挠性及刚挠印制板生产工艺二.docx
《挠性及刚挠印制板生产工艺二.docx》由会员分享,可在线阅读,更多相关《挠性及刚挠印制板生产工艺二.docx(12页珍藏版)》请在冰豆网上搜索。
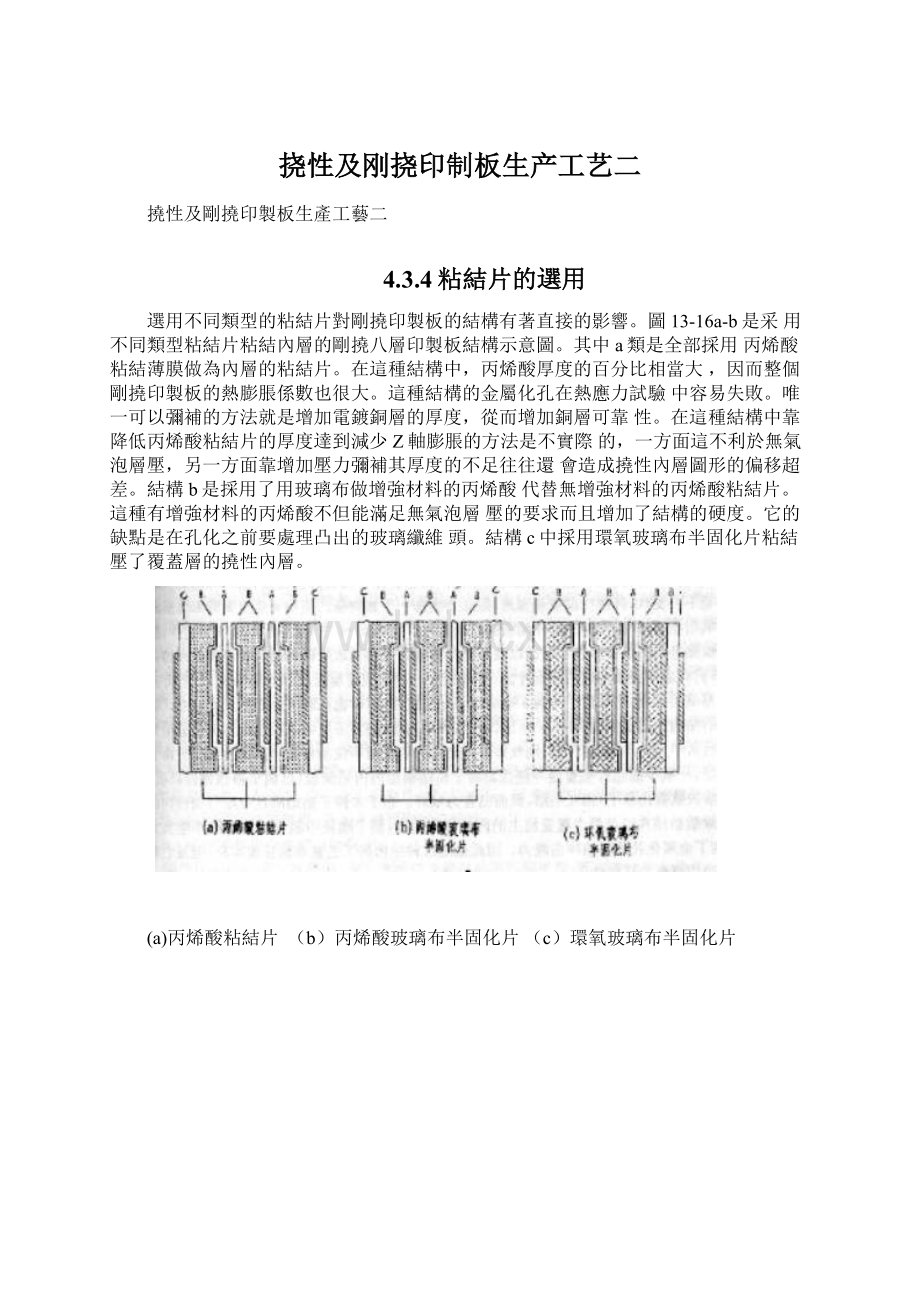
挠性及刚挠印制板生产工艺二
撓性及剛撓印製板生產工藝二
4.3.4粘結片的選用
選用不同類型的粘結片對剛撓印製板的結構有著直接的影響。
圖13-16a-b是采用不同類型粘結片粘結內層的剛撓八層印製板結構示意圖。
其中a類是全部採用丙烯酸粘結薄膜做為內層的粘結片。
在這種結構中,丙烯酸厚度的百分比相當大,因而整個剛撓印製板的熱膨脹係數也很大。
這種結構的金屬化孔在熱應力試驗中容易失敗。
唯一可以彌補的方法就是增加電鍍銅層的厚度,從而增加銅層可靠性。
在這種結構中靠降低丙烯酸粘結片的厚度達到減少Z軸膨脹的方法是不實際的,一方面這不利於無氣泡層壓,另一方面靠增加壓力彌補其厚度的不足往往還會造成撓性內層圖形的偏移超差。
結構b是採用了用玻璃布做增強材料的丙烯酸代替無增強材料的丙烯酸粘結片。
這種有增強材料的丙烯酸不但能滿足無氣泡層壓的要求而且增加了結構的硬度。
它的缺點是在孔化之前要處理凸出的玻璃纖維頭。
結構c中採用環氧玻璃布半固化片粘結壓了覆蓋層的撓性內層。
(a)丙烯酸粘結片 (b)丙烯酸玻璃布半固化片(c)環氧玻璃布半固化片
(d)環氧玻璃布(或丙烯酸玻璃布)半固化片
(e)環氧玻璃布(或丙烯酸玻璃布)半固化片
A:
0.05mm厚雙面覆35μm銅箔聚酰亞胺薄膜
B:
帶丙烯酸粘結片的0.025mm厚聚酰亞胺覆蓋層
C:
雙面覆銅箔環氧玻璃布層壓板
D:
雙面覆銅箔聚酰亞胺玻璃布層壓板
圖13-16剛撓多層印製板結構示意圖
由於環氧樹脂與聚酰亞胺薄膜的結合力較差,因此在安裝和使用過程中,易產
生內層分層的現象。
可以通過在環氧玻璃布與聚酰亞胺之間加一層丙烯酸膠增加結合力,這樣做的結果是又引進了丙烯酸而且還增加了生產的複雜性。
因此,這種結構不宜採用。
結構d中取消了覆蓋層,內層的粘結全部採用環氧玻璃布半固化片或環氧玻璃布做增強材料的丙烯酸。
撓性覆銅箔基材在表面的銅被蝕刻掉之後露出的是一層丙烯酸膠,因而它與環氧的結合力非常好。
同時,由於環氧材料的大量引入大大降低了整個剛撓印製板的熱膨脹係數,因此大大提高了金屬化孔的可靠性。
由於去掉了大量的覆蓋層,這種印製板在高溫工作環境下會變軟,其撓性段更是如此,因此要增加一個加固板。
結構e是用聚酰亞胺層壓板代替環氧層壓板,可以改善剛撓印製板的耐高溫性。
結構a-e中,除了c不宜採用之外,制造商可以根據自己的設備和技術情況以及剛撓印製板的應用要求來確定剛撓印製板的結構。
近來,國外的製造商突破傳統的層壓方法。
