板带钢生产工艺及自动控制.docx
《板带钢生产工艺及自动控制.docx》由会员分享,可在线阅读,更多相关《板带钢生产工艺及自动控制.docx(88页珍藏版)》请在冰豆网上搜索。
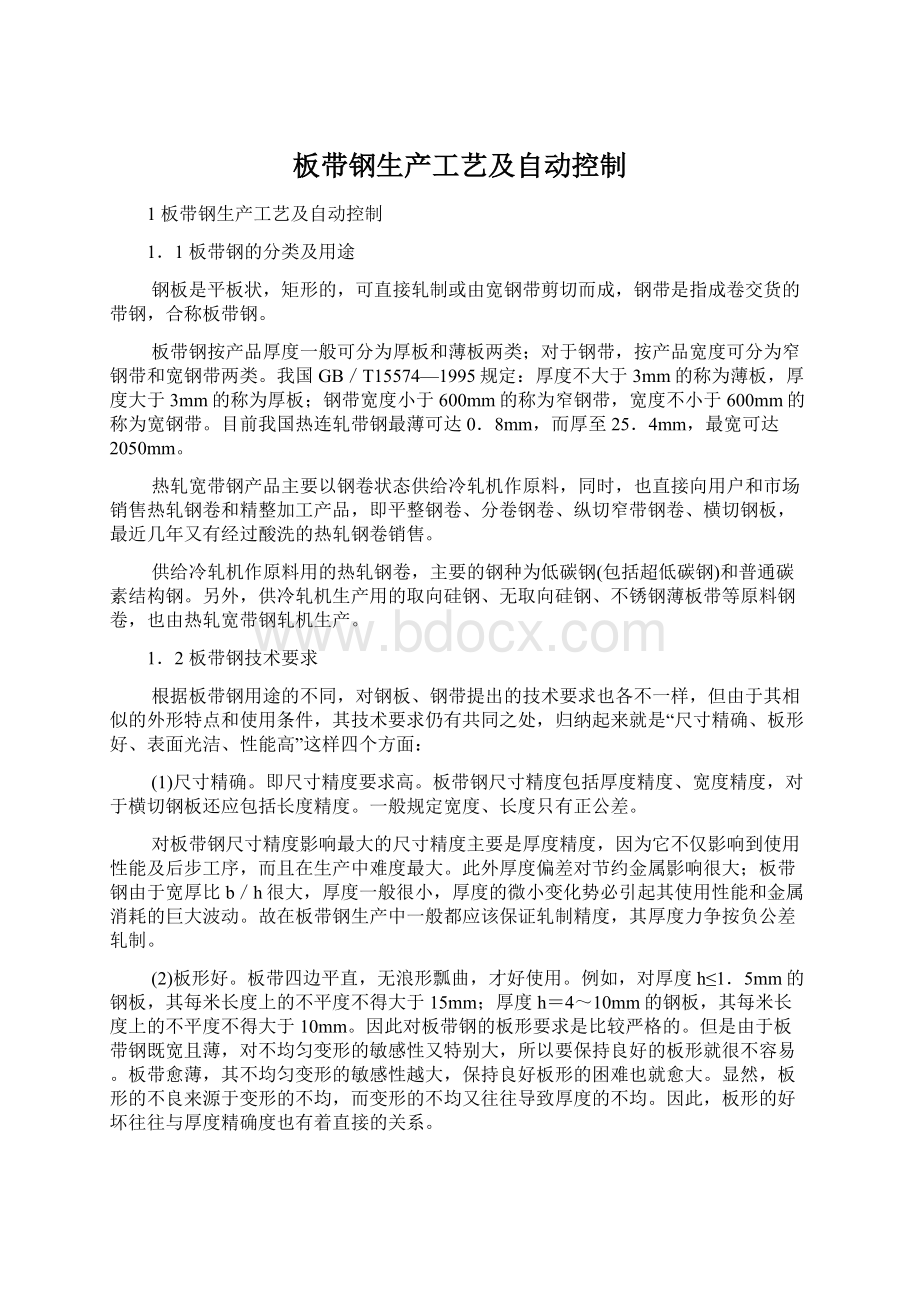
板带钢生产工艺及自动控制
1板带钢生产工艺及自动控制
1.1板带钢的分类及用途
钢板是平板状,矩形的,可直接轧制或由宽钢带剪切而成,钢带是指成卷交货的带钢,合称板带钢。
板带钢按产品厚度一般可分为厚板和薄板两类;对于钢带,按产品宽度可分为窄钢带和宽钢带两类。
我国GB/T15574—1995规定:
厚度不大于3mm的称为薄板,厚度大于3mm的称为厚板;钢带宽度小于600mm的称为窄钢带,宽度不小于600mm的称为宽钢带。
目前我国热连轧带钢最薄可达0.8mm,而厚至25.4mm,最宽可达2050mm。
热轧宽带钢产品主要以钢卷状态供给冷轧机作原料,同时,也直接向用户和市场销售热轧钢卷和精整加工产品,即平整钢卷、分卷钢卷、纵切窄带钢卷、横切钢板,最近几年又有经过酸洗的热轧钢卷销售。
供给冷轧机作原料用的热轧钢卷,主要的钢种为低碳钢(包括超低碳钢)和普通碳素结构钢。
另外,供冷轧机生产用的取向硅钢、无取向硅钢、不锈钢薄板带等原料钢卷,也由热轧宽带钢轧机生产。
1.2板带钢技术要求
根据板带钢用途的不同,对钢板、钢带提出的技术要求也各不一样,但由于其相似的外形特点和使用条件,其技术要求仍有共同之处,归纳起来就是“尺寸精确、板形好、表面光洁、性能高”这样四个方面:
(1)尺寸精确。
即尺寸精度要求高。
板带钢尺寸精度包括厚度精度、宽度精度,对于横切钢板还应包括长度精度。
一般规定宽度、长度只有正公差。
对板带钢尺寸精度影响最大的尺寸精度主要是厚度精度,因为它不仅影响到使用性能及后步工序,而且在生产中难度最大。
此外厚度偏差对节约金属影响很大;板带钢由于宽厚比b/h很大,厚度一般很小,厚度的微小变化势必引起其使用性能和金属消耗的巨大波动。
故在板带钢生产中一般都应该保证轧制精度,其厚度力争按负公差轧制。
(2)板形好。
板带四边平直,无浪形瓢曲,才好使用。
例如,对厚度h≤1.5mm的钢板,其每米长度上的不平度不得大于15mm;厚度h=4~10mm的钢板,其每米长度上的不平度不得大于10mm。
因此对板带钢的板形要求是比较严格的。
但是由于板带钢既宽且薄,对不均匀变形的敏感性又特别大,所以要保持良好的板形就很不容易。
板带愈薄,其不均匀变形的敏感性越大,保持良好板形的困难也就愈大。
显然,板形的不良来源于变形的不均,而变形的不均又往往导致厚度的不均。
因此,板形的好坏往往与厚度精确度也有着直接的关系。
(3)表面质量光洁。
板带钢是单位体积的表面积最大的一种钢材,又多用作外围构件,故必须保证表面的质量。
无论是厚板或薄板表面皆不得有气泡、结疤、拉裂、刮伤、折叠、裂缝、夹杂和压人氧化铁皮,因为这些缺陷不仅损害板制件的外观,而且往往败坏性能或成为产生破裂和锈蚀的策源地,成为应力集中的薄弱环节。
