年产3万吨甲醇工艺设计毕业设计.docx
《年产3万吨甲醇工艺设计毕业设计.docx》由会员分享,可在线阅读,更多相关《年产3万吨甲醇工艺设计毕业设计.docx(29页珍藏版)》请在冰豆网上搜索。
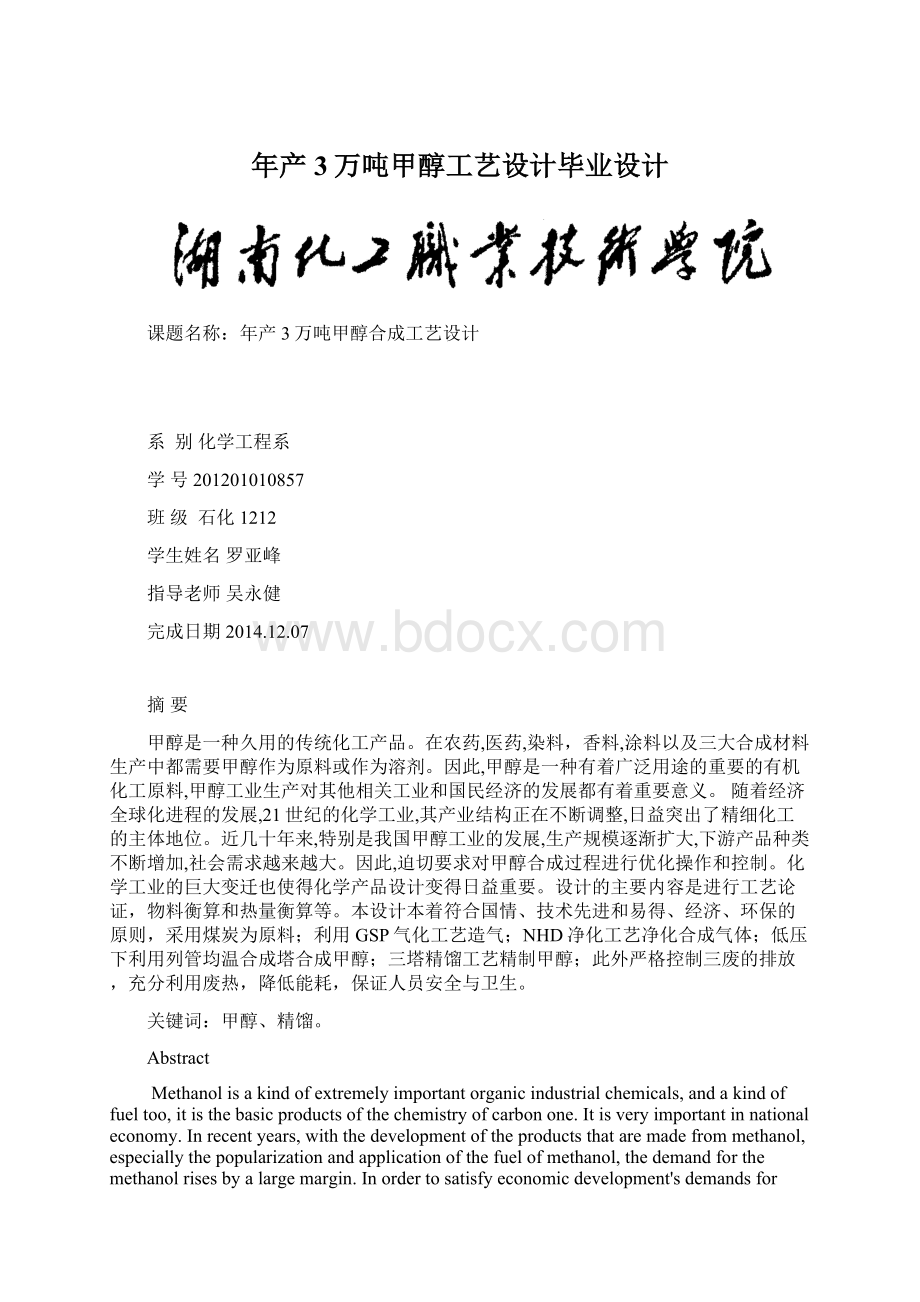
年产3万吨甲醇工艺设计毕业设计
课题名称:
年产3万吨甲醇合成工艺设计
系别化学工程系
学号201201010857
班级石化1212
学生姓名罗亚峰
指导老师吴永健
完成日期2014.12.07
摘要
甲醇是一种久用的传统化工产品。
在农药,医药,染料,香料,涂料以及三大合成材料生产中都需要甲醇作为原料或作为溶剂。
因此,甲醇是一种有着广泛用途的重要的有机化工原料,甲醇工业生产对其他相关工业和国民经济的发展都有着重要意义。
随着经济全球化进程的发展,21世纪的化学工业,其产业结构正在不断调整,日益突出了精细化工的主体地位。
近几十年来,特别是我国甲醇工业的发展,生产规模逐渐扩大,下游产品种类不断增加,社会需求越来越大。
因此,迫切要求对甲醇合成过程进行优化操作和控制。
化学工业的巨大变迁也使得化学产品设计变得日益重要。
设计的主要内容是进行工艺论证,物料衡算和热量衡算等。
本设计本着符合国情、技术先进和易得、经济、环保的原则,采用煤炭为原料;利用GSP气化工艺造气;NHD净化工艺净化合成气体;低压下利用列管均温合成塔合成甲醇;三塔精馏工艺精制甲醇;此外严格控制三废的排放,充分利用废热,降低能耗,保证人员安全与卫生。
关键词:
甲醇、精馏。
Abstract
Methanolisakindofextremelyimportantorganicindustrialchemicals,andakindoffueltoo,itisthebasicproductsofthechemistryofcarbonone.Itisveryimportantinnationaleconomy.Inrecentyears,withthedevelopmentoftheproductsthataremadefrommethanol,especiallythepopularizationandapplicationofthefuelofmethanol,thedemandforthemethanolrisesbyalargemargin.Inordertosatisfyeconomicdevelopment'sdemandsformethanol,havelaunchedthemethanolprojectofthis30,000t/a.Maincontentthatdesigntocarryoncraftprove,suppliesweighingapparatusregardaswithheatweighingapparatuschargingetcTheprincipleofthedesigninlinewithaccordingwiththenationalconditions,technologicallyadvancedandapt,economy,protectingenvironment,.Coalsisadoptedasrawmaterials;thecraftofGSPgasificationisutilizedtomakewatergas;thecraftofNHDpurificationisutilizedtopurifythesyngas;tubularaverage-temperaturereactionisutilizedtosynthesizemethanolkeepinginlowpressure;therectificationcraftofthreetowersisutilizedtorectifymethanol;Inadditioncontrolthedischargeofthethreewastesstrictly,fullyutilizeusedheat,reduceenergyconsumption,guaranteethepersonalsecurityandhygiene.
