看板控制的单阶段供应链系统.docx
《看板控制的单阶段供应链系统.docx》由会员分享,可在线阅读,更多相关《看板控制的单阶段供应链系统.docx(14页珍藏版)》请在冰豆网上搜索。
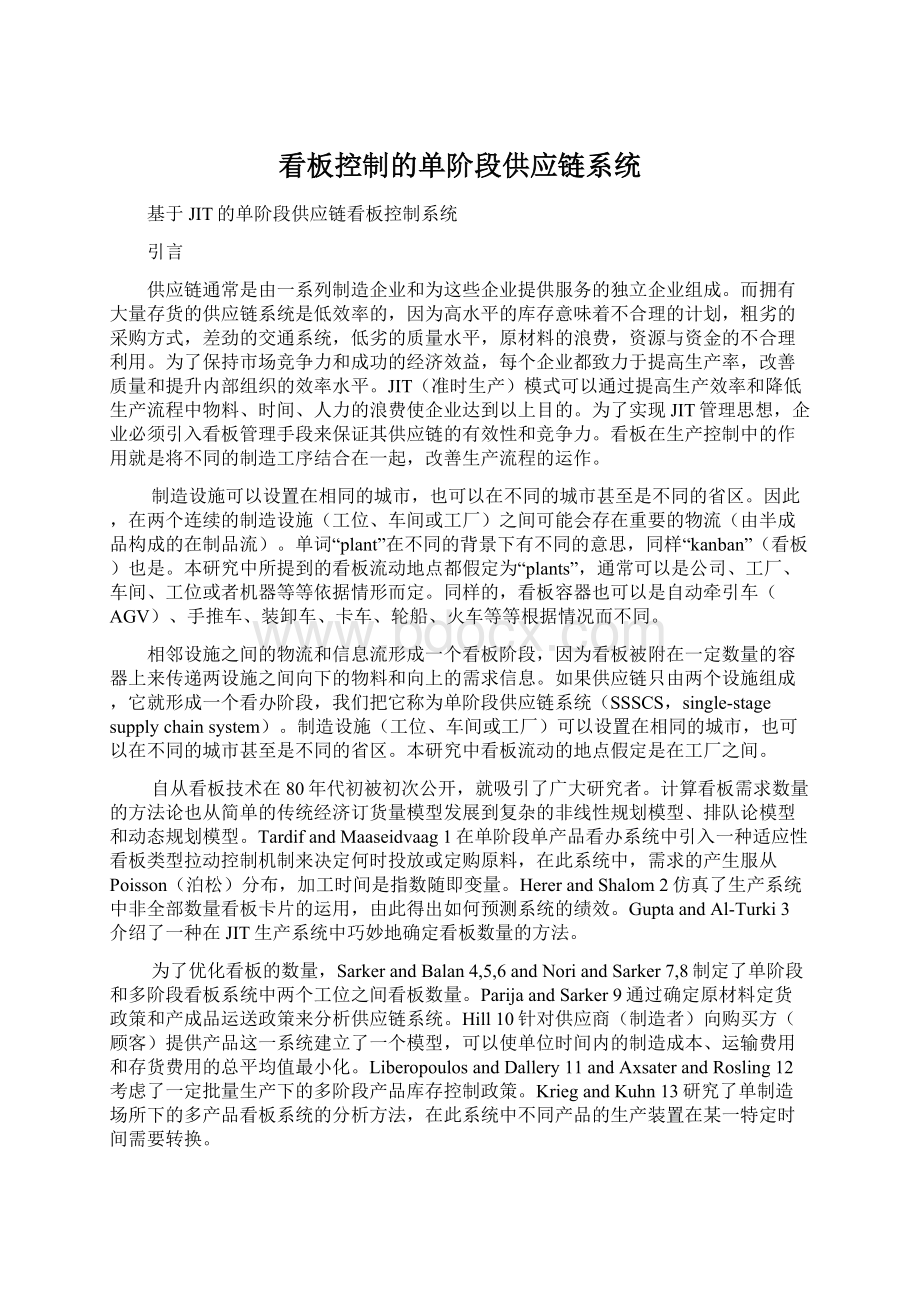
看板控制的单阶段供应链系统
基于JIT的单阶段供应链看板控制系统
引言
供应链通常是由一系列制造企业和为这些企业提供服务的独立企业组成。
而拥有大量存货的供应链系统是低效率的,因为高水平的库存意味着不合理的计划,粗劣的采购方式,差劲的交通系统,低劣的质量水平,原材料的浪费,资源与资金的不合理利用。
为了保持市场竞争力和成功的经济效益,每个企业都致力于提高生产率,改善质量和提升内部组织的效率水平。
JIT(准时生产)模式可以通过提高生产效率和降低生产流程中物料、时间、人力的浪费使企业达到以上目的。
为了实现JIT管理思想,企业必须引入看板管理手段来保证其供应链的有效性和竞争力。
看板在生产控制中的作用就是将不同的制造工序结合在一起,改善生产流程的运作。
制造设施可以设置在相同的城市,也可以在不同的城市甚至是不同的省区。
因此,在两个连续的制造设施(工位、车间或工厂)之间可能会存在重要的物流(由半成品构成的在制品流)。
单词“plant”在不同的背景下有不同的意思,同样“kanban”(看板)也是。
本研究中所提到的看板流动地点都假定为“plants”,通常可以是公司、工厂、车间、工位或者机器等等依据情形而定。
同样的,看板容器也可以是自动牵引车(AGV)、手推车、装卸车、卡车、轮船、火车等等根据情况而不同。
相邻设施之间的物流和信息流形成一个看板阶段,因为看板被附在一定数量的容器上来传递两设施之间向下的物料和向上的需求信息。
如果供应链只由两个设施组成,它就形成一个看办阶段,我们把它称为单阶段供应链系统(SSSCS,single-stagesupplychainsystem)。
制造设施(工位、车间或工厂)可以设置在相同的城市,也可以在不同的城市甚至是不同的省区。
本研究中看板流动的地点假定是在工厂之间。
自从看板技术在80年代初被初次公开,就吸引了广大研究者。
计算看板需求数量的方法论也从简单的传统经济订货量模型发展到复杂的非线性规划模型、排队论模型和动态规划模型。
TardifandMaaseidvaag1在单阶段单产品看办系统中引入一种适应性看板类型拉动控制机制来决定何时投放或定购原料,在此系统中,需求的产生服从Poisson(泊松)分布,加工时间是指数随即变量。
HererandShalom2仿真了生产系统中非全部数量看板卡片的运用,由此得出如何预测系统的绩效。