例如,硅钢片表面的氧化铁皮和表面的光洁度就直接影响磁性,深冲钢板表面的氧化铁皮会使冲压件表面粗糙甚至开裂,并使冲压工具迅速磨损,至于对不锈钢板等特殊用途的板带,还可提出特殊的技术要求。
(4)性能高。
板带钢的性能要求主要包括机械性能、工艺性能和某些钢板的特殊物理或化学性能。
一般结构钢板只要求具备较好的工艺性能,例如,冷弯和焊接性能等,而对机械性能的要求不很严格。
对于重要用途的结构钢板,则要求有较好的综合性能,即除了要有良好的工艺性能、强度和塑性以外,还要求保证一定的化学成分,保证良好的焊接性能、常温或低温的冲击韧性,或一定的冲压性能、—定的晶粒组织及各向组织的均匀性等等。
除了上述各种结构钢板以外,还有各种特殊用途的钢板,如高温合金板、不锈钢板、硅钢片、复合板等,它们或要求特殊的高温性能、低温性能、耐酸耐碱耐腐蚀性能,或要求一定的物理性能(如磁性)等。
1.3热连轧带钢生产工艺流程
图1—1为热带钢连轧机生产工艺流程图,概括了现代的热轧宽带钢轧机生产过程,是典型的工艺流程,不同之处仅在于有无定宽压力机,边部加热器等。
1.4带钢热连轧机自动化发展概况
1.4.1综述
带钢连轧机生产效率高,质量易于控制,轧制过程连续,易于实现机械化和自动化,而且这种轧机潜力大,只要稍加改善轧制工艺便可以大幅度地提高产量和改善产品质量,其经济效益非常显著。
所以各种先进的科技成果都竞相应用于连轧过程,大大促进了连轧过程自动化的发展,其中尤以热连轧轧机自动化的发展最为迅速和成熟,所以热连轧板带材轧机自动化的发展,可以反映整个轧制过程自动化的发展过程。
带钢热连轧机电气自动控制技术的发展,在20世纪大致经历了以下几个阶段:
50年代以前,即早期的带钢热连轧机,基本上没有自动控制,主要靠人工操作、断续控制(对电动机的启动、停止、加减速和正反转的控制)。
50年代中、后期,为手动操作加上单机自动控制系统(如主传动速度调节系统、压下机构辊缝调节系统、活套量控制系统、闭环模拟厚度控制系统等)。
60年代,进入到单机自动控制与计算机并存(1960年美国麦克劳思厂在带钢热连轧机的精轧机组上,首先采用计算机设定精轧机组的辊缝和速度;1961年美国钢铁公司大湖分公司投产的2032mm热带钢轧机,在精轧机上首先采用升速轧制技术;60年代末,英国实现了从加热炉到卷取机的整个带钢热连轧计算机控制)。
70年代,实现了全部计算机控制[主要采用直接数字控制和过程控制计算机对带钢的厚度和终轧温度、卷取温度进行控制,厚度自动控制采用电动压下(电动AGC),宽度只有预设定,没有板形控制]。
80年代,主要发展了板形控制和粗轧宽度自动控制,以及广泛采用液压厚度自动控制(液压AGC),使带钢的厚度、宽度、温度、板形等质量指标进一步提高;开发了直接热装和直接轧制技术,大大节省了能源。
控制的范围也从热轧生产线向两侧扩展,包括了对板坯库、钢卷库、成品库的控制和管理。
