步进驱动液压工作台的控制系统设计说明书.docx
《步进驱动液压工作台的控制系统设计说明书.docx》由会员分享,可在线阅读,更多相关《步进驱动液压工作台的控制系统设计说明书.docx(42页珍藏版)》请在冰豆网上搜索。
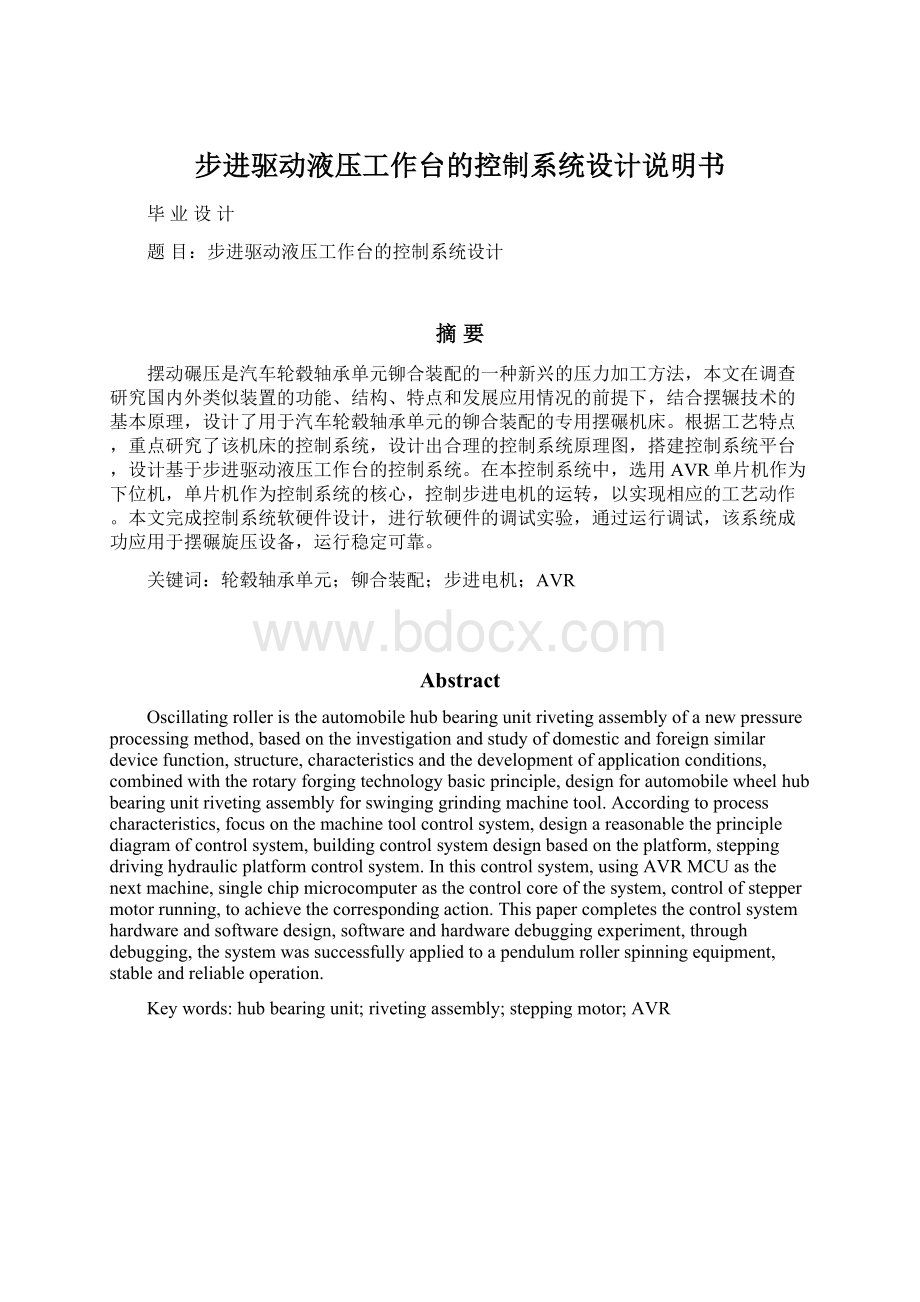
步进驱动液压工作台的控制系统设计说明书
毕业设计
题目:
步进驱动液压工作台的控制系统设计
摘要
摆动碾压是汽车轮毂轴承单元铆合装配的一种新兴的压力加工方法,本文在调查研究国内外类似装置的功能、结构、特点和发展应用情况的前提下,结合摆辗技术的基本原理,设计了用于汽车轮毂轴承单元的铆合装配的专用摆碾机床。
根据工艺特点,重点研究了该机床的控制系统,设计出合理的控制系统原理图,搭建控制系统平台,设计基于步进驱动液压工作台的控制系统。
在本控制系统中,选用AVR单片机作为下位机,单片机作为控制系统的核心,控制步进电机的运转,以实现相应的工艺动作。
本文完成控制系统软硬件设计,进行软硬件的调试实验,通过运行调试,该系统成功应用于摆碾旋压设备,运行稳定可靠。
关键词:
轮毂轴承单元;铆合装配;步进电机;AVR
Abstract
Oscillatingrolleristheautomobilehubbearingunitrivetingassemblyofanewpressureprocessingmethod,basedontheinvestigationandstudyofdomesticandforeignsimilardevicefunction,structure,characteristicsandthedevelopmentofapplicationconditions,combinedwiththerotaryforgingtechnologybasicprinciple,designforautomobilewheelhubbearingunitrivetingassemblyforswinginggrindingmachinetool.Accordingtoprocesscharacteristics,focusonthemachinetoolcontrolsystem,designareasonabletheprinciplediagramofcontrolsystem,buildingcontrolsystemdesignbasedontheplatform,steppingdrivinghydraulicplatformcontrolsystem.Inthiscontrolsystem,usingAVRMCUasthenextmachine,singlechipmicrocomputerasthecontrolcoreofthesystem,controlofsteppermotorrunning,toachievethecorrespondingaction.Thispapercompletesthecontrolsystemhardwareandsoftwaredesign,softwareandhardwaredebuggingexperiment,throughdebugging,thesystemwassuccessfullyappliedtoapendulumrollerspinningequipment,stableandreliableoperation.
