JS02精炼炉工艺技术规范.docx
《JS02精炼炉工艺技术规范.docx》由会员分享,可在线阅读,更多相关《JS02精炼炉工艺技术规范.docx(10页珍藏版)》请在冰豆网上搜索。
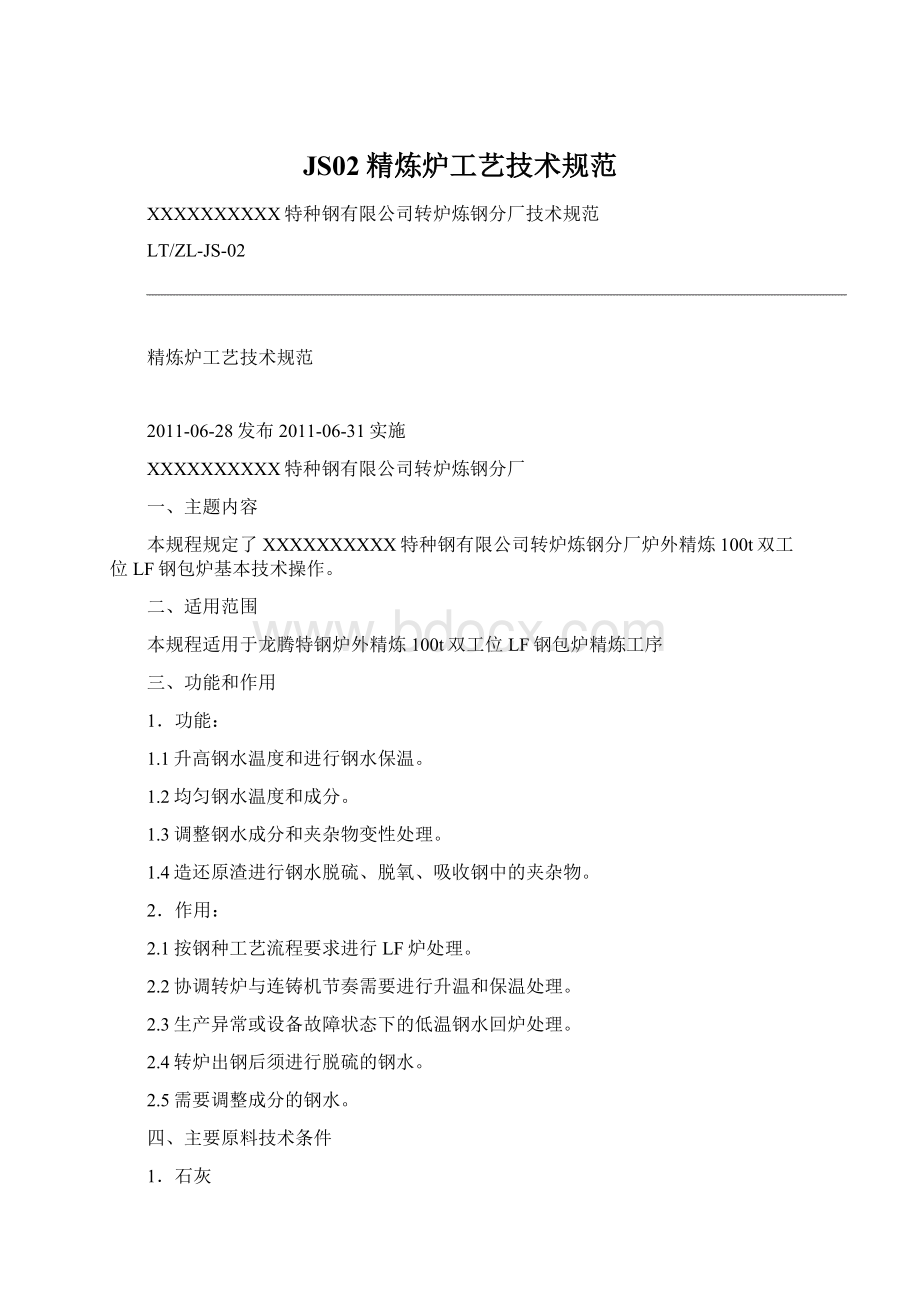
JS02精炼炉工艺技术规范
XXXXXXXXXX特种钢有限公司转炉炼钢分厂技术规范
LT/ZL-JS-02
精炼炉工艺技术规范
2011-06-28发布2011-06-31实施
XXXXXXXXXX特种钢有限公司转炉炼钢分厂
一、主题内容
本规程规定了XXXXXXXXXX特种钢有限公司转炉炼钢分厂炉外精炼100t双工位LF钢包炉基本技术操作。
二、适用范围
本规程适用于龙腾特钢炉外精炼100t双工位LF钢包炉精炼工序
三、功能和作用
1.功能:
1.1升高钢水温度和进行钢水保温。
1.2均匀钢水温度和成分。
1.3调整钢水成分和夹杂物变性处理。
1.4造还原渣进行钢水脱硫、脱氧、吸收钢中的夹杂物。
2.作用:
2.1按钢种工艺流程要求进行LF炉处理。
2.2协调转炉与连铸机节奏需要进行升温和保温处理。
2.3生产异常或设备故障状态下的低温钢水回炉处理。
2.4转炉出钢后须进行脱硫的钢水。
2.5需要调整成分的钢水。
四、主要原料技术条件
1.石灰
1.1化学成份要求:
执行公司原材料技术标准
1.2要求纯净,在仓内储存≤3天。
1.3粒度要求:
5~45mm
2.萤石
2.1化学成份要求:
执行公司原材料技术标准
2.2杂质<5%。
2.3粒度要求:
5~20mm。
3.合成渣、预熔精炼渣
3.1化学成份要求:
执行公司原材料技术标准
3.2粒度要求:
5~20mm
4.铁合金
4.1合金粒度:
10~30mm
4.2合金料必须按成份、品种分类存放,合金称量准确。
5.平台备料:
铝粉、硅铁粉、增碳剂及所需金属料等
五、精炼工艺制度
1.LF工艺流程
钢水进站−→吹氩搅拌−→钢包就位−→测温预加渣料−→加热造渣−→测温取样−→升温造渣−→成分调整−→测温取样−→喂丝处理−→软吹−→加保温剂−→钢包离位−→卸吹氩管−→吊包−→连铸
若出钢前的测温取样所得分析成分和温度仍不满足出钢要求,需继续进行成分和温度调整,直至合格为止。
根据钢种需要,可以在喂丝处理之前进行“定氧”。
2.精炼正常工作条件
2.1设备完好,水、电、气、油、风等各种介质运行正常。
2.2电极长度调整好,确保通电功率正常。
2.3冶炼前辅助料准备齐全。
2.4各种连锁检查到位。
2.5炉前工器具准备周到。
2.6钢包底搅拌系统畅通、完好。
2.7出钢用的钢包内渣圈最宽处小于250mm,钢包包沿的冷钢、冷渣处理干净,包沿渣顶部高度应小于100mm,内壁宽度应小于100mm,外壁宽度应小于100mm。
2.8最少钢水处理量:
60吨/炉,一般处理量为100吨/炉。
2.9钢液面以上钢包自由空间高度应不小于500mm。
2.10钢包钢水表面结壳时,电极不可以通电起弧,必须要破坏渣壳后方可冶炼,以免电极断裂。
2.11“LF”炉的水冷系统无报警(温度、流量)。
2.12变压器的冷却系统无报警(温度、流量)。
2.13电极升降系统无报警,炉盖在低位,钢包车到工作位。
2.14“LF”炉的液压系统无报警。
2.15“LF”炉的气动系统无报警。