90年代,对热轧产品质量和节能要求进一步提高,热轧控制技术又有新的进展,如交叉辊(PC)轧机和在线磨辊(ORG)、连续可变凸度(CVC)控制板形技术、神经元网络技术等。
常规热带轧机设计产品厚度最薄到0.8~1.0mm,为此而设置了距精轧机50~60m的近距离卷取机,但是,在传统的热轧宽带钢轧机上轧制如此超薄的带钢没有取得稳定的发展。
1995~1996年,日本川崎钢铁公司千叶厂开发成功无头连续轧制宽带钢技术。
该技术解决了在常规热连轧机上生产厚度0.8~1.2mm超薄带钢的一系列技术难题。
无头连续轧制带钢技术,是在精轧机组前将两卷中间带坯头尾端切齐并由电感应加热器将头尾接合起来,进行连续轧制的技术。
在卷取机前由高速飞剪将带钢再切分开来,经地下卷取机卷成钢卷。
无头轧制采用动态变规格技术,一组带钢厚度是分步减薄的,穿带和最后一卷带钢为厚度稍厚的带钢,如厚度为1.26~1.66mm。
实现无头轧制的主要设备与技术为:
3个卷位的卷取箱、中间带坯切头尾飞剪和电感应接合装置、精轧机组高速高精度厚度变更技术、卷取机前高速切分飞剪及高速穿带装置。
新建的带钢热连轧机都配备了计算机控制系统,而且在对旧有轧机的改造工程中,最重要的一项内容就是采用计算机控制。
1959~1978年的20年间,我国热轧宽带钢轧机及生产技术处于低水平阶段。
已有的一套半连续式宽带钢轧机基本上是手动操作、人工设定的操作方式,轧机的主要生产工艺技术指标相当于第一代(20世纪40、50年代水平)热带轧机技术装备水平。
1978年12月投产的武汉钢铁公司1700mm热连轧机计算机系统,是我国引进的第一套带钢热连轧计算机控制系统,主要工艺技术指标超过了第二代(20世纪60年代水平)热带轧机。
1989年宝钢2050mm热连轧机的建成投产,使我国热轧宽带钢轧机的生产技术和技术装备又上了一个新的高度,达到了当代国际上最先进的现代化热轧宽带钢轧机水平。
该轧机的主要生产工艺技术指标属于第三代(1968年作为第三代开始)热带轧机水平,板坯热装技术、粗轧机宽度自动控制、精轧机液压AGC、板形控制技术(CVC系统)、全液压卷取机、完善的4级计算机自动化控制系统都处于世界一流水平。
20世纪90年代我国建成投产7套热轧宽带钢轧机,是我国热轧宽带钢轧机的高速发展时期。
其中有4套全新的热带轧机,即宝钢1580mm热轧机、鞍钢1780mm热轧机、珠钢1500mm及邯钢1900mm薄板坯连铸连轧机。
1580mm热轧机、1780mm热轧机采用和连铸机直接连接布置和生产一贯管理的连续生产线,紧凑型双机架可逆式粗轧机组、板坯定宽压力机、精轧机组板形控制双交叉辊(PC)轧机、精轧机全液压AGC系统、全液压卷取机、完善的4级计算机自动化控制和生产管理控制系统,这些都体现了20世纪90年代热带轧机最先进的技术装备水平和一流的产品质量控制水平。
珠钢于1999年8月建成中国第一套薄板坯连铸连轧生产线,邯钢于1999年12月建成第二套,包钢在2001年底建成第三套薄板坯连铸连轧生产线。
