测控新技术.docx
《测控新技术.docx》由会员分享,可在线阅读,更多相关《测控新技术.docx(10页珍藏版)》请在冰豆网上搜索。
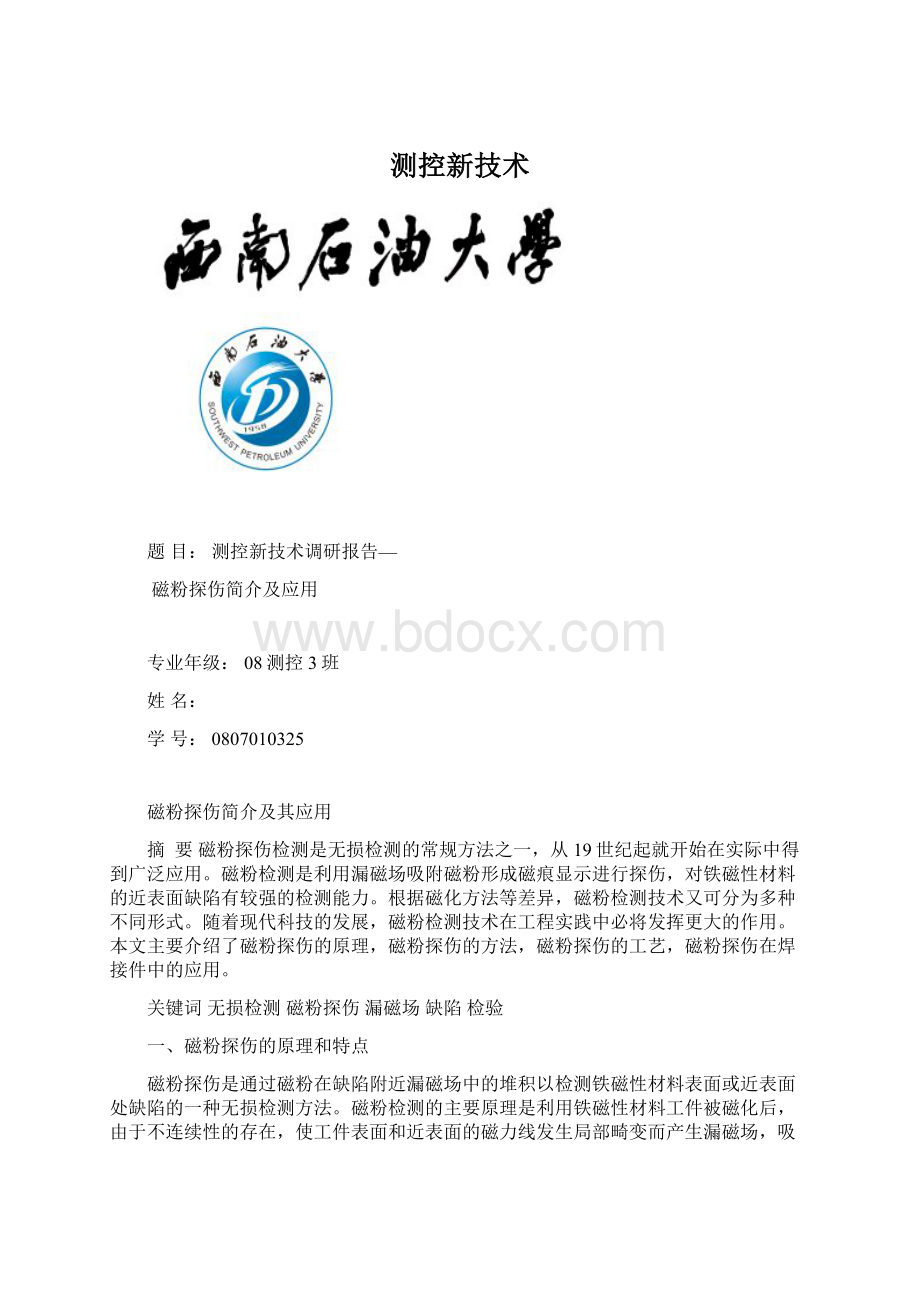
测控新技术
题目:
测控新技术调研报告—
磁粉探伤简介及应用
专业年级:
08测控3班
姓名:
学号:
0807010325
磁粉探伤简介及其应用
摘要磁粉探伤检测是无损检测的常规方法之一,从19世纪起就开始在实际中得到广泛应用。
磁粉检测是利用漏磁场吸附磁粉形成磁痕显示进行探伤,对铁磁性材料的近表面缺陷有较强的检测能力。
根据磁化方法等差异,磁粉检测技术又可分为多种不同形式。
随着现代科技的发展,磁粉检测技术在工程实践中必将发挥更大的作用。
本文主要介绍了磁粉探伤的原理,磁粉探伤的方法,磁粉探伤的工艺,磁粉探伤在焊接件中的应用。
关键词无损检测磁粉探伤漏磁场缺陷检验
一、磁粉探伤的原理和特点
磁粉探伤是通过磁粉在缺陷附近漏磁场中的堆积以检测铁磁性材料表面或近表面处缺陷的一种无损检测方法。
磁粉检测的主要原理是利用铁磁性材料工件被磁化后,由于不连续性的存在,使工件表面和近表面的磁力线发生局部畸变而产生漏磁场,吸附施加在工件表面的磁粉,在合适的光照下形成目视可见的磁痕,从而显示出不连续性的位置、大小、形状和严重程度。
研究磁粉检测技术,首先要明确它的物理基础。
磁粉检测是磁场效应的一种应用。
磁场就是磁体或通电导体周围具有磁力作用的空间。
磁场的大小、方向和分布情况可以用磁力线表示。
磁力线是闭合的曲线,在磁体内由S极到N极,在磁体外由N极穿过空气进入S极。
磁力线总是由磁阻最小的路径通过。
不同的材料根据其被磁化的难易程度可以分为铁磁质、顺磁质和抗磁质。
铁磁性材料如铁、钴、镍等,在一定磁场强度下,会产生一定的磁力线密度。
磁导率越大,材料越易被磁化,其呈现的磁性也越强。
磁粉检测是利用漏磁场吸附磁粉形成磁痕显示进行探伤。
所谓漏磁场,就是铁磁性材料磁化后,在不连续处或磁路截面变化处,磁感应线离开和进入表面时形成的磁场。
漏磁场形成的原因,是由于空气的磁导率远远小于铁磁性材料的磁导率。
如果在磁化了的工件上存在不连续性或裂纹,则磁感应线优先通过磁导率高的工件,这就迫使部分磁感应线从缺陷下面绕过,形成磁感应线的压缩。
但是,工件上这部分可容纳的磁感应线数目也是有限的,又由于同性磁感应线相斥,所以部分磁感应线从不连续中穿过,另一部分磁感应线遵循折射定律几乎垂直从工件表面进入空气中绕过缺陷又折回工件,形成了漏磁场。
漏磁场可分解为水平分量Bx和垂直分量By,水平分量与工件表面平行,垂直分量与工件表面垂直。
假设有一矩形缺陷,则在矩形中心漏磁场的水平分量有极大值并左右对称,而垂直分量为通过中心点的曲线。
如果将两个分量合成,就得到了缺陷的漏磁场。