Keyword:
Methanol,synthesis.
一、甲醇的国内外发展简况及市场用途…………………………………………6
1、生产得发展………………………………………………………………6
2、生产技术得发展…………………………………………………………7
3、甲醇的用途………………………………………………………………7
二、甲醇合成的主要方法…………………………………………………………8
三、甲醇合成的生产原理及影响因素……………………………………………9
1、合成系统中的反应…………………………………………………………9
2、甲醇合成生产得影响因素…………………………………………………9
2.1温度的影响………………………………………………………………9
2.2压力的影响…………………………………………………………………9
2.3原料配比的影响………………………………………………………10
2.4催化剂颗粒尺寸的影响…………………………………………………10
2.5空速的影响………………………………………………………………10
2.6反应器结构的影响………………………………………………………11
四、设计依据…………………………………………………………………12
五、工艺流程说明……………………………………………………………13
六、生产工艺设计……………………………………………………………13
1、物料衡算…………………………………………………………………13
1.1新鲜气、驰放气摩尔流量…………………………………………………14
1.2循环比的计算……………………………………………………………16
1.3转化率得计算……………………………………………………………17
2、热量衡算………………………………………………………………17
2.1入塔气与出塔气的热交换过程热量衡算……………………………18
2.2合成器冷却器得热量衡………………………………………………24
3、设备选型与计算……………………………………………………………27
3.1催化剂用量………………………………………………………………27
3.2冷却冷凝器的设备计算与选型…………………………………………27
3.3粗甲醇储槽………………………………………………………………29
3.4循环压缩机的计算……………………………………………………30
七、讨论……………………………………………………………………31
八、参考文献……………………………………………………………………32
一、甲醇的国内外发展简况及甲醇的用途
甲醇作为极其重要的有机化工原料,是碳一化学工业的基础产品,在国民经济中占有重要地位。
长期以来,甲醇都是被作为农药,医药,染料等行业的工业原料,但随着科技的进步与发展,甲醇将被应用于越来越多的领域。
1.生产的发展
1)世界甲醇工业的发展
总体上说,世界甲醇工业从90年代开始经历了1991-1998的供需平衡,1998-1999的供大于求,从2000年初至今的供求基本平衡三个基本阶段。
[1]据NexantChemSystems公司的最新统计,全球2004年甲醇生产能力为4226.5万t/a[2]以下是近几年的甲醇需求统计。