正在嘗試一種大膽的覆蓋層部分層壓法。
這種方法具有顯而易見的優點;它保留了結構a中結合力好的優點,同時也克服了熱膨脹大的缺點。
這種層壓法的結構示意圖如圖13-17所示。
在這種結構中,撓性多層印製板最外邊的覆蓋層只伸入到剛性區中大約1/10的位置,剛性外層與撓性內層採用不流動環氧半固化片粘結。
由於沒有覆蓋層,環氧半固化片主要是與撓性基材上粘結銅箔的丙烯酸膠(當銅箔被蝕刻掉以後,這層丙烯酸膠就露出來了)相互粘結,因而結合力很好。
由於去掉了粘結剛性外層與撓性內層的兩層丙烯酸粘結片以及兩個覆蓋層上的丙烯酸粘結片,整個剛撓印制板的熱膨脹係數大大降低,提高了金屬化孔的耐熱衝擊能力。
因此雖然這種結構的工藝複雜而且成本高,但是它卻提高了剛撓印製板的可靠性。
圖13-17 覆蓋層部分層壓法
傳統的 改進的
剛性外層與剛性內層的粘結首先要注意所選用的粘結片流動度應低於2%,主要是為了防止樹脂從剛性部分的下部溢流到撓性視窗部分。
改性丙烯酸薄膜,低流動度環氧樹脂薄膜和不流動環氧玻璃布半固化片都是可供選用的粘結材料。
丙烯酸與聚酰亞胺的結合力強,而且不會在剛撓結合部出現餘膠堆積,它的缺點是熱膨脹係數大。
環氧樹脂與聚酰亞胺的結合力稍差,但是它的熱膨脹係數較小。
它的主要缺點是會在剛撓結合部形成餘膠堆積,因而在無法解決余膠問題時,最好還是選用丙烯酸做粘結片。
4.3.5層壓的襯墊材料
襯墊材料的選用對於撓性及剛撓印製板的層壓質量十分重要。
理想的襯墊材料應該具有良好的敷形性,流動度低,冷卻過程不收縮的特點,以保證層壓無氣泡和撓性材料在層壓中不發生變形。
襯墊材料通常分為軟性體系和硬性體系。
軟性體系主要包括聚氯乙烯薄膜或輻射聚乙烯薄膜等熱塑性材料。
這種材料在各個方面的壓力以及成形都比較均勻,而且敷形性非常好,能滿足無氣泡層壓的要求。
但是這種材料在壓力較大的情況下,其流動度大大增加,從而造成撓性材料的變形超差,因而這種襯墊材料最適合於簡單的撓性印製板。
硬性體系主要是採用玻璃布做增強材料的矽橡膠。
矽橡膠在各個方向的壓力都十分均勻,並且在Z軸方向上適應凹凸不平的電路,具有良好的敷形效果。
其中的玻璃布則起到限制矽橡膠在X,Y方向上的移動,即使層壓的壓力較大,也不會引起撓性內層的變形。
矽橡膠的價格雖然比聚氯乙烯薄膜昂貴,但是它卻可以重複使用,是十分理想的襯墊材料。
4.3.6剛撓印製板撓性窗口的保護:
剛撓印製板的層壓過程中,為了保證撓性視窗的層壓和平整,要在窗口放入墊片。
墊片應當表面光潔,具有脫膜性,這是為了保證撓性視窗的外觀和墊片易於拆卸。
墊片的厚度應與剛性外層的厚度一致,墊片的大小應與窗口匹配。
墊片的尺寸太小會使撓性視窗產生不規則壓痕影響外觀;墊片太大則不利於排氣和拆卸。