漏磁场对磁粉的吸附可看成是磁极的作用,如果有磁粉在磁极区通过,则将被磁化,呈现出N极和S极,并沿着磁感应线排列起来。
当磁粉的两极和漏磁场的两极相互作用时,磁粉就会被吸附并加速移动到缺陷上去。
漏磁场的磁力作用在磁粉微粒上,其方向指向磁感应线最大密度区,即指向缺陷处。
由于漏磁场的宽度要比缺陷实际的宽度大数倍至数十倍,所以磁痕对缺陷宽度具有放大的作用,可以将目视不可见的缺陷转变为目视可见的磁痕使之容易观察出来。
磁粉探伤的基本原理:
将待测物体置于强磁场中或通以大电流使之磁化,若物体表面或表面附近有缺陷(裂纹、折叠、夹杂物等)存在,由于它们是非铁磁性的,对磁力线通过的阻力很大,磁力线在这些缺陷附近会产生漏磁。
当将导磁性良好的磁粉(通常为磁性氧化铁粉)施加在物体上时,缺陷附近的漏磁场就会吸住磁粉,堆集形成可见的磁粉迹痕,从而把缺陷显示出来,如图1所示。
(a)(b)
图1磁粉探伤原理示意图
(a)表面缺陷(b)近表面缺陷
磁粉探伤的用途:
在工业中,磁粉探伤可用来作最后的成品检验,以保证工件在经过各道加工工序(如焊接、金属热处理、磨削)后,在表面上不产生有害的缺陷。
它也能用于半成品和原材料如棒材、钢坯、锻件、铸件等的检验,以发现原来就存在的表面缺陷。
铁道、航空等运输部门、冶炼、化工、动力和各种机械制造厂等,在设备定期检修时对重要的钢制零部件也常采用磁粉探伤,以发现使用中所产生的疲劳裂纹等缺陷,防止设备在继续使用中发生灾害性事故。
磁粉探伤的特点:
磁粉探伤对钢铁材料或工件表面裂纹等缺陷的检验非常有效;设备和操作均较简单;检验速度快,便于在现场对大型设备和工件进行探伤;检验费用也较低。
但它仅适用于铁磁性材料;仅能显出缺陷的长度和形状,而难以确定其深度;对剩磁有影响的一些工件,经磁粉探伤后还需要退磁和清洗。
二、磁粉探伤的磁化
1、磁化方法磁粉探伤必须在被检工件内或在其周围建立一个磁场,磁场建立的过程就是工件的磁化过程。
根据建立磁场的方向不同,磁化方法可作如下分类:
(1)周向磁化给工件直接通电,或者使电流流过贯穿工件中心孔的导体,在工件中建立一个环绕工件并且与工件轴线垂直的闭合磁场。
周向磁化用于发现与工件轴线(或电流方向)平行的缺陷。
(2)纵向磁化电流通过环绕工件的线圈,使工件中的磁力线平行于线圈的轴线。
纵向磁化用于发现与工件轴线相垂直的缺陷。
利用电磁轭磁化使磁力线平行于工件纵轴亦属于与这一类。
(3)复合此线将周向磁化和纵向磁化同时作用与工件上,使工件得到由两个互相垂直的磁力线的作用而产生的合成磁场,其指向构成扇形磁化场。
(4)旋转磁化将绕有激磁线圈的二线磁铁交叉放置,各通以不同相位的交流电,产生圆形或椭圆形磁场(既合成磁场的方向作圆形旋转运动)。
旋转磁化能发现沿任意方向分布的缺陷。
2、磁化磁场的方向与磁场强度当磁化磁场的磁力线与缺陷断面垂直时,能在缺陷处获得最大的漏磁场。
在焊缝磁粉探伤中,为得到较高的探测灵敏度,通常在被探件上至少使用两个近似相互垂直方向的磁化(包括使用旋转磁化的情况)。
