曲轴磨床体壳铸造工艺设计说明书.docx
《曲轴磨床体壳铸造工艺设计说明书.docx》由会员分享,可在线阅读,更多相关《曲轴磨床体壳铸造工艺设计说明书.docx(10页珍藏版)》请在冰豆网上搜索。
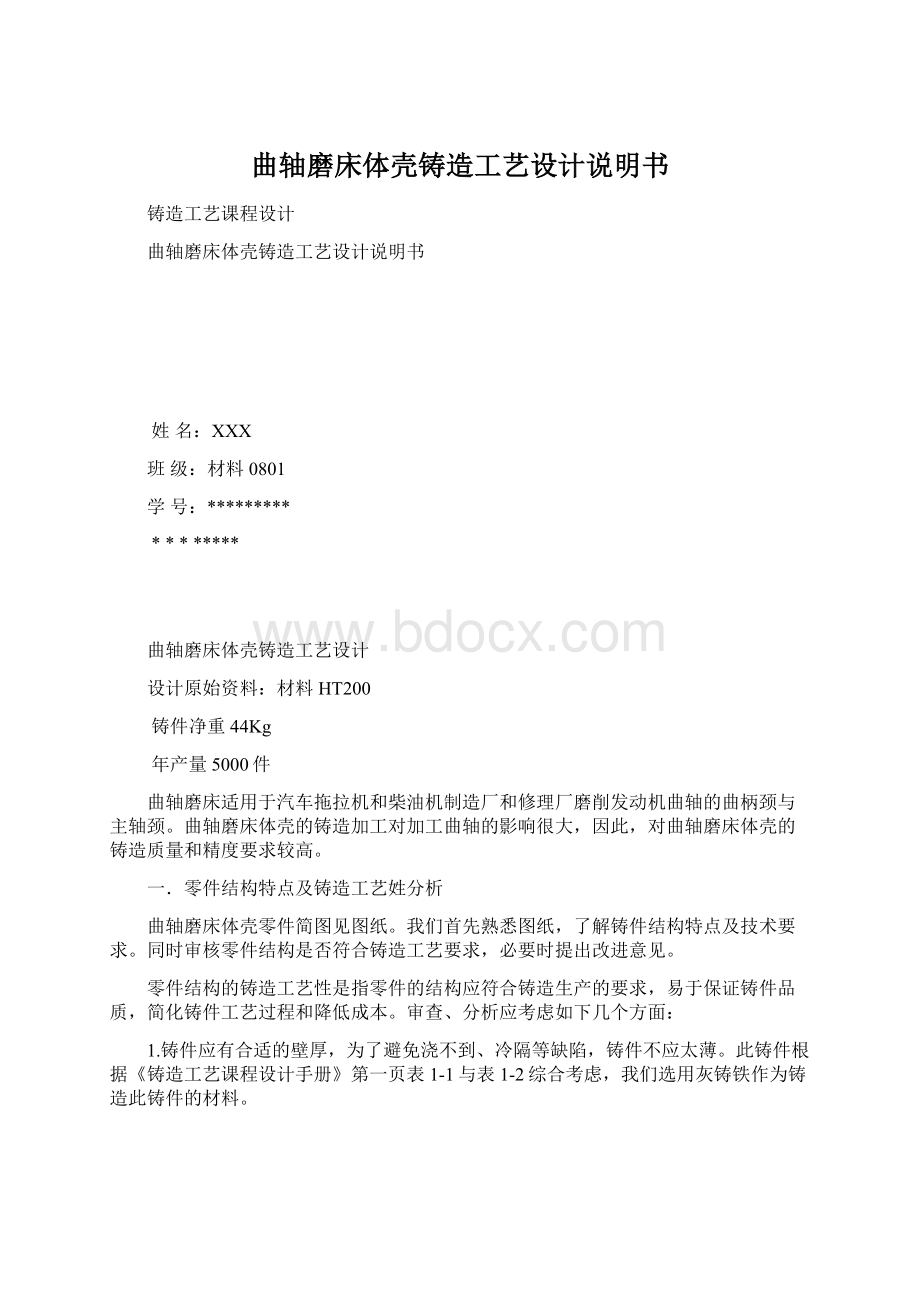
曲轴磨床体壳铸造工艺设计说明书
铸造工艺课程设计
曲轴磨床体壳铸造工艺设计说明书
姓名:
XXX
班级:
材料0801
学号:
*********
********
曲轴磨床体壳铸造工艺设计
设计原始资料:
材料HT200
铸件净重44Kg
年产量5000件
曲轴磨床适用于汽车拖拉机和柴油机制造厂和修理厂磨削发动机曲轴的曲柄颈与主轴颈。
曲轴磨床体壳的铸造加工对加工曲轴的影响很大,因此,对曲轴磨床体壳的铸造质量和精度要求较高。
一.零件结构特点及铸造工艺姓分析
曲轴磨床体壳零件简图见图纸。
我们首先熟悉图纸,了解铸件结构特点及技术要求。
同时审核零件结构是否符合铸造工艺要求,必要时提出改进意见。
零件结构的铸造工艺性是指零件的结构应符合铸造生产的要求,易于保证铸件品质,简化铸件工艺过程和降低成本。
审查、分析应考虑如下几个方面:
1.铸件应有合适的壁厚,为了避免浇不到、冷隔等缺陷,铸件不应太薄。
此铸件根据《铸造工艺课程设计手册》第一页表1-1与表1-2综合考虑,我们选用灰铸铁作为铸造此铸件的材料。
2.铸件结构不应造成严重的收缩阻碍,注意薄壁过渡和圆角,铸件薄厚壁的相接拐弯等厚度的壁与壁的各种交接,都应采取逐渐过渡和转变的形式,并应使用较大的圆角相连接,避免因应力集中导致裂纹缺陷。
3.铸件内壁应薄于外壁,铸件的内壁和肋等,散热条件较差,应薄于外壁,以使内、外壁能均匀地冷却,减轻内应力和防止裂纹。
4.壁厚力求均匀,减少肥厚部分,防止形成热节。
5.利于补缩和实现顺序凝固。
6.防止铸件翘曲变形。
7.避免浇注位置上有水平的大平面结构。
对于曲轴磨床体壳的铸造工艺性审查、分析如下:
砂型铸造条件下该轮廓尺寸为442mm*270mm*223mm,净重为44Kg,允许的最小壁厚查《铸造工艺课程设计手册》第一页表1-1与表1-2得:
最小允许壁厚为12mm,最大壁厚为25mm。
此件材质牌号为HT200是普通灰铸铁,在一般情况下不会产生浇不足现象,也不会产生缩松和缩孔缺陷。
铸件内腔和外部形状比较简单,起模方便,内腔砂芯形状简单,下芯方便,芯子稳定性好。
根据《铸造工艺课程设计手册》第一页表1-3、表1-4与表1-5经过检验零件图上各处的铸造圆角、壁厚的过度形式、铸件壁的连接形式均较合理,符合要求。
二.铸型种类的选择
曲轴磨床体壳铸件结构比较简单,尺寸比较小,重量也比较轻,属于中、小型铸件,铸型选取湿型较为合理。
因为用湿型铸造有很多的优点:
