利用Ansys对Eicher1110底盘车架进行分析与验证外文文献翻译中英文翻译外文翻译.docx
《利用Ansys对Eicher1110底盘车架进行分析与验证外文文献翻译中英文翻译外文翻译.docx》由会员分享,可在线阅读,更多相关《利用Ansys对Eicher1110底盘车架进行分析与验证外文文献翻译中英文翻译外文翻译.docx(18页珍藏版)》请在冰豆网上搜索。
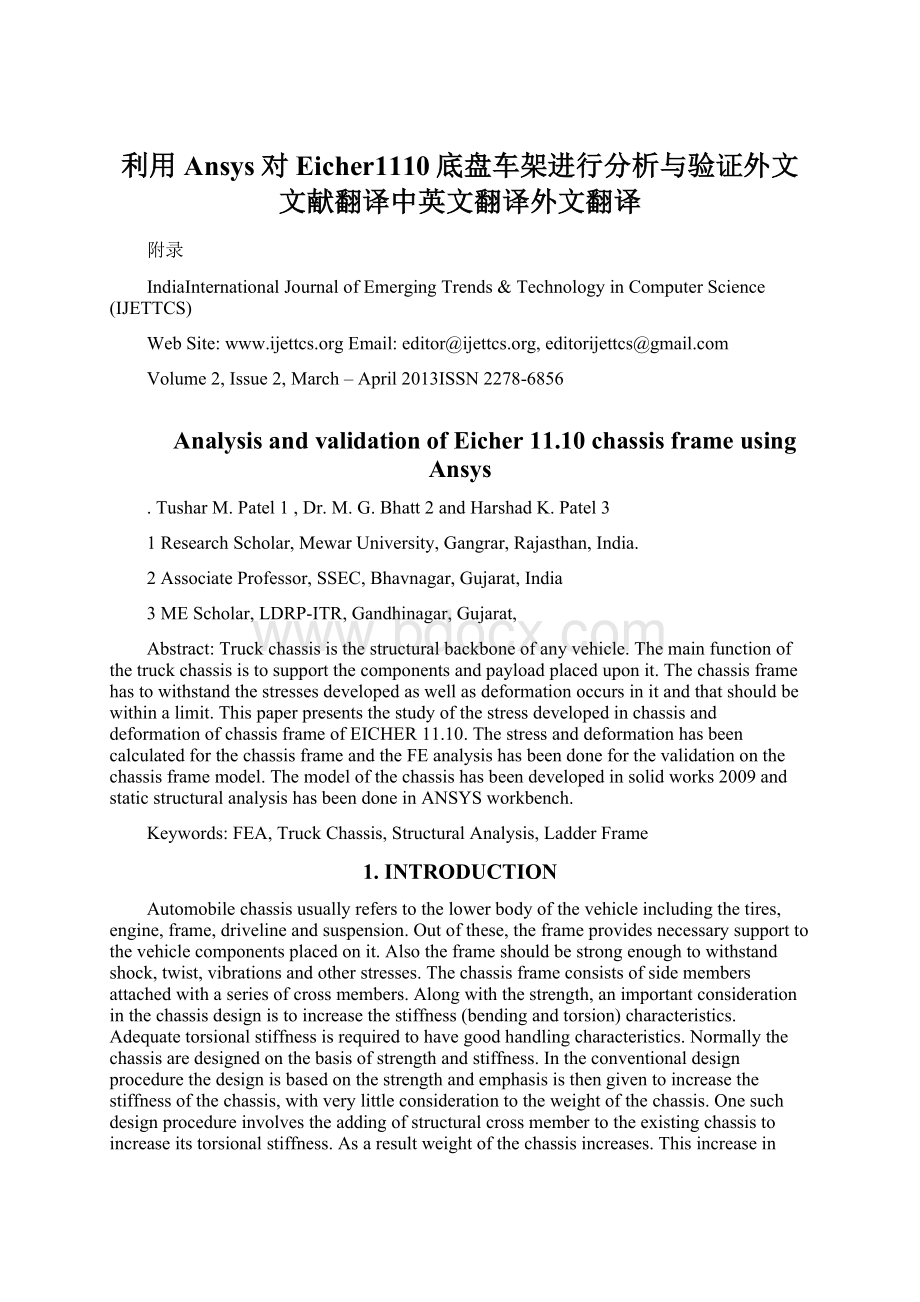
利用Ansys对Eicher1110底盘车架进行分析与验证外文文献翻译中英文翻译外文翻译
附录
IndiaInternationalJournalofEmergingTrends&TechnologyinComputerScience(IJETTCS)
WebSite:
www.ijettcs.orgEmail:
editor@ijettcs.org,editorijettcs@
Volume2,Issue2,March–April2013ISSN2278-6856
AnalysisandvalidationofEicher11.10chassisframeusingAnsys
.TusharM.Patel1,Dr.M.G.Bhatt2andHarshadK.Patel3
1ResearchScholar,MewarUniversity,Gangrar,Rajasthan,India.