为了保证探伤结果的准确性,磁化磁场必须有足够的强度,而且必须控制在适当的范围内(通常在±25%)。
由于影响磁场的因素众多,很难建立严格的磁场强度规则,且使用规范有相应标准或技术条件列出。
对于新产品,应使用已知缺陷的工件进行试验来确定磁场强度。
三、磁粉探伤的工艺
根据被探件的材料、形状、尺寸及需检查缺陷的性质、部位、方向和形状等的不同,所采用的磁粉探伤方法也不尽相同,但其探伤步骤大体如下:
1、探伤前的准备校验探伤设备的灵敏度,除去被探伤件表面的油污、铁锈、氧化皮等。
2、磁化
(1)确定探伤方法对高碳钢或经热处理(淬火、回火、渗碳、渗氮)的结构钢零件用剩磁法探伤;对低碳钢、软钢用连续法。
(2)确定磁化方法。
(3)确定磁化电流种类一般直流电结合干磁粉、交流电结合湿磁粉效果较好。
(4)确定磁化方向应尽可能使磁场方向与缺陷分布方向垂直。
(5)确定磁化电流磁化电流的选择是影响磁粉检验灵敏度的关键因素。
磁化电流的大小一般是根据磁化方式再由相应的标准或技术文件中给出。
(6)确定磁化的通电时间采用连续法时,应在施加磁粉工作结束后在切断磁化电流。
一般是在磁悬液停止流动后必须再通几次电,每次时间为0.5~2s。
采用剩磁法时,通电时间一般为0.2~1s。
3、喷洒磁粉或磁悬液采用干法检验时,应使干磁粉喷成雾状;湿法检验时,磁悬液需经过充分的搅拌,然后进行喷洒。
4、对磁痕进行观察及评定用于非荧光法检验的白色光强度应保证试件表面有足够的亮度。
若发现有裂纹、成排气孔或超标的线形或圆形显示,均判定为不合格。
5、退磁当工件进行两个以上方向的磁化后,若后道工序不能克服前道工序剩磁影响时,应进行退磁处理。
6、清洗、干燥、防锈
7、结果记录
四、磁粉检测的主要优点
①能直观的显示缺陷的位置、形状、大小,并可大致确定缺陷的性质;②检测灵敏度较高,目前可检测出的最小缺陷宽度约为0.1微米;③几乎不受试件大小和形状的限制;④检测速度快;⑤检测工艺简单;⑥检测费用低。
五、磁粉检测的局限性
①只能检测铁磁性材料,不能检测非铁磁性材料(如铜、铝等有色金属,奥氏体不锈钢,非金属);②只能检测表面或接近表面缺陷,可探测的缺陷深度一般在1-2毫米以内;③对缺陷取向有一定的限制,一般要求磁化场的方向与缺陷主平面的夹角大于20°;④对试件表面的质量要求较高;⑤深度方向的缺陷定量与定位困难。
目前,磁粉检测主要应用于金属铸件、锻件和焊缝的检测。
六、磁粉探伤在焊接件中的应用
目前,焊接技术在冶金、机械、石油和化工等部门中的应用已经相当普遍。
随着工业技术的发展,高强度焊接结构的应用日趋广泛。
高强钢在焊接时产生缺陷的倾向比普通焊接结构钢要大。
因此随着高强钢的应用对探伤技术也就提出了更高的要求。
裂纹尤其是表层裂纹在焊接结构中,特别是在承受疲劳应力作用的焊接结构中,是一种危害极大的缺陷,为保证焊接结构安全运行,就必须加强焊接件的检验,发现裂纹并及时排除。