生产率高,生产周期短,适合成批、大量生产;砂型不需要烘干,节约燃料、设备和车间生产面积;铸型不易发生变形,得到铸件精度高;砂型的落砂性好,砂箱使用寿命较长。
三.造型造芯方法的选择
曲轴磨床体壳铸件属于大批量生产,一般采取机械化生产。
因为在这种条件下用机器造型和造芯,不但可以改善铸件质量,提高生产率,而且制造模版、砂箱、芯盒等工艺装备在经济上也是合理的。
选择造型和造芯机械还应根据铸件结构和工厂生产设备条件总和考虑。
根据要求我们选用Z148B造型机。
四.浇注位置的选择
铸件浇注位置是指铸件在铸型中浇注时所处的位置。
浇注位置选择得正确与否,对保证铸件质量、简化造型工艺有很大影响。
选择铸件浇注位置时,主要以保证铸件质量为前提,同时尽量做到简化造型工艺和浇注工艺。
根据生产经验应注意如下几项原则:
1.铸件质量要求高的或主要的加工面,浇注时应朝下
2.有宽大平面的铸件,浇注时应将大面朝下
3.为了保证铸件薄壁部分能充满液体金属,浇注时应尽量将薄壁部分放在铸件下面或放在内浇口以下
4.浇注位置选择应尽量减少砂芯的数量
5.容易产生缩松、缩孔的铸件,应将厚大部分朝上或放在侧面
根据以上原则我们选择的内浇口均满足以上要求,且铸件大部分处于下箱,使上箱高度减低;内腔砂芯下芯头大于上芯头,下芯方便,芯子稳定性好。
五.分型面的选择
分型面是指两半铸型相互接触的表面。
分型面的优劣在很大程度上影响铸件的尺寸精度、成本和生产率。
选择分型面时应注意一下原则:
1.应使铸件全部或大部分置于同一半型内
2.应尽量减少分型面的数目
3.分型面应尽量选用平面
4.便于下芯、合箱和检测
5.不使砂箱过高
6.受力件的分型面的选择不应削弱铸件结构强度
7.注意减轻铸件清理和机械加工量
综上,为了下芯合箱方便,只能从轴孔水平中心线分型。
其优点为浇注位置与分型面一致;内腔砂芯和外砂芯下芯方便,稳定性好。
六.砂箱中铸件数目的确定
造型生产线上Z148B,砂箱最大尺寸为850*475,体壳铸件与其它中小型铸件一起组成中小型铸件生产线根据零件尺寸,一个砂箱中可以放置一个铸件。
七.工艺参数的确定
1.铸件尺寸精度
影响尺寸精度的主要因素有铸造工艺、铸造收缩率和模具装备精度三方面。
由于生产条件不同,这三个方面对铸件尺寸精度影响的程度也不同。
我们选用的是机械化造型,根据下表,机器造型时工艺方面是造成尺寸偏差的主要因素。
根据年产量5000件为大件量生产,确定铸件精度为六级精度。
公称重=铸件净重+加工余量重。
铸件净重为44Kg;
加工余量和不铸出孔的铸铁重量,根据此件估计占铸件重5%;
公称重=44*(1+5%)=46.2Kg。
由《铸造工程师手册》查得重量公差等级为8级铸件重量偏差差的为6%,即得到的铸件重量不超过49Kg。
2.铸件收缩率的确定
铸造收缩率的选择正确与否,影响铸件尺寸精度。
大批量机器造型时,收缩率通过试制来纠正,因而影响较小。