Keywords:
hubbearingunit;rivetingassembly;steppingmotor;AVR
1.
第一章绪论
1.1引言
近年来,汽车工业迅速发展,汽车轮毂轴承单元的制造技术在不断发展,将旋压用于轮毂轴承单元的轴铆合装配,是当前轮毂单元制造技术的最新进展。
旋压(摆动碾压)是一种新兴的压力加工方法,属于局部加压,连续成形,具有省力﹑零件尺寸精度高﹑振动小﹑噪音低﹑投资小等优点。
从七十年代开始,在世界锻造行业被广泛应用,军工产品如导弹壳的制造等是其最重要的应用领域之一。
目前在国内的研究还处于空白状态,设计开发出用于轮毂轴承单元轴端铆合装配的专用生产设备,将填补国内空白,使有关轴承生产企业突破新型轮毂单元装配制造的工艺瓶颈,有重大创新意义。
1.2本课题的研究意义与主要任务
轮毂轴承单元的铆合技术显然在当代和将来的汽车发展中都起到十分重大的作用,但是当代的中国的大部分工厂都没有相应的专用铆合设备或者是工厂因受到技术的封锁而不能引进国外的设备和技术。
国内的轮毂轴承的市场大部分都由国外的厂家占用。
本文的主要任务是调查研究国内外类似装置的功能、结构、特点和发展应用情况的前提下,结合摆辗技术的基本原理,设计了用于汽车轮毂轴承单元的铆合装配的专用摆碾机床。
根据工艺特点,重点研究了该机床的控制系统,设计出合理的控制系统原理图,搭建控制系统平台,设计基于步进驱动液压工作台的控制系统。
在本控制系统中,选用AVR单片机作为下位机,单片机作为控制系统的核心,控制步进电机的运转,以实现相应的工艺动作。
完成控制系统软硬件设计,进行软硬件的调试实验。
1.3最新汽车轮毂轴承铆接工艺应用
汽车轮毂轴承的作用主要是承受汽车的重量及为轮毂的传动提供精确的向导。
轮毂轴承既承受径向载荷又承受轴向载荷,是一个非常重要的安全件。
现在国产车大多仍采用传统的两套单独的圆锥滚子轴承或角接触球轴承,这种结构在汽车装配时要经过调整游隙、预紧、加脂等诸多工序,参杂较多人为控制因素,装配难度较大,从而造成汽车装配线加长,成本过高且可靠性差,难以适应激烈的市场竞争。
近年来,随着前置前驱动轿车的飞速发展,轮毂轴承发生了很大变化,尤其是国外知名的汽车生产厂家与轴承制造商联合研发,新型轮毂轴承单元不断涌现,目前己迸人第四代。
NSK铆压成形第三代轮毂铀承在传统的第三代轮毂轴承单元的设计中,两个内圈是用锁紧螺母牢固地连接在一起的,而NSK开发的新结构是通过轴端的铆压成形轴向力使带凸缘的内圈产生塑性变形,与小内圈压紧。
去掉螺母有助于减小轮毂单元的重量和尺寸,提高可靠性。
驱动轮和非驱动轮都适用。
采用铆压成形技术,可靠性将得以提高,即使连接螺母松动轴承自身也可以提供预载保证。
图1.1、内置内圈2、铆头3、轮毂轴
铆压成形采用的是铆接工艺(如图),倾斜的铆头(上模)在轴承组件上铆压时,带凸缘内圈的轴端受到来自下部的压力产生塑性变形,直至小内圈牢固地连在一起。
在成形过程中,轮毂变形分为三个阶段:
第一阶段,铆头下降,与轮毂轴接触,变形开始。
第二阶段,变形进一步扩展,轮毂轴沿径向扩展,与内圈倒角接触。
最后是第三阶段,铆接过程完成。
在第一阶段,几乎所有的铆头压力都用于轮毂轴的最初成形,内圈载荷很小且恒定。
进入第二阶段,铆头压力传递到内圈,内圈载荷迅速增大。
在第三阶段,由于铆头压力使内圈载荷逐渐增大直至饱和,铆压结束后,甚至铆头已抬起,内圈载荷仍未消除,仍保留某些载荷。