磁粉探伤是检验钢制焊接结构表层缺陷的最佳方法,具有设备简单、灵敏可靠、探伤速度快和成本低等特点。
(一)焊接件探伤的内容与范围
1、坡口探伤
坡口可能出现的缺陷有分层和裂纹,前者是轧制缺陷,它平行于钢板表面,一般分布在板厚中心附近。
裂纹有两种,一种是沿分层端部开裂的裂纹,方向大多平行于板面;另一种是火焰切割裂纹。
坡口探伤的范围是坡口和钝边。
2、焊接过程中的探伤
(1)层间探伤某些焊接性能差的钢种要求每焊一层检验一次,发现裂纹及时处理,确认无缺陷后再继续施焊。
另一种情况是特厚板焊接,在检验内部缺陷有困难时,可以每焊一层用磁粉探伤检验一次。
探伤范围是焊缝金属及邻近坡口。
(2)电弧气刨面的探伤目的是检验电弧气刨造成的表面增碳导致产生的裂纹。
探伤范围应包括电弧气刨面和临近的坡口。
3、焊缝探伤
焊缝探伤的目的主要是检验焊接裂纹。
探伤范围应包括焊缝金属及母材的热影响区,热影响区的宽度大约为焊缝宽度的一半。
因此,要求探伤的宽度应为两倍焊缝宽度。
4、机械损伤部位的探伤
在组装过程做,往往需要在焊接部件的某些位置焊上临时性的吊耳和卡具,施焊完毕后要割掉,在这些部位有可能产生裂纹,需要探伤。
这种损伤部位的面积不大,一般从几平方厘米到十几平方厘米。
(二)探伤方法选择
用于焊缝探伤的磁化方法有多种,各有特点。
要根据焊接件的结构形状、尺寸、检测的内容和范围等具体情况加以选择。
1、磁轭法
磁轭法是指便携式交流电磁铁。
其特点是设备简单、操作方便。
但是磁轭只能单方向磁化在,因此,为了检出各个方向的缺陷,必须在同一部位至少作两次互相垂直的探伤,而且应将焊缝划分为若干个受检段,做出标记,每个受检段的长度应比两级之间的距离小10~20毫米,电磁轭之间最佳距离为100~150毫米。
2、支杆法
支杆法也是单方向磁化的方法。
其主要优点是电极间距可以调节,可根据探伤部位情况及灵敏度要求确定电极间距和电流大小。
同一部位至少作两次互相垂直的探伤。
3、交叉磁轭法
用交叉磁轭旋转磁化的方法检验焊缝表层裂纹可以得到满意的效果。
其主要优点是灵敏度可靠并且探伤效率高。
目前在焊缝探伤中尤其在锅炉压力容器探伤中应用越来越广。
4、线圈法
对于管道圆周焊缝可以用线圈法探伤。
方法是在焊缝附近沿圆周方向用电缆绕4~6匝,对管道进行轴向磁化。
这种方法只能发现焊缝和热影响区以纵向为主的裂纹。
(三)焊接件探伤实例
1、坡口探伤
使用交叉磁轭检验坡口缺陷是利用交叉磁轭外侧的磁化场磁化坡口,操作方法是把交叉磁轭置于靠近坡口的钢板面上,沿坡口方向连续行走探伤。
为检验探伤灵敏度,可在远离交叉磁轭一侧的坡口边上贴试片进行试验。
一般情况下,在检验板厚不大于50mm钢板坡口时可达30/100A型试片的探伤灵敏度。
对于更硬的钢板经试验达不到灵敏度要求时,可在坡口两侧各进行一次探伤。