曲轴磨床体壳材料为HT200,重44Kg,收缩时受阻。
查表得出收缩率为0.9%。
3.机械加工余量的确定
铸件的加工余量就是铸件上要用机械加工的方法切去的金属层厚度。
对于铸件加工表面,必须留有适当的机械加工余量,才能使铸件在机械加工之后获得光洁的表面和尺寸精度,以符合图纸要求。
铸件加工余量的大小决定于铸件的生产类型、铸件最大尺寸、加工余量等级、铸造合金的种类、铸件的公称尺寸等因素,在工艺设计时应根据铸件的实际情况合理地确定。
对于大量、成批量生产的铸件,因为可以采用机械化程度较高或工艺装备较完善的铸造方法,所以一般选用较小的机械加工余量,以节省机械加工工时。
根据以上得:
曲轴磨床体壳为六级精度铸件,查表得最大加工余量为4.0mm,最小加工余量为3.0mm。
4.铸孔
曲轴磨床体壳铸件是大量生产,铸孔尺寸查资料得最大尺寸为30mm。
以下几种情况孔或槽可以不铸出:
A.用机械加工方法比铸造出来经济合理
B.孔或槽必须用机械加工的方法才能保证精度要求
C.孔或槽的深度很深,而空的直径或槽的宽度很小
体壳上的孔为Φ15,Φ10,螺纹孔为M8和M6,所以均为不铸出孔,将来成型后可再进行机械加工。
5.拔模斜度
为了便于起模或自芯盒中取出砂芯,模样垂直于分型面的壁,应该有向着分型面逐渐扩大的斜度,该斜度成为拔模斜度。
拔模斜度的大小取决于模样材料的表面光洁度、模样上垂直于分型面壁的高度,以及造型材料特点和造型方法等
曲轴磨床体壳拔模斜度,根据已确定铸件浇注位置和分型面,分析起模情况,从资料查出拔起斜度为0°45′。
八.砂芯设计
砂芯是组成铸型的重要部分,砂芯是用来形成铸件内腔、各种成形孔及外形不易起模的部分。
砂芯的设计直接影响到砂芯制造工艺、芯盒结构的复杂程度以及铸型装配质量。
确定砂芯形状的基本原则:
1.保证逐渐内墙尺寸精度。
2.保证操作方便。
3.保证铸件壁厚均匀。
使砂芯的起模斜度和模样的起模斜度大小,方向一致,保证铸件壁厚均匀。
4应尽量减少砂芯数目。
5.填砂面应宽敞,烘干支撑面是平面。
根据铸件尺寸大小和结构特点以及其体生产条件,进行砂芯分割,确定合理的砂芯数目与形状。
在下列情况下,要把砂芯分割成数块:
1.为了简化复杂大型铸件内部空腔的砂芯尺寸和形状
2.为了造芯方便
3.在成批量生产时,为了使用机器来制造砂芯
4.为了造芯和下芯方便或防止较长的砂芯在烘干时发生变形
5.制造形状比较复杂的砂芯
6.为了保证铸件尺寸精度及铸型合箱方便
根据以上原则,曲轴磨床体壳的铸造采用两个砂芯,图纸上的1#和2#砂芯,采用冷凝树脂砂,热芯盒制造。
九.浇注系统
浇注系统是铸型中液态金属流入型腔的通道之总称,它由浇口杯、直浇道、直浇道窝、横浇道和内浇道组成。
1.选择浇注系统类型
浇注系统分为封闭式浇注系统,开放式浇注系统。