表1全球主要地区甲醇消费构成
2001年
2002年
2003年
2004年
按用途分
甲醛
940(31)
970(32)
1010(32)
1050(33)
MTBE
830(28)
810(26)
780(25)
760(22)
(其中美国)
470(16)
430(14)
340(11)
270(8)
醋酸
270(9)
290(9)
300(10)
310(10)
MMA
90(3)
90(3)
100(3)
100(3)
其它
880(29)
900(29)
930(30)
970(30)
需求合计
3020(100)
3060(100)
3100(100)
3180(100)
按地区分
亚洲
920(30)
940(31)
990(32)
1040(33)
北美
1000(33)
1000(33)
980(31)
970(30)
西欧
630(21)
640(21)
650(21)
670(21)
其它
470(16)
480(16)
490(16)
500(16)
需求合计
3020(100)
3060(100)
3110(100)
3180(100)
从上表可以看出,到2004年为止,甲醇仍主要用于制造甲醛和MTBE。
用于制造甲醛的甲醇用量随年份成增长趋势,而MTBE的需求量则逐年降低。
亚洲需求量增长比较迅速,与此相反,北美地区需求则在减少。
2)我国甲醇工业发展
我国的甲醇工业经过十几年的发展,生产能力得到了很大提高。
1991年,我国的生产能力仅为70万吨,截止2004年底,我国甲醇产能已达740万吨,ll7家生产企业共生产甲醇440.65万生产甲醇,2005年1~9月甲醇量达393.22万t,因此增长22.2%,进口量99.1万t,因此下降3.1%。
2.生产技术的发展
1)装置大型化
与上世纪末相比,现在新建甲醇规模超过百万吨的已不在少数。
在2004~2008年新建的l4套甲醇装置中平均规模为134万t/a,其中卡塔尔二期工程项目高达230万t/a。
最小规模的是智利甲醇项目,产能也达84万t/a,一些上世纪末还称得上经济规模的6O万t/a装置因失去竞争力而纷纷关闭。
2)二次转化和自转化工艺
合成气发生占甲醇装置总投资的50%~60%,所以许多工程公司将其视为技术改进重点。
已经形成的新工艺主要是Synetix(前ICI)的先进天然气加热炉转化工艺(AGHR)、Lurgi的组合转化工艺(CR)和Topse的自热转化工艺(ATR)
3)新甲醇反应器和合成技术
大型甲醇生产装置必须具备与其规模相适应的甲醇反应器和反应技术。
传统甲醇合成反应器有ICI的冷激型反应器、Lungi的管壳式反应器、Topsdpe的径向流动反应器等近期出现的新合成甲醇反应器有日本东洋工程(TEC)的MRF—Z反应器等,而反应技术方面则出现了Lurgi推出的水冷一气冷相结合的新流程。
4)引入膜分离技术的反应技术
通常的甲醇合成工艺中,未反应气体需循环返回反应器,而KPT则提出将未反应气体送往膜分离器,并将气体分为富含氢气的气体,前者作燃料用,后者返回反应器。
5)液相合成工艺’
传统甲醇合成采用气相工艺,不足之处是原料单程转化率低、合成气净化成本高、能耗高。
相比之下,液相合成由于使用了比热容高、导热系数大的长链烷烃化合物作反应介质,可使甲醇合成在等温条件下进行。
3.甲醇的用途
甲醇是重要的化工原料,甲醇主要用于生产甲醛,其消耗量约占甲醇总量的30%-40%,其次作为甲基化剂,生产甲胺、甲烷氯化物、丙烯酸甲酯、甲基丙烯酸甲酯、对苯二甲酸二甲酯等,甲醇羰基化可生产醋酸、醋酐、甲酸甲酯、碳酸二甲酯等。
从甲醇低压羰基化生产醋酸,近年来发展很快。