可以认为残余载荷形成了卡紧力。
传统的模锻使整个工件压缩,产生塑性变形。
因此,加工大尺寸工件时,需要很大的压力,而且当运用于轴承上时,变形往往超出中心区域。
在这种巨大压力作用下,球与滚道受到挤压,在加工过程轴承很可能损坏,而铆接工艺只在局部产生变形并且只用很小的压力。
通过控制加载的压力,这种加工用于轴承的装配十分适合。
通过重载下的运转耐久性试验检验了铆压成形缘的疲劳强度和内圈抗蠕变能力。
进行静强度试验以考察铆压成形缘的静强度以及轴承的力矩载荷刚变试验,因为轴承的刚性会影响车辆转弯时的操纵稳定性。
根据各项试验的结果,NSK新开发的铆压成形内圈自锁第三代轮毂轴承等同于甚至优于带锁紧螺母的传统型轮毂轴承。
在保证高可靠性的前提下,重量和尺寸减小,满足了当前的市场需求,降低了车辆燃料消耗。
1.4铆接机铆接质量情况及旋压铆合技术的优越性
轮毂轴承单元轴端铆质量是整个轮毂轴承单元装配的重要技术指标。
在实验铆接过程,传统做法是确定不同的铆接行程,调整死顶块的距离,达到不同的铆接效果,其缺点是对操作要求高,调整过程困难,铆接过程往往出现工件被压坏,或是铆接行程不够,铆接精度和质量达不到理想的铆接实验效果。
基于一般的铆接机的缺点,现提出铆接驱动过程实行伺服控制思路。
在液压系统中增加伺服控制环节,通过压力传感器检测铆接过程,并发出电信号控制换向卸荷回路,铆头铆接动作将得到精确的控制,通过调整压力传感器的不同值将可以达到理想的铆接实验效果,有效保证铆接精度和质量。
传统设计的轮毂单元在装配时两个内圈是用锁紧螺母牢固地连接在一起的,如图1-2(a)所示。
这种方式所存在的缺点是:
需要在装配的时候通过控制螺母的预紧量来控制轮毂单元的轴向卡紧力,由于单元中的零件存在制造误差而使卡紧力的控制不精确,预压量的波动较大,从而导致轴承的负游隙量偏离最优值而使轴承寿命下降,寿命离散度大大增加,使得其韦布尔分布中的斜率较大,90%可靠性下降;在使用过程中,由于螺纹卡紧采用的螺纹防松结构可能因振动等因素而松动,从而导致预载荷卸载,严重时甚至失效,存在重大安全隐患。
而新的结构是通过轴端的旋压成形,使带凸缘的内圈产生塑性变形,从而与小内圈压紧。
这种方式使车轮支架和车轮法兰不再是安装驱动轴之后才相互连接.而是经卷边铆接成为具有正常功能的轮毂轴承单元,大大减轻了下一步的装配工作。
采用轴铆合装配方式,对非驱动轮而言(如图1-2(b)所示),可直接去掉螺母;对驱动轮而言(如图1-2(c)所示),因为不再需要较大的拧紧力矩,可以使用轻型螺母将驱动轴固定在车轮法兰中,驱动轴带齿的轴颈也可大大缩短,从而有助于减小轮毂单元的重量和尺寸,降低成本,使紧固部分更加紧凑,提高燃油经济性。
而且旋压过程中对轴向载荷(卡紧力)可实时精确控制,消除零件制造误差的影响,从而使预紧量的波动大大减少,保证每一个轮毂单元都在装配后获得最佳预紧量,这意味着可以大大提高轴承使用寿命,并使韦布尔分布曲线的斜率变小,90%可靠性得到显著提高;且由于铆合联接是不可逆装配,不会因使用过程中的
振动等因素发生变化,从而消除螺纹防松结构中可能的卸载隐患,大大提高可靠性,也就提高了产品的安全性。
(a)(b)(c)
图1-2轮毂单元装配方法