虽然封闭式浇注系统但充型速度快,冲刷力大,易产生喷溅,金属液易氧化。
但是它全部的全部截面上的金属液压力均高于型壁气体压力能使金属液充满浇注系统。
而且控流截面积在内浇道,浇注开始后,金属液容易充满浇注系统,呈有压流动状态。
阻渣能力强,适用于各种铸铁件。
此零件的重量为44Kg,壁厚为7mm(铸造工艺手册上查得为薄壁件),所以铸件为小型铸件。
综合考虑,薄壁件经常会出现浇不足的现象,所以对流速要求较大。
所以选择封闭式浇注系统。
2.确定内浇道在铸件上的位置、数目、金属引入方向
根据零件结构图确定分为两个模板进行造型,零件上下模详见图纸。
为了方便造型,内浇道开设在分型面上。
经过对零件图的分析为了防止浇注时会产生的铸造缺陷决定开设一个内浇道。
而且可以看出零件的底部结构比较上部分来说较为简单,这样可以是逐渐由简单到复杂的顺序来凝固,将来可是补缩效果良好。
所以把内浇道设在为横浇道,设在铸件的的侧面。
使金属液可以从侧面引入。
为了使造型方便,所以把内浇道开设在砂型的分型面上。
在设计内浇道时采用扁平梯形,这样可以有效防止夹杂物流入铸型型腔,而且不易在铸件连接处产生缩松,同时便于清理。
横浇道采用高梯形,这样可进一步增强阻渣能力,为内浇道提供干净的金属液。
直浇道为圆柱形,浇口杯采用普通漏斗形。
从铸造工艺手册得下表:
浇注系统选择的是封闭式浇注系统,各浇道的截面积之比为:
F内:
F横:
F直=1:
1.1:
1.15
为了使金属也能平稳的均匀的流入横浇道,一般会在直浇道的起始地方,也就是浇口,会设置一个浇口杯这样可以减小金属液垂直流入时浇道的冲刷力,从而减小沙粒的的脱落,而且这样可以降低对工人师傅的技术要求使浇注变得相对简单点。
横浇道和直浇道相连的地方通常设有一个直浇道窝,它的作用是为横浇道提供一个平稳流动的金属液,因当金属液从直浇道留下来时,有很大的冲压力,如果不设置直浇道窝,使金属液直接进入横浇道,这样会使流入横浇道的金属液由于在拐角处的冲力产生的紊流而夹杂大量的气体,且金属液流动的很不平稳,这样势必会造成铸造缺陷(气孔,砂眼等)所以在此设置一个直浇道窝是很有必要的。
而横浇道采取如图所示的多阶梯式,这样可以增强其阻渣的能力,也能进一步控制金属液的流动平稳性,降低冲刷力,减小铸造缺陷。
3.浇注系统计算
内浇口最小截面采用水力学计算公式计算:
∑F内=G/(0.31*u*t*√Hp)
式中:
∑F内—内浇口总截面积,c㎡
G—铁型中铁水总重,即铸铁重与浇冒口重只和,该件浇冒口重占铸件总重的25%,故G=44*(1+25%)=55Kg
T—浇注时间,s
U—流速系数,查得u=0.5
Hp—平均压力头,Hp=H0-P²/2c,H0为上箱高度,H0=250mm
曲轴磨床体壳浇注时间计算公式,采用公式:
t=s√G
式中:
s—壁厚系数
根据《铸造工程师手册》查得s为22.