甲醇作为重要原料在敌百虫、甲基对硫磷、多菌灵等农药生产中,在医药、染料、塑料、合成纤维等工业中有着重要的地位。
甲醇还可经生物发酵生成甲醇蛋白,用作饲料添加剂。
甲醇不仅是重要的化工原料,而且还是性能优良的能源和车用燃料。
它可直接用作汽车燃料,也可与汽油渗合使用,它可直接用于发电站或柴油机,或经zsM—5分于筛催化剂转化为汽油,它可与异丁烯反应生成甲基叔丁基醚,用作汽油添加剂。
二、甲醇合成方法
当今甲醇生产技术主要采用中压法和低压法两种工艺,并且以低压法为主,这两种方法生产的甲醇约占世界甲醇产量的80%以上。
高压法:
(19.6-29.4MPa)是最初生产甲醇的方法,采用锌铬催化剂,反应温度360-400℃,压力19.6-29.4MPa。
高压法由于原料和动力消耗大,反应温度高,生成粗甲醇中有机杂质含量高,而且投资大,其发展长期以来处于停顿状态。
低压法(5.0-8.0MPa)是20世纪60年代后期发展起来的甲醇合成技术。
低压法基于高活性的铜系催化剂,其活性明显高于锌铬催化剂,反应温度低(240-270℃)。
在较低压力下可获得较高的甲醇收率,且选择性好,减少了副反应,改善了甲醇质量,降低了原料的消耗。
此外,由于压力低,动力消耗降低很多,工艺设备制造容易。
中压法(9.8-12.0MPa):
随着甲醇工业的大型化,如采用低压法势必导致工艺管道和设备较大,因此在低压法的基础上适当提高合成压力,即发展成为中压法。
中压法仍采用高活性的铜系催化剂,反应温度与低压法相同,但由于提高了压力,相应的动力消耗略有增加。
比较以上三者的优缺点,以投资成本,生产成本,产品收率为依据,选择低压法为生产甲醇的工艺路线。
三、甲醇合成的生产原理及影响因素
1.合成系统中的反应
CO2+H2→CO+H2O+102.37kJ/mol
CO+H2→(CH3)2O+H2O+200.39kJ/mol
CO+3H2→CH4+H2O+115.69kJ/mol
CO2+H2→CO+H2O-42.92kJ/mol
4CO+8H2→C4H9OH+3H2O+49.62kJ/mol
2.甲醇合成生产的影响因素
1)温度
用来调节甲醇合成反应过程的工艺参数中,温度对于反应混合物的平衡和速率,都有很大影响。
由一氧化碳加氢生成甲醇的反应和由二氧化碳加氢生成甲醇的反应,均为可逆的放热反应。
(1)一氧化碳加氢合成甲醇的最佳温度
对于可逆放热反应而言,存在最佳反应温度曲线。
当甲醇含量较低时,由于平衡的影响相对的很小,最佳温度高,随着反应的进行,甲醇含量升高,平衡影响增大,最佳温度就低。
反应器操作时,沿着最佳温度线进行,则反应速率最高而可得最大产量,但温度不能超过催化剂耐热允许温度,对于铜基催化剂一般不超过300℃。
最佳温度值受操作压力,反应气体混合物的初始组成以及所用催化剂的颗粒大小等因素影响。
(2)有二氧化碳参加反应时的最佳温度
由于两个反应的速率常数和平衡常数不同,同一组成下,两个反应的最佳温度不同。
故使两个反应速率之和最大时的温度,才是该反应系统的最佳温度。
实现最佳温度的方法,工业上采用连续换热式或多段冷激式催化剂筐,使催化床的温度尽可能沿最佳温度分布。
2)压力
压力也是甲醇合成反应过程的重要工艺条件之一。
甲醇合成反应时分子数减少,因此增加压力对平衡有利,由于压力高,组分的分压提高,因而催化剂的生产强度也提高。
操作压力的选用与催化剂的活性温度范围有关。
对于锌铬催化剂,其起始活性温度在320℃,由于反应平衡的限制,只能选用25-30mpa。
再高的压力则会导致副反应加速,造成温度猛升而损坏催化剂。
而铜系催化剂的活性温度范围在200-300℃,操作压力可降至5MPa,若能解决移热问题,则可设计高压下铜基催化剂合成甲醇的系统。
