与此相对应的变形是平板毛坯的局部胀形、内孔翻边、空心毛坯的胀形等。
图1.3.2 冲压应力图
2.冲压毛坯变形区受两向压应力的作用
在轴对称变形时,可以分为下边两种情况:
σr<σθ<0,且σt=0
σθ<σr<0,且σt=0
这两种情况在冲压应力图中处于COD及DOE(第Ⅲ象限)范围内,而在冲压变形图中则处于GOE及GOL范围内,与此相对应的变形是缩口变形等。
3.冲压毛坯变形区受异号应力的作用,而且拉应力的绝对值大于压应力的绝对值,在轴对称变形时,可以分为下面两种情况:
σr>0>σθ,σt=0及|σr|>|σθ|
σθ>0>σr,σt=0及|σθ|>|σr|
这两种情况在冲压应力图中处于GOF及AOB范围内,而在冲压变形图中处于MON及COD范围内,与此相对应的冲压变形是扩口等。
1.3.3冲压变形图
4.冲压毛坯变形区受异号应力的作用,而且压应力的绝对值大于拉应力的绝对值,在轴对称变形时,可以分为以下两种情况:
σr>0>σθ,σt=0及|σθ|>|σr|
σθ>0>σr,σt=0及|σr|>|σθ|
这两种情况在冲压应力图中处于EOF及BOC范围内,而在冲压变形图中处于MOL及DOE范围内,与此相对应的冲压变形是拉深等。
综合上面四种受力情况的分析结果,可以把全部冲压变形概括为两大类别:
伸长类变形与压缩类变形。
当作用于毛坯变形内的拉应力的绝对值最大时,在这个方向上的变形一定是伸长变形,称这种冲压变形为伸长类变形。
伸长类变形包括冲压变形图中的MON、NOA、AOB、BOC及COD等五个区。
当作用于毛坯变形区内的压应力的绝对值最大时,在这个方向上的变形一定是压缩变形,称这种冲压变形为压缩类变形。
压缩类变形包括冲压变形图中的MOL、LOH、HOG、GOE及EOD等五个区。
伸长类成形的极限变形参数主要决定于材料的塑性,并且可以用板材的塑性指标直接或间接地表示。
例如多数实验结果证实:
平板毛坯的局部胀形深度、圆柱体空心毛坯的胀形系数、圆孔翻边系数、最小弯曲半径等都与伸长率有明显的正比关系。
压缩类成形的极限变形参数(如拉深系数等),通常都是受毛坯传力区的承载能力的限制,有时则受变形区或传力区的失稳起皱的限制。
由于两类成形方法的极限变形参数的确定基础不同,所以影响极限变形参数的因素和提高极限变形参数的途径和方法也不一样。
1.3.3冲压成形中的变形趋向性及其控制
在冲压过程中,成形毛坯的各个部分在同一个模具的使用下,却有可能发生不同形式的变形,即具有不同的变形趋向性。
这时候,毛坯的各个部分是否变形和以什么方式变形,以及我们能不能借助于正确地设计冲压工艺和模具来保证,在进行和完成预期变形的同时,排除其它一切不必要的和有害的变形等等,则是获得合格的高质量冲压件的根本保证。
也是对冲压过程中变形趋向性及其控制方法进行研究的目的所在。
图1.3.4变形趋向性对冲压工艺的影响
变形区发生塑性变形所必需的力,是由模具通过传力区获得的。
而同一个毛坯的变形区和传力区都是相毗联的图1.3.1,所以在变形区与传力区的分界面上使用的内力的性质与大小一定是完全相同的。
在同一个内力的使用下,变形区和传力区都有可能产生塑性变形。
但是,由于它们可能产生的塑性变形的方式不同,而且也由于变形区和传力区之间的尺寸关系不同,通常总是有一个区需要比较小的塑性变形力,首先进入塑性状态,产生塑性变形。
因此,可以认为这个区是相对的弱区。