曲轴磨床体壳壁厚为9到15cm,故t=s√G≈15s
验证浇注时间是否合适,型腔内金属液上升速度用下列公式计算:
V=c/tmm/s
式中c为铸件最低点到最高点的距离,按浇注时间的位置确定,此件c取27mm,
则v=270/15=18mm/s
从《铸造工程师手册》查得型内金属液最小上升速度为10到20mm/s。
计算结果在规定值内,浇注时间15s是合理的。
查得各个浇到=道截面积:
内浇口:
48*45*15mm
横浇道:
32*23*28mm
直浇道:
底部直径D=32mm。
工装设计
铸造工艺装备简称工装,它是造型、造芯和合箱过程中所使用的装置及工模具的总称。
例如模样、模板(型板)、模板框、芯盒、砂箱、套箱、托板、压板、烘芯板(器)、样板、定位销套、锁箱卡具、砂芯组装夹具及浇、冒口模样等等。
因为工艺装备是为铸型工艺过程服务的,所以合理的工艺装备对提高铸件的尺寸精度、表面光洁度有直接的影响,对提高生产率,改善劳动条件起着重要的作用。
对工艺装备的要求是好用、好造和好修。
首先要坚固耐用,轻巧方便,满足工艺的要求;其次要容易制造,成本低;还要便于维修和修理等等。
在不同生产批量条件下使用的工装有着不同的要求,设计时应特别注意。
一.金属模样
模样是造型工艺过程必须的工艺装备,用来形成铸型的型腔,因此直接关系着铸件的形状和尺寸精确
1.金属模样的选择
为了使模样在造型操作时不损坏,不变形,以及获得表面光洁、尺寸精确的铸件,模样必须要有足够的强度和刚度,一定的尺寸精度和表面光洁度。
除此之外,还应当使用方便,制造简单,成本低。
曲轴磨床体壳为大批量生产,所以用金属模样,该金属模样的材料选用如下:
模样:
铸铁,铸铁的强度高,耐磨性好,模样表面光滑,材料易得,价格便宜,加工性尚好。
通过对各种模样材料进行耐磨性的试验研究表明,无论从质量或尺寸变化上看以灰铸铁和球墨铸铁为最好。
因此,在大批大量生产的条件下,建议优先采用灰铸铁和球墨铸铁来制作模具。
选用HT200
出气针、气孔针:
45#钢
2.金属模样尺寸的确定
金属模样的尺寸直接影响到铸件的尺寸,因此正确地确定金属模样的尺寸极为重要。
金属模样的尺寸除了考虑产品零件的尺寸外,还要考虑零件的铸造工艺尺寸和零件材料的铸造收缩率。
零件尺寸从产品零件图上查得;零件的铸造工艺尺寸包括各种工艺参数,芯头尺寸和零件的铸造收缩率,这些可从铸造工艺图上查得。
由于机械加工用的是标准尺,因此凡是形成铸件的模样尺寸,一律要根据铸件尺寸依据铸造收缩率进行放大,才能作为标注在模样上的工作尺寸。
模样尺寸=铸件尺寸
(1+铸造线收缩率)
=(零件尺寸±铸造工艺尺寸)×(1+铸造线收缩率)
注:
“+”用于模样凸体部位的尺寸;“-”用于模样凹体部位的尺寸。
曲轴磨床体壳的线收缩率K=0.9%。
3.金属模样的结构
金属模样的结构在满足工艺要求,保证铸件质量的前提下,尽可能要便于加工制造。
金属模样一般多采用机械加工方法制造,对于形状复杂加工费工时的金属模样可用陶瓷型精密铸造直接铸出。
考虑金属模样加工方法时应尽量采用机床加工工艺,减少钳工的工作量,否则消耗工时太多,成本高。
为了使尺寸较大的空心模样具有较高的强度和高度,在模样内腔(非工作面)应设计加强筋,加强筋的数量、厚度和布置形式取决于模样的尺寸大小和形状。