經過層壓以後,剛撓印製板的撓性視窗還要經過一系列的濕法工序,在這些工序中都應對撓性視窗進行特殊的保護。
綜上所述可以看出,撓性多層板尤其是剛撓印製板的層壓比普通剛性多層印製板複雜得多。
無論是基材的選擇,粘結片的選擇還是襯墊材料的選擇都十分講究。
只有在正確選擇材料的基礎上,正確的把握工藝條件才能達到理想的層壓效果。
4.4鑽孔
由於撓性剛撓印製板的結構複雜,因此確定鑽孔的最佳工藝參數對取得良好的孔壁十分重要。
為防止內層銅環以及撓性基材的釘頭現象,首先要選用鋒利的鑽頭。
如果所加工的印製板數量大或加工板內的數量多,還要在鑽夠一定孔數時更換鑽頭。
鑽頭的轉速以及進給是最重要的工藝參數。
進給太慢時,溫度急劇上升產生大量鑽汙。
而進給太快則容易造成斷鑽頭,粘結片以及介質層的撕裂和釘頭現象。
通常Ф0.6孔,其典型的鑽孔工藝參數為:
進給量70mm/sec,轉速50000rpm。
對於有附連測試圖形的在制板,附連測試圖形的孔應最後鑽,這樣才能真實的反映加工板孔內的情況。
上,下墊板的使用對鑽孔質量也十分重要。
上墊板能防止板子的上表面產生毛刺和鑽頭鑽偏,起導向作用。
上墊板一般採用0.3mm厚的硬鋁板,鋁板還能起到散熱從而減少鑽汙的作用。
下墊板具有保護工作臺,防止板子下表面產生毛刺的作用。
下墊板的厚度一般為1.5mm,應具有均勻,平整,對鑽頭磨損小以及不含能引起鑽汙的成份等特點。
一種覆鋁箔層壓板是較為理想的下墊板,它是以木屑和紙漿為芯,兩面是硬鋁箔,用不含樹脂的膠作粘結劑。
從所周知,印製板孔內的鑽汙的形成主要是由於鑽孔時的高溫使印製板中的樹脂發生熔化。
實驗證明,印製板的鑽污水平和厚度隨著鑽孔時溫度的升高而增加,在樹脂的玻璃化溫度之上增加更快。
因而有些製造商曾嘗試冷凍法鑽孔,通過降低加工板上的溫度而達到減少鑽汙的效果。
具體做法是:
先將剛撓印製板在低溫下(放入冷庫或冰箱中)冷凍數小時,取出後在冷氣保溫條件下鑽孔。
採用這種方法鑽的孔,孔壁銅環光亮,只有少許鑽汙,效果十分明顯。
4.5去鑽汙和凹蝕
經過鑽孔的印製板孔壁上可能有樹脂鑽汙,只有將鑽汙徹底清除才能保證金屬化孔的質量。
在剛撓印製板中,由於覆蓋層和丙烯酸粘結片上鍍層結合力差,在經受熱衝擊時,易造成鍍層與孔壁分離,所以孔壁除了要求徹底去除鑽汙外,還要求有20μm左右的凹蝕,以使內層銅環與電鍍銅呈可靠性更高的三點接觸,大大提高金屬化孔的耐熱衝擊性。
通常,聚酰亞胺產生的鑽汙較少,而環氧和改性丙烯酸產生的鑽汙較多。
環氧鑽汙可用濃硫酸去除,而丙烯酸鑽汙只能用鉻酸去除。
鉻酸法處理過程中板子的持拿及清洗都十分不方便。
又由於聚酰亞胺不耐強堿,因此強鹼性的高錳酸鉀去鑽汙根本不適用於撓性和剛撓印製板。
因此,許多廠家都使用等離子體法去鑽汙和凹蝕。