2AssociateProfessor,SSEC,Bhavnagar,Gujarat,India
3MEScholar,LDRP-ITR,Gandhinagar,Gujarat,
Abstract:
Truckchassisisthestructuralbackboneofanyvehicle.Themainfunctionofthetruckchassisistosupportthecomponentsandpayloadplaceduponit.Thechassisframehastowithstandthestressesdevelopedaswellasdeformationoccursinitandthatshouldbewithinalimit.ThispaperpresentsthestudyofthestressdevelopedinchassisanddeformationofchassisframeofEICHER11.10.ThestressanddeformationhasbeencalculatedforthechassisframeandtheFEanalysishasbeendoneforthevalidationonthechassisframemodel.Themodelofthechassishasbeendevelopedinsolidworks2009andstaticstructuralanalysishasbeendoneinANSYSworkbench.
Keywords:
FEA,TruckChassis,StructuralAnalysis,LadderFrame
1.INTRODUCTION
Automobilechassisusuallyreferstothelowerbodyofthevehicleincludingthetires,engine,frame,drivelineandsuspension.Outofthese,theframeprovidesnecessarysupporttothevehiclecomponentsplacedonit.Alsotheframeshouldbestrongenoughtowithstandshock,twist,vibrationsandotherstresses.Thechassisframeconsistsofsidemembersattachedwithaseriesofcrossmembers.Alongwiththestrength,animportantconsiderationinthechassisdesignistoincreasethestiffness(bendingandtorsion)characteristics.Adequatetorsionalstiffnessisrequiredtohavegoodhandlingcharacteristics.Normallythechassisaredesignedonthebasisofstrengthandstiffness.Intheconventionaldesignprocedurethedesignisbasedonthestrengthandemphasisisthengiventoincreasethestiffnessofthechassis,withverylittleconsiderationtotheweightofthechassis.Onesuchdesignprocedureinvolvestheaddingofstructuralcrossmembertotheexistingchassistoincreaseitstorsionalstiffness.Asaresultweightofthechassisincreases.Thisincreaseinweightreducesthefuelefficiencyandincreasesthecostduetoextramaterial.Thedesignofthechassiswithadequatestiffnessandstrengthisnecessary.
2、LITERATUREREVIEW
Manyresearchershadconductedanalysisonchassisofvariousheavyvehicles.Thedynamiccharacteristicsoftruckchassissuchasthenaturalfrequencyandmodeshapeweredeterminedusingfiniteelementmethod.ExperimentalmodalanalysiswascarriedouttovalidatetheFEmodels[2].VijayPateletal.performedthestaticstructuralanalysisofthetruckchassis.Structuralsystemsofthechassiscanbeeasilyanalyzedusingthefiniteelementtechniques.Soaproperfiniteelementmodelofthechassishasbeendeveloped.ThechassiswasmodeledinPRO-E.FEAwasdoneonthemodeledchassisusingtheANSYSWorkbench.Thehigheststressproducewas106.08MPabyFEanalysis.Thecalculatedmaximumshearstresswas95.43Mpa.TheresultofFEanalysiswas10%biggerthantheresultofanalyticalcalculation.Themaximumdisplacementofnumericalsimulationresultwas3.0294mm.Theresultofnumericalsimulationwas5.92%biggerthantheresultofanalyticalcalculationwhichis2.85mm.Thedifferencewascausedbysimplificationofmodelanduncertaintiesofnumericalcalculation[3].AbdRahmanetal.investigatedstressanalysisonaheavy-dutytruckchassisusingfiniteelementmethod.Finiteelementresulthadshownthatthecriticalpointofstressoccursatopeningofchassiswhichwasincontacttothebolt.Thusitwasimportanttoreducestressmagnitudeatthespecificlocation.PreviousFEAagreewiththemaximumdeflectionofsimplebeamloadedbyuniformlydistributedforce[4].Ebrahimietal.constructedahaytrailermodelanditscomponentsanalysiswascarriedout[5].Saneetal.performedstressanalysisonalightcommercialvehiclechassisusingiterativeprocedureforreductionofstresslevelatcriticallocations[6].Koszalkaetal.accomplishedstressanalysisonaframeofsemilowloaderusingFEM.Twoversionsofframedesignwereanalyzed,focusingonthepartofbeamwherethehigheststresseswerelocated[7].
3、FINITEELEMENTANALYSIS
3.1、BasicConceptofFEM
Thefiniteelementmethod(FEM)isacomputationaltechniqueusedtoobtainapproximatesolutionsofboundaryvalueproblemsinengineering.Simplystated,aboundaryvalueproblemisamathematicalprobleminwhichoneormoredependentvariablesmustsatisfyadifferentialequationeverywherewithinaknowndomainofindependentvariablesandsatisfyspecificconditionsontheboundaryofthedomain.