GuptaandAl-Turki3介绍了一种在JIT生产系统中巧妙地确定看板数量的方法。
为了优化看板的数量,SarkerandBalan4,5,6andNoriandSarker7,8制定了单阶段和多阶段看板系统中两个工位之间看板数量。
ParijaandSarker9通过确定原材料定货政策和产成品运送政策来分析供应链系统。
Hill10针对供应商(制造者)向购买方(顾客)提供产品这一系统建立了一个模型,可以使单位时间内的制造成本、运输费用和存货费用的总平均值最小化。
LiberopoulosandDallery11andAxsaterandRosling12考虑了一定批量生产下的多阶段产品库存控制政策。
KriegandKuhn13研究了单制造场所下的多产品看板系统的分析方法,在此系统中不同产品的生产装置在某一特定时间需要转换。
ZhaoandNakashimaetal14研究了一种综合的机制下的生产系统,此系统基于一种新型控制策略:
“推动式”的工件分配和“拉动式”(看板机制)的在制品控制相结合。
他们通过在工位上实施看板使产成品数量最大化同时使在制品数量最小化。
Askinetal15在他们的研究中使存货成本和缺货成本总量最小化。
对于少量工件类型或多工件类型的M/G/1系统,已经得出了统一稳定的研究结果。
论述相关观点著作的研究者还有AminandAltiok16、AytugandDogan17、Chauyetetal18、HorngandCochran19andKrajewskietal20。
本研究的目的是建立一个基于JIT生产理论的看板控制的SSSCS模型。
它致力于提高生产流程的效率,减少不必要的物料储存,使物料和时间浪费最小化。
本研究中的供应链系统包括三个实体:
供应商、制造商和零售商。
来自供应商的原料,生产阶段的在制品和运往零售商的产成品都由看板来控制。
看板的数量和生产批量的大小根据不同的情况来确定。
看板运作的规划要考虑装载时间、卸载时间和运输时间。
结合基于跨工厂作业的成本控制和管理约束,建立一个后勤支持模型来控制供应链系统。
以上所提到的所有的研究都谈论了看板控制供应链系统的以下两个问题:
设计和运作。
设计是要确定JIT制造方式的看板数量,而运作是要谋划一个看板运行方案。
在本研究中,班班控制的这两个问题都会考虑到。
看板阶段的问题描述
通过图1所示的SSSCS系统,看板的功能可以很好的解释。
在这个供应链系统中,生产首先被最后设施(最后工序)的需求所触发。
在看板运作中,当最后工序中满载容器中的第一个工件被取用时,就把附在容器上的传送看板取下,然后放在传送看版盒(WK)内。