为保证冲压过程的顺利进行,必须保证在该道冲压工序中应该变形的部分—变形区成为弱区,以便在把塑性变形局限于变形区的同时,排除在传力区产生任何不必要的塑性变形的可能。
根据上述的道理,可以得出一个十分重要的结论:
在冲压过程中,需要最小变形力区是个相对的弱区,而且弱区必先变形,
图1.3.5环形毛坯的变形趋向
a)变形前的工具与毛坯 b)拉深 c)翻边 d)胀形
在设计工艺过程,选定工艺方案、确定工序和工序间尺寸时,也必须遵循“弱区必先变形,变形区应为弱区”的道理。
如图1.3.4所示的零件,当D-d较大,h较小时,可用带孔的环形毛坯用翻边方法成形;但是当D-d较小,h较大时,如用翻边方法成形,则不能保证毛坯外环是需要变形力较大的强区,以及翻边部分是变形力较小的弱区条件。
所以在翻边时,毛坯的外径必然收缩,使翻边成形成为不可能实现的工艺方法。
在这种情况下,就必须改变原工艺过程为拉深后切底和切外缘的工艺方法,或采用加大外径的小环形毛坯,经翻边成形后再冲切外圆的工艺过程(如虚线所示)。
在实际生产当中,用来控制毛坯的变形趋向性的措施,有下列几个方面。
1.合理的确定毛坯尺寸
变形毛坯各部分的相对尺寸关系,是决定变形趋向性的最为重要的因素,所以在设计工艺过程中,一定要合理地确定初始毛坯的尺寸和中间毛坯的尺寸,保证变形的趋向符合于工艺的要求。
图1.3.5(a),所示的毛坯,由于其尺寸D0与dp的相对关系不同,具有三种可能的变形趋向.因此,必须根据冲压件的形状,合理地确定毛坯的尺寸,用以控制变形的趋向,获得所要求的零件形状和尺寸精度。
改变毛坯的尺寸,可得到图1.3.5三种变形中的一种。
当D0/dp与d0/dp都较小时,宽度为D0-dp的环形部分成为弱区,于是得到毛坯外径收缩的拉深变形(b)图;当D0/dp与d0/dp都比较大时,宽度为dp-d0的环形部分成为弱区,于是得到毛坯内孔扩大的翻边变形(c)图;当D0/dp很大,而d0/dp很小或等于零时(不带内孔的毛坯),虽然毛坯外环的拉深变形与内部的翻边变形的变形阻力都增大了,但是毛坯的内部仍是相对的弱区,产生的变形是内部的胀形(d)图。
胀形时,毛坯的外径和内孔的尺寸都不发生变化,或者变化很小,成形仅靠毛坯厚度的变薄实现。
图中所示毛坯的相对尺寸与变形趋向之间的关系,列表。
表1.3.2 平板环形毛坯的变形趋向
尺寸关系
成形方式(变形趋向)
备注
D0/dp<~2,d0/dp<
拉深
D0/dp>,d0/dp>~
翻边
要得到图1.3.5(c)所示的零件,d0/dp的值必须加大,否则内孔会开裂
D0/dp>,d0/dp<
胀形
d0/dp=0时,是完全胀形
以变形毛坯尺寸关系对变形趋向性的控制实例很多,如图1.3.6是钢球活座套的冲压工艺过程,共包括有落料a)、拉深b)、冲孔c)、翻边d)等四道冲压工序。
在第二道工序拉深时,毛坯的外形是弱区,所以塑性变形发生在毛坯的外形部位,并使其外径由Φ59减到Φ52,当冲Φ24内孔以后,使毛坯的中间部分由强区变成弱区,并使原来是弱区的外缘部分转变成为相对的强区,其结果变形区由毛坯的外部转移到毛坯的中间部分,从而保证了第四道工序内孔扩翻边变形的进行。
图1.3.6钢球活座套的冲压工艺过程中的变形趋向性的控制
a)落料b)拉深c)冲孔d)翻边
2.正确设计模具工作部分形状和尺寸
改变模具工作部分的几何形状和尺寸也能对毛坯的变形趋向性起控制使用。