对于平均轮廓尺寸小于150mm的模样可设计成不设加强筋的空心模样,对于尺寸较大或者较高的空心模样必须设置加强筋。
选择加强胫厚度为18mm,矩型排列。
4.金属模样的装配
根据模样尺寸的大小,结构特点及加工制造条件的不同,模样装配形式不同,常用的有平板式和嵌入式。
金属模样的装配,一般都利用模样形成的凸缘或凸耳,在没有现成的凸缘、凸耳或不够用时须在模样内侧专门设计凸耳,并设置定位销孔,紧固螺栓孔。
曲轴磨床体壳模样采用一个定位销直径20mm,一个导向销直径20mm。
5.金属模样的技术要求
模样的尺寸精度、表面光洁度是影响铸件质量的一个重要因素,因此对其
面光洁度和尺寸偏差应严格控制。
由《铸造工艺课程设计手册》查表6-29与表6-30得:
模样表面的粗糙度为3.2,模样与模板接触面的粗糙度为6.3。
二.模板
模板也称型板,是由模底板和模样、浇冒口系统及定位销等装配而成。
模底板用来连接与支承模样、浇冒系统、定位销等。
本设计采用单模底板,其工作面是平面。
1.模底板材料
对模底板材料的要求是有足够的强度,有良好的耐磨性,抗震耐压,铸造和加工性。
根据模样的结构及生产要求,选用灰铸铁作为模底板的材料。
模底板尺寸的确定
模底板长=砂箱长+2×砂箱分型面出边缘厚度
=950mm
模底板宽=砂箱宽+2×砂箱分型面出边缘厚度
=606mm
2.模底板高度
模底板高度必须根据使用情况和选用的造型机来确定。
普通平面式模底板高度H,铸铁的一般控制在80到150mm,这里H=80mm。
3.模底板定位销孔中心距
模底板定位销孔中心距是根据所配用的砂箱销套的中心距来确定的,一般制造时都用同一个钻模钻出。
当砂箱的销套中心距未定时,可由砂箱内廓尺寸A和箱耳尺寸中的M来决定。
模地板版定位销孔中心距常用C表示,C=A+2M=850mm。
三.芯盒
芯盒是制造砂芯的专用模具。
芯盒尺寸精度和结构合理与否,将在很大程度上影响砂芯的质量和造芯效率。
设计芯盒时应以铸造工艺图、生产批量以及造芯设备的条件为依据。
根据砂芯结构形状和尺寸,来确定芯盒的结构形式和尺寸。
四.砂箱
砂箱是砂型的成型和运输工具,不论生产性质如何,砂箱总是造型必须具备的工装。
砂箱的结构和尺寸合理与否,对铸件质量、生产效率、劳动强度有很大的影响。
砂箱的结构和尺寸必须满足下列要求:
1.砂箱的内框尺寸要保证模样和浇冒口与箱壁之间有合理的吃砂量;定位装置的公差配合应保证铸件的尺寸精度;箱壁与箱带的结构尺寸在保证砂箱强度和刚度的前提下,要有利于粘附型砂,并便于落砂时脱出铸件;箱壁不能阻碍排气,箱带不能与浇冒口位置相碰和阻碍铸件的收缩;在实砂和经受反复加热冷却条件下砂箱变形要小等等
2.要保证安全生产,砂箱的吊轴、吊环、手把和紧固装置要稳定可靠。
3.在满足工艺要求确保安全的前提下,还要制造方便,选材来源广,价格低廉,使用轻便。
4.砂箱规格要尽量标准化和系列化,以减少砂箱的品种规格,便于制造、选用、管理和降低成本。
参考文献:
1.铸造工艺学下册丁根宝主编机械工业出版社1985.6
2.机械设计课程设计手册吴学译罗圣国主编高等教育出版社1992.3
3.铸造成形手册黄天佑主编化学工业出版社2009.7
4.铸造工艺学李魅盛主编机械工业出版社2010.7