2、电弧气刨面的探伤
探伤时,把交叉磁轭跨在电弧气刨沟槽中间,沿沟槽方向连续行走。
探伤时,应根据构件位置采用喷洒或刷涂磁悬液的方法,原则是交叉磁轭通过后不得使磁悬液残留在电弧气刨沟槽中,否则将无法观察判断。
3、球形压力容器的开罐检查
现以手工电弧焊焊接的球形容器的开罐检查为例简述磁粉探伤的实施方法。
(1)探伤部位球形容器的内外侧所有焊缝和热影响区以及母材机械损伤部分。
(2)表面清整应把焊缝表面的焊接波纹及热影响区表面的飞溅用砂轮进行打磨,不得有凸凹不平的棱角。
若做过磁粉探伤,已经打磨过,表面只有浮锈时,可用喷砂或钢丝刷除去焊缝及热影响区表面的浮锈。
(3)探伤操作
①检验对接焊缝时时把交叉磁轭跨在焊缝上连续行走探伤。
当检查球罐纵缝时,交叉磁轭行走方向要自上而下。
②进出气孔及排污孔管板接头的角焊缝,用交叉磁轭紧靠管子边缘沿圆周方向探伤。
七、磁粉探伤在大型铸锻件中的应用
1.铸钢件磁粉检测
(1)铸钢件探伤的特点大型铸钢件通常采用支杆法或磁轭法并用干磁粉进行检验。
检验时主要注意三个问题:
1)不论用支杆还是磁轭磁化,每次都应有少量重叠,并做两次互相垂直方向的磁化和检查。
2)喷洒磁粉不要太急太快,否则会冲走已形成的显示或无法使不连续处集聚磁粉。
3)铸钢件由于内应力影响,有些裂纹延迟开裂,所以铸后不宜立即检测,而应等一、二天后再检测。
(2)空心十字铸钢件磁粉检测
根据工件的结构特点,为了发现各个方向的缺陷,采用的磁化方法是:
使用两次中心导体法周向磁化,并使用两次绕电缆法纵向磁化。
磁化电流可采用交流电或整流电。
根据钢材磁特性可采用连续法或剩磁法,用湿法检验。
2.锻钢件磁粉检测
锻钢件的工艺过程一般为:
下料—加热—锻造—探伤—热处理—探伤—机械加工—表面热处理—机械加工—最终探伤—成品。
从以上的工艺过程可以看出,锻钢件经历了冷热加工工序,而且多数工件形状复杂,这就使锻钢件容易产生各种性质的缺陷。
锻钢件产生的缺陷主要有:
锻造裂纹、锻造折叠、淬火裂纹、磨削及矫正裂纹等。
在使用过程中还可能产生应力疲劳引起的裂纹。
(1)曲轴磁粉检测
曲轴有模锻和自由锻两种,以模锻为多。
由于曲轴形状复杂且有一定的长度,一般采用连续法轴通电方式进行周向磁化,线圈分段纵向磁化。
(2)塔形试样磁粉检测
塔形试样是用于抽样检验钢棒和钢管原材料缺陷的试验件,磁粉检测的主要目的是检查发纹和非金属夹杂物。
塔形试样检验时工艺要点:
1)发纹都是沿轴向或成一夹角,所以只进行轴向通电法检验。
2)塔形试样都是在热处理前检测,所以采用湿式连续法。
3)磁化电流可按各台阶的直径分别计算,磁化和检验的顺序是从最小直径到最大直径,逐阶磁化检验,也可选按最大直径选择电流检验塔形的所有表面,若发现缺陷,再按相应直径规定的磁化电流磁化和检验。
八、磁粉探伤在在役与维修件中的应用
1.在役与维修件检验的特点是