3.通电操作
3.1档位电压,见下表
档位
1档
2档
3档
4档
5档
6档
7档
8档
9档
10档
11档
12档
13档
电压V
330
319
308
298
289
280
272
264
256
250
243
237
231
电流A
31490
32580
33740
34870
3.2通电起弧之前,应将电压档位调到低档位(6档),待渣料基本化清,电弧比较平稳时,将档位调到中高档位(2-4档),进行脱氧升温,在通电到5分钟后,进行测温取样,根据测温结果再调整电压档位,根据取样结果再调整成分,在调整成分和补加渣料之后,必通电化渣及合金熔化,待成分和温度基本符合工艺内控成分后,根据生产节奏,可顺用低档位(6或7档)进行保温操作。
注意在使用过程中最好不使用1档和13档。
3.3除初期起弧化渣外,全过程均须埋弧操作,严禁用高电压裸弧强制调温,以免损坏包衬,不能实现埋弧时要加入埋弧渣。
增碳、合金化及测温取样时须停电并抬起电极。
3.4加热时优先采用自动方式,异常情况采用手动。
3.5三根电极中的任意两根电极臂以下长度差超过150mm时须重新调整电极,使电极臂以下长度相等,电极下端在同一平面。
3.6严禁用电极增碳,掉入钢包内的电极头必须及时扒出。
3.7每次供电时间最长不能大于10分钟。
3.8尽量减少高压分闸次数,原则上每个浇次分闸1次。
4.吹氩操作
4.1正常操作:
在钢水包就位到钢包车之后,接通氩气,调整吹氩压力或流量,一般开吹压力不少于6bar,吹开后,调到压力3-5bar,总的吹氩流量不少于25Nm3/h,单个透气砖吹氩流量约15Nm3/h。
若在钢包车上停留时间较长,则再调低吹氩压力,直至钢水微微搅动,严禁钢水翻腾剧烈,当钢水精炼时,氩气压力调回至4-6bar。
在处理结束吊包前,停止吹氩,卸氩气管。
注意处理过程中,钢水液面不能裸露。
4.2若在精炼初期或在等待位时,发现钢包底部两个搅拌透气孔均堵塞,立即将该钢包开离精炼位,并用行车将钢水吊到吹氩站用事故氩枪进行紧急处理。
4.3在进行增碳、加渣料、加合金等操作时,钢包底吹氩控制在6bar。
遇到增碳困难时,可以打开旁通阀。
若氩气量仍不符合操作要求,可以接通手动吹氩;严重时,将钢包开出精炼位,吊运至吹氩站用事故氩枪进行紧急处理。
4.4加热期间,钢水溶池表面的搅拌部位的最大高度约50mm,搅拌直径约100mm,不允许发生喷溅现象。
具体压力视供氩系统的压力损失(管接头及钢液的静压力)而定。
4.5测温取样时,钢包底吹氩压力调至4~5bar,约40秒钟后,调氩至2-3bar,然后进行取样测温操作。
4.6在精炼等待位进行喂丝操作时,底吹压力不超过4-5bar。
4.7精炼结束时,需要进行软搅拌,底吹压力控制在3-4bar,使得渣面微微搅动,钢水不得裸露。
5.造渣操作
钢水进入工作位后,根据钢种和钢包内渣况,加入还原剂(如铝粉、硅铁粉等),同时加入约一半或全部造渣料,吹氩搅拌3~5分钟,然后再取样测温;完成以上操作后,根据钢水温度,确定供电时间,开始供电,供电过程中如渣料已熔化,可以把剩余的渣料加入,石灰加入总量为700~1000kg,萤石加入总量为100~200kg。
5.1造渣操作:
指钢包到精炼位后预加渣料开始,通过升温化渣、调渣,直至炉渣发白,碱度和粘度满足工艺要求。