对于现有合成塔的操作,催化剂使用初期,活性好,操作压力可较低;催化剂使用后期,活性降低,往往采用较高压力,以保持一定的生产强度。
3)原料配比
实验证明,最大反应速率时的组成并不是化学计量组成,由动力学方程确定的最佳氢碳比表明,在远离平衡的情况下,Zn-Cr催化剂最大反应速率的组成H2:
CO=4,据报道,氢含量还可以减少副反应以及降低催化剂的中毒程度。
以上所指组成的氢碳比是合成反应器内的组成,近似于循环气组成,至于合成系统的进口新鲜气组成,则应根据整个合成系统的物料平衡而定,以维持系统的稳定生产。
CO2的存在对于甲醇合成是有益的,一般维持在2-6%即可,新鲜气中CO2含量还可略高些。
新鲜气的组成,一般受上游流程的制约,但也要尽量满足本系统的要求。
按化学计量要求(H2O2)与(CO+CO2)的摩尔比一般为2.05-2.15。
惰性气体的含量也能影响反应速率,含量太高,降低反应速率,生产单位产量的动力消耗也大;维持低惰性气含量,则放空量加大,多损失有效气体。
一般来说,惰性气体含量要根据具体情况来定,而且这也是调节工况的手段之一。
4)催化剂颗粒尺寸
由动力学研究可知,催化剂颗粒大小对甲醇合成的宏观速率有显著的影响。
催化剂颗粒小,内表面利用率大,从而宏观反应速率大,可减少催化剂用量;粒度减小,会使床层压力降增大,从而增加动力消耗。
因此催化剂的最佳颗粒尺寸尚需视气流和床层的特性即有关的具体情况而定。
较合理的情况是,反应器上部装小颗粒,下部则装大颗粒催化剂。
5)空速
对于甲醇合成过程,若采用较低空速,则反应速率变化较大,反应过程中气体混合物的组成与平衡组成较接近,反应速率较低,催化剂的生产强度较低,但单位甲醇产品所需循环气量小,气体循环的动力消耗小,预热未反应气体到催化剂进口温度所需换热面积较小,且离开反应器气体的温度较高,热能利用价值高。
若采用较高空速,则反应速率变化较小,催化剂的生产强度提高,但增大了预热所需传热面积,热能利用率降低,增大了循环气体通过设备的压力降及动力消耗,并且由于气体中反应产物的浓度降低,增加了分离反应产物的费用。
还应注意,空速增大到一定程度后,催化剂床层温度不能维持。
因此,必须综合多方面因素来考虑最佳空速的问题。
6)反应器结构
甲醇合成塔内件的型式繁多,内件的核心为催化剂筐,他的设计好坏直接影响合成塔的产量和消耗定额。
一个好的催化剂筐设计应满足以下要求:
(1)能保证催化剂在升温、还原过程中操作正常、还原充分,尽可能地提高催化剂的活性,达到最大的生产强度。
(2)能有效地移去反应热,合理地控制催化剂层的温度分布,使其逼近最佳操作温度线,提高甲醇净值和催化剂的使用寿命。
(3)能保证气体均匀地通过催化剂层,阻力小,气体处理量大,甲醇产量高。
(4)充分利用高压空间,尽可能多装催化剂,提高容积利用系数。
(5)操作稳定、调节方便,能适应各种操作条件的变化。
(6)结构简单,运转可靠,装卸催化剂方便,制造、安装和维修容易等。
(7)妥善处理各个内件的连接与保温,避免产生热应力,使内件在塔内能自由胀缩。
如上所述,合成塔内件型式很多,有各自的特点和适用场合,因此不能用简单的方法肯定一种塔型或全部否定一种塔型。
传统的高压法甲醇合成多用连续换热的三套管并流式和单管并流式,中低压法流程则多用多层冷激式合成塔和管式合成塔以及两者的改进型合成塔。
无论在何种压力下操作,为减少阻力面应用径向合成塔或轴、径向复合式合成塔。
四、设计依据
1.生产规模:
3万吨/年
2.年工作时间:
300天(7920小时)
3.产品纯度:
大于99%(质量分数)
4.甲醇衡算数据:
见下表
表2甲醇衡算数据表
组分