例如增大凸模的圆角半径rp,减小凹模的圆角半径rd(图1.3.5),可以使拉深变形的阻力增大,并使翻边的阻力减小,所以有利于翻边变形的实现。
反之,增大凹模圆角半径rd和减小凸模的圆角半径rp,则有利于实现拉深变形,而不利于实现翻边变形。
利用模具工作部分的圆角半径控制毛坯变形趋向的情况,在生产中是常常见到的。
3.改变毛坯与模具表面的摩擦条件
改变毛坯与模具接触表面之间的摩擦阻力,借以控制毛坯变形的趋向,这也是生产中时常采用的一个方法。
例如,加大图1.3.5中所示的压边力Q的作用使毛坯和压边圈及凹模面之间的摩擦阻力加大,结果不利于拉深变形,而有利于翻边和胀形变形的实现。
反之,增加毛坯与凸模表面的摩擦阻力,减小毛坯与凹模表面的摩擦阻力,都有利于拉深变形。
所以,对变形毛坯的润滑以及对润滑部位的选择,也都是对毛坯变形趋向起相当重要作用的因素。
如拉深毛坯的单面润滑就是这个道理。
4.其它工艺措施
采用局部加热或局部深冷的办法,降低变形区的变形抗力或提高传力区的强度,都能达到控制变形趋向性的目的,可使一次成形的极限变形程度加大,提高生产效率。
板料冲压成形性能及冲压材料
1.4.1板料的冲压成形性能
板料的冲压成形性能是指板料对各种冲压加工方法的适应能力。
如便于加工,容易得到高质量和高精度的冲压件,生产效率高(一次冲压工序的极限变形程度和总的极限变形程度大),模具消耗低,不易产生废品等。
板料的冲压成形性能是一个综合性的概念,冲压件能否成形和成形后的质量取决于成形极限(抗破裂性),贴模性和形状冻结性。
成形极限是指板料成形过程中能达到的最大变形程度,在此变形程度下材料不发生破裂。
可以认为,成形极限就是冲压成形时,材料的抗破裂性。
板料的冲压成形性能越好,板料的抗破裂性也越好,其成形极限也就越高。
板料的贴模性指板料在冲压成形过程中取得模具形状的能力,形状冻结性指零件脱模后保持其在模内获得的形状的能力。
影响贴模性的因素很多,成形过程发生的内皱、翘曲、塌陷和鼓起等几何缺陷都会使贴模性降低。
形状冻结性影响的最主要因素是回弹,零件脱模后,常因回弹过大而产生较大的形状误差。
材料冲压成形性能中的贴模性和形状冻结性是决定零件形状精度的重要因素,而成形极限是材料将开始出现破裂的极限变形程度。
破裂后的制件是无法修复使用。
因此生产中以成形极限作为板料冲压成形性能的判定尺度,并用这种尺度的各种物理量作为评定板料冲压成形性能的指标。
1.4.2板材冲压成形试验的试验方法
板料冲压性能试验方法通常分为三种类型:
力学试验、金属学试验(统称间接试验)和工艺试验(直接试验)。
其中常用的力学试验有简单拉伸试验和双向拉伸试验,用以测定板料的力学性能指标,而这些性能与冲压成形性能有着密切的关系;金属学试验用以确定金属材料的硬度、表面粗糙度、化学成分、结晶方位与晶粒度等;工艺试验也称模拟试验,它是用模拟生产实际中的某种冲压成形工艺的方法测量出相应的工艺参数,试件的应力状态和变形特点与相应的冲压工艺基本一致,试验结果能反映出金属板料对该种冲压工艺的成形性能。
例如Swift的拉深试验,测出极限拉深比LDR;TZP试验,测出对比拉深力的T值;Erichsen试验,测出极限胀形深度Er值;扩孔试验测出极限扩孔率λ等。
有关的试验方法参见金属板料试验标准。
1.4.3金属板料的力学性能与冲压成形性能的关系
金属板料的力学性能是用板料试样作单相拉伸试验求得的,由于试验的目的