5.2渣量调整:
一般钢包内总渣量在8~12kg/t,渣料配比:
CaO一般不超过10kg/t,CaF2一般不超过4kg/t,石灰和萤石的比例控制在2.5~3.0:
1(CaO,CaF2量包含转炉出钢时加的量);实际生产中,根据钢种要求的目标[S]含量及钢液实际[S]含量及炉渣的流动性而确认追加还原剂及渣量,直至渣白。
5.3渣样测试:
用细直吹氧管粘取少量渣样,冷却后观察判别。
5.4判定标准:
炉渣颜色:
黑色、褐色、灰色、绿色、黄色、和白色。
5.4.1渣呈白色或灰白色,表面气泡状、厚度适中(2~3mm厚),冷却后迅速风化,为理想的白渣;表明渣表明渣中(FeO)+(MnO)等氧化物85%以上以被还原,脱硫比较好。
5.4.2渣呈黑色,黑褐色,表明渣中(FeO)+(MnO)含量大于6%,需进一步还原。
5.4.3渣呈灰色,表明渣中(FeO)+(MnO)含量大于2%,需还原。
5.4.4渣呈绿色,表明渣中含氧化铬。
5.4.5渣薄、带有玻璃光泽,表明碱度偏低,(SiO2)或CaF2含量高,需要加石灰调整;加入石灰后必须通电,待渣全部化掉后重新取样观察。
5.4.6渣厚、表面粗糙,表示石灰加入过多,应加萤石或火砖屑调整。
6.脱氧操作
6.1脱氧操作在造渣过程中进行,并控制脱硫反应。
6.2钢包就位后,首先要根据钢水的氧化性强弱和转炉出钢下渣情况,选择合理脱氧方式。
6.3若钢水氧化性过强或转炉出钢过程中下渣严重,可以根据钢种的成分要气选用适量的较强的沉淀脱氧剂(如硅铝钡钙、铝块、铝铁、铝锰铁等)进行预脱氧,加新渣待渣料基本化清后(电弧稳定后),加0.3-0.5kg/t的精炼渣根据钢种特殊要求可加SiC2、硅铝粉或铝粉等还原剂,进行扩散脱氧。
注意,脱氧时,关上精炼炉门,保持炉门还原气氛。
待还原3-4分钟后,开炉门试渣,根据渣色判定,再决定是否继续加还原剂和渣料,直至得到白渣为止。
6.4还原剂加入注意事项:
先多加快加强脱氧剂,待渣转黄或浅黄色后,要勤加少加脱氧剂。
6.5脱氧温度控制在液相线以上30-40℃温度,炉渣碱度2.8以上。
7.合金调整
7.1加入条件:
通电至钢液温度达到1560℃以上,渣子基本变白后,取目标样(根据钢种、出钢过程中合金加入量及初始目标样,具体参见相应钢种工艺操作要点)进行补加合金。
7.2合金计算方法:
合金加入量(kg)=
7.3在成分控制范围之内,尽可能提高锰硫比、锰硅比。
8.时间控制
8.1精炼时间:
指钢包就位,炉盖降下到冶炼结束炉盖提升之间的时间。
8.2白渣时间:
指钢包内渣稳定于白渣状态时,所保持的白渣状态时间。
对于B级钢精炼时间不得少于20min,白渣(或黄白渣)保持时间不得少于10min,冶炼A36、30MnSi等钢种,精炼时间不得少于25min,白渣时间不得少于15min。
8.3出钢后钢水进行软搅拌,时间不得少于8min。
8.4精炼结束前5min之内,不允许添加任何合金料和渣料。
8.5钢水在开浇前10分钟之内停止搅拌,不得过早地吊运到连铸大包回转台
或保镇静时间大于5分钟以上。
9.测温取样
9.1测温
9.1.1测温次数:
测温时间一般在钢包炉刚开始通电之初、中间取样时及出钢前三个阶段进行测温,第一次和出钢前这两次必须进行测温。
9.1.2测温操作:
a)测温之前,检查测枪与仪表之间的线路完好性,然后用手工将热电偶轻轻的套在测温枪上,顶住测温头,但不能用力过大,以免损坏测温器内部热敏元件。
b)测温若采用手动模式时,测温点要求在电极和钢包内衬壁中间的搅拌中心部位进行,绝不允许在钢包电极节圆之内和靠近钢包壁进行测温,否则视为无效操作。
c)测温深度应为热电偶长度的三分之二,角度与熔池面呈70度。
d)测温应在电极停电后0.5~1.0min之内进行,且氩气处于开通情况下进行。
e)测温之后将测温枪上残余测温器卸下放置于规定地点。
9.2取样
9.2.1取样方式:
采用浸入式取样器,进行人工取样
9.2.2取样操作:
先将取样器套在取样棒上并塞紧。
在电极断电1min之内进行。
以70~80°斜直插入钢液中,插入深度一般在300mm~500mm。
9.2.3取样位置;取样点应搅拌的中心部位进行。
10.喂线操作
10.1技术要求:
10.1.1铝线线径Φ12±0.1mm,合金包芯线线径13±0.5mm。
10.1.2喂线速度:
铝线、合金包蕊线线速参见工艺要求,装线和卸线时的速度≤1M/s。
(操作速度旋钮调节,操作用手动操作)
10.1.3喂线时线要垂直于钢液面,其误差应控制在75-105°。
10.1.4喂线时线的出口距钢液面的距离应在300-800mm。
10.1.5喂线时线应喂到钢包中心直径为1000mm的区域。
10.2操作前的准备:
10.2.1每周必须校称一次,如果计量异常应随时校称。
10.2.2确认是否有线,线是否插进输线辊中。
10.2.3检查设备是否送电,各开关及指示灯是否正常。
10.2.4确认钢包是否在喂线位置。
10.3喂线操作:
10.3.1手动操作:
a)将“手动/自动操作旋钮”选到手动。
b)操作开关松开放线机的抱闸。
c)操作开关将导线管放下。
d)操作开关将压下轮压下。
e)启动喂线电机开按钮喂线,计数器开始计数。
f)当计数器的计数,达计划值时按以上相反顺序操作停止喂线。
10.3.2自动操作:
a)通过仪表设定所加线种和线量。
b)将手动/自动操作旋钮选到自动。
c)启动自动喂线按钮,系统将按预选设定的程序工作,指示灯亮。
放线机松闸→导线管放下→电机旋转→压下辊放下→喂线开始→仪表计数→放线机关闸→至设定量→喂线自动停止→电机失电→电机停转→压下辊抬起→导线管抬起→指示灯灭。
10.4当设备停车,报警灯亮时,应检查是否断线,如果断线,在处理好后按复位设备恢复正常,否则及时处理。
11.出钢前温度控制
钢水温度必须满足下一工序正常生产要求,具体见各钢种工艺要点。
一般经过LF炉后直接上连铸进行浇注,一般温度控制如下
喂线之前
喂线之后
开浇第一炉
T0+(80±5)℃
T0+(75±5)℃
连浇
T0+(70±5)℃
T0+(60±5)℃
说明:
T0是钢液的液相线温度;
对新钢包,LF出钢温度应适当再提高10~20℃;
以上温度参数还应结合实际生产调度情况。
12.电极使用更换
12.1操作前准备
当电极位置指示灯报警或电流表指示不足1/3刻度时,要求松电极或更换电极。
12.1.1高压分闸:
通知变电所将高压开关分闸,主控室高压急停按钮按下,通电允许开关锁定,钥匙拔下,并检查室外三相带电指示灯是否带电,如带电要查分闸情况,确保高压分闸成功。