传送看板盒中的看板定时或不定时的被运送车取走并且送到前道工序的生产看板盒(PK)中。
传送看板上显示容器中所需要补充的工件数量,使用此工件的前一道和后一道工序,看板的收集时间间隔等。
传送看板然后被附在前道工序的存货容器上来代替生产看板下达生产指令,此指令要求前道工序工人生产所需要数量的工件;也就是说,生产看板的取走触发了前道工序的生产。
带有传送看板的装满工件的容器被运输车运到前道工序。
这个看板循环实现了前后两道工序之间工件流动的平稳性,及时性和无耗性。
Figure1Asingle-stagekanbansupplychainsystem.
图中有K张看板(容器数量也是K),看板的序号用1、2……K表示。
一张看板通常包括以下内容:
工件号、工件描述、容器、单元装载(每个容器的容量)、储存地(从哪取货)、目的地(运往哪)。
供应链中的看板系统有一个普遍的目的,也就是说它不仅是一个信息载体,更是一个物料载体(即容器)。
但在本研究的供应链系统中,一张看板仅仅是附在传送工具上的卡片。
图中的空容器用空白的方框表示(如1、2、3),装满的容器用全阴影的方框表示(如5、……、K-1、K),而第2道工序上半满的容器用半阴影的方框表示(如4),即来自上道工序的成品正在被2道工序取用。
图中原材料(RM)的库存水平和产成品(FG)的存放水平分别在第1道工序之前和第2道工序之后显示,相应地,在制品(WIP)水平在图的下方表示。
实际上,原材料(RMs)、成品(FGs)、和在制品(WIPs)存放分别在上游、下游和第1道工序上。
为了图形表示的方便,用形式上的设址和容器的操纵来反映两道工序之间的JIT运作。
为了通过看板传送物料,首先,要确定每一阶段的生产批量;其次,研究运输时间、装卸载时间和基于所确定批量的需要的看板容器数量;再次,确定第一阶段向供应商订货的策略和最后一阶段向零售商发货的策略;最后,规划每一阶段的看板运转流程。
这些问题要通过最小化供应链总成本来解决。
看板控制的SSSCS所要解决的以上问题可以通过以下两步来完成:
一、建立一个描述供应链系统的数学模型,利用模型可以求解一定时期每一阶段的批量大小,几批和产品总量。
二、建立一个基于总成本描述看板机制的排队模型,通过此模型可以得出最优的容器数量。
运用以上的结果就可以制定看板的运转方案了。
单阶段供应链系统模型
典型的SSSCS的性能表现在三个成本要素上。
它们分别是第一道工序的原材料成本,两工序间的在制品成本和第二道工序的产成品成本。
这三项成本加起来就是SSSCS的总成本。
用下列符号表示:
指标:
i:
表示工序号i=1,2.