1)维修件探伤的目的主要是为了检查疲劳裂纹和应力腐蚀裂纹,所以探伤前,要充分了解工件在使用中的受力状态、应力集中部位、易开裂部位以及裂纹的方向。
2)疲劳裂纹一般出现在应力最大部位,因此,在许多情况下,只需要进行局部检查。
3)用磁粉检测检查时,常用触头法、磁轭法、线圈(及电缆)法等,小的工件也可用固定式磁粉探伤机进行检查。
4)对一些不可接近或视力不可达部位的检查,可以采用其它检测方法辅助进行。
5)有覆盖层的工件,根据实际情况采用特殊工艺或去掉覆盖层后进行检测。
6)磁粉检测后往往需要记录磁痕,定期检查原来就有磁痕的部位,以观察疲劳裂纹的扩展。
2.飞机大梁螺栓孔的磁粉检测
飞机大梁螺栓容易在飞机服役过程中产生疲劳裂纹,裂纹的方向与孔的轴线平行,集中出现在孔的受力部位。
在飞机定期检测中,对于螺栓孔多采用磁粉检测-橡胶铸型法来检查疲劳裂纹。
(1)预处理将螺栓分解下来,用000号砂布装到手电钻上对孔壁进行打磨,直到没有任何锈蚀痕迹,然后用干将抹布将孔擦拭干净。
(2)磁化工件用中心导体法磁化螺栓孔,将铜棒穿入孔中,电流取I=40D。
(3)施加磁悬液用手指堵住孔的底部,将黑色磁粉与无水乙醇配制的磁悬液注入孔内,直至注满,停留10s左右,待磁痕形成后,让磁悬液流掉,再用无水乙醇漂洗掉内壁的多余磁粉。
(4)进行橡胶铸型让孔壁彻底干燥,用胶布或软木塞等将孔的下部堵住,将加入硫化剂的室温硫化硅橡胶注入孔中,直至灌满。
(5)取出铸型橡胶固化后,可从孔的上端或下端将橡胶铸型拔出,或从孔的底部轻轻地顶出。
(6)观察磁痕在良好的光线下用10倍放大镜检查橡胶铸件,或在实体显微镜下观察。
(7)退磁。
参考文献
1)赵熹华主编,焊接检验,北京:
机械工业出版社,1993
2)全国锅炉压力容器无损检测人员资格鉴定考核委员会编,磁粉探伤,北京:
劳动人事出版社,1989
3)任吉林主编,电磁无损检测,北京:
航空工业出版社,1989
4)刘贵明主编,无损检测技术,北京:
国防工业出版社,2006
5)李喜孟,无损检测,北京:
机械工业出版社,2001
6)李路明.提高漏磁检测量化精度的研究[D].北京:
清华大学,1996
7)李丽茹.表面检测—磁粉,渗透与涡流[M].北京:
机械工业出版社,2009
8)邓红军.无损检测实训[M].北京:
机械工业出版社,2010.
9)魏锋,寿比南等.压力容器检验及无损检测:
化学工业出版社,2003
10)wardsCE,PalmerSB.Themagneticleakagefieldofsurfacebreakingcracks[J].JPhysD:
ApplyPhys,1986,19(4):
657-673.
11)AthertonD,HaugeC.LinepressurestressaffectsMFLsignals[J].OilGasJ,1996,18(3):
92-99