另一方面,因为轮毂单元的最薄弱的环节不是锁紧位置,而是凸缘根部,而通过FEM分析可知,小内圈在汽车行驶过程中所承受的轴向载荷不是很高,通过对当前的轮毂单元的结构分析,我们认为其轴承组件部分还可进一步精减,只要将带凸缘的轴在端部直接旋压成滚道形状,就可省略小内圈,达到轴承组件零件数目的绝对最小化,进一步精减轮毂单元的结构,提高可靠性,降低生产成本。
1.5汽车轮毂轴承单元的国内外情况调查
随着前置驱动轿车的飞速发展,国外轮毂轴承发生了很大的变化,已从传统的分离式轴承发展到轴承单元,经历四代的发展。
汽车轮毂轴承单元的作用主要是承受汽车的重量并为轮毂的传动提供精确的向导。
轮毂轴承既承受径向载荷又承受轴向载荷,是一个非常重要的安全件。
近年来,随着前置前驱动轿车的飞速发展,轮毂轴承发生了很大变化,尤其是国外知名的汽车生产厂家与轴承制造商联合研发,新型轮毂轴承单元不断涌现,目前已进入第四代。
第一代轮毂轴承
第一代是外圈整体型双列角接触球轴承或圆锥滚子轴承。
它由一个外圈和两个内圈组成。
为了确保装到车轮上时轴承的预紧力,要求沟心距有很高的精度。
为此,砂轮用一个具有高尺寸精度的旋转成形修形器来进行修形。
外圈滚道进行同步磨削可以达到理想的高加工精度。
内圈滚道也必须有一个非常精确的定位,应用与外圈一样的成形旋转修形器,通过多角度磨削可以实现高精密的加工。
这种结构的主要优点是可靠、有效载荷间距短、易安装、无需调整、结构紧凑等。
这种轴承已经相当实用化,我国引进车型大多采用此类轴承。
第二代轮毂单元
第二代是将与轴承相配合的零件即轮毂或转向节与轴承套圈制成一体的结构型式(图1.3)。
开发该单元的重点是了为保证质量和尽可能缩短生产周期,为此这种单元最终采用了流水线生产。
第一代产品的淬火是分批完成的,而第二代则采用在线高频加热的方式进行淬火。
在回火工艺中也使用了感应加热系统以节省空间并缩短生产周期。
为了减少热处理变形所需的磨削时间,在热处理后紧接着引入一次装夹车削两个滚道的工序,以减少车削时刀架的重复拆卸时间。
第三代轮毂单元
日本公司已经成功开发出了获得最佳预紧力(负游隙)的技术,它既能提高汽车悬架所需的车轮稳定性,又能提高轴承寿命。
该技术已经能加工出满足刚度和寿命的最佳间隙和结构变形,带凸缘的内圈和另一个内圈是一体的,这使装配变得极其困难。
已前普遍接受的常规设计(图1.4)是小内圈与带凸缘的内圈进行压配合,并用锁紧螺母把它们固定在一起。
对装配的要求包括:
小内圈与带凸缘的较大内圈必须确保固定在一起。
一旦小内圈从带凸缘的内圈上松脱会导致轮子与车身脱离,因此必须防止这种情况的发生。
1带凸缘的外圈2保持架3内圈4球
图1.3第二代轮毂单元
1带凸缘的外圈2保持架3小内圈礴4锁紧螺母5球6带凸缘的内圈
图1.4第二代轮毂单元
轴向力的产生应确保小内圈的轴向紧固:
防止两个内圈之间相对旋转(蠕变),确定合适的预紧力以提高寿命、刚性和旋转精度。
当受到外力时,防止两个内圈上相互配合的接触表面发生分离。
(1)SKF带有ABS传感器的第三代轮毂轴承单元制动系防抱死系统(ABS)对车辆安全性作出了巨大贡献。
据报道,从2000年起,欧洲所有的轿车及轻型商用车都要将ABS作为标淮配置安装。
把ABS传感器安装到轮毂单元中,有许多优点,其中汽车制造商最感兴趣的是节约成本。
SKF为汽车工业生产轮毂轴承已经近60年。
由SKF提出的整体环状传感器是基于感应原理的被动ABS传感器。
一个带有29齿的脉冲环经过一个外部有线圈的永久磁场铁旋转。
当车轮转动时,线圈产生一个感应电信号,电信号的频率及大小与车辆转速有关。