参数:
pi:
第i道工序的生产率,件/年
D:
需求率,件/年
c:
每件产品的变动成本或价格,美元/件
Hr:
原材料的存储成本,美元/件/年
Hw:
在制品的存放成本,美元/件/年
Hf:
产成品的存储成本,美元/件/年
Ar:
订货成本,美元/次(订购)
Asi:
第i道工序的制造成本,美元/批
Aw:
在制皮的传送成本,美元/次(传送在制品)
Af:
最后工序上产成品的运输成本(运往顾客),美元/次(运往顾客)
t:
时间,年
It:
第i年的库存水平,件
Iavg:
平均库存,件
Iavg:
周期时间,年
Tui:
第i道工序的正常运行时间,年
Cr:
原材料库存成本,美元/年
Cw:
在制品库存成本,美元/年
Cf:
产成品库存成本,美元/年
TC:
供应链总成本,美元/年
变量:
Q:
一个T时期内的产成品数量,件/年
Qr:
订购数量,件/次(订购)
Qw:
在制品传送数量,件/次(传送在制品)
Qf:
产成品运输数量,件/次(向顾客运输)
K:
传送工具(容器)的数量
no:
原材料的订购次数
mi:
正常工作时间第i阶段的容器配置数量
n:
最后一道工序(产成品)的容器配置数量
s:
正常工作时间最后一道工序的容器配置数量
原材料库存成本
对于原材料库,经济的订货数量被分解成订货次数no和订货批量Qr。
所订货物按照固定的间隔时间到达,所以原材料库可以在整个需求时期内(通常指每个循环的生产周期T)保持稳定的库存水平。
库存模型的变动在图2中表示,即需求率为D的EOQ(经济订货量)模型下经典的锯齿图。
图2原材料库存
此处的库存指的是在传统的经济批量模型下的。
模型中的原材料总成本Cr由以下公式得出:
Q/Qr是一个循环周期内的订购次数,D/Q是一定时期(一年)内的循环次数。
而平均库存Iavg=Qr/2,原材料总成本由以下公式
(1)得出:
在制品库存成本
在制品库存的显著特征由图3表示。
第一道工序消耗原材料,产生半成品构成在制品库存。
当工序1上的半成品水平达到批量标准Qw时,这些半成品被运到下一道工序。
每个运输容器都有一张看板,看板的数量与容器的数量(K)相等。
正常工作时,工序1连续的生产产品。
该运输的时候,Qw个工件和看板一起被装在容器中,然后运往下道工序。
这时,在制品水平不会降为零。
然后,在制品再次以pl的速率增长。
当第2次运送时刻到达时,又有Qw个工件被运往下道工序,就这样反复循环。
图3在制品库存
正常工作时间Tul所生产的产品数量为Q。
在此时间内,共有m批的在制品被运往下道工序。
当工序1的产品数量足够满足工序2的需求时,工序1停止生产,但在工序1停工的时间,工序2耗用在制品。
为了计算平均库存,图3转化为图4的模式。
实际的库存水平(包括运输的在制品)用虚线表示。
因此,平均的库存水平用以下公式
(2)得出:
产成品库存成本
工序2的产出构成产成品库存模型。
本阶段的产成品总库存水平以速率p2增长。
很明显,产成品的库存特征与半成品库存的一样。
因此,上面计算半成品平均库存水平的公式(3)可以直接用来计算产成品的平均库存:
而产成品的总成本可由下式得出:
SSSCS总成本
库存总成本包括原材料,制造过程和产成品发生的成本之和。
因此,总成本的计算可按以下公式(6):
此处n0、K、和n都是大于1的整数,Q是正数。
公式(6)是一个MINLP(非纯整数非线性规划)问题。
为了方便标记,用正的松弛变量x1、x2和x3替换式(6)中的整数值n0、K、和n,相应地,我们定义x=(x1,x2,x3,Q)。
同样,用Z替换TC。
因此,公式(6)变形为:
求解方法
MINLP问题可以通过多种算法解决,比如分支定界法、GBD算法(generalizedBenders'