组成
合成塔出
口气中
甲醇含量3.95%
新鲜气(mol)
驰放气(mol)
粗甲醇kg/100kg
溶解气NM3/t
CO2
0.1164
0.0680
0.8522
4.9280
CH4
0.0196
0.1560
----
0.1008
N2
0.0112
----
0.5824
H2
0.8528
0.6644
0.0001
3.1808
CO
0.1050
0.0068
0.5712
CH3OH
----
0.0056
79.1140
0.6944
(CH3)2O
----
0.0003
0.5480
0.0560
C4H9OH
----
----
0.1990
----
H2O
----
0.0007
19.2409
0.1008
五、工艺流程说明
工艺流程可简略的表示为下图:
图1甲醇合成工艺流程示意图
本工艺采用低压法,新鲜气与由压缩机产生的循环压缩气混合,形成入塔气,其温度为40℃,压力为10MPa。
在进入合成塔前,入塔气与出塔气进行热交换,温度升到150℃,压力仍为10.0MPa,经铜系催化剂催化反应后,温度变为220℃,压力变为9.6MPa。
出塔气与入塔气热交换后,进入冷却冷凝器,此过程大部分甲醇冷凝,温度降至25℃。
少量未冷凝的甲醇与其它气体一起进入循环压缩机,然后再与新鲜气混合。
在进入压缩机前,有一排气口,将少部分冷凝后的气体排放,以减少惰性气体在体系中的累积。
冷凝后的甲醇进入闪蒸罐,得到粗甲醇和闪蒸气。
闪蒸气排空,粗甲醇进入精馏系统精制。
六、工艺流程设计
1.物料衡算
以1吨粗甲醇为基础,对整个系统作总的物料衡算,物料衡算图如图2所示。
图2总物料衡算图
CO2
CH4
N2
H2
CO
CH3OH
(CH3)2O
C4H9OH
H2O
sum
质量/kg/h
8.522
0
0
0.001
0.068
791.14
5.48
1.99
192.409
999.61
摩尔
流量/Kmol/h
0.194
0
0
0.0005
0.002
24.723
0.110
0.027
10.689
35.746
摩尔
分率
5.42E-03
0
0
1.40E-05
6.79E-05
6.92E-01
3.07E-03
7.52E-04
2.99E-01
1
由甲醇衡算数据表,可计算出第7流股中各组分质量,摩尔流量,摩尔分率
表3第7流股各组分构成情况
以CO2为例:
mCO2=0.8522×10=8.522kg/h
nCO2=8.522/44=0.194kmol/h
xCO2=0.194/∑xini=5.42e-03
表4第8流股各组成构成情况
CO2
CH4
N2
H2
CO
CH3OH
(CH3)2O
C4H9OH
H2O
sum
体积/NM3
4.928
0.101
0.582
3.181
0.571
0.694
0.056
0
0.101
摩尔流量/Kmol/h
0.220
0.005
0.026
0.142
0.026
0.031
0.003
0
0.005
0.456
摩尔分率
0.482
0.010
0.057
0.311
0.056
0.068
0.005
0
0.010
1.000
1)新鲜气、驰放气摩尔流量
设新鲜气摩尔流量为F,CO的摩尔含量为x。
驰放气摩尔流量为Q,其中甲烷含量为y。
根据原子平衡,可得以下方程:
C原子:
F×(0.136+x)=25.532+Q×(0.1792+y)……1
O原子:
F×(0.2328+x)=36.442+Q×0.2476……2
N原子:
0.0112×F=0.026+Q×(0.156-y)……3
H原子:
F×(1.784-2x)=121.649+Q×(1.354+4y)……4