SKF的这种结构在技术上有下列几点:
防锈性能提高,节省重量和空间,由于传感器和脉冲环间存在空气间隙更加耐用,信号强等优势。
信号强意味着速度极限更低,通常为3.7kn公h,甚至降到2.okmlh,这意味汽车的安全性进一步提高。
内置ABS传感器的第三代驱动轮毂单元已成为发展趋势,各大轴承公司都在积极研制。
(2)NSK旋压成形第三代轮毂轴承在传统的第三代轮毂轴承单元的设计中,两个内圈是用锁紧螺母牢固地连接在一起的,而NSK开发的新结构是通过轴端的旋压成形,轴向力使带凸缘的内圈产生塑性变形,与小内圈压紧。
去掉螺母有助于减小轮毂单元的重量和尺寸,提高可靠性。
驱动轮和非驱动轮都适用。
采用旋压成形技术,可靠性将得以提高,即使连接螺母松动轴承自身也可以提供预载保证。
旋压成形采用的是旋转模锻工艺(如图1.5),倾斜的上模在轴承组件上转动时,带凸缘内圈的轴端受到来自下部的压力产生塑性变形,直至小内圈牢固地连在一起。
1内置内圈2冲头3轮毂轴
图1.5旋压成形工艺示意图
在成形过程中,轮毂变形分为三个阶段:
第一阶段,冲头下降,与轮毂轴接触,变形开始。
第二阶段,变形进一步扩展,轮毂轴沿径向扩展,与内圈倒角接触。
最后是第三阶段,铆合过程完成。
在第一阶段,几乎所有的冲头压力都用于轮毂轴的最初成形,内圈载荷很小且恒定。
进入第二阶段,冲头压力传递到内圈,内圈载荷迅速增大。
在第三阶段,由于冲头压力使内圈载荷逐渐增大直至饱和,旋压结束后,甚至冲头已抬起,内圈载荷仍未消除,仍保留某些载荷。
可以认为残余载荷形成了卡紧力。
传统的模锻使整个工件压缩,产生塑性变形。
因此,加工大尺寸工件时,需要很大的压力,而且当运用于轴承上时,变形往往超出中心区域。
在这种巨大压力作用下,球与滚道受到挤压,在加工过程轴承很可能损坏,而旋压模锻只在局部产生变形并且只用很小的压力。
通过控制加载的压力,这种加工用于轴承的装配十分适合。
通过重载下的运转耐久性试验检验了旋压成形缘的疲劳强度和内圈抗蠕变能力。
进行静强度试验以考察旋压成形缘的静强度以及轴承的力矩载荷刚变试验,因为轴承的刚性会影响车辆转弯时的操纵稳定性。
根据各项试验的结果,NsK新开发的旋压成形内圈自锁第三代轮毂轴承等同于甚至优于带锁紧螺母的传统型轮毂轴承。
在保证高可靠性的前提下,重量和尺寸减小,满足了当前的市场需求,降低了车辆燃料消耗。
第四代轮毂轴承单元
第四代是把等速万向节与轴承做成整体化,这种形式最引注目的是废除轮毂花键轴,更加小型化,安装更加合理,如图1.6所示。
图1.6第四代轮毂轴承单元
汽车轮毂轴承已从传统的分离式轴承发展到轴承单元。
轮毂轴承正逐步成为与车轮支承总成连为一体的内部部件,第四代已研制成功,距离实用化不会遥远。
这些单元产品的特点是:
不需要调整轴承组装间隙(过选择间隔形式或按照力矩调整间隙),轴承组装工艺合理化,轻量化和小型化,提高可靠性、一次性装脂,免维护,降低整体成本。
国产车大多仍采用传统的两套单独的圆锥滚子轴承或角接触球轴承,这种结构在汽车装配时要经过调整游隙、预紧、加脂等诸多工序,参杂较多人为控制因素,装配难度较大,从而造成汽车装配线加长,成本过高且可靠性差,难以适应激烈的市场竞争。
我国在汽车轮毂轴承单元开发研制方面起步较晚,对产品设计和制造尚停留在仿制阶段,目前成系列开发生产的轮毂轴承单元只到第二代,第三代还处于试制阶段。
我国与工业发达国家的技术差距主要是制造技术方面的差距,轴承制造业也不例外。
长期以来,美国、日本、瑞典、德国等轴承强国一直在不遗余力地开发先进的轴承制造技术,以满足主机的使用要求,力争在激烈的全球经济竞争中保持其领先地位。
由于先进制造技术往往关系到一个公司甚至一个国家的经济发展,因而工业发达国家发展先进制造技术都带有垄断性。
国外轴承同行向来对中国封锁先进的轴承制造技术,这一点是我国轴承行业出访人员的共同感受。
我国轴承制造业必须在借鉴国外先进经验的基础上自主开发本国的先进制造技术。
在改善实施先进制造技术的基础条件的同时,优先发展适用先进的制造技术。
先进制造技术的研究开发立项要效益与水平并重,大中小企业需求并重,大批量制造与特种小批量制造技术并重,目的在于通过提高轴承性能、品质、寿命可靠性来满足主机的配套要求,增强国产轴承在国内外市场上的竞争力。
今后10年我国轴承制造业应重点发展的具有共性的关键制造技术包括:
节材节能增寿的轴承套圈精密冷辗扩技术,高精度高效率高稳定性的轴承套圈磨削—超精研自动生产技术以及与其相配套的轴承自动装配技术,G3级精密钢球研磨技术、精密凸度圆锥滚子磨削—超精研自动生产技术,精密保持架制造与测量技术,超精密轴承加工与测量技术,轴承仿真试验技术,以及轴承减振降噪、润滑和密封技术。
1.6汽车轮毂轴承单元的发展和前景
随着轮毂轴承单元一代一代改进和发展,结构刚性越来越高、可靠性越来越强、安装维护越来越方便,特别是第三代轮毂轴承单元,性能优良、安装方便,深受汽车设计师和汽车用户的青睐。
第三代轮毂轴承单元最早应用是在二十世纪九十年代,首先在各类乘用车上,后来很快发展到中型商用车上批应用;到二十一世纪,又进行了第四代轮毂轴承产品的开发,为汽车制造商提供样品,通过台架试验和道路试验,得到了汽车制造商的认可。
第五、六代轮毂轴承单元的设计思路尚在概念阶段,要形成产品或投入使用尚须时日。
而我国在汽车轮毂轴承单元的开发研制方面起步较晚,但近几年发展很快,目前从第一代到第三代轮毂轴承单元,在品种规格上已基本与国际市场同步,第四代还处于试制阶段,未形成系列化和规模化生产。
下表是2008年国内外轿车所用各代汽车轮毂轴承单元情况的大致比例,基本上能反映市场的实际情况。
载重车使用轮毂轴承单元的进展远比轿车滞后。
研究国内外汽车产品的发展历程,我们可以认为,轮毂轴承单元化技术已经成为现代汽车轴承发展的重要内容。
单元化集成件的优化组合、集成件的性能优化、高可靠度、低成本制造与维护将是轮毂轴承研究和发展的重点。
表1.1国内外各轿车轮毂轴承比较
国家为扶持汽车产业发展,制定了多项产业鼓励政策。
汽车轮毂轴承也属于鼓励类项目,如《外商投资产业指导目录(2007年修订)》中鼓励类第十七“通用机械制造业”中的第14条“第三、四代轿车轮毂轴承(轴承内、外圈带法兰盘和传感器的轮毂轴承功能部件),⋯⋯制造”的要求;《产业结构调整指导目录(2007年本)征求意见稿》中鼓励类第十二“机械”中的第4条“汽车高性能轴承、铁路轴承、精密轴承、低噪音轴承制造”的要求;国家四部委(工信部、科技部、财政部、国资委)工信部联装[2009]707号《重大技术装备自主创新指导目录}(2009年版)附件中编号l7.2.5“中高档汽车轴承”将“更新换代的集成化轴承的开发技术”列为需突破的关键技术之一,市场预测或产业化前景明确为“年需求量2亿套,市场约100亿元,国内市场占有率2011年达3O%,2015年达5O%.
随着汽车工业的发展,第三代轮毂轴承单元的使用越来越广泛,甚至一些经济型轿车和中重型商用车也开始使用第三代轮毂轴承单元。
据保守估计,到2014年,国内汽车配套市场对于第三代轮毂轴承单元的需求量可能达到2500万套以上;而国内汽车维修市场需用的第三代轮毂轴承单元将接近1000万套。
’在北美、欧洲、日本等工业发达国家生产的汽车,从上世纪九十年代就开始配装了第三代轮毂轴承单元,估计到2014年,全球整车配套市场和维修市场对于第三代轮毂轴承单元的需求量均将达到1.5-1.8亿套。
通过如上的分析预测,我们对汽车轮毂轴承单元的发展前景有了非常清晰的认识,可以确定,汽车轮毂轴承单元,尤其是第三代轮毂轴承单元,集成了传统滚动轴承和现代电子技术于一体,将是一个非常具有市场潜力的新生代产品,从而也为传统的滚动轴承产品开辟了一个全新的发展空间.
2.
第二章摆动辗压基本原理及工艺点
2.1摆动辗压的原理
摆辗工模具的运动形式比较复杂。
与摆辗几的机床轴心线同心的模具为下模,其上固定工件,模具与工件一起绕自轴旋转。
轴心线与机床轴心线成r角斜交的模具为锥体模,即摆头。
它绕自轴旋转。
下模的旋转与锥体模同步。
两个模具中有一个模具沿机床轴心线方向平移实现轧制的压下进给。
以床身为参照物,锥体模与工件的接触面位置不变,即轧制变形力合力作用线相对静止,也可以说锥体模轴线上任意点的运动轨迹在接触面上的投影是一个点。
所以,此类摆辗摆头的运动轨迹是点。
图2.1摆辗机摆头运动示意图
由于攻击变形与模具和工件之间的相对运动有关,所以必须分析模具与工件的运动关系。
以工件为参照物,下模相对静止。
锥体模(摆头)轴线与机床轴线的交点作直线运动,锥体模轴线上其余各点,作螺旋运动,其参数方程为:
式中R——回转半径(mm)
——摆头旋转角速度(r/s)
t——时间(s)
s——时间t内模具沿机床轴向平移的距离(mm)。
锥体模轴线上任意点相对工件螺旋运动轨迹在工件上平面(xoy面)上的投影为圆,用极坐标表示为:
或用直角坐标的方程表示为:
摆辗锥体模在工件上表面运动轨迹的投影为圆,所以也可以叫圆轨迹。
由于锥体模在工件上滚动,其接触摩擦是滚动摩擦,摩擦力小,因而更有利于金属的塑性流动,能充分发挥轧制变形的特性,减少了锥体模的滑动磨损,成为摆辗的一个优点。
再者,由于工件随锥体模同向转到,其接触面与机床的相对位置不变,所以摆辗压力的合力作用线处于机床的固定位置,可以用一般轴承作运动副,机床结构简单,造价低廉,维修容易,寿命长。
2.2摆动辗压的特点
(1)省力。
因摆辗是以连续局部变形代替常规锻造工艺的一次整体变形,因此可以大大降低变形力。
实践证明,加工相同锻件,其辗压力仅是常规锻造方法变形力的1/5~1/20;
(2)产品质量高,节省原材料,可实现少无切削加工。
如果模具制