鞍钢、唐钢、马钢、涟钢薄板坯连铸连轧生产线亦相继投产,由于其流程短、规模适当、投资费用较低,所生产的热轧普通用途的带钢具有较好的市场竞争力。
薄板坯连铸连轧带钢生产工艺技术,是20世纪80年代钢铁工业生产具有突破性的重大技术进步。
薄板坯连铸连轧技术有德国西马克(SMS)的CSP、德马克(DEMAG)的ISP、日本住友的QSP、意大利达涅利(DANIELl)的FTSC和奥钢联(VAl)的CONROLL等共5种类型。
珠钢、邯钢、包钢、马钢、涟钢采用的是SMS公司研制开发的CSP技术及装备,鞍钢采用的是VAI的CONROLL铸机,唐钢采用的是DANIELI的FTSC铸机。
CSP生产线的连轧机组装有全液压AGC、CVC及弯辊板形控制技术,是生产高尺寸精度带钢的最先进的技术装备。
唐钢的薄板坯连铸连轧生产线是一套超薄带钢连铸连轧生产线,最小厚度亦可以达到0.8mm。
薄板坯在很高的温度下进入轧制线,经过很长的辊底式均热炉,采用半无头轧制工艺轧制厚0.8~4.0mm、宽850—1680mm的薄带钢卷,单位宽度卷重为18kg/mm。
该生产线与CSP技术所不同的是板坯厚度为90/70mm,采用2架不可逆式粗轧机和5架精轧机,末架最高出口速度为23.2m/s。
这是当今生产热轧宽而薄的带钢最前沿的现代化技术,国外第一套同类型设备是2000年初投入热试生产的。
1993年11月,武汉钢铁公司、重庆钢铁设计研究院、北京科技大学合作完成了武钢1700mm热连轧计算机系统的更新改造工程。
随后,在1995年5月,武汉钢铁公司、北京科技大学等单位又共同完成了太原钢铁公司1549mm热连轧计算机系统的建立和开发。
2001年,鞍山钢铁公司和北京科技大学(高效轧制国家工程研究中心)共同在鞍钢1700mm半连轧翻新改造项目中,完成了自行设计的三级计算机控制系统,其厚度、板形各项控制功能均达到了较先进的水平。
武钢和太钢带钢热连轧计算机控制全部应用软件立足国内,以及鞍钢带钢热连轧计算机控制“系统及应用软件”全部立足国内的成功,标志着我国已经有能力依靠自己的力量设计和开发像热连轧这样控制过程极为复杂、要求快速响应的计算机控制系统及其支持软件和应用软件。
1.4.2带钢热轧计算机控制功能
带钢热轧生产是目前应用计算机控制最为成熟的一个领域,其控制范围包含了整个生产过程,从加热炉人口,甚至从连铸出口开始到成品库,包括了轧制计划,板坯库管理,数学模型,设备控制和质量控制以及传动(电气及液压传动)数字控制等各个层次,是轧钢自动化领域中最为庞大,最为复杂的控制系统。
1.4.2.1基础自动化控制功能
基础自动化面向机组,面向设备及设备的机构。
随着电气传动的数字化以及液压传动的广泛应用,数字传动已逐步与基础自动化成为一个整体。
基础自动化控制功能按性质可分为轧件跟踪及运送控制:
顺序控制和逻辑控制;设备控制及质量控制。
A轧件跟踪及运送控制
轧件(钢坯、带坯、带钢)的运送是生产工艺所要求的基本功能之一,其基本任务是控制各区段辊道速度及其转停,使轧件以最快速度从加热炉人口运送到加热炉、粗轧、精轧、卷取,并在各区进行加工处理后由运输链运出,但在保证最快速度运送的同时还要保证自动轧钢时前后轧件不相碰撞,维持一定的节奏。
为了能根据工艺要求对生产线上多根轧件(从加热炉出口到运输链最多可有7~8根轧件)进行运送及顺序控制,基础自动化各控制器需要知道每一个轧件在轧线上的位置及其位置的变化,因此轧件跟踪实质上是协调各程序并获取“事件”的重要程序。
轧件跟踪将在基础自动化、过程自动化及生产控制级中分别进行,但各级的要求不同,并都以基础自动化的位置跟踪结果为依据。
基础自动化的跟踪实质上是对生产线各轧件的位置及其变化进行跟踪,并为顺序控制提供“事件发生”信号(热金属检测器由OFF变为ON或由ON变为OFF都称作为一个事件)。
基础自动化的位置跟踪结果将上送过程自动化。
过程自动化的跟踪实质上是对各轧件的数据进行跟踪以使数据和轧件能对上号,能正确地设定计算和自学习,同时亦利用一些“事件”来启动某些程序的投入。
生产控制级的跟踪将用于质量控制及报表打印。
B顺序控制和逻辑控制
逻辑控制是生产过程自动化的基本内容之一。
实际上基础自动化所有控制功能都含有一定的逻辑功能,包括功能的联锁,功能执行或停止的逻辑条件等,因此每一个功能都将存在逻辑部分和控制部分两个部分,除此之外,根据工艺需要将设置一些只包括逻辑部分的顺序控制功能,主要是炉区及粗轧区辊道的运转(自动加速、稳速、减速以及反转)的顺序控制。
C设备控制
设备控制包括设备的位置控制和速度控制,包括轧机辊缝定位、侧导板定位、窜辊位置控制、推钢机行程控制、主传动速度控制等,还包括弯辊装置的恒压力控制。
全生产线有上百个设备控制回路,因此可以说设备控制是最基本的控制功能。
设备控制接受过程自动化级数学模型计算所得的各项设定值(辊缝、速度、弯辊力等),对各执行机构进行位置和速度整定,在半自动状态下则接受操作人员通过人—机界面输人的设定值并进行位置和速度整定。
随着电气及液压传动的数字化,设备控制将逐步由数字传动控制承担。
D质量控制
对带钢热连轧来说质量控制包括:
厚度控制,终轧温度控制,卷取温度控制(包括冷却速度控制),宽度控制,板形控制,表面质量控制。
过程自动化设定模型的主要任务是对各执行机构的位置、速度进行设定以保证带钢头部的厚度、温度、板形质量,而质量控制功能则用于保证带钢全长的厚度、温度、板形等精度。
1.4.2.2过程自动化控制功能
过程自动化面向整个生产线,其中心任务是对生产线上各机组和各个设备进行设定计算,为此其核心功能为对粗轧、精轧机组负荷进行分配(包括最优化计算)及数学模型的预(报)估,为了实现此核心功能,过程控制计算机必须设有板坯(数据)跟踪、初始数据输入、在线数据采集以及模型自学习等为设定模型服务及配套的功能。