圖13-18為剛撓多層印製板未去淨鑽汙而]造成內層互連斷路的顯微剖切實例。
圖13-18 X200內層膩汙導致內層斷路
等離子體去鑽汙是國外八十年代才開始採用的技術。
等離子體是電離的氣體,整體上顯電中性,是一種帶電粒子組成的電離狀態,稱為物質第四態。
應用等離子去除剛撓板及撓性板孔壁的鑽汙可看作是高度活化狀態的等離子氣體與孔壁高分子材料和玻璃纖維發生氣固化學反應,同時生成的氣體產物和部分未發生反應的粒子被抽氣泵排出,是一個動態的化學反應平衡過程。
等離子體氣體的生成條件為:
(1)將一容器抽成真空(0.2-0.5Torr),並保持一定的真空度;
(2)向真空容器中通入所選氣體,必須保持一定的真空度;(3)開啟射頻電源向真空器內正負電極間施加高頻高壓電場,氣體即在正負極間電離,放出輝光,形成等離子體,此時氣體不斷輸入,真空泵一直工作以使真空器內保持一定真空器。
由於等離子體處理需要專用設備以及電子級專用氣體,因此採用等離子體去鑽汙凹蝕比較昂貴。
圖13-19為等離子體去鑽汙,凹蝕的工藝流程圖。
撓性或剛撓印製板→ 鑽孔→ 去毛刺→ 高壓水洗→ 濕噴砂→ 烘板
等離子體阻蝕處理→ 高壓水洗→ 孔金屬化
圖13-19等離子體去鑽汙凹蝕工藝流程圖4.5.1高壓濕噴砂:
高壓濕噴砂是用600目左右的剛玉(AL2O3)在高壓水條件下對多層板孔壁進行清洗的過程。
高壓水洗與顯噴砂都是為了提供潔淨的孔壁,減少後續等離子體處理的負荷。
4.5.2烘板:
主要是為了去除加工板中的潮氣。
因為丙烯酸樹脂和聚酰亞胺樹脂的吸潮係數比環氧樹脂大得多。
如果印製板中的潮氣因低真空而進入真空系統,必然降低真空度,同時在真空泵中凝結,會對真空泵造成極大的損害。
另外,對等離子體的化學活性也有影響。
烘板的工藝條件為:
1200C下烘3至4小時。
4.5.3等離子體處理
印製板專用的等離子體化學處理系統-等離子體去膩汙凹蝕系統,一般由五部分組成:
真空腔體,真空泵,RF發生器,微機控制器,原始氣體。
各類型等離子體處理設備只是在真空腔內電極的結構和氣體的輸入位置和方式上略有差別。
圖13-20為PC-760等離子體系統的外形。
圖13-21為真空腔體內部結構。
整個等離子體處理過程為分批間歇操作,分為三步,各步驟的典型工藝參數如表13-7所示。
第一階段是用高純度的N2氣為處理氣,產生等離子體。
目的是使整個系統處於N2氛圍;N2自由基與孔壁附有的氣體分子反應,使孔壁清潔且使孔壁實氮,同時預熱印製板,使高分子材料處於一定的活化態,以利於後續階段反應。
第二階段以O2,CF4,為原始氣體,混合後產生O,F等離子體,與丙烯酸,聚酰亞胺和環氧樹脂,玻璃纖維反應,達到去鑽汙凹蝕的目的。
第三階段採用O2為原始氣體,生成的等離子體與反應殘餘物反應使孔壁清潔。
等離子體處理的工藝參數主要包括:
氣體比例,流量,射頻功率,真空度和處理時間。
氣體比例是決定生成等離子體活性的重要參數。
要達到較好的處理效果,一般02為50-90%和CF4為50-10%。
純02等離子體與孔壁材料反應速度慢且產生熱量大,導致銅的氧化。
而50%-10%的CF4增加了反應由凹蝕速度,能產生極化度高,活性強的氧氟自由基。
射頻(RF)功率大小約在2-5kw之間。
高的功率使氣體電離度提高,提高了反應速度,但同時也產生大量的熱量。
從而增加了間歇式反應的次數。
系統氣體壓力主要由射頻功率和氣體流量,比例決定。
在較低的壓力下,等離子體放電不均勻,但粒子的平均自由程加大,可增加粒子進入小孔的能力;高的氣體壓力使粒子的滲透能力降低,且產生大量輝光。
增加功率水平可以改善滲透能力。
通常比較理想的系統壓力在200-300mTorr之間。
圖13-20PC-760等離子體處理系統
圖13-21真空腔的內部結構
表13-7等離子體去鑽汙凹蝕工藝參數
工藝參數(系統壓力280mTorr)
第一階段
第二階段
第三階段
CF4氣百分比(%)
0
20
0
O2氣百分比(%)
0
80
100
N2氣百分比(%)
100
0
0
真空度(mTorr)
110
110
110
射頻功率(kw)
2.5
2.5
2.5
處理時間(min)
5
40
5
等離子體去鑽汙凹蝕是複雜的物理化學過程,有許多影響因素。
包括工藝參數
,鑽孔質量,前處理效果,印製板潮濕程度和溫度,印製板上孔的分佈和大小等。
總之,只有充分考慮各類影響因素,正確確定前處理和等離子處理的工藝參數才能確保去鑽汙凹蝕的質量。
4.6孔金屬化和圖形電鍍
4.6.1工藝流程,見圖13-22所示。
經等離子體處理加工板 →除玻璃纖維 →化學鍍銅 →電鍍銅加厚
成像 →圖形電鍍
圖13-22 金屬化孔和圖形電鍍工藝流程
4.6.2去除玻璃纖維
採用等離子體除去撓性和剛性印製板孔內鑽汙時,各種材料的凹蝕速度各不相同,從大到小的順序是:
丙烯酸膜,環氧樹脂,聚酰亞胺,玻璃纖維和銅。
從顯微鏡中能明顯地看到孔壁有凸出的玻璃纖維頭和銅環。
為了保證化學鍍銅溶液能充分接觸孔壁,使銅層不產生空隙和空洞,必須將孔壁上等離子反應的殘餘物,凸出的玻璃纖維和聚酰亞胺膜除去,處理方法,包括化學法和機械法或二者結合。
化學法是用氟化氫胺溶液浸泡印製板,再用離子表面活性劑(KOH溶液)調整孔壁帶電性。
機械法包括高壓濕噴砂和高壓水沖洗。
採用化學法和機械法相結合的效果最好。
4.6.3化學鍍銅
由於剛撓或撓性印製板中撓性部分基材如丙烯酸和聚酰亞胺不耐鹼,因此孔的前處理溶液應儘量採用酸性的,活化宜採用酸性的膠體鈀而不宜採用鹼性的離子鈀。
如果採用鹼性化學鍍銅溶液,要控制好化學鍍銅的沉積速率。
沉積速率過慢,反應時間長,鹼性溶液會導致撓性內層材料溶脹;太快則溶液不穩定,銅層機械能差。
合適的速率為5*5cm2玻璃布試驗引發時間5-6s,覆蓋時間15-20s。
化學鍍銅宜採用鍍薄銅工藝。
因為化學鍍銅層的機械性能(如延展率)較差,在經受熱衝擊時易產生斷裂。
一般在化學鍍銅層達到0.3-0.5μm時,立即進行全板電鍍銅加厚至3-4μm,以保證在後續的處理過程中孔壁鍍層的完整。
4.6.4成像
剛撓及撓性多層板在層壓之後表面不如剛性多層印製板平整,最好採用真空貼膜和真空曝光工藝。
孔周圍的不平整還易影響幹膜的顯影從而形成殘膜。
因而顯影後的清洗一定要乾淨徹底,以防幹膜殘渣污染孔壁,最終造成孔內空洞。
圖13-23剛撓多層印製板的吸潮
4.6.5圖形電鍍
首先圖形電鍍的銅延展率十分重要,要求電鍍銅層的延展率大於剛撓及撓性多層印製板的熱膨脹率並且有較高的抗強度。
在經受熱衝擊時,剛撓多層印製板基材的總膨脹率比孔中鍍銅層大1.65%,而這一指標在剛性多層板中僅為0.03%。
由此可見,剛撓印製板中金屬化孔所承受的拉應力比剛性多層板大得多。
同時,鍍銅層的厚度對剛撓印製板的可靠性也有一定影響。
大多數剛撓多層板製造商都靠增加孔壁銅層厚度來提高金屬化孔的可靠性。
但是片面增加銅層厚度不能提高金屬化孔的可靠性,這是由於隨金屬化孔鍍層厚度的增加,孔內橫向應力增加。
最合適的銅層厚度為40-50μm.最後,控制好電鍍溶液的成份及工藝參數是生產出高品質金屬化孔的保證。
(1)要求的
(2)可接受的
(3)不能接受的
圖13-24 覆蓋層的分層
4.7熱熔/熱風整平
由於撓性和剛撓印製板的吸潮性大,因此在熱熔或熱風整平之前一定要烘板去除潮汽,以防止在經受熱衝擊時,金屬化孔斷裂或內層分層。
通常應在1200C下烘4-6小時。
烘完的印製板應立即進行熱熔或熱風整平,以防止板子重新吸潮。
圖13-23為剛撓印製板在50%相對濕度,室溫條件下的吸潮情況。
從圖可以看出,在24小時之內,板子的潮濕水平急劇升高。
熱熔工藝通常採用甘油熱熔,它比紅外線熱熔更容易控制。
撓性印製板由於很軟,在熱風整平時應固定在特製的夾具上。
4.8外形銑
撓性印製板的外形加工在大批量時是用專用沖膜(橡皮模具)沖,小批量時用剪刀剪。
剛撓印製板則要在銑床上銑外形,主要應注意撓性部分,因為撓性部分易於扭曲而造成銑出的外形參差不齊和粗糙。
可以在撓性視窗的上下墊入與剛性外層厚度一致的墊片,並且在銑外形時壓緊,就可以確保銑出光潔而且均勻的外形邊緣。
銑外形的典型工藝參數為進給量25mm/s,轉速45000rpm。
低進給高轉速會造成印製板邊緣燒焦,反之進給大而轉速低則會造成銑刀折斷和印製板外形的參差不齊。
5.撓性及剛撓印製板的性能要求
撓性及剛撓印製板在大多數通用要求上與剛性印製板是一致的,針對其引進了撓性材料的特點,還有以下幾方面的特殊要求。
1,覆蓋層分層:
撓性及剛撓印製板的覆蓋層分層應符合以下規定,如圖13-24所示。
圖13-25 連接盤上的粘結劑
1) 離開導線隨機位置分層的面積不大於6.5mm2(約直徑2.5mm),離印製板邊緣或余隙孔邊緣的距離不小於1mm。
在任意6.5cm2覆蓋層表面區域內,分層的個數不多於3個。
2) 沿導線邊緣的分層寬度不大於0.5mm或不大於相鄰導線間距的20%,(以較小者為准)。
3) 覆蓋層外邊緣無分層。
4) 在滿足1)-2)條要求的情況下,允許覆蓋層有皺褶。
2,連接盤上粘結劑:
元件孔連接盤上的粘結劑應不使環寬小於0.13mm(金屬化)孔)或0.25mm(非金屬化孔),見圖13-25.
3,覆蓋層余隙孔:
當每個元件孔絕緣層為單個余隙孔時,其重合度應不使最小環寬小於0.13mm(金屬化孔),0.25mm(非金屬化孔)。
有盤趾加固的連接盤,盤趾應被覆蓋層塔蓋,見圖13-26.
圖13-26 余隙孔位
4,增強層的附著性:
撓性印製板與增強層間的最小剝離強度應不小於0.55N/mm.5,耐彎折性:
1型板和2型板的彎折半徑應為撓性印製板彎折處總厚度的6倍,但應不小於1.6mm.3型板,4型板和5型板的彎曲半徑應為撓性印製板彎折處總厚度的12倍,但應不小於1.6mm。
在經歷13-27次彎折後,撓性和剛撓印製板應不出現性能降低或不可接受的分層現象。
耐彎折性應按圖13-27所示的方法進行試驗。
佈設總圖中應規定下列實驗要求:
a:
彎折方向;b:
彎折度數。
C:
彎折週期數;d:
彎折半徑;e:
彎折點。
彎折週期的定義為:
取試樣的一端,使它圍繞心軸彎折,然後解除彎折回到原來位置,在一個方向彎折1800,然後在相反方向彎折1800.彎折週期也可以定義為:
取試樣兩端互相向著同一方向彎折,然後解除彎折回到原來位置,每一端在一個方向彎折900.然後在相反方向彎折900.試驗時,將心軸放在試樣的一側與試樣接觸,然後將心軸放在式樣的另一側與試樣接觸,分別做完規定的彎折週期數。
做完彎折試驗後檢驗印製板的電性能。
6,耐撓曲性:
1型和2型板的撓曲半徑為撓曲處總厚度的6倍,最小約為1.6mm。
3型,4型,5型板的撓曲半徑應為撓曲處總厚度的12倍,最小約為1.6mm。
撓性和剛撓印製板應能耐100000次撓曲而無斷路,短路,性能降低或不可接受的分層現象。
耐撓曲性採用專用設備(例如撓性疲勞延展性測試儀FOF-1型),也可採用等效的儀器測定,被測試樣應是符合有關技術規範要求。
佈設總圖應規定下列要求:
a撓曲週期數;b撓曲半徑;c撓曲速率;d撓曲點;e回轉行程(最小25.4mm).
圖13-27耐彎折性實驗