AnunsophisticateddescriptionoftheFEmethodisthatitinvolvescuttingastructureintoseveralelements(piecesofstructure),describingthebehaviorofeachelementinasimpleway,thenreconnectingelementsatnodesasifnodeswerepinsordropsofgluethatholdelementstogether(Figure1).Thisprocessresultsinasetofsimultaneousalgebraicequations.Instressanalysistheseequationareequilibriumequationsofthenodes.Theremaybeseveralhundredorseveralthousandsuchequations,whichmeanthatcomputerimplementationismandatory.
Figure1:
Discretizationofmodel[4]
3.2、AGeneralProcedureforFEA。
Therearethreemainsteps,namely:
preprocessing,solutionandpostprocessing.Inpreprocessing(modeldefinition)includes:
definethegeometricdomainoftheproblem,theelementtype(s)tobeused,thematerialpropertiesoftheelements,thegeometricpropertiesoftheelements(length,area,andthelike),theelementconnectivity(meshthemodel),thephysicalconstraints(boundaryconditions)andtheloadings.
Insolutionincludes:
thegoverningalgebraicequationsinmatrixformandcomputestheunknownvaluesoftheprimaryfieldvariable(s)areassembled.Thecomputedresultsarethenusedbybacksubstitutiontodetermineadditional,derivedvariables,suchasreactionforces,elementstressesandheatflow.Actuallythefeaturesinthisstepsuchasmatrixmanipulation,numericalintegrationandequationsolvingarecarriedoutautomaticallybycommercialsoftware.
Inpostprocessing,theanalysisandevaluationoftheresultisconductedinthisstep.Examplesofoperationsthatcanbeaccomplishedincludesortelementstressesinorderofmagnitude,checkequilibrium,calculatefactorsofsafety,plotdeformedstructuralshape,animatedynamicmodelbehaviorandproducecolor-codedtemperatureplots.Thelargesoftwarehasapreprocessor
andpostprocessortoaccompanytheanalysisportionandthebothprocessorcancommunicatewiththeotherlargeprograms.Specificproceduresofpreandpostaredifferentdependentupontheprogram。
4、MODELINGOFEXISTINGCHASSISFRAME
.Themodelofexistingchassisasperthedimensioniscreatedinsolidworks2009asshownonFigure2.ThemodelisthensavedinIGESformatwhichcanbedirectlyimportedintoANSYSworkbench.Figure3showstheimportedmodelinANSYSworkbench.
.
Figure2:
CADmodelofchassisinsolidworks2009
Figure3:
GeometryofchassisframeinAnsys
4.1.MaterialofModel
Fortheframegeometryofchassisgenerallysteelanditsalloysareused.Fortheframemodels,varietyofmaterials,compositematerialsanddifferentkindofalloyscanbeused.Inthepresentstudy,ST52isusedanditspropertiesareasgivenbelow.
Table1:
Materialpropertiesofchassis[1]
MaterialST52
ModulusofElasticityE2x105N/mm2
PossionRatio0.3
TensileStrength520N/mm2
YieldStrength360N/mm2
4.2.ConnectionType
Theconnectiontypebetweenthesidebars,bracketandcrossbarcanbewelded,rivetedoritcanbebolted.NormallyrivetedjointisusedsoheretherivetedconnectionisdefinedinmodelingasshowninFigure4.2
Figure4:
Connectiontypeofchassisframe
4.3MeshingofChassisFrame
Themeshingisdoneonthemodelwith85466No.Ofnodesand38369No.ofTetrahedralelements.Figures5and6showtetrahedralelementandmeshingofmodel。
Figure5:
Tennodetetrahedralelement
Figure6:
Meshingofchassisframe
4.4.LoadingConditionofChassisFrame
Thetruckchassismodelisloadedbystaticforcesfromthetruckbodyandload.Forthismodel,themaximumloadedweightoftruckandbodyis10,000kg.Theloadisassumedasauniformdistributedobtainedfromthemaximumloadedweightdividedbythetotallengthofchassisframe.DetailloadingofmodelisshowninFigure7and8.Themagnitudeofforceontheuppersideofchassisis117720Nwhichiscarriedbytwosidebarssoloadononesidebaris58860N.
Figure7:
Loadonfirstsidebarofchassisframe
Figure8:
Loadonsecondsidebarofchassisframe
5、RESULTOFANALYSIS
Figure9:
Flowchartforvalidation
Theanalysisdoneonthechassismodelgivesthemaximumgeneratedshearstressvalue100.13KN(figure11).Basedonstaticsafetyfactortheory,themagnitudeofsafetyfactorforthisstructureis1.43[4].Theformulaofdesignstressisdefinedby[1]
DesignStress=YieldStress/FactorofSafety
J.P.Vidosicrecommendssomevalueofsafetyfactorforvariousconditionofloadingandmaterialofstructures.Thevalueof1.5to2forwellknownmaterialsunderreasonablyenvironmentalcondition,subjectedtoloadsandstressesthatcanbedeterminedreadily.Basedonthisresult,itisnecessarytoreducethestressmagnitudeofcriticalpointinordertogetthesatisfySFvalueoftruckchassis.Thetruckcha