热连轧过程自动化控制的主要功能是精轧机组的厚度设定数学模型和板形设定数学模型,设定值计算后下送基础自动化,由设备控制功能执行。
1.4.2.3生产控制级功能
生产控制级主要完成生产计划的调整和发行,生产实绩的收集、处理和上传给生产管理级,对板坯库、钢卷库、成品库进行管理,以及进行产品质量控制等任务。
1.4.2.4生产管理级
生产管理级主要完成合同管理、生产计划编制、各生产线的相互协调、按合同申请材料,将作业计划下发给生产控制级,并收集生产控制级的生产实绩,跟踪生产情况和质量情况,组织成品出厂发货,以及财务管理等任务。
为了更好说明过程自动化与基础自动化各功能间的关系,以及各相关功能间的关系,图1—2给出了带钢热连轧计算机控制主要功能总框图。
1.4.3我国热轧带钢计算机控制系统
我国的钢铁企业,除宝钢等一批新建的厂子外,装缶都比较落后,计算机控制和管理水平较低。
为适应市场发展的需要,各钢铁公司在近十几年来都特别注重自动化方面的改造和新建工作,以期用最少的投入,获得最大的经济效益。
从目前国内的热轧宽带钢厂来看,基本上都建立了基础自动化系统和过程控制计算机系统。
宝钢1580、2050,珠钢1500,鞍钢1780等少数热轧带钢厂还设有生产控制计算机系统,但仅宝钢才有生产管理计算机系统,实现了从接受用户订货开始,到产品出厂为止的全过程计算机管理和控制。
现在国内许多钢铁公司都在按自己的生产设备情况和管理特点,逐步建立自己的计算机系统。
1.5计算机对轧制过程控制的基本内容
1.5.13/4连续式热连轧机设备布置
某1700mm3/4连续式带钢热连轧机轧制线设备布置如图1—3所示,主要设备有步进式加热炉、粗轧机组、精轧机组,层流冷却装置和卷取机组、精整作业线等。
将厚度为150~250mm的板坯,经粗轧和精轧机组轧成厚度为1.2~12.7mm的带钢卷,其中一部分可以作为成品出厂,另一部分可以供冷轧厂和硅钢厂作为再次加工的坯料。
在计算机控制下的生产流程与人工操作时基本相同,但操作人员的操作方式和操作内容发生了变化,更多的是通过人机界面(显示器和键盘等)来了解实际的轧制情况和进行某些辅助的操作和必要的干预。
因此,操作人员应该深入了解各个设备的计算机控制系统是如何工作的以及计算机之间是如何通信的。
带钢热连轧生产线进行自动化轧钢时,板坯和轧制计划的原始数据由生产控制级计算机下传给过程控制级计算机,板坯原始数据包括钢种、化学成分、板坯厚度、板坏宽度、板坯长度、板坯重量、板坯在库中的位置及钢卷厚度、宽度等,如果没有生产控制级计算机,通过初始数据输入(PDA)终端直接输入到过程控制级计算机中。
1.5.2加热区的自动化过程
根据轧制计划表中所规定的顺序,某块板坯由起重机吊到上料A辊道上后,就处于过程控
制级计算机的跟踪之下。
板坯在A辊道上,受到冷金属检测器的跟踪,并由冷金属检测器控制辊道的运转和控制板坯在辊道上的位置。
为了避免计算机误动作,上料时不论是长板坯还是短板坯,一组辊道上只能放—块板坯,不能跨组放,也不能在同一组辊道上放两块板坯。
板坯上了A辊道后,要测量长度和重量,测量装置自动完成测量后,把实测数据传给计算机,计算机对数据进行检查,发现异常时输出报警信息,请求操作人员进行相应处理。
计算机把PDA中的板坯号和由操作人员通过人机接口MMI装置输入的标在实际板坯上的号码比较,进行板坯确认或叫板坯识别。
如果发现异常,要进行重新排序、做“缺号处理”或将板坯吊销。
对已经测量和确认过的板坯按照规定的炉号、炉列进行板坯移动和炉前定位控制,控制板坯在炉前对中停止,这由B辊道自动位置控制系统APC程序完成。
板坯要推人加热炉时,计算机确定推钢机的移动行程,并且对这一设定计算值进行合理性检查,在满足装钢条件时,通过APC程序控制推钢机把板坯装入加热炉内预定位置。
板坯在炉内移动的位置用冷金属检测器3l、32、33作为跟踪的起始点。
板坯在加热炉中由步进梁一步一步的将它移向出料端,步进梁正常向前一步的行程为600mm。
为了防止炉内最前面的板坯越位而碰到出料炉门上,甚至掉下去,所以在距出料端墙1450mm处的侧墙上设有γ射线检测器,用来控制步进梁停止前进。
为了保证抽出机的正常操作,当γ射线检测器出故障时,步进梁可由计算机控制其停止前进。
步进梁进行上升、前进、下降、后退的反复循环动作,以及当出钢时间大于规定时间,步进梁进行上升、下降的踏步动作,均由计算机控制。
加热炉的燃烧控制,由计算机进行设定和计算,而用相应的温度和流量调节器来执行其控制功能。
计算机根据轧件的尺寸和轧件的“运动方程”预测轧件在粗轧区、精轧区、卷取区的运行时间,并根据轧线上的生产状况和加热炉烧钢状况,决定板坯从加热炉抽出的时间,进行轧制节奏(MillPacing)控制,除了全自动抽钢方式外,还有定时抽钢和强制抽钢方式。
当有抽钢请求时,计算机首先检查抽钢的各种条件是否满足,然后进行抽钢机行程设定值计算,并通过APC程序控制抽钢机前进和后退,把加热好的板坯放在出炉辊道中心线上根据前进方向是否有钢坯来决定出炉辊道的速度,移动板坯进入粗轧区。
1.5.3粗轧区的自动化过程
从加热炉的出炉辊道到卷取机的整个轧制线上,为适应工艺过程自动化的要求,在相应的设备处均设置有热金属检测器,用来跟踪轧件,以便计算机根据热金属检测器检测出板坯、带坯或带钢的位置,对轧制线上的相应设备进行设定和控制。
当下一块板坯将被抽出时,过程控制计算机通过数学模型进行粗轧机组各设定值计算,如水平轧机各机架各道次的压下位置即轧前辊缝、立辊轧机各机架各道次的开口度、侧导板位置、水平轧机各架的咬人速度、轧制速度、抛钢速度、立辊轧机速度、前后辊道速度、除鳞方式、测量仪表基准值、压下补偿值等,对粗轧机组设定计算有两次,时间分别是从加热炉抽钢时和板坯到达粗轧机入口时,第二次比第一次精确。
基础自动化级各计算机接受这些设定值后,通过各自的自动位置控制系统APC程序和各自的速度控制系统,在规定的时间内把水平轧机卜工作辊位置、轧辊速度、立辊轧机开口度、侧导板位置等正常轧制工艺要求的各个设定项目实际值调整到与设定值允许的偏差范围内。
出炉后的板坯通过热金属检测器来控制辊道的运转,将板坯送人到大立辊(VSB)中,大立辊给予板坯一定的侧压/量,一方面是减缩板坯的宽度;另·方面是用于破碎附在板坯表面上的炉生氧化铁皮,在大立辊之后设有高压水喷嘴,用来破除板坯表面上的氧化铁皮。
为了进一步提高板坯表面质量,在板坯进入二辊不可逆式轧机R1之前,再用高压水喷除氧化铁皮。
轧件在Rl轧机上仅轧制一道次,然后立即自动地将轧件送往四辊可逆式轧机R2中继续进行轧制,根据钢种和压下规程的不同,在R2轧机上轧制3~5或7道次,有的也可轧制9道次。
由于R2可逆式轧制道次有可以选择的余地,为了适应轧制多品种规格轧件,在操作台上设计有半自动设定。
所谓半自动设定就是由操作人员利用人机接口来设定R2轧机各道次的工艺参数,并将所设定的信号输出给基础自动化控制器,由它来执行控制。
R2轧机进行往复轧制时,在奇数道次的情况下,入口侧导板将轧件对中,小立辊Ez对轧件给予侧压下,轧件进入R2之前要用高压水进一步除鳞,而在偶数道次情况下,R2后面的侧导板将轧件移正,此时R2前面的侧导板(即入口侧导板)打开,小立辊E2不给予侧压下。
R2轧机正反转和高压水喷嘴的给定,由人口侧和出口侧的热金属检测器34和40发出信号进行控制。
由于R2轧机前后工作环境条件差,有水雾干扰,为了保证此热金属检测器34和40能可靠地工作,而采用了γ射线检测器。
轧件继续进入R3和风四辊不可逆式轧机中进行双机连轧。
凡轧机采用交流同步机传动,而R3轧机是采用直流电动机传动,其速度是可变的。
凡轧机的速度设定是根据R4轧机的速度和金属秒流量相等的关系进行计算,考虑到轧制过程中被轧金属性能和工艺参数的变化,为了保证双机连轧过程能稳定地进行,R3与R4轧机之间的带钢采用无张力控制。
在R3和R4轧机的入口侧均设有高压水除鳞喷嘴,根据成品规格的不同来确定是否喷水,一般来说,厚度大于2.5mm的成品带钢,当轧件在R3和R4中轧制时,均采用高压水进一步除鳞。
在R4轧机出口侧的中间辊道上,设置有γ射线测厚仪、光电测宽仪和光学高温计RT4。
实测出来的厚度、宽度和温度值输送给计算机,用来作为设定精轧机穿带时的温降计算、设定各机架的出口厚度,以及粗轧机组进行宽度控制用。
概括起来,粗轧区的自动化对象和内容如下:
(1)粗轧机组各设备的基本设定项目。
Rl、R3和R4轧机的压下位置;R2轧机的轧制道次及其各道次的压下位置;大立辊(VSB)和小立辊E3和E4的开口度,以及Ez小立辊机架奇数道次的开口度VSB,R1、R4的入口侧导板的位置,以及R2轧机前后侧导板的位置;R2轧机咬钢和抛钢的速度,Rl、R2,和R4轧机的轧制速度,R2轧机的轧制时间和反转时间的设定;R2轧机前后侧以及R3和R4轧机入口侧高压水除鳞喷嘴的设定;粗轧机组出口侧测厚仪、测宽仪和测温仪的整定以及其他等。
(2)带坯宽度的控制。
根据在精轧机组出口