12.1.2电极操作开关选择“现场操作”。
12.1.3电极台架停放在中间停放位。
12.2松电极
12.2.1行车小钩钩好电极上端的连接吊环,然后将电极提升臂往下降,直至吊钩张紧为止。
12.2.2将电极夹紧开关钥匙插入对应的相位孔,并打到松开位。
12.2.3将电极臂提升到电极长度适当位置,然后将夹紧开关打到夹紧位,拔下钥匙。
12.2.4电极臂提升250-300mm,将行车吊钩松出。
12.2.5注意电极夹环,严禁夹在电极接口处,要求夹在电极白线内。
12.3电极更换
12.3.1更换条件,电极松到上限位,仍不能满足供电要求,即电流不足,达不到刻度表的1/3。
12.3.2将需要更换的电极先吊出,插入电极存放架内,并从存放架上吊起事先续接好的电极插入相应的相位内适当长度,再夹紧。
12.4电极继接
a)将需接长的电极固定好,拧下提升塞头,并检查接口是否有裂纹及缺损情况,如有裂纹,丝口损坏超1/5就不能使用。
然后用有油压缩空气将电极螺纹内孔及电极端面吹扫干净(不能用钢棉或铁刷清扫擦拭),将联接用螺纹塞头也吹扫干净,插入螺纹内孔,用手拧紧(不加任何外力)且使之不能倾斜。
b)将需接上的电极去掉头、尾部包装,然后用有油压缩空气将电极螺纹内孔及电极端面吹扫干净(不能用钢棉或铁刷清扫擦拭),将提升塞头也吹扫干净插入螺纹内孔,用手拧紧(不用任何外力)且使之不能倾斜;把另一端(没有提升塞头的一端)用软垫子垫起来(以免在提升过程中损坏)。
c)用悬臂吊吊住电极尾部提升塞头的吊环,慢慢提起到待接电极的上方,对正,再慢慢落下,用专用扳手拧紧,拧紧前上下电极相距3-5mm时,要求再次用压缩空气将两电极端面吹扫,避免残留杂物影响导电,两节电极之间不得有空隙,不能松动。
d)电极连接的目标是:
要使相邻两节电极之间的连接处具有各向机械应力相等,断面上具有连惯的导电性和连接坚固牢靠。
12.5电极的下放
a)电极下放时的高度,要使电极处于上限时,电极下端的高度应高于钢包200mm以上。
b)电极夹紧时把持器把持部位应在电极安全线以外。
13.保温剂加入操作
13.1在LF炉处理所有操作结束后,加入保温剂。
13.2保温剂加入时要均匀铺盖在钢液面上。
14.事故的预防和处理
14.1严禁在炉盖漏水的情况下进行精炼操作。
14.2精炼过程中发现炉盖漏水等情况立即停止电极供电,提起电极、停止吹氩并抬起包盖,若包内无水将钢包车开到非工作位,对事故部位进行处理;若钢包进水,须首先关闭炉盖进水总节门,处理事故部位,待包内水蒸发干后在动车。
14.3钢包底吹透气砖安全可靠,操作机构灵活、安全可靠,钢包异常或钢包漏钢须立刻停止精炼,进行倒包或回炉处理。
14.4操作过程中随时检查电极抱紧情况,发现异常及时处理,防止电极折断掉入钢包。
14.5观察孔平台附近原料堆放整齐,保持操作空间开阔,精炼职工在观察孔测温取样或加料时,注意侧身对应观察孔,避免钢渣、钢水溅出伤人。
14.6准备喂丝线时,必须从线卷的椭圆形开口处抽出喂丝线,防止喂线过程中卡线,造成喂丝线断裂伤人。
在线喂丝过程中,开始需缓慢进线,待喂丝线进入升降导管后再加速到规定速度,避免喂丝线跑偏,接触电极,引发触电。
14.7电极接长和下放过程中,注意电极坠落伤人。
14.8精炼职工必须穿专用绝缘鞋,防止触电。
编制/日